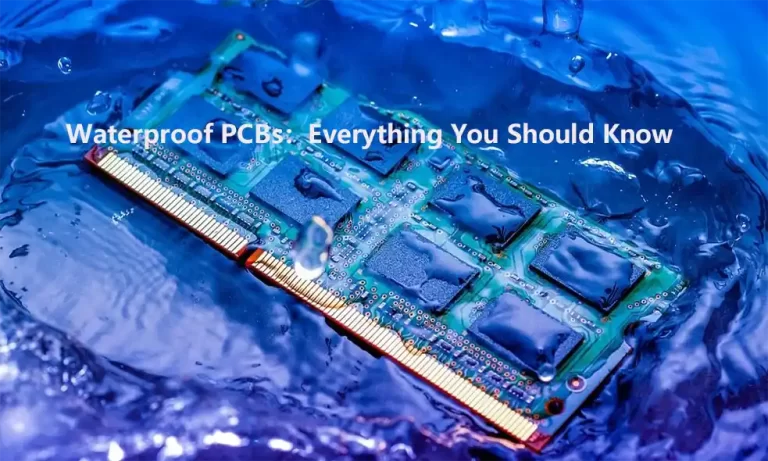
When the various components of a circuit board are subjected to tap water, it might result in short-circuits or lower the efficiency of the circuit. Thus, there’s an eminent need to shield these components from moisture and corrosion. At first, we need to must be done is to check and see if the fundamental circuitry of their device is resistant to water. In situations such as these, the adoption of waterproof PCB could be appropriatec. This guide will delve into their nature, significance, applications, and their prodution by manufacturers
What is a Waterproof PCBs?
Waterproof PCB possess a protective covering that equips them with resistance against moisture and other environmental attributes. Such PCBs are concurrently termed as waterproof printed circuit boards. This protective overlay is generally resin-based, enveloping the entire circuit board and its singular components. This fabricates a robust barricade impeding the penetration of water, dust, and other contaminants onto the board.
This waterproofing technique applies to both rigid and flexible circuit boards, offering increased safety for sensitive electronic components and electronics as a whole. It’s typical to see the implementation of waterproof printed circuit boards for critical components across diverse industries and applications. This includes realms such as medical, aerospace, military along with industrial and consumer electronics sectors
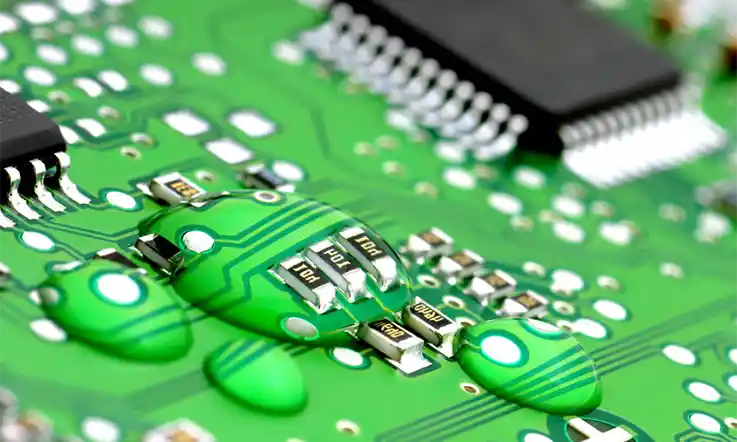
How to Waterproof Your PCB Boards?
Waterproof PCB are critically indispensable for any electronic apparatus that holds the potential to interact with water or moisture. It is possible to waterproof a printed circuit board in a variety of methods, such as the utilization of water-resistant PCB substrates, sealing of connectors, application of waterproof paint, and the deployment of waterproof material over the topmost stratum. The success of these methods can alter with varied types of PCB boards, depending primarily on the PCB’s applications and the extent of waterproofing required.
Under any and all circumstances, the optimal approach is to prevent moisture and water from reaching electronic appliances by isolating them. However, in conditions where the atmospheric water content significantly escalates, the application of waterproof PCBs is recommended for electronic circuit board usage. The PCBs employed in marine-based applications endure extremely high moisture levels throughout their operational lifespan. Consequently, standard PCBs fail to deliver effectiveness in such environments due to their propensity to absorb water.
