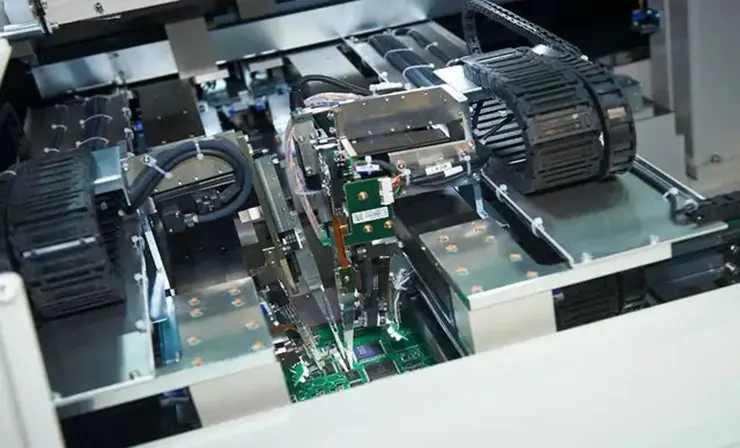
Military PCBs (Printed Circuit Boards) represent the backbone of countless defense systems. Their design and manufacturing demand not only technical expertise but also a deep understanding of the unique challenges presented by military applications. In this guide, we’ll dive deep into the intricacies of military PCB design, military PCB manufacturing, and military PCB assembly, sharing insights to help you navigate the complex landscape of military electronics.
Military PCB Design Requirements and Critical Considerations
Adhering to MIL-PRF Standards for Military PCB Design
When it comes to military electronics, following specific standards isn’t just a checkbox on a to-do list—it’s the name of the game. MIL-PRF-55110 and MIL-PRF-31032 are two guidelines that define the performance and reliability benchmarks for military PCBs. These standards detail rigorous criteria for everything from material selection to environmental performance, ensuring our professional team in uniform have the dependable technology they need to perform their duties.
Adhering to these standards means choosing materials that can stand up to extreme temperatures, shock, and humidity. Military equipment often finds itself in rugged environments, from the sweltering heat of deserts to the bone-chilling cold of arctic tundras. For instance, using high-performance FR4 materials is common for PCBs in many military applications, but when it comes to extreme conditions, polyimide might take the cake due to its superior thermal stability.
Table 1: Material Comparison for Military PCBs
Material | Temperature Range | Benefits | Use Case Examples |
FR4 | -40°C to +130°C | Cost-effective, good electrical properties | General-purpose military electronics |
Polyimide | -60°C to +200°C | Excellent thermal stability | Spacecraft, high-performance applications |
Ceramic | -55°C to +125°C | High-frequency performance | Radar systems, communication devices |
Layout Strategies for High-Reliability Military PCBs
Designing a military PCB isn’t just about throwing some components on a board and calling it a day. It requires strategic thinking and a solid grasp of electromagnetic principles. High-frequency and high-power applications often mean that even the tiniest layout error can spell disaster.
Controlled impedance design is a technique worth its weight in gold when it comes to maintaining signal integrity in these demanding environments. This technique involves carefully designing trace widths and spacing to ensure consistent impedance throughout the PCB, reducing signal reflections that can lead to performance issues.
Let’s talk spacing: it’s not just a matter of aesthetics. Proper spacing between traces can help prevent crosstalk, a common issue in high-frequency designs where signals interfere with one another. Via placement is another critical consideration. Strategically placing vias can help in routing signals effectively while minimizing inductance.
Example: The Consequences of Poor Layout
Consider a military communication device designed for rapid deployment. If the PCB layout doesn’t adhere to best practices, such as adequate ground plane design, the device could experience issues like signal degradation or increased noise, ultimately affecting mission success. By investing the time to get the layout right, engineers can avoid these costly pitfalls.
