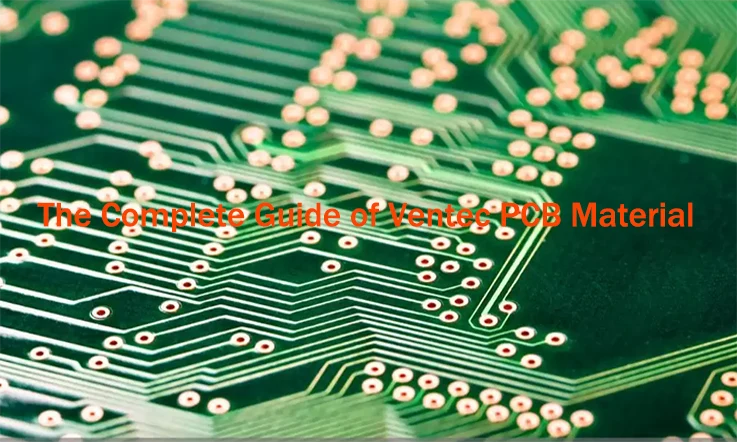
In today’s highly competitive electronics landscape, precision and reliability are non-negotiable. Whether you’re designing the latest automotive electronics, high-frequency communication systems, or intricate aerospace components, the materials you choose for your Printed Circuit Boards (PCBs) play a significant part in ensuring performance. Among the key players in the PCB material market, Ventec PCB materials stand out for their superior thermal management, signal integrity, and versatility across industries.
Ventec PCB materials have gained widespread recognition for offering high-quality laminates that meet the demanding specifications of various industries. In this guide, we will explore what makes Ventec materials ideal for high-performance applications, the range of products available, and how their advanced features can be leveraged in PCB design and manufacturing.
Types of Ventec PCB Materials for Specialized Use
Selecting the right PCB material is foundational in developing efficient, long-lasting, and high-performance electronics. Ventec offers a range of PCB materials specifically engineered for specialized applications, each with unique properties and benefits that make it an ideal choice for industries with high demands. Whether the priority is heat resistance, frequency stability, or durability, Ventec materials cover all bases, and here’s why they’re trusted by leading manufacturers.
Properties and Benefits of Polyimide Ventec PCB Materials
Polyimide is known for its resilience in high-temperature and harsh environmental conditions, making it a popular choice for aerospace and military electronics. Ventec’s polyimide materials go through rigorous thermal stability and chemical resistance testing, delivering a high-performance option that’s built to withstand the elements and the stresses of extreme applications.
In addition to their impressive thermal endurance (typically handling temperatures upwards of 200°C), these materials offer excellent mechanical stability, resisting cracking and warping under thermal cycling. This makes polyimide a robust choice for applications where both temperature resilience and long-term reliability are priorities.
Polyimide PCB Material Comparison-
Property | Industry Standard | Ventec Polyimide |
Temperature Resistance | 180°C – 220°C | 200°C – 260°C |
Peel Strength (lbs/in) | ≥ 8 | 10 |
Dielectric Constant (Dk) | 3.8 – 4.2 | 4.0 |
CTE (ppm/°C) | ≤ 50 | 45 |
Ventec’s polyimide exceeds standard expectations, offering reliable thermal resistance and structural stability even in prolonged use, a necessity for applications in defense electronics and aerospace.
High-Performance FR-4 and Copper-Clad Laminates
FR-4 laminates, enhanced with copper cladding, provide a versatile and cost-effective solution for numerous electronic products. Ventec’s high-performance FR-4 materials are engineered to ensure high Tg values and reduced thermal expansion, making them suitable for multilayer PCBs and fine-pitch component mounting.
These PCB laminates are highly customizable, allowing for variations in thickness, thermal conductivity, and copper weight, which is advantageous for applications where specific electrical and thermal properties are required. By offering stability in heat and minimal signal loss, Ventec’s FR-4 solutions stand out as a dependable choice in the development of advanced consumer electronics and industrial controls.
High-Performance FR-4 vs. Standard FR-4-
Property | Standard FR-4 | Ventec High-Performance FR-4 |
Glass Transition (Tg) | 135°C | 170°C |
Thermal Conductivity (W/mK) | 0.3 – 0.5 | 0.6 |
Peel Strength (lbs/in) | 7 | 10 |
Ventec’s FR-4 laminates bring added resilience, providing the performance consistency essential for high-tech consumer devices and manufacturing processes.
High-Frequency Laminate Options for RF and Microwave PCBs
When it comes to RF and microwave applications, high-frequency laminates are a must-have to keep signals intact and prevent any loss. Ventec’s high-frequency laminates are engineered with top-notch dielectric properties that minimize signal fade, ensuring smooth and reliable performance, no matter the frequency. These materials are a perfect fit for cutting-edge sectors like telecommunications and radar technology, where precision isn’t just a goal—it’s a necessity.
Ventec’s high-frequency laminates are built to keep the Dk (dielectric constant) and Df (dissipation factor) as low as possible, making sure there’s minimal signal loss even at high speeds. This means engineers can trust these materials to maintain steady signal integrity, ensuring their RF and microwave applications perform like clockwork. With these laminates, designers can relax, knowing their devices are going to work as expected, delivering reliable performance without any hiccups.
