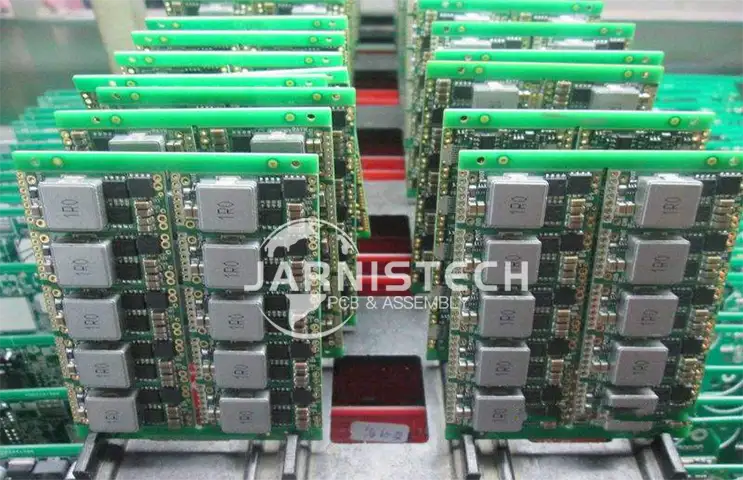
At JarnisTech, we specialize in low-volume PCB assembly, offering comprehensive turnkey solutions tailored to meet your unique needs. Our services encompass fabrication, component mounting, assembly testing, and timely delivery. With a dedicated team of skilled engineers, we ensure that small-scale PCB projects are completed with the shortest lead times possible.
As a leading small-batch PCB manufacturer, we leverage state-of-the-art equipment and advanced capabilities to fulfill our customers’ demands for quality and quick turnaround. By implementing techniques such as Design for Manufacturing (DFM) and Design for Testing (DFT), we proactively identify and address potential issues before final production, optimizing the entire assembly process.
Since 1999, we have proudly held ISO 9001:2015 certification, and our personnel are IPC-certified. Our commitment to quality is reinforced by our rigorous Triple Process Inspection, ensuring that every aspect of small batch PCB assembly meets the highest standards. Our QA team employs a range of inspection and testing technologies, including laser inspections and X-ray tests, guaranteeing reliability in each assembly. Each small batch production PCB is crafted with expert support, thorough reliability testing, and skilled craftsmanship.
Ready to take your PCB project to the next level? Partner with JarnisTech for reliable, high-quality low-volume PCB assembly!
Understanding Low-Volume PCB Assembly
What is Low-Volume PCB Assembly?
Low-volume PCB assembly refers to the production of printed circuit boards in smaller quantities, typically ranging from a few units to a few hundred. This approach is particularly beneficial for companies that are in the initial stages of product development or those testing new designs before committing to mass production.
Think of low-volume PCB assembly as the “dress rehearsal” for your product. Instead of throwing all your chips on a massive production run, you can produce a limited batch to gather feedback from potential users. This method allows for flexibility and reduces financial risk, so you’re not putting all your eggs in one basket!
●Key Characteristics of Low-Volume PCB Assembly:
Customization: Manufacturers often cater to specific design requirements, providing tailored solutions for unique projects.
Quick Turnaround: Many service providers focus on delivering orders in a timely manner, allowing companies to pivot based on market feedback.
Diverse Techniques: Various assembly techniques, such as Surface Mount Technology (SMT) and through-hole assembly, can be utilized to meet project needs.
Importance of Low-Volume PCB Assembly in Prototyping and Product Development
Low-volume PCB assembly is like having a secret weapon in your back pocket during the prototyping phase of product development. It allows engineers and designers to test their concepts in real-world scenarios, making adjustments as necessary before full-scale production. This iterative process is key to fine-tuning designs and ensuring product viability.
●Example: The Prototyping Process
Let’s say a company is developing a new wearable fitness tracker. During the initial stages, they create a prototype using low-volume PCB assembly to test functionality and gather user feedback. Based on this information, they might find that some adjustments are in order—perhaps they need to shift component placement or tweak the circuitry to amp up performance.
Prototyping Phase | Action | Outcome |
Initial Design | Create prototype using low-volume assembly | Test functionality |
User Testing | Gather feedback from real users | Identify areas for improvement |
Adjustments | Modify design based on feedback | Enhance product performance |
This approach not only saves time and resources but also leads to better end products. In today’s competitive market, having a well-tested product can mean the difference between success and fading into the background.
Advantages of Choosing Chinese PCB Assembly Services
Cost-Effective Solutions for Low-Volume PCB Assembly
When it comes to low-volume PCB assembly, Chinese manufacturers often offer a pocket-friendly option that makes your wallet happy. This affordability stems from various factors, such as lower labor costs and streamlined production processes. As a result, businesses can enjoy high-quality assembly without breaking the bank.
●Competitive Pricing for Low-Volume PCB Assembly
Chinese PCB assembly services are known for their competitive pricing. Imagine you’re a startup looking to test the waters with a new electronic device. By opting for low-volume assembly in China, you can keep your expenses in check while ensuring that your product meets the required standards. For instance, a company might find that they can produce 100 units for the price they’d pay for just 50 units domestically.
Cost Comparison | Domestic Assembly | Chinese Assembly |
Cost per unit | $20 | $10 |
Total for 100 units | $2,000 | $1,000 |
This kind of cost efficiency enables businesses to allocate resources elsewhere, like marketing or further product development. It’s all about getting more bang for your buck!
