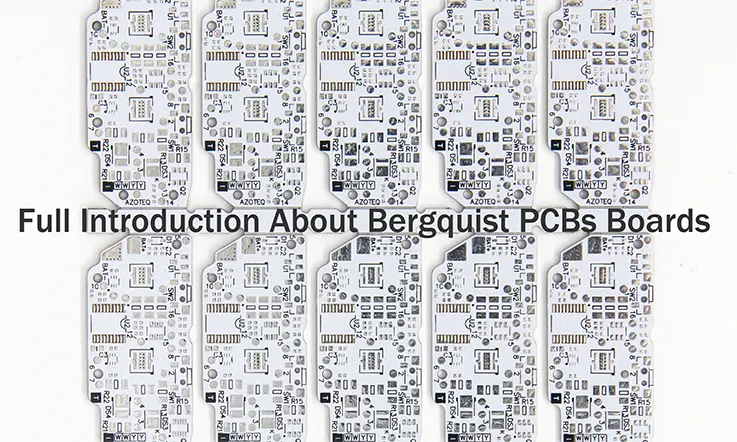
Managing heat in electronic systems is no cakewalk. It’s one of those make-or-break aspects that can decide the success of a device. Enter Bergquist PCBs, an innovative solution offering superior thermal management. For professionals in LED lighting, high-power electronics, and PCB manufacturing, this article dives deep into Bergquist PCBs, explaining their design, applications, manufacturing and Assembly details.
What is a Bergquist PCB and Its Core Benefits?
Bergquist PCBs are high-performance circuit boards specifically designed to solve one of the most critical issues in modern electronics: thermal management. These PCBs utilize Thermal Clad technology, offering advanced heat dissipation capabilities that make them ideal for demanding applications such as LED lighting, high-power electronics, and automotive systems. By offering superior thermal conductivity, electrical insulation, and environmental compliance, Bergquist PCBs stand out in industries where heat is a constant challenge. Below is a deeper dive into their key properties, thermal characteristics, and material advantages.
Overview of Bergquist Thermal Clad Technology
Bergquist’s Thermal Clad PCB technology is engineered to improve the efficiency of heat dissipation from electronic components, particularly in devices that generate a significant amount of heat. The design incorporates a metal-based core (commonly aluminum or copper) and a highly thermally conductive dielectric layer, ensuring that heat is efficiently transferred away from the components.
The most distinctive feature of Thermal Clad PCBs is their ability to integrate metal substrates with standard PCB layouts. This technology supports a robust thermal interface and significantly reduces the overall thermal resistance compared to traditional FR4 (fiberglass-based) boards.
Thermal Management Comparison
Property | Bergquist Thermal Clad PCBs | Traditional FR4 PCBs |
Thermal Conductivity | 2.4 – 7.5 W/mK | 0.3 – 0.6 W/mK |
Base Material | Aluminum/Copper | Fiberglass |
Heat Transfer Efficiency | High | Moderate to Low |
Dielectric Layer Thickness | 0.2mm – 1mm | 0.5mm – 2mm |
Operating Temperature Range | -40°C to +150°C | -40°C to +130°C |
As seen in the table above, Bergquist Thermal Clad PCBs outperform traditional FR4-based boards in terms of thermal conductivity and heat transfer efficiency. With a thermal conductivity range of 1-9.0 W/mK, Bergquist materials allow heat to be transferred more efficiently, which is a crucial factor in preventing thermal failure in high-power systems.
Key Properties of Bergquist PCBs
Bergquist PCBs offer a variety of advantages, especially when it comes to maintaining high performance in high-power electronics. Let’s explore the key properties in more detail:
1.Superior Thermal Conductivity-
One of the most impressive features of Bergquist PCBs is their ability to conduct heat away from heat-sensitive components. The copper or aluminum substrates provide excellent thermal transfer capabilities, ensuring uniform temperature distribution across the board.
●Copper Substrate: 390 W/mK conductivity
●Aluminum Substrate: 205 W/mK conductivity
These values are significantly higher than those of typical FR4 boards, making Bergquist an ideal choice for LED or high-power industrial applications.
2.Electrical Insulation-
Despite the focus on heat transfer, Bergquist PCBs are designed to provide superb electrical insulation between components, preventing electrical shorts while handling high-power loads.
3.Durability and Longevity-
These PCBs are built to handle challenging environments, resisting damage from factors like strong vibrations, elevated temperatures, and moisture exposure. Their robust construction makes them well-suited for demanding applications such as automotive electronics, where reliability over extended periods and under harsh conditions is non-negotiable. When the going gets tough, these boards stay steady, delivering performance you can count on.
4.Compact and Lightweight-
Bergquist PCBs allow for compact designs without sacrificing performance. The efficient thermal transfer means that manufacturers can create smaller devices that pack a big punch, making them ideal for applications like LED lighting and wearable technology.
