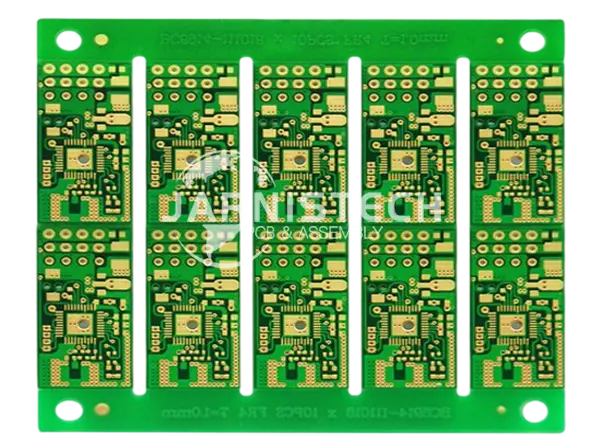
The world of electronics is constantly evolving, and the need for high-performance materials is more critical than ever. As electronic devices become smaller, faster, and more powerful, the demand for reliable thermal management solutions has surged. One such solution that has gained significant attention is High TG PCB (Thermal Glass Transition) technology. These printed circuit boards (PCBs) offer unmatched performance when it comes to thermal and mechanical properties, making them an essential component in the design and manufacturing of advanced electronics.
What is High TG PCB?
High TG PCBs refer to printed circuit boards engineered with a high glass transition temperature (TG). This is the temperature at which the material transitions from a rigid state to a rubbery one. For conventional boards, TG values range between 130°C to 150°C, but High TG PCBs push this boundary to 170°C and beyond, creating a robust foundation for devices exposed to thermal stress.
Core Characteristics of High TG PCBs
●Thermal Durability:These boards resist deformation and maintain electrical integrity even when temperatures peak during heavy-duty operations.
●Enhanced Reliability: By lowering the coefficient of thermal expansion (CTE), High TG PCBs prevent mechanical stress on components, ensuring extended operational lifespans.
Why High TG PCBs Are the Solution?
Thermal management is a significant challenge in modern electronics. As devices become smaller and more powerful, the amount of heat they generate increases, pushing the limits of traditional circuit board materials. The ability to effectively manage heat is paramount in maintaining system reliability, preventing thermal failure, and ensuring the longevity of electronic components. For applications that require superior thermal performance, High TG PCBs offer a clear advantage by withstanding higher temperatures than standard materials. This section explores the importance of thermal stress and how High TG PCBs provide an effective solution in demanding environments.
The Impact of Thermal Stress on Electronic Devices
Thermal stress is one of the most common causes of failure in electronic components. As power demands increase, particularly in high-frequency and high-power applications, the heat generated by these components rises. When the PCB fails to dissipate this heat effectively, the result can be circuit failure, reduced lifespan, and even catastrophic breakdowns.
High-temperature conditions can degrade the performance of standard FR4 PCBs (a common material for circuit boards), which have a lower glass transition temperature (TG) — around 130°C. In contrast, High TG PCBs are designed with materials that can withstand temperatures up to 180°C or higher, making them ideal for environments with elevated thermal stresses. The higher TG of these materials allows them to maintain mechanical integrity and electrical functionality under extreme conditions.
Thermal Challenges in Power Electronics
Power electronics are at the heart of many modern innovations, from electric vehicles to renewable energy solutions. We constantly face the challenge of dissipating heat in circuits that deal with high currents. As these systems evolve, so does the need for better thermal management. High TG PCBs are a solution designed specifically to meet these demands.
The following table showcases how High TG PCBs improve thermal performance in specific power electronics applications.
Application | Typical Power Consumption | Thermal Challenges | Solution Using High TG PCBs |
Electric Vehicle Battery | 50 kW – 100 kW | Overheating, power loss | Enhanced heat dissipation with High TG |
Power Converters | 10 kW – 20 kW | Excessive heat in components | High thermal resistance materials |
Solar Inverters | 5 kW – 10 kW | Overheating of capacitors | Integrated thermal vias and heat sinks |
High TG PCBs excel in these applications by offering a higher thermal conductivity, enabling faster heat dissipation and improving device longevity.
How High TG PCBs Are Designed to Overcome Thermal Limitations?
The design of High TG PCBs centers around the use of specialized materials that can handle higher thermal loads without compromising performance. From material selection to layer stack-up, every aspect of the design is optimized for heat management. One of the most effective ways to handle heat is by using thermal vias and heat sinks to draw heat away from components. These materials and techniques ensure that the electrical performance of the PCB remains intact even under extreme conditions.
Beyond material selection, the PCB design process for high-performance applications involves careful consideration of the layer stack-up, trace widths, and power distribution networks. These design techniques optimize heat distribution and ensure that heat-sensitive components receive proper cooling.
The table below compares the typical design considerations for High TG PCBs and standard FR4 PCBs in handling thermal loads.
