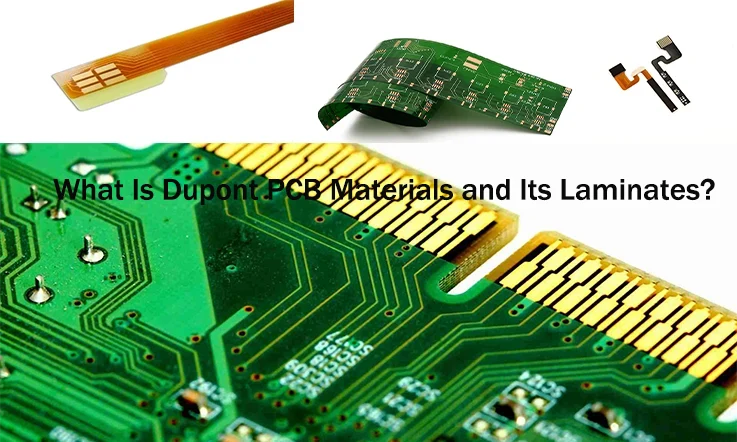
DuPont’s PCB materials offer a unique combination of reliability, efficiency, and versatility that’s hard to beat. From medical technologies requiring precise and flexible circuits to industrial electronics demanding high thermal performance, DuPont materials are designed to meet the rigorous demands of modern electronics. If you’re working in any of these fields, diving deep into the specific properties and advantages of DuPont’s materials will help you make the most of their offerings and stay ahead of the curve in today’s competitive market.
This guide delves deep into the various Dupont PCB materials, their diverse applications, and best practices for selecting, designing, and manufacturing with these high-performance laminates.
Why Choose Dupont PCB for Your Electronics Projects?
When selecting materials for electronic circuit boards (PCBs), Dupont offers unparalleled quality, versatility, and reliability. Whether you’re working on flexible electronics, high-frequency systems, or high-performance computing, Dupont’s PCB laminates deliver consistent results across industries. Here’s why Dupont should be your go-to choice for your next electronics project.
High-Quality Laminates for Reliable Performance
Dupont’s PCB materials are designed with one goal in mind: ensuring long-term, consistent performance in a range of demanding applications. From signal integrity in high-speed data transmission to the mechanical resilience required in flexible designs, Dupont’s laminates meet the toughest industry standards.
1.Signal Integrity in High-Speed Electronics: Dupont’s Teflon-based laminates are a prime example of materials that preserve signal quality in high-frequency applications, such as 5G communications, satellite systems, and wireless technology. These materials help ensure data transmission stays clear, even over long distances, preventing signal loss that could disrupt crucial operations.
2.Flexibility Meets Durability: In the world of wearables, medical devices, and automotive tech, flexible PCBs are a must-have. Dupont’s Pyralux AP and Pyralux LF materials deliver the right mix of flexibility and durability, able to keep up with constant movement while maintaining solid electrical performance. For instance, wearable ECG monitors rely on these flexible circuits to stay on track, delivering accurate readings as users go about their daily activities without missing a beat.
3.Thermal Management: Dupont’s high-performance laminates are designed to manage heat efficiently. In industries like electric vehicles and power electronics, thermal management is key to preventing overheating and prolonging the lifespan of devices. Dupont’s materials, including thermally conductive substrates, effectively dissipate heat, allowing systems to function efficiently without damaging sensitive components.
Below is a table summarizing the different performance aspects of Dupont PCB materials:
Feature | Description | Example Applications |
Signal Integrity | Maintains high signal quality, even at high frequencies | 5G communication, satellite systems |
Mechanical Resilience | Withstands stress and bending without breaking | Wearable electronics, automotive sensors |
Thermal Management | Effectively dissipates heat, preventing overheating | Power electronics, electric vehicles |
Pro Tip: When selecting materials for power electronics or automotive applications, look for PCBs that offer superior heat resistance. Dupont’s Pyralux series not only ensures mechanical flexibility but also excels in managing high temperatures, reducing the risk of failure.
Industry-Wide Applications of Dupont Materials
Dupont’s materials aren’t just suited for one or two applications—they span a wide array of industries, providing tailored solutions for virtually any electronic design.
1.Medical Electronics: For mission-critical devices like pacemakers, hearing aids, and infusion pumps, Dupont flexible and rigid-flex PCBs offer the durability and biocompatibility necessary for safe operation within the human body. Pyralux AP materials are commonly used in these devices for their ability to withstand continuous mechanical stress while remaining reliable.
2.Consumer Electronics: With the drive for smaller, more efficient products, consumer electronics manufacturers turn to Dupont PCBs to achieve high-density interconnects (HDI). For example, smartphones and gaming consoles require compact PCBs that provide high-speed data transfer, and Dupont’s Teflon laminates ensure that signal integrity is maintained at a smaller scale.
