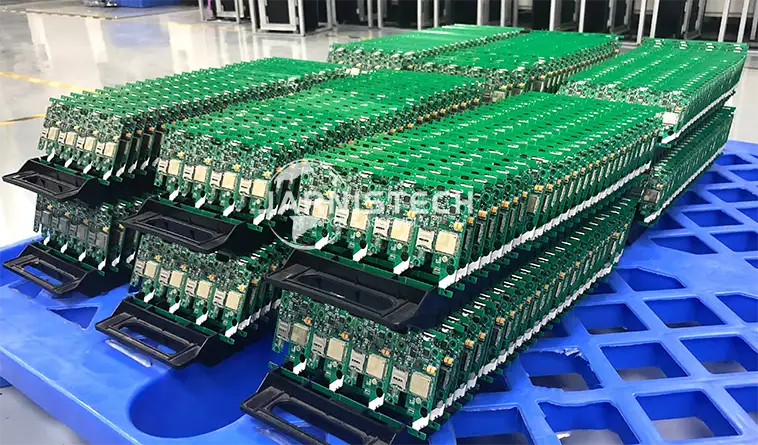
High volume PCB assembly represents a significant portion of the electronics manufacturing sector. As technology advances, the demand for efficient production processes continues to grow. Companies need to ensure they can scale their operations while maintaining quality and cost-effectiveness. With customer demands shifting quickly, mastering the complexities of high-volume production becomes a strategic advantage, helping businesses secure their market position.
When it comes to PCB assembly, your volume requirements can significantly impact pricing. At JarnisTech, we’re all about delivering top-notch high-volume PCB assembly solutions without busting your budget. If you’re gearing up for a mass production run, teaming up with an experienced provider-Jarnistech,we can handle the demands of large-scale production is the way to go—especially for projects involving 10,000 pieces or more.
At JarnisTech, our infrastructure is built to churn out bulk-volume printed circuit boards that hit the mark every time. And let me tell you, while some folks might think that cranking out massive quantities means cutting corners, that’s a big fat no! Every single PCB goes through a rigorous testing process, ensuring you get nothing but the best.
Introduction to High Volume PCB Assembly
In the dynamic landscape of electronics manufacturing, high volume PCB assembly is the real deal. This method zeroes in on producing substantial quantities of printed circuit boards (PCBs) with pinpoint accuracy and efficiency. Think of it as a finely tuned machine designed to crank out products, enabling manufacturers to jump right in and tackle increasing demand without burning a hole in their budgets.
What Constitutes High Volume PCB Assembly?
High volume PCB assembly typically means churning out thousands, sometimes millions, of units. By harnessing the power of automation, manufacturers streamline their operations, leading to faster production cycles and cost-effective outcomes. This approach minimizes manual labor, cutting down on time and reducing the chances of human error—an absolute must when you’re trying to keep your product quality in check.
Example: Consider a company that designs consumer electronics, such as smartphones. With the ability to produce 100,000 PCBs a week through automated assembly lines, they can meet market demand swiftly and efficiently, ensuring they’re not left in the dust while competitors race ahead.
Significance in Electronics Manufacturing
As electronic devices become staples in our daily lives, the demand for high volume assembly has never been more pronounced. This method serves as a critical driver not just for the consumer electronics market but also for sectors like automotive, aerospace, and medical technology. In these industries, where safety and reliability are non-negotiable, manufacturers need a robust assembly process that can deliver without missing a beat.
Industries Benefiting from High Volume PCB Assembly
Industry | Application Example | Benefits |
Automotive | Engine control units | Enhanced reliability |
Aerospace | Avionics systems | Compliance with safety standards |
Medical | Diagnostic equipment | Consistent performance |
Consumer Electronics | Smartphones | Rapid product iterations |
Key Benefits of Adopting High Volume Production
1.Cost Efficiency: Mass production allows manufacturers to cut costs per unit significantly. By purchasing components in bulk and optimizing production workflows, it’s like finding a sweet deal at your local warehouse store—more savings and less hassle!
2.Consistent Quality: With automated processes taking the reins, the variability that can come with manual labor is drastically reduced. This means you can expect your products to look sharp and function flawlessly every single time.
3.Scalability: When demand shoots through the roof, manufacturers shift gears and ramp up production smoothly, avoiding any unnecessary hiccups. This flexibility gives businesses the upper hand, allowing them to handle sudden order surges and adapt to market shifts without skipping a beat. Being able to respond fast means meeting deadlines head-on, keeping customers satisfied, and staying on top of operational targets.