Grounding Techniques for Military Applications
Effective grounding plays a major role in military PCB design. A robust ground plane significantly cuts down on electromagnetic interference (EMI), ensuring that the PCB performs reliably in challenging environments. Techniques like star grounding, where all ground connections converge at a single point, can be particularly effective in minimizing ground loops, enhancing overall performance. This approach helps maintain signal integrity and reduces noise, which is especially crucial in military applications. Don’t overlook the importance of a solid grounding strategy—taking the time to implement these techniques can lead to better reliability and performance in the field!
Material Selection for Military PCB Applications
Evaluating Materials for Military PCB Design
Selecting materials for military PCB design is no trivial matter. The choice of materials can significantly impact how a board performs under demanding conditions. Among the common contenders, FR4, polyimide, and ceramic really stand out, each offering distinct advantages tailored to specific military needs.
FR4 is often regarded as the workhorse of the PCB world. It balances performance with cost-effectiveness, making it a reliable choice for various military electronics. Whether it’s in communication devices or control systems, FR4’s robust properties make it a go-to for many standard applications.
On the flip side, polyimide is where the heat resistance comes into play. With a temperature range that can handle the hottest of environments, polyimide is perfect for situations where high thermal stability is a must. For instance, in systems deployed in desert operations, using polyimide ensures the PCB can withstand scorching temperatures without breaking a sweat.
Ceramic materials might hit the wallet harder, but they offer stellar performance in high-frequency applications. When you need reliable signal integrity in radar systems or advanced communication devices, ceramic can deliver the kind of performance that justifies the extra cost. It’s like putting premium fuel in a high-performance sports car—it helps the whole system operate at its best.
Table 1: Material Comparison for Military PCBs
Material | Temperature Range | Benefits | Use Case Examples |
FR4 | -40°C to +130°C | Cost-effective, good electrical properties | General military electronics |
Polyimide | -60°C to +200°C | Excellent thermal stability | Equipment in extreme heat environments |
Ceramic | -55°C to +125°C | High-frequency performance | Radar systems, communication devices |
The Importance of Thermal Management in Military PCB Manufacturing
Heat isn’t just an inconvenience; it’s the sworn enemy of electronics. In military PCB manufacturing, managing heat can be the difference between success and failure. Whether it’s from the harsh environment or the components themselves, overheating can lead to catastrophic results.
Incorporating advanced thermal management techniques into your designs is key to keeping the electronics cool under pressure. This includes strategies like heat sinks, which dissipate heat away from sensitive components, and thermal vias that conduct heat through the PCB layers to the outer surfaces. These techniques create pathways for heat to escape, preventing the board from turning into a ticking time bomb.
Proper airflow considerations are equally important. Designing enclosures that allow air to circulate freely can make a significant difference. A good rule of thumb is to ensure that air can flow across the surface of the PCB, particularly in high-density designs where heat can accumulate quickly.
Example: A Practical Look at Thermal Management
Take, for example, a military communication device that’s deployed in a vehicle. If this device lacks effective thermal management, it risks overheating during long missions, leading to system failures. By integrating heat sinks and ensuring adequate airflow, engineers can help the device maintain operational temperatures, keeping communication lines open and soldiers safe.
Signal Integrity and Electromagnetic Compatibility in Military PCB Designs
Controlling Signal Integrity for Military PCB Design
When it comes to military applications, maintaining signal integrity isn’t just a nice-to-have; it’s a non-negotiable requirement. High-speed signals travel at lightning speeds, and even the slightest degradation can lead to malfunctions with potentially dire consequences for mission success and personnel safety.
To keep those signals crystal clear, it’s a smart move to implement techniques like differential signaling and proper termination. Differential signaling involves using pairs of conductors that carry opposite signals, effectively canceling out any noise that might sneak in. This approach shines in high-speed applications, such as radar and communication systems, where maintaining clarity is paramount. By prioritizing these methods in your designs, you not only enhance performance but also safeguard the integrity of your signals. Don’t leave it to chance—make sure your designs are equipped with these strategies to ensure top-notch signal quality!
