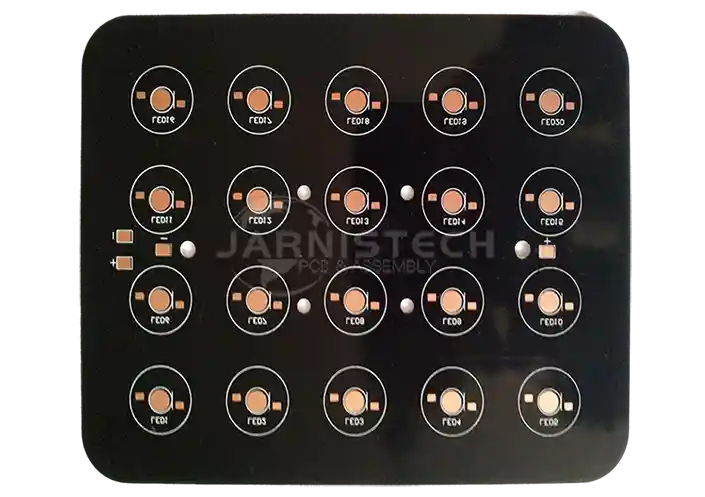
Aluminum PCBs are an indispensable part of modern electronic systems. From LED lighting applications to power-intensive devices, these specialized printed circuit boards (PCBs) offer solutions for managing heat, improving performance, and enabling durability. Manufacturers, engineers, and suppliers must have a solid understanding of aluminum core PCB design, materials, and production techniques to create reliable solutions that meet the demands of high-performance industries.
This article will dive deep into the world of aluminum PCBs, providing insights into their types, structures, material properties, and applications, with a specific focus on LED lighting, thermal management, and PCB manufacturing. By the end of this guide, you’ll have a clear understanding of how aluminum PCBs can address the challenges of modern electronics.
What Are Aluminum PCBs?
Aluminum PCBs are a specialized type of circuit board featuring a metal substrate, typically an aluminum alloy, rather than traditional fiberglass or plastic. They share similarities with standard PCBs, including layers of copper, solder mask, and silk screen. However, the standout feature lies in the aluminum core, which provides exceptional thermal conductivity and structural strength. These boards are often designed as single-sided, although double-sided options are also available. The creation of multi-layered aluminum PCBs, while possible, presents technical challenges due to the complexity of layering metal cores.
One of the most common uses of aluminum PCBs is in LED lighting systems. High-intensity LEDs generate significant heat during operation, which, if unmanaged, can degrade performance and reduce lifespan. Aluminum PCBs address this issue by efficiently dispersing heat away from sensitive components. This results in improved durability and reliability, making them indispensable in applications like traffic lights, household lighting, and industrial illumination.
Beyond lighting, aluminum PCBs are also employed in power electronics such as converters and motor controllers, where they assist in current switching and system stability. While less common in other industries, their thermal and mechanical advantages have led to growing adoption in automotive, aerospace, and renewable energy systems.
Common Applications of Aluminum PCBs
Application | Advantages of Aluminum PCBs | Examples |
LED Lighting | Enhanced heat dissipation, longer lifespan, and stable operation | Traffic lights, household LEDs |
Power Electronics | Efficient thermal control, improved system reliability | Motor controllers, power converters |
Automotive | Withstands high temperatures, durable in harsh environments | LED headlights, engine management systems |
Aerospace | Lightweight yet robust, optimal heat management | Avionics, satellite systems |
Renewable Energy | High efficiency under thermal stress | Solar inverters, wind turbine controllers |
By choosing aluminum PCBs, industries gain a reliable solution for managing heat and enhancing the longevity of electronic systems. It’s time to take the next step—explore how aluminum PCBs can transform your projects today!
How Aluminum PCBs Outperform Traditional PCB Materials?
Aluminum PCBs have become a dominant choice in industries requiring high thermal performance and durability. The choice of substrate material for printed circuit boards is crucial, especially when it comes to demanding applications like LED lighting, automotive electronics, and high-power devices. Aluminum PCBs offer significant advantages over traditional materials like FR4 and copper in terms of heat dissipation and cost-effectiveness.
The key difference lies in the superior thermal conductivity of aluminum compared to FR4 and other common PCB materials. Aluminum’s ability to efficiently transfer heat ensures that components stay at optimal temperatures, preventing overheating and extending the lifespan of the device. As a result, it’s not only ideal for LED applications, where heat management is crucial, but also for automotive and power electronics that require heat dissipation without compromising on performance or cost.
Let’s explore how aluminum PCBs are designed to manage heat better than traditional materials and how these benefits make them a go-to choice in specific applications.
Thermal Management: The Core Advantage of Aluminum PCBs
When it comes to thermal management, aluminum PCBs simply blow other materials, like FR4, out of the water. This is because aluminum has a far superior thermal conductivity compared to standard PCB materials, meaning it can handle heat more efficiently. In electronics, where heat buildup is one of the biggest performance killers, aluminum-based substrates keep things in check by quickly dissipating excess heat.
