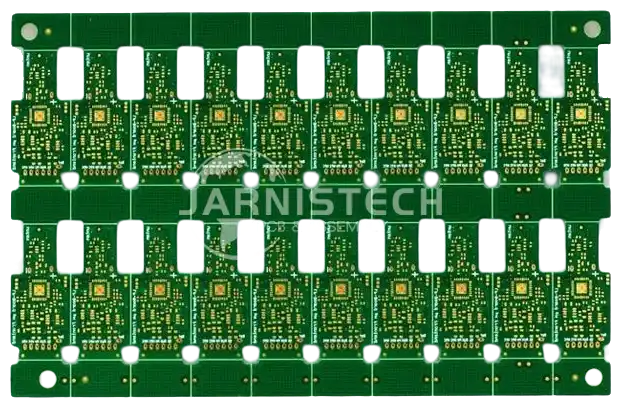
Introduction:
Why Nelco Laminates Elevate PCB Manufacturing?
Nelco PCBs have earned a reputation for their top-tier performance in applications ranging from high-frequency circuits to automotive electronics. With the continuous push toward 5G infrastructure, medical electronics, and automotive sensor development, manufacturers demand high-quality materials that ensure reliability under stress. Nelco’s product line—like N4000-13, N4000-29, and N4350-13 laminates—delivers solutions that align with these modern requirements. This article provides a comprehensive breakdown of how engineers and manufacturers can use Nelco laminates to meet stringent industry demands, ensuring seamless PCB design and manufacturing.
What Are the Materials Used in Nelco PCBs?
When it comes to manufacturing Nelco PCBs, a range of specialized materials are used, each chosen for its unique properties to meet specific industry demands. The performance and reliability of the final product are heavily influenced by these material choices, making it essential to match the right laminate or prepreg to the intended application.
Common Materials Used in Nelco PCB Production
Here’s a breakdown of the key materials commonly found in Nelco PCBs:
1.FR (Flame Retardant) Materials-
●N4000-NF, N7000-1, N7000-3: These are popular choices for high-performance applications due to their excellent thermal and electrical properties.
●N4000-2, N4000-6, N4000-7: Known for their high glass transition temperatures, making them suitable for lead-free assembly processes.
●N4000-6F, N4000-7S1, N4000-13: Engineered for multilayer designs with enhanced reliability and signal integrity.
●N4000-13 SI, N4000-29 NF: These materials are tailored for low-loss applications, making them ideal for RF and microwave circuits.
2.Nelcote7 Advanced Composites-
●F-529, E-765, E-761, E-752, E-746: Advanced composite materials designed to withstand rigorous environmental conditions and provide high mechanical strength.
3.Nelcote7 Digital Electronic Materials-
●N4000-13, N4000-13 EP, N4000-29, N4000-7 EF: These materials are optimized for digital applications, ensuring fast signal transmission and minimal crosstalk.
4.Nelcote7 RF/Microwave Materials-
●N4350-13 RF, N4380-13 RF, N9000-13 RF: Specifically designed for RF and microwave applications, these materials feature low dielectric loss and high thermal stability.
5.Meteorwave Series-
●Meteorwave 8000, Meteorwave 8350, Meteorwave 1000NF: These are high-frequency materials that offer excellent performance for advanced wireless communication systems.
Key Considerations When Choosing Materials
When selecting materials for Nelco PCBs, several factors come into play:
●Operating Frequency: Different materials perform better at specific frequencies. For instance, N4000-29 is excellent for high-frequency RF applications, while N4000-13 is versatile for various digital designs.
●Thermal Stability: Assess the thermal requirements of your application. High Tg materials are recommended for environments with extreme heat.
●Cost vs. Performance: Finding the right balance between budget constraints and performance needs is essential. While some high-performance materials might come with a higher price tag, their durability and efficiency can lead to long-term savings.
Get Started with Your Prototype!
If you’re considering developing a prototype for a Nelco PCB, JarnisTech is here to help! We pride ourselves on delivering top-quality Nelco printed circuit boards tailored to your unique requirements. Don’t hesitate to reach out for personalized service and expert guidance on selecting the best materials for your projects!
Important Characteristics of Different Types of Nelco PCB Materials
Nelco PCB materials stand out in the electronics industry due to their unique properties tailored for various applications. Let’s explore some notable characteristics of key Nelco materials:
1. Meteorwave 1000NF
●High Performance: This product is renowned for its high-quality construction, providing excellent electrical performance.
●Thermal Resistance: Capable of withstanding temperatures up to 240°C, making it suitable for applications where heat is a concern.
●Lead-Free Composition: This makes it an environmentally friendly option, aligning with contemporary manufacturing standards.
2. Meteorwave 8000
●Cost-Effectiveness: A reliable choice that balances performance with affordability.