Design Element | Standard FR4 PCB | High TG PCB |
Glass Transition Temperature (TG) | 130°C | 170°C – 220°C |
Thermal Conductivity | Moderate | High (Improved via materials) |
Material Used | Epoxy resin | Ceramic-filled epoxy, Polyimide |
Thermal Via Integration | Not common | Common |
Power Handling Capacity | Low to Moderate | High |
By incorporating high-performance resins and advanced thermal vias, High TG PCBs are able to better manage heat in high-power applications, such as electric vehicles and renewable energy systems. These systems generate significant heat, so efficient heat dissipation is key to maintaining reliable performance. The use of thermal vias allows the heat to be transferred away from sensitive areas, reducing the risk of overheating and failure.
Example Case: How High TG PCBs Save Lives in Medical Devices?
In fields like medical technology, precision and reliability cannot be compromised. High TG PCBs help keep critical systems, such as pacemakers and implantable insulin pumps, working seamlessly even in fluctuating temperatures. These devices must be able to handle the heat generated by internal circuits while maintaining electrical insulation to ensure patient safety.
Medical Device | Temperature Range | Thermal Challenge | High TG PCB Benefits |
Pacemakers | 35°C – 40°C | Heat generation from battery and circuits | Stable performance at higher temperatures |
Implantable Insulin Pumps | 30°C – 37°C | Overheating risks affecting microelectronics | Excellent heat dissipation, extended lifespan |
Neural Stimulation Systems | 25°C – 45°C | High-frequency signals creating heat | High thermal tolerance and long-term reliability |
In these medical applications, the ability of High TG PCBs to manage heat ensures that these devices remain functional, safe, and durable, which is a matter of life and death.
The Journey of a High TG PCB: From Design to Manufacturing
The creation of High TG PCBs is a meticulous process that requires careful planning, specialized knowledge, and cutting-edge manufacturing techniques. Whether it’s a high-power automotive system or a complex power amplifier, the journey starts long before the first component is soldered onto the board. The goal is to ensure that the PCB can effectively handle the thermal challenges posed by modern electronic systems while maintaining the electrical integrity needed for optimal performance.
Every aspect of the design and manufacturing process must be fine-tuned to withstand thermal stress and high operating temperatures. From the choice of materials to the design of the layers and components, each decision impacts the ability of the PCB to perform reliably in harsh environments. This section takes a deep dive into the design process, advanced manufacturing techniques, and best practices for OEMs when working with High TG PCBs.
Understanding the Design Process for High TG PCBs
Designing a High TG PCB begins with a clear understanding of the specific requirements of the application. The first order of business is tackling thermal management, especially in high-power or high-frequency environments, where temperatures can climb rapidly. For instance, applications like power amplifiers, automotive power systems, and server-grade computing equipment all produce significant amounts of heat, which must be kept under control to ensure reliable performance. Effective thermal management is woven into the PCB’s design, incorporating materials and features such as thermal vias, heat sinks, and high-performance resins, ensuring the board can withstand demanding conditions and continue to function reliably over time. By factoring in these needs from the start, we can ensure the final product can handle the heat without compromising performance.
Here are the core aspects engineers focus on during the design phase:
1. Thermal Expansion and Material Behavior-
Thermal expansion refers to the way materials expand or contract with changes in temperature. It’s important for the PCB’s material properties to match the expansion rates of the components it houses, to prevent stress or warping under extreme heat. Engineers use polyimide or ceramic-filled epoxy materials in High TG PCBs to ensure minimal thermal expansion while maintaining the strength and electrical conductivity needed for demanding applications.
2. Layer Stack-up Configurations-
The stack-up is one of the most important decisions in PCB design, especially when high heat is involved. By choosing the right configuration, we can ensure efficient heat dissipation and mechanical stability. For high-performance systems such as electric vehicle inverters or medical imaging devices, multiple layers are often employed to channel heat away from sensitive areas, which maintains the overall functionality of the system.
3. Solder Mask and Surface Finishes-
The solder mask and surface finishes used on High TG PCBs must also be chosen with heat management in mind. A poor finish can result in excess heat generation at the solder joints, which can compromise the entire system’s performance. The use of Nickel-Gold plating or immersion silver finishes provides better thermal performance and reduces the risk of component failure due to thermal stress.
Once these aspects are considered, electromagnetic simulation tools are used to validate the design and ensure that the board will perform as expected under various thermal conditions. Engineers also run thermal analysis to identify potential hotspots where heat might accumulate and make adjustments accordingly.
Example:
Design Element | Standard FR4 | High TG PCB |
Thermal Expansion Coefficient | Higher, more prone to warping | Lower, better for high heat environments |
Material Used | Epoxy-based | Polyimide, Ceramic-filled Epoxy |
Layer Configurations | Simple 1-2 layer boards | Multi-layer with heat dissipation features |
Solder Mask Material | Standard epoxy | High-temperature resistant solder mask |
Surface Finish | OSP (Organic Solderability Preservative) | Immersion Silver or Nickel-Gold |
Advanced Manufacturing Techniques for High TG PCBs
When it comes to manufacturing High TG PCBs, traditional methods can no longer handle the demanding requirements of modern electronics. Advanced PCB fabrication techniques are necessary to ensure that High TG PCBs can withstand extreme thermal conditions while delivering the required performance.