●Affordable Prototyping Services
Prototyping is a crucial phase in product development, and Chinese manufacturers excel in offering affordable prototyping services. This allows companies to create a small batch of prototypes to gather feedback without the hefty price tag. Think of it as a trial run before the big show.
Consider a tech firm developing a new gadget. They can create several prototypes to test different features, ensuring they hit the nail on the head when launching the final product. By keeping costs low, they can iterate quickly and effectively.
Efficiency in Production with PCB Assembly Services
In product development, timing is everything, and Chinese PCB assembly services excel in efficiency. By leveraging cutting-edge manufacturing methods and well-established supply chains, these services can greatly reduce production timelines. This streamlined approach allows for faster turnaround, enabling businesses to bring their products to market more quickly.
With a focus on precision and quality, these services not only expedite the assembly process but also ensure that the final product meets the highest standards. When you choose Chinese PCB assembly, you’re not just getting a service; you’re investing in a partnership that prioritizes your project’s success.
●Quick Turnaround Times
Chinese manufacturers often provide quick turnaround times, allowing businesses to get their products to market faster. Imagine you’re racing against competitors and need to launch your device before the next big event. With efficient production capabilities, your assembly partner can deliver high-quality PCBs in a fraction of the time it might take elsewhere.
For example, a company might place an order for low-volume assembly and receive their products within two weeks. This rapid response can be the difference between leading the pack or trailing behind.
Production Timelines | Standard Lead Time | Chinese Assembly Lead Time |
Low-volume assembly | 4-6 weeks | 1-2 weeks |
●Flexibility in Custom PCB Assembly
One of the standout features of Chinese PCB assembly services is their flexibility. Whether you need a specific component, unique layout, or specialized testing, these manufacturers are often willing to accommodate your needs. It’s like having a partner who’s ready to roll with the punches and adapt as your project evolves.
For instance, if you decide to tweak your design midway through production, many manufacturers can adjust their processes without significant delays. This adaptability makes it easier to refine your product based on feedback or new insights.
Ready to take advantage of cost-effective and efficient PCB assembly services in China? By choosing the right partner-JarnisTech, you can enhance your product development process and keep your budget in check. Don’t miss out—reach out today and see how these services can elevate your projects to the next level!
Core Features of Low-Volume PCB Assembly Services
Low-Volume PCB Assembly
Customization and High Mix Low Volume Capabilities in PCB Assembly
One of the standout features of low-volume PCB assembly services is their ability to offer customization. This flexibility allows companies to create unique solutions tailored to their specific needs, making it easier to differentiate themselves in a crowded market.
●Tailored PCB Designs
Customization in PCB design is not just a luxury; it’s a necessity for many businesses looking to bring innovative products to life. Whether you need a specific layout, unique component placement, or specialized features, the ability to tailor your PCB design is invaluable.
Think about it: a tech startup may have a revolutionary idea for a smart device that requires a one-of-a-kind PCB layout. By working with a manufacturer that specializes in tailored designs, they can ensure that every component is perfectly positioned to maximize performance. This level of personalization sets the stage for success.
Customization Aspect | Standard PCB Design | Tailored PCB Design |
Layout | Fixed | Flexible |
Component Placement | Generic | Optimized |
Unique Features | Limited | Extensive |
●Small Quantity Assembly
Low-volume assembly offers the advantage of producing small quantities without sacrificing quality. This is particularly beneficial for businesses testing new products or entering niche markets.
Imagine a company launching a new gadget that appeals to a specific audience. By utilizing low-volume assembly, they can produce a limited run of their product to gauge market interest before committing to larger production. This strategy not only saves money but also allows for quick adjustments based on initial feedback.
Quality Assurance Practices in PCB Assembly Services
Quality assurance is a must-have in PCB assembly services. In an industry where precision is paramount, effective quality assurance practices are key to delivering dependable products. This commitment to quality means implementing rigorous testing and inspection processes that leave no room for error.
●Rigorous Testing and Inspection
Before any PCB leaves the production line, it undergoes a series of rigorous tests and inspections. This process ensures that each board meets the required specifications and performs as intended.
For instance, manufacturers may employ Automated Optical Inspection (AOI) and functional testing to catch any issues early. By identifying problems before they reach the customer, companies can avoid costly recalls and enhance their reputation.
Testing Method | Purpose | Outcome |
Automated Optical Inspection | Detect surface defects | High-quality output |
Functional Testing | Ensure functionality | Reliable performance |
Environmental Testing | Simulate real-world conditions | Durability assurance |
●Reliable Material Sourcing Strategies
Quality PCB assembly starts with quality materials. Reputable manufacturers prioritize reliable sourcing strategies to ensure that only top-notch components are used in production.
By forging strong relationships with suppliers, manufacturers can secure the best materials at competitive prices. This not only enhances the overall quality of the final product but also contributes to cost savings for businesses.
If you’re ready to take advantage of the core features of low-volume PCB assembly services, don’t hesitate to reach out. With customized solutions and stringent quality assurance practices, you can develop products that not only meet your expectations but also resonate with your target audience. Get in touch today and let’s make your vision a reality!
The PCB Assembly Process in Detail
Overview of the Low-Volume PCB Assembly Workflow
The low-volume PCB assembly process consists of a carefully coordinated series of steps that convert concepts into physical products. Gaining insight into this workflow is essential for anyone engaged in electronic manufacturing.