3.Automotive and Aerospace: In the automotive sector, Dupont’s rigid-flex PCBs are everywhere – from navigation systems to on-board diagnostics and infotainment setups. These durable, high-performance materials stand up to the rigors of automotive environments, ensuring everything functions smoothly. Over in aerospace, Dupont’s Pyralux materials show up in high-stakes systems like LiDAR sensors and flight control electronics, providing the reliability needed to perform in extreme conditions. Whether it’s cruising down the highway or flying at 30,000 feet, Dupont’s materials keep everything running like clockwork.
Here’s a quick look at where Dupont’s materials shine in various industries:
Industry | Applications | Benefits of Dupont PCB Materials |
Medical Electronics | Pacemakers, hearing aids, medical sensors | Flexible designs, reliable performance |
Consumer Electronics | Smartphones, wearables, gaming consoles | High-density interconnects (HDI) |
Automotive & Aerospace | Navigation systems, LiDAR, flight control electronics | Flexibility, durability, heat resistance |
Environmental Sustainability with Dupont Laminates
With increasing environmental concerns, sustainability has become a major consideration in PCB manufacturing. Dupont’s commitment to producing eco-friendly PCB materials demonstrates how companies can balance performance with environmental responsibility.
1.Green Manufacturing Practices: Dupont’s manufacturing processes emphasize environmental sustainability, offering RoHS-compliant materials that meet stringent environmental standards. These materials are created without harmful chemicals, making them a solid choice for industries like medical electronics, where safety is a top consideration. By using Dupont’s environmentally friendly materials, manufacturers can meet global regulatory requirements while ensuring reliable product performance, all while maintaining high-quality standards.
2.Recyclability of Materials: Dupont’s materials are not only designed for performance but also for sustainability. Many of their PCBs are manufactured with recyclability in mind, making it easier for companies to dispose of and recycle them at the end of their lifecycle. This helps reduce electronic waste and aligns with global initiatives to promote a circular economy.
3.Longer Product Lifespan: Dupont PCB materials are engineered to last longer, meaning fewer replacements and less waste. In applications such as automotive electronics and high-performance computing, Dupont’s durability helps ensure that products don’t need to be replaced as frequently, which ultimately cuts down on the carbon footprint of manufacturing processes.
The following table summarizes Dupont’s efforts in sustainability:
Sustainability Aspect | Description | Impact |
RoHS Compliance | Materials meet the Restriction of Hazardous Substances directive | Reduces harmful chemicals in PCBs |
Recyclability | Materials are designed for easy recycling | Reduces electronic waste |
Durability | Long-lasting materials reduce the need for frequent replacements | Helps in the reduction of manufacturing waste |
Exploring Dupont PCB Design Innovations
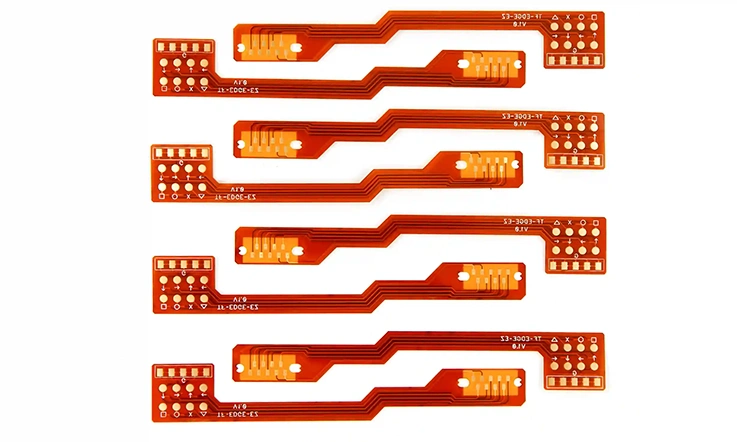
In modern electronics, precision and reliability are at the forefront of innovation. Dupont PCB materials offer unmatched flexibility, signal management, and structural integrity, ensuring optimal performance for complex applications across industries. Let’s delve into the details of flexible PCB design, advancements in signal integrity, and the capabilities of rigid-flex designs.
Flexible PCB Design Using Pyralux Laminates
Flexibility is a key trend in PCB design today. From wearables to medical sensors and even foldable smartphones, flexible PCBs are in high demand. Dupont’s Pyralux laminates are specifically engineered for these types of applications, offering the required bendability, low profile, and excellent thermal performance.
Material Strengths-
●Durability: Pyralux laminates maintain structural integrity even under repetitive bending, twisting, and folding, enabling use in dynamic environments.
●Thermal Efficiency: High thermal conductivity supports performance in temperature-sensitive applications.
●Lightweight Design: Reduces product weight, a critical factor in portable devices.
Design Optimization-
●Bend Radius Management: Proper bend radius ensures long-term reliability, particularly in compact devices like hearing aids or fitness trackers.
●Layer Construction: Engineers can create multi-layer structures to integrate additional functionalities in limited spaces.
