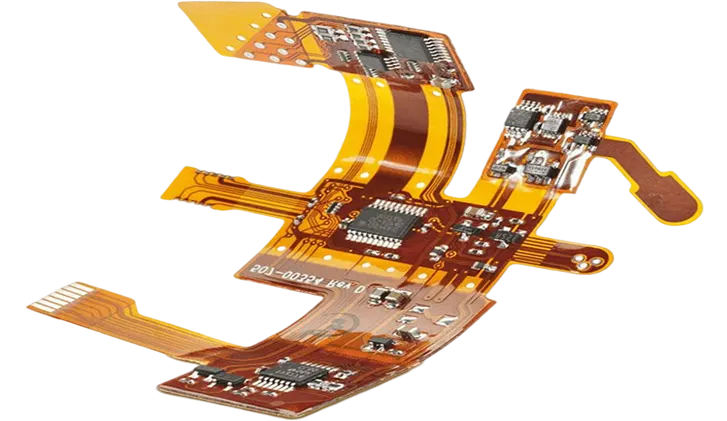
Whether you’re a startup building the next big thing or a Fortune 500 giant, JarnisTech has your back with a complete suite of PCB services—from components sourcing to manufacturing, assembly, and testing. We know how messy things can get when multiple vendors are involved, which is why we’re here to help you streamline your production, cut delays, and raise the bar on quality—all under one roof.
Flex PCB (Flexible Printed Circuit Boards) assembly offers unique opportunities and challenges compared to traditional rigid PCBs. As technology advances, flexible and rigid-flex circuits are becoming increasingly popular, particularly in automotive, medical, and wearable devices where lightweight, compact, and bendable designs are needed. This guide dives deep into the assembly processes, materials, equipment, and industry use cases for Flex PCBs. Whether you’re a design engineer, electronics manufacturer, procurement specialist, or an OEM, this article provides the insights you need.
Core Principles and Benefits of Flex (FPC) PCB Assembly
Flex PCBs, also known as Flexible Printed Circuit Boards, have become an integral part of modern electronic design due to their ability to conform to unique shapes and spaces. Unlike rigid PCBs, which are stiff and flat, FPC circuits offer a flexible solution, making them ideal for devices where weight, form factor, and durability are top priorities. From wearables and medical equipment to automotive electronics, these circuits help companies build compact, reliable products that meet high-performance requirements. Let’s take a closer look at what makes these boards so useful, and how they stack up against traditional rigid counterparts.
What Are Flex (FPC) Circuits?
Flex PCBs consist of layers of conductive traces laminated between flexible materials like polyimide (PI) or polyester (PET) films. This flexible construction allows them to fold, bend, or twist while maintaining electrical connectivity. The design eliminates the need for bulky connectors and cables, enabling seamless integration into compact spaces. Because of this flexibility, FPC assemblies are widely used in devices like smartphones, pacemakers, and automotive control systems.
One standout feature of FPCs is their ability to maintain performance under constant movement or vibration, which is particularly useful for medical wearables and industrial sensors. Additionally, double-sided flex PCBs allow for higher component density, making them suitable for IoT devices and foldable screens.
Why Choose Flex PCBs?
Space Efficiency-
Flex circuits offer an ingenious way to reduce the overall size of electronic assemblies. Their thin profile—typically ranging between 25 to 100 microns—allows manufacturers to fold or layer multiple circuits in confined spaces. Imagine trying to fit complex circuitry into a smartwatch or a hearing aid without sacrificing performance—this is where FPCs shine. For multi-layer designs, engineers can stack circuits without bulky connectors, creating compact modules that reduce assembly complexity.
Application | Space Utilization |
Smartphones | Slim battery compartments and foldable screens |
Automotive Displays | Curved dashboards with integrated controls |
Wearable Health Devices | Compact sensors for real-time monitoring |
Durability and Flexibility-
Flex circuits aren’t just about bending; they offer resilience against vibrations and mechanical stress. For instance, in automotive environments, flex boards withstand constant engine vibrations, while in medical devices, they survive repeated movements without losing signal integrity. Their ability to flex thousands of times without cracking makes them ideal for dynamic applications.
Additionally, FPCs are highly resistant to moisture, chemicals, and extreme temperatures—key factors for harsh environments like industrial equipment or aerospace control panels. Engineers often pair FPC assemblies with EMI shielding materials to protect signals from interference, ensuring consistent performance even in high-frequency communication systems.
Pro tip: When designing with flex circuits, always factor in the bend radius to avoid over-stressing the copper traces—this prevents potential failure down the road.
Weight Reduction-
In industries where every gram counts, such as aerospace and automotive, FPC assemblies offer a substantial advantage. By eliminating the need for connectors and wires, these circuits reduce the overall weight of electronic modules, contributing to better fuel efficiency in vehicles and improved battery life in portable devices. For example, in drones, replacing traditional rigid PCBs with lightweight FPCs helps extend flight time, while in electric vehicles (EVs), the reduced weight contributes to longer driving ranges.