●CAF Resistance: It exhibits strong resistance to Conductive Anodic Filamentation (CAF), which enhances the reliability of multilayer PCBs in humid environments.
3. Meteorwave 8350
●High-Temperature Capability: This material is designed for high-performance applications that encounter elevated temperatures.
●Exceptional Dielectric Strength: Ensures consistent performance in RF and microwave applications, maintaining signal integrity even under stress.
4. N4000-29NF
●Superior Temperature Resistance: Known for its ability to endure extreme temperatures without compromising performance.
●Leadless Composition: Aligns with industry trends towards safer manufacturing processes, suitable for lead-free soldering.
5. Other Noteworthy Nelco Materials
●N4000-7: Designed for high reliability in complex multilayer designs, with excellent mechanical and electrical properties.
●N4000-6 and N4000-6F: Both materials are well-regarded for their robust performance in high-speed applications, ensuring minimal signal loss.
Considerations for Choosing the Right Material
When selecting Nelco PCB materials, consider the specific demands of your application. Factors such as operating environment, thermal profiles, and electrical requirements can significantly influence your choice.
Here’s a quick comparison table to summarize the characteristics of these materials:
Material | Key Features | Temperature Rating | Lead-Free |
Meteorwave 1000NF | High-quality, low-flow, long-lasting | Up to 240°C | Yes |
Meteorwave 8000 | Reliable, cost-effective, CAF resistant | Varies | Yes |
Meteorwave 8350 | High-temperature, extreme dielectric strength | High | Yes |
N4000-29NF | Superior temperature resistance | High | Yes |
N4000-7 | High reliability in multilayer designs | High | Yes |
N4000-6 | Robust performance in high-speed applications | High | Yes |
N4000-6F | Minimal signal loss | High | Yes |
Comparing Nelco Laminates to Standard FR-4 Substrates
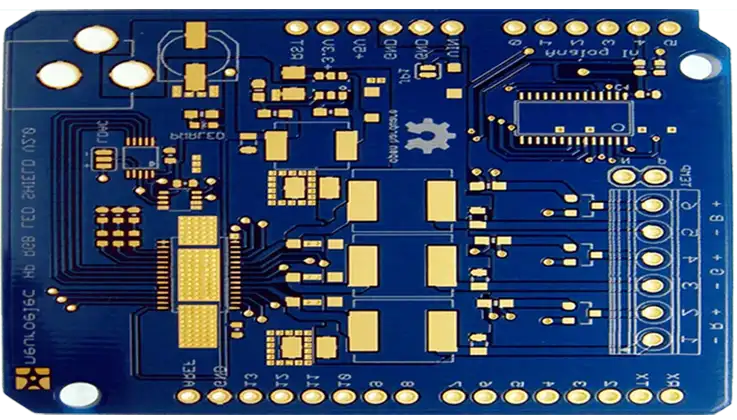
When engineers choose materials for PCB construction, a few factors always come into play: cost, thermal stability, and electrical performance. While FR-4 laminates have long been the industry standard for a variety of applications, they exhibit limitations that can hinder performance in more demanding environments. This is where Nelco PCBs come into play, offering distinctive advantages that cater to the needs of modern electronics.
What Makes Nelco Different?
Higher Tg (Glass Transition Temperature)-
Nelco laminates, particularly those in the N4000 series, boast a higher glass transition temperature than standard FR-4 materials. This characteristic allows them to endure elevated temperatures during lead-free assembly processes. For instance, when dealing with automotive electronics that require durability under fluctuating temperatures, using N4000-29 can lead to more reliable performance than FR-4. Think of it as bringing a heavy-duty jacket for those chilly days—your circuits will thank you for keeping them warm!
Lower Df (Dissipation Factor)-
The lower dissipation factor (Df) of Nelco materials significantly reduces signal loss, making them an excellent choice for high-frequency applications like RF circuits and 5G infrastructure. These materials excel by preserving signal strength over longer distances, ensuring smooth data transmission with minimal degradation. In fact, recent comparative studies show that RF circuits built with Nelco laminates experience approximately 20% less signal loss than those using conventional FR-4 substrates—offering engineers a noticeable performance boost.
Think of it like swapping out a clunky bicycle for a sleek sports car: with Nelco, your signals glide through circuits with fewer slowdowns. This makes them a perfect match for the demanding requirements of next-gen networks, where every bit of efficiency counts. If you’re working on advanced telecom infrastructure or high-speed communication modules, investing in these materials will help ensure your design stays ahead of the curve!