Applications and Benefits-
Sector | Example Application | Material Advantage |
Wearables | Fitness trackers | High flexibility and low weight |
Automotive | In-cabin displays | Heat resistance and vibration damping |
Medical Devices | Patient monitoring systems | Biocompatibility and precision |
When designing with flexible PCBs, engineers need to consider factors such as material thickness, bend radius, and the layer structure. Dupont’s Pyralux series allows for the creation of circuits that are both lightweight and durable—perfect for the next generation of electronics. Whether you’re working on a compact medical device or an automotive display, Dupont’s flexible materials can handle the job.
Enhancing Signal Integrity in High-Speed Designs
In the world of high-speed electronics, signal integrity is non-negotiable. Dupont materials such as Teflon-based laminates are specifically designed to maintain signal clarity over long distances or through complex layer structures. Whether you’re working with RF applications, 5G devices, or automotive communication systems, selecting the right material makes all the difference. Dupont’s low-loss laminates help you hit your performance targets without giving up power efficiency. With Dupont, you can rest assured that your designs will deliver top-notch performance, keeping your systems operating at peak efficiency.
Performance Features-
●Low Dielectric Constant (Dk): Ensures minimal signal delay and phase distortion.
●Minimal Signal Loss: Maintains data clarity even in multi-layer configurations or over extended distances.
●Thermal Reliability: Supports thermal stability in power-dense environments.
Design Challenges Addressed-
●Impedance Control: Facilitates precise control over transmission line characteristics, ensuring design predictability.
●Crosstalk Minimization: Dupont materials help to reduce noise and minimize interference, especially when dealing with high-density circuit boards.
●Material Scalability: Ideal for complex designs, including HDI and RF modules.
Use Cases-
Application | Material | Specific Benefit |
5G Base Stations | Teflon Laminates | Maintains low loss at high frequencies |
Satellite Systems | Low-Loss Substrates | Improves signal clarity in RF environments |
Automotive Communication | Multi-Layer PCB Materials | Enhanced signal-to-noise ratio |
Engineer’s Note: For high-speed and high-frequency designs, Dupont’s low-loss materials simplify signal management and minimize design iterations, translating to faster time-to-market.
With Dupont PCBs, impedance matching is straightforward, and crosstalk and signal degradation are minimized, making them ideal for HDI boards, high-speed data transmission, and high-frequency systems.
Rigid-Flex PCB Design for Complex Applications
Designing rigid-flex PCBs using Dupont’s laminates opens up possibilities for compact electronics in industries like aerospace and medical devices. These PCBs combine the best of both worlds: the rigidity of traditional PCBs with the flexibility required for intricate designs. Dupont’s Pyralux and Teflon-based materials offer the strength and flexibility necessary to build these high-performance circuits.
Advantages of Rigid-Flex Designs-
●Compact Form Factor: Combines flexible and rigid layers to reduce space requirements.
●Connector Elimination: Enhances signal reliability by removing interconnect points.
●Environmental Resilience: Performs well under mechanical stress, extreme temperatures, and exposure to chemicals.
Key Applications-
●Aerospace: Flight navigation systems utilizing rigid-flex boards reduce connector-related failures while withstanding high vibration environments.
●Medical: Devices like endoscopes or surgical instruments benefit from reduced weight and enhanced flexibility.
●Automotive: Infotainment systems and advanced driver-assistance systems (ADAS) thrive on rigid-flex boards for compact design and reliability.
Industry | Product Application | Material Advantage |
Aerospace | Control Panels | Vibration resistance and compact design |
Medical Devices | Imaging Equipment | Flexible design for precision |
Consumer Electronics | Foldable Smartphones | Seamless integration of rigid-flex layers |
In industries like aerospace, where reliability is non-negotiable, rigid-flex PCBs made with Dupont materials are a common choice. They are also used in applications that require flexible circuit boards that can withstand harsh environments without compromising electrical performance.
What PCB Laminate Options Do Dupont Materials Provide?
Dupont has long been recognized for its innovative laminate solutions tailored to meet the diverse demands of industries such as telecommunications, automotive, aerospace, and medical devices. Their materials are specifically designed to address challenges like high temperatures, signal clarity, and power management. Let’s dive into their offerings and understand how they bring value to various applications.
Pyralux AP for High-Temperature and Flexible Applications
Pyralux AP is a standout material in the Dupont PCB portfolio. With its excellent thermal stability and flexibility, it is perfect for applications requiring high-temperature resistance. Automotive electronics, medical devices, and aerospace circuits all benefit from the durability and reliability of Pyralux AP.
Material Attributes-
●Temperature Tolerance: Operates efficiently in environments exceeding 200°C, making it ideal for high-power circuits and systems exposed to heat.
●Durability in Flex Applications: Maintains mechanical integrity even with repeated bending or flexing.
●Chemical Resistance: Withstands exposure to harsh chemicals, making it a preferred choice for medical or industrial environments.
Applications-
●Wearable Technology: Used in fitness trackers, smartwatches, and flexible sensors due to its lightweight nature.
●Aerospace Systems: Suitable for components exposed to thermal and mechanical stress.