Industry | Impact of Weight Reduction |
Aerospace | Improved fuel efficiency, extended flight time |
Automotive | Reduced vehicle weight, better fuel economy |
Wearable Tech | Enhanced comfort and portability |
Balancing Costs and Benefits: Is Flex Worth It?
It’s no secret that flex PCBs cost more upfront compared to rigid PCBs, due to specialized materials and production processes. However, when you factor in the savings from reduced assembly steps, fewer connectors, and lighter modules, the investment often pays off in the long run. Many companies adopt turnkey assembly solutions to streamline production, bundling fabrication, SMT assembly, and testing under one roof to minimize lead times and logistical challenges.
Pro tip: Consider starting with a prototype run before committing to full-scale production to fine-tune the design and avoid costly mistakes.
Materials and Components for FPC Assembly
When diving into flexible PCB (FPC) assembly, choosing the right materials and components is like picking the best ingredients for a gourmet meal—everything matters. The combination of polyimide substrates, RA copper foil, and various connectors can make or break your design. Let’s take a closer look at what goes into crafting these high-performance circuits.
Polyimide, Adhesives, and RA Copper Foil
When it comes to flexible circuits, polyimide doesn’t just show up—it dominates. This material can stand the heat without breaking a sweat, making it a top pick for applications where other substrates would wave the white flag. Whether you’re dealing with high-temp environments or situations that demand chemical resistance, polyimide delivers every time. That’s why you’ll find it powering through in automotive systems, medical equipment, and other harsh-use applications.
RA Copper Foil: The Flexible Conductor-
Rolled Annealed (RA) copper foil is often the go-to choice for conductive layers in FPCs. Here’s why:
●Flexibility: Unlike standard copper, RA copper can bend and flex without cracking, maintaining electrical performance even in tight spots. It’s like having a rubber band that conducts electricity!
●High Conductivity: With superior conductivity, RA copper minimizes resistance, ensuring that signals travel smoothly—no bottlenecks here!
Material | Benefits |
Polyimide | Excellent thermal & chemical resistance |
RA Copper Foil | Flexibility and high conductivity |
Adhesives | Strong bond between copper and substrate |
Adhesives: Bonding It All Together-
The right adhesive can make a world of difference in FPC assembly. These materials are designed to form a strong bond between the copper layers and the polyimide substrate. This means you need to choose an adhesive that can endure flexing and maintain its grip over time. Whether it’s pressure-sensitive adhesives (PSAs) or thermosetting adhesives, ensure they match the application requirements. You wouldn’t want your circuit delaminating like an old sandwich, right?
Connectors, Stiffeners, and Shielding Materials
Connectors: Making Modular Designs Work-
Connectors in flexible circuits function much like LEGO bricks—adaptable and ready to align with ever-changing demands. They allow for modular designs that simplify upgrades and streamline repairs. When selecting connectors, focus on dimensions, durability, and how well they fit into the circuit’s overall structure. A carefully matched connector keeps things smooth, reducing downtime and making future enhancements a breeze.
Types of Connectors:
●ZIF (Zero Insertion Force) connectors are perfect for applications requiring frequent connection and disconnection.
●FFC (Flat Flexible Cable) connectors are great for tight spaces, allowing for easy connection between layers.
Stiffeners: Supporting Sensitive Areas-
While flex circuits are known for their bendability, some areas need a little extra backing. Stiffeners provide mechanical support where it’s needed most—typically around connectors and mounting points. Common materials include polyimide or FR-4, which add rigidity without compromising the flexible nature of the circuit.
Pro tip: Consider using bonded stiffeners that adhere directly to the flex circuit, providing a seamless finish without added weight.
Shielding Materials: Keeping Interference at Bay-
Electromagnetic interference (EMI) can be a real party crasher in the world of electronics. To keep your signals clear, incorporating shielding materials is a must. Options include conductive foils, metalized films, or even specialized coatings. These materials act like a protective fortress, keeping unwanted signals from disrupting performance.
Component | Function |
Connectors | Enable modular designs and easy upgrades |
Stiffeners | Provide support in sensitive areas |
Shielding Materials | Protect against EMI and signal interference |
Flex PCB Assembly Production Equipment
Flex PCB assembly isn’t your typical manufacturing process—it requires precision machinery tailored to handle thin, bendable substrates. Below, we dive into the core equipment used for surface mount technology (SMT) on flexible circuits, laser cutting, reflow soldering, and inspection, along with some real-world examples to highlight their importance.
1. Pick-and-Place Machines with Flexible Feeders
Placing tiny components onto a flexible board is no cakewalk. Traditional pick-and-place machines struggle with the delicate nature of flex circuits, which are prone to shifting during operation. That’s where specialized feeders come in. These machines are optimized to:
●Grip thin, light substrates without damaging them.