Apply Waterproof Material on Printed Circuit Board:
This technique is utilized for the production of particularly specialized items, such as printed circuit boards for use in the control systems of vessels (ships, submarines, etc.). In this method, you can make the surface of the PCB board waterproof by adding a particular material to it, such as parylene C or parylene n.
In fact, parylene C and parylene N are the identical material. Both these substances are high-density polymers and have the potential to be morphed into exceedingly thin layers. The majority of the time, during application onto the circuit board, they exist in a liquid state. Post a specific time duration, they start the process of solidification, eventually resulting in a waterproof finish. In comparison to standard sealants like epoxy resin, Parylene C typically exhibits only around 2 mils (0.05 mm) thickness. Consequently, for achieving water resistance for PCB board, you can select be made between parylene C or parylene N.
Apply Waterproof Paint on the Printed Circuit Board:
Should the necessity for a waterproof PCB discover itself post-production, or if there’s a requirement to waterproof a DIE printed circuit board, it can be achieved through the application of waterproof paint. Equally, this approach can be employed to waterproof your PCB prior to production. Besides usability, the additional waterproof paint layer contributes considerably to augmenting the protective aspect of the board.
Implementing this methodology to safeguard PCB from moisture proves to be both proficient and cost-effective. Nonetheless, you should be careful about the quality of the paint. The market offers a plethora of waterproofing paints, but their quality and dependability are not uniformly high.

Apply Waterproofing Material to Seal up the Connectors:
Should the intention be to manufacturing a non-specific-use waterproof PCB, the choice is available to utilize waterproof materials to insulate the connectors on the printed circuit board. During usage, Connectors’ primary function is to facilitate the joining of various components, including wires, terminals, and sensors, amongst others, to one another and to other components.. Without thorough sealing, it leads to water permeating the PCB board, the consequential damage could instantaneously render your electronic devices or PCB inoperable.
Note:
When applying a conformal coating, it is necessary to examine and optimize the following four factors:
● The materials used in making the conformal coating.
● How to apply coatings.
● Steps for curing and drying conformal coating.
● Procedures, for inspecting conformal coating.
The ideal decision for each of these facets will hinge upon variables such as the volume of production and lead periods, the fixtures presently at disposal, environmental conditions, intricacy level of the PCB, among other elements.
Benefits of Waterproof PCBs
The following is a list of some of the most important advantages offered by waterproof PCBA:
Longer lifespan:These sorts of printed circuit boards typically have a longer lifespan than ordinary PCB since they are subjected to more strict quality inspections and are waterproofed.
High durability: Waterproof PCB can withstand high levels of water and dust. They have oxidation and corrosion resistance.
Excellent functionality: Waterproof printed circuit boards commonly use high-precision boards capable of supporting rapid transfer rates. Consequently, irrespective of meteorological conditions, they are expected to uphold an unwavering level of performance. Furthermore, additional testing is required to guarantee that they are of high quality and perform properly.
Comprehensive range of applications: For example, portable programs such as the ones on your mobile or smartphone can be used in regions with harsher weather.
The Limitations of Waterproof PCBs
The following are some of the key limitations of waterproof PCB:
● They have a higher overall cost, both in terms of production and buying.
● Producing waterproof PCB takes additional time. The application of conformal coatings as well as resin coatings is the primary cause of this issue. In addition to that, they demand extremely thorough testing.
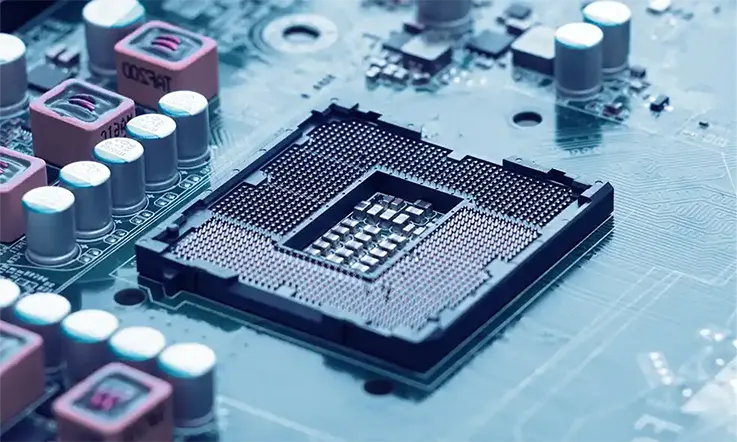
Test a Waterproof PCB Methods
Two techniques exist to determine if PCBs are waterproof:
● Using another compound: By applying a varied mixture to the conformal coatings, you can test their application. For instance, the addition of epoxy to a conformal coating that lacks epoxy. If the PCB has been coated uniformly, the concocted mixture will fail to adhere to the PCB.