●Initial Design and Prototyping Stages
The journey begins with the initial design phase. Engineers collaborate to create detailed schematics and layouts for the PCB. This stage is where creativity meets practicality. Designers utilize specialized software to craft blueprints, ensuring that every component is in the right spot.
Once the designs are finalized, prototyping kicks in. This phase allows for the creation of a small number of initial boards to test the concept in real-world conditions. It’s akin to a dress rehearsal—perfect for identifying any potential hiccups before the final performance. Feedback gathered during this stage is invaluable, guiding necessary adjustments.
Design Stage | Activities | Outcome |
Initial Design | Create schematics and layouts | Detailed blueprint |
Prototyping | Produce small batches for testing | Real-world feedback |
●Manufacturing Processes: SMT Assembly and Through-Hole Techniques
Once the designs are validated, the manufacturing phase commences. Two primary techniques dominate this stage: Surface Mount Technology (SMT) and through-hole assembly.
Surface Mount Technology (SMT) allows for components to be mounted directly onto the surface of the PCB. This method is favored for its efficiency and the ability to place a high number of components in a compact space. On the flip side, through-hole assembly involves inserting component leads through holes in the PCB, securing them with solder on the opposite side. This technique is often used for components requiring greater durability or higher power.
Each method has its own set of advantages, and many manufacturers combine both to leverage the benefits of each.
Manufacturing Technique | Advantages | Applications |
SMT | Higher density, faster assembly | Consumer electronics |
Through-Hole | Stronger mechanical bonds | Industrial equipment |
●Quality Control Measures
Quality control is the backbone of the PCB assembly process. Before any PCB reaches the customer, it undergoes rigorous testing and inspection. This includes automated optical inspections (AOI) to detect surface defects, as well as functional testing to ensure each board operates as intended.
Implementing these measures helps catch potential issues early, reducing the likelihood of costly mistakes down the line. It’s like having a safety net that ensures your product will perform as promised.
Engineering Support for Low-Volume PCB Assembly
Engineering support is an invaluable component of the low-volume PCB assembly process. It serves as the bridge between production and client satisfaction.
●Continuous Client Feedback
Maintaining open lines of communication with clients is essential. Engineers actively seek feedback throughout the assembly process to ensure that the final product aligns with expectations. This iterative approach allows for real-time adjustments, enhancing the overall outcome.
For example, if a client identifies a design flaw during testing, engineers can swiftly address the issue without significant delays. This responsiveness not only fosters trust but also leads to better products.
●Addressing Design Iterations
Design iterations are an integral part of the PCB assembly process. As new information becomes available, modifications may be required to improve functionality or respond to market dynamics. The ability to adapt is key to thriving in this industry.
Engineers work closely with clients to implement design revisions, ensuring that every iteration moves the product closer to perfection. This flexibility allows businesses to stay ahead of the curve and meet evolving consumer demands.
Specialized Techniques in Low-Volume PCB Assembly
Specialized techniques in low-volume PCB assembly ensure high-quality production tailored to specific needs. By grasping these techniques, manufacturers and engineers can choose the most effective methods for their projects, enhancing both efficiency and output quality. Understanding the nuances can make a real difference, helping to avoid costly mistakes down the line. When selecting techniques, it’s important to weigh factors like cost, material compatibility, and time constraints.
Surface Mount Technology (SMT) for Low-Volume PCB Assembly
Surface Mount Technology (SMT) has become a cornerstone of modern PCB assembly, particularly for low-volume production runs. This technique involves mounting components directly onto the surface of the PCB, rather than inserting them through holes.
SMT stands out for its capacity to support a higher density of components within a compact space, making it ideal for today’s slim electronic devices. This method leads to faster assembly times and lower material costs, which is why manufacturers increasingly opt for it to streamline their operations. By embracing SMT, companies can not only boost productivity but also adapt to market demands efficiently. So, if you’re looking to tighten your processes, consider making the switch to SMT!
For example, consider a startup developing a new wearable device. By utilizing SMT, they can fit a variety of sensors and chips onto a small PCB, enhancing the product’s functionality without inflating the size.
Advantage of SMT | Impact on Production |
High component density | Smaller product size |
Faster assembly | Reduced labor costs |
Lower material waste | Increased profitability |
Through-Hole Technology for Complex PCB Assembly Designs
While SMT offers many benefits, Through-Hole Technology remains relevant, especially for complex PCB designs that require robust connections. This method involves inserting component leads through drilled holes in the PCB and soldering them on the opposite side.
Through-hole assembly excels in applications where durability and mechanical strength are paramount, such as in industrial equipment and aerospace applications. Components like connectors and large capacitors often rely on this technique for their sturdy mounting.
For instance, in an automotive application where reliability is non-negotiable, manufacturers may opt for through-hole components to ensure the assembly can withstand harsh conditions. This decision not only enhances the product’s reliability but also builds consumer confidence.
Through-Hole Advantages | Ideal Applications |
Strong mechanical bonds | Industrial and aerospace electronics |
Easy to hand-solder | Prototyping and repairs |
Suitable for larger components | Power supply circuits |
Hybrid Assembly Techniques for Diverse Applications
In many cases, manufacturers employ hybrid assembly techniques that combine SMT and through-hole methods to take advantage of the strengths of each. This approach allows for the optimal placement of components based on their specific requirements.
