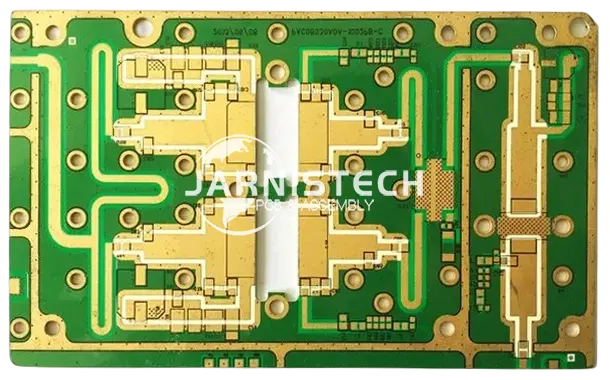
When you’re designing high-performance electronic systems, there’s no room for compromise on reliability or efficiency. Arlon PCB materials are a top-tier choice, particularly when it comes to applications demanding high-frequency performance and thermal stability. These two critical aspects often serve as the foundation for innovations in fields like communications, automotive electronics, and military technologies. In this section, we dive into how Arlon PCBs stand out for their performance in these areas and why they’re a go-to solution for professionals who require top-notch quality and durability.
Key Features and Benefits of Arlon PCB Materials
Arlon PCB materials stand out due to their exceptional properties that cater to the demands of high-performance electronic systems. Whether you are designing high-frequency circuits or thermal management solutions, Arlon’s PCBs provide reliable and durable performance across a wide range of industries. Let’s take a deeper dive into the top features and benefits that make these materials indispensable for engineers and manufacturers alike.
High-Frequency Performance of Arlon PCB Materials
When it comes to high-speed signal transmission, Arlon PCBs are built to handle the heat – figuratively and literally. These materials boast low dielectric constants and low loss tangents, making them ideal for RF (radio frequency) applications where minimizing signal degradation is a must. Whether you’re working on telecommunications, satellite systems, or 5G network components, the signal fidelity maintained by Arlon materials ensures the integrity of data transmission, even at microwave frequencies.
Take 5G infrastructure – the demands for high-frequency signal handling are intense, and Arlon’s materials offer the reliability engineers need to push the envelope. By reducing signal distortion and improving signal quality, Arlon PCBs ensure that performance meets the high expectations of next-gen communication systems.
Feature | Benefit |
Low Dielectric Constant | Minimizes signal loss and distortion |
Low Loss Tangent | Ensures high signal integrity |
Stable Performance | Withstands high-frequency operation |
These properties make Arlon materials the go-to choice for demanding applications where precision and reliability are a non-negotiable part of the equation. So, if you’re in the telecommunications, defense, or aviation industries, Arlon is the real deal.
Thermal Stability Advantages of Arlon PCB Materials
When your designs need to go the distance—whether in automotive systems, medical devices, or power management solutions—the ability to handle extreme temperatures without losing their edge is key. Arlon PCB materials are designed with high glass transition temperatures (Tg), making them perfect for tough, high-heat environments where keeping things cool is a must. These materials are built to keep your circuit boards performing at their peak, no matter how hot it gets.
One of the most noticeable benefits of Arlon materials is their thermal stability. For instance, Arlon 85N features a glass transition temperature of up to 280°C, which means it can endure heat spikes without degrading. This makes it the go-to choice in applications that require high-temperature stability without compromising electrical conductivity.
Think about automotive electronics in electric vehicles. The materials inside these vehicles need to handle heat cycling from engine compartments while maintaining electrical integrity. Arlon PCB materials not only perform well under thermal stress, but they also provide long-lasting reliability throughout the lifespan of these vehicles.
Benefits in Thermal Stability-
●Excellent Heat Resistance: Arlon materials are engineered to survive and perform in high-temperature environments.
●Thermal Expansion Control: The coefficient of thermal expansion (CTE) of Arlon materials is well-suited to maintain the dimensional stability of PCB designs, which is vital in high-precision applications.
●Reduced Risk of Warping: Due to their resistance to thermal expansion, Arlon PCBs offer reliable performance even when exposed to rapid temperature changes.
Property | Impact |
High Glass Transition Temp (Tg) | Withstands high-heat environments |
Low Thermal Expansion | Maintains dimensional stability |
Robust Under Temperature Cycles | Ensures long-term reliability |
So, whether you’re designing for solar power systems or automotive electronics, Arlon materials stay solid when others might falter.
Reliability and Durability in Arlon PCB Laminates
Engineers and manufacturers alike are big fans of Arlon PCB materials, and for good reason—their reliability is top-notch. These materials are designed to last, offering impressive longevity even under harsh conditions. Whether you’re dealing with moisture exposure or mechanical stress, Arlon PCBs stand strong, ensuring that your circuits perform as expected for the long haul. This makes them a go-to choice for applications that demand both durability and consistent performance.