●Minimize misalignment by adjusting pressure settings dynamically.
●Handle odd-shaped or fine-pitch components used in wearables and medical devices.
For example, a smartwatch with a flex circuit might contain ultra-miniature components that require precise placement to ensure functionality. Using smart feeders and nozzles, these machines maintain high-speed assembly without sacrificing accuracy.
Machine Feature | Function | Application Example |
Flexible Feeders | Handles thin substrates carefully | Smartwatch assembly |
Vision Systems | Aligns components accurately | Medical sensors |
Why it matters: You don’t want a customer’s wearable to fail because a tiny resistor was a hair out of place. Precision here saves headaches down the line!
2. Laser Cutting and Drilling Machines
High-precision UV lasers are the MVPs of flex PCB fabrication. These machines are used for:
●Drilling microvias that connect different layers in double-sided or multilayer flex circuits.
●Cutting out intricate patterns required for flexible shapes that fit snugly into compact devices like earbuds or cameras.
●Ensuring clean, burr-free edges, which is critical to prevent tearing during use.
An example: Imagine a fitness tracker with multiple sensors spread across different parts of the band. These sensors are connected by a flex circuit with dozens of tiny vias drilled by UV lasers to ensure flawless signal transmission between sensors.
Laser Equipment | Purpose | Industry Example |
UV Laser Drilling | Creates microvias | Fitness trackers |
Laser Pattern Cutting | Shapes intricate flex layouts | Wearable sensors |
Fun fact: Burrs left from poor drilling can mess with signal integrity. A clean cut means no interference!
3. Reflow Ovens with Adjustable Profiles
Reflow soldering on flexible boards presents its own unique challenges—too much heat and the whole thing warps; too little heat and solder joints fail. That’s where programmable reflow ovens come into play. These ovens divide into multiple temperature zones, each tailored to:
●Gradually heat and cool the board to avoid thermal shock.
●Maintain optimal solder flow without warping the flex material.
●Use specialized nitrogen environments when soldering sensitive components.
For example, if you’re assembling a hearing aid circuit, even a slight misalignment due to warping can throw the whole device off. Adjustable reflow profiles ensure perfect alignment, every time.
Reflow Oven Feature | Benefit | Example |
Multi-Zone Control | Prevents thermal warping | Hearing aid circuits |
Nitrogen Environment | Protects delicate components | Medical devices |
Takeaway: Dialing in the reflow oven settings isn’t just science—it’s part art, part voodoo. But when it’s right, you know it!
4. Inspection and Testing Equipment: X-Ray and Flying Probe Testers
When it comes to inspecting hidden solder joints—especially under BGAs (Ball Grid Arrays)—you can’t rely on traditional optical inspection. X-ray machines let you see inside the assembly, spotting voids and misaligned joints that could otherwise escape notice. Meanwhile, flying probe testers ensure:
●Electrical continuity by testing signals through specific points on the circuit.
●No physical damage to the fragile board since no fixtures are required.
Let’s say you’ve got a rigid-flex assembly with hidden solder joints under a BGA in a military-grade drone controller. X-ray inspection ensures the solder balls are perfectly placed, while flying probe testing verifies the circuit works before it’s deployed in the field.
Testing Method | Function | Use Case |
X-Ray Inspection | Detects hidden solder defects | Drone controllers |
Flying Probe Testing | Verifies electrical integrity | Medical-grade wearables |
Pro Tip: X-ray inspection isn’t just cool—it’s a lifesaver when you’re working with invisible defects that could cost you big bucks later.
8 Additional Critical Aspects of Flex PCB Assembly
The assembly of flexible PCBs (FPCs) involves more than just the basics. Here are eight additional aspects that can make or break your assembly process. Let’s dive in and ensure your project runs without a hitch!
1. Handling and Storage of Flexible Circuits
When it comes to flex circuits, proper handling and storage can make a world of difference. These delicate boards are prone to damage if mishandled, so follow these best practices:
Gentle Handling: Always handle FPCs by the edges to avoid bending or creasing the circuits. Think of them as fine china—one wrong move, and it’s all over!
Ideal Storage Conditions: Store FPCs in a controlled environment, ideally between 20-25°C (68-77°F) and 30-50% humidity. Using anti-static bags can also help prevent electrostatic discharge, which can be a real headache.
Handling Tip | Description |
Edge Handling | Avoid touching the circuit area directly |
Controlled Environment | Store in a dry, temperature-controlled space |
Heads Up! Always inspect boards for defects before assembly. A little TLC goes a long way!
2. Panelization Techniques for Flexible PCB Assembly
Why Panelization?: It allows multiple FPCs to be fabricated on a single panel, streamlining the manufacturing process. This approach saves time and reduces costs, making it a win-win!