High-Frequency Laminate Specifications-
Property | Industry Standard | Ventec High-Frequency |
Dielectric Constant (Dk) | 3.2 – 3.8 | 3.4 |
Dissipation Factor (Df) | ≤ 0.003 | 0.0025 |
Thermal Conductivity (W/mK) | 0.5 – 0.8 | 0.8 |
Signal Loss (dB/m) | ≤ 0.1 | 0.08 |
With Ventec’s high-frequency laminates, electronic devices can run at higher speeds without losing their signal clarity—a big win for engineers working on complex RF applications. These materials keep things sharp and steady, so designers don’t have to worry about performance drops. Whether you’re working on telecommunications or radar tech, Ventec’s laminates are built to handle the fast-paced demands without skipping a beat.
Get Ready to Enhance Your PCB Designs with Ventec’s Specialized Materials
When it comes to specialized PCB applications, Ventec’s materials lead the pack. If you’re aiming for reliability, consistency, and performance in your designs, these laminates and prepregs offer the fine-tuned properties that make a difference. Connect with Jarnistech’s team today to discuss your specific needs and explore how their advanced materials can bring your designs to life.
Key Advantages of Ventec PCB Material in Critical Applications
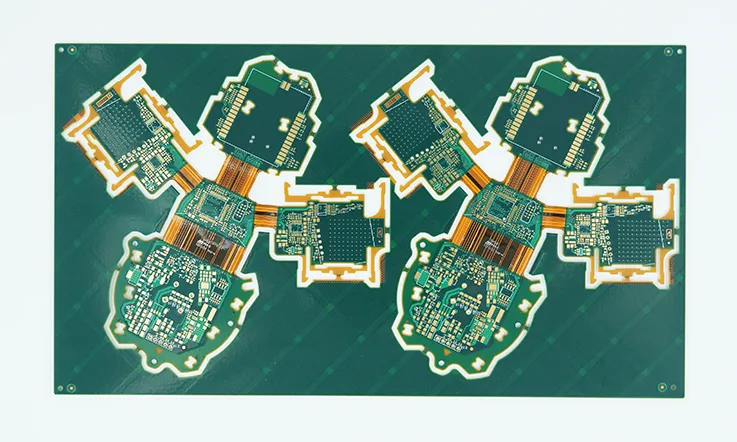
When designing for demanding environments, the choice of PCB material can make or break the performance of electronic systems. Ventec’s suite of materials stands out due to its exceptional thermal properties, reliability under stress, and adaptability for diverse industries. Below, we explore their standout features and how they excel in challenging applications.
Thermal Reliability of Ventec PCB Laminates in Automotive Electronics
Automotive systems, particularly in electric and hybrid vehicles, generate significant heat due to high-current operations. Ventec’s PCB laminates are engineered to handle these conditions with finesse. By using advanced materials with superior thermal conductivity and stability, these laminates prevent overheating and extend the lifespan of components.
One of the major advantages of Ventec materials lies in their ability to manage heat dissipation even under prolonged stress. For example, in electric vehicle power control modules, the laminates maintain consistent performance across wide temperature ranges, ensuring that systems such as inverters and motor drives operate without a hitch.
Thermal Properties of Ventec vs. Standard PCB Laminates-
Property | Standard Laminates | Ventec High-Tg Laminates |
Glass Transition (Tg) | 140°C – 170°C | ≥ 180°C |
Thermal Conductivity | 0.3 W/mK | 0.6 W/mK |
Decomposition Temp (Td) | 320°C | 350°C |
With Ventec’s materials, automotive manufacturers gain the peace of mind that their systems will perform seamlessly, even during peak operational demands.
Applications of Ventec PCB Materials in Aerospace and Defense Electronics
In aerospace and defense, PCBs are subjected to extreme conditions, from rapid temperature shifts to intense vibrations and electromagnetic interference. Ventec’s materials are designed to handle these challenges head-on, offering unmatched reliability and precision.
Features That Matter:
●Dimensional Stability: For radar and navigation systems where precision is non-negotiable, these materials ensure the highest level of accuracy. Whether it’s for tracking or navigation, these systems demand components that perform consistently and without failure.
●High-Frequency Performance: Ventec’s high-frequency laminates minimize signal distortion in communication equipment.
●Thermal Endurance: Ideal for avionics that operate in high-altitude environments.
For example, Ventec’s materials have been successfully integrated into military-grade UAVs (Unmanned Aerial Vehicles), where every ounce of weight matters and performance is non-negotiable. These materials stand up to intense thermal and mechanical pressures, maintaining reliable signal integrity even in the harshest conditions.
Comparison with Other Ventec PCB Laminates for High-Tg Needs
When choosing PCB laminates for high-thermal applications, it’s essential to align material properties with specific project requirements. Ventec offers a range of high-Tg laminates, each crafted to meet the unique demands of different industries. Whether you’re tackling extreme heat in automotive electronics or dealing with precision requirements in aerospace, Ventec’s selection provides options that hold up under pressure, ensuring that your designs stay strong and reliable, no matter the temperature.
