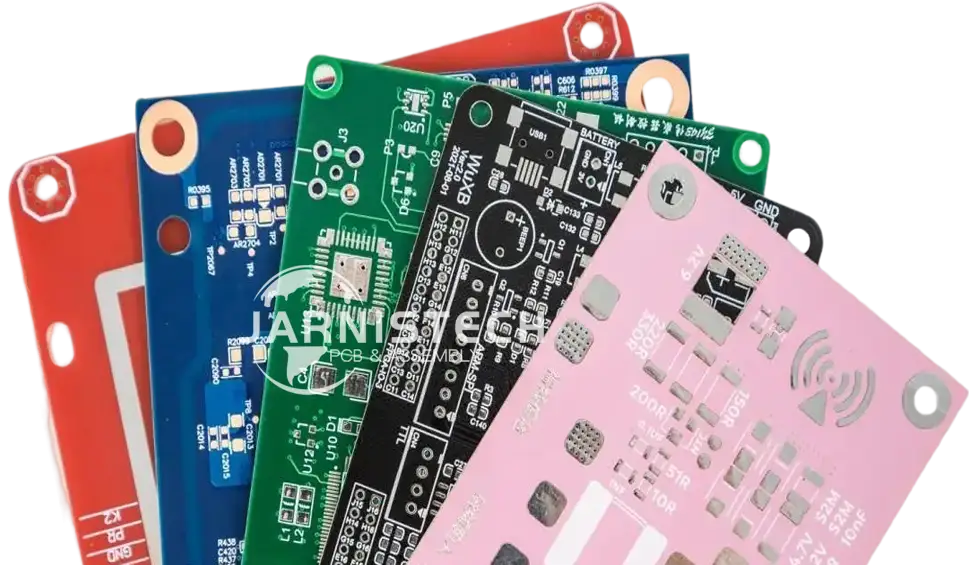
PCB soldermask is one of the unsung components of a