Techniques: There are several panelization methods to consider, including:
●Array Panelization: Multiple identical FPCs arranged in a grid pattern.
●V-Scoring: Cutting a shallow groove into the PCB, allowing easy separation after assembly.
Technique | Advantages |
Array Panelization | Maximizes board usage and minimizes waste |
V-Scoring | Facilitates easy manual or automated separation |
Pro Tip: Make sure the panel design doesn’t compromise the performance or integrity of individual circuits!
3. Flex PCB Assembly Using Automated Optical Inspection (AOI)
Automated Optical Inspection (AOI) is a powerful ally in the FPC assembly process. Here’s how it helps keep quality in check:
●What is AOI?: This technology uses cameras to capture images of the assembled PCBs and compares them against the design specifications. It’s like having a hawk-eyed assistant to spot mistakes!
●Benefits of AOI: This process catches defects that human eyes might miss, such as misplaced components or soldering issues. By integrating AOI into your workflow, you’ll ensure that only the best boards make it out the door.
AOI Benefits | Description |
High Precision | Detects tiny defects that can cause failures |
Increased Efficiency | Reduces inspection time and labor costs |
Let’s Get Real: If you’re not using AOI, you might as well be throwing darts in the dark. It’s a smart move to invest in this technology!
4. Specialized Reflow Profiles for FPC Assembly
Creating the perfect solder joint on flexible substrates requires specialized reflow profiles. Here’s what you need to know:
●Temperature Control: Unlike rigid PCBs, flex circuits can bend or warp when exposed to high heat. Crafting a reflow profile that gradually increases and decreases temperature helps avoid damage. This careful approach ensures the integrity of the circuit during the soldering process.
●Profile Testing: Always conduct tests to find the sweet spot for your specific materials. This might take a bit of trial and error, but it’s worth it for reliable solder joints!
Reflow Profile Step | Importance |
Ramp Up | Slowly increase temperature to avoid warping |
Soak | Maintain temperature to ensure proper soldering |
Pro Tip: Keep records of your reflow profiles. They can save time and headaches for future projects!
5. Use of Stiffeners in FPC Assembly
Stiffeners provide mechanical support where flexible circuits may need a little extra muscle. Here’s how they come into play:
●Purpose of Stiffeners: These components are added to specific areas of an FPC to provide rigidity during assembly or operation. This is particularly helpful for connectors or heavy components.
●Materials: Common materials for stiffeners include FR4, aluminum, or even polyimide. The choice depends on the application and desired rigidity.
Stiffener Material | Use Cases |
FR4 | Commonly used for general applications |
Aluminum | Best for lightweight and high-strength needs |
6. Challenges in Double-Sided and Multilayer FPC Assembly
As your designs get more complex, double-sided and multilayer assemblies can pose unique challenges:
Alignment Issues: Proper alignment of layers during assembly is crucial to avoid connectivity problems. This is especially true in double-sided assemblies where vias must line up perfectly.
Thermal Considerations: Multilayer boards often face thermal management challenges. Ensuring even heat distribution during soldering is necessary to prevent warping and other issues.
Challenge | Solution |
Alignment | Use precision tools to maintain layer alignment |
Thermal Management | Test reflow profiles to ensure uniform heating |
Tip of the Day: Be proactive in addressing these challenges. The earlier you tackle potential problems, the smoother the process will be!
7. BGA and Fine-Pitch Component Placement on Flex PCBs
When it comes to modern electronics, placing Ball Grid Array (BGA) and fine-pitch components on FPCs can be tricky but rewarding:
Precision Placement: These components have tight lead spacing, requiring accurate placement for effective soldering. Using pick-and-place machines designed for this purpose can help ensure precision.
Soldering Techniques: Different soldering techniques, such as jetting or stencil printing, may be needed to accommodate these fine-pitch components effectively.
Component Type | Placement Tips |
BGA | Ensure proper alignment and solder paste application |
Fine-Pitch | Use high-quality solder stencils for accuracy |
Let’s Do This: Investing in the right equipment for placing BGA and fine-pitch components can take your assembly to the next level. Don’t cut corners here!
8.Implementing Turnkey Flex PCB Assembly Services
For those looking to streamline their assembly process, turnkey services can be a great solution:
What Are Turnkey Services?: These services handle everything from design to assembly to testing, all under one roof. It simplifies the process and often leads to faster turnaround times.
Benefits: By opting for turnkey services, companies can focus on what they do best—designing innovative products—while leaving the nitty-gritty assembly details to the experts.
Turnkey Service Advantage | Description |
Simplified Process | Reduces coordination hassles |
Expertise | Access to specialized knowledge and equipment |
Final Thoughts: If you’re looking to save time and improve efficiency, consider leveraging turnkey services. We can help you stay ahead of the competition!