Laminate Type | Typical Tg (°C) | Thermal Conductivity (W/mK) | Ideal Application |
Ventec VT-47 | 180 | 0.6 | Automotive and industrial control |
Ventec VT-901 | 220 | 0.8 | Aerospace and high-power electronics |
Ventec VT-4B Series | 200 | 0.7 | Consumer electronics and telecom |
The VT-901 series, for example, is an excellent choice for aerospace and defense applications due to its superior Tg value and low dielectric loss. Meanwhile, the VT-47 strikes a balance between cost-effectiveness and thermal stability, making it ideal for automotive industries.
Dielectric Properties and Signal Integrity in Ventec PCB Materials
In high-frequency and high-speed applications, how the PCB material interacts with electrical signals directly influences performance. The dielectric properties of these materials play a key role in controlling signal transmission, managing impedance, and optimizing the circuit’s overall behavior. Ventec’s range of PCB materials is specifically designed with precise dielectric characteristics, allowing engineers to create robust, high-performance circuits. This makes them a perfect match for industries such as telecommunications, automotive, aerospace, and medical electronics, where reliability and precision are a must.
When choosing a PCB material, engineers need to carefully consider how the material will interact with electrical signals. Properties like the dielectric constant (Dk) and dissipation factor (Df) are major players in determining how well the material allows signals to pass through without causing unnecessary loss, distortion, or interference. These factors become even more pressing in high-speed circuits where precision is everything. Ventec’s materials are engineered to boost signal integrity, delivering reliable and consistent performance across various frequencies and use cases, whether it’s for complex RF systems or automotive electronics.
Role of Dielectric Properties in High-Speed Applications
In high-speed circuit designs, the dielectric constant (Dk) helps define how a material responds to an electric field. It reflects how easily a material can become polarized when exposed to electrical energy. For high-speed applications, materials with a lower Dk are generally preferred, as they reduce signal delay and minimize unwanted interference or cross-talk. This ensures that high-frequency circuits remain reliable and efficient, even under demanding conditions.
For instance, the Ventec VT-47 laminate, specifically engineered for high-speed digital circuits, has a Dk of 3.45. This value makes it a great fit for high-speed signal transmission, as it minimizes delays and keeps the signal clean as it moves through the board. With such low Dk, the material helps avoid any unwanted noise or distortion, making it a top choice for applications where maintaining data clarity is a must—think communication systems or computing devices that rely on accuracy and reliability.
Additionally, in the design of high-frequency PCBs, such as those found in 5G networks or automotive radar systems, the impact of signal reflection and impedance mismatch must be mitigated. These challenges can be alleviated by selecting materials with carefully optimized dielectric properties. Ventec’s materials are engineered to maintain a consistent impedance profile over a wide frequency range, ensuring that signal reflections and distortions are minimized, thus preserving the signal integrity even at high speeds.
Achieving Signal Integrity with Ventec PCB Materials in RF Circuits
When working with Radio Frequency (RF) circuits, it’s necessary to track the dissipation factor (Df). Df indicates how much energy is lost as heat when a signal travels through the material. A lower Df means less energy is wasted, allowing the signal to travel with minimal distortion. This is especially relevant in RF applications, where maintaining signal quality and strength is a primary concern.
Ventec RF-35, for instance, is designed with an excellent Df of 0.004. This is a significant improvement over many conventional PCB materials, which have higher dissipation factors, leading to greater loss at high frequencies. The low Df of Ventec RF-35 ensures that RF signals maintain their strength and integrity, even in long-distance or high-demand environments such as satellite communication, military radar systems, or industrial RF equipment.
Moreover, the thermal stability of Ventec’s materials helps preserve signal integrity over extended periods. In RF circuits, which often operate in challenging environments, temperature fluctuations can lead to physical changes in the PCB material, potentially causing signal degradation or even failure. Materials like Ventec’s VT-5 are engineered with robust thermal stability, ensuring that the material’s properties remain stable and predictable, even in the face of extreme temperature changes. This capability makes these materials ideal for use in situations where consistent performance is required despite environmental stressors.
Choosing Ventec PCB Materials for Optimal Signal Stability
Choosing the right PCB material is a balancing act between dielectric constant, dissipation factor, and thermal stability. For applications that require stable signal transmission under varying conditions, Ventec PCB materials like Ventec VT-47 and Ventec VT-5 provide the best of all worlds.
Consider the impact of high-frequency signal stability in sectors like aerospace, automotive, and industrial applications. In these fields, temperature fluctuations, mechanical stress, and long-term durability are often part of the equation. Materials such as Ventec VT-47 excel here, providing excellent thermal conductivity and low dielectric loss. Their ability to maintain impedance over extended periods of use ensures long-term signal integrity, making them a reliable choice for mission-critical applications.
Moreover, engineers need to carefully evaluate the performance of the PCB material at the operational frequencies. For instance, Ventec RF-35 provides superior performance at frequencies typically used in 5G and microwave communication, ensuring that signal losses due to high-frequency effects are kept to a minimum.