Additionally, proper termination minimizes reflections that can occur when signals hit the end of a transmission line. By ensuring that your circuits are properly terminated, you not only maintain the integrity of the signals but also enhance the overall performance of your military systems.
Table 1: Techniques for Maintaining Signal Integrity
Technique | Description | Benefits |
Differential Signaling | Uses two wires carrying opposite signals | Reduces noise and improves signal clarity |
Proper Termination | Ensures impedance matching at circuit ends | Minimizes reflections and enhances performance |
Controlled Impedance | Designs PCB traces to maintain consistent impedance | Helps maintain signal integrity over distance |
Ensuring Electromagnetic Compatibility (EMC) in Military PCB Manufacturing
Electromagnetic interference (EMI) can really mess things up, especially in military settings where devices are often crammed together. For military PCB manufacturing, it’s a must to weave in strategies for electromagnetic compatibility (EMC) right from the get-go in the design phase. By addressing these concerns early on, manufacturers can help ensure that devices perform smoothly without unwanted disruptions. This proactive approach not only protects the integrity of the circuits but also keeps systems functioning as intended in challenging environments. So, roll up your sleeves and prioritize EMC in your designs to keep everything in sync!
Effective strategies include shielding, filtering, and proper grounding. Shielding involves using conductive enclosures or coatings to block EMI from affecting the PCB. Filtering employs components that allow desired signals to pass while blocking unwanted frequencies. Grounding, meanwhile, provides a common reference point for all electronic components, reducing the potential for noise and interference.
Think of it this way: if you want your tech to play nice with others, you’ve got to give it the tools to do so. Implementing robust EMC practices can mean the difference between a system that operates seamlessly and one that’s plagued with glitches and malfunctions.
Example: EMC in Action
Let’s consider a military drone that relies on multiple systems for navigation, communication, and payload management. If these systems don’t play well together due to EMI, you could end up with a situation where the drone loses control or, worse, becomes inoperable during a critical mission.
By employing effective shielding and grounding techniques during the PCB manufacturing process, engineers can ensure that each component operates smoothly, even in the chaotic electromagnetic environment of a military operation.
Advanced PCB Stack-Up Configurations for Military Applications
Optimized Military PCB Stack-Up for Rugged Performance
Stack-up configurations are like the secret sauce of military PCB design—getting it right can make all the difference in durability and performance. In the rugged environments where military equipment operates, an optimized stack-up can boost dependability in harsh conditions. Multi-layer boards shine in this regard, allowing for compact designs while still delivering high performance. This makes them an ideal choice for military applications, where space is often tight. So, don’t cut corners—invest in a thoughtful stack-up design to ensure your PCBs stand tall under pressure!
When determining the ideal stack-up, factors like dielectric thickness, material properties, and layer arrangement come into play. For instance, selecting materials with low dielectric constants can significantly improve signal integrity by reducing capacitance. A thoughtfully designed stack-up can lead to clearer signals, better thermal management, and improved mechanical strength—all crucial elements in high-stakes situations where precision matters.
Table 1: Key Considerations for Military PCB Stack-Up Design
Factor | Description | Impact on Performance |
Dielectric Thickness | Thickness of insulation layers | Influences signal integrity and capacitance |
Material Properties | Characteristics of substrates and laminates | Affects thermal performance and mechanical strength |
Layer Arrangement | Order of conductive and insulating layers | Impacts overall board function and reliability |
Military Rigid-Flex PCB Solutions
In the world of military design, space can be tight—this is where rigid-flex PCBs step in as a lifesaver. These innovative boards merge the benefits of both rigid and flexible circuits, making them an ideal choice for applications that demand flexibility without sacrificing durability. Whether it’s in avionics, communication systems, or portable military devices, rigid-flex technology can elevate your designs to new heights.
Rigid-flex PCBs are a marvel of modern engineering, offering the perfect blend of flexibility and structural strength. These boards are designed to navigate complex geometries effortlessly, making them ideal for applications that experience continuous movement or vibration. This adaptability significantly lowers the chance of fatigue failures, a common issue with traditional rigid boards.