1.Moisture Resistance: Arlon’s unique formulation minimizes moisture absorption, making it an ideal choice for environments exposed to outdoor elements, such as communication equipment and automotive electronics. When materials absorb moisture over time, they are at risk of corrosion, which can negatively impact both the structural strength and electrical conductivity of circuits. Arlon’s moisture-resistant properties ensure that their PCBs remain durable and continue to perform effectively, even in high-humidity conditions. This makes them a reliable option for long-term use, reducing the likelihood of performance degradation due to moisture-related damage.
2.Mechanical Durability: Arlon PCBs are designed to endure the mechanical stresses that come with high-performance applications. Whether it’s vibration resistance in military-grade systems or impact resistance in consumer electronics, Arlon materials maintain their integrity even in harsh conditions.
Example: Arlon’s 85N laminate is commonly used in aerospace applications, where reliable performance under extreme conditions is non-negotiable. Engineers trust that Arlon materials will survive the long haul – even when subjected to high vibrational forces or temperature extremes.
Durability Benefits:
●Low Moisture Absorption: Prevents corrosion and ensures a longer lifespan in high-humidity environments.
●Strong Mechanical Properties: Resists warping, cracking, and breaking under stress, making it suitable for rugged and high-demand applications.
●Long-Term Stability: Arlon laminates have been proven to maintain their performance over many years, reducing the need for frequent replacements and repairs.
Feature | Benefit |
Moisture Resistance | Prevents corrosion and damage |
Mechanical Strength | Withstands vibration and impact |
Longevity | Reduces need for frequent replacements |
Types of Arlon PCB Laminates and Their Applications
Arlon PCB laminates are used in a wide array of industries, from communications to automotive electronics, and they each serve a specific purpose based on their properties. Understanding the different types of Arlon PCB laminates and how they perform in various environments can help you make the best choice for your projects. Let’s take a deeper look at the characteristics, properties, and applications of these materials to see how they can benefit your designs.
Characteristics of Arlon PCB Laminate
Arlon offers a variety of PCB laminates that feature high-performance characteristics tailored to meet the demands of diverse applications. The core characteristics of Arlon laminates include high dielectric strength, low loss tangent, and thermal stability, which makes them ideal for high-frequency, high-temperature, and high-reliability applications.
For instance, Arlon 85N is widely known for its superior thermal stability, while Arlon 35N is designed to excel in high-frequency environments. Whether you’re dealing with signal transmission in 5G networks or thermal management in automotive electronics, Arlon’s laminates offer stability, strength, and reliability.
If you’re designing a 5G antenna system, you need a material that won’t mess with your signal integrity. Arlon laminates, with their low loss tangent, help keep your signals sharp, ensuring that the data you send and receive stays clean and fast.
Feature | Benefit |
Low Loss Tangent | Reduces signal distortion |
High Dielectric Strength | Withstands high voltages without failure |
Thermal Stability | Performs in extreme temperature ranges |
Properties of Arlon PCB Material
The properties of Arlon PCB materials make them stand out from other laminates on the market. Arlon’s thermally stable materials, such as Arlon 85N and Arlon 25N, are designed to provide long-term performance in high-temperature applications without degrading. These laminates are engineered with specific materials like polyimide, PTFE (Teflon), and epoxy resin to enhance their electrical, mechanical, and thermal properties. These materials are commonly used in RF/microwave circuits, power electronics, and aerospace components.
Properties that Make Arlon Materials Stand Out-
●Low Dielectric Constant: For minimal signal attenuation in high-speed applications.
●High Glass Transition Temperature (Tg): Ensures stability in high-heat environments.
●Low Moisture Absorption: Keeps the performance consistent in humid conditions.
In automotive powertrain systems, where heat can be a real issue, using Arlon’s polyimide-based materials helps keep the circuit integrity intact over time, preventing failures that could cost manufacturers dearly.
Property | Effect |
Polyimide-based Laminates | Ideal for high-temperature applications |
Low Moisture Absorption | Keeps performance stable over time |
Low Dielectric Loss | Ensures accurate data transmission |
These properties make Arlon PCB materials reliable for industries that need consistent performance under extreme conditions.
Arlon Polyimide-Based PCB Laminates for Harsh Environments
Arlon’s polyimide-based laminates are engineered to withstand some of the most demanding conditions, making them perfect for harsh environments. These materials are thermal-resistant, chemically stable, and mechanically durable, making them the ideal choice for aerospace, defense, automotive, and industrial applications where reliability is a must.
Polyimide-based materials like Arlon 85N and Arlon 35N are built to endure extreme temperature fluctuations, high-vibration environments, and high-stress conditions. Whether you’re designing for satellite systems or electric vehicles, Arlon’s polyimide-based materials ensure that your PCBs remain functional and reliable throughout their lifecycle.
Imagine designing a satellite communication system. The system needs to be able to withstand the temperature extremes of space while maintaining reliable signal transmission. Polyimide-based PCBs from Arlon can handle the thermal cycling and mechanical stresses associated with space missions, ensuring that your design works flawlessly even in the harshest of environments.