The table below summarizes the critical dielectric and electrical properties of various Ventec PCB materials, highlighting their suitability for specific applications:
Material | Dielectric Constant (Dk) | Dissipation Factor (Df) | Thermal Conductivity (W/m·K) | Ideal Frequency Range (GHz) | Operating Temperature Range (°C) |
Ventec VT-47 | 3.45 | 0.002 | 0.75 | 1 – 15 | -40 to 150 |
Ventec RF-35 | 3.30 | 0.004 | 0.70 | 1 – 20 | -40 to 130 |
Ventec VT-5 | 3.15 | 0.003 | 0.80 | 0.5 – 10 | -40 to 140 |
Thermal Management Capabilities in Ventec PCB Materials for Extreme Conditions
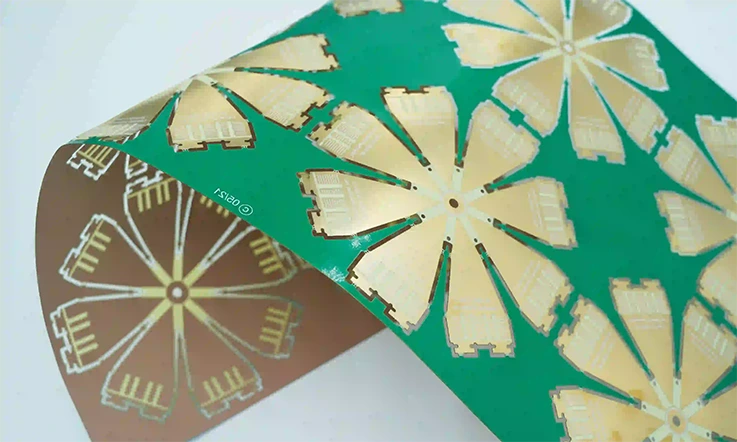
In applications that demand high reliability under extreme temperatures, thermal management becomes a top priority. Whether you’re working with automotive electronics, aerospace applications, or high-power computing, the ability to effectively manage heat within a PCB is no longer optional—it’s a must. Ventec PCB materials are designed to meet these challenges, offering enhanced thermal stability and heat dissipation capabilities that help maintain the integrity of your circuits under the harshest operating conditions.
Thermal management in PCBs involves several key factors, such as thermal conductivity, glass transition temperature (Tg), and coefficient of thermal expansion (CTE). These properties work together to ensure that your PCB can not only withstand extreme temperatures but also dissipate heat efficiently, preventing circuit failures due to overheating or thermal stress. In this section, we’ll explore how Ventec’s thermal management materials provide solutions for high-performance applications.
Enhancing Heat Dissipation with Ventec Laminates
When it comes to high-performance electronic applications, the efficiency of heat dissipation is a defining factor in system reliability. Ventec PCB laminates are engineered with advanced thermal conductivity to move heat away from sensitive components. This allows the system to perform reliably, even in high-power situations.
Ventec materials such as VT-5 and VT-47 are designed with high thermal conductivity properties that ensure efficient heat transfer. These materials are ideal for designs where heat must be removed quickly to avoid component degradation or failure. The high thermal conductivity of Ventec VT-5 makes it particularly well-suited for use in automotive or telecommunications equipment, where heat generated by components like processors and power transistors needs to be dissipated rapidly to ensure stable operation.
For instance, Ventec VT-47 has a thermal conductivity of 0.75 W/m·K, which helps regulate the temperature by allowing heat to move away from sensitive components. With better heat dissipation, these materials also help prevent thermal accumulation, which could otherwise cause damage over time.
To compare the thermal properties of some of Ventec’s top laminates:
Material | Thermal Conductivity (W/m·K) | Glass Transition Temperature (Tg) (°C) | Coefficient of Thermal Expansion (CTE) |
Ventec VT-5 | 0.80 | 180 | 13 ppm/°C |
Ventec VT-47 | 0.75 | 170 | 14 ppm/°C |
Ventec RF-35 | 0.70 | 150 | 15 ppm/°C |
This table shows how Ventec laminates compare in terms of thermal conductivity, Tg, and CTE. These factors all contribute to a material’s ability to manage heat effectively and remain stable in high-temperature environments.
Prepreg Options to Support Thermal Management in PCBs
Another significant component in PCB thermal management is the use of prepregs—materials that are impregnated with resin to form the matrix of the PCB. The right prepreg material can significantly enhance the thermal performance of the board, ensuring that heat is evenly distributed and dissipated efficiently.
Ventec’s prepregs are available in a variety of formulations that cater to different needs. For high-power applications, Ventec’s high-Tg prepregs are designed to handle the heat generated by high-performance components. The Tg of the prepreg is the temperature at which the resin transitions from a rigid to a more flexible state, and it directly impacts the board’s thermal stability. In high-performance applications, such as 5G infrastructure or electric vehicles, prepregs with a higher Tg are necessary to maintain the structural integrity of the PCB under thermal stress.
For example, Ventec’s VT-47 prepreg has a Tg of 170°C, ensuring that the material remains stable and maintains its electrical and mechanical properties even when exposed to extreme operating temperatures. It helps in preventing thermal degradation of the PCB structure, ensuring that the performance of the electronic devices remains unaffected even under high-power conditions.
Role of High-Tg Ventec PCB Materials in Thermal Stability
The glass transition temperature (Tg) of PCB materials plays a key part in determining their thermal stability. For applications that involve high temperatures, materials with a higher Tg are the preferred choice. These materials are more capable of handling thermal stress, which helps prevent issues like warping, delaminating, or the loss of mechanical integrity. This ensures that the PCB maintains its performance, even when exposed to elevated temperatures over time.