Bergquist PCB Laminates Types
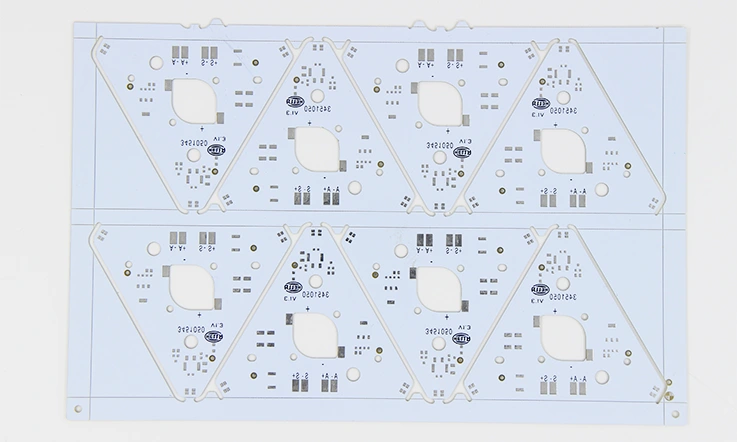
Bergquist’s PCB laminates are designed with one purpose in mind: to provide superior thermal management and mechanical stability for a wide range of electronic applications. Each laminate type is crafted to meet specific demands, such as heat dissipation, durability, and performance under high-stress conditions. In this section, we will explore Bergquist PCB laminates, focusing on their composition, unique characteristics, and where each type excels. Whether you’re designing for LED lighting systems, automotive electronics, or high-performance computing, understanding the differences in laminate types is crucial for achieving the best results.
1.Bergquist HT-07006: High-Temperature Laminate for Demanding Applications
HT-07006 is a high-temperature PCB laminate designed for use in environments where both high power density and elevated operating temperatures are common. This laminate is often used in power electronics and other systems that need to manage significant heat levels while ensuring the integrity of the components.
Key Features:
●Thermal Resistance: With exceptional thermal conductivity, the HT-07006 efficiently transfers heat from sensitive components, preventing damage.
●High-Temperature Stability: Designed to operate at temperatures up to 150°C, it ensures long-term durability, even under high-heat conditions.
●Electrical Insulation: Provides excellent electrical insulation, making it safe to use in power systems where high-voltage components are present.
Example Use Cases:
●Automotive Power Systems: Ideal for electric vehicle electronics, where components need to withstand high temperatures from continuous operation.
●Industrial Electronics: In industries like power generation, HT-07006 excels by ensuring power modules remain stable despite fluctuating temperatures.
Key Features & Specifications of HT-07006-
Property | HT-07006 |
Thermal Conductivity | 4.1 W/m·K |
Operating Temperature | Up to 150°C |
Dielectric Strength | 20 kV/mm |
Glass Transition Temp. | 180°C |
Flammability Rating | UL94 V-0 |
Electrical Insulation | Yes |
Material Type | Ceramic-Aluminum |
Applications | Power Electronics, Automotive |
HT-07006 stands out due to its ability to withstand high temperatures while maintaining efficient heat dissipation, making it an excellent choice for high-power devices like electric vehicle powertrains or industrial electronics.
2.Bergquist MP-06503: Medium-Performance Laminate for Versatility
MP-06503 is a reliable PCB laminate known for its adaptability and ability to manage thermal demands in medium-power electronic systems. Engineered for consistent output, it excels in applications requiring steady operation across varying environmental conditions. Its balance of thermal performance and durability ensures it holds its own, whether handling fluctuating temperatures or powering through moderate energy loads. Simply put, it’s a solid pick for when your setup needs that extra edge without breaking a sweat.
Key Features:
●Medium Thermal Conductivity: While not as high as HT-07006, the MP-06503 offers a respectable thermal conductivity that allows for effective heat dissipation.
●Electrically Insulated: Like other Bergquist laminates, this type provides electrical isolation, ensuring the safety of both components and operators.
●Adaptability: The laminate’s design makes it highly adaptable, suitable for applications that don’t require extreme thermal resistance but still need reliable performance.
Example Use Cases:
●Consumer Electronics: MP-06503 is frequently used in LED lighting and telecommunications equipment.
●Portable Power Systems: Its versatility makes it suitable for battery packs and power chargers that need reliable heat management.
Key Features & Specifications of MP-06503-
Property | MP-06503 |
Thermal Conductivity | 2.4 W/m·K |
Operating Temperature | Up to 130°C |
Dielectric Strength | 20 kV/mm |
Glass Transition Temp. | 150°C |
Flammability Rating | UL94 V-0 |
Electrical Insulation | Yes |
Material Type | Epoxy Glass |
Applications | Consumer Electronics, Telecom |
MP-06503 is commonly used in LED lighting systems and communication equipment due to its thermal management and versatility, ensuring stable performance under moderate environmental stress.
3.Bergquist HPL-03015: High-Power Laminate for Advanced Applications
HPL-03015 is a high-power laminate engineered for systems where heat loads are much higher than average. This material excels in high-performance electronics, where both electrical insulation and efficient thermal management are necessary for long-term reliability.
Key Features:
●Superior Heat Dissipation: Thanks to its high thermal conductivity, this laminate effectively manages heat in high-power systems, ensuring efficient thermal flow.
●Electrical Insulation: Designed with electrical isolation, it prevents short circuits while maintaining optimal thermal performance.
●Enhanced Durability: Its robust structure can withstand extreme environments, from high-frequency circuits to military-grade electronics.
Example Use Cases:
●High-Power LED Arrays: In applications where LED lights are clustered together for industrial illumination, this laminate ensures that heat generated is quickly dissipated.
●Military and Aerospace Electronics: The HPL-03015 is a popular choice in military and space electronics where systems must function reliably in extreme conditions.
Key Features & Specifications of HPL-03015-
Property | HPL-03015 |
Thermal Conductivity | 7.5 W/m·K |
Operating Temperature | Up to 180°C |
Dielectric Strength | 25 kV/mm |
Glass Transition Temp. | 200°C |
Flammability Rating | UL94 V-0 |
Electrical Insulation | Yes |
Material Type | Copper-Aluminum |
Applications | Power Electronics, LED Arrays, Aerospace |
HPL-03015 excels in applications requiring reliable long-term heat dissipation, such as high-performance power systems or military electronics.