For example, a hybrid assembly may utilize SMT for compact, low-profile components while incorporating through-hole technology for larger, high-power components that require additional stability. This combination not only maximizes space efficiency but also enhances overall functionality.
By embracing hybrid techniques, companies can address a wider range of applications, from consumer electronics to specialized industrial devices. The ability to adapt the assembly method to suit the project’s needs is a game plan that keeps businesses competitive.
Hybrid Technique | Benefits |
Combines SMT and through-hole | Versatile solutions for diverse needs |
Optimizes space and performance | Increased design flexibility |
Enhances product durability | Suitable for high-performance applications |
Ready to explore specialized techniques for your low-volume PCB assembly needs? Whether you’re looking to leverage SMT, through-hole technology, or hybrid methods, we’re here to help. Let’s collaborate to find the perfect solution that aligns with your project goals. Reach out today, and let’s get the ball rolling!
Challenges in Low-Volume PCB Assembly
Low-Vulume PCB Assembly Services
Low-volume PCB assembly provides adaptability and customization, but it also presents a variety of challenges. Manufacturers must be aware of these obstacles to enhance their workflows and deliver high-quality products. From sourcing components to managing production timelines, each step requires careful consideration. By tackling these issues head-on, companies can refine their processes and achieve better results. Don’t let challenges hold you back—embrace them and elevate your PCB assembly project!
Balancing Quality and Cost in PCB Assembly Services
One of the biggest challenges in low-volume PCB assembly is finding the sweet spot between quality and cost. On one hand, manufacturers want to keep costs down to remain competitive; on the other, they must ensure that their products meet high-quality standards.
This balancing act often requires meticulous planning and strategic sourcing of materials. For instance, opting for cheaper components can lead to lower initial costs but might result in increased failures down the line. In a tight-knit market, a faulty product can tarnish a brand’s reputation faster than you can say “quality assurance.”
A practical approach is to perform a cost-benefit analysis, weighing the long-term implications of material choices. Companies might also consider investing in quality certifications that could justify a higher price point while reinforcing their commitment to excellence.
Cost Strategies | Quality Considerations |
Bulk purchasing discounts | Quality audits and inspections |
Material substitution | Supplier reliability checks |
Design-for-manufacturing | Regular feedback loops with clients |
Managing Supply Chain Dynamics for Low-Volume PCB Assembly
Supply chain dynamics can significantly affect low-volume PCB assembly operations. With fluctuating demand and varying lead times, maintaining a smooth supply chain is no small feat.
For example, a sudden spike in demand for a product can leave manufacturers scrambling to procure necessary components, potentially leading to delays. Conversely, ordering too many components can result in excess inventory, tying up capital that could be better utilized elsewhere.
To tackle these issues, companies should adopt a just-in-time inventory approach, allowing them to respond quickly to changing market conditions without incurring unnecessary costs. Building strong relationships with reliable suppliers can also enhance flexibility, enabling quick adjustments when needed. It’s all about rolling with the punches!
Supply Chain Strategies | Potential Challenges |
Just-in-time inventory | Risk of stockouts during demand spikes |
Strong supplier partnerships | Possible delays in component availability |
Regular supply chain reviews | Over-commitment to unreliable suppliers |
Ensuring Scalability for Future PCB Assembly Needs
As business expand, their PCB assembly requirements frequently shift. Achieving scalability in low-volume PCB assembly processes can be a challenge but is key for long-term success. Organizations must strategize for future growth while avoiding the pitfalls of overcommitting resources. It’s about balancing flexibility and efficiency, ensuring that your processes can adapt as needs evolve. Preparing for tomorrow today can keep you ahead of the curve.
For instance, a small tech startup might begin with a limited run of a new product. As the product gains traction, they must quickly ramp up production while maintaining quality. This requires foresight in designing processes that can easily scale.
Implementing modular assembly techniques can be one way to accommodate growth. This flexibility allows for easy adjustments to production lines, ensuring manufacturers can meet increased demand without sacrificing quality. You’ve got to be ready to pivot when the market shifts!
Scalability Solutions | Growth Considerations |
Modular production lines | Investment in versatile equipment |
Automation of repetitive tasks | Training workforce for adaptability |
Collaborative planning with clients | Anticipating market trends and demands |
Navigating the challenges of low-volume PCB assembly requires expertise and strategic thinking. If you’re facing these hurdles, we’re here to help! Let’s work together to find solutions tailored to your unique needs. Don’t hesitate—reach out today, and let’s get the wheels turning!
Best Practices for Successful Low-Volume PCB Assembly
In the competitive landscape of low-volume PCB assembly, implementing best practices can lead to remarkable outcomes. By focusing on communication, prototyping, and lean manufacturing principles, businesses can set themselves up for success.
Effective Communication with PCB Assembly Manufacturers
Effective communication is the backbone of successful collaboration with PCB assembly manufacturers. Keeping an open line of dialogue can significantly enhance the outcomes of your project. Clear expectations and regular updates help ensure everyone is on the same page, which can lead to smoother workflows and quicker problem resolution. When both parties are aligned, it paves the way for innovative solutions and higher-quality results. Don’t underestimate the power of straightforward conversations; they can make a real difference in getting the job done right.
1.Establishing Clear Expectations: From the get-go, it’s essential to outline project specifications, timelines, and quality standards. By doing so, both parties can avoid misunderstandings that could derail the process. As the saying goes, “A stitch in time saves nine!”