Ventec’s high-Tg PCB materials like VT-5 and RF-35 offer enhanced thermal performance. The higher the Tg, the better the material’s thermal stability, which is crucial in applications that operate at high temperatures or experience frequent thermal cycling. For instance, Ventec VT-5, with its Tg of 180°C, is ideally suited for automotive electronics, where high-temperature fluctuations are a common occurrence due to engine heat or other external environmental factors.
High-Tg materials help minimize thermal-induced failures, such as delamination and warping, which can be a major concern in applications like aerospace electronics, where precise performance is required in extreme conditions. Ventec VT-47, with a Tg of 170°C, is often used in telecommunications infrastructure, where equipment operates in outdoor environments with frequent temperature changes.
Designing Multi-Layer PCBs with Ventec Prepreg and Stack-Up Solutions
In advanced electronics, the design of multi-layer PCBs is a crucial factor for maximizing performance and reliability. Effective stack-up design directly impacts signal integrity, thermal management, and durability. Ventec’s range of prepreg and laminate materials supports a wide variety of stack-up configurations, enabling custom solutions that cater to the unique demands of each application.
With the rise in complexity of electronic devices, designers often face challenges like signal crosstalk, electromagnetic interference (EMI), and thermal dissipation. The right stack-up solution allows engineers to address these issues by strategically arranging layers and selecting prepregs that enhance electrical integrity and manage thermal loads efficiently. In this section, we’ll break down how Ventec’s multi-layer stack-up solutions help overcome design challenges in high-performance PCB manufacturing.
Optimizing Layer Stack-Up for Electrical Integrity and Performance
When designing multi-layer PCBs, selecting the right stack-up structure is key to achieving top-notch performance and electrical stability. Ventec’s offerings in multi-layer stack-ups cater to both rigid and flex-rigid designs, delivering flexible choices that align with diverse electrical needs.
A well-optimized stack-up arranges signal layers, ground planes, and power planes in a way that minimizes crosstalk and maintains signal clarity. For high-speed applications, maintaining low impedance and proper trace isolation are key. Ventec offers specialized laminates with low-loss and high-Dk (dielectric constant) properties, allowing signals to travel with minimal degradation, which is a boon for applications requiring fast signal processing.
To boost electrical performance even further, Ventec offers high-Tg prepregs that ensure strong bonding between layers, making them perfect for RF and microwave designs where keeping signals clean is a must. For example, when used in telecom or computing setups, materials like VT-47 or VT-901, with their solid thermal stability and great dielectric properties, keep signals steady—even when dealing with high power or intense heat.
Layer Stack-Up Example:
Layer Number | Function | Material | Property |
1 | Signal Layer | VT-47 | Low-loss, High Dk |
2 | Ground Plane | VT-901 | High Tg, Thermal Stable |
3 | Power Plane | VT-4B | Good Thermal Conductivity |
4 | Signal Layer | VT-47 | Maintains Signal Integrity |
This example demonstrates a basic four-layer stack-up, showcasing how Ventec materials are used to balance electrical integrity and thermal management.
Ventec Prepreg Options for High-Performance PCB Manufacturing
Ventec’s prepregs are developed to meet the specialized needs of multi-layer PCB designs. With options for high-Tg and low-Dk prepregs, Ventec provides the flexibility designers need to achieve their performance goals.
Prepreg materials act as the adhesive between PCB layers, ensuring that the board remains structurally sound while also enhancing thermal and electrical properties. For instance, VT-47 prepreg is an ideal choice for applications requiring a blend of thermal and electrical stability, such as automotive or industrial electronics. Its high Tg prevents warping and delamination, which is essential for boards exposed to fluctuating temperatures or mechanical stress.
In high-frequency designs, such as those in telecommunications or radar applications, VT-901 prepreg offers a low-Dk profile, ensuring that signals propagate with minimal attenuation. This makes it a strong contender for any design focused on signal fidelity in RF and microwave applications.
Prepreg Comparison Table:
Prepreg Type | Dielectric Constant (Dk) | Tg (°C) | Ideal Applications |
VT-47 | 4.3 | 170 | Automotive, Industrial Electronics |
VT-901 | 3.6 | 180 | RF, Microwave, High-Frequency Designs |
Benefits of Ventec Multi-Layer Configurations in Advanced Electronics
As technology continues to evolve, the demand for high-density multi-layer PCBs is growing in fields such as aerospace, medical devices, and high-performance computing. Ventec’s materials support multi-layer configurations that can tackle the unique challenges presented by these applications.
For example, in aerospace electronics, the use of high-density multi-layer boards is often necessary to handle complex circuits within a limited space. Here, Ventec’s materials provide both mechanical strength and thermal management, ensuring that the boards can endure the extreme environments often found in aerospace applications. The high-Tg laminates like VT-5A ensure dimensional stability and resistance to thermal cycling, which prevents delamination and warping over time.
In medical devices, especially in imaging equipment and portable electronics, multi-layer PCBs are used to house the intricate circuitry needed for precise functionality. Ventec’s stack-up solutions ensure that these multi-layer boards remain compact without sacrificing performance. The low-Dk materials also minimize signal loss, ensuring that sensitive equipment, such as MRI or ultrasound machines, maintains accurate data transmission without interference.