● Using an alcohol spray: In order to test for liquid conformal coatings, we make use of this technology. After spraying the alcohol spray, if droplets start to form, this indicates that the waterproof PCB you have has a conformal coating that is liquid-based.
● Using Manual or automated inspection: Using a lamp, an inspector can perform a manual check to ensure that the coating is watertight. Alternately, we may make use of a computerized scanning or optical instrument.
The only alternate method to verify the effective waterproofing of the PCB is through its exposure to humidity. However, this approach could harbor a degree of risk. Consequently, we emphatically recommend restricting this method exclusively to the examination of prototype PCB.
How Should the Waterproof Application on PCB Be Handled?
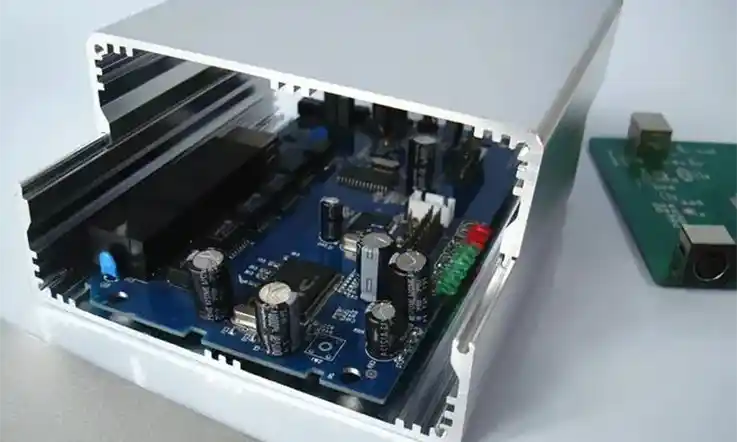
Dispensing:
This method of application is by far the most popular approach utilized for painting PCB boards. The paints are initially held in a hopper before being pumped into a gun as part of this operation. With the use of a spray gun, the paint will be applied to the PCB board by spraying it on.
Manual Spray:
This method mirrors dispensing closely, yet if a specialized paint machine is not available or diverse types of PCB boards, incompatible with the dispensing method, need to be painted, manual spraying can be utilized as a substitute. If provided with a choice, manual spraying is promoted over the dispense method, as it endows the operator with a high-level precision during painting and facilitates a smoother surface finish on the PCB board.
Dipping Process:
At this step, the PCB board is subjected to a coating process, where it is immersed in a paint tank – a commonly adopted industry process. Yet, owing to the requisite thickness of PCB boards, the dipping procedure is generally dissuaded while fabricating PCB boards and electronics. When the PCB boards are introduced to the clear coat through submersion, a considerable portion of the coat adheres onto the PCB board’s surface, while the residue loiters in the paint tank. This culminates in a non-uniform clear coat PCB coating on the PCB board.
Conformal Coating of a Waterproof PCB: How to Remove?
To implement repairs or modifications on an Epoxy PCB, the removal of the conformal coating may be deemed necessary. This can be achieved through various methods:
● Grinding (AKA Scraping): The PCB could be harmed using this technique. It entails manually scraping the PCB’s covering. It works best against polyurethane, parylene, and epoxy. Grinding, however, carries a risk because it could harm the PCB.
● Using Solvent: Waterproof coatings that are vulnerable to removal by solvents such as acetone compounds can be removed by these solvents.
● Micro-blasting: To remove the coating from the PCB, operators use a spray that combines compressed air and a soft abrasive. Epoxy and parylene resins are the most amenable to this technique.