To break it down, thermal conductivity measures how well a material can transfer heat. Aluminum PCBs usually have thermal conductivity ratings in the range of 1.0 to 9.0 W/m·K, significantly higher than FR4, which typically sits at 0.3 to 0.4 W/m·K. This makes aluminum a clear winner in high-power applications like LED lighting, automotive electronics, and power supply systems where heat management can make or break the device.
But that’s not all aluminum PCBs have to offer. A standout feature is the use of thermal vias, typically made of copper. These little channels allow heat to move from the top layers of the PCB directly into the aluminum base. This design prevents heat from building up in the circuit, which can otherwise lead to component failures or shortened lifespans. The heat gets routed away from sensitive areas, helping to maintain optimal performance even under heavy load or continuous operation. It’s a smart design that keeps everything working without breaking a sweat.
In addition to thermal vias, the copper thickness used in aluminum PCBs also contributes to their stellar thermal management. A thicker copper layer improves heat dissipation even further, making the PCB more capable of managing high-power components like LED drivers. When electronics manufacturers specify a higher copper thickness for aluminum-based PCBs, it ensures that heat doesn’t just escape, but it’s actively driven away from sensitive components.
Material | Thermal Conductivity (W/m·K) | Heat Dissipation Efficiency | Typical Application |
Aluminum | 1-9 | High | LED Lighting, Automotive |
FR4 | 0.3-0.4 | Low | Consumer Electronics |
Copper | 5-10 | High | High-Power Electronics |
Example: Let’s take a closer look at LED lighting. LEDs generate significant heat, and without an efficient PCB, that heat would remain trapped, reducing the lifespan of the lighting system. Aluminum PCBs, however, keep things running by effectively drawing heat away from the LED components. That’s why high-power LED street lights or automotive lighting systems rely heavily on aluminum-based boards.
Cost-Effective Manufacturing with Aluminum Substrates
When it comes to cost efficiency, aluminum PCBs don’t break the bank, even though they’re a step above standard FR4 in terms of performance. The material costs associated with aluminum-based PCBs are surprisingly competitive, especially when you consider the long-term savings they provide. Aluminum itself is relatively inexpensive, and the manufacturing process has become streamlined over time, making it a viable choice for high-volume production.
One reason aluminum PCBs are so cost-effective is the ability to scale manufacturing without sacrificing quality. Whether you’re producing a small batch of high-end automotive electronics or ramping up production for LED lighting, aluminum substrates allow manufacturers to scale up without facing huge increases in cost per unit.
Let’s face it – when designing cutting-edge electronics, managing costs effectively is key. Aluminum PCBs offer an affordable option that also extends the life of components, leading to fewer repairs and replacements down the line. For industries like automotive, where dependability is a top concern, aluminum PCBs make it possible to design products that stand up to tough conditions, all while keeping the price tag reasonable. It’s the perfect combo of durability and cost-efficiency that delivers results over time.
Material | Unit Cost (USD) | Manufacturing Speed (Units/Day) | Best Application |
Aluminum | 0.50 | 200-500 | LED Lighting, Automotive |
FR4 | 0.10 | 500-1000 | Consumer Electronics |
Copper | 2.00 | 100-300 | High-Power Electronics |
Not only is the raw material affordable, but the manufacturing process is faster too. Aluminum PCBs don’t require extensive curing times or complicated processing steps, which speeds up production. This benefit is particularly impactful in industries such as LED lighting, where the speed of bringing a product to market can have a huge effect on success. The quicker production also helps prevent delays in inventory, allowing companies to move products faster and meet customer demands without unnecessary waiting times.
Aluminum PCB Structures and Types: Choosing the Right Solution
When it comes to electronic circuit design, the structure of your PCB is just as important as the materials you choose. With aluminum-based PCBs, understanding the differences in structures—such as single-sided, double-sided, and multilayer PCBs—is key to selecting the right option for your application. The structure directly influences everything from thermal management to electrical conductivity, signal integrity, and overall performance. Let’s break down how different PCB structures can be utilized across various industries and applications.
How PCB Structure Impacts Design and Performance?
The structure of a PCB refers to its core materials, dielectric layers, and how they are assembled to create a complete circuit. These elements affect several critical performance aspects, including electrical conductivity, signal integrity, and heat distribution.
●Circuit Copper Layer: Circuit copper layer (usually with the electrolytic copper foil) is etched to create the circuit printed, which is used to implement connections and assembly of devices. In comparison to the conventional FR-4 which has similar thickness and same line width the aluminum substrate can hold a greater current.
●Metal Core Materials: When choosing materials for the core of a PCB, the material selection is one of the biggest influences on its thermal and electrical properties. For aluminum PCBs, the core material is typically aluminum, which provides excellent thermal conductivity—a key benefit for applications like LED lighting and automotive electronics. Ceramic or polyimide substrates may also be used, offering varying degrees of thermal and electrical performance based on the specific needs of the design.