Want to dive into the world of high volume PCB assembly and see how it can elevate your manufacturing game? Don’t wait—contact us today to learn more about our services and how we can help streamline your production processes!
Differentiating Between Low and High Volume PCB Assembly
Knowing the ropes between low and high volume assembly can save you a heap of trouble down the line. Understanding the differences between these two approaches is key to making informed decisions in your manufacturing process.
Cost Analysis: High Volume vs. Low Volume
High Volume Assembly: Generally costs less per unit due to economies of scale. This approach allows manufacturers to purchase components in bulk, driving down the cost per unit. It’s like finding a deal on a big pack of toilet paper—less cash out of pocket for more product!
Example: Let’s say you’re producing a run of 100,000 PCBs for a consumer electronics device. The bulk pricing for components can reduce costs significantly compared to ordering just 1,000 units, where the setup and customization costs take a bigger bite out of your budget.
Low Volume Assembly: On the flip side, low volume assembly usually hits you with higher costs per unit. This is due to the necessary setups and customizations that can rack up expenses, making it less appealing for large-scale projects.
Cost Comparison of High vs. Low Volume PCB Assembly
Assembly Type | Cost per Unit (Estimated) | Setup Costs | Ideal Quantity |
High Volume | $0.10 – $0.50 | $5,000 – $10,000 | 10,000+ units |
Low Volume | $1.00 – $5.00 | $2,000 – $5,000 | 100 – 1,000 units |
Lead Times: Quick Turnaround Solutions
When it comes to lead times, high volume PCB assembly often means quicker turnaround solutions, which is crucial in a market that moves at lightning speed. With smart supply chain management and automated processes, manufacturers can respond to customer needs faster than a New York minute. This agility not only helps businesses meet tight deadlines but also enhances customer satisfaction.
Example: Picture a tech company launching a new product just in time for the holiday season. By relying on high volume assembly, they can quickly scale up production and ensure that shelves are stocked when demand peaks.
Design Considerations for High Volume Production
When designing PCBs for high volume assembly, keep these pointers in your back pocket to streamline the process:
Standardization: Use common components across different product lines to simplify sourcing and assembly. This approach reduces lead times and the complexity of your inventory management. Think of it as cleaning out your toolbox—keeping similar tools together makes for a smoother project!
Design for Manufacturability (DFM): Ensure your designs are straightforward and easy to produce. Complicated designs can lead to costly errors and extended production times. Remember, the simpler, the better—don’t complicate things unnecessarily!
Prototyping: Before diving headfirst into full production, prototype your designs to iron out any kinks. This allows you to test and refine your PCB before committing to high volume runs, saving you time and money in the long run.
Essential Components of High Volume PCB Assembly
Utilizing Surface Mount Technology (SMT)
Benefits of SMT for Large Scale Production
Surface Mount Technology (SMT) allows you to place components directly on the surface of the PCB, which opens up a whole new world of design possibilities. This technique not only paves the way for more compact designs but also enhances efficiency. By minimizing the size of the components, manufacturers can fit more functionality into a smaller footprint, which is a huge win for high volume production.
Benefit | Description |
Space Efficiency | Components take up less space, allowing for compact PCB designs. |
Faster Assembly | Automated processes speed up assembly, saving time and costs. |
Higher Component Density | Enables more features on a single board, increasing functionality. |
Quality Assurance Measures for SMT Processes
To keep your SMT assembly processes on point, you need robust testing methods to catch any defects before they snowball into bigger issues. Automated Optical Inspection (AOI) provides precise, real-time assessments by scanning components for misalignments, missing parts, and solder joint issues. Meanwhile, X-ray inspection digs deeper, spotting hidden defects like voids and cold solder joints that might slip past visual checks.
Inspection Method | Purpose |
Automated Optical Inspection (AOI) | Uses cameras and algorithms to detect defects early. |
X-ray Inspection | Provides insights into hidden solder joints and through-hole components. |
Automated Optical Inspection (AOI): This technique uses cameras and advanced algorithms to inspect PCBs for defects, ensuring components are correctly placed and soldered. It’s a smart move to catch mistakes early—think of it as a double-check before a big presentation!