Step-by-Step Process of Flex (FPC) PCB Assembly
Assembling flexible PCBs (FPCs) requires precision at every phase. From the initial design to final soldering, each task must be handled with care to ensure everything clicks together seamlessly. Treat the process like a smooth, synchronized routine—any slip-up can lead to headaches later. Let’s break down the process and see what makes each step tick!
1. Design File Preparation (Gerber Files and BOM Validation)
It all starts with laying a solid foundation. The first step in FPC assembly is the preparation of the Gerber files and the Bill of Materials (BOM). Think of Gerber files as the blueprint for your PCB; they contain all the necessary data to manufacture your circuit.
●Gerber Files: These files include detailed information on copper layers, solder mask, and silkscreen. Ensuring these files are precise can save a lot of headaches later on.
●BOM Validation: A validated BOM lists all components needed for the project. Double-checking this list is like making sure you have all your ingredients before cooking a meal—missing items can lead to delays and costly rework.
Pro Tip: Utilize software tools to cross-check Gerber files against your BOM for errors. This will help you dodge potential pitfalls before they occur!
2. Laser Cutting, Drilling, and Etching Techniques
Once your files are ready, it’s time to bring your design to life. The manufacturing process for flex PCBs often starts with laser cutting and drilling. These steps require exact execution to prevent issues later in the process.
●Laser Cutting: This method offers unmatched precision when cutting complex shapes and patterns. The result is a smooth finish that eliminates the need for post-processing.
●Drilling: Accurate hole placement is key for component assembly. Specialized drilling equipment is used to create holes that align perfectly with the Gerber files.
Etching Process-
Next up is the etching process, which involves removing unwanted copper to define the circuit traces and component pads. It’s like carving out a masterpiece from a block of stone!
Acid Etching: This common method uses a chemical solution to remove the excess copper. The result is a finely detailed circuit layout ready for components.
Process | Description |
Laser Cutting | Provides precision for complex shapes |
Drilling | Ensures accurate hole placement |
Etching | Defines circuit traces and pads |
3. SMT Assembly for Flex PCBs
Now we’re getting to the fun part: Surface Mount Technology (SMT) assembly. This step involves placing components onto the flexible boards, which requires a delicate touch.
●Component Placement: Pick-and-place machines designed for flexible materials are employed to handle the delicate nature of FPCs. These machines are programmed to ensure components are accurately positioned, minimizing the chance of mistakes. Imagine having a robot buddy who never misses a beat!
●Handling and Alignment: Because of the thin and flexible nature of FPCs, careful handling during placement is crucial. Operators should ensure that boards are kept flat and free from stress to avoid any damage.
Heads Up: Make sure to keep your workspace tidy! A clean area reduces the risk of contamination and keeps your assembly process on track.
4. Reflow Soldering on Flexible Substrates
Finally, it’s time to solder. Reflow soldering is a common method used in FPC assembly, and special care is taken here to accommodate the unique properties of flexible substrates.
●Specialized Reflow Profiles: Since flex circuits can deform under high temperatures, specialized reflow profiles help prevent damage. This requires fine-tuning the heating and cooling rates during soldering to maintain stability and alignment.
●Solder Paste Application: A thin layer of solder paste is applied to the pads before placing components. Once the board enters the reflow oven, the paste melts and forms a secure bond between the component leads and the PCB.
Step | Considerations |
Solder Paste Application | Apply thin, even layers to prevent excess |
Reflow Temperature | Use profiles tailored for flexible materials |
Testing, Certification, and Quality Assurance for Flex PCB Assembly
When it comes to Flex PCB assembly, you want to make sure everything runs like a well-oiled machine from start to finish. This process isn’t just about getting circuits onto a flexible board—it’s about verifying performance, meeting safety standards, and keeping customers happy by delivering consistent quality. Below, we dive into testing methods, industry certifications, and best practices, along with a few tips to keep you ahead of the curve.
1. Testing Methods: ICT, Functional Testing, and Beyond
Reliable testing is the backbone of any manufacturing process, ensuring that assembled circuits do what they were designed to do. In Flex PCB assembly, two primary methods take center stage:
In-Circuit Testing (ICT)-
ICT checks for electrical issues like shorts, opens, and incorrect component values by probing specific test points on the PCB. Since flex boards can twist and bend, specialized ICT setups with customized fixtures are often required to prevent warping during the test. This step helps catch flaws early in the production line, saving time and money in the long haul.
Functional Testing-
This method ensures that the assembled product performs under real-world conditions. Functional tests can include anything from signal transmission analysis to checking how well components withstand mechanical stress or extreme temperatures. A smartphone flex circuit, for instance, might be tested by bending it thousands of times to mimic everyday use.
Testing Method | Purpose | Example Applications |
In-Circuit Testing | Detect electrical shorts, opens | Ensures components on smartwatches work |
Functional Testing | Simulate real-world conditions | Stress-testing flex boards in medical devices |
Pro Tip: Treat ICT like your first line of defense, and rely on functional testing to catch the outliers. Better to find flaws in-house than have customers calling you out!