●Dielectric Layers: The dielectric material separates the conductive layers of the PCB, ensuring electrical isolation. Common dielectric materials for aluminum PCBs include polyimide, FR4, or ceramic, with each offering distinct heat dissipation and electrical properties. For instance, polyimide is often chosen for its high thermal resistance and flexibility, making it suitable for flexible, high-performance applications in automotive and medical electronics.
●Impact on Heat Distribution: The PCB’s structure also determines how heat is distributed throughout the board. Aluminum substrates, in particular, leverage features like thermal vias and copper thickness to effectively conduct heat away from high-power components such as LEDs. The efficiency of heat flow can vary based on the number and placement of thermal vias, as well as the overall thickness of the copper layers.
●Signal Integrity: The layout and stack-up design of the PCB—particularly in multilayer boards—can influence signal quality. With aluminum PCBs, signal integrity is typically improved by keeping power and signal traces separated, preventing interference that could otherwise cause performance issues in automotive or high-frequency designs.
Core Material | Thermal Conductivity (W/m·K) | Electrical Conductivity | Typical Applications |
Aluminum | 180-200 | Good | LED Lighting, Automotive |
Polyimide | 0.3-0.4 | Moderate | Flexible Electronics, Sensors |
Ceramic | 160-200 | Very Good | High-Temperature Electronics |
Types of Aluminum PCBs: Single-Sided, Double-Sided, and Multilayer
When choosing an aluminum PCB, the structure type—single-sided, double-sided, or multilayer—can make all the difference in determining which solution is best for your application. The type of PCB affects the number of components that can be placed, signal integrity, heat dissipation, and overall functionality.
1. Single-Sided Aluminum PCBs-
Single-sided aluminum PCBs are a simple and effective solution for applications that don’t require complex circuit layouts. These PCBs have components placed only on one side of the aluminum substrate, making them cost-effective and efficient to manufacture.
These types of PCBs are commonly used in basic LED lighting applications, where managing heat and keeping costs low are top priorities. . They’re also used in simpler power electronics where the circuit is straightforward, and a single layer of components suffices.
Example: A manufacturer of LED street lights can utilize single-sided aluminum PCBs to keep production costs low, while still providing excellent heat dissipation from the LEDs.
2. Double-Sided Aluminum PCBs-
Double-sided PCBs have components on both sides of the aluminum base, which allows for a more compact design. This type is ideal for mid-complexity applications that are moderately complex, where space-saving is a must and managing heat is still a top concern.
Example: In automotive electronics, where space is often limited, a double-sided aluminum PCB might be used to power LED headlights or infotainment systems, providing more efficient use of space and a more balanced heat distribution.
3. Multilayer Aluminum PCBs-
Multilayer aluminum PCBs are the most advanced type, consisting of multiple layers of copper, dielectric, and aluminum materials stacked on top of each other. These PCBs are ideal for complex applications that require higher component density, such as smart devices, power supply circuits, and automotive electronics where multiple signals need to be routed efficiently.
The multilayer construction enhances thermal dissipation and signal integrity, as the layers are designed to isolate power traces from signal traces, improving overall performance and reliability.
Example: In smart home devices, multilayer PCBs can be used to manage the intricate connections between sensors, wireless modules, and power supply systems. The multilayer design enables efficient use of space, while thermal vias help to manage heat from the high-power components.
Type | Layers | Best Use Case | Thermal Performance | Cost |
Single-Sided | 1 Layer | Basic LED Lighting, Small Power Devices | Good | Low |
Double-Sided | 2 Layers | Automotive Electronics, Basic Consumer Electronics | Very Good | Medium |
Multilayer | 3+ Layers | Complex Systems (Smart Devices, Power Electronics) | Excellent | High |
Design Considerations for Aluminum PCBs: Key Elements for Success
Designing aluminum PCBs requires a thoughtful approach to ensure optimal thermal management, reliable performance, and cost efficiency. While the material itself provides outstanding thermal conductivity, it’s how the PCB is designed and manufactured that ultimately determines its success in real-world applications. In this section, we’ll dive into the key elements to consider when designing aluminum-based PCBs, covering everything from thermal simulations to DFM guidelines.
Key Design Principles for Aluminum PCBs
Designing aluminum PCBs for maximum performance requires considering several core elements, including thermal performance, component placement, and layer stack-up. Let’s take a closer look at the primary design principles to keep in mind when developing your aluminum PCB.
●Thermal Management: One of the main reasons designers choose aluminum PCBs is their ability to dissipate heat. However, simply using aluminum isn’t enough—you need to design your PCB to enhance this property. Strategic placement of thermal vias—small conductive paths that connect the copper traces to the back of the PCB—can significantly improve heat flow from high-power components, such as LEDs and semiconductors.
●Component Placement: The arrangement of components affects how heat is distributed across the board. Components that generate more heat should be placed in positions that allow for better heat transfer to the aluminum base. Reducing the distance between heat-sensitive parts and the core enhances the flow of heat. Strategic placement of components also ensures an even distribution of thermal load, which helps prevent excessive temperature buildup in certain areas.