Superior CAF Resistance-
CAF (Conductive Anodic Filamentation) presents a real challenge to PCB reliability, especially when moisture becomes a factor. Nelco materials are specifically designed to combat this issue, extending the durability and operational lifespan of the board under demanding conditions. For instance, medical devices, where consistent performance is non-negotiable, benefit greatly from these laminates, ensuring reliable function over time. In essence, Nelco laminates stand strong, unaffected by the challenges that humidity can throw their way. Imagine a marathon runner pushing through humid conditions without breaking stride—Nelco laminates are built with that kind of endurance.
Comparison of Key Properties of Nelco Laminates vs. FR-4
Property | Nelco N4000 Series | FR-4 |
Glass Transition Temperature (°C) | 170-180 | 130-150 |
Dissipation Factor (Df) | 0.02-0.03 | 0.02-0.05 |
CAF Resistance | Excellent | Moderate |
Thermal Conductivity (W/mK) | 0.3-0.4 | 0.2-0.3 |
N4000 Series Performance in Automotive Electronics-
The N4000 series, especially the N4000-29, combines solid thermal stability with electrical reliability, making it a top pick for demanding applications. Picture this: with ADAS tech steering modern vehicles, the last thing you want is a hiccup in the circuitry when it’s navigating or dodging obstacles. These laminates hold steady under pressure—like a cool-headed driver on a hairpin turn—keeping things humming along no matter how intense it gets. When the road ahead is unpredictable, Nelco ensures your circuits stay locked in, handling the heat and the workload without breaking a sweat.
If you’re still relying on standard FR-4 for your designs, it’s time to rethink your material choices. Embracing Nelco laminates can open the door to enhanced performance and reliability in your PCB applications. So why not take the plunge? Don’t settle for less—upgrade to Nelco and see the difference! Your projects deserve it!
How Do Nelco PCBs Differ from Isola PCBs?
Nelco and Isola PCBs are both prominent choices in the high-frequency printed circuit board market, each offering unique advantages that cater to specific needs in electronic design and manufacturing. Let’s dive deeper into how these two materials compare in terms of composition, performance, and application.
1. Composition and Material Differences
Laminates and Prepregs: Nelco PCBs utilize a diverse range of laminates and prepreg materials designed to optimize thermal and mechanical performance. This variety allows for tailored solutions that can meet specific design requirements, making them a popular choice among designers looking for flexibility.
Copper-Clad Dielectric: In contrast, Isola PCBs typically employ copper-clad dielectric materials for their prepregs and laminates. This construction is particularly well-suited for applications where a more standardized approach is desired, providing a reliable and consistent performance across various uses.
2. Thermal and Mechanical Performance
Thermal Properties: Nelco and Isola PCBs both shine when it comes to managing heat, but they take different paths to get there. Nelco materials are crafted to deliver solid thermal stability, making them a go-to choice for high-heat applications, like those in the automotive and telecommunications sectors. This heat resistance is often reflected in the temperature ratings of their laminates, which makes them perfect for tough environments. So, if you’re looking for boards that can handle the heat without breaking a sweat, Nelco’s got your back!
Mechanical Strength: When it comes to mechanical performance, Nelco materials often have a reputation for superior mechanical properties, which can result in better durability in high-layer count designs. Isola materials also provide good mechanical integrity, but they might not always match the robustness of Nelco’s offerings, especially in applications with extreme conditions.
3. Applications and Use Cases
Both Nelco and Isola PCBs are suitable for high-frequency applications, but their specific use cases may differ:
Nelco PCBs: These are frequently chosen for complex multilayer designs in high-speed communications, RF applications, and advanced computing systems. Their versatility in material selection allows manufacturers to customize solutions that meet unique project specifications.
Isola PCBs: While also used in high-frequency environments, Isola PCBs are often found in consumer electronics and automotive applications where a standardized solution is sufficient. Their use of copper-clad dielectrics supports reliable mass production without compromising quality.
Comparison Table: Nelco vs. Isola PCB
Feature | Nelco PCB | Isola PCB |
Material Composition | Various laminates and prepregs | Copper-clad dielectrics |
Thermal Performance | High thermal stability | Good thermal management |
Mechanical Strength | Superior mechanical properties | Reliable but may vary |
Applications | Telecommunications, RF, advanced computing | Consumer electronics, automotive |
Flexibility | Highly customizable | More standardized |
When it comes to choosing between Nelco and Isola PCBs, it ultimately depends on your specific project requirements. If you’re in the market for a tailored high-frequency PCB solution, Nelco might be your best bet. However, if you need a reliable, standardized board, Isola offers great options too!
How Do Taconic PCBs Differ from Nelco PCBs?
When comparing Taconic and Nelco PCBs, the differences primarily arise from the types of materials utilized in their construction, which directly impact their performance, applications, and suitability for various electronic designs. Let’s take a closer look at these distinctions.