4.Bergquist HT-04503: High-Thermal-Performance Laminate for Power Electronics
HT-04503 is another high-thermal-performance laminate, specifically designed for applications that involve high-power systems with significant heat dissipation requirements. Its ability to perform in high-temperature conditions makes it a popular choice for industries like automotive, telecommunications, and high-frequency circuits.
Key Features:
●Enhanced Thermal Management: With improved thermal conductivity compared to standard PCBs, HT-04503 ensures that heat is moved away from sensitive components, preventing overheating.
●Long-Term Reliability: Designed to endure extreme conditions, HT-04503 guarantees long-lasting durability even in high-stress environments.
●Electrically Insulated: It also maintains electrical insulation, allowing it to be used in both low and high-voltage systems without risk of electrical interference.
Example Use Cases:
●Power Electronics: The HT-04503 is a go-to choice for high-performance power converters, where maintaining efficiency under load is key.
●Electric Vehicles: For EV powertrains, HT-04503 supports heat management while delivering the required electrical insulation to keep the system safe.
Key Features & Specifications of HT-04503-
Property | HT-04503 |
Thermal Conductivity | 4.1 W/m·K |
Operating Temperature | Up to 175°C |
Dielectric Strength | 22 kV/mm |
Glass Transition Temp. | 190°C |
Flammability Rating | UL94 V-0 |
Electrical Insulation | Yes |
Material Type | Copper-Polymer |
Applications | Power Converters, Electric Vehicles |
HT-04503 is ideal for applications such as electric vehicle chargers or high-frequency power supplies due to its excellent thermal management and robust insulation.
Bergquist PCB Laminates
Below is a comparison of all four Bergquist PCB laminates discussed, allowing you to quickly assess the differences in thermal conductivity, dielectric strength, and other key characteristics.
Property | HT-07006 | MP-06503 | HPL-03015 | HT-04503 |
Thermal Conductivity | 4.1 W/m·K | 2.4 W/m·K | 7.5 W/m·K | 4.1 W/m·K |
Operating Temperature | Up to 150°C | Up to 130°C | Up to 180°C | Up to 175°C |
Dielectric Strength | 20 kV/mm | 20 kV/mm | 25 kV/mm | 22 kV/mm |
Glass Transition Temp. | 180°C | 150°C | 200°C | 190°C |
Flammability Rating | UL94 V-0 | UL94 V-0 | UL94 V-0 | UL94 V-0 |
Electrical Insulation | Yes | Yes | Yes | Yes |
Material Type | Ceramic-Aluminum | Epoxy Glass | Copper-Aluminum | Copper-Polymer |
Applications | Power Electronics, Automotive | Consumer Electronics, Telecom | Power Electronics, LED Arrays, Aerospace | Power Converters, Electric Vehicles |
Design Considerations for Bergquist PCBs
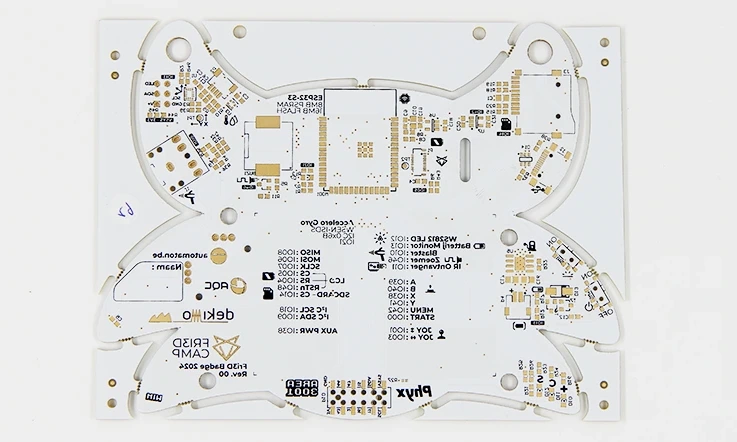
When designing Bergquist PCBs for high-performance applications, there are several factors that need to be considered to ensure the PCB performs effectively in challenging environments. Thermal management is one of the most pressing concerns, as excessive heat can lead to reduced reliability, lower performance, and even component failure. By taking a structured approach to substrate selection, heat dissipation, and custom layouts, engineers can optimize their designs to meet the demands of modern electronics.
Selecting the Right Substrate for Thermal Needs
Choosing the right PCB substrate material plays a huge part in designing a Bergquist PCB. It impacts how heat is handled, making sure everything stays in check. Aluminum and copper substrates are top choices for their ability to conduct heat efficiently and provide solid performance under pressure. Whether it’s heat management or reliable operation, these substrates deliver exactly what’s needed to keep the system in top shape.
Aluminum vs. Copper Substrates: A Comparison-
Property | Aluminum PCB | Copper PCB |
Thermal Conductivity | 1 W/mK to 7.5 W/mK | 4.0 W/mK to 9.0 W/mK |
Cost | More cost-effective for standard designs | More expensive but offers superior performance |
Applications | Used in mid-range power applications, LEDs | Best for high-performance, high-watt-density applications |
Durability | Good resistance to thermal stress | Superior in high-heat environments |
Ease of Fabrication | Easier to fabricate and assemble | Requires specialized processes for high-performance designs |
Aluminum PCBs are a go-to option for mid-range power needs, particularly when it comes to LED lighting systems. With their solid thermal conductivity and budget-friendly price tag, they’re a sweet spot for designs that require heat management without cranking up the power too high. These boards offer a good balance between performance and cost, making them perfect for projects where steady heat control is a must, but without the high power demands.