Characteristic | Advantage |
High Thermal Resistance | Ideal for space, automotive, and military applications |
Low Moisture Absorption | Maintains performance in harsh, wet environments |
Chemical Stability | Performs in environments with harsh chemicals |
Manufacturing Process for High-Performance Arlon PCB Materials
The manufacturing process for high-performance Arlon PCB materials is a precise and intricate operation that requires attention to detail at every step. Whether you’re using polyimide-based materials, high-frequency laminates, or thermal-resistant layers, ensuring the integrity and reliability of these materials is key to creating durable, high-performing printed circuit boards. In this section, we’ll take a closer look at the steps involved in manufacturing Arlon PCBs, from lamination to storage and handling.
Lamination Techniques for Arlon PCB Materials
Lamination is a key part of creating top-notch Arlon PCBs, and it’s not something you want to skip. When the heat and pressure come into play, they ensure the copper foil and substrate really stick together, forming a durable, reliable board. Think of it like making a killer sandwich—if the layers aren’t properly pressed, they won’t hold up when things get heated. Without that solid bond, the whole PCB could lose its punch and underperform. So, nailing the lamination process is like laying down the foundation for a sturdy, high-performance circuit board that’s ready to handle the tough stuff.
In Arlon’s case, polyimide-based laminates and high-frequency PCBs often undergo a double-sided lamination process. This process typically involves a combination of hot pressing and autoclaving, depending on the specific type of laminate used. The goal is to ensure that the layers are uniform and that there is no delamination or air pockets between them, which could affect the PCB’s performance under stress.
For instance, Arlon 85N laminates used for high-frequency applications are subjected to a precise controlled lamination process that ensures a consistent dielectric constant and minimal signal loss. The end result is a PCB that performs optimally even in high-frequency circuits or aerospace components.
Pro Tip: The key to a successful lamination process is maintaining the right temperature and pressure for the specific Arlon material being used. Too much heat can cause material degradation, while too little can lead to insufficient bonding. Always follow manufacturer guidelines for optimal results.
Lamination Type | Recommended Application |
Single-sided lamination | Ideal for simple, low-cost designs |
Double-sided lamination | Perfect for high-performance RF and high-frequency applications |
Autoclave lamination | Used for high-temperature and aerospace circuits |
Best Practices for Storing Arlon PCB Laminates
Proper storage is a key part of ensuring that Arlon PCB laminates maintain their quality and performance. These materials are sensitive to both moisture and temperature, and improper storage can lead to delamination, reduced thermal stability, and performance degradation.
Arlon recommends that PCB laminates be stored in a climate-controlled environment, ideally between 18°C to 30°C (64°F to 86°F), with humidity levels maintained between 40% and 60%. If you’re working with polyimide-based laminates, avoid exposure to extreme humidity or temperature swings, as these can cause the laminate to absorb moisture, leading to layer separation during manufacturing.
To maintain the quality and stability of laminates, it’s not just about controlling temperature and humidity—you’ll also want to keep them out of direct sunlight or any strong UV exposure. Over time, UV rays can alter the chemical properties of the materials, potentially affecting their performance in the long run. A bit of TLC goes a long way in preserving these laminates!
Real-World Tip: Many PCB manufacturers use specialized laminate storage cabinets that provide temperature and humidity control to keep Arlon laminates at their peak performance. If you’re working in an environment where storage conditions aren’t ideal, you may want to consider investing in sealed storage bags or vacuum-sealed packaging to protect your materials.
Storage Recommendation | Benefit |
Store in a climate-controlled room | Preserves material integrity and reduces risk of moisture absorption |
Avoid exposure to sunlight | Prevents degradation and material breakdown |
Store in sealed bags or containers | Protects from contamination and moisture during transportation |
By following these storage best practices, you’ll ensure that your Arlon PCB materials are in optimal condition when it’s time to use them in your manufacturing.
Handling Challenges with Arlon PCB During Manufacturing
When manufacturing Arlon PCBs, handling can be one of the trickiest aspects of the process. These materials are often sensitive to stress, and improper handling can lead to defects or reduce their long-term reliability.
For example, Arlon polyimide-based materials are more flexible than traditional FR4 materials, but they are also more prone to damage during handling if not properly supported. In such cases, gentle handling and proper equipment (such as cleanroom gloves and tools designed for handling delicate materials) are a must.
Another challenge arises during the etching process. While Arlon PCB and other high-frequency PCB laminates are designed to withstand the rigors of PCB manufacturing, they require careful etching techniques to avoid compromising the signal integrity. For RF PCBs, using laser direct imaging (LDI) and chemical etching allows manufacturers to produce intricate, fine-line designs without damaging the PCB’s electrical properties.
Pro Tip: When handling Arlon laminates, always use antistatic equipment to prevent static discharge, which could damage sensitive materials or compromise the electrical properties of your boards.
Handling Challenge | Solution |
Delicate materials (Polyimide) | Use gentle handling techniques and cleanroom tools |
Etching high-frequency boards | Use laser direct imaging and chemical etching to preserve signal integrity |
Static discharge | Utilize antistatic tools to avoid damage to materials |
By staying mindful of these challenges and incorporating the right handling procedures into your manufacturing process, you can maintain the quality and integrity of Arlon PCB materials throughout production.