1. Material Composition
Taconic PCBs: These boards predominantly utilize PTFE (Polytetrafluoroethylene) laminates. PTFE is known for its excellent thermal stability and low dielectric constant, making it a favorite for high-frequency applications. This material is particularly advantageous in RF and microwave designs, providing low signal loss and high performance at elevated temperatures.
Nelco PCBs: In contrast, Nelco employs a diverse range of materials including:
●High-Speed Epoxy: Ideal for high-frequency applications, ensuring minimal signal degradation.
●FR-4: A widely used material that balances cost and performance for many electronic applications.
●High-Tg Epoxy: Suitable for applications that experience high thermal stress.
●Enhanced Materials: Such as cyanate ester, BT, and polyimide, which are employed to improve performance characteristics in demanding environments.
This variety allows Nelco PCBs to cater to a broader range of applications, from telecommunications to automotive electronics.
2. Performance and Application Suitability
Thermal and Electrical Performance-
●Taconic PCBs: The use of PTFE contributes to exceptional thermal stability, making these boards perfect for high-frequency applications like satellite communications and advanced RF systems.
●Nelco PCBs: With their range of materials, Nelco boards excel in diverse applications, including high-speed computing and automotive, where a balance of thermal performance and electrical reliability is necessary.
3. Fabrication of Enhanced Multilayer PCBs
Both Taconic and Nelco PCBs support the fabrication of enhanced multilayer designs. However, the specific material characteristics will influence the design process and final performance. For instance, Taconic’s PTFE laminates enable robust performance in environments requiring low signal loss, while Nelco’s mix of materials allows for flexible design choices catering to a variety of applications.
4. Quality Certifications
Both Taconic and Nelco PCBs are subject to rigorous quality certifications to ensure reliability and compliance with industry standards. For Nelco PCBs, notable certifications include:
●Underwriters’ Laboratory (UL) Certification
●RoHS Compliance: Ensuring reduced hazardous substances in electronic equipment.
●Conformité Européenne (CE) Regulation
●ASTM and ISO Quality Standards
These certifications reinforce the trust in Nelco PCBs, affirming their commitment to quality and safety.
Taconic vs. Nelco PCB
Feature | Taconic PCB | Nelco PCB |
Material Composition | Predominantly PTFE laminates | Variety of materials (high-speed epoxy, FR-4, etc.) |
Thermal Performance | Excellent thermal stability | Good thermal stability, tailored for application needs |
Application Focus | High-frequency and RF applications | Broader applications including automotive and computing |
Multilayer Capability | Supports enhanced multilayer PCBs | Supports enhanced multilayer PCBs |
Quality Certifications | UL certified, RoHS compliant | UL certified, RoHS compliant, CE, ASTM, ISO standards |
When deciding between Taconic and Nelco PCBs, consider your specific application needs. If high-frequency performance and thermal stability are your primary concerns, Taconic may be the way to go. However, if you require a versatile PCB that can adapt to various applications with a range of material options, Nelco stands out.
Application-Specific Use Cases for Nelco Laminates
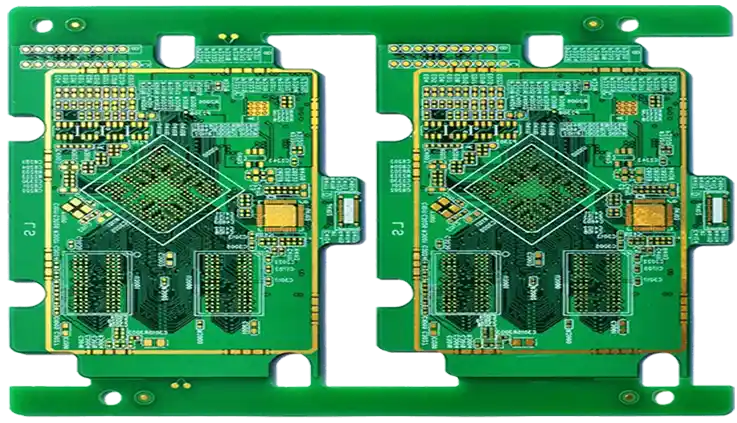
When it comes to specialized applications, Nelco laminates really step up as top materials for demanding environments. Their unique properties make them suitable for a wide range of sectors, ensuring technology keeps cruising along without any hiccups. Let’s dive into some specific scenarios where these laminates excel.
Telecommunications and 5G Infrastructure
In the bustling world of telecommunications, even a minor signal disruption can throw everything off balance. That’s where Nelco’s low-loss laminates, like the N4000-13, step in. With a lower dissipation factor, these materials significantly reduce signal loss, ensuring that data flows effortlessly across the network.
Why Nelco Laminates Matter in 5G?-
In the world of 5G infrastructure, reliability is everything. Antenna arrays and base stations rely on consistent signal transmission to ensure top-notch connectivity. When engineers select N4000-13, they’re opting for a material that can truly take the heat, both in terms of temperature and performance! These laminates are designed to withstand high-frequency operations, making them ideal for maintaining strong connections in busy urban areas.