●Advanced Medical Devices: Ideal for compact, intricate devices like hearing aids or surgical tools.
Industry | Example Use Case | Key Feature |
Consumer Electronics | Smart Bands | Flexibility and reliability |
Medical Technology | Catheter-based diagnostic tools | Sterile and durable |
Automotive | Flexible display backplanes | Heat-resistant flexibility |
This material can be used in both flexible and rigid-flex designs, making it a versatile option for various industries. Whether you need to withstand extreme temperatures or operate under continuous mechanical stress, Pyralux AP provides an excellent solution for your PCB needs.
High-Frequency Laminates for RF and 5G
Dupont’s high-frequency laminates are designed to minimize signal degradation, ensuring your signals stay sharp and clear. These materials are perfect for applications like RF circuits, 5G technology, and satellite communication systems, where accuracy and top-tier performance are a must. With Dupont’s advanced laminates, you can count on superior signal transmission, even in the most demanding environments.
Material Attributes-
●Low Dielectric Constant (Dk): Ensures minimal signal delay for high-frequency circuits.
●Low Dissipation Factor (Df): Reduces energy loss, keeping signals intact over long distances.
●Smooth Copper Foil: Enhances signal integrity, a critical aspect for RF applications.
Applications-
●Telecommunication Networks: Backbone for 5G base stations and IoT devices.
●Radar Systems: For automotive and aerospace radar technologies, Dupont’s materials are a go-to solution.
●High-Speed Data Processing: Found in data servers requiring precise and high-speed signal management.
Application | Material Type | Performance Highlight |
5G Infrastructure | Low-Loss Laminates | Clear signal transmission |
Aerospace Radar | High-Frequency Laminates | Reliable frequency handling |
IoT Devices | RF Substrates | Reduced interference |
Engineer’s Note: Signal fidelity is a make-or-break factor in high-frequency designs. Dupont laminates minimize interference, letting your innovations speak volumes.
For designers and engineers working with high-frequency signals, Dupont’s materials offer low dielectric constants and low loss tangents that enhance performance, reduce heat generation, and optimize the overall signal quality.
Thermally Robust Laminates for Power Applications
In power electronics, thermal management is a significant concern. Dupont offers materials that can withstand high temperatures while maintaining excellent electrical properties. Power modules, LED lighting systems, and automotive circuits all benefit from Dupont’s thermally robust laminates. These materials help dissipate heat efficiently, ensuring long-term performance in applications that generate significant heat during operation.
Material Attributes-
●Thermal Management: High conductivity materials dissipate heat effectively, protecting sensitive components.
●Electrical Stability: Consistent dielectric properties ensure optimal electrical performance even under temperature fluctuations.
●Structural Reliability: Maintains form and function in high-power, high-stress environments.
Applications-
●Electric Vehicles (EVs): Battery management systems and inverters benefit from these materials.
●Renewable Energy Systems: Solar inverters and wind turbines use these laminates for thermal control.
●Industrial Automation: Drives and control systems in factories leverage the heat-resistant properties.
Sector | Use Case | Feature Highlight |
Electric Vehicles | Inverter Boards | High thermal conductivity |
Renewable Energy | Solar Panel Controllers | Temperature resilience |
Factory Automation | High-Power Drives | Structural and thermal stability |
Designing for heat-intensive applications? Don’t skimp on materials that can make or break your device’s longevity. Explore Dupont’s thermally robust laminates for results you can trust.
Considering Factors for Choosing Dupont PCB Materials
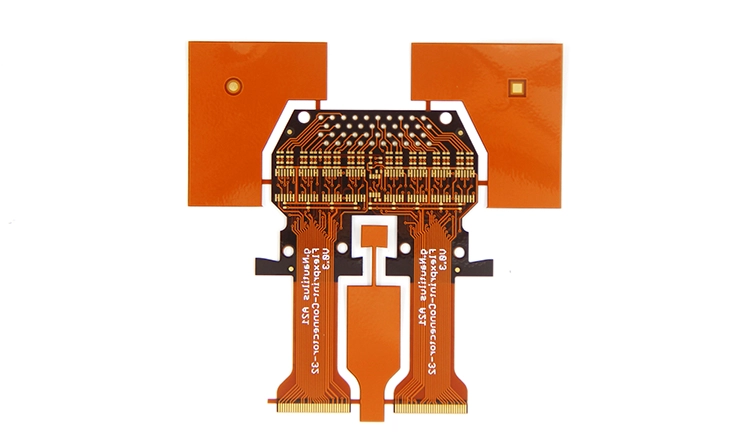
Choosing the right materials for PCB projects is an essential step in achieving the desired performance, durability, and compliance. Dupont offers a range of specialized materials tailored for diverse industries, making it crucial to align the material’s features with project requirements. This section provides insights into how to evaluate materials effectively, ensuring both performance and cost-efficiency.