Assembly Considerations with Arlon PCB Materials
When working with Arlon PCB materials, the assembly process presents its own set of unique considerations. From soldering techniques to multilayer stacking and optimizing designs for RF circuits, every detail counts in ensuring the final product meets stringent performance standards. These materials are highly engineered to withstand demanding environments, whether you are assembling high-frequency boards for aerospace or high-temperature circuits for automotive applications. Let’s dive into some key assembly considerations when using Arlon PCB laminates.
Soldering Techniques for High-Temperature Arlon PCB
Soldering is one of the most fundamental tasks in PCB assembly, and when working with Arlon materials, precision is a must. Given that Arlon PCB materials are often used in high-temperature applications, soldering techniques need to be adapted to the specific laminate type to prevent material degradation and maintain reliable electrical connections.
One of the biggest challenges when soldering high-temperature Arlon PCBs is managing the thermal stress caused by elevated temperatures. Arlon’s polyimide-based laminates, such as Arlon 85N, are engineered to endure extreme heat without compromising their thermal stability. However, during soldering, it’s important to use controlled heating methods to avoid exceeding the material’s glass transition temperature (Tg).
Best Practices for Soldering High-Temperature Arlon PCBs:
1.Pre-heat the PCB: Slowly ramping up the temperature to ensure uniform heat distribution across the board helps avoid thermal shock to the laminate.
2.Use lower-temperature soldering fluxes: This reduces the risk of thermal damage while ensuring good solder joint formation.
3.Use reflow soldering techniques: For Arlon high-frequency PCBs, reflow soldering helps achieve uniform solder joints, especially when handling fine pitch components.
4.Avoid excessive heat exposure: Prolonged exposure to high temperatures can result in delamination or warping of the laminate.
Pro Tip: If you’re working with Arlon PCB materials that are designed for RF or high-temperature environments, make sure to use specialized soldering tools and keep an eye on the temperature profile during the soldering process.
Soldering Method | Recommended Application |
Reflow soldering | Ideal for high-frequency boards requiring fine pitch components |
Wave soldering | Suitable for larger assemblies with less delicate components |
Hand soldering with low-heat flux | Best for high-temp Arlon boards to avoid thermal damage |
Multilayer Stacking with Arlon PCB Laminates
For complex circuit designs, stacking multiple layers is often necessary, especially with high-performance materials like Arlon laminates. This approach proves useful in high-frequency or high-temperature applications, where added layers help to handle intricate configurations or improve heat management. For instance, Arlon 85N, known for its stable thermal characteristics and minimal signal loss, serves as a popular choice for multilayer boards that require both frequency stability and efficient thermal dissipation.
Multilayer stacking requires meticulous planning and precision during both lamination and assembly to ensure that each layer aligns perfectly and adheres properly.
Here are a few considerations when stacking Arlon PCB laminates:
1.Layer Alignment: Accurate alignment of all layers is necessary to avoid signal interference and to ensure electrical continuity across all layers.
2.Via Technology: For multilayer Arlon PCBs, using via-in-pad or blind vias can help ensure a proper connection between layers while maintaining signal integrity, especially in RF designs.
3.Curing Process: After stacking the layers, ensure proper curing during the lamination process to avoid delamination or weak bonds.
4.Thermal Management: As multilayer designs tend to generate more heat, Arlon PCBs designed for high-temperature applications should be combined with heat sinks or thermal vias to improve heat dissipation.
Pro Tip: For multilayer Arlon boards, double-check the stack-up configuration before proceeding with via drilling and layer lamination to avoid costly reworks or potential performance issues later in the process.
Multilayer Consideration | Best Practice |
Via-in-pad technology | Useful for high-density interconnections in RF applications |
Layer alignment | Ensure precision alignment to avoid signal interference |
Thermal management | Integrate thermal vias to disperse heat in high-performance designs |
Optimizing Arlon PCB for RF Circuit Assembly
The optimization of Arlon PCB materials for RF circuit assembly requires special attention to the materials’ dielectric properties and signal transmission characteristics. In RF applications, even the smallest interference can degrade signal quality, which is why Arlon PCB laminates are specifically designed to meet the demands of high-frequency circuit designs.
Arlon’s RF PCB laminates, such as Arlon 25N and Arlon 85N, are engineered with low-dielectric constants to reduce signal loss and transmission delay. To optimize Arlon PCBs for RF circuit assembly, consider the following:
1.Material Selection: Ensure that you’re using the right Arlon material for the desired frequency range. For instance, Arlon 85N has excellent performance at high frequencies with minimal signal attenuation, while Arlon 25N is more suited for lower-frequency applications.
2.Minimize Signal Loss: The layer structure and via design play a major role in minimizing signal loss in RF designs. Use blind vias or buried vias to keep signal paths as short as possible.