Key Properties of Nelco N4000-13 for Telecommunications
Property | N4000-13 |
Glass Transition Temperature (°C) | 170-180 |
Dissipation Factor (Df) | 0.02-0.03 |
Thermal Conductivity (W/mK) | 0.3 |
CAF Resistance | Excellent |
In a recent project, a telecommunications company found that switching to N4000-13 improved their signal strength by nearly 30% in challenging urban environments. That’s no small potatoes! This kind of boost not only enhances customer satisfaction but also ensures smoother operations. So, if you’re in the telecom biz, don’t just stick with the old guard—make the switch to Nelco and keep your systems running like a well-oiled machine!
Automotive Sensors and Advanced Driver Assistance Systems (ADAS)
The automotive industry is no cakewalk; it’s a high-pressure arena where electronics undergo intense thermal and mechanical strain. With systems like Advanced Driver-Assistance Systems (ADAS) that rely heavily on sensors for both safety and performance, selecting the right materials can be the deciding factor between a smooth journey and a rough ride.
How Nelco Laminates Handle the Heat?-
N4000-29 and similar laminates are designed to thrive in high-temperature environments, making them ideal for automotive applications. Imagine a car cruising down the highway, packed with sensors and control units working overtime. With Nelco’s materials, those components can operate without a hitch, even when the heat is on!
Applications: Take, for instance, a major automotive manufacturer that integrated N4000-29 into their latest ADAS. They reported that the stability of their sensors improved significantly, leading to better real-time data processing and, ultimately, enhanced safety features. When you’re talking about keeping drivers and passengers safe, every detail counts.
Key Properties of Nelco N4000-29 for Automotive Applications
Property | N4000-29 |
Glass Transition Temperature (°C) | 180-190 |
Dissipation Factor (Df) | 0.02-0.04 |
Thermal Conductivity (W/mK) | 0.4 |
CAF Resistance | Superior |
Key Electrical and Thermal Properties of Nelco Materials
Understanding the electrical and thermal properties of materials is a must for engineers designing high-performance PCBs. Nelco laminates deliver impressive characteristics that set them apart from traditional substrates. Let’s dive into the specifics!
Dielectric Constant (Dk) and Signal Integrity
Maintaining signal integrity is non-negotiable in high-frequency designs. The dielectric constant (Dk) of a laminate can significantly influence the performance of RF circuits, especially in telecommunications. Nelco laminates provide a consistent Dk across a wide range of frequencies, which translates to smoother data flow and reduced crosstalk.
The Importance of Consistency in Dk-
In high-frequency applications, variations in Dk can lead to signal degradation, resulting in potential data loss. With Nelco materials, engineers can expect a Dk stability that supports high-frequency signal transmission. For instance, the N4000-13 laminate maintains a Dk of approximately 3.2-3.5, making it a solid choice for RF circuit design. This stability means fewer headaches down the road and better overall performance.
Example: A leading telecommunications provider integrated Nelco laminates into their RF modules, reporting a 25% increase in signal fidelity compared to previous designs using standard FR-4. That’s no small feat! The enhanced signal integrity allows for clearer communications, enabling the rollout of next-gen services. So if you’re looking to boost your signal quality, it’s time to consider Nelco!
Comparison of Dk Values for Nelco Laminates
Laminate Type | Dk Range |
Nelco N4000-13 | 3.2-3.5 |
Nelco N4000-29 | 3.4-3.6 |
Standard FR-4 | 4.0-4.5 |
Thermal Expansion and Reflow Process Compatibility
When it comes to lead-free reflow soldering, the last thing engineers want is warping. Nelco’s high Tg laminates are designed to withstand the thermal stresses of reflow processes, maintaining their structural integrity even under extreme conditions. This durability helps prevent delamination and ensures compatibility with multilayer boards.
Understanding Thermal Expansion-
Thermal expansion is a real concern when different materials expand and contract at varying rates. Nelco laminates are engineered to minimize these discrepancies, allowing for a smoother assembly process and more reliable end products. This means fewer production delays and reworks, which is music to any engineer’s ears!
Case in Point: Consider a manufacturer who used Nelco N4000-29 for a complex multilayer PCB. They noted that the laminate’s high Tg allowed them to conduct multiple reflow cycles without any signs of warping or delamination. This performance translates directly to cost savings and increased reliability for the end product—something every manufacturer can get behind.