Matching Materials to Application Needs
Selecting the right Dupont PCB material is a crucial decision that depends on the specific needs of the application. Flexible circuits, rigid-flex PCBs, and high-frequency applications all have distinct requirements that can be best met with Dupont’s specialized materials.
1.Flexible PCB Design: If your project involves wearables, automotive displays, or smart sensors, Dupont’s Pyralux flexible laminates offer outstanding mechanical performance while maintaining flexibility. For designs where space is a constraint, such as medical implants or compact consumer electronics, Pyralux AP provides the ideal balance of strength and flexibility, ensuring reliable performance even under stress.
2.High-Frequency Applications: For industries relying on high-speed communication, such as 5G networks, satellite communication, and RF devices, Dupont’s high-frequency laminates (e.g., Teflon-based materials) provide the best signal integrity with minimal loss. These materials reduce signal attenuation and crosstalk, ensuring optimal transmission quality for demanding RF applications.
3.Power Electronics: In power-intensive industries like electric vehicles (EVs) or power supplies, Dupont’s thermally robust materials are critical for managing the heat dissipation required for long-term reliability. Thermally conductive materials from Dupont effectively disperse heat generated in power electronics, enabling efficient operation and improved lifespan.
Cost vs. Performance
When picking Dupont PCB materials, striking the right balance between cost and performance is key. For less demanding projects, Dupont has budget-friendly options that still deliver solid electrical performance and durability. But when you’re dealing with high-stakes applications, like medical electronics or aerospace systems, upgrading to high-performance materials like Pyralux AP or Teflon-based laminates might be worth the extra investment. These materials provide the extra edge you need to ensure top-tier performance, even if they come with a higher price tag.
Therefore, finding the sweet spot between cost and performance is all about understanding your project’s priorities. While some materials provide high-end features, others offer reliable functionality without breaking the bank.
●Tailored Choices: For simple consumer electronics, Dupont’s standard laminates provide durability at a lower cost. For mission-specific designs—such as aerospace instruments—investing in top-tier materials like Pyralux AP ensures peace of mind.
●Long-Term Benefits: While premium laminates may seem pricier upfront, their ability to reduce maintenance and enhance product longevity often outweighs the cost over time.
Example: A startup producing IoT devices opted for mid-tier Dupont laminates, which provided just the right mix of affordability and performance to meet their tight budget constraints without compromising quality.
Keep in mind that the upfront cost of materials might be outweighed by long-term benefits such as reduced failure rates, improved device longevity, and increased overall system performance.
Environmental and Compliance Considerations
Environmental sustainability is more than just a buzzword—it’s a real-world necessity in today’s global market. Dupont’s PCB materials meet various global standards, including RoHS (Restriction of Hazardous Substances), UL certifications, and ISO compliance, making them the go-to choice for manufacturers seeking to adhere to environmental regulations.
●RoHS Compliance: All Dupont laminates avoid hazardous substances, aligning with global eco-regulations.
●UL94 Flame Resistance: These materials provide safety assurances in high-temperature environments.
●ISO Certifications: Demonstrating adherence to international quality and safety benchmarks.
Example Compliance Matrix:
Standard | Material | Industry Applications |
RoHS | Pyralux AP | Consumer electronics, medical devices |
UL94 V-0 | Thermally Robust Laminates | Aerospace, automotive systems |
ISO 9001 | Teflon-based Laminates | Telecommunications, industrial machinery |
These materials also help meet the growing demand for eco-friendly products in industries such as consumer electronics, automotive, and medical equipment. By selecting Dupont materials that comply with these standards, we can confidently offer PCB plates that are both high-performing and environmentally responsible.
Differences Between DuPont PCB Materials and Other High-Performance PCB
High-performance PCB laminates, such as those from Rogers, Shengyi, Taconic, and others, are designed to meet the unique needs of industries like telecommunications, aerospace, and consumer electronics. While DuPont materials offer many advantages, understanding how they differ from other top-tier options is crucial for selecting the right material for your application. Below, we provide an in-depth comparison:
Key Comparison Areas
Criteria | DuPont | Competitors |
Flexible Laminates | Pyralux Series | Limited flexibility options (e.g., Shengyi lacks dedicated flexible laminates) |
High-Frequency | Teflon-Based Laminates | Rogers RO3000, RO4000, Taconic TLY offer competitive dielectric properties |
Thermal Conductivity | Pyralux HT, Teflon Series | Panasonic R-5515, Bergquist Thermal Clad lead in thermal management |
Cost Efficiency | Higher upfront cost | More budget-friendly options (ITEQ, Shengyi, Nanya) |
Sustainability | RoHS-compliant, Green Focus | Compliance varies across manufacturers |
1. Flexible PCB Laminates
●DuPont: Offers Pyralux laminates, designed specifically for flexible and rigid-flex PCBs. These materials are suitable for compact devices requiring durability and heat resistance, such as wearables and automotive displays.
●Competitors: While options like Shengyi and ITEQ provide high-quality laminates, their focus leans more towards rigid PCBs, lacking the advanced flexibility of Pyralux materials.