2. Certification Requirements: IPC, ISO, and UL Standards
Meeting industry standards isn’t just about avoiding fines—it’s about proving your product meets safety and reliability benchmarks that customers trust. Let’s break down some of the must-have certifications-
IPC Standards:
The IPC-6013 standard defines performance expectations for flex PCBs. Compliance ensures that the boards meet industry-wide norms for reliability and workmanship. IPC standards also cover issues like contamination, mechanical defects, and solder quality, giving buyers peace of mind.
ISO 9001 Certification-
This international standard focuses on quality management systems. Achieving ISO certification signals that you have repeatable processes in place to maintain product quality from batch to batch. It’s often the golden ticket for landing contracts with top-tier OEMs and automotive manufacturers.
UL Certification-
Underwriters Laboratories (UL) certification is particularly crucial for safety-critical devices. UL testing evaluates whether the materials used in flex circuits can withstand heat and prevent electrical hazards. Many wearable devices and medical sensors need UL certification before hitting the market.
Certification | Focus Area | Where It’s Required |
IPC-6013 | PCB quality and performance | Consumer electronics, aerospace |
ISO 9001 | Quality management processes | Automotive, manufacturing contracts |
UL Certification | Product safety and material standards | Medical devices, wearables |
Heads Up: Certifications aren’t just paperwork—they’re your golden ticket into industries like automotive and medical tech, where quality isn’t negotiable.
3. Best Practices for Flex PCB Quality Assurance
Implementing a solid quality assurance (QA) system is the secret sauce that keeps your customers happy and your production lines humming. Here are a few strategies that’ll help you raise the bar:
AOI (Automated Optical Inspection)-
Automated Optical Inspection (AOI) systems utilize high-resolution cameras to check solder joints and component placements. Given that flex PCBs are thin and can easily deform, it’s essential to use an AOI system specifically designed for flexible substrates. These specialized machines quickly identify missing components or cold solder joints, helping to keep scrap rates down. Stay sharp and ensure quality by integrating these systems into your workflow!
Reflow Profiling for Flex Circuits-
Flex circuits are more sensitive to heat compared to rigid boards, so dialing in the reflow oven profile is key. Using specialized reflow settings helps prevent warping, ensuring components remain properly aligned after soldering. Some manufacturers even attach stiffeners temporarily during the reflow process to keep things flat and neat.
Documentation and Traceability Systems-
Maintaining traceability means that every board can be tracked back to its source materials and assembly conditions. If something goes sideways, you can quickly identify where things went off the rails and fix the issue without overhauling your entire production line.
4. Common Pitfalls and How to Avoid Them
No production process is without its challenges, and Flex PCB assembly is no exception. Here are a few common pitfalls and how to steer clear of them:
Delamination Issues-
If the adhesive layer between copper and polyimide isn’t bonded properly, it can peel apart during operation. Avoid this by using high-quality adhesives and ensuring precise temperature control during lamination.
Brittle Solder Joints-
Flex boards, by nature, move around. Over time, poor solder joints can crack under stress. Choose for flexible solder paste and monitor soldering conditions closely to prevent this problem.
Problem | Cause | Solution |
Delamination | Poor bonding during lamination | Use high-quality adhesives, control temperature |
Brittle Solder Joints | Stress-induced cracking | Use flexible solder paste |
5. The Final Check: Functional Burn-In Testing
For mission-critical applications like aerospace or medical technology, manufacturers often go one step further with burn-in testing. This process involves running the circuit under elevated stress conditions (like high voltage or extreme heat) for an extended period. The goal? Weed out components that might fail early—before they ever leave the factory.
Flex PCB Assembly, Rigid PCB, and Rigid-Flex PCB Assembly Difference
Understanding the differences between flex, rigid, and rigid-flex PCBs can make a world of difference in your design and manufacturing choices. Let’s break down the key aspects to help you decide which type is best for your project!
1. Mechanical Differences and Use Cases
When it comes to mechanical properties, each type of PCB has its strengths and weaknesses. Here’s a closer look:
Rigid PCBs: These boards are constructed from a solid substrate, typically fiberglass or epoxy resin, providing excellent structural stability. They excel in applications where the PCB must endure physical stress and vibration. Think desktop computers or network routers, where reliability is non-negotiable.
Flex PCBs: These circuits use flexible materials such as polyimide, allowing them to bend and conform to various shapes. This flexibility opens up a world of design possibilities, making them a favorite for compact and innovative applications, like wearable devices and medical sensors. When you need a circuit to fit into tight spots, flex circuits are your best bet.
Rigid-Flex PCBs: Combining the best of both rigid and flexible technologies, rigid-flex designs feature both rigid sections and flexible areas. This duality allows for complex layouts in devices that require durability and flexibility, like aerospace systems or military-grade electronics. You get the structural integrity where you need it while keeping the flexibility for moving parts.