Thermal Properties of Nelco Laminates
Property | Nelco N4000-13 | Nelco N4000-29 | FR-4 |
Glass Transition Temperature (°C) | 170-180 | 180-190 | 130-150 |
Coefficient of Thermal Expansion (CTE) | 17-20 ppm/°C | 15-18 ppm/°C | 20-25 ppm/°C |
Maximum Reflow Temperature (°C) | 260 | 260 | 260 |
Manufacturing and Assembly Processes with Nelco Laminates
The journey from idea to finished product can be quite the adventure, especially in the bustling electronics sector. When manufacturers choose for Nelco laminates, they find a dependable ally that makes the whole process smoother and more efficient. Let’s take a closer look at how these materials support everything from initial prototyping to high-volume production, as well as their application in flexible design projects. Whether you’re just getting started or scaling up, Nelco laminates help keep things on track and ready for whatever challenges come your way!
From Prototyping to High-Volume Production
In the PCB world, timing is everything. Whether you’re whipping up a quick-turn prototype or scaling up for a large production run, Nelco laminates consistently deliver predictable performance that manufacturers can count on. This reliability translates into reduced lead times without sacrificing quality.
Streamlined Processes-
Using Nelco materials in PCB manufacturing can make all the difference. With turnkey assembly services, companies can quickly adapt to changing demands while maintaining rigorous quality standards. This adaptability means manufacturers can take on last-minute projects without breaking a sweat.
Take, for example, a tech startup that needed to develop a prototype for a new wearable device. By choosing Nelco laminates, they were able to cut their prototyping time in half, getting their product to market faster than competitors. The same materials were then scaled for mass production, resulting in consistent quality across thousands of units.
Advantages of Using Nelco Laminates in Manufacturing
Aspect | Benefit |
Turnaround Time | Reduced from weeks to days |
Quality Control | Consistent performance across all batches |
Flexibility | Easily adapts to design changes |
Rigid, Flex, and Rigid-Flex PCB Designs
As technology advances, the demand for flexible and rigid-flex PCB designs is on the rise, especially in industries like wearables and aerospace. Nelco materials are engineered to meet these evolving needs, striking the perfect balance between mechanical flexibility and high-frequency stability.
The Rise of Flexible Designs-
Incorporating Nelco laminates into flexible designs means you can bend the rules—literally! These laminates allow for the creation of compact and lightweight circuits without compromising on performance. Whether it’s a sleek fitness tracker or an intricate aerospace control panel, Nelco materials can handle the job.
Case in Point: A leading aerospace manufacturer integrated Nelco’s rigid-flex designs into their latest flight control systems. They reported that the flexibility of these materials allowed for a 20% reduction in weight while improving the overall reliability of their systems.
Comparison of Rigid, Flex, and Rigid-Flex PCB Designs
Design Type | Key Characteristics | Typical Applications |
Rigid | High stability, suited for static designs | Consumer electronics |
Flex | Flexible and lightweight | Wearable devices, medical equipment |
Rigid-Flex | Combines rigidity with flexibility | Aerospace, automotive |
Signal Integrity Solutions for PCB Designers
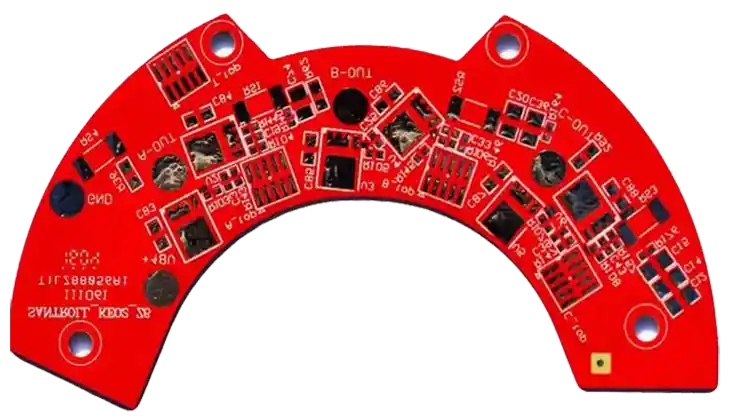
In PCB design, signal integrity can determine the success of a project. Ensuring that signals move smoothly through circuits without interference or distortion is key. When dealing with multilayer boards, challenges such as crosstalk and impedance mismatch can complicate matters. This is where Nelco materials come in, providing reliable electrical properties that help keep your circuits aligned. With Nelco, you can tackle these challenges effectively, ensuring your designs operate efficiently and without a hitch!
Reducing Signal Loss and Crosstalk in Multilayer PCBs
Crosstalk and signal loss can be like uninvited guests at a party—nobody wants them there. They can cause data corruption and lead to the dreaded “failure to communicate” in your circuits. Fortunately, with the right materials, designers can build multilayer PCBs that maintain clean signal paths, even in complex environments.