2. High-Frequency Applications
●DuPont: Teflon-based laminates excel in high-frequency applications, with low dielectric loss and minimal signal degradation. These features make them ideal for 5G networks, RF devices, and satellite communications.
●Rogers and Taconic: Rogers’ RO3000 and RO4000 and Taconic’s TLY Series are industry leaders for RF and microwave PCBs, offering excellent signal integrity with ultra-low dissipation factors. However, they may not provide the same heat tolerance as DuPont’s solutions.
Material | Dielectric Constant (Dk) | Dissipation Factor (Df) |
DuPont Teflon | 2.1 – 2.5 | ~0.001 |
Rogers RO3000 | 3.0 – 3.2 | ~0.002 |
Taconic TLY Series | 2.2 – 2.4 | ~0.002 |
3. Thermal Management
●DuPont: Pyralux HT and Teflon materials provide effective thermal conductivity, ideal for high-power applications like electric vehicles (EVs) and industrial equipment.
●Panasonic and Bergquist: Lead the market in thermal management with materials like Thermal Clad, offering superior heat dissipation for applications like LED lighting. While DuPont excels in durability, Bergquist is preferred for extremely high-heat scenarios.
4. Cost Efficiency
●DuPont: Positioned as a premium solution. While upfront costs are higher, the long-term reliability reduces maintenance expenses, particularly in critical systems like medical or aerospace applications.
●Competitors: Budget-friendly alternatives like Nanya and ITEQ cater to less demanding industries but may require more frequent replacement.
5. Sustainability and Certifications
●DuPont: Complies with global standards, including RoHS, UL certifications, and ISO 14001, with an emphasis on eco-friendly production.
●Competitors: Compliance levels vary; while leaders like Isola and Rogers match DuPont’s certifications, smaller manufacturers may fall short in sustainability initiatives.
Key Takeaways:
●For flexible and high-density designs, DuPont materials offer unparalleled advantages with their Pyralux series.
●For high-frequency applications, Rogers and Taconic remain strong contenders, offering competitive alternatives to DuPont Teflon laminates.
●In thermal management, Bergquist and Panasonic may outperform DuPont for specific high-heat scenarios.
●If cost is a concern, materials like Shengyi or Nanya might suffice, but with potential trade-offs in durability and performance.
What are the Challenges of Manufacturing DuPont PCB Circuit Boards?
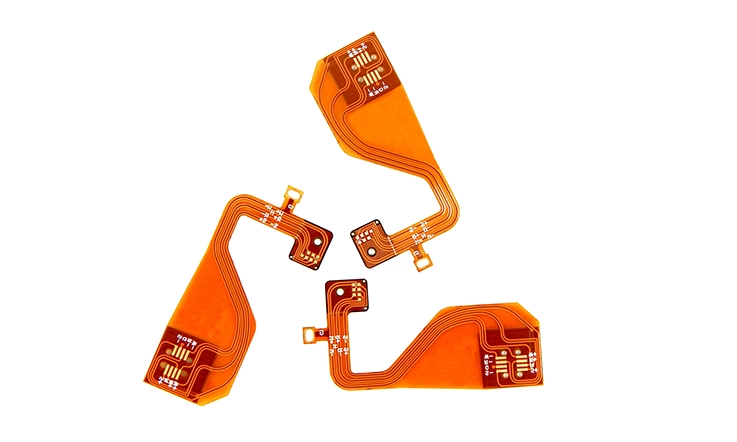
Manufacturing DuPont PCB circuit boards presents a number of challenges that require careful planning, specialized equipment, and expertise in both material science and manufacturing processes. Here are some of the key challenges:
1. Material Handling and Processing
Dupont’s high-performance laminates, such as Pyralux and Teflon-based materials, are sensitive and require careful handling. These materials are designed to meet specific performance standards but can be more challenging to process compared to traditional PCB materials. For example, Teflon-based laminates require precise control of temperature and pressure during lamination to avoid warping or delamination.
●Challenge: Achieving consistent processing quality while handling expensive and delicate materials can increase manufacturing costs and time.
2. Design Complexity for High-Density Circuits
High-performance PCBs using Dupont materials often involve complex multilayer designs or rigid-flex configurations, demanding careful attention to the layer stack, impedance control, and signal integrity. Dupont’s materials allow for high-density interconnections (HDI), but these designs require highly skilled engineers to ensure the integrity of the circuits.
●Challenge: The increased complexity of high-density designs means more intricate routing, vias, and pad configurations, requiring advanced design software and meticulous design validation.
3. Thermal Management
Thermal performance is a significant consideration when working with Dupont PCBs, especially for applications like power electronics, EVs, and medical devices. Dupont offers thermally robust materials, but the dissipation of heat in high-power circuits must be managed carefully.
●Challenge: Designers must balance electrical properties and thermal conductivity, requiring careful material selection and potentially the use of specialized heat dissipation techniques to prevent overheating or degradation of components.