On the other hand, copper PCBs are typically used in high-performance applications where superior heat dissipation is required, such as high-watt-density applications or power electronics. Copper’s higher thermal conductivity allows it to more effectively transfer heat away from critical components, ensuring that the device operates at optimal temperatures.
For example, when designing a high-power LED module or a power converter for electric vehicles, using a copper PCB can help prevent overheating and ensure the system maintains efficiency even under heavy load.
Choosing the Best Substrate for Your Application-
●Aluminum PCBs are best suited for applications that require efficient heat management but don’t have extremely high thermal demands, such as general LED lighting.
●Copper PCBs, while more costly, are the go-to option for designs that need exceptional heat dissipation and durability in demanding environments, like power supplies for electric vehicles or telecommunications equipment.
Optimizing Heat Dissipation in Layouts
Proper heat dissipation is a critical component of any PCB design, especially when dealing with high-watt-density applications. To manage heat effectively, thermal vias, heat sinks, and copper pours are commonly used in Bergquist PCB designs. These techniques help channel excess heat away from sensitive components, maintaining performance and extending the lifespan of the PCB.
Thermal Vias and Their Role in Heat Transfer-
Thermal vias are small holes drilled into the PCB that allow heat to pass from one side of the board to the other. These vias are typically filled with copper to facilitate the heat flow from the heat-generating components to the heat-dissipating layers. Properly designed thermal vias ensure that the heat is distributed evenly, preventing hot spots and thermal damage to components.
Copper Pours: Enhancing Heat Distribution-
A copper pour refers to a solid layer of copper used to connect heat-sensitive areas of a PCB, offering a path to disperse heat more evenly across the board. The larger the copper pour, the better the thermal conductivity, as the copper helps in spreading the heat to areas where it can be dissipated.
Heat Sinks: Maximizing Thermal Performance-
Heat sinks are another tool often employed to improve thermal management. These devices are typically attached to Bergquist PCBs to help draw heat away from high-power components. They act as additional heat exchangers, expanding the surface area for heat dissipation and increasing the efficiency of the overall design.
Optimizing Thermal Performance: A Case Study-
Consider a power electronics system used in electric vehicles that requires precise thermal management. By implementing thermal vias to connect the copper pour to a heat sink, engineers can efficiently manage heat distribution, preventing the system from overheating under high demand. Using Bergquist HT-07006 substrate materials with an integrated copper pour and heat sink will help ensure the system performs consistently, even under heavy usage.
Custom Layouts for High-Watt Applications
Designing custom PCBs for high-watt-density applications—like LED modules, power electronics, and automotive power systems—requires a tailored approach. The key to success lies in creating layouts that maximize thermal dissipation while also optimizing signal integrity and component placement.
High-Watt-Density Applications-
In high-watt-density applications, components tend to generate a substantial amount of heat, which can compromise the performance and longevity of the device. Creating a custom layout with proper thermal management techniques, such as thermal vias and copper pours, will ensure that heat is evenly distributed and doesn’t concentrate around sensitive areas.
Designing for LEDs and Power Modules-
When designing LED modules or power modules for demanding applications such as electric vehicles or industrial machines, engineers must consider both electrical and thermal requirements. Custom layouts allow designers to strategically position high-power components and implement efficient thermal paths, making use of Bergquist materials like Hi-Flow or Sil-Pad to maximize heat transfer.
For Example: A high-watt LED module in a street lighting system must be designed with a custom PCB layout that considers heat from both the LED itself and its driving electronics. By using Thermal Clad PCBs and placing thermal vias directly under the LED to connect to a heat sink, designers can ensure the system operates optimally for a long lifespan.
Custom PCB Manufacturing for High-Watt Applications: A Real-World Approach
Application | Design Feature | Thermal Management Solution |
Power Modules | High-density component placement | Custom layout with thermal vias and copper pour |
LED Systems | High-brightness, high-power LED | Heat sink integration with thermal vias |
Automotive Power Systems | Power inverters, batteries | Copper substrates, custom layout for heat dissipation |
Manufacturing Process for Bergquist PCBs
Creating high-performance Bergquist PCBs involves a precise, multi-step manufacturing process that ensures the end product meets the stringent demands of thermal management and electrical efficiency. With a focus on advanced quality control, automation, and innovative thermal solutions, the manufacturing of these PCBs is designed to handle everything from standard applications to high-watt-density systems.
Thermal Clad Material Preparation
The first step in manufacturing Bergquist PCBs is the preparation of Thermal Clad materials. This process is the backbone of creating substrates that efficiently transfer heat, making them suitable for use in a range of high-power applications.
Layering Process of Bergquist PCB Materials-
1.Base Material Selection: The process starts with selecting the appropriate base material, whether it’s aluminum, copper, or a specialized thermal substrate. These materials are chosen based on the thermal conductivity and mechanical strength needed for the final application.
2.Thermal Interface Layering: The next step involves applying a thermal interface material, like Gap Pad or Sil-Pad, between the substrate and the electronic components. This helps in improving heat transfer while maintaining electrical insulation.
3.Bonding Layer: In this step, a thermally conductive adhesive or Bond-Ply is used to bond the layers together, ensuring a firm attachment and excellent heat transfer.