Additionally, the streamlined nature of rigid-flex designs reduces the number of interconnects, leading to improved performance and reliability—especially in high-stakes environments.
Example: Rigid-Flex PCB in Action
Consider a military drone that requires a compact, lightweight solution for its control systems. By utilizing a rigid-flex PCB, engineers can design the circuit board to fit snugly within the drone’s limited space while ensuring that it withstands the rigors of flight. This adaptability not only conserves space but also simplifies assembly, reducing potential failure points.
Military PCB Manufacturing Best Practices
Essential Processes in Military PCB Manufacturing
Building a military-grade PCB is no easy feat—it takes meticulous attention to every single detail. Processes like via filling, advanced plating methods, and the strategic use of microvias are key to creating boards that can handle the rigorous conditions military applications throw their way. These specialized techniques ensure that the boards are tough enough to withstand demanding environments without compromising performance.
Via Filling: This process significantly improves the board’s ability to manage heat while enhancing its durability. By using high-grade filling materials, manufacturers prevent delamination and ensure vias stay intact, even under tough conditions. When heat dissipation is a priority, choosing the right materials ensures optimal thermal conductivity, keeping the PCB circuit board performing under pressure.
Plating Techniques: Proper plating techniques are fundamental in ensuring robust electrical connections. The plating process creates a conductive layer that connects the different components of the PCB, providing a pathway for signals and power. Techniques such as electroless plating and electroplating can improve the quality and reliability of connections, especially in high-frequency and high-current applications.
Microvias: These tiny vias allow for more complex circuit designs and denser layouts, which are increasingly necessary in modern military technology. Microvias can facilitate better signal routing and reduce the overall size of the PCB, making them a popular choice for advanced military applications.
Table 1: Key Processes in Military PCB Manufacturing
Process | Description | Benefits |
Via Filling | Filling vias to improve thermal performance | Prevents delamination and enhances reliability |
Plating Techniques | Creating conductive layers for connections | Ensures strong electrical pathways |
Microvias | Utilizing small vias for complex designs | Facilitates denser layouts and better signal routing |
Maintaining ITAR Compliance in Military PCB Manufacturing
Compliance isn’t just about ticking boxes; it’s a matter of national security. ITAR (International Traffic in Arms Regulations) governs the export and import of military technologies, and adhering to these regulations is a must for any company involved in military PCB manufacturing.
To ensure compliance, companies must implement rigorous internal protocols and maintain constant vigilance over their processes. This includes proper documentation, employee training, and regular audits of production practices. By fostering a culture of compliance, manufacturers not only protect their business but also contribute to the safety of our armed forces.
Imagine a scenario where a military PCB is improperly exported due to lack of compliance. The ramifications can be severe, leading to legal issues and jeopardizing sensitive military operations. Therefore, maintaining ITAR compliance is an investment in your company’s integrity and the safety of those who serve.
Quality Control in Military PCB Manufacturing
Testing Procedures for High-Reliability Military PCBs
Quality control isn’t just a checkbox; it’s a way of life in military PCB manufacturing. When it comes to high-reliability military PCBs, the stakes are sky-high. Rigorous testing procedures are in place to ensure these boards can perform under the most demanding conditions.
Key Testing Procedures-
Thermal Cycling: This test involves subjecting the PCB to extreme temperature variations, simulating real-world conditions it might face in the field. By rapidly cycling between high and low temperatures, manufacturers can identify weak points that may lead to failure.
Vibration Testing: Military equipment often experiences significant vibrations, whether in land vehicles or aircraft. Vibration testing assesses the PCB’s resilience, ensuring it can withstand the jolts and shakes without compromising performance.
Humidity Resistance Tests: Moisture can wreak havoc on electronic components. By exposing PCBs to high humidity conditions, manufacturers can evaluate how well the boards resist corrosion and other moisture-related issues.