Understanding Impedance Matching-
Impedance mismatch is a common culprit behind signal integrity issues. When different layers of a PCB have varying impedance, signals can reflect back, leading to potential data loss. Using Nelco laminates with predictable electrical characteristics can simplify this process. Designers can easily calculate and maintain consistent impedance throughout the board, resulting in smoother signal transmission.
Signal Integrity Challenges and Solutions
Challenge | Description | Solution with Nelco Materials |
Crosstalk | Interference between adjacent signal paths | Low-loss laminates to minimize interference |
Impedance Mismatch | Reflection of signals at layer transitions | Predictable Dk values for easier matching |
Signal Attenuation | Loss of signal strength over distance | High-quality materials that preserve signal strength |
Optimizing Data Rates in Telecommunications-
A telecommunications company faced significant signal integrity issues in their multilayer PCB designs, affecting data rates and overall system performance. By integrating Nelco laminates, they managed to enhance signal clarity and reduce crosstalk by over 30%. This upgrade not only improved data rates but also reduced the number of failed transmissions, boosting the company’s reputation in the market.
Best Practices for PCB Design with Nelco Laminates
When designing PCBs with Nelco laminates, a thoughtful approach can significantly enhance the performance and reliability of your final product. Here are some best practices to consider:
Consider Layer Stackup
Layer stackup is like the foundation of a house—get it right, and everything stands strong. In PCB design, a well-thought-out layer stackup is key to maintaining impedance control and minimizing electromagnetic interference (EMI).
●Maintain Consistent Impedance: Aim for a uniform distance between layers to ensure consistent impedance throughout the PCB. This will help prevent reflections and signal integrity issues.
●Use Reference Planes: Implementing solid ground and power planes can reduce noise and enhance signal stability. Consider a stackup that balances the dielectric material thickness to achieve optimal performance.
Example of Layer Stackup Design
Layer Type | Material | Thickness |
Signal Layer 1 | Nelco N4000-13 | 0.2 mm |
Ground Plane | Copper | 0.35 mm |
Signal Layer 2 | Nelco N4000-29 | 0.2 mm |
Power Plane | Copper | 0.35 mm |
Use Simulation Tools
Simulation tools are your best buddies in the design process. They can help you predict how signals will behave, ensuring you choose the right materials for high-frequency designs.
●EM Simulation Software: Tools like ANSYS HFSS or CST Microwave Studio can simulate how electromagnetic fields interact with your PCB layout. This allows you to optimize component placement and routing for better performance.
●Signal Integrity Analysis: Conducting signal integrity analysis early in the design phase helps catch potential issues before they become costly problems down the line. Utilizing simulation tools can give you the confidence that your design is ready for production.
How to Choose the Right Nelco Laminate for Your Application?
Selecting the appropriate Nelco laminate is a critical step in ensuring your PCB meets performance expectations. Here’s a breakdown of key factors to consider when making your choice:
Frequency Considerations
Knowing the operating frequency of your application is a must. Nelco laminates are designed for specific frequency ranges, ensuring that you get the right fit for your needs. Therfore, different Nelco laminates are tailored for specific frequency ranges.
High-Frequency Applications: If you’re diving into high-frequency RF designs, consider the N4000-29. It’s engineered to maintain signal integrity and minimize loss, making it a perfect fit for 5G antennas and other RF applications.
General High-Tg Applications: The N4000-13 laminate is a fantastic choice for applications where thermal properties are a priority but the frequency demands aren’t as stringent. This laminate can handle diverse operating conditions while delivering consistent performance.
Frequency Comparison Table
Laminate Model | Operating Frequency Range | Best Use Case |
N4000-29 | Up to 40 GHz | RF Designs, 5G Applications |
N4000-13 | Up to 20 GHz | General High-Tg Applications |
Thermal Requirements
The thermal environment greatly influences laminate selection. Understanding the temperature profiles your application will face is essential.
Extreme Heat Conditions: If your application is exposed to high temperatures, laminates with a higher Tg (Glass Transition Temperature) are the way to go. For example, the N4000-29 can withstand higher thermal stress, ensuring that your circuits operate effectively even under demanding conditions.
Standard Thermal Environments: For applications with moderate thermal exposure, the N4000-13 laminate provides reliability without the added cost of higher Tg materials.
Thermal Performance Table-
Laminate Model | Tg (°C) | Recommended Temperature Range | Application Suitability |
N4000-29 | 170 | -40 to 130 | High-Temperature Applications |
N4000-13 | 155 | -40 to 85 | Standard Temperature Applications |
Cost vs. Performance
Navigating the balance between budget and performance can be tricky. Understanding the long-term benefits of each laminate type can help justify the initial costs.
Investment in Quality: While the N4000 series laminates may come with a higher upfront cost, their superior performance often leads to fewer failures and reduced maintenance costs over time. Think of it as a long-term investment in reliability.