4.Solder Mask Application: The solder mask, which protects the PCB from environmental damage and ensures that components are properly aligned during assembly, is then applied to the substrate.
5.Drilling and Etching: After the base and bonding layers are in place, precision drilling is used to create holes for vias and components. Etching is then used to carve out the circuit paths on the copper layer.
Advanced Manufacturing Techniques for Layering-
In Bergquist PCB manufacturing, thermal clad materials are engineered with specific attention to detail, ensuring that the entire layering process is optimized for thermal conductivity and mechanical reliability. The final result is a PCB that delivers consistent performance in power-hungry applications, including LED lighting and automotive systems.
Advanced Quality Control Techniques
The quality of Bergquist PCBs is assured through a range of high-precision manufacturing and quality control measures. These techniques ensure that each PCB meets the thermal and electrical performance standards required for mission-critical applications. The process involves several layers of inspection, from initial fabrication to final assembly.
Inspection Methods for Thermal and Electrical Integrity-
1.Thermal Testing: This includes using thermal cameras and infrared sensors to monitor the heat distribution across the PCB during operation. By checking the heat map, we can verify if the thermal vias and heat sinks are effectively managing the heat load.
2.Electrical Integrity Testing: After the thermal tests, the electrical paths are checked for conductivity and signal quality. This ensures there are no disruptions or inefficiencies in the circuit.
3.Automated Optical Inspection (AOI): AOI systems are used to visually inspect the solder joints and PCB traces. This is particularly important in the high-precision manufacturing of Bergquist PCBs, as it helps identify any defects that could cause failure under thermal stress.
4.X-Ray Inspection: For more complex assemblies, X-ray inspection is used to check the integrity of vias and solder joints, ensuring that there are no hidden issues beneath the surface of the PCB.
Achieving Consistency and Reliability-
JarnisTech ensures that each board goes through rigorous inspections to guarantee that the thermal integrity and electrical performance are up to par with industry standards. Whether it’s testing for thermal conductivity or checking the electrical integrity, every Bergquist PCB undergoes a multi-step inspection to make sure it’s up to the task.
Innovations in PCB Manufacturing
In addition to traditional manufacturing methods, jarnistech is at the forefront of incorporating automation and advanced machinery into the PCB manufacturing process. These innovations not only streamline production but also improve the consistency, efficiency, and thermal performance of the finished products.
Automation in PCB Manufacturing-
1.Automated Assembly Lines: Modern assembly lines have been fully automated, reducing the potential for human error and improving the speed at which Bergquist PCBs are produced. Automated pick-and-place machines, for example, ensure that components are accurately placed on the board, ready for soldering.
2.Robotic Arms for Soldering: Robotic arms equipped with precision soldering tips help ensure that the solder joints are uniformly applied, maintaining both electrical integrity and thermal conductivity.
3.Smart Monitoring Systems: Advanced monitoring systems track each step of the manufacturing process, from material preparation to final inspection. This allows for real-time adjustments, reducing defects and increasing overall product quality.
Thermal Solutions and Advanced Machinery-
The use of specialized machinery for thermal solutions is key to ensuring the high-performance of Bergquist PCBs. High-speed CNC machines are used for precision drilling, ensuring that thermal vias are placed in exactly the right positions to optimize heat dissipation. Additionally, laser etching technology is used to create fine, accurate traces on the PCB, further enhancing the board’s electrical and thermal properties.
Emerging Trends in PCB Manufacturing-
3D Printing: One exciting area of development in PCB manufacturing is the use of 3D printing to create complex, customized PCB designs. While this is still in its infancy, it holds great promise for applications that require highly specialized PCB layouts or integration with other components.
Flexible PCBs: Flexible Bergquist PCBs are becoming more popular for applications in wearables and medical devices. These flexible boards allow for a more compact and adaptable design, all while maintaining excellent thermal performance.
Assembly Techniques for Bergquist PCBs
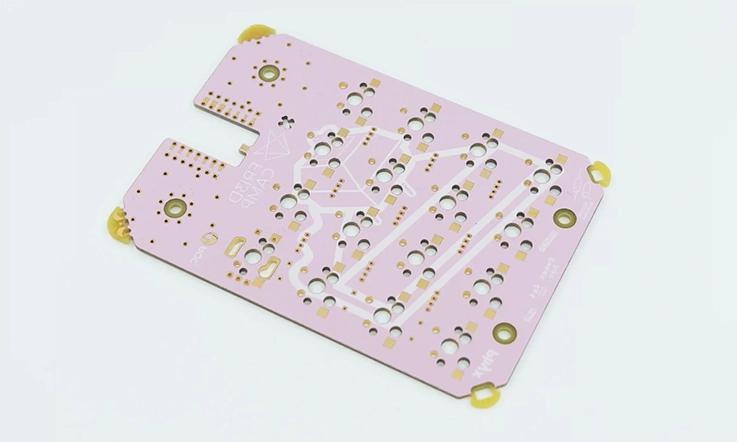
Best Practices for Component Placement
When assembling Bergquist PCBs, the precision of component placement directly impacts performance, especially when dealing with thermal management needs. The first rule of thumb in PCB assembly is to always align components in a way that promotes uniform heat distribution. The right orientation and positioning not only make a difference in how well thermal conductivity works, but also ensure that heat flows out smoothly, without causing any issues.
Best Practices:
1.Automated Pick-and-Place Machines: These machines play a crucial role in optimizing the component placement process, ensuring accuracy and minimizing the risk of human error.