These tests help to weed out potential failures before they become real problems. The goal? Delivering a product that meets or exceeds military standards every time. As they say, “An ounce of prevention is worth a pound of cure!”
Table 1: Key Testing Procedures in Military PCB Manufacturing
Testing Procedure | Purpose | Outcome |
Thermal Cycling | Simulates temperature extremes | Identifies weak points under thermal stress |
Vibration Testing | Assesses resilience to vibrations | Ensures performance under dynamic conditions |
Humidity Resistance | Evaluates moisture resistance | Prevents corrosion and related failures |
Automated Inspection Techniques for Military PCB Assembly
With the stakes so high, manual inspection alone just won’t cut it. The military deserves nothing less than perfection. That’s where automated inspection techniques come into play.
Automated Optical Inspection (AOI)-
This cutting-edge technology uses high-res cameras paired with advanced algorithms to give your PCBs a thorough once-over. AOI (Automated Optical Inspection) spots issues like missing components, misalignments, and soldering mistakes at breakneck speed. When you’re working with tight tolerances, this level of precision makes all the difference.
AOI is especially handy for high-volume production where manual inspections just can’t keep up. By automating the defect detection process, you save time while ensuring top-notch quality across the board.
X-Ray Testing-
When it comes to catching those sneaky defects, X-ray testing is your go-to tool. It gives manufacturers a clear look inside multi-layered boards, pinpointing issues like voids in solder joints or other hidden anomalies that can’t be spotted from the outside. It’s like having X-ray vision for your PCBs, helping you ensure that everything inside is up to spec without any guesswork.
X-ray testing is especially useful for high-density boards where a visual inspection just won’t cut it. By scanning beneath the surface, you get a detailed view of potential problem areas before they turn into bigger headaches down the line.
These automated techniques are indispensable tools in military PCB assembly. They catch defects that human eyes might miss, ensuring your boards are up to snuff before they head out into the field. The result? A robust, reliable product ready to stand the test of time.
Military PCB Assembly Techniques for Defense Systems
Advanced Military PCB Assembly Methods
Assembling military PCBs isn’t just a task; it’s an art form that requires precision and specialized techniques. Two of the most widely used methods in military PCB assembly are Surface Mount Technology (SMT) and Through-Hole Technology (THT). Each method has its unique advantages, and the choice between them often hinges on the specific application and environmental demands.
Surface Mount Technology (SMT)-
SMT is a go-to for high-density applications, especially when space is at a premium. This method allows components to be mounted directly onto the surface of the PCB, making it perfect for compact designs. The advantages of SMT include:
●Compactness: Allows for smaller board sizes, which is a major plus in military applications where space is often limited.
●Automated Assembly: SMT (Surface Mount Technology) is perfect for automation, making the assembly process faster and more efficient. By reducing the need for manual labor, it helps to lower costs while keeping production on schedule, even when deadlines are tight. When you’re up against the clock, SMT can be the go-to option for speeding up production without sacrificing precision.
While SMT (Surface Mount Technology) brings a lot of advantages to the table, it also comes with its own set of challenges. One of the big ones? Solder joints in SMT can be more prone to mechanical stress. This makes it super important to design with environmental factors in mind, like vibrations or shifts in temperature, which can cause thermal expansion.
Through-Hole Technology (THT)-
On the flip side, THT offers enhanced mechanical strength, making it a solid choice for military gear that may endure a lot of physical stress. This method involves inserting components through holes in the PCB and soldering them to the opposite side, providing:
●Robust Connections: THT connections are less likely to fail under extreme conditions, ensuring reliability when it matters most.
●Higher Current Capacity: It’s a go-to for components that require higher power, which is often necessary in military applications.
When deciding between SMT and THT, consider the specific operational environment. Each method serves its purpose, and the best choice can mean the difference between mission success and failure.
Soldering Standards and Techniques for Military PCB Assembly
In military PCB assembly, getting the soldering process right is make-or-break. Precision in soldering isn’t just a nice-to-have—it’s a requirement, especially when your boards are being used in demanding military environments. Every joint needs to be solid and up to strict standards, ensuring long-lasting reliability where it matters most.