X-ray Inspection: For hidden solder joints and through-hole components, X-ray inspection provides a clear view of what’s going on beneath the surface. It’s like having X-ray vision for your PCBs—no stone goes unturned!
Through-Hole Technology and Its Applications
When to Choose for Through-Hole Assembly?
While SMT is all the rage, sometimes you gotta go old school! Through-hole assembly is perfect for components that need a little extra muscle, like connectors and hefty capacitors. These parts are more robust and provide better durability for certain applications.
Component Type | Application |
Connectors | Require strong physical connections. |
Large Capacitors | Need secure mounting due to size. |
Example: When it comes to heavy-duty applications like automotive PCBs, durability is non-negotiable. These boards endure extreme conditions, such as constant vibration, heat fluctuations, and mechanical stress, making component reliability a top priority. That’s where through-hole technology (THT) steps in—it delivers the ruggedness needed to handle these challenges. Unlike surface-mount components, through-hole parts anchor securely to the board with leads passing through drilled holes, offering enhanced mechanical strength.
Inspection Protocols for Enhanced Reliability
Rock-solid inspection protocols are non-negotiable for ensuring the reliability of through-hole assemblies. Implementing robust testing methods, including functional testing and environmental testing, ensures that your products can stand the test of time.
Testing Type | Description |
Functional Testing | Checks PCB operation under real conditions. |
Environmental Testing | Tests performance in extreme conditions. |
Functional Testing: This involves checking the completed PCB for correct operation in real-world conditions. It’s like giving your product a dry run before it hits the market!
Environmental Testing: This is all about putting your PCBs through their paces in extreme conditions—think heat, humidity, and vibration. Ensuring your product performs under pressure is key to building trust with your customers.
Comprehensive Manufacturing Processes
Turnkey Solutions in PCB Assembly
Turnkey solutions are like one-stop shopping for your PCB needs! These comprehensive services provide everything from design to assembly and testing, making life a whole lot easier for manufacturers.
Turnkey Solution Component | Benefits |
Design Services | Streamlined collaboration from start to finish. |
Assembly Services | Efficient assembly processes reduce lead times. |
Testing Services | Comprehensive testing ensures quality assurance. |
Example: A tech startup looking to launch a new gadget can partner with a turnkey provider to handle the entire PCB assembly process. This not only saves time but also allows them to focus on what they do best—innovating!
Strategic Component Sourcing
Building solid relationships with reliable suppliers can make all the difference in your manufacturing process. A dependable supply chain can prevent hiccups and ensure you have the quality components you need when you need them.
Tip: Regularly assess your suppliers and maintain open lines of communication. It’s all about teamwork!
Implementing Quality Control in High Volume PCB Assembly
The Critical Role of Quality Assurance
Quality assurance isn’t just a formality—it’s the backbone that keeps high-volume PCB assembly on track. A bulletproof quality management system (QMS) ensures every phase of the process, from design to final assembly, is locked in with accuracy. Think of it as the thread that pulls everything together, making sure every board that rolls off the line is as precise as the last.
Quality Management System (QMS) Overview
QMS Component | Description |
Documentation Control | Keep detailed records of all processes. |
Training Programs | Regularly train staff on quality standards. |
Continuous Improvement | Implement feedback loops to refine processes. |
Example: Regular audits of the QMS can help identify bottlenecks and inefficiencies, allowing you to streamline operations. It’s like tuning up your car; a little maintenance goes a long way!
Advanced Testing and Inspection Techniques
In high-volume assembly, utilizing advanced testing methods is a must for identifying defects at the earliest stages. Techniques such as In-Circuit Testing (ICT) and functional testing empower manufacturers to catch problems before products make their way to store shelves. These proactive approaches not only enhance product reliability but also minimize the risk of costly recalls down the line.
Testing Method | Purpose | Benefits |
In-Circuit Testing (ICT) | Tests components in the circuit for faults. | Detects defects quickly, minimizing waste. |
Functional Testing | Checks if the PCB operates as intended. | Ensures the product meets specifications. |
In-Circuit Testing (ICT): This method involves testing each component in its operational environment. Think of it as giving your PCB a full body scan to ensure everything’s functioning properly.
Functional Testing: Here, the entire assembly is tested in real-world scenarios. It’s like taking your product out for a test drive—gotta make sure it runs like a dream before it’s released!
Compliance with RoHS and Industry Standards
Staying compliant with RoHS (Restriction of Hazardous Substances) is non-negotiable. This ensures your PCBs are eco-friendly and safe, which isn’t just a good practice; it’s good business. Compliance can enhance your brand reputation and open up new market opportunities.