●Layer Stack-Up: For double-sided or multilayer aluminum PCBs, the arrangement of layers is an essential factor to consider. The number of layers and their configuration affect both signal integrity and heat dissipation. In multilayer designs, special attention must be paid to how signal and power layers are stacked. This arrangement helps avoid interference between heat and electrical signals, ensuring efficient operation and better signal quality.
●Design for Manufacturing (DFM): Incorporating DFM guidelines during the design phase ensures that the PCB can be manufactured efficiently and cost-effectively. This involves optimizing component placement to reduce board complexity, choosing materials that suit the manufacturing process, and ensuring that the design is compatible with assembly techniques. Keeping these factors in mind can save time and reduce errors during the production phase.
Design Element | Recommended Practices | Benefits |
Thermal Via Placement | Strategically place thermal vias near high-heat components | Maximizes heat dissipation from heat-generating components |
Component Layout | Place high-heat components near the aluminum core | Ensures efficient heat transfer and maintains component performance |
Layer Stack-Up | Use proper dielectric materials and stack-up design | Maintains signal integrity while ensuring effective heat dissipation |
DFM Guidelines | Optimize for simpler designs, reduce complexity | Minimizes production time, lowers costs, and improves yield |
Simulation and Testing for Thermal and Mechanical Integrity
Designing aluminum PCBs isn’t a one-step process—it requires careful validation through thermal simulations and mechanical testing to ensure the board will perform as expected under real-world conditions. Here’s why and how you should test your designs before manufacturing.
●Thermal Simulation: Thermal simulation software can predict how heat will be distributed across your PCB. By creating a digital model of your aluminum PCB, these tools can simulate the effects of high-power components and their potential thermal hotspots. For example, you might use a thermal simulation tool like ANSYS Icepak to visualize temperature gradients across the PCB and identify areas where heat may accumulate. This allows you to modify the design—such as adjusting thermal via size or copper thickness—before the manufacturing process begins.
●Stress Testing: Mechanical stress testing helps identify physical weaknesses in the PCB design that could lead to failure, such as bending or cracking. Since aluminum is relatively stiff, it can cause stress points in PCBs, especially during thermal cycling or physical impact. To ensure your aluminum PCB will withstand the rigors of real-world use, subjecting it to stress tests like vibration or thermal cycling tests can reveal weak spots in the solder joints or vias.
●Mechanical Validation: Once the design passes thermal simulations, the mechanical validation phase ensures that all physical elements of the PCB are structurally sound. This involves testing the mechanical properties of the aluminum substrate, checking for factors like warping and component fixation. Using tools like SolidWorks or Autodesk Inventor, we can assess the structural integrity of the PCB under various mechanical stresses.
By leveraging these simulation tools and testing techniques, you can ensure that your aluminum PCB design will perform reliably and safely in its intended application, avoiding costly failures after manufacturing.
Simulation/Testing Type | Purpose | Tools/Methods Used | Benefits |
Thermal Simulation | Predict heat distribution across the PCB | ANSYS Icepak, COMSOL Multiphysics | Identifies potential hotspots before production, optimizing thermal management |
Stress Testing | Evaluate physical stress on the PCB | Vibration testing, thermal cycling tests | Ensures the PCB can withstand physical and environmental stresses |
Mechanical Validation | Verify structural integrity of components | SolidWorks, Autodesk Inventor | Confirms physical durability and helps prevent failures from physical stress |
The Manufacturing Process of Aluminum PCBs
The manufacturing of aluminum PCBs involves a series of meticulous steps, each designed to ensure high-performance and reliability in the final product. The unique characteristics of aluminum as a material require specific processes to make sure that it can be used effectively in electronic devices such as LED lighting, automotive systems, and communication devices. Let’s dive into the detailed steps and challenges faced in the aluminum PCB manufacturing process.
Steps in Aluminum PCB Fabrication
The aluminum PCB fabrication process requires precision and attention to detail at every stage, from material selection to final testing. Let’s break it down step by step to understand how each phase contributes to the high quality of the final product.
1. Material Selection-
The process of aluminum PCB fabrication begins with selecting the right materials. Aluminum substrates are chosen for their impressive thermal conductivity, but attention also needs to be paid to the dielectric layer. This layer must pair well with aluminum and offer proper insulation. Materials such as polyimide and epoxy fiberglass are commonly chosen for their dielectric qualities. The right combination of materials ensures the PCB will stand up to demanding applications and maintain strong performance over time.
Selecting the right aluminum substrate is the foundation of a successful PCB. Therefore, when we evaluate the following factors when selecting materials:
●Thermal Conductivity: The aluminum layer’s ability to conduct heat directly impacts the board’s performance. Typical values range from 1.0 W/m·K to 2.2 W/m·K.