4. Material Consistency and Quality Control
Maintaining consistency in Dupont laminates is a must. If there’s any variation in the material properties, it can throw off production and lead to poor yield or even total product failure. Dupont materials do come with specific tolerances, but even small discrepancies during manufacturing or procurement can create serious headaches down the line, impacting the final PCB quality. It’s all about making sure every batch hits the mark, so you don’t end up wasting time, effort, or resources.
●Challenge: Stringent quality control processes are required at every stage of production, from material sourcing to the final assembly, to maintain the performance characteristics that Dupont materials promise.
5. Advanced Fabrication Equipment and Expertise
Dupont’s PCB materials require precision fabrication techniques, such as laser drilling, microvia technology, and advanced lamination processes. Not all PCB manufacturers have access to the high-end equipment needed to work with these materials, and specialized expertise is often required to handle them.
●Challenge: Acquiring and maintaining the necessary fabrication equipment, as well as training staff in advanced techniques, adds both cost and complexity to the production process.
How Dupont Ensures Quality Assurance in PCB Production?
Dupont’s approach to quality assurance in PCB manufacturing is a meticulous blend of rigorous testing, advanced engineering practices, and strict adherence to global standards. These processes ensure their materials consistently meet the high demands of modern electronics.
Testing for Electrical and Mechanical Properties
Dupont’s PCB materials undergo exhaustive evaluations to confirm they deliver consistent performance under varied conditions. These tests include:
1.Electrical Conductivity and Dielectric Performance: To verify signal integrity and minimize loss, Dupont conducts tests using advanced impedance analyzers and TDR (Time-Domain Reflectometry) equipment. This ensures compatibility with high-speed and RF applications, such as 5G networks and IoT devices.
2.Mechanical Strength and Flexibility: For materials like Pyralux, several tests are carried out, such as tensile strength, elongation, and flex cycles. These tests are especially relevant for applications like wearables or medical implants, where the material needs to be tough and durable but also flexible enough to adapt to continuous motion. It’s all about finding that sweet spot where durability and flexibility meet, ensuring the material can withstand real-world conditions without compromising on performance.
Property | Testing Method | Material | Use Case |
Electrical Conductivity | Four-Point Probe | Teflon Laminates | High-speed RF circuits |
Flexibility | Mandrel Bend Test | Pyralux Flexible PCB | Wearables and automotive |
Dielectric Performance | TDR Analysis | High-Frequency PCBs | 5G infrastructure |
Thermal and Environmental Durability
Dupont materials are engineered to endure harsh environments and extended operational cycles. The rigorous testing includes:
●Thermal Resistance: Materials are subjected to Thermal Shock Tests and Temperature Cycling from extreme cold to high heat, ensuring reliability in environments like aerospace or automotive electronics.
●Moisture Resistance: Dupont conducts Humidity Testing, exposing laminates to prolonged moisture and high temperatures. For example, Teflon-based laminates demonstrate minimal water absorption, making them suitable for marine or humid environments.
●Chemical Resistance: Testing against solvents and corrosive substances ensures the materials retain structural integrity and performance in industrial and medical settings.
Meeting IPC and ISO Standards
Adherence to global standards underscores Dupont’s commitment to quality. They ensure compliance with:
●IPC Standards: Dupont materials align with IPC-6012 (rigid PCBs), IPC-4101 (base materials), and IPC-6013 (flexible PCBs) requirements. This guarantees interoperability and quality in multi-vendor environments.
●ISO Certification: Manufacturing facilities operate under ISO 9001 for quality management and ISO 14001 for environmental practices. These certifications reassure manufacturers of consistent quality and sustainable processes.
Standard | Description | Example Compliance |
IPC-6012 | Rigid PCB Qualification | Pyralux Laminates |
IPC-6013 | Flexible PCB Specification | Pyralux AP Series |
ISO 14001 | Environmental Management Standards | Sustainable Production Lines |
Why It Matters?
Dupont’s commitment to exhaustive quality assurance means their materials are trusted for demanding applications, from space exploration to medical innovations. If you’re designing a system where reliability isn’t optional, Dupont provides the peace of mind that only top-tier quality assurance can deliver.
Why Choose JarnisTech for Dupont PCB Manufacturing?
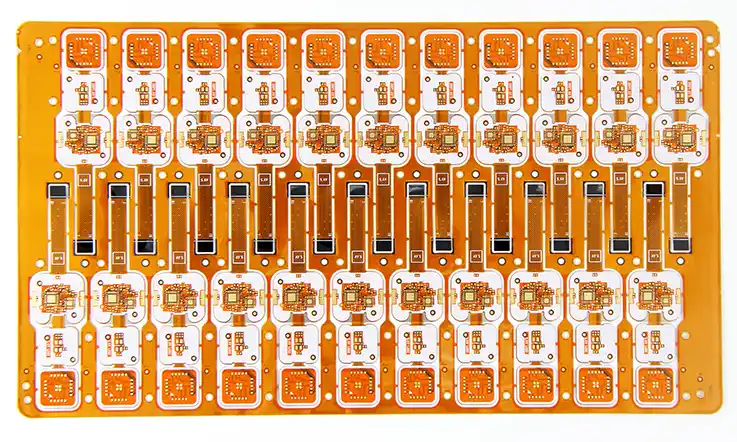
At JarnisTech, we’ve mastered the art of manufacturing Dupont PCB circuit boards tailored to meet diverse industry needs. Whether you’re designing flexible circuits for wearable tech or multilayer PCBs for automotive systems, we ensure seamless execution with top-notch materials and unmatched expertise.