2.Regular Updates and Feedback Loops: Schedule regular check-ins and updates throughout the assembly process. This keeps everyone aligned and allows for quick adjustments if needed. After all, it’s easier to steer a ship when you know where it’s headed!
3.Utilizing Collaborative Tools: Employ project management and communication tools to facilitate collaboration. Platforms like Slack or Trello can help keep everyone in sync and on the same page.
Communication Practice | Description |
Establishing Clear Expectations | Outline specifications, timelines, and quality standards |
Regular Updates and Feedback Loops | Maintain alignment and allow for adjustments |
Utilizing Collaborative Tools | Use platforms for seamless communication |
Utilizing Prototyping for Design Validation in Low-Volume PCB Assembly
Prototyping is your best friend when it comes to design validation. It allows for testing and refinement before full-scale production begins.
1.Rapid Prototyping Techniques: Leverage techniques like 3D printing or CNC machining to quickly create prototypes. These methods can save time and costs, allowing for faster iterations. It’s like having a dress rehearsal before the big show!
2.Iterative Testing: After creating a prototype, conduct thorough testing to identify any design flaws. This process should be iterative, enabling you to make necessary adjustments before the final assembly. Remember, “Measure twice, cut once!”
3.Gathering User Feedback: If possible, involve end-users in the prototyping phase to gather valuable feedback. Their insights can lead to improvements that might not have been considered initially.
Prototyping Practice | Description |
Rapid Prototyping Techniques | Use quick methods to create prototypes |
Iterative Testing | Test and refine designs before final assembly |
Gathering User Feedback | Involve users for insights and improvements |
Implementing Lean Manufacturing Principles in PCB Assembly Services
Adopting lean manufacturing principles can enhance efficiency and reduce waste in low-volume PCB assembly.
1.Streamlining Processes: Review and eliminate any unnecessary steps in the assembly workflow. This can lead to a more efficient operation, minimizing bottlenecks. As they say, “Less is more!”
2.Fostering a Culture of Continuous Improvement: Encourage team members to suggest improvements to processes. A culture that values feedback can lead to innovative solutions and enhancements over time.
3.Utilizing Just-In-Time Inventory: Implementing a Just-In-Time (JIT) inventory system can help reduce excess stock and associated costs. By aligning material orders with production schedules, businesses can optimize their operations.
Lean Principle | Description |
Streamlining Processes | Eliminate unnecessary steps for efficiency |
Fostering Continuous Improvement | Encourage team suggestions for enhancements |
Utilizing Just-In-Time Inventory | Align orders with production to reduce costs |
Why You Should Use a Cost Calculator for Low-Volume PCB Assembly?
In low-volume PCB assembly, managing costs effectively can really set a project apart. Utilizing a cost calculator helps streamline budgeting, ensuring manufacturers maintain a strong grip on their finances. These tools offer various advantages, like providing quick estimates and highlighting potential areas for savings. By integrating a cost calculator into the planning process, manufacturers can make informed decisions that align with their budgetary constraints. This approach not only aids in tracking expenses but also fosters better resource allocation. So, why not take the plunge? Let’s explore how these calculators can optimize your financial strategy and keep your projects on the right track!
Benefits of Cost Estimation Tools for PCB Assembly Services
Cost estimation tools are like your trusty roadmap in the complex journey of PCB assembly. They provide a clear picture of potential expenses, allowing companies to make informed decisions.
1.Transparency in Pricing: Cost calculators break down every component, from materials to labor, giving you a crystal-clear understanding of where your money is going. This transparency helps avoid nasty surprises down the road. As they say, “What you see is what you get!”
2.Informed Decision-Making: Armed with accurate estimates, businesses can compare options and choose the most cost-effective solutions. Whether it’s selecting materials or determining assembly methods, having the numbers at your fingertips makes all the difference.
3.Efficiency Gains: By using cost calculators, teams can quickly generate estimates, reducing the time spent on manual calculations. This efficiency means more time to focus on design and production. Time is money, after all!
Benefit | Description |
Transparency in Pricing | Clear breakdown of costs helps avoid surprises |
Informed Decision-Making | Facilitates comparison of options |
Efficiency Gains | Reduces time spent on calculations |
How Cost Calculators Improve Budget Management for Low-Volume PCB Assembly?
Using cost calculators is not just a smart move; it’s a savvy strategy for effective budget management. Here’s how they help:
1.Accurate Budget Forecasting: With reliable estimates, businesses can set realistic budgets. This ensures that they don’t overspend or underspend, keeping the financial ship sailing smoothly.
2.Scenario Analysis: Cost calculators often allow users to input different variables, such as order quantity and material choices. This enables scenario analysis, helping companies understand how changes in parameters affect overall costs. It’s like having a crystal ball for your budget!
3.Enhanced Collaboration: When everyone is on the same page regarding costs, teams can work together more effectively. Cost calculators foster communication between design, procurement, and production teams, ensuring that everyone understands the financial implications of their choices.
Improvement | How It Helps |
Accurate Budget Forecasting | Sets realistic spending expectations |
Scenario Analysis | Visualizes cost impacts of different choices |
Enhanced Collaboration | Promotes teamwork and understanding across departments |
Why Choosing Us as Your Low-Volume PCB Solutions Provider?
SMT&THT Low-Volume PCB Assembly
When it comes to low-volume PCB assembly, selecting the right partner can make all the difference. Here’s why choosing us is a smart move for your PCB assembly needs.