Whether you’re working on mission-critical electronics or high-tech military systems, you can’t cut corners when it comes to soldering. At JarnisTech, we follow the most rigorous soldering protocols, ensuring that every board that leaves our facility is built to withstand the toughest conditions.
Key Soldering Techniques-
●Lead-Free Soldering: With a strong push for environmentally friendly solutions, lead-free soldering has become a standard in military PCB assembly. It’s a smart move that doesn’t compromise on performance—safety first, right?
●High-Temperature Soldering: In many military environments, equipment can be exposed to extreme heat. High-temperature soldering processes ensure that the joints remain intact, even in challenging conditions.
Table 1: Comparison of SMT and THT in Military PCB Assembly
Method | Advantages | Considerations |
Surface Mount Technology (SMT) | Compact design, automated assembly, high density | More sensitive to mechanical stress |
Through-Hole Technology (THT) | Robust connections, higher current capacity | Requires more space, more manual labor |
Military PCB Testing and Certification
Meeting MIL-STD-810 and MIL-PRF-31032 Standards
When it comes to military PCBs, certification isn’t just a nice-to-have; it’s a badge of honor that showcases the quality and reliability of your boards. Meeting the MIL-STD-810 and MIL-PRF-31032 standards proves your PCBs are geared up to handle the harsh realities of military life.
Comprehensive Testing Protocols-
These standards come with rigorous testing protocols that cover a wide range of environmental conditions. Here’s what you can expect:
Thermal Shock Testing: This test simulates extreme temperature fluctuations, ensuring that your PCBs can handle the heat—or the cold—without missing a beat.
Vibration Testing: With military equipment often exposed to intense vibrations, this test ensures that your boards remain functional in dynamic environments, such as during transportation or combat scenarios.
Humidity Resistance Testing: Given the unpredictable weather conditions military gear may face, this testing checks the board’s resilience against moisture and corrosion.
By adhering to these comprehensive testing protocols, you ensure that every inch of your PCB meets or exceeds military expectations. Think of it as putting your boards through boot camp—only the toughest make it through!
Table 1: Overview of Testing Procedures for MIL-STD-810 and MIL-PRF-31032
Testing Type | Purpose | Key Conditions Tested |
Thermal Shock Testing | Simulates rapid temperature changes | Extreme heat and cold cycles |
Vibration Testing | Ensures functionality under movement | Various frequency and amplitude ranges |
Humidity Resistance | Tests moisture resistance | Prolonged exposure to high humidity levels |
ITAR and Global Export Compliance in Military PCB Manufacturing
In today’s interconnected landscape, compliance isn’t just a matter of ticking boxes; it’s a whole new ball game. For any organization in military PCB manufacturing, understanding International Traffic in Arms Regulations (ITAR) is a must.
The Importance of ITAR Compliance-
ITAR governs the export and import of military technologies, and compliance is non-negotiable. Here’s why:
Protecting Sensitive Technologies: Following ITAR regulations safeguards sensitive military technology from falling into the wrong hands, ensuring national security remains intact.
Supply Chain Vigilance: Ensuring that your supply chain and manufacturing processes adhere to these regulations isn’t just about protecting your business; it’s about contributing to the safety of our armed forces.
Emerging Trends in Military PCB Design and Manufacturing
Innovations in HDI and Flex Circuits for Military PCB Applications
The military PCB landscape is not standing still; it’s constantly shifting thanks to groundbreaking technological advancements. High-Density Interconnect (HDI) technology is leading the charge, transforming the way military electronics are designed. By utilizing smaller pads and vias, HDI PCBs enable a higher circuit density that is often necessary in military applications, where real estate on the board is at a premium.
Why HDI Matters?
Space Optimization: As military equipment becomes more compact and multifunctional, HDI technology allows designers to fit more circuits into a smaller area without compromising performance.