Some electronics Manufacturers often use several advanced methods to ensure that High TG PCBs meet the high standards required for power electronics, automotive systems, and other demanding applications:
1. HDI (High-Density Interconnect) Technology-
One of the most advanced techniques used in High TG PCB manufacturing is HDI technology, which allows for higher density component placement, smaller vias, and improved thermal paths. By using microvias and laser drilling, manufacturers can create High TG PCBs with more efficient thermal dissipation capabilities and better component integration.
2. Multilayer Construction for Thermal Efficiency-
To ensure the PCB is capable of handling high thermal loads, multilayer constructions are often employed. These multilayer PCBs use a combination of ceramic-filled substrates and polyimide layers to improve heat resistance and prevent damage to critical components.
3. Advanced Circuit Bonding Materials-
During the soldering process, High TG PCBs require specialized circuit bonding materials. These materials must withstand extreme temperatures without degrading or causing reliability issues. PCB Manufacturers use high-temperature-resistant resins and epoxies to ensure a stable bond that will not fail under thermal stress.
Additionally, high-quality thermal cycling tests and high-temperature aging tests are conducted to ensure the High TG PCB can maintain its performance over extended periods and under varying temperature conditions.
Example:
Manufacturing Technique | Standard FR4 PCBs | High TG PCBs |
HDI (High-Density Interconnect) | Not commonly used | Key for smaller, complex designs |
Thermal Cycling Tests | Occasional testing | Extensive, rigorous testing to ensure reliability |
Ceramic-filled Substrates | Not used | Common for better heat distribution |
Laser Drilling for Microvias | Rarely used | Standard for high-density, efficient thermal paths |
Materials and Manufacturing Techniques for High TG PCBs
Designing and manufacturing High TG PCBs is a multi-step process that starts with the selection of materials and ends with rigorous testing to ensure that the boards can handle extreme thermal conditions. In this section, we will explore the materials used in High TG PCBs, the lamination process that strengthens their durability, and the quality control techniques that guarantee their performance.
The materials chosen for High TG PCBs are critical in determining the board’s ability to withstand high temperatures without compromising its electrical performance. Alongside material selection, the manufacturing process and quality assurance steps also play a massive role in ensuring reliability under extreme heat and mechanical stress.
Key Materials Used in High TG PCBs
1. High TG FR4-
FR4 is one of the most widely used materials for printed circuit boards, but its properties change significantly when we’re dealing with High TG PCBs. Standard FR4 has a glass transition temperature (TG) around 130°C, but High TG FR4 can withstand temperatures ranging from 170°C to 180°C or even higher, depending on the resin formulation. This material retains its strength and stability at these elevated temperatures, which is crucial in applications where high-power components generate substantial heat. The high-performance resin system used in High TG FR4 also contributes to better thermal cycling resistance, making it ideal for environments with fluctuating temperatures, such as automotive or industrial electronics.
2. Polyimide-
Polyimide is another material commonly used in High TG PCBs, especially for applications requiring even higher temperature resistance. With a TG upwards of 250°C, polyimide provides the necessary thermal stability for ultra-high-performance electronics that need to withstand extreme operating environments. Polyimide is known for its outstanding electrical properties and is used for flexible circuit boards, making it particularly valuable in applications such as aerospace, telecommunications, and military systems.
3. Ceramic Materials-
Ceramic-filled substrates are increasingly used in High TG PCBs due to their excellent thermal conductivity and low thermal expansion coefficients. By integrating ceramic particles into the resin, these materials can dissipate heat efficiently, reducing the risk of thermal damage to sensitive components. These materials are particularly useful in high-power electronics, such as power converters, LED lighting systems, and power electronics in electric vehicles. Ceramic substrates also tend to have better rigidity and mechanical strength, making them suitable for applications that require long-term durability under high heat.
Example of Material Performance
Material | Glass Transition Temperature (TG) | Thermal Conductivity | Common Applications |
High TG FR4 | 170°C – 180°C | Moderate | Automotive, industrial, power systems |
Polyimide | 250°C+ | Low to Moderate | Aerospace, military, high-frequency systems |
Ceramic-filled FR4 | 180°C – 200°C | High | Power converters, LED systems |
Lamination Process in High TG PCB Production
The lamination process in High TG PCB production is key to ensuring the durability and heat resistance of the board. This step involves bonding multiple layers of material together, under high heat and pressure, to create a solid, reliable structure. This stage is particularly intricate for High TG boards, as the materials used must be aligned and bonded in a way that supports their ability to withstand high operating temperatures and mechanical stress. By ensuring even pressure distribution and controlled thermal application, this process helps create PCBs that perform consistently in demanding applications, such as aerospace systems and high-frequency industrial equipment.