Comprehensive PCB Assembly Services Offered
We provide a wide range of PCB assembly services tailored specifically for low-volume projects. Our offerings are designed to meet diverse customer needs, ensuring that we cover all bases.
1.Tailored Solutions for Unique Needs: We understand that each project is unique. That’s why we offer customized PCB assembly solutions, from design to production. Whether you need specific components or a unique layout, we’ve got you covered. As they say, “If you can dream it, we can build it!”
2.Full-Service Capabilities: Our services include everything from PCB design and prototyping to final assembly and testing. This full-service approach means you won’t have to juggle multiple vendors—everything is handled under one roof. It simplifies your workflow and keeps things running like a well-oiled machine.
3.Advanced Technologies and Techniques: Utilizing state-of-the-art technology in our assembly processes, we ensure high precision and quality. We employ both Surface Mount Technology (SMT) and Through-Hole techniques, ensuring that we can handle any design complexity with ease.
Service Category | Description |
Tailored Solutions | Customizable services to meet specific project needs |
Full-Service Capabilities | Comprehensive handling from design to assembly |
Advanced Technologies | Use of modern techniques for precision and quality |
Proven Track Record and Client Testimonials in Low-Volume PCB Assembly
Our reputation speaks volumes, backed by a proven track record in the industry. Client testimonials highlight our commitment to quality and customer satisfaction.
1.Successful Project Examples: We have successfully delivered numerous projects across various sectors, including medical devices, consumer electronics, and automotive applications. One of our recent projects involved a healthcare client needing a complex circuit board for a diagnostic device. By working closely with them, we met their tight deadlines while ensuring top-notch quality. That’s what we call “knocking it out of the park!”
2.Client Satisfaction Stories: Our clients frequently share their positive experiences with our services. They appreciate our responsiveness and dedication to making adjustments based on their feedback. As one client noted, “Working with this team has been a breath of fresh air—they truly listen to our needs.”
3.Long-Term Partnerships: We strive to build lasting relationships with our clients. Many of our customers return for their next projects, knowing they can count on us for reliability and quality. Building trust is at the heart of our operations.
Client Feedback | Summary |
Successful Project Examples | Demonstrated ability to meet tight deadlines |
Client Satisfaction Stories | Responsive to feedback and adjustments |
Long-Term Partnerships | Focus on building lasting client relationships |
Choosing us as your low-volume PCB solutions provider means selecting a partner committed to your success. With our comprehensive services and proven track record, you can focus on what you do best—innovating and growing your business. Let’s team up and bring your vision to life!
The Difference Between Low Volume PCB Assembly and Prototype PCB Assembly
Grasping the distinctions between low-volume PCB assembly and prototype PCB assembly can make a world of difference for businesses aiming to fine-tune their production processes. Each assembly type caters to specific needs and stages of product development. Low-volume assembly focuses on smaller quantities, allowing for more customization and flexibility, making it perfect for initial product launches or limited runs. On the flip side, prototype assembly zeroes in on testing designs and functionalities before mass production kicks off. Understanding these differences helps companies choose the right path forward, ultimately leading to more efficient production and better product outcomes. So, if you’re looking to enhance your assembly strategy, dive deep into these distinctions to make informed choices!
Key Distinctions in Purpose and Application of PCB Assembly
Low-volume PCB assembly and prototype PCB assembly are not interchangeable; they cater to different needs within the electronics industry.
●Purpose and Objectives
Low-Volume PCB Assembly: This process is often utilized when companies require small quantities of circuit boards for limited production runs. This could include initial market testing or specific customer orders. The focus here is on delivering quality at a manageable cost, allowing businesses to gauge demand without committing to large-scale production.
Prototype PCB Assembly: This is typically the first step in bringing a new electronic product to life. Prototype assembly focuses on validating designs and testing functionality before mass production. It’s all about trial and error—getting it right the first time is key to saving time and resources later.
●Applications in Different Stages of Development
Low-volume assembly might be used for specialized devices or niche products that do not warrant large quantities. Think of a boutique gadget that caters to a specific audience.
Prototype assembly is often used in R&D settings, where engineers test various iterations of their designs. For instance, a tech startup might create several prototypes before launching their device to the public.
Assembly Type | Purpose | Typical Applications |
Low-Volume PCB Assembly | Quality production in small quantities | Limited product runs, niche markets |
Prototype PCB Assembly | Design validation and testing | R&D, initial product development |
Understanding the Production Processes in Low-Volume PCB Assembly
The production processes for low-volume PCB assembly are distinct from those used for prototypes, reflecting the differing objectives.
Streamlined Workflow: Low-volume PCB assembly emphasizes efficiency without sacrificing quality. Processes are designed to minimize waste while ensuring that each board meets rigorous standards. This includes using advanced assembly techniques that allow for flexibility in production.
Quality Control Measures: In low-volume production, rigorous testing protocols are essential. Each batch undergoes detailed inspections, ensuring that all components function as intended. For instance, a manufacturer might implement Automated Optical Inspection (AOI) to catch defects early, reducing rework and ensuring consistency.
Material Sourcing and Management: Material choices can vary significantly between low-volume and prototype assembly. While prototypes may utilize a broader range of materials for testing, low-volume production typically focuses on reliable sources to ensure consistency in the final product. This often means negotiating with suppliers for optimal pricing and availability.