1.Comprehensive Dupont Laminates Portfolio
JarnisTech offers an extensive range of Dupont laminates, including single-sided, double-sided, multilayer flex, and rigid-flex options. Each laminate is crafted with precision to meet the highest engineering standards, ensuring exceptional mechanical stability, reduced thermal expansion, and superior performance under demanding conditions. For instance:
●Pyralux Flexible Laminates: Perfect for compact designs like medical devices or wearables.
●High-Frequency Laminates: Engineered for RF and 5G communication systems.
●Thermally Robust Options: Ideal for power applications, such as electric vehicles.
2.Unrivaled Expertise Backed by Two Decades
With over 20 years in the PCB manufacturing industry, our specialized knowledge sets us apart. Our materials ensure superior signal integrity and durability, making them a trusted backbone for high-density designs across rigid and flexible substrates. A recent collaboration with a leading IoT company showcased how our Pyralux solutions optimized signal integrity in a multi-circuit, compact wearable device, exceeding client expectations.
3.Tailored Support from Design to Delivery
Your vision is our mission. Our Design Team and experienced Layout Engineers collaborate closely with you, analyzing your schematics and design drawings to recommend the best materials and configurations. Whether you’re working on prototypes or high-volume production, we’ll ensure your designs integrate seamlessly into real-world applications.
Key Services Include:
●Material matching for specific performance requirements.
●Detailed design consultations to optimize layouts.
●Fast prototyping and on-time delivery to meet critical project timelines.
Service | Benefit |
Layout Optimization | Reduced failure rates and improved signal flow. |
Material Consultation | Tailored solutions for thermal and mechanical needs. |
Efficient Delivery | Timely production cycles to keep your projects on track. |
4.Streamlined Prototyping and Manufacturing
Efficiency drives everything we do. By leveraging advanced rendering and quoting systems, we simplify prototyping without sacrificing precision. For example, our recent partnership with a medical device firm resulted in a 15% reduction in production lead times, thanks to our agile prototyping processes.
Your Go-To Manufacturing Partner
Choosing JarnisTech means embracing reliability, quality, and expertise under one roof. From small-scale custom designs to large-scale industrial production, we’re here to make your Dupont PCB projects a resounding success.
FAQ
What are Dupont PCB laminates typically used for?
Dupont laminates, such as Pyralux and Teflon-based materials, are widely used in applications like flexible circuits for wearables, high-frequency RF devices, 5G systems, and power electronics. Their specialized properties support designs requiring flexibility, high-speed signal integrity, or thermal management.
What makes Dupont Pyralux unique compared to other flexible PCB materials?
Pyralux laminates offer exceptional flexibility, low-profile designs, and reliable performance under mechanical and thermal stress. They are particularly valued for their ability to integrate seamlessly into compact devices like medical implants and foldable electronics.
How do Dupont materials improve signal integrity in high-frequency applications?
Dupont’s high-frequency laminates, often made with Teflon-based compositions, minimize signal loss, reduce crosstalk, and ensure consistent impedance. This makes them ideal for 5G infrastructure, satellite communications, and other RF-based systems.
Are Dupont PCB materials compliant with international standards?
Yes, Dupont laminates comply with RoHS (Restriction of Hazardous Substances), UL, and ISO standards, making them suitable for environmentally sustainable and globally accepted manufacturing processes.
What industries most commonly use Dupont PCBs?
Dupont materials are prominent in industries like aerospace, automotive, telecommunications, medical devices, and consumer electronics, particularly for their ability to meet stringent reliability and performance demands.
How do Dupont’s thermally robust laminates handle high-power applications?
These materials are designed to manage heat dissipation effectively, enhancing the longevity and efficiency of power electronics in sectors such as EVs, renewable energy systems, and industrial power supplies.
What is the difference between Dupont Pyralux and Teflon-based laminates?
●Pyralux: Primarily used for flexible and rigid-flex applications, offering mechanical durability and adaptability.
●Teflon-based: Engineered for high-frequency systems, prioritizing low dielectric loss and consistent signal transmission.
Can Dupont materials be used for multilayer PCB designs?
Absolutely. Dupont’s laminates support multilayer designs, including rigid-flex configurations. They enable high-density interconnects (HDIs) and complex layer stacks, ensuring durability and precision for advanced electronic systems.
Our special materials
PCB Fabrication
Dupont PCB Laminates & Materials