Improved Performance: With shorter interconnections, HDI designs help reduce signal loss and improve speed, which is a big win for mission-critical applications.
Flex circuits are shaking things up in the military PCB sector, offering a lightweight and space-saving solution that’s tough to rival. These circuits bring the flexibility needed to squeeze into tight spaces while still delivering full functionality. Their ability to bend and fit around irregular shapes makes them perfect for gear like wearable tech, helmet displays, and other intricate assemblies found in today’s advanced military equipment.
With flex circuits, you’re not just saving space—you’re boosting the efficiency of your designs without adding unnecessary bulk. If you’re dealing with complex layouts or looking for innovative ways to streamline your military tech, flex circuits from JarnisTech offer a reliable way to get the job done.
Need to add some flexibility to your next project? Hit us up at JarnisTech, and let’s explore how flex circuits can be the game-changer your military tech needs!
Table 1: Key Benefits of HDI and Flex Circuits
Technology | Key Benefits | Ideal Applications |
HDI | Higher circuit density, reduced signal loss | Compact military electronics |
Flex Circuits | Lightweight, adaptable to irregular shapes | Wearable tech, complex assemblies |
Exploring New Materials in Military PCB Manufacturing
The search for the next big thing doesn’t stop with circuit designs. The development of new materials is a thrilling trend in the military PCB sector. While traditional materials like FR4 have served us well, they’re increasingly being supplemented—or even replaced—by advanced materials that deliver superior performance characteristics.
Innovative Materials Making Waves-
Graphene and Carbon Nanotubes: These materials are gaining attention for their remarkable electrical properties and impressive strength-to-weight ratios. Imagine packing a lot of power into a lighter package—that’s what these materials promise.
Thermal Management: Utilizing these advanced materials can enhance the thermal performance of PCBs, ensuring that military electronics can withstand extreme conditions without overheating.
By incorporating such innovative materials, military electronics can not only boost performance but also shave off weight—an absolute must when you’re operating in the field. A lighter load means better mobility and efficiency, which can make all the difference in a battlefield scenario.
Why Choose Us as Your Military PCB Board and PCB Assembly Supplier?
JarnisTech offers quality, long-lasting, and durable PCBs that can be used in a range of defense and military applications. JarnisTech has ISO 9001:2008 and is certified by UL as well as RoHS certified, so you can expect these printed circuit boards to perform well under the challenging conditions that military equipment is subjected to. We also make a variety of PCBs that are suitable for various applications in the defense and military.
When it comes to military or defense applications that require quality printed circuit boards, Find out why countless companies in virtually every major industry trust JarnisTech. In contrast to other PCB makers, we also provide PCB assembly services. As a result, you don’t need to waste time looking for a good assembly service and transporting your materials, as we handle all everything, so your operations can run more smoothly. Our stock includes many special military grade materials, such as Arlon, Taconic PCB, and Teflon PCB and more.
1.Unmatched Quality Assurance & Certifications
At JarnisTech, we take pride in our robust quality assurance system that ensures our PCBs meet the rigorous demands of the aerospace and defense sectors. Our facilities are ITAR registered and certified, consistently exceeding the requirements set forth by various aerospace and government programs. This commitment to excellence guarantees that our products deliver the reliability and performance needed for critical applications.
Our quality control processes are thorough, incorporating a range of testing methodologies, including thermal cycling and vibration testing, to ensure every board stands up to the most challenging conditions.
2.Advanced Capabilities for Specialized PCBs
Thanks to our cutting-edge technology, we have the capability to produce highly specialized aerospace and government program military PCBs that meet the toughest design criteria. Whether it’s a complex multilayer board with up to 40 layers, via-in-pad configurations, or advanced laser-drilled microvias, we’ve got you covered.
Our capabilities also extend to producing oversized boards and heavy copper options—up to 40 ounces—allowing us to meet the diverse needs of our clients. For example, our microwave and antenna boards are designed to perform reliably in high-frequency applications, making them perfect for military communications systems.