Certified Quality Control and IPC Standards in Ventec PCB Manufacturing
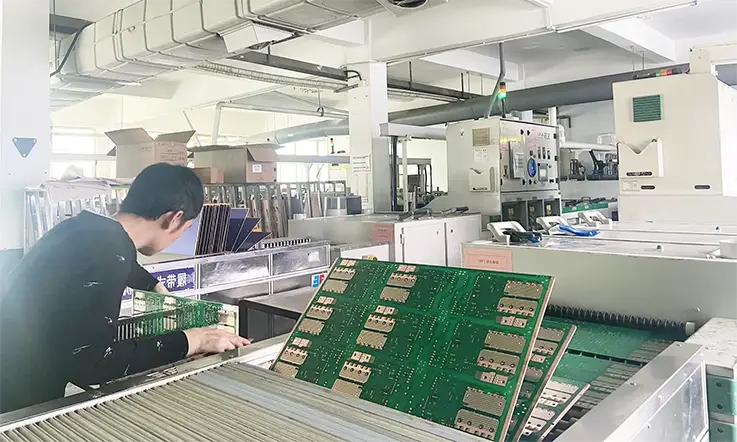
In the competitive field of PCB manufacturing, maintaining rigorous quality standards isn’t just a formality; it’s a commitment to delivering reliable, high-performance products. Ventec’s adherence to the IPC 4101 standards is a testament to that commitment, ensuring materials meet stringent requirements for quality and performance across a variety of industries. IPC 4101 covers performance specifications for laminate and prepreg materials used in PCBs, setting a recognized benchmark for consistency, durability, and reliability.
With Ventec’s certified quality control systems in place, clients across sectors such as aerospace, automotive, and telecommunications can trust in the dependability of the materials used in their critical applications. Let’s dive deeper into how IPC standards and quality certifications translate into tangible advantages for OEMs and PCB manufacturers alike.
Understanding IPC 4101 and Quality Certification in PCB Production
IPC 4101 specifies the standards for laminate and prepreg materials—setting comprehensive benchmarks for material durability, thermal performance, and electrical properties. For a PCB material to be IPC 4101 certified, it must undergo a series of quality checks and performance assessments that test its ability to maintain properties under stress, including temperature fluctuations, moisture exposure, and mechanical strain.
Ventec’s IPC 4101-certified materials are developed to ensure stability and uniformity, minimizing the risk of defects in final products. This certification is particularly critical in high-stakes industries, where any variation in material performance could lead to significant failures or safety concerns. Ventec’s commitment to IPC standards also extends to ongoing quality assessments—every production batch undergoes rigorous testing to confirm compliance with IPC standards, ensuring a stable supply chain that OEMs and manufacturers can trust.
IPC 4101-Certified Material Properties Table-
Material Property | Standard Value (per IPC 4101) | Ventec’s Certification Level |
Tg (Glass Transition Temperature) | ≥ 130°C | 170-190°C (varies by material) |
CTE (Coefficient of Thermal Expansion) | ≤ 3.0% | 2.8% or lower |
Dk (Dielectric Constant) | 3.5 – 4.5 | 3.6 – 4.3 |
Moisture Absorption (%) | ≤ 0.2% | 0.15% |
Flammability | UL94 V-0 | Compliant |
The table above shows a sample comparison of IPC 4101 requirements with the properties of Ventec’s certified materials, highlighting Ventec’s commitment to exceeding baseline specifications.
Benefits of Certification for OEMs and PCB Manufacturers
For OEMs and PCB manufacturers, using certified materials like those from Ventec can streamline production, reduce risk, and ultimately cut costs. When materials come pre-certified, manufacturers can eliminate extra testing phases and quality audits typically required to verify compliance. This means faster turnaround times and fewer headaches for manufacturers looking to stay on schedule.
Beyond operational efficiencies, certified PCB materials provide an extra layer of assurance in terms of product longevity and performance under extreme conditions. For instance, automotive and aerospace sectors, where exposure to high temperatures and fluctuating pressures is common, can rely on Ventec materials to sustain performance over time. In sectors where safety is non-negotiable, certified materials eliminate potential failure points and ensure devices operate reliably under varied environmental stresses.
The benefits also extend into customer satisfaction: end clients who see OEMs and PCB manufacturers using certified materials are more likely to trust in the product’s dependability. In an industry where trust is earned through consistency, Ventec’s certification processes offer an assurance of quality that builds client confidence.
Quality Control in Ventec PCB Material Manufacturing Processes
Ventec employs a robust quality control protocol throughout each stage of the PCB material manufacturing process. This begins with raw material selection, where only high-grade materials are used, and continues through every step, from prepreg production to laminate processing. Quality checks include moisture resistance tests, thermal cycling assessments, and mechanical durability checks, all conducted with advanced equipment to ensure precise measurements.
By consistently monitoring parameters such as resin content, thickness uniformity, and dimensional stability, Ventec is able to catch potential issues before they impact the final product. In-house laboratories equipped with advanced testing tools allow for real-time data analysis, enabling swift adjustments and improvements in response to test results.