Process Element | Low-Volume PCB Assembly | Prototype PCB Assembly |
Workflow | Streamlined for efficiency | Iterative for design testing |
Quality Control | Rigorous testing and inspections | Functional testing for design validation |
Material Sourcing | Reliable suppliers for consistency | Varied materials for testing purposes |
Key Technologies Enhancing Low-Volume PCB Assembly
In the competitive landscape of electronics manufacturing, leveraging the right technologies can significantly enhance low-volume PCB assembly. Here’s a closer look at the key advancements shaping this space.
Automation in PCB Assembly Processes
Automation is transforming the landscape of PCB assembly, making it faster and more efficient.
Robotic Assembly Systems: Automated systems reduce human error and increase precision. Robotic arms can handle delicate components with ease, ensuring consistent placement on circuit boards. For example, a robotic pick-and-place machine can position thousands of components per hour, drastically reducing assembly time.
Conveyor Systems for Workflow Efficiency: Implementing automated conveyor systems streamlines the production line, allowing for smoother transitions between assembly stations. This reduces bottlenecks and enhances overall productivity, ensuring that production schedules are met without a hitch.
Real-time Data Monitoring: Advanced automation tools offer real-time tracking of production metrics. This data enables quick adjustments to processes, ensuring optimal output. For instance, if a certain machine is lagging, operators can quickly reroute resources to maintain efficiency.
Automation Technology | Benefits | Example |
Robotic Assembly Systems | Increased precision and speed | Robotic pick-and-place machines |
Conveyor Systems | Streamlined workflow | Automated assembly lines |
Real-time Data Monitoring | Immediate adjustments for efficiency | Production metric dashboards |
Advanced Inspection Technologies for PCB Assembly
Quality control is non-negotiable in PCB assembly. Advanced inspection technologies ensure that each board meets stringent standards.
Automated Optical Inspection (AOI): AOI systems use high-resolution cameras to inspect PCBs for defects. They can quickly identify misplaced components, soldering issues, and other common problems. This technology minimizes the risk of defective products reaching the market.
X-ray Inspection for Complex Assemblies: For assemblies with intricate designs, X-ray inspection allows for a detailed view of solder joints and hidden components. This is particularly useful for double-sided boards where visual inspection is insufficient.
Functional Testing Equipment: Implementing functional tests post-assembly ensures that the PCB operates as intended. Testing setups can simulate real-world conditions, helping to catch issues before products are shipped.
Inspection Technology | Purpose | Application |
Automated Optical Inspection | Detecting visual defects | Pre-shipment quality assurance |
X-ray Inspection | Inspecting complex solder joints | Double-sided PCB assemblies |
Functional Testing Equipment | Ensuring operational integrity | Final product validation |
Software Solutions for PCB Design and Production Management
The adoption of software solutions significantly enhances the management of PCB assembly processes. These tools streamline workflows, improve communication, and enable better tracking of components and production stages. By integrating software, manufacturers can gain real-time insights, which lead to quicker decision-making and increased accuracy. For instance, using project management software helps teams coordinate tasks efficiently, while inventory management systems ensure materials are available when needed.
PCB Design Software: Modern design tools allow engineers to create and modify PCB layouts efficiently. They provide features like 3D visualization and simulation to test designs before production. For example, software like Altium Designer streamlines the entire design process, reducing time from concept to prototype.
Production Management Software: Implementing ERP (Enterprise Resource Planning) systems helps manage inventory, scheduling, and workflows seamlessly. This ensures that materials are available when needed, reducing downtime and optimizing resource allocation.
Collaboration Tools: Clear communication among teams makes a huge difference in project success. Using cloud-based platforms fosters real-time collaboration, allowing for quick design revisions and timely feedback that keeps projects moving forward. These tools help everyone stay on the same page, reducing misunderstandings and streamlining workflows.
Software Solution | Function | Benefits |
PCB Design Software | Creating and simulating PCB layouts | Faster design cycles |
Production Management Software | Managing resources and workflows | Increased operational efficiency |
Collaboration Tools | Facilitating team communication | Enhanced project coordination |
Selecting the Right PCB Assembly Partner in China
Low-Volume PCB Assembly Services
Selecting the right PCB assembly partner in China can make all the difference. A trustworthy manufacturer not only addresses technical specifications but also helps manage costs and ensures timely deliveries. It’s not just about checking off boxes; it’s about finding a partner that aligns with your project goals. When you work with a reliable manufacturer, you can focus on innovation and growth instead of worrying about production hiccups. So, do your homework and choose wisely to set your projects up for success!
Criteria for Choosing a Low-Volume PCB Assembly Manufacturer
When selecting a low-volume PCB assembly manufacturer, several key factors should be considered.
●Industry Experience and Customer Reviews
Industry Experience: Choose for manufacturers with extensive experience in the PCB assembly industry. They tend to handle complex designs and demands more effectively. For example, a company with over 10 years of experience often accumulates valuable knowledge in technology and processes.
Customer Reviews: Reading customer reviews provides genuine feedback, helping you assess the quality and reliability of the manufacturer’s services. Platforms for third-party reviews allow you to gauge customer satisfaction and experiences.
Criteria | Description | Example |
Industry Experience | Provides background on technical capabilities and solutions | 10+ years of industry experience |
Customer Reviews | Genuine feedback ensures service quality | Customer ratings on third-party platforms |
●Proven Case Studies in Low-Volume PCB Assembly
Successful Case Studies: Understanding the manufacturer’s previous successful projects can help you judge their capability and adaptability. For instance, a manufacturer that successfully delivered customized PCBs for a startup demonstrates flexibility and professionalism in low-volume production.