PCB Type | Structural Features | Ideal Applications |
Rigid PCB | Solid, inflexible structure | Desktop computers, routers |
Flex PCB | Lightweight, bendable design | Wearable devices, medical sensors |
Rigid-Flex PCB | Combination of rigid and flexible areas | Aerospace systems, military electronics |
Quick Tip: Choose the PCB type that aligns with your application needs. Don’t be afraid to think outside the box!
2. Cost Comparison Between Flex, Rigid, and Rigid-Flex PCBs
Rigid PCBs: Generally, these are the most affordable option due to simpler manufacturing processes. Their straightforward design makes them cost-effective for bulk production.
Flex PCBs: While flex circuits might hit your wallet a bit harder initially, they deliver unmatched flexibility and can be a sound investment in the long run. Their durability can lead to lower failure rates and maintenance costs, which can pay off in high-stakes applications.
Rigid-Flex PCBs: The price tag here tends to be on the higher side, reflecting the complexity of their design and manufacturing. However, if your project demands both flexibility and rigidity, the benefits can outweigh the costs. Rigid-flex boards can simplify assembly processes and reduce the number of components needed, ultimately saving you money.
PCB Type | Cost | Long-Term Value |
Rigid PCB | Most affordable | Lower initial cost, best for high volumes |
Flex PCB | Higher initial cost | Savings from durability and reduced failures |
Rigid-Flex PCB | Highest cost | Justifiable for complex, multi-functional applications |
Budget Alert: Don’t just look at the upfront cost. Think long-term and consider the total cost of ownership. Sometimes, spending a bit more can save you a bundle later on!
3. Ideal Applications for Each PCB Type
Understanding where each PCB type shines can help you make informed decisions. Here are the typical use cases:
Flex PCBs: These are the go-to choice for devices that require a sleek, lightweight design. Common applications include:
●Wearable Technology: Smartwatches and fitness trackers thrive on flex circuits due to their lightweight and bendable nature.
●Medical Devices: Devices like heart monitors benefit from the compact design and flexibility, allowing them to be integrated into wearable patches.
Rigid PCBs: Perfect for applications where size and weight aren’t as much of a concern. They are frequently used in:
●Consumer Electronics: From televisions to laptops, these boards are found everywhere in our tech-heavy lives.
●Industrial Equipment: Rigid boards are the backbone of many machines, providing stability and reliability under demanding conditions.
Rigid-Flex PCBs: Best suited for applications that require a combination of rigidity and flexibility. These include:
●Aerospace Systems: The ability to withstand extreme conditions while maintaining flexibility makes rigid-flex circuits ideal for aircraft instrumentation.
●Military-Grade Electronics: Rigid-flex PCBs are often found in defense technology where performance and reliability are paramount.
PCB Type | Common Applications |
Flex PCB | Wearables, medical sensors |
Rigid PCB | Desktop computers, routers |
Rigid-Flex PCB | Aerospace systems, military-grade electronics |
Heads Up: Always match your PCB choice with the application requirements. The right fit can make all the difference!
JarnisTech: Your One-Stop Solution for High-Efficiency PCB Assembly
Since 2002, JarnisTech has been at the forefront of turnkey PCB assembly, offering end-to-end solutions across a wide range of industries. Whether you need rigid boards, flexible circuits, or rigid-flex assemblies, we’ve got the expertise, technology, and experience to bring your ideas to life. If you’re looking for a reliable partner to manage your flex PCB assembly needs, you’ve come to the right place. We’re more than happy to chat about your next big project—let’s make things happen together!
Why JarnisTech?
Choosing a PCB assembly partner isn’t just about price tags—it’s about finding a team with the know-how, precision, and infrastructure to deliver the goods without skipping a beat. With JarnisTech, you get the best of process engineering, supply chain management, and hands-on expertise.
Here’s a deep dive into how we bring precision and speed to every order:
1. Quick-Turn Quality PCB Assemblies—From Boards to Full Systems
Tired of long lead times dragging down your production? At JarnisTech, we’ve got rapid process engineering nailed down. Whether you’re looking to get small-batch prototypes built fast or need full-scale systems assembled in record time, we’ll keep things moving.
How we do it: We employ optimized workflows that connect engineering with production, so your project goes from concept to completion without a hitch.
Example: We’ve helped clients in telecom and medical industries meet tight deadlines with high-mix, low-volume production schedules—without a single compromise in quality.
Need a quick turnaround? Our nimble processes ensure that even complex assemblies get completed faster than you can say “on the clock.”
2. Seamless Scalability—From Prototype to Production
Got a product launch coming up? We’ll help you scale. Our production capabilities flex to your needs, whether it’s a handful of prototypes or thousands of units.