●Cost-Effectiveness: While aluminum-based PCBs may have higher upfront material costs compared to FR4 boards, their efficiency in dissipating heat often reduces long-term maintenance costs.
Substrate Material | Thermal Conductivity (W/m·K) | Typical Applications |
Standard Aluminum | 1.0 – 1.5 | General-purpose LED lighting |
High-Conductivity Aluminum | 2.0+ | Automotive electronics, industrial applications |
●Optimizing Thermal Performance: The dielectric layer between the copper and aluminum substrate serves as an insulator while still allowing heat to be transferred effectively. Thinner dielectric layers improve heat conductivity but require precision to ensure that electrical insulation remains intact. Additionally, the incorporation of thermal vias and appropriate copper thickness helps to enhance heat dissipation, making aluminum PCBs a reliable choice for power-intensive applications.
2. Etching-
Once the material is chosen, the next step is etching, where the copper layer is transferred onto the PCB surface. Photolithography comes into play here, as a resist layer is applied to the copper and exposed to UV light. Areas not exposed to light are washed away, leaving behind the copper traces that form the circuit. This process is fundamental for creating the precise patterns that enable electrical connections on the PCB, ensuring everything fits together as it should.
3. Solder Masking-
After etching, the next step for the PCB is solder masking. During this process, a thin layer of solder mask is applied over the copper traces, leaving only the spots where components will be soldered exposed. This layer helps to shield the copper paths from potential short circuits and any other unwanted connections. It’s like putting a protective coat on the traces to ensure no accidental contact happens during soldering. Beyond just protection, the solder mask helps with the long-term durability of the board, preventing wear and tear during assembly. It ensures the PCB can handle the tough jobs ahead without any hiccups down the line.
4. Final Testing-
After all manufacturing steps are completed, the final testing phase ensures that the aluminum PCB meets all electrical and mechanical specifications. Electrical testing checks for short circuits, open circuits, and ensures the signal integrity of the PCB. Mechanical testing involves checking for physical defects such as warping or dimensional inaccuracies that could affect performance. High-precision testing tools and machines, such as automated optical inspection (AOI) systems, are used to detect even the smallest defects, ensuring that only the best-quality products make it through the process.
Fabrication Step | Description | Key Benefits |
Material Selection | Choosing aluminum and dielectric materials that offer good thermal conductivity and electrical insulation | Ensures optimal heat dissipation and reliability |
Etching | Transfer of copper patterns to the PCB surface using photolithography | Provides accurate, high-density circuits |
Solder Masking | Applying a protective layer over the copper to prevent short circuits | Protects the integrity of the copper traces and ensures durability |
Final Testing | Electrical and mechanical testing to check for defects and performance issues | Guarantees the PCB meets all performance standards before shipping |
Challenges in Aluminum PCB Production
While aluminum PCB manufacturing is a robust and proven process, it is not without its challenges. In this section, we’ll address the most common production issues and the innovative solutions that we employ to overcome them.
1. Adhesion Issues-
In aluminum PCB production, one of the frequent challenges is ensuring a strong bond between the dielectric layer and the aluminum substrate. Aluminum’s naturally smooth surface can make it difficult to create a durable bond with the dielectric material, which impacts the board’s thermal and electrical properties. To address this, we can rely on advanced adhesive methods to secure a strong connection. Additionally, techniques like anodizing are applied to roughen the aluminum’s surface, which helps improve the adhesion and ensures the dielectric layer remains properly attached during use, especially in demanding applications.
2. Thermal Stress Management-
Thermal stress is a significant concern in aluminum PCBs, especially in high-power applications like LED lighting or automotive electronics. As the components on the PCB generate heat, the thermal expansion of the aluminum can cause stress at the solder joints or lead to warping of the PCB itself. To manage thermal stress, we can incorporate thermal vias and copper plating to help distribute heat evenly across the board. Additionally, high-precision soldering techniques are used to ensure that components remain securely attached to the PCB, even under thermal stress.
3. Material Sourcing-
The sourcing of high-quality aluminum and dielectric materials can be challenging, particularly when dealing with supply chain fluctuations or when sourcing materials that meet the specific needs of high-performance PCBs. we can mitigate this challenge by establishing long-term relationships with trusted suppliers and ensuring that all materials meet the required specifications for thermal conductivity, insulation resistance, and mechanical strength.
Manufacturing Challenge | Solution | Impact on Performance |
Adhesion Issues | Use of advanced adhesive technologies and surface treatments like anodizing | Ensures strong bonding and reliable PCB function |
Thermal Stress Management | Implementation of thermal vias, copper plating, and high-precision soldering | Distributes heat evenly and prevents thermal damage |
Material Sourcing | Establishment of partnerships with reliable material suppliers | Ensures high-quality materials and reduces manufacturing delays |
The Assembly of Aluminum PCBs: Best Practices for High-Quality Results
Aluminum PCB assembly demands precision and careful planning to ensure both performance and longevity. This process involves specialized soldering techniques, exact placement of components, and well-thought-out decisions regarding automation to meet the unique needs of industries such as automotive electronics, industrial automation, and LED lighting. It’s all about getting the little details right—whether it’s selecting the right soldering process, ensuring components fit just right, or knowing when to go with automated solutions. These decisions make sure the end product can withstand the demands of tough environments while performing at its peak.