● Peeling: A complex process in which an operator manually removes the coating from the PCB. Peeling often only works on hard silicone coatings.
● Applying concentrated heat: By applying heat, we are able to remove the majority of conformal coatings. However, there is a risk that this procedure will damage the PCB as well as the electronic components on it.
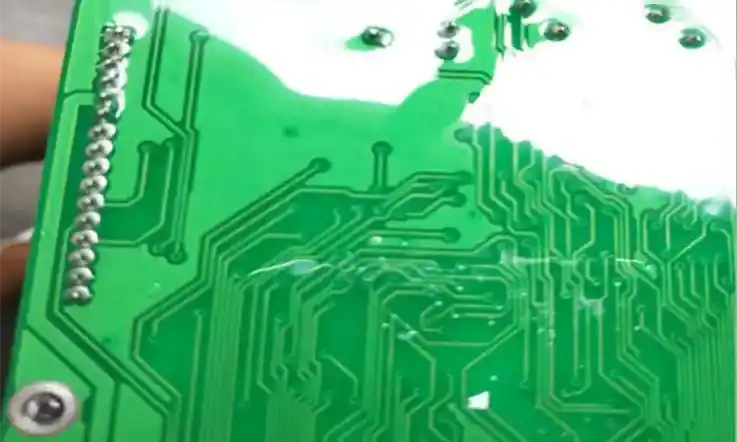
Is There a Solution Beyond Conformal Waterproof Coatings?
As we known that the conformal waterproof coating is one of the most useful and well-liked materials that are utilized to protect PCB boards. It is an extremely thin, elastic and protective layer that can be dispersed over the PCB circuit board to ensure its water resistance. Due to its property, PCB acquire protection against potential damage across multiple environment. Regardless of their extensive utility, conformal waterproof coatings bear certain weaknesses that merit attention. In specific situations, they fail to afford adequate protection to PCB board due to their inherent limitations. Predominantly, two central factors contribute to this predicament:
● The conformal waterproof coating doesn’t stick well so it can’t fully protect the PCB board from water seepage.
● In conditions or highly corrosive environments the PCB board could still get damaged despite the waterproof coating keeping water out.
In the past, PCB manufacturers solely relied on the application of conformal waterproof coatings as their protective measure for the boards. The absence of any alternative approaches left them directionless in dealing with this issue. Consequently, they had to exercise meticulous scrutiny over the design of the PCB board and utilize specific PCB materials to ensure the board’s water resistance capabilities.
When to Use Waterproof Enclosure and Conformal Coating?
Enclosures stand apart from conformal coatings.If you need to make your electronics waterproof, you will need to employ enclosures. The major task of safeguarding your electrical devices from both air and water is accomplished by the use of enclosures. Aptly compared to the role of a conformal coatings, an enclosure provides shielding to your electronics or PCB Circuit Boards from various environmental exposures such as water, air, corrosive gases and other potentially detrimental factors.
In order to ensure that the surface of a PCB board is waterproof, conformal waterproof coatings are often sprayed onto the board.
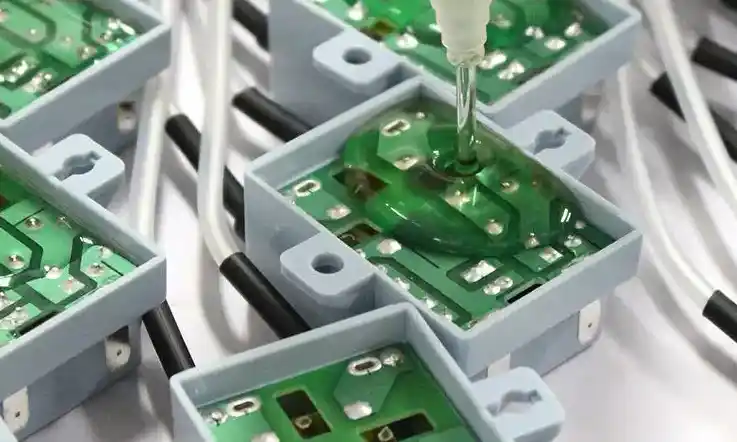
So Which One Do You Need?