2.Thermal Pad Positioning: Ensure that heat-sensitive components are placed in close proximity to Thermal Gap Pads or Heat Sinks to enhance heat dissipation.
3.Component Spacing: Avoid overcrowding; ensure there’s adequate space for heat dissipation and airflow, especially around high-power components.
4.Board Orientation: When designing layouts, components should be placed with an understanding of the thermal gradients they will experience.
Example: For instance, in LED lighting applications, placing heat-sensitive ICs away from high-power LEDs is crucial for extending their life and improving thermal management.
Lead-Free Soldering and Compatibility
With the increasing focus on sustainability, lead-free soldering has become a standard in PCB manufacturing, especially for applications like Bergquist PCBs, where thermal management and component integrity are non-negotiable. While lead-based solders were once the go-to material, lead-free solders such as SAC305 (tin-silver-copper alloy) are now widely used for their environmental benefits and excellent thermal performance.
Key Considerations:
1.Solder Paste Selection: Choose the right solder paste that works effectively with high-thermal conductivity substrates like Bergquist’s aluminum-based PCBs.
2.Soldering Process Control: Adjust the reflow soldering profile to accommodate lead-free alloys, ensuring that components do not overheat or experience thermal shock during assembly.
3.PCB Compatibility: Lead-free soldering requires adjustments in temperature and process timing. Bergquist materials, with their excellent thermal conductivity, offer an advantage here, as they can better manage the heat during the soldering process without compromising component quality.
Example: In automotive applications, using lead-free solder ensures that the PCBs meet both environmental standards and performance benchmarks, such as those set by RoHS (Restriction of Hazardous Substances).
Enhancing Durability During Assembly
Ensuring that Bergquist PCBs can withstand the mechanical and thermal stresses of daily use is a top priority during assembly. Durability is not just about heat dissipation; it’s also about building electrically robust PCBs that can handle the long-term rigors of the end-use environment, whether it’s for high-power electronics or LED lighting systems.
Best Practices for Durability:
1.Thermal Stress Relief: During the assembly, incorporate thermal vias and copper pours to help spread heat evenly across the PCB and reduce hotspots. This can dramatically improve the overall thermal stability of the product.
2.Protective Coatings: Applying a conformal coating can prevent damage from environmental factors such as moisture or chemicals, especially for applications in automotive or industrial machinery.
3.Reflow Soldering Precision: High temperatures during reflow soldering can result in warping or stress fractures on the PCB. Careful temperature ramping and cooling rates can prevent these issues.
Example: For high-watt density applications, such as telecommunications or server equipment, it’s essential to use materials that prevent cracking during expansion and contraction cycles, ensuring that the PCB retains its performance for longer periods.
Key Data Points Table for Assembly Techniques
Assembly Practice | Technique | Benefit | Application Example |
Component Placement | Use of pick-and-place machines for precision | Accurate, consistent placement of components | LED systems, high-power electronics |
Lead-Free Soldering | Adoption of lead-free solder (SAC305) | Environmentally friendly and durable solder | Automotive, power modules |
Thermal Stress Relief | Application of copper pours and thermal vias | Helps distribute heat evenly, reducing hotspots | High-watt-density applications |
Protective Coatings | Conformal coating to protect from moisture | Prevents damage in harsh environments | Industrial machinery, automotive |
Comparing Bergquist PCBs to Standard FR4 Boards
When it comes to PCB materials, not all options are created equal. If you’re looking to push the limits of performance and longevity, Bergquist PCBs will often come out on top when compared to the traditional FR4 boards. Let’s dig deeper into how Bergquist PCBs outclass FR4 in key areas, and how this translates into real-world applications.
Thermal Performance Advantages
One of the standout features of Bergquist PCBs is their superior thermal management. Traditional FR4 boards, while cost-effective, are not exactly built for high-thermal applications. In comparison, Bergquist PCBs—specifically those featuring Thermal Clad materials—are engineered with thermal conductivity in mind, which can make a world of difference when you’re dealing with power-hungry components.
●Thermal Resistance: Traditional FR4 boards often have a thermal conductivity in the range of 0.2 to 0.3 W/mK, which means they struggle to efficiently disperse heat. In contrast, Bergquist PCBs, especially those made with aluminum or copper substrates, boast significantly higher thermal conductivity (up to 1.0 W/mK or more). This means Bergquist PCBs can keep heat at bay, preventing overheating and thermal damage.
●Heat Management: Bergquist’s materials like Thermal Gap Pads and Hi-Flow offer tailored heat dissipation solutions, allowing for higher density designs and better heat distribution. This results in more stable performance and longer lifespan in high-power applications.
Material | Thermal Conductivity (W/mK) | Application Example |
Bergquist PCBs (Aluminum) | 1.0 – 9.0 | LED lighting, power electronics |
FR4 | 0.2 – 0.3 | Low-power systems, consumer electronics |
Durability in Harsh Environments
Another area where Bergquist PCBs outperform FR4 is in their durability. Bergquist boards are designed to withstand harsh environments, making them suitable for industries like automotive, industrial machinery, and telecom, where components are subjected to high temperatures, vibrations, and corrosive environments. FR4, while sufficient for consumer electronics, can struggle when exposed to extreme conditions.
●Mechanical Stress: Bergquist PCBs, thanks to their robust aluminum and copper substrates, can handle more mechanical stress than FR4. Whether it’s the shock of a bump, vibration, or even bending, Bergquist materials tend to maintain structural integrity much better.