Ventec’s process doesn’t end with testing; detailed records are maintained for every production batch, facilitating traceability and transparency for OEMs and manufacturers alike. This comprehensive approach to quality control underscores Ventec’s dedication to providing reliable, high-quality PCB materials, creating a strong foundation for any PCB project.
Advanced Manufacturing Techniques for Ventec PCB Materials
In today’s competitive market, precision and consistency in PCB manufacturing are non-negotiable. Ventec PCB materials stand out due to their advanced manufacturing techniques, which ensure top-tier performance, reliability, and environmental responsibility. Ventec leverages cutting-edge technologies to produce laminates and prepregs with unparalleled precision and consistency, fulfilling the demanding requirements of industries ranging from automotive to telecommunications.
Consistent Quality in Laminate and Prepreg Production
Ventec’s manufacturing process starts with meticulous control over the raw materials used to produce laminates and prepregs. Through state-of-the-art automation, Ventec guarantees high precision during the entire production process, ensuring that each batch meets strict quality standards.
The laminate and prepreg production begins with the careful selection of base materials, including fiberglass cloth and resin. This is followed by coating, curing, and lamination steps that are closely monitored to achieve consistent material properties, such as dielectric constant (Dk), glass transition temperature (Tg), and thermal stability. To ensure a uniform product, the manufacturing process incorporates continuous inspections and testing, allowing for real-time adjustments and minimizing potential variations.
Laminate and Prepreg Consistency Data-
Parameter | Standard | Ventec’s Average |
Dielectric Constant (Dk) | 3.5 – 4.5 | 3.6 |
Glass Transition Temperature (Tg) | ≥ 130°C | 170°C |
Moisture Absorption (%) | ≤ 0.2% | 0.15% |
Coefficient of Thermal Expansion (CTE) | ≤ 3.0% | 2.8% |
These consistency metrics showcase the precision that Ventec achieves during the manufacturing process, delivering materials with highly predictable and reliable characteristics.
Quality Assurance and Testing in Ventec PCB Fabrication
At Ventec, quality assurance is more than a process—it’s a commitment. With every batch of laminate and prepreg produced, the company uses a combination of in-line sensors and advanced testing to ensure that the materials meet or exceed industry standards. These testing procedures are designed to assess mechanical strength, thermal performance, and electrical integrity across a variety of real-world conditions.
Ventec employs multiple test protocols, including thermal cycling tests, moisture absorption tests, and flexural strength tests to simulate the most demanding environments. Additionally, each material batch undergoes visual inspections to check for any imperfections or inconsistencies. With dedicated quality assurance teams, Ventec maintains the highest standards throughout the entire production cycle, ensuring that clients receive nothing short of excellence.
Environmental Responsibility in Ventec PCB Production
Sustainability is integral to Ventec’s manufacturing process. With a growing focus on reducing the environmental impact of PCB production, Ventec has taken steps to minimize waste and emissions across all stages of its manufacturing process. From sourcing eco-friendly materials to optimizing energy efficiency during production, the company works continuously to align its operations with global sustainability goals.
For example, Ventec has introduced water-based resins and solvent-free technologies in its production lines to reduce volatile organic compound (VOC) emissions. By embracing green technologies and implementing waste recycling programs, Ventec ensures that their manufacturing process not only meets but exceeds environmental regulations in various regions, including REACH and RoHS compliance.
Environmental Impact Comparison-
Environmental Metric | Industry Standard | Ventec’s Commitment |
VOC Emissions (g per sq.m) | ≤ 10 g | ≤ 5 g |
Water Usage (L per unit) | 2-3 L | 1.5 L |
Energy Efficiency (%) | 70% | 85% |
Material Waste (%) | 3-4% | 2% |
This table illustrates Ventec’s superior environmental efforts, underscoring the company’s determination to minimize its ecological footprint while still producing high-performance, high-quality materials.
Why Choose Us?
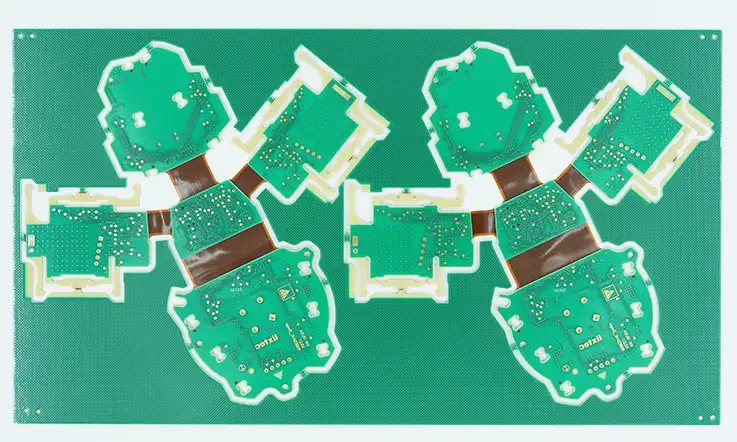
As a premier Ventec PCB manufacturer in China, JarnisTech combines cutting-edge technology, proven engineering, and extensive experience to provide exceptional PCB solutions. Here are the key benefits of working with us.