Cost-Effective Options: If your project has budget limitations, laminates like the N4000-13 offer solid performance without putting a strain on your wallet, particularly for applications that aren’t too demanding.
Cost-Benefit Analysis Table-
Laminate Model | Upfront Cost | Long-Term Benefits | Best for Budget-Conscious Projects |
N4000-29 | High | High durability, fewer replacements | Not recommended |
N4000-13 | Moderate | Reliable performance for standard use | Recommended for budget-sensitive needs |
Don’t roll the dice on your laminate selections! Dive deep into the details of your application and see how each Nelco laminate can hit the mark with your goals. Reach out to our team for expert advice customized just for you, making sure your PCB designs and manufacturing are all set for success!
Why Choose Us?
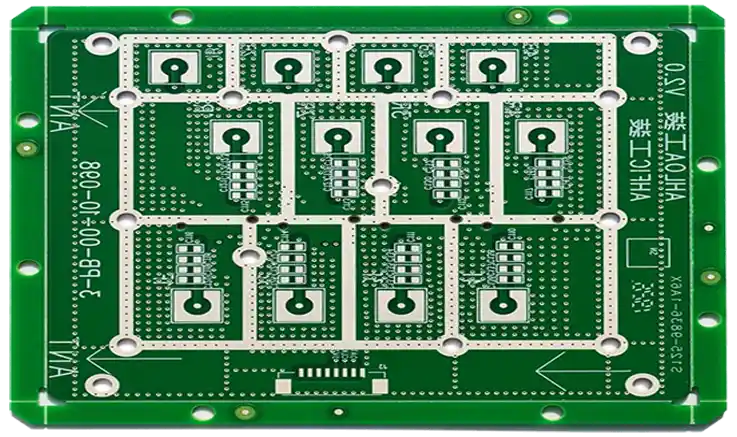
We Are Your Leading Nelco PCB Supplier in China
At JarnisTech, we take pride in being a premier manufacturer of Nelco PCBs, leveraging cutting-edge RF technology and digital microwave capabilities primarily to support the telecommunications infrastructure and internet technologies. Our commitment to quality ensures that our PCBs meet the rigorous demands of today’s high-performance applications.
Diverse Applications for Nelco PCBs-
We offer an extensive range of Nelco PCBs suitable for various high-end computing and automotive applications. Our products excel in environments requiring top-tier mechanical and electrical properties, making them ideal for complex high-layer digital layouts.
Our Nelco PCBs are engineered for:
●Low Loss/High-Speed Designs: Perfect for intricate multilayer configurations that require precise line specifications.
●Backplane Applications: Designed to handle multiple signal layers, ensuring efficient data transfer.
●Networking Communication Servers: Optimized for robust performance in networking systems.
●Wireless Technology and Mobile Devices: Tailored for the latest in wireless communication, from mobile phones to IoT devices.
●Automotive Electronics: Crafted to withstand the unique challenges faced in automotive applications.
●Versatile Containers and Mounts: Suitable for diverse mounting solutions, enhancing installation flexibility.
Quality and Performance You Can Count On-
One of the standout features of JarnisTech’s Nelco PCBs is their exceptional CAF resistance (Conductive Anodic Filament) and thermal stability, particularly during lead-free assembly processes. This reliability helps ensure that your products perform consistently under varying conditions, reducing the risk of failures and downtime.
We utilize a variety of high-quality materials in our manufacturing process, including:
●FR4: A well-known material providing a good balance of performance and cost.
●High-Speed Epoxy Prepreg/Laminate: Ideal for fast-paced applications requiring rapid signal transmission.
●Advanced Circuit Materials: Such as polyimide, cyanate ester, and BT, which enhance thermal performance and stability.
Why Choose JarnisTech?
Are you on the hunt for superior Nelco PCBs for your electronic or business projects? Look no further! Shopping with a reputable manufacturer like JarnisTech guarantees that you receive top-quality products tailored to meet your specific needs.
Let’s elevate your projects to the next level! Connect with us today to explore our range of Nelco PCBs and discover how we can support your innovative solutions. Experience the difference with JarnisTech—your trusted partner in high-quality PCB manufacturing!
Frequently Asked Questions (FAQ) About Nelco PCBs
What are the advantages of using Nelco over FR-4?
Nelco offers higher Tg, low Df, and better CAF resistance, making it a superior option for high-frequency and automotive applications.
Can Nelco materials handle lead-free assembly?
Yes, they support RoHS-compliant lead-free soldering processes.
What industries benefit most from Nelco PCBs?
Key industries include telecommunications, automotive, medical electronics, and aerospace.
How do Nelco laminates ensure signal integrity?
They provide low Df and stable Dk values, reducing crosstalk and maintaining clear signals in RF circuits.