1. Layer Formation-
The process begins with the preparation of the materials that will form each layer of the PCB. For High TG PCBs, this often involves layering polyimide, ceramic-filled FR4, or High TG FR4 depending on the board’s application. The layers are precisely aligned to ensure that the thermal and electrical properties are evenly distributed across the board.
2. Prepreg Application-
Prepregs (pre-impregnated materials) are commonly used in the lamination process. These are materials, such as resin-impregnated fiberglass, that have been partially cured and are then layered with other materials to form a multilayer structure. The use of prepreg ensures uniform bonding and increased thermal stability in High TG PCBs.
3. Curing Process-
Once the layers are stacked, the board is placed in a press and subjected to heat and pressure. This curing process allows the resin to flow and bond the layers together while solidifying. The curing time and temperature are carefully controlled to prevent the High TG PCB from warping or delaminating. This process ensures that the High TG PCB can withstand high thermal stress without losing its mechanical integrity.
4. Quality Check of Laminated Structure-
After lamination, the PCB is thoroughly checked for defects, such as air pockets, voids, or delaminations, which could compromise its thermal and electrical performance. Advanced X-ray inspection and ultrasonic testing are often employed to identify any potential issues in the lamination process.
Example of Lamination Process for High TG PCBs
Step | Description | Result |
Layer Formation | Multiple layers of polyimide, ceramic-filled FR4, or High TG FR4 materials are stacked. | Forms the structural foundation of the PCB |
Prepreg Application | Pre-impregnated fiberglass or resin is applied to layers. | Ensures uniform bonding and thermal stability |
Curing Process | The board is heated and pressed to bond layers and solidify the resin. | Forms a solid, heat-resistant structure |
Quality Check | The board is inspected for defects using X-ray and ultrasonic testing. | Ensures that the High TG PCB is structurally sound and thermally stable |
Quality Control in High TG PCB Manufacturing
Quality control (QC) in High TG PCB manufacturing is an integral part of ensuring that the final product can reliably perform in high-temperature, high-stress environments. Given the thermal demands placed on High TG PCBs, every step of the manufacturing process must be carefully monitored to detect issues that could lead to performance failure under extreme conditions.
1. Thermal Testing-
Once the PCB is manufactured, it undergoes a series of thermal tests to simulate the conditions it will face in real-world applications. These tests often include thermal cycling, where the PCB is subjected to rapid temperature changes to ensure that it can withstand thermal expansion and contraction without cracking or warping.
2. Visual Inspection-
A visual inspection is carried out to check for physical defects such as surface damage, misalignment, or improper soldering. This inspection is typically conducted using high-powered microscopes or automated optical inspection (AOI) systems that can detect minute defects that could lead to failures under thermal stress.
3. Electrical Performance Testing-
After passing thermal tests, the High TG PCB is subjected to electrical performance testing. This ensures that the board maintains proper signal integrity and electrical functionality even under high temperatures. High-frequency signal tests and impedance testing are common for high-speed applications.
4. Aging and Stress Tests-
Aging tests are performed to simulate long-term usage of the High TG PCB under extreme conditions. These tests help ensure that the material and electrical components maintain their functionality even after years of exposure to high temperatures and stresses.
Quality Control Testing:
Test | Description | Purpose |
Thermal Cycling | The PCB is subjected to temperature extremes and rapid changes. | Tests for thermal expansion and durability |
Visual Inspection | High-powered microscopes or AOI systems are used for defect detection. | Ensures physical integrity and manufacturing accuracy |
Electrical Performance Testing | The PCB is tested for signal integrity and impedance at high speeds. | Verifies that the PCB can handle high-frequency signals |
Aging and Stress Tests | Long-term exposure to elevated temperatures and mechanical stress. | Simulates the PCB’s lifespan under extreme conditions |
High TG PCBs in Thermal Management: The Role They Play
High TG PCBs excel in thermal management, making them a go-to option for electronic systems that operate under high-temperature conditions or experience rapid temperature changes. Their robust design ensures stable performance and durability, even in the face of challenging thermal demands. Let’s explore how these advanced PCBs mitigate heat-related issues and support reliable performance.
Thermal Stability and High Temperature Resistance in High TG PCBs
One of the standout characteristics of High TG PCBs is their ability to maintain stability when exposed to elevated temperatures. For systems like power amplifiers, LED lighting, or automotive electronics, which can reach extreme operating temperatures, this feature is invaluable.
Why Thermal Stability Matters-
●Resistance to Deformation: High TG materials, such as High TG FR4 or ceramic-filled substrates, maintain their mechanical properties and prevent warping when temperatures soar above 170°C.
●Improved Heat Dissipation: These PCBs leverage superior thermal conductivity, enabling heat to disperse evenly and avoid localized hotspots.
Thermal Testing Results for High TG PCBs-
Material | Glass Transition Temperature (TG) | Max Continuous Temp | Thermal Expansion (Z-axis) |
Standard FR4 | 130°C | 110°C | 4.0% |
High TG FR4 | 170°C | 150°C | 2.2% |
Ceramic Substrate | 260°C | 230°C | 0.8% |
In LED modules used for automotive headlights, heat buildup can affect performance and longevity. High TG PCBs stabilize the operation by providing consistent thermal resistance, ensuring brighter and more reliable light output over time.