● Should you undertake the creation of your own electronic devices or waterproofing of circuit boards, you’ll unquestionably need to consider conformal waterproof coatings along with enclosures. Utilizing them in tandem is advisable under circumstances where the environment is exceedingly corrosive or moisture-laden, rendering the use of just one inadequate. It is conceivable that the necessity to confer a waterproof attribute to your electronic devices or PCB boards only arises under specific conditions. In such unique situations, one might opt for conformal coating as an alternative to enclosures.
● Securing printed circuit boards from moisture intrusion during exposure to corrosive and humid conditions can be achieved through the application of conformal coatings. It is emphatically suggested to employ conformal coatings for the protection of any electronic devices or PCB when operating in environments characterized by combined factors of moisture and corrosiveness.
● It is not necessary to employ conformal waterproof coatings at all if you are constructing a waterproof PCB for a specific purpose.Such as the fabrication of PCB for the control systems of maritime vessels ships and submarines does not necessitate these types of protections. This is because it is not permitted that water get into the control system, since this could result in the ship or submarine sinking.
All in all, There are many strategies can be employed to render your circuit boards or other electronic devices water resistant. You hold the liberty to cherry-pick an approach that precisely meets your needs. For ensuring your electronics or PCB are waterproof against humid conditions, it’s advisable to first apply a conformal coating, followed by enclosures if required. This is because conformal coatings are more water resistant than enclosures. With this methodology, your electrical components or PCB receive comprehensive protection, not just against moisture but also corrosion and other potential harm inducers.
Temperature Changes’ Effects on Waterproof PCBs
Temperature shifts that are outside the parameters of the waterproof PCB could cause it to become damaged. As previously mentioned, exceedingly high temperatures might compromise the integrity of the conformal coating layer. In such instances, it would be futile to endeavor waterproofing the area utilizing this technique.
In addition, to the application of conformal coating and the waterproof enclosure any excess heat produced within the circuit board may not dissipate effectively. This could negatively affect the performance of the PCB board and shorten its lifespan. Hence it is crucial to assess the suitability of the coating material. Its thickness and calculate the amount of heat generated before applying conformal coating
Are Waterproof PCBs Customizable by Your Company?
We can customize most waterproof PCB during the manufacturing process. However, once we apply the waterproof coating, it becomes nearly hard to modify the PCB’s design, unless you use structural waterproofing to remove the encasing without causing any damage to it.
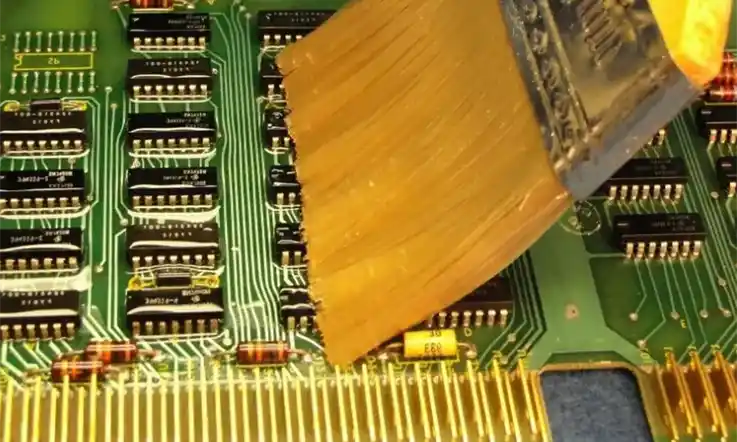
Conclusion
When it comes to excessive humidity and corrosion, a waterproof PCB is your best bet. The waterproof PCB excel in environments with high humidity, making them ideal for marine and military use.
At present, enclosures and conformal coating are the main two ways of PCB waterproof.
The method for the conformal coating encompasses the application of an excruciatingly svelte stratum of chemical composites including parylene, urethane, and acrylic on the uppermost tier of the PCB, with the intention of sealing it. Contrarily, waterproofing enclosures are boxes constructed from plastic or stainless steel. These enclosures act as a protective shield separating the Printed Circuit Boards and the exterior environment, and they proffer an enhanced defiance to water relative to conformal coatings.
Related Posts:
1.How to Build a Heater PCB Circuit Boards?
2.What is a Round Printed Circuit Board (PCB)?