●Thermal Stability: Bergquist’s Thermal Clad technology also ensures that the board won’t warp or degrade under heat, offering outstanding thermal stability. This makes Bergquist PCBs ideal for high-temperature environments like automotive engine compartments or military applications. On the other hand, FR4 has a lower glass transition temperature, making it prone to warping at high temperatures.
Material | Mechanical Stress Resistance | Thermal Stability | Application Example |
Bergquist PCBs (Aluminum/Copper) | High | High (up to 150°C) | Automotive, industrial |
FR4 | Moderate | Moderate (up to 130°C) | Consumer electronics, PCBs |
Cost Efficiency Over Time
While Bergquist PCBs might have a higher upfront cost compared to FR4 boards, when you factor in maintenance savings, downtime reduction, and long-term performance, they often prove to be the more cost-effective solution over the long run.
●Long-Lasting PCB: With superior heat dissipation and durability, Bergquist PCBs tend to have a longer lifespan than FR4 boards. Fewer failures and less frequent replacements mean that over time, Bergquist PCBs save you both money and hassle.
●Maintenance Savings: Bergquist PCBs also reduce the need for frequent maintenance and repairs. Since they can handle higher heat loads and extreme environments, components stay intact longer. On the other hand, FR4 boards might need repairs or replacements more frequently in high-demand environments.
Material | Upfront Cost | Lifespan | Maintenance Frequency | Application Example |
Bergquist PCBs | High | Long | Low | Telecom, automotive |
FR4 | Low | Short to Medium | High | Consumer electronics, computers |
Advanced Applications of Bergquist PCBs in Key Industries
The demand for high-performance electronic solutions has significantly increased in various industries, from LED lighting to automotive systems and high-power electronics. Bergquist PCBs have found an indispensable position in the market due to their outstanding thermal management capabilities and robust construction. Let’s dive into the diverse applications of Bergquist materials in these fields.
Enhancing LED Lighting Systems with Bergquist PCBs
LED lighting has truly transformed how we light up our spaces, offering energy-efficient alternatives that stand the test of time. But as LEDs get more powerful and brighter, managing heat becomes a bigger concern. That’s where Bergquist Thermal Clad PCBs come in, providing the perfect fix for LED lighting designs.
LEDs, especially in high-intensity applications, generate a significant amount of heat. Without proper heat dissipation, this can lead to performance degradation and reduced lifespan of the lighting units. Bergquist PCBs, with their superior thermal conductivity, help in quickly dissipating heat away from sensitive components. By using Bergquist materials like Thermal Clad and Gap Pads, LED lighting manufacturers can ensure longer-lasting, high-performance fixtures.
Key Benefits of Bergquist PCBs in LED Lighting Systems-
Feature | Benefit |
High Thermal Conductivity | Keeps LED components cool, ensuring optimal performance. |
Electrical Insulation | Protects against short circuits and ensures safety. |
Compact Design | Enables the creation of space-saving, efficient LED modules. |
Reliability | Reduces heat-related failure rates, extending the product lifespan. |
Application: Take commercial LED lighting systems used in large shopping malls or industrial settings. These systems require high-brightness LEDs and heat management to function without degradation. Bergquist PCBs, such as the HT-07006, are commonly used to maintain optimal operating temperatures, reducing maintenance costs and ensuring reliability.
Supporting High-Power Electronics with Bergquist PCBs
In the field of high-power electronics, the need for precise thermal control and durability has never been greater. Whether you’re designing power supplies, electric vehicles, or industrial equipment, Bergquist PCBs offer the thermal performance necessary to handle the demanding needs of high-power applications.
As power electronics often generate large amounts of heat, efficiency in heat transfer is essential. Bergquist materials like Bond-Ply, Sil-Pad, and Thermal Clad effectively manage thermal energy, preventing overheating and damage to sensitive components.
Applications in High-Power Electronics-
Application | Bergquist Material | Benefit |
Power Supplies | Bergquist Thermal Clad | Prevents heat buildup, maintains system efficiency. |
Electric Vehicle Powertrains | Bergquist Gap Pads | Ensures heat dissipation in compact spaces. |
Industrial Equipment | Bergquist Hi-Flow | Enhances performance in high-power density environments. |
Automotive Applications of Bergquist PCBs
The automotive industry has seen a substantial shift toward electric vehicles (EVs) and advanced driver-assistance systems (ADAS). These systems demand reliable electronic components that can withstand extreme environments, including fluctuating temperatures and vibrations. Bergquist PCBs meet these challenges with their high thermal conductivity, reliability, and rugged construction.
Bergquist PCBs are designed to handle components like inverters, battery management systems (BMS), and electronic control units (ECUs) with ease. These systems require proper heat dissipation to avoid overheating and ensure long-lasting performance. Bergquist PCB’s solutions work by efficiently directing heat away from sensitive parts, reducing the chance of system failures or malfunctions. In the world of electric vehicles, where performance and reliability are non-negotiable, Bergquist PCB’s thermal management is a smart solution for keeping these systems at their best, ensuring they stay reliable through tough conditions.
Bergquist PCB Applications in Automotive Systems-
Component | Bergquist Material | Benefit |
Inverters | Bergquist HT-04503 | Ensures efficient heat transfer for power conversion. |
Battery Management Systems (BMS) | Bergquist Bond-Ply | Offers thermal insulation and heat dissipation. |
Electronic Control Units (ECUs) | Bergquist Sil-Pad | Provides electrical insulation while transferring heat. |
Why Choose Us as Your Bergquist PCB Supplier?