3.Controlled Impedance: For RF circuits, keeping impedance stable is necessary. Arlon PCB materials are crafted to ensure consistent impedance across high-frequency circuits like antennas and microwave systems, which allows for smoother signal flow and reliable performance. By minimizing impedance fluctuations, these materials support RF systems in maintaining signal quality, preventing typical issues like distortion or loss. For sensitive RF designs, Arlon’s specialized materials offer the steady performance needed to keep the circuit functioning dependably.
Example: When designing a 5G antenna array, using Arlon 85N or Arlon 25N ensures minimal signal interference even at the high frequencies required. This results in an efficient signal path with enhanced network reliability.
Pro Tip: Always use microwave simulation tools to model your RF circuit’s performance before assembly. This will help you choose the correct Arlon material and optimize the layout for minimal loss.
RF Optimization Consideration | Solution |
Signal loss in high-frequency circuits | Use low-dielectric Arlon materials like 85N |
Controlled impedance | Ensure layer stack-up and via technology are optimized for impedance control |
Via design for RF circuits | Use blind and buried vias to reduce signal path lengths |
Advantages of Using Arlon PCB in High-Performance Electronics
Arlon PCB materials have long been recognized for their unparalleled performance in high-tech and demanding electronics. These materials provide several advantages that make them the go-to choice for high-frequency circuits, advanced RF applications, and environments that require thermal and mechanical stability. Let’s dive deeper into these key advantages.
Enhanced Signal Integrity in Arlon PCB Materials
In high-frequency electronics, ensuring signal quality over long distances or through intricate circuit paths is the name of the game. With demand ramping up for faster and more dependable communication, Arlon PCB materials come through by reducing signal loss and attenuation, which is especially helpful in RF and microwave setups. These materials are engineered to keep signals flowing with minimal interference, making them a top pick for designs where clean, steady data transmission is a non-negotiable. In other words, Arlon PCBs help keep everything clicking along, even in the trickiest circuits.
How Arlon Maintains Signal Integrity-
●Low loss factor: Materials like Arlon 85N have an extremely low dissipation factor, which means less energy is wasted as heat, ensuring more of the signal gets through.
●Stable dielectric constant: Arlon PCBs exhibit consistent dielectric properties across a wide range of frequencies, preventing signal distortion and ensuring clean transmission.
●Tightly controlled impedance: With Arlon PCBs’ precise impedance control, signals flow smoothly across the board with minimal interference, making them a dependable choice for high-speed digital circuits. This capability enhances the efficiency of data transmission, which is especially beneficial in environments where signal clarity and rapid processing are key. By maintaining stable impedance levels, Arlon PCBs support the integrity of high-frequency signals, reducing potential disruptions and ensuring that performance remains steady across complex circuits.
Feature | Benefit |
Low loss factor | Minimizes signal loss, especially at high frequencies |
Stable dielectric constant | Consistent performance across multiple frequencies |
Controlled impedance | Efficient signal transmission with minimal interference |
Pro Tip: For RF circuit applications that demand precise signal transmission, Arlon materials with low signal loss are an excellent choice, offering enhanced data quality and reliability over extended usage. These materials effectively reduce interference, allowing signals to maintain integrity even over greater distances or in challenging conditions.
Low Coefficient of Thermal Expansion in Arlon PCBs
In high-performance electronics, managing thermal stress is a big deal. The coefficient of thermal expansion (CTE) of a material is a crucial parameter that determines how much the material expands or contracts when subjected to temperature fluctuations. Arlon PCB materials are engineered with a low CTE, which means they are far less likely to experience warping, cracking, or delamination when exposed to temperature shifts.
Why Low CTE Matters in Arlon PCBs-
●Prevents delamination: As components heat up during operation, Arlon PCBs expand at a similar rate, reducing the risk of delamination—a major failure mode in traditional materials.
●Long-term durability: This thermal stability ensures that Arlon PCBs can withstand temperature cycling, which is common in automotive, military, and space applications.
●Precision in high-heat environments: For high-power applications, like power amplifiers or automotive control systems, Arlon PCBs maintain their shape and performance despite extreme conditions.
For instance, Arlon 85N has a low CTE that makes it the ideal choice for high-temperature environments like automotive ECUs where temperature fluctuations can be dramatic. This thermal resistance ensures that the PCB maintains its structural integrity even in harsh conditions.
Material Property | Benefit |
Low CTE | Prevents warping and delamination during temperature cycling |
High thermal stability | Ensures consistent performance in high-heat environments |
Temperature cycling resistance | Withstands extreme temperature fluctuations, maintaining board reliability |
Pro Tip: For applications with extreme thermal conditions, Arlon PCB materials with a low CTE are indispensable for ensuring reliability, especially when components are subjected to thermal cycling.
Arlon PCB Materials in Thermal and Mechanical Stability
High-performance electronics need to hold up not only under thermal stress but also against mechanical forces. The combination of thermal stability and mechanical strength makes Arlon PCB materials an optimal choice for applications where both heat and physical strain are present. Whether in aviation, automotive, or industrial electronics, Arlon materials deliver outstanding performance.