1. Cutting-edge Ventec PCB Manufacturing Technology
At JarnisTech, we leverage Ventec’s advanced materials alongside high-precision manufacturing techniques, ensuring unmatched performance in heat management, electrical integrity, and structural durability. Our manufacturing process includes automated optical inspection, precise layer alignment, and multi-layer lamination, resulting in reliable PCBs suited for rigorous environments.
●Precision Layer Alignment: In multilayer PCB fabrication, alignment accuracy is fundamental for electrical performance and signal integrity. We achieve a layer alignment accuracy of +/- 0.05mm, surpassing the industry standard of +/- 0.10mm and effectively minimizing potential signal interference and electrical noise.
●Full Automation in Optical Inspection: Unlike other manufacturers that typically achieve 70-80% inspection coverage, we implement 100% automated optical inspection to ensure defect-free products and enhanced reliability.
●High-Tg Material Expertise: For applications requiring heat resilience, we use Ventec materials with a Tg rating of up to 220°C, making our PCBs ideal for demanding applications like automotive electronics and industrial settings.
JarnisTech vs. Standard PCB Manufacturers:
Feature | JarnisTech | Standard Manufacturers |
Layer Alignment Accuracy | +/- 0.05mm | +/- 0.10mm |
Optical Inspection Coverage | 100% | 70-80% |
High-Tg Laminate Capability | Up to 220°C | Up to 180°C |
Our meticulous approach to manufacturing ensures robust PCB performance even in challenging environments.
2. Fast Delivery Time for Prototypes
JarnisTech is known for its quick delivery on prototype orders, allowing you to shorten your time to market. Our streamlined processes and automated equipment ensure that we maintain high standards of quality while offering rapid turnaround times. From single-layer boards to complex multilayer designs, we can deliver within industry-leading timeframes.
Prototype Type | Standard Delivery | Expedited Option |
Single-layer PCB | 1-2 days | 24 hours |
Multilayer PCB (4-6 layers) | 3-5 days | 48 hours |
High-Tg and HDI Boards | 5-7 days | 72 hours |
Our fast-delivery service empowers you with a competitive edge, bringing projects from design to production without delay.
3. 15+ Years of Engineering Expertise
With over 15 years in PCB manufacturing, our engineering team is highly skilled in process innovation and design optimization. Our engineers go beyond fabrication, working closely with clients from initial design through material selection and layer stack optimization, ensuring every stage of the project aligns with ultimate performance goals.
●Custom Stack-Up Design: We customize stack-ups to boost signal clarity and cut down on signal loss, which is a must for high-speed applications. This ensures that signals travel efficiently with minimal interference, making sure everything stays crisp and clear, even in demanding designs.
●Material Recommendation: We advise on materials based on thermal and electrical requirements, ensuring optimal product performance.
●Quality Control & Troubleshooting: Our engineers proactively identify and address potential issues early in production, reducing costs and enhancing final product reliability.
Our team’s expertise adds substantial value, making us more than just a manufacturing partner.
Trusted Ventec PCB Manufacturer in China – JarnisTech
As a reliable Ventec PCB manufacturer, JarnisTech is committed to producing high-quality PCBs that meet stringent industry standards. Our reputation for quality, durability, and service excellence has made us a preferred partner across automotive, medical, aerospace, and consumer electronics sectors worldwide.
JarnisTech PCBs are engineered for long-term performance and consistent stability, providing a robust solution for your application needs.
Ready to take your PCB project to the next level? Contact us today and experience the synergy of quality and efficiency in PCB manufacturing with JarnisTech!
FAQ
What makes Ventec PCB materials suitable for high-speed applications?
Ventec PCB materials are engineered with low dielectric constants (Dk) and low dissipation factors (Df), making them ideal for high-speed applications. These properties minimize signal loss and distortion, ensuring the transmission of clear and consistent signals, even in complex designs.
What types of PCB materials does Ventec offer?
Ventec offers a wide range of PCB materials, including standard FR4 laminates, high-frequency materials, high-Tg prepregs, and flexible materials. These materials are designed to meet the needs of various applications, from general-purpose PCBs to high-speed and RF circuits.
How does Ventec’s high-Tg material enhance PCB performance?
Ventec’s high-Tg (glass transition temperature) materials can withstand higher temperatures without losing their mechanical properties. This makes them perfect for applications that experience thermal stress, such as power electronics or automotive circuits, where temperature fluctuations can affect performance.
What makes Ventec’s PCB materials reliable in RF and microwave applications?
Ventec’s materials, such as VT-47 and VT-901, are specifically engineered for RF and microwave applications. They offer low loss, stable dielectric properties, and excellent thermal stability, ensuring consistent performance in high-frequency designs like telecommunications and radar systems.
Can Ventec PCB materials handle both rigid and flexible designs?
Yes, Ventec offers both rigid and flex-rigid PCB materials, making them versatile for a wide range of applications. Whether you need a traditional rigid board or a flexible design for compact or wearable electronics, Ventec has the materials to suit your needs.
What is the thermal stability of Ventec’s PCB materials?
Ventec’s PCB materials, especially their high-Tg products, are engineered for excellent thermal stability. These materials can withstand extreme temperatures without compromising their performance, ensuring long-term reliability in demanding applications such as automotive, industrial, and telecommunications.