How High TG PCBs Prevent PCB Failure Due to Heat?
Heat-induced failure is a nightmare for PCB designers, as it can cause cracking, delamination, and signal degradation. High TG PCBs are specifically engineered to counteract these effects through enhanced thermal conductivity and dimensional stability.
Mechanisms That Prevent Heat-Related Failures-
●Low Dielectric Loss: These PCBs reduce electrical energy loss as heat, maintaining consistent signal integrity even at higher temperatures.
●Strong Bonding Layers: Special adhesives and prepregs in High TG PCBs ensure that layers remain bonded despite thermal cycling, reducing the risk of delamination.
●Enhanced Conductivity Pathways: By using copper layers with optimized thickness, High TG PCBs ensure efficient thermal transfer, directing heat away from sensitive components.
Failure Rate Comparison: High TG vs. Standard PCBs
Temperature Range (°C) | Standard PCBs: Failure Rate | High TG PCBs: Failure Rate |
100–130°C | 25% | 5% |
130–170°C | 50% | 10% |
170–200°C | 90% | 20% |
This demonstrates that High TG PCBs significantly reduce the likelihood of thermal stress failures, keeping circuits humming even in the most demanding environments.
Low Coefficient of Thermal Expansion (CTE) in High TG PCBs
Thermal expansion can wreak havoc on PCBs, especially in multilayer designs with high-density interconnects. A low coefficient of thermal expansion (CTE) minimizes the mismatch between PCB materials and components, ensuring dimensional stability.
How Low CTE Improves PCB Performance-
●Dimensional Accuracy: With a low CTE, High TG PCBs resist expansion and contraction during temperature fluctuations, preventing cracks or misalignments.
●Enhanced Mechanical Strength: A stable Z-axis expansion profile protects plated through holes (PTHs) and vias, ensuring reliable connections across layers.
CTE Comparison: High TG vs. Standard PCBs
PCB Type | CTE (Z-axis) | Thermal Cycling Resistance |
Standard FR4 | ~4.0% | Moderate |
High TG FR4 | ~2.2% | High |
Ceramic Hybrid | ~0.8% | Exceptional |
In satellite communication systems, RF circuits demand stable impedance to ensure accurate signal transmission, especially under fluctuating temperatures. High TG PCBs, characterized by their low coefficient of thermal expansion (CTE), minimize impedance variability caused by thermal stress. This stability is particularly valuable in maintaining consistent signal integrity during the rapid temperature changes experienced in space environments. By reducing the likelihood of thermal drift, these boards support the precise alignment and reliability needed for complex satellite transmissions, ensuring consistent performance across extreme conditions.
High TG PCBs for High-Speed and High-Frequency Applications
When designing high-speed and high-frequency applications, such as 5G networks, Internet of Things (IoT) devices, and advanced communication systems, signal integrity is a top priority. These devices rely on High TG PCBs to maintain robust performance, minimize signal degradation, and reduce noise interference. With their specialized thermal and electrical properties, High TG PCBs are increasingly recognized for their ability to enhance the reliability and efficiency of circuits operating at ultra-high speeds and frequencies.
In this section, we will dive into how High TG PCBs help with signal integrity, impedance control, and reduced signal loss in applications like 5G and RF/microwave circuits.
Enhancing Signal Integrity with High TG PCBs
Signal degradation is one of the most common issues in high-speed data transmission, especially in environments like 5G and IoT applications. As the demand for faster and more reliable connections increases, High TG PCBs offer a unique solution. Their superior thermal stability and electrical performance help to mitigate common problems such as signal attenuation and crosstalk, ensuring clean, high-speed transmission.
How High TG PCBs Address Signal Degradation:
●Improved Material Stability-
High TG PCBs are designed to maintain their structural and electrical integrity even when exposed to high temperatures. Their impressive thermal resistance minimizes the risk of material expansion or contraction, which could otherwise disrupt signal pathways. For high-frequency applications, where signals are particularly sensitive to environmental changes, this stability ensures consistent transmission without distortion.
●Lower Dielectric Loss-
The dielectric constant of materials used in High TG PCBs is generally lower compared to traditional FR4, which helps reduce signal loss as the signal travels through the board. Lower dielectric loss translates into better signal integrity, ensuring data is transmitted without significant attenuation or distortion.
●Enhanced Thermal Management-
As 5G and IoT devices push performance boundaries, their increased power demands often result in higher operational temperatures. High TG PCBs effectively address this by distributing heat across the board to prevent localized hotspots, ensuring that components work harmoniously without interference. By keeping the board’s temperature in check, these PCBs help preserve signal clarity, minimizing issues like noise or distortion that can disrupt device functionality. It’s like giving your electronics a reliable cooling system to keep them in top shape, even under heavy workloads.