Compliance Aspect | Description |
RoHS Compliance | Limits hazardous substances in electronics. |
Industry Standards | Adheres to best practices in manufacturing. |
RoHS Compliance: Your PCBs will be free from harmful substances like lead and mercury, ensuring they’re safer for consumers and gentler on the planet. This commitment to environmental responsibility not only protects public health but also enhances your brand’s reputation.
Industry Standards: Aligning your processes with established standards (like IPC-A-610 for acceptability of electronic assemblies) ensures that your products are market-ready and meet customer expectations.
Ready to take your quality control to the next level? Partner with us today to optimize your high volume PCB assembly process, ensuring top-notch quality every step of the way. Don’t let defects derail your production—let’s work together for a brighter, error-free future!
Strategies for Cost Optimization in High Volume PCB Assembly
Advantages of Mass Production on Costs
Mass production is a powerhouse for savings. Think of it this way: just like snagging a bulk deal at Costco, high volume PCB assembly allows manufacturers to reduce costs per unit by purchasing components in larger quantities. This approach isn’t just a nice-to-have; it’s a game plan for enhancing profit margins.
Cost Savings Breakdown
Cost Factor | Description | Impact on Overall Costs |
Bulk Purchasing | Buying components in larger quantities. | Lowers the cost per unit dramatically. |
Reduced Labor Costs | Automation minimizes manual labor needs. | Cuts labor costs significantly. |
Economies of Scale | Spreading fixed costs over a larger number of units. | Further reduces average costs. |
Example: If you buy resistors in bulk, you might cut costs from $0.05 per piece to $0.02, which can lead to substantial savings across thousands of units. It’s like switching from name-brand to store-brand—same quality, lower price!
Streamlining Supply Chain Operations
To keep your supply chain lean and mean, adopting Just-in-Time (JIT) inventory systems can work wonders. JIT minimizes the amount of stock held, reducing waste and freeing up cash flow faster than you can say “savings.”
JIT Inventory System Overview
JIT Component | Description | Benefits |
Reduced Inventory Levels | Only stock what’s needed for immediate production. | Decreases storage costs and waste. |
Improved Supplier Relations | Build close ties with suppliers for timely deliveries. | Ensures a steady flow of components. |
Responsive Production | Adjust production schedules based on real-time demand. | Enhances flexibility and responsiveness. |
Example: Implementing JIT means you’re not holding onto excess materials that could become obsolete. It’s like cleaning out your closet—less clutter and more space for what matters!
Long-term Cost Implications and Analysis
Conducting a thorough cost-benefit analysis is key to understanding the long-term implications of high volume assembly. Knowledge is power, my friends! This analysis should consider not just the immediate costs but also future savings and potential market changes.
Cost-Benefit Analysis Framework
Analysis Aspect | Considerations | Outcomes |
Initial Setup Costs | Evaluate the costs of new equipment and automation. | Identify necessary investments. |
Long-term Savings | Analyze projected savings from mass production. | Calculate ROI over time. |
Market Trends | Assess potential fluctuations in demand. | Adjust strategies to mitigate risks. |
Example: If you project a consistent demand increase, investing in automated assembly now can yield significant savings down the line, keeping your operations agile and cost-effective.
Challenges in High Volume PCB Assembly
Managing Production Line Efficiency
Keeping production lines operating at peak efficiency isn’t just about flipping a switch. It requires constant monitoring, fine-tuning, and sometimes a complete overhaul. Implementing Lean principles can significantly aid in identifying waste and optimizing workflows. Lean focuses on eliminating non-value-adding activities, which can enhance overall efficiency and reduce costs.
Lean Principles Breakdown
Lean Principle | Description | Benefits |
Value Stream Mapping | Analyze the flow of materials and information. | Identifies bottlenecks and inefficiencies. |
5S Methodology | Sort, Set in order, Shine, Standardize, Sustain. | Creates a clean and organized workspace. |
Kaizen (Continuous Improvement) | Encourage small, incremental changes. | Promotes a culture of ongoing efficiency. |
Example: By implementing value stream mapping, a PCB manufacturer identified a bottleneck in the soldering process. By reallocating resources and rearranging the workflow, they reduced production time by 20%. That’s like finding cash in your couch cushions!