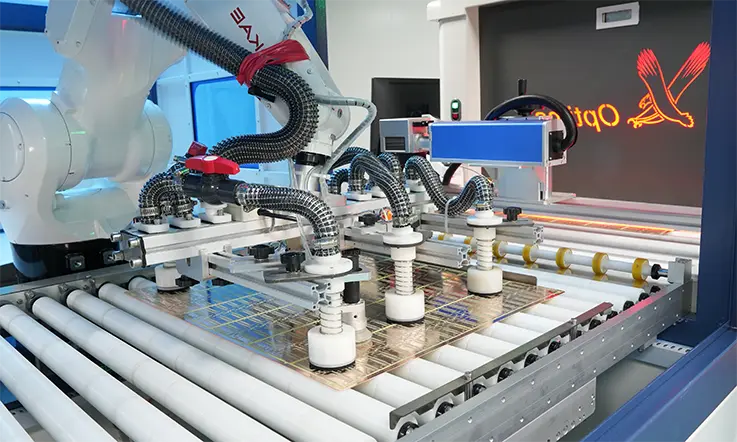
If you’re looking for a trusted partner in PCB manufacturing, look no further than JarnisTech. As a leading supplier of Bergquist PCB circuit boards, we have built a reputation for delivering premium quality PCBs with the highest standards of precision and performance. We pride ourselves on offering competitive rates, innovative solutions, and timely deliveries, making us your go-to source for all Bergquist PCB needs.
Key Benefits of Choosing JarnisTech as Your Bergquist PCB Supplier
Benefit | Description |
Advanced Automotive Technology | Incorporating automotive-grade technology ensures high performance in demanding applications. |
Cutting-Edge Manufacturing | Use of automation and advanced machinery ensures precision and quality across all products. |
On-Time Delivery | Commitment to meeting deadlines, ensuring you receive your Bergquist PCBs as per schedule without delays. |
Customer Support | 24/7 customer support to assist you with any inquiries, product selection, or troubleshooting. |
Competitive Pricing | Offering high-quality PCBs at competitive prices, ensuring you get value without sacrificing quality. |
Premium Quality | Bergquist PCBs meet the highest quality standards, designed to deliver superior performance even in harsh environments. |
Our Bergquist PCB Offerings:
To meet the demands of diverse industries, we offer a wide range of Bergquist PCB laminates, including:
Bergquist PCB Laminate | Application | Key Feature | Thermal Performance |
Bergquist HPL-0301 | High-performance applications | Superior thermal conductivity and stability | Excellent thermal resistance |
Bergquist HT-04503 | Power electronics, automotive | High heat load management | High thermal conductivity |
Bergquist MP-06503 | Multi-layer PCB, electronics | Multi-layer design, enhanced thermal dissipation | High thermal performance |
Bergquist HT-07006 | Automotive, industrial applications | Robust thermal management for harsh conditions | Outstanding thermal resistance |
Bergquist HPL-03015 | High-watt-density applications | Optimized for LED and power electronics | Excellent heat dissipation |
Bergquist HR T30.20 | High-temperature environments | High thermal resistance for extreme conditions | Superior heat resistance |
Why JarnisTech is Your Ideal Bergquist PCB Supplier?
With years of experience in the PCB industry, JarnisTech has developed a deep understanding of the Bergquist brand’s capabilities. We offer custom solutions, reliable support, and a commitment to high-quality standards that align with industry demands. Whether you’re working on a new project or need a reliable supplier for ongoing production, JarnisTech delivers the tools you need to succeed.
Ready to take your PCB project to the next level? Reach out to JarnisTech today and experience the difference we can make for your designs. We’re committed to helping you make smarter, more efficient, and cost-effective choices for your Bergquist PCB needs!
FAQ
What are Bergquist PCBs, and how do they differ from standard PCBs?
Bergquist PCBs are specialized thermal clad printed circuit boards designed for superior heat dissipation. Unlike standard PCBs, they integrate a metal core (typically aluminum or copper) for improved thermal conductivity, making them ideal for high-power and heat-sensitive applications.
What industries commonly use Bergquist PCBs?
Bergquist PCBs are widely utilized in automotive, LED lighting, power electronics, telecommunications, and industrial automation due to their efficient thermal management and durability in harsh environments.
What materials are used in Bergquist PCBs?
The primary materials include:
●Aluminum substrates for lightweight and cost-effective solutions.
●Copper substrates for higher thermal and electrical performance.
●Various thermal interface materials (TIMs) like Gap Pad, Sil-Pad, and Bond-Ply.
What are the thermal performance advantages of Bergquist PCBs?
Bergquist PCBs provide exceptional thermal resistance and conductivity, reducing heat buildup in components. This extends the lifespan of devices and ensures stable operation under high-power loads.
How do Bergquist PCBs improve durability in harsh environments?
With robust metal cores and high-quality insulating layers, Bergquist PCBs withstand thermal cycling, vibration, and mechanical stress. They are resistant to high temperatures and moisture, making them suitable for automotive and outdoor applications.
Can Bergquist PCBs be customized for specific applications?
Yes, they can be tailored with specific layouts, thermal interface materials, and substrate types to meet unique project requirements. Applications like high-watt-density LEDs or power modules often require custom designs.
What are the cost implications of using Bergquist PCBs?
While the initial cost may be higher compared to standard PCBs, their longevity, reduced cooling requirements, and enhanced performance often result in long-term cost savings, especially in power-intensive applications.
Our special materials
PCB Fabrication
Bergquist PCB Laminates & Materials