Example of High TG PCBs in 5G Applications
Device | Challenge | Solution with High TG PCB |
5G Base Stations | High-speed signal transmission with minimal loss. | High TG PCBs provide low dielectric loss, maintaining signal integrity. |
IoT Sensors | Maintaining accurate data transmission over long distances. | High TG PCBs ensure minimal signal degradation over long-range transmissions. |
Impedance Control in High-Speed Circuits Using High TG PCBs
In high-speed RF and microwave circuits, ensuring consistent impedance is the secret sauce to achieving reliable signal flow. Mismatched impedance can act like a speed bump for signals, leading to reflections, energy loss, and interruptions in data transmission. These effects become especially problematic at high frequencies, where even the slightest deviation can disrupt the circuit’s overall performance.
How High TG PCBs Achieve Consistent Impedance Control:
●Precise Trace Design-
In High TG PCBs, precise control over the trace width and the spacing between the traces is necessary to ensure that the PCB maintains the required impedance for high-speed and high-frequency signals. The high-temperature properties of High TG PCBs ensure that the traces maintain their consistency during the PCB’s operational life, especially in environments where temperature fluctuations are common.
●Material Properties and Consistency-
Materials used in High TG PCBs, such as polyimide and ceramic-filled resins, have low thermal expansion coefficients, ensuring that the PCB’s impedance remains stable. This consistency prevents the impedance variations that could lead to reflections and signal loss.
●Controlled Impedance Layers-
High TG PCBs often include specific controlled impedance layers for high-frequency applications. By using materials that offer stable electrical characteristics and integrating precise fabrication techniques, the PCB ensures that the impedance of the signal path is tightly controlled, even in the most demanding applications.
Impedance Control in RF Circuits:
Application | Challenge | Solution with High TG PCB |
Microwave Circuits | Maintaining signal clarity over long distances. | High TG PCBs maintain consistent trace impedance, reducing reflections. |
RF Amplifiers | Impedance mismatch causing signal distortion. | Controlled impedance design in High TG PCBs ensures high signal fidelity. |
Reduced Signal Loss and Crosstalk in High-Frequency Applications
In high-frequency applications, such as 5G communication and radar systems, signal loss and crosstalk are two of the most pressing challenges. Signal loss results in reduced power transfer, while crosstalk leads to interference between neighboring traces. Both of these issues can cause significant performance degradation, especially in densely packed circuits where signals operate at high speeds and frequencies.
How High TG PCBs Minimize Signal Loss and Crosstalk:
●Lower Signal Loss-
High-frequency signals experience attenuation when traveling through the PCB, especially when the PCB material exhibits higher dielectric losses. High TG PCBs use materials with low dielectric constants and low loss factors to minimize signal degradation over distance. This ensures that the signals maintain strength and clarity even as they traverse long paths on the board.
●Separation of Signal Paths-
By maintaining precise trace width and spacing, High TG PCBs reduce the possibility of crosstalk, where signals from one trace interfere with others nearby. This is crucial for circuits that carry high-frequency signals, where even the smallest electromagnetic interference (EMI) can distort data. The low dielectric loss and carefully managed trace routing in High TG PCBs help minimize this issue.
●Effective Shielding and Grounding-
High TG PCBs often incorporate advanced shielding and grounding techniques to further reduce the impact of crosstalk and signal loss. This is achieved through well-designed planes that prevent electromagnetic interference from affecting the signal paths.
Example of Signal Loss and Crosstalk Reduction in 5G Networks
Application | Challenge | Solution with High TG PCB |
5G Communication | Signal degradation due to loss and interference. | High TG PCBs minimize signal loss and crosstalk, enhancing data integrity. |
Radar Systems | Crosstalk and interference between signal paths. | Effective shielding and precise trace separation reduce crosstalk. |
Industrial and Military Applications of High TG PCBs
High TG PCBs are engineered to withstand the extreme demands found in harsh environments, ensuring reliability where standard circuit boards would typically fail. From industrial machinery to military electronics, these PCBs perform where others simply cannot. They thrive in sectors requiring exceptional durability, high thermal resistance, and precise functionality, even when exposed to rapid temperature changes, humidity, and vibrations. Their use in critical systems like avionics, radar, and power distribution units showcases their ability to handle severe conditions while maintaining peak performance.
In industrial automation, military defense systems, and aerospace technologies, the need for reliable electronics that continue to function flawlessly under harsh conditions has never been more pressing. High TG PCBs meet these requirements, excelling in high-stakes environments where failure is not an option. Below, we delve into their applications and how they are transforming industries requiring high reliability under extreme conditions.
High TG PCBs in Harsh Environments
In industries such as oil and gas, power generation, and heavy machinery, electronics are subjected to vibrations, thermal stress, and moisture. High TG PCBs provide a solution, offering enhanced durability and thermal stability. These boards are designed to excel in high-temperature environments, with the ability to maintain stability and integrity even when exposed to rapid temperature cycling, moisture, and mechanical stresses.