Addressing Material Shortages and Supply Chain Disruptions
Material shortages and supply chain disruptions can throw a wrench in your assembly operations. To tackle these challenges, developing a diverse supplier base and maintaining safety stock is key. This not only buffers against sudden shortages but also keeps production flowing.
Supply Chain Management Strategies
Strategy | Description | Advantages |
Diversified Supplier Base | Partner with multiple suppliers for critical components. | Reduces dependency on a single source. |
Safety Stock | Keep a reserve of materials to handle unexpected demand spikes. | Prevents production delays. |
Supplier Relationship Management | Foster strong relationships with suppliers for better communication. | Enhances responsiveness to issues. |
Example: A manufacturer faced delays due to a sudden shortage of capacitors. By having multiple suppliers lined up, they were able to switch sources quickly, keeping their production on track. It’s like having a backup plan for your vacation—always a smart move!
Balancing Quality with Speed
Striking the right balance between maintaining quality and meeting production speed is a perennial challenge in high volume PCB assembly. To address this, adopting a culture of continuous improvement can help create an environment where quality doesn’t take a backseat to speed.
Quality vs. Speed Strategies
Strategy | Description | Outcome |
Standard Operating Procedures (SOPs) | Establish clear guidelines for production. | Ensures consistent quality across batches. |
Cross-Training Employees | Train workers in multiple areas of the production line. | Increases flexibility and reduces downtime. |
Regular Quality Audits | Conduct frequent checks to assess quality. | Identifies issues before they escalate. |
Example: A company implementing SOPs noticed a drop in defects by 15% over three months. By ensuring that everyone was on the same page, they not only sped up production but also improved quality. Talk about a win-win!
Best Practices for High Volume PCB Assembly
Lean Manufacturing Principles in PCB Assembly
Embracing Lean manufacturing principles is a game plan to streamline operations and eliminate waste. The focus here is on working smarter, not harder! Lean principles can help you identify inefficiencies, optimize workflows, and create a more responsive manufacturing environment.
Key Lean Principles to Implement
Lean Principle | Description | Benefits |
Value Stream Mapping | Analyze each step in your production process. | Helps pinpoint waste and bottlenecks. |
Just-In-Time (JIT) | Produce only what is needed, when it is needed. | Reduces inventory costs and waste. |
Kaizen | Foster a culture of continuous, incremental improvement. | Keeps the team engaged and proactive. |
Example: A PCB manufacturer using value stream mapping discovered that excess motion during component retrieval was slowing down the assembly line. By reorganizing the workspace layout, they cut assembly time by 15%. It’s like getting a bonus without lifting a finger!
Employee Training and Skill Development
Investing in your workforce is a no-brainer. Ongoing training ensures that your team remains sharp, adaptable, and prepared to tackle new challenges. A well-trained workforce can adapt to new technologies and processes, leading to increased productivity and efficiency.
Training Strategies
Training Method | Description | Outcome |
Hands-On Workshops | Practical sessions focusing on specific skills. | Enhances technical expertise. |
Cross-Training | Train employees in multiple roles within production. | Increases flexibility in the workforce. |
Online Learning Platforms | Utilize e-learning for continuous education. | Allows for self-paced skill development. |
Example: A company that implemented a cross-training program noticed a 25% reduction in downtime when employees were able to fill in for each other during peak production times. Talk about teamwork making the dream work!
Continuous Improvement Methodologies
Adopting methodologies like Six Sigma can drive continuous improvement efforts in high volume PCB assembly. These methodologies focus on data-driven decision-making, leading to enhanced processes and reduced defects. Because when you stop improving, you start declining.
Six Sigma Framework
Six Sigma Concept | Description | Benefits |
Define | Identify the problem and project goals. | Sets a clear direction for improvement. |
Measure | Collect data to understand current performance. | Establishes a baseline for future comparison. |
Analyze | Identify root causes of defects. | Helps target specific areas for improvement. |
Improve | Develop solutions to eliminate defects. | Enhances overall quality and efficiency. |
Control | Implement controls to sustain improvements. | Ensures that gains are maintained over time. |
Example: A manufacturer utilizing Six Sigma methods achieved a reduction in defects from 5% to less than 1% in just six months. That’s the kind of turnaround that keeps customers coming back!
Selecting the Right High Volume PCB Assembly Partner
Key Qualities to Look For in an Assembly Partner
When searching for a PCB assembly partner, keep an eye out for key attributes that can make or break your project. Look for experience, certifications, and solid customer feedback. A dependable partner is worth their weight in gold!