Showcasing Custom Solutions: Review how they handled specific customer needs, especially projects that faced challenges, to better assess their responsiveness and technical innovation.
Evaluation Method | Content | Significance |
Online Reviews | Visit the website for service offerings and capabilities | Reflects company strength and reputation |
Social Media Interaction | Observe social media performance and customer engagement | Understand customer service attitude |
Research Strategies for Reliable PCB Assembly Manufacturers
To find reliable PCB assembly manufacturers, employ effective research strategies.
●Networking and Recommendations
Industry Networking and Recommendations: Utilize industry events, trade shows, and professional social platforms to build connections. Engaging with industry peers can provide trusted recommendations, helping you narrow down your options.
Peer Evaluations: Consult with other companies or industry experts for firsthand feedback. For example, asking questions in industry forums can yield diverse opinions.
Strategy | Description | Example |
Industry Networking | Build connections for reliable information | Attend industry trade shows and social events |
Peer Evaluations | Obtain feedback from industry professionals | Inquire on industry forums for recommendations |
●Evaluating Online Presence
Online Reviews and Information: Visit the manufacturer’s website to understand their service offerings, technical capabilities, and customer cases. A professional website often reflects a company’s strength and reputation.
Social Media and Customer Interaction: Observe the manufacturer’s performance on social media and their interaction with customers, which can give insights into their customer service attitude and brand image. Companies that actively respond to customer feedback usually prioritize customer experience.
Evaluation Method | Content | Significance |
Online Reviews | Visit the website for service offerings and capabilities | Reflects company strength and reputation |
Social Media Interaction | Observe social media performance and customer engagement | Understand customer service attitude |
Sum Up
The Ultimate Choice for Low-Volume PCB Assembly Services in China
When it comes to selecting a partner for low-volume PCB assembly in China, making the right choice can set the stage for your project’s success. With a myriad of options available, it’s essential to evaluate manufacturers based on experience, customer reviews, and proven success in the industry.
So, Ready to take the next step? If you’re looking for a partner that understands your needs and can help you navigate the complexities of low-volume PCB assembly, don’t hesitate to reach out. Let’s work together to turn your ideas into reality!
FAQs about Low-Volume PCB Assembly in China
What Defines Low-Volume PCB Assembly?
Low-volume PCB assembly typically refers to production runs that consist of fewer than 1,000 units. This method is ideal for testing new designs or introducing products to the market without committing to large-scale production.
How Can I Ensure Quality in Low-Volume PCB Assembly?
To ensure quality, collaborate closely with your manufacturer. Ask about their quality assurance processes and testing protocols. Regular communication and updates throughout the assembly process can help identify and resolve issues early.
What Are the Costs Associated with Low-Volume PCB Assembly?
Costs can vary based on factors such as material choices, assembly techniques, and project complexity. Using a cost calculator can help you estimate expenses accurately and make informed decisions.
Can I Make Changes to My Design During the Assembly Process?
Yes, many manufacturers accommodate design changes even during the assembly process, particularly for low-volume orders. However, it’s essential to communicate any changes as early as possible to minimize disruptions.
What Materials Are Commonly Used in Low-Volume PCB Assembly?
Common materials include FR-4 for the substrate, along with various types of copper for traces and components. Depending on your project’s requirements, you may also consider specialized materials for specific applications.
How Long Does the Low-Volume PCB Assembly Process Take?
Turnaround times can vary, but many manufacturers offer quick lead times for low-volume orders, often completing projects within a few weeks. Factors such as complexity, component availability, and manufacturing capabilities can influence the timeline.
Advanced PCB Assembly
PCBs We Can Assemble
- Min size: PCB whose width/length is less than 30mm should be panelized.
- Max size: single board 500mm*400mm | panel board 310mm*410mm.
- Layer Count: 1-60 layers (1-20 layers for mass production).
- Copper Thickness: 1/2oz – 17oz.
- PCB Types: Rigid PCBs, Flex PCBs, Rigid Flex PCBs, Rogers PCBs, Ceramic PCBs, etc.
- Surface Finishes: Lead/Lead-free HASL, ENIG, ImSilver, OSP, Gold plated, Immersion Gold, etc.
Components We Can Assemble
- SMT sizes: 01005, 0201 or larger.
- BGA pitch: 0.35mm or greater.
- BGA Ball count: 2 – 50.
- Fine pitch: 0.4mm or greater.
- WLCSP pitch: 0.35mm or greater.
- Components Height: 0.1mm – 12mm.
- BGA, micro-BGA, POP, CSP, LGA package, Flip chip, Hard metric connectors, Cable & wire, etc.
- Min. Components Spacing: 0.20mm for SMT parts, no specific demand for Thru-hole parts.
Custom PCB Assembly Capabilities
- Quick Turn.
- IPC III standard compliant.
- Prototype Quantities to Production Quantities.
- Single PCB Assembly and PCB Panel Assembly.
- Single and Double-sided PCB Assembly.
- Leaded Assembly, Lead-free or RoHS Compliant Assembly and No-clean Process Assembly.
- SMT Assembly, Thru-hole (DIP) Assembly, and Combo of SMT and Thru-hole Assembly.
- Consigned PCB Assembly, Partial consigned PCB Assembly and Full turnkey PCB Assembly.