For example, in oil drilling operations, sensors and controllers are exposed to high pressures and temperature extremes. High TG PCBs are ideal for use in the motor controllers and power supplies of drilling rigs, where thermal cycling can be intense. By maintaining low thermal expansion, High TG PCBs ensure that the components stay securely in place and resist damage from temperature fluctuations, ultimately prolonging their service life and performance.
Moreover, High TG materials are highly resistant to moisture and humidity. In coastal or humid environments, such as coastal power plants, these PCBs prevent corrosion and maintain reliable performance, even when exposed to constant moisture.
Feature | Example: High TG PCB for Harsh Environments |
Thermal Stability | Withstands up to 180°C (S1000-2M) |
Moisture Resistance | High resistance to water-induced damage |
Vibration Resistance | Robust under industrial machine vibrations |
Applications | Oil rigs, power plants, robotics, automated lines |
Durability of High TG PCBs in Aerospace Technologies
Aerospace technology demands precision and reliability, especially when dealing with systems like avionics, satellite electronics, and spacecraft power management. High TG PCBs are indispensable in this field, providing the thermal stability and mechanical durability required for space and aviation applications.
Satellites, for instance, must endure both extreme heat from solar exposure and the freezing cold of space. High TG PCBs are built to resist these temperature extremes, with laminates such as polyimide offering the necessary insulation and thermal resistance. These boards remain stable, ensuring that critical systems, such as power distribution and signal processing, continue to operate even when exposed to rapid thermal cycling. Furthermore, with their low coefficient of thermal expansion (CTE), High TG PCBs avoid issues like solder joint fatigue that could otherwise lead to failure in fine-pitch components.
High TG PCBs are also used extensively in avionics. In aircraft, avionics systems are constantly subjected to temperature variations, from the cold of high altitudes to the warmth of ground-level operations. These temperature changes can cause instability in lower-grade PCBs, leading to malfunctions. High TG PCBs ensure that avionics systems—such as navigation, autopilot, and communication systems—continue to function without interruption, regardless of environmental fluctuations.
Feature | Example: High TG PCB in Aerospace |
Thermal Cycling Resistance | Withstands extreme temperature shifts |
Mechanical Durability | High resistance to vibrations and shocks |
Low Coefficient of Thermal Expansion (CTE) | Prevents solder joint fatigue |
Applications | Satellites, avionics, spacecraft systems |
Defense Electronics: Advanced Capabilities of High TG PCBs
Defense electronics must operate flawlessly in some of the toughest conditions, where even minor failures can result in disastrous consequences. High TG PCBs are designed to meet these high-performance demands, ensuring that military-grade electronics function reliably in extreme environments.
Radar systems, electronic warfare equipment, and missile guidance systems are just a few examples of defense technologies that depend on High TG PCBs. These systems often operate in high-G environments, such as fighter jets or anti-missile defense systems, where rapid acceleration and deceleration create mechanical stress. High TG PCBs are built to withstand these forces, ensuring that all electronic components remain securely in place and continue to function properly under high shock and vibration conditions.
In missile guidance systems, for example, the PCBs must remain thermally stable even in the face of intense heating caused by propulsion systems. The enhanced thermal conductivity of High TG materials like Rogers 4350B ensures that signals are transmitted without degradation, even during rapid temperature fluctuations.
The robustness of High TG PCBs in military electronics extends beyond thermal and mechanical performance. Their ability to operate in high-pressure, high-shock environments ensures that critical systems, such as radar sensors or satellite communications, can continue to operate in the field without interruptions.
Feature | Example: High TG PCB for Defense Electronics |
High-G Environment Stability | Withstands extreme acceleration and shock |
Thermal Performance | Maintains stability under rapid temperature changes |
Mechanical Reliability | Resistant to vibrations and mechanical stresses |
Applications | Radar systems, unmanned vehicles, missile guidance |
Why Choose Us for High TG PCB Fabrication?
At JarnisTech, we are committed to delivering custom high-temperature PCB solutions tailored to your unique requirements. With decades of experience and a dedicated team, we bridge the gap between challenging thermal demands and reliable PCB designs, ensuring your projects succeed in even the most unforgiving environments.
1.Contact JarnisTech for Expert High TG PCB Support
Are you navigating the complexities of high-temperature circuit board design? Let us simplify the process for you. At JarnisTech, we don’t just manufacture PCBs—we collaborate with you to optimize materials and design strategies that align perfectly with your application.
●Material Selection Assistance: Whether it’s FR-4, polyimide, or ceramic substrates, we guide you through the selection process based on your project’s thermal, mechanical, and electrical needs.
●RoHS Transition Support: For companies upgrading to RoHS-compliant processes, we offer insights into selecting environmentally friendly, high-performance laminates that meet stringent regulations.
2.Offering High-Temperature PCB Solutions that Work
We specialize in producing high-temperature PCBs designed for exceptional durability and performance. Whether your project involves industrial machinery, automotive electronics, or high-power systems, our high-TG PCBs are built to handle demanding applications with ease.