Essential Qualities to Consider
Quality | Description | Why It Matters |
Experience | A partner with years in the game understands the nuances of the industry. | Their expertise can save you time and money. |
Certifications | Look for ISO, IPC, and other relevant certifications. | Certifications reflect adherence to industry standards. |
Customer Feedback | Positive reviews and case studies can provide insights into reliability and performance. | Happy clients usually mean quality service! |
Example: A manufacturer partnered with a company that had a strong track record and ISO certifications. This relationship resulted in a 30% reduction in assembly errors and improved delivery times. When you find a solid partner, you reap the rewards!
Evaluating Manufacturing Capabilities and Technologies
Do your homework on potential partners’ manufacturing capabilities and technologies. Look for modern equipment and skilled personnel—they’re your ticket to success!
Criteria for Evaluation
Capability | Description | Benefits |
Equipment | Ensure they have state-of-the-art machinery for both SMT and through-hole assembly. | Modern equipment boosts efficiency and precision. |
Technology Integration | Evaluate their use of advanced technologies like automation and robotics. | These technologies can streamline processes and reduce costs. |
Skilled Workforce | Check if they invest in employee training and development. | A knowledgeable team can troubleshoot issues swiftly. |
Example: A company that switched to a partner with automated assembly equipment saw their production speed increase by 40%. Investing in the right technology pays off!
Importance of Communication and Collaboration
Good communication is the glue that holds successful projects together. Establish clear lines of dialogue to keep everyone on the same page and foster collaboration throughout the project.
Strategies for Effective Communication
Strategy | Description | Outcome |
Regular Updates | Schedule weekly check-ins to discuss progress and challenges. | Keeps all stakeholders aligned and informed. |
Open Feedback Loops | Encourage team members to share insights and concerns. | Fosters a culture of transparency and improvement. |
Collaboration Tools | Use tools like Slack or Trello for real-time communication. | Enhances efficiency and reduces misunderstandings. |
Example: A project team that used collaborative tools managed to cut down on misunderstandings, leading to a 20% improvement in project timelines. When everyone’s on the same page, things flow!
Why Choose Us?
Our High-Volume PCB Assembly Capabilities
With over 20 years of experience under the hood, we know the twists and turns of electronics manufacturing and EMS inside and out. Over time, we’ve added fresh talent and cutting-edge tech to our production floor, so we can tackle massive orders without skipping a beat. Got a job that needs thousands of PCBAs in one go? We’re ready to deliver. Here’s the lowdown on our high-volume assembly capabilities that have kept our customers coming back.
High-Volume PCB Assembly Features
Feature | Details |
Mixed Technology | We offer hybrid boards with both SMT and THT components. This combo is perfect for clients looking for compact design without sacrificing durability. |
Versatile PCB Types | We support rigid, flexible, rigid-flex, and Rogers PCBs—ideal for industries like aerospace, automotive, telecom, and more. |
Lead-Free and Leaded Soldering | Both hand soldering and automated soldering are available, giving us the flexibility to meet environmental standards while handling large batches efficiently. |
Comprehensive Testing | We run SPI, AOI, X-ray inspections, ICT, and functional tests to catch flaws before your product hits the market. |
Laser-Cut Stencils | Our stainless steel SMT stencils guarantee precision soldering—no smudges, no shorts. |
Shipping Partnerships | Partnering with top-tier shipping companies ensures that your boards arrive when you need them. No delays, no excuses. |
Consigned & Turnkey Options | Whether you want us to source everything (turnkey) or you supply components (consigned), we’ve got you covered. |
Custom Turnaround Times | Tight on time? We can speed up production and match your go-to-market schedule. |
Testing That Leaves No Stone Unturned
●In-Circuit Testing (ICT): Catch electrical faults early.
●Functional Testing: Verify that each board works as it should.
●Solder Paste Inspection (SPI): Ensure flawless solder paste application.
●Automated Optical Inspection (AOI): Quick scans for surface defects.
●X-Ray Inspection: Identify hidden issues in complex packages like BGAs.
From NPI to Mass Production—We’ve Got Your Back
We’ve mastered the New Product Introduction (NPI) process, ensuring your products flow smoothly from prototypes to full-scale production. From the first RFQ to final delivery, we integrate DFM and DFT principles, helping you cut costs and save time without compromising quality.