Soldering and Mounting on Aluminum PCBs
Advanced Soldering Techniques-
Soldering components onto aluminum PCBs presents unique challenges due to their superior heat dissipation properties. During soldering, the aluminum substrate rapidly absorbs heat, potentially causing uneven solder joints. To counter this, we often use reflow soldering with specialized thermal profiles or conductive adhesives to ensure consistent connections.
Key best practices include:
●Preheating the PCB: Gradual preheating minimizes thermal shock and allows for more even solder flow.
●Selecting Low-Temperature Solder Alloys: These alloys reduce stress on components during the soldering process, especially for sensitive semiconductors.
●Utilizing High-Precision Reflow Ovens: Equipment with advanced temperature control ensures that every solder joint meets stringent quality requirements.
Component Placement Challenges-
Thermal expansion caused by the heating and cooling cycles during assembly can affect component reliability. To mitigate this:
●Use flexible adhesive compounds for components subjected to thermal cycling.
●Ensure robust thermal simulation at the design phase to anticipate potential hotspots and stress points.
Technique | Advantages | Applications |
Reflow Soldering | Uniform solder joints, high-speed processing | High-volume manufacturing |
Conductive Adhesive Bonding | Reduced thermal stress, no heat requirement | Thermally sensitive components |
Automated vs Manual Assembly: Choosing the Right Approach
Automated Assembly for Precision and Efficiency-
In large-scale production environments, automated assembly lines are favored for their speed and precision. These systems excel at handling repetitive tasks, such as placing surface-mounted devices (SMDs) or applying solder paste. Benefits of automation include:
●Consistent solder quality and component alignment.
●Reduced labor costs and error rates.
●Capability to scale up production for high-demand markets like LED arrays or consumer electronics.
Manual Assembly for Customization-
Despite the benefits of automation, certain projects benefit from manual assembly. For example:
●Small-Batch Runs: Custom designs or prototypes often require the hands-on approach of skilled technicians.
●Specialized Applications: Components that need precise placement or adjustments during assembly benefit from manual handling.
Assembly Type | Best For | Limitations |
Automated | High-volume production, repetitive tasks | High initial setup costs |
Manual | Prototyping, custom designs | Slower, labor-intensive process |
In the LED lighting industry, aluminum PCBs are extensively used to manage heat generated by high-power diodes. Automated assembly lines place LEDs and drivers with micron-level precision, ensuring high efficiency and longevity of the final product. Meanwhile, manual adjustments might be applied for custom lighting arrays tailored for architectural projects.
Whether you’re running a high-volume assembly line or creating custom PCB solutions, understanding these assembly methods and their applications can make all the difference. Ready to level up your manufacturing process? Contact us today to explore tailored assembly strategies for your aluminum PCBs!
Aluminum PCB Vs Copper Base PCB and Ceramic PCB
To understand the distinctions among these three popular PCB types, it’s key to examine their manufacturing processes, performance attributes, applications, and cost considerations. Each type offers specific advantages tailored to meet various industry needs, making them a good fit for different technological challenges. Below is a detailed comparison:
Manufacturing Process
● Aluminum PCB: Aluminum PCBs use an aluminum base with a thin dielectric layer for insulation and thermal management. They are produced through techniques like etching and layering, emphasizing thermal conductivity and mechanical stability. Single-layer designs are common, though multi-layer versions require complex manufacturing.
● Copper Base PCB: Copper PCBs feature a copper substrate, ideal for high-power applications. Their production involves precision etching and layering of thicker copper cladding, enhancing current-carrying capacity. The base can be copper alone or bonded with other materials.
● Ceramic PCB: Ceramic PCBs are crafted using ceramic substrates like alumina or aluminum nitride. Manufacturing includes laser drilling and metallization. They are usually printed using thick-film or thin-film technology, allowing for compact layouts with minimal thermal resistance.
Performance Attributes
● Aluminum PCBs: Moderate thermal conductivity (1-9 W/mK), lightweight, and resistant to corrosion. Suitable for applications with mid-level heat dissipation needs. Electrical performance is sufficient for most LED or low-frequency applications.
● Copper Base PCBs: Outstanding thermal conductivity (up to 400 W/mK) and electrical performance. Heavier and less suited for weight-sensitive projects but excellent for high-power applications.
● Ceramic PCBs: Exceptional thermal conductivity (up to 170 W/mK for AlN). Superior electrical insulation and stability under high-frequency conditions. However, they are brittle and require careful handling.