The table given below catalogues the most frequently resorted to materials for high-TG PCBs:
Material | TG (DSC, °C) | Td (Wt, °C) | CTE-z (ppm/°C) | Td260 (min) | Td288 (min) |
S1141 (FR4) | 175 | 300 | 55 | 8 | / |
S1000-2M (FR4) | 180 | 345 | 45 | 60 | 20 |
IT180 | 180 | 345 | 45 | 60 | 20 |
Rogers 4350B | 280 | 390 | 50 | / | / |
Our High TG PCB products boast a thermal rating of up to 180°C and are available in a range of laminate materials suitable for diverse applications. Whether you require multi-layer boards, heavy copper PCBs, or HDI configurations, we have the tools to deliver.
Wide Industry Coverage-
From electric vehicle control systems to satellite communications, our PCBs ensure reliability where conventional boards fall short. We cater to industrial, aerospace, and automotive sectors, providing robust designs that maintain performance even under thermal stress.
High TG PCB Materials We Use:
Material Type | TG Rating (°C) | Thermal Expansion (Z-axis) | Common Applications |
FR-4 Standard High TG | 170–180 | Low | Power converters, industrial machinery |
Polyimide | 200+ | Ultra-low | Aerospace electronics, medical devices |
Ceramic Composites | 250+ | Minimal | Military and satellite systems |
3.Technical Expertise for Tailored Solutions
At JarnisTech, we thrive on challenges. Whether your PCB design involves intricate layouts, high-layer counts, or specific thermal tolerances, we have the expertise to make it happen.
●Precision Engineering: We ensure tight tolerances and optimal trace designs for reliable signal transmission, even in high-frequency applications.
●Thermal Stress Testing: Our PCBs undergo rigorous testing to simulate real-world conditions, ensuring performance consistency over their lifetime.
●Streamlined Production: We utilize advanced manufacturing techniques to minimize production lead times without compromising on quality.
4.Our High TG PCB Manufacturing Capabilities
No matter how complex or specialized your requirements, JarnisTech delivers solutions that exceed expectations. Partner with us to unlock the benefits of cutting-edge PCB technologies. Our proven track record and innovative approach make us the go-to choice for high-performance boards. Check our capabilities here:
Feature | Our Capability |
Quality Grade | Standard IPC 2 |
Number of Layers | 2 – 60 layers |
Order Quantity | 1 pc – 10,000+ pcs |
Build Time | 2 days – 5 weeks |
Material | S1141 (FR4), S1000-2M (FR4), IT180, Rogers 4350B |
Board Size | Min: 6 mm x 6 mm |
Board Thickness | 0.4 mm – 6.5 mm |
Copper Weight (Finished) | 0.5 oz – 30 oz |
Min Tracing/Spacing | 3 mil / 3 mil |
Solder Mask Sides | As per the file |
Solder Mask Color | Green, White, Blue, Black, Red, Yellow |
Silkscreen Sides | As per the file |
Silkscreen Color | White, Black, Yellow |
Surface Finish | HASL (Hot Air Solder Leveling) |
Lead-Free HASL (RoHS) | |
ENIG (Electroless Nickel/Immersion Gold – RoHS) | |
Immersion Silver (RoHS) | |
Immersion Tin (RoHS) | |
OSP (Organic Solderability Preservatives – RoHS) | |
Min Annular Ring | 4 mil |
Min Drilling Hole Diameter | 6 mil |
Other Techniques | Gold Fingers |
Blind/Buried Vias | |
Countersink Holes |
Don’t Wait—Get Your Custom High TG PCB Quote Now! Contact us at 0086-0075-23034656, email us, or fill out our online form. Let’s take your project to the next level.
FAQ About High TG PCBs
How do High TG PCBs impact signal integrity?
High TG PCBs maintain better signal integrity under high temperatures. Their higher TG value and better thermal stability help minimize signal degradation that can occur when the board material softens at high temperatures. This is particularly important in high-frequency and high-performance electronic devices.
Can High TG PCBs be used in consumer electronics?
Yes, High TG PCBs can be used in consumer electronics, but they are typically preferred for products requiring high durability, thermal resistance, or reliability under extreme conditions. While consumer electronics like smartphones or laptops don’t always need the extra heat resistance, they may be used in premium or high-performance devices.
What types of materials are typically used for High TG PCBs?
Common materials used for High TG PCBs include FR4, S1000-2M, IT180, and Rogers 4350B. These materials are selected for their ability to withstand higher temperatures while maintaining the mechanical properties and electrical conductivity required for reliable performance.
How do High TG PCBs contribute to the overall longevity of electronic devices?
High TG PCBs help improve the longevity of electronic devices by resisting thermal fatigue and mechanical damage caused by thermal cycling and vibration. Their ability to maintain structural integrity over time reduces the likelihood of failures, making them more reliable and longer-lasting.
Are High TG PCBs more expensive than regular PCBs?
Yes, High TG PCBs are generally more expensive than regular PCBs due to the specialized materials used and the additional manufacturing processes required to handle their higher temperature resistance. However, their increased durability and performance in harsh environments often justify the higher cost, particularly for mission-critical applications.