Thermal Stability in Arlon PCBs-
●Heat resistance: Arlon PCBs are built tough, made to hold their shape and electrical quality even when temperatures run high. This resilience makes them a great match for demanding setups, like engine control units (ECUs) and power management circuits, where heat is part of the deal. These boards stay stable under pressure, ensuring that performance doesn’t take a hit just because things heat up.
●Resistance to thermal cycling: Arlon laminates are built to endure rapid temperature changes, maintaining performance despite frequent exposure to heat.
Mechanical Stability in Arlon PCBs-
●Dimensional stability: With high mechanical strength, Arlon PCBs resist distortion or bending even under physical stress. This makes them ideal for automotive control boards, where both thermal and mechanical stability are required.
●Impact resistance: The polyimide resins used in Arlon materials provide exceptional impact resistance, which is ideal for rugged environments where vibrations and shock loads are common.
Example: In automotive applications, such as engine control systems and battery management systems, where exposure to both high temperatures and mechanical stresses is a constant challenge, Arlon PCBs stand out for their reliability and resilience.
Material Property | Benefit |
High thermal resistance | Withstands high temperatures without degradation |
Mechanical strength | Prevents bending or distortion under physical stress |
Impact resistance | Withstands vibration and shock in harsh environments |
Pro Tip: When working in environments subject to both extreme temperatures and mechanical stress, consider Arlon PCB materials for their dual capability in both thermal and mechanical stability.
Comparing Arlon PCB Materials with Other PCB Laminates
When it comes to high-performance printed circuit board (PCB) materials, making the right choice can have a major impact on your project’s reliability, signal integrity, and thermal stability. Arlon PCB materials stand out in specific areas like high-frequency performance, thermal cycling, and mechanical stability, but how do they stack up against other popular materials like Rogers PCB and FR-4 PCB? Let’s break it down.
Arlon PCB vs. Rogers PCB Materials
Rogers PCB materials are often considered the gold standard for high-frequency applications, with a reputation for superb signal integrity and low loss factor. However, Arlon PCB materials also have a strong track record in these areas, offering distinct advantages in certain environments.
Key Differences-
●Performance at high frequencies: Both Rogers and Arlon are known for their low loss tangent and high dielectric constant stability. However, Arlon PCB materials like 85N and Adelphia series are especially suited for low-thermal expansion applications, making them a better fit for automotive or industrial electronics where both signal integrity and thermal stability are required.
●Cost-effectiveness: When comparing costs, Arlon materials tend to be more affordable than Rogers, which makes them a solid choice for applications that need to balance performance and cost.
●Temperature resistance: Arlon offers materials with excellent thermal stability, especially for high-temperature applications like automotive electronics and power modules, where Rogers PCB materials can struggle in certain extreme temperature conditions.
Example: In 5G base station applications, Rogers PCB might be preferred for pure signal clarity due to its ultra-low loss factor, but for autonomous vehicles that also need the material to hold up under heat and mechanical stress, Arlon materials might be a better choice due to their enhanced thermal stability.
Feature | Arlon PCB | Rogers PCB |
High-frequency performance | Excellent for high-speed data transfer | Excellent for RF applications |
Cost-effectiveness | More budget-friendly | Higher cost for specialized needs |
Thermal stability | Better for high-heat environments | May not perform as well in extreme heat |
Pro Tip: If your application is cost-sensitive but still requires high-frequency performance and thermal resistance, Arlon PCB materials may offer the right mix of performance and value.
Arlon PCB vs. FR-4 PCB Materials
FR-4 is the most commonly used PCB material, known for being both affordable and versatile. However, Arlon PCB materials offer a range of advantages when it comes to high-frequency applications, thermal management, and mechanical strength.
Key Differences-
●Signal integrity: While FR-4 works well for low to mid-frequency applications, Arlon PCBs outperform FR-4 in applications requiring high-frequency and high-speed data transmission, such as 5G or RF circuits. Arlon’s low loss factor and stable dielectric constant ensure that signals remain clear even in complex setups.
●Thermal resistance: Arlon PCB materials excel in environments where temperature cycling is a concern. FR-4 can perform adequately at room temperature but tends to break down or lose its mechanical integrity in higher temperatures. Arlon’s materials, like Polyimide, are ideal for high-heat environments, offering better thermal resistance.
●Mechanical strength: Arlon offers better mechanical stability than FR-4, making it ideal for rugged environments where vibration or physical shock could damage the board. This makes it especially beneficial for military or automotive applications.
Example: In space applications, where both high-frequency performance and temperature extremes are a concern, Arlon PCBs outperform FR-4 in terms of signal clarity and thermal endurance.
Feature | Arlon PCB | FR-4 PCB |
Signal integrity | Superior for high-speed and RF signals | Works well for low-frequency circuits |
Thermal performance | Superior in high-temperature environments | Can struggle in high-heat applications |
Mechanical stability | Excellent for rugged environments | May not withstand shock or vibration |
Pro Tip: If you’re designing high-frequency circuits or working in high-heat conditions, Arlon PCB materials will outshine FR-4 in terms of performance and durability.