Here’s how we helped an automotive client:
●Challenge: Assemble 10,000 rigid-flex PCBs for vehicle modules with tight environmental constraints.
●Solution: Our engineers identified unnecessary design elements during NPI and recommended alternatives.
●Outcome: We slashed production time by 15% and saved the client thousands in costs.
PCB Package Capabilities
Package Type | Minimum Size |
QFN, QFP, LGA, BGA | 0.2mm |
Passive Components | 0201 imperial (0603 metric) |
Our precision work ensures even the tiniest packages fit like a glove on your boards, delivering high reliability for demanding applications.
Wrapping Up: Selecting an Expert PCB Assembly Partner
In the bustling market of high-volume PCB assembly, selecting the right manufacturing partner can make or break your project. As we’ve noted, certain qualities stand out when evaluating potential partners: cutting-edge technology, a knowledgeable workforce, and solid quality assurance practices all contribute to a partner’s trustworthiness. Effective communication and the right manufacturing capabilities are key ingredients in ensuring your project runs smoothly.
Don’t gamble with the success of your PCB assembly. Grab the reins and connect with potential partners who match your project needs. Whether you’re gearing up for large-scale production or seeking all-in-one turnkey solutions, a solid partnership is where everything comes together. Reach out today to discover how our expertise in high-volume PCB assembly can drive your projects forward and boost your business in the competitive electronics landscape.
Connect with us today to explore how our expertise in high-volume PCB assembly can propel your projects forward and elevate your business in the competitive electronics market. Let’s make things happen together!
Frequently Asked Questions (FAQ)
What is High Volume PCB Assembly?
High volume PCB assembly refers to the mass production of printed circuit boards, emphasizing efficiency and cost-effectiveness.
How does High Volume PCB Assembly differ from Low Volume Assembly?
High volume assembly typically involves larger production runs, lower costs per unit, and faster turnaround times compared to low volume assembly.
What are the cost implications of High Volume PCB Assembly?
High volume assembly can lead to significant cost savings due to economies of scale, though initial setup costs may be higher.
What quality control measures are essential in High Volume PCB Assembly?
Common practices include rigorous testing protocols, automated inspections, and adherence to industry standards.
How can automation impact High Volume PCB Assembly?
Automation enhances efficiency, reduces labor costs, and minimizes human error, making it a valuable investment for high volume production.
What are the latest trends in High Volume PCB Assembly?
Current trends include advancements in AI, automation, and sustainable manufacturing practices.
How to choose a reliable High Volume PCB Assembly partner?
Evaluate potential partners based on their experience, capabilities, and communication practices to ensure a successful collaboration.
Advanced PCB Assembly
PCBs We Can Assemble
- Min size: PCB whose width/length is less than 30mm should be panelized.
- Max size: single board 500mm*400mm | panel board 310mm*410mm.
- Layer Count: 1-60 layers (1-20 layers for mass production).
- Copper Thickness: 1/2oz – 17oz.
- PCB Types: Rigid PCBs, Flex PCBs, Rigid Flex PCBs, Rogers PCBs, Ceramic PCBs, etc.
- Surface Finishes: Lead/Lead-free HASL, ENIG, ImSilver, OSP, Gold plated, Immersion Gold, etc.
Components We Can Assemble
- SMT sizes: 01005, 0201 or larger.
- BGA pitch: 0.35mm or greater.
- BGA Ball count: 2 – 50.
- Fine pitch: 0.4mm or greater.
- WLCSP pitch: 0.35mm or greater.
- Components Height: 0.1mm – 12mm.
- BGA, micro-BGA, POP, CSP, LGA package, Flip chip, Hard metric connectors, Cable & wire, etc.
- Min. Components Spacing: 0.20mm for SMT parts, no specific demand for Thru-hole parts.
Custom PCB Assembly Capabilities
- Quick Turn.
- IPC III standard compliant.
- Prototype Quantities to Production Quantities.
- Single PCB Assembly and PCB Panel Assembly.
- Single and Double-sided PCB Assembly.
- Leaded Assembly, Lead-free or RoHS Compliant Assembly and No-clean Process Assembly.
- SMT Assembly, Thru-hole (DIP) Assembly, and Combo of SMT and Thru-hole Assembly.
- Consigned PCB Assembly, Partial consigned PCB Assembly and Full turnkey PCB Assembly.