Prototype to Production in One Go: We know it’s a pain switching between suppliers during scaling phases. That’s why we keep it all in-house.
Supply Chain Mastery: Our established network of reliable suppliers ensures there are no material bottlenecks—even if you’re ramping up for a large release.
Launch stress-free with a production partner who can keep pace with your growing demand—no delays, no excuses.
3. Complex Engineering Challenges? No Sweat
Not every project is a walk in the park, and that’s where JarnisTech’s multidisciplinary engineering expertise really shines. With years of hands-on experience, we’ve seen—and solved—it all, from intricate BGA layouts to flexible circuits with challenging tolerances.
Our Three Pillars of Success:
People: Engineers who think on their feet and know what it takes to make your project succeed.
Process: Optimized workflows that eliminate bottlenecks and keep the lines humming.
Equipment: State-of-the-art machines that handle everything from laser cutting to precision soldering.
When your design gets tricky, our team’s got your back—because the only way is forward.
4. Time Is Money—Accelerate Your Time to Market
Got a deadline breathing down your neck? We understand the hustle. Our quick-response quoting system means you’ll get pricing info within an hour, so you can lock in your next steps ASAP. And our 24/7 support team? They’ve got answers at the ready, whenever you need them.
Example: A customer in the automotive industry came to us with an urgent request for a sensor assembly. With our fast-track production, we delivered the first batch in just three days—weeks ahead of their internal timeline.
When time-to-market matters, we’re the partner that’ll keep you ahead of the curve—because every second counts.
5. Certifications and Quality You Can Count On
We don’t just talk about quality—we live it. At JarnisTech, we maintain a rigorous Quality Management System and push the boundaries of process improvement to keep things fresh and flawless. ISO, UL, and IPC certifications are just the beginning. Every product we touch goes through multiple quality gates to ensure it meets your exact requirements.
Continuous Improvement: We treat every project as an opportunity to level up—because good enough isn’t good enough.
Quality Control at Every Stage: From design to delivery, our quality team keeps a close eye on every phase to catch issues before they become problems.
We believe in doing it right the first time—because nobody likes rework.
Full Turnkey Capabilities—From Design to Delivery
Our all-inclusive turnkey solutions mean you don’t have to sweat the details—we handle everything from circuit design to final assembly. Whether you’re building flexible circuits for wearables or rigid-flex boards for aerospace, we’ve got the tools and talent to make it happen.
Here’s What We Offer:
Service | Description | Examples |
Circuit Design | From schematic creation to layout optimization | IoT devices, medical sensors |
Prototype Assembly | Small-batch production for testing and validation | Wearables, connected home gadgets |
Full-Scale Production | Large-volume runs with tight deadlines | Automotive systems, telecom hardware |
Post-Assembly Testing | ICT, AOI, and functional testing to ensure reliability | Satellite modules, EV control units |
Let’s Talk—Your Next Project Starts Here
When it comes to PCB assembly, JarnisTech brings experience, precision, and passion to the table. Why waste time dealing with multiple vendors when you can get it all done under one roof? Give us a call today and let’s discuss how we can bring your ideas to life, from prototype to production.
JarnisTech isn’t just a service provider—we’re your partner in making great things happen.
Advanced PCB Assembly
PCBs We Can Assemble
- Min size: PCB whose width/length is less than 30mm should be panelized.
- Max size: single board 500mm*400mm | panel board 310mm*410mm.
- Layer Count: 1-60 layers (1-20 layers for mass production).
- Copper Thickness: 1/2oz – 17oz.
- PCB Types: Rigid PCBs, Flex PCBs, Rigid Flex PCBs, Rogers PCBs, Ceramic PCBs, etc.
- Surface Finishes: Lead/Lead-free HASL, ENIG, ImSilver, OSP, Gold plated, Immersion Gold, etc.
Components We Can Assemble
- SMT sizes: 01005, 0201 or larger.
- BGA pitch: 0.35mm or greater.
- BGA Ball count: 2 – 50.
- Fine pitch: 0.4mm or greater.
- WLCSP pitch: 0.35mm or greater.
- Components Height: 0.1mm – 12mm.
- BGA, micro-BGA, POP, CSP, LGA package, Flip chip, Hard metric connectors, Cable & wire, etc.
- Min. Components Spacing: 0.20mm for SMT parts, no specific demand for Thru-hole parts.
Custom PCB Assembly Capabilities
- Quick Turn.
- IPC III standard compliant.
- Prototype Quantities to Production Quantities.
- Single PCB Assembly and PCB Panel Assembly.
- Single and Double-sided PCB Assembly.
- Leaded Assembly, Lead-free or RoHS Compliant Assembly and No-clean Process Assembly.
- SMT Assembly, Thru-hole (DIP) Assembly, and Combo of SMT and Thru-hole Assembly.
- Consigned PCB Assembly, Partial consigned PCB Assembly and Full turnkey PCB Assembly.