Selecting Between Arlon and Alternative High-Frequency Materials
When choosing between Arlon and other high-frequency PCB materials, it’s important to consider both your performance needs and your budget. Alternative materials like Rogers or Taconic are often better suited for pure signal integrity but may fall short in thermal stability or mechanical strength compared to Arlon PCBs.
Considerations-
●Performance vs. cost: If you’re looking for the best high-frequency performance, Rogers may be the best choice. However, if cost-efficiency is a factor, Arlon provides similar performance with a more affordable price tag.
●Environmental factors: For applications in automotive or military environments, Arlon PCB materials can handle extreme temperatures and vibrations better than Rogers or FR-4, which may not be as robust in these situations.
●Signal clarity and heat resistance: While Rogers materials excel in RF performance, Arlon maintains signal integrity over a longer lifespan in harsher conditions, such as high-power or high-heat applications.
Example: In high-frequency applications for RF communication, Rogers PCB materials might be the first choice due to their excellent dielectric stability. However, for automotive systems or military technology, Arlon’s combination of signal clarity and thermal resistance makes it the more practical choice.
Feature | Arlon PCB | Rogers/Taconic |
High-frequency performance | Excellent for complex signal transmission | Superior signal clarity for pure RF |
Thermal resistance | Superior in high-temperature environments | Struggles with extreme heat conditions |
Mechanical durability | Better for rugged or mobile applications | Less durable under mechanical stress |
Pro Tip: Always consider your project’s unique needs—Arlon offers the best balance for rugged, high-frequency applications, especially when dealing with thermal cycling or mechanical stress.
Procurement Guide for Sourcing Arlon PCB Materials
When sourcing Arlon PCB materials, a detailed and methodical approach is necessary to ensure the success of your project. Whether you’re working with automotive, telecommunications, or RF technology, selecting the right Arlon laminates requires a blend of technical expertise, cost considerations, and a reliable supplier base.
How to Select the Right Arlon PCB Material for Specific Needs?
Choosing the right Arlon PCB material? Well, it’s no cookie-cutter deal. You’ve got to think about the specific needs of your application. It depends heavily on your application’s specific requirements, including thermal resistance, mechanical strength, signal integrity, and cost-effectiveness.
Key Considerations for Selection-
●Performance Requirements: Whether you’re designing for high-frequency circuits, RF communication, or automotive electronics, you’ll need to select materials with the right dielectric properties and signal loss characteristics. For high-frequency applications, materials like Arlon 85N or Adelphia series are an excellent choice due to their stable dielectric constant and low loss factor.
●Temperature and Environment: For applications where temperature cycling or harsh environments are a concern, Arlon Polyimide offers superior thermal stability. On the other hand, for general-purpose applications, FR-4 materials may suffice but won’t perform under high-heat conditions as well as Arlon’s more specialized offerings.
●Mechanical and Durability Needs: If your application requires mechanical robustness (e.g., automotive or military), Arlon PCBs like AD300 or Arlon 25N provide high thermal conductivity and excellent vibration resistance.
Quick Selection Tip: If you’re working on consumer electronics and require a balance of performance and cost, Arlon FR-4 could be the go-to. However, for more demanding, high-performance projects, Arlon’s specialized laminates like polyimide-based materials should be your first choice.
Sourcing Reliable Arlon PCB Manufacturers
After you’ve pinpointed the right Arlon PCB materials for your project, the next step is to select a trusted supplier. Finding a reliable PCB manufacturer is a major piece of the puzzle when it comes to getting your product delivered on time and in top condition.
Factors to Look for in a Supplier-
●Reputation and Reviews: Check for manufacturers with a proven track record of working with high-performance materials like Arlon PCBs. Look for reviews and testimonials from companies in your industry to gauge their expertise.
●Production Capabilities: Ensure the manufacturer has experience with your specific Arlon material. Not all manufacturers handle specialized materials like Arlon Polyimide or high-frequency laminates with equal proficiency. Ask about their production processes and the technology they use to ensure they can handle complex, multi-layer designs.
●Certifications and Compliance: Ensure that the manufacturer meets the industry standards such as ISO 9001, UL certification, or other relevant quality certifications. This ensures their products meet global standards of safety and quality.
●Lead Time and Communication: Choose for a supplier who offers clear communication and transparent lead times. Ask about order tracking, shipping times, and their responsiveness to questions or adjustments during production.
Pro Tip: Get multiple quotes and ask for samples before committing to a large order. This helps verify both the quality of the material and the manufacturer’s ability to meet your specific project needs.
Understanding Cost Considerations for Arlon PCB Procurement
Cost considerations are an integral part of the procurement process for Arlon PCB materials. While these materials provide unmatched performance, they may come with a higher upfront cost compared to traditional FR-4 boards. Understanding how to balance quality, quantity, and cost will help you make informed procurement decisions.