Attribute | Aluminum PCB | Copper Base PCB | Ceramic PCB |
Thermal Conductivity | Moderate (1-9 W/mK) | High (5-10 W/mK) | Very High (20-330 W/mK) |
Electrical Resistance | Medium | Low | Very Low |
Mechanical Durability | Lightweight, robust | Heavy, sturdy | Fragile under stress |
Operating Temperature | -40°C to 150°C | -40°C to 300°C | -55°C to 850°C |
Applications
● Aluminum PCB: Aluminum boards shine in LED lighting systems, power electronics, and automotive components. They are widely used where moderate heat dissipation and lightweight designs are required.
● Copper Base PCB: These are go-to choices for high-current devices like inverters, power amplifiers, and industrial equipment. They thrive in scenarios demanding superior heat management and electrical conductivity.
● Ceramic PCB: Ceramic boards dominate industries requiring high thermal and electrical performance, such as aerospace, medical devices, and high-frequency electronics. Their ability to withstand extreme temperatures makes them indispensable for cutting-edge applications.
Cost Comparison
● Aluminum PCBs: Cost-effective, with prices ranging from $10 to $50 per square meter depending on complexity and layers.
● Copper Base PCBs: More expensive than aluminum, typically $50 to $150 per square meter due to the cost of raw materials and processing.
● Ceramic PCBs: The highest cost, ranging from $100 to $500 per square meter, influenced by specialized materials and manufacturing requirements.
Type | Material Cost | Manufacturing Cost | Overall Cost per Unit |
Aluminum PCB | Low | Medium | Affordable |
Copper PCB | High | High | Expensive |
Ceramic PCB | Medium to High | Very High | Premium Pricing |
Why Choose JarnisTech as Your Aluminum PCB Manufacturer in China?
1.Expertise Backed by Scale and Experience
JarnisTech takes pride in being one of the leading PCB manufacturers in China, operating within a state-of-the-art facility spanning over 30,000 square meters. With a legacy of manufacturing excellence, we have honed our craft in delivering precision-engineered Printed Circuit Boards tailored to meet diverse client needs across industries. Our extensive infrastructure allows us to handle projects of any scale efficiently while maintaining top-tier quality.
2.Advanced Aluminum PCB Manufacturing Capabilities
With years of focused experience in aluminum PCB production, JarnisTech offers unmatched capabilities in creating high-performance solutions. From LED lighting systems to power-intensive automotive and industrial applications, our aluminum PCBs are designed for durability, optimal thermal performance, and reliability. Features of our services include:
●Comprehensive Manufacturing Processes: Our production facilities are equipped to handle the entire fabrication process, ensuring precision at every step. This includes material selection, drilling, etching, and solder mask application.
●Free DFM Checks: We offer a Design for Manufacturing (DFM) evaluation at no extra cost, enabling clients to optimize their designs for manufacturability, reducing errors, and ensuring a seamless production process.
Here is our aluminum PCB capabilities based on the provided specifications:
Specifications | Details |
Layer | 1-12 Layers |
Build Time | 1 Day to 4 Weeks |
Aluminum PCB Types | Single-sided, Double-sided, Aluminum flexible PCB, Single-layer, Double-layer, Multilayer |
Quality Level | IPC-A-600 Class 3/2 |
Thermal Conductivity | 1W/mK to 9W/mK |
Aluminum PCB Substrate Material | 3003 (pure aluminum), 5052 (Al-Mg alloy), 6061 (Al-Mg-Si alloy), 1100 (pure aluminum) |
Dielectric Layer Material | Polymer Filled with Ceramic |
Copper Thickness | 1OZ to 8OZ (35μm to 280μm) |
Manufacturing Condition | Full-line operation; production machines and equipment specialized for aluminum PCBs |
Surface Finish | ENIG, OSP, HASL (LF HASL), Immersion Tin, Immersion Silver, Immersion Gold |
3.Quality That Meets Diverse Industry Needs
JarnisTech aluminum PCBs are extensively utilized in demanding fields such as:
●LED Lighting: Our manufacturing the boards enhance thermal management, which enhances the lifespan and performance of high-power LEDs.
●Automotive Systems: From control systems to lighting modules, our PCBs are engineered to perform in high-temperature and high-stress environments.
●Power Equipment: With robust construction and superior heat dissipation, our products cater to the needs of heavy-duty industrial and energy equipment.
4.Why JarnisTech Stands Out?
Feature | Benefit |
State-of-the-art facility | Ensures high production capacity and precision |
Experienced workforce | Decades of expertise in PCB manufacturing |
Cost-Effective Solutions | Competitive pricing without compromising on quality |
Industry Applications | Proven track record in automotive, industrial, and consumer electronics sectors |
On-Time Delivery | Efficient processes to meet deadlines, even for high-volume production |
Partner with JarnisTech for a Seamless Experience
When partnering with JarnisTech, you’re not just getting a supplier; you’re gaining a true collaborator focused on taking your projects to the next level. Whether you’re developing a new product or refining an existing design, our aluminum PCB solutions ensure top-tier performance and reliability.
Ready to bring your PCB designs to life? Contact JarnisTech today and experience manufacturing excellence firsthand!