Capability | Description |
Layers | Up to 40 layers for complex designs |
Via Types | Via-in-pad and laser-drilled microvias |
Copper Weight | Heavy copper options, up to 20 ounces |
Board Types | Microwave/antenna boards, oversized boards |
3.Seamless Manufacturing to Assembly Transition
Choosing JarnisTech means partnering with a leading one-stop service PCB manufacturer in China. We excel in providing rapid turnaround times and accommodating small quantity assembly requests, ensuring you get what you need when you need it.
Our integrated approach allows for a smooth transition from manufacturing to assembly. This streamlining of processes not only reduces lead times but also enhances the overall quality of the final product.
4.Extensive Material Selection for High Performance
Choosing the right materials can make all the difference when it comes to aerospace and government PCB design. At JarnisTech, we’ve got you covered with a range of high-performance materials that are specifically engineered to handle the demands of the aerospace and defense sectors. Whether you’re working on cutting-edge aircraft systems or high-stakes government projects, we have the advanced materials that deliver the reliability and performance you need.
For example, we utilize high-frequency laminates for microwave applications and thermally conductive materials to manage heat effectively. This diverse material palette allows us to address specific challenges head-on, ensuring that your military electronics can withstand the rigors of their operational environments.
From handling extreme temperatures to providing top-notch electrical performance, our selection of materials is tailored to meet the unique challenges of these industries. If you’re looking for a supplier that truly understands the ins and outs of aerospace and defense PCBs, look no further. JarnisTech is here to help you take your projects to the next level with materials that won’t let you down.
Ready to Elevate Your Military PCB Needs?
Let JarnisTech be your go-to partner for military PCB boards and assembly. With our unmatched quality assurance, advanced capabilities, and a commitment to seamless service, we’re here to ensure your projects succeed. Contact us today to discuss your specific needs and see how we can help you take your military applications to the next level!
FAQ
What are military PCBs, and how do they differ from standard PCBs?
Military PCBs are specially designed printed circuit boards used in defense and aerospace applications. They differ from standard PCBs in terms of durability, reliability, and compliance with specific military standards like MIL-PRF and MIL-STD. Military PCBs must withstand extreme conditions, making their design and manufacturing processes more stringent.
How do I ensure compliance with military standards in PCB manufacturing?
Ensuring compliance with military standards involves understanding the specific requirements set by regulations like MIL-PRF and MIL-STD. It’s essential to work with experienced manufacturers who are familiar with these standards and implement rigorous testing and quality control measures throughout the manufacturing process.
What materials are commonly used in military PCB design?
Common materials for military PCBs include FR4, polyimide, and ceramic. Each material has unique properties suited for specific applications. For example, polyimide offers excellent thermal stability, making it ideal for high-temperature environments, while FR4 provides a good balance of performance and cost.
What testing procedures are necessary for military PCBs?
Testing procedures for military PCBs typically include thermal cycling, humidity resistance, vibration testing, and electrical testing. These procedures ensure that the PCBs can perform reliably in extreme conditions, addressing potential failure points before deployment.
How can I choose the right military PCB manufacturer?
Choosing the right manufacturer involves evaluating their expertise in military PCB design and manufacturing, reviewing their certifications and compliance history, and assessing their ability to communicate effectively. Look for a partner with a proven track record in delivering high-quality military PCBs on time.
What role do emerging technologies play in military PCB design?
Emerging technologies like High-Density Interconnect (HDI) and new materials such as graphene and carbon nanotubes are transforming military PCB design. These advancements allow for more compact designs with enhanced performance and durability, catering to the evolving needs of modern military applications.
How does the assembly process differ for military PCBs?
The assembly process for military PCBs involves specialized techniques and standards to ensure reliability. Methods like Surface Mount Technology (SMT) and Through-Hole Technology (THT) are commonly used, with a focus on strict soldering standards and thorough quality checks to guarantee that each assembly meets military specifications.