Breaking Down Costs-
●Material Cost: High-performance Arlon PCB laminates (e.g., polyimide and high-frequency materials) generally cost more than standard FR-4. However, the increased performance can lower long-term costs by reducing the need for repairs or replacements in high-stress environments.
●Manufacturing Costs: Specialized Arlon PCB materials may require more intricate manufacturing techniques, which can add to the overall cost. For example, multi-layer PCB designs using Arlon’s materials may involve more complex lamination processes and additional quality checks.
●Volume Discounts: Purchasing in bulk can help reduce the unit cost. Consider your production needs and whether large-scale procurement might lower the price per unit. Most suppliers offer discounts for bulk orders, but make sure to factor in shipping and storage costs.
Example: If you’re working on a large automotive project, sourcing Arlon PCB materials in bulk may give you a better deal on each unit. However, for smaller-scale applications, you may need to balance costs and performance by selecting FR-4 or Arlon’s more cost-effective options.
Cost Factor | Arlon PCB | FR-4 PCB |
Material cost | Higher due to specialized properties | Generally lower, but limited in performance |
Manufacturing complexity | Higher due to multi-layer and thermal requirements | Less complex to produce |
Volume discounts | Available for large orders | Typically lower in bulk purchasing |
Pro Tip: If you’re working on high-stakes projects where performance cannot be compromised, consider the long-term value of Arlon PCBs over cheaper alternatives. Reduced maintenance costs, fewer design revisions, and higher overall reliability can justify the initial investment.
Why Choose JarnisTech for Your Arlon PCB?
When it comes to Fabrication high-performance Arlon PCBs, JarnisTech stands out as one of the leading manufacturers in the industry. With over 20 years of experience in producing high-quality PCBs and electronic components, we are committed to providing our clients with top-tier products and outstanding service. Whether you need Arlon PCBs for telecommunications, automotive electronics, aerospace applications, or other specialized uses, we have the expertise to deliver solutions tailored to your needs.
At JarnisTech, we understand the importance of precision and durability in your projects. That’s why we offer customized Arlon PCB manufacturing options based on your specific requirements, including thickness, size, and shape. We leverage cutting-edge technology and top-grade materials to ensure that your PCBs meet the highest industry standards.
Why JarnisTech?
●20+ years of experience: We’ve honed our craft over two decades, delivering exceptional results across diverse sectors.
●Customizable options: From thickness to shape and size, we can adapt to the unique specifications of your project.
●Fast delivery: We prioritize on-time delivery so that your projects keep moving forward without delay.
●Competitive pricing: We offer highly competitive prices, ensuring you get the best value for your investment without compromising on quality.
●Comprehensive support: Our team is here to provide you with guidance at every step of the way, from design to assembly.
Whether you’re looking for high-frequency performance or thermal stability in your PCBs, JarnisTech delivers Arlon PCB materials that excel in these critical areas. Our expertise allows us to cater to a wide range of applications, ensuring your designs function optimally in even the most demanding environments.
At JarnisTech, we know that reliability and quality matter, which is why we manufacturing Arlon PCB circuit boards are to withstand tough conditions and maintain their signal integrity and thermal stability. No matter the challenge, you can trust JarnisTech to provide the solutions you need for your next project.
Reach out to us today! Whether you need a quote, want to discuss your Arlon PCB needs, or are ready to place an order, JarnisTech is here to help. Send us your inquiries at [email protected], and let’s get your project off the ground with superior PCBs at the best prices in the market!
JarnisTech is not just a supplier, but a partner in innovation. Together, we’ll build solutions that meet your exact needs, driving your success and creating long-term value for your business. Let’s build something great together!
FAQ
What are Arlon PCBs used for?
Arlon PCBs are a go-to choice in high-frequency sectors such as telecommunications, radar systems, automotive electronics, and aerospace because they excel in maintaining signal clarity and managing heat. These materials are particularly effective in environments where both precision and durability are non-negotiable, like in military and medical devices.
What makes Arlon PCBs suitable for high-frequency applications?
Arlon PCBs are designed with low dielectric loss and stable dielectric constants that ensure superior signal integrity at high frequencies. These properties reduce signal degradation, making Arlon PCBs ideal for high-frequency applications like 5G networks, RF circuits, and satellite communications.
How do Arlon PCBs handle high temperatures?
Arlon materials, especially their polyimide-based laminates, offer outstanding thermal stability and can endure extreme temperatures.
Are Arlon PCBs more expensive than other materials?
Arlon PCBs are typically more expensive than standard FR-4 PCBs due to their advanced materials and specialized manufacturing processes. However, their high performance, reliability, and longer lifespan often justify the cost in high-end applications, especially where reliability is non-negotiable.
Can Arlon PCBs be used in multilayer designs?
Yes, Arlon PCBs are well-suited for multilayer designs because of their excellent thermal and electrical properties. These characteristics help maintain reliable performance across multiple layers, particularly in RF and high-power applications.
Our special materials
PCB Fabrication
Arlon PCB Laminate & Materials Series