Aluminum PCB Industry Trends
As industries push the envelope of technological innovation, the aluminum PCB sector continues to evolve. From the development of flexible substrates to the integration of artificial intelligence (AI) and IoT technologies, these advancements are redefining possibilities for applications ranging from wearable devices to smart factories.
Flexibility and Hybrid Materials: The Future of Aluminum PCBs
Advancements in Flexible Aluminum PCBs-
Flexible aluminum PCBs represent a cutting-edge approach to designing lightweight, adaptable circuits suitable for modern electronics. These boards are gaining traction in:
●Wearable Technologies: Flexible PCBs conform seamlessly to the contours of fitness trackers and smartwatches, ensuring durability and comfort.
●Automotive and Aviation Applications: Their ability to fit into curved spaces makes them ideal for dashboards and control panels.
Manufacturers are exploring combinations of flexible dielectric materials with thin aluminum layers to achieve superior performance without sacrificing flexibility. Enhanced bendability has opened new possibilities for medical imaging devices and foldable displays, bridging the gap between innovation and practicality.
Hybrid Materials for Thermal Management-
In high-performance applications, hybrid aluminum PCBs that combine aluminum substrates with ceramic layers are gaining attention. This approach ensures that the systems operate without a hitch, even under demanding conditions.
Material Type | Benefits | Applications |
Flexible Aluminum PCB | Lightweight, adaptable to curves | Wearables, medical imaging |
Aluminum-Ceramic Hybrid | Superior thermal conductivity | High-performance LEDs, power modules |
AI and IoT Integration in PCB Manufacturing
AI-Driven Design Optimization-
Artificial intelligence is transforming the design phase of aluminum PCBs by automating tasks such as:
●Thermal Simulation: AI algorithms predict potential heat issues and recommend design changes early in the process.
●Component Placement Optimization: By analyzing data, AI ensures efficient layouts that maximize performance and minimize production costs.
IoT in Smart Manufacturing-
The IoT is ushering in an era of smarter manufacturing environments, where interconnected devices monitor and control every aspect of production. Benefits include:
●Real-Time Quality Checks: IoT-enabled sensors detect defects during fabrication, reducing waste and improving yields.
●Predictive Maintenance: Smart systems anticipate equipment failures, reducing downtime and maintenance costs.
Technology | Function | Impact |
AI in Design | Optimizes thermal and electrical layouts | Reduces design errors |
IoT in Production | Tracks manufacturing processes | Enhances efficiency and quality |
The aluminum PCB industry is charging forward with groundbreaking innovations. Whether you’re developing wearable electronics or optimizing high-power LED systems, staying informed about these trends can give you a competitive edge. Explore these new technologies today and transform your designs for the future.
FAQ About Aluminum PCBs
1. What makes aluminum PCBs different from copper-clad laminates?
Aluminum PCBs use a metal substrate for improved heat dissipation, while copper-clad laminates rely on fiberglass or epoxy resin for structural support. This difference makes aluminum PCBs better suited for high-power applications.
2. Can aluminum PCBs be used in flexible electronic devices?
Yes, aluminum-based flexible PCBs are available. They combine the thermal management benefits of aluminum with the flexibility of polymer layers, suitable for wearable electronics and bendable displays.
3. How does the thickness of the aluminum layer affect PCB performance?
The thickness of the aluminum substrate impacts the board’s ability to dissipate heat. Thicker aluminum layers offer better thermal performance but may add weight and cost.
4. What are the environmental benefits of using aluminum PCBs?
Aluminum is recyclable and has a lower environmental impact compared to some traditional PCB materials. This makes aluminum PCBs a greener choice for industries focusing on sustainability.
5. Are there specific design tools for aluminum PCBs?
Yes, PCB EDA design tools like Altium Designer and KiCAD support the design of aluminum PCBs, including simulations for thermal management and mechanical stress.
6. How do aluminum PCBs perform in high-frequency applications?
Aluminum PCBs can handle high-frequency signals well when paired with appropriate dielectric materials. They maintain signal integrity while effectively managing heat.
7. What surface finishes are recommended for aluminum PCBs?
Common surface finishes for aluminum PCBs include ENIG (Electroless Nickel Immersion Gold), OSP (Organic Solderability Preservative), and HASL (Hot Air Solder Leveling), depending on the application and budget.
8. What are the typical failure modes of aluminum PCBs, and how can they be avoided?
Failures such as thermal cracking, delamination, and oxidation can occur. These can be minimized by using high-quality materials, ensuring proper thermal vias, and conducting rigorous stress testing during production.
Related Posts:
1. Differentiating FR4 Glass Fiber and Aluminum Substrate for PCBs
2.Leading Global 10 Aluminum PCB Manufacturers
3.Aluminum Base PCBs: The Future of High-Power Electronics
4.Overview of LED Aluminum PCB
5.Significance of Aluminum Clad PCBs in Advancing Electronic Device
6.How Leveraging Aluminum PCB Substrates: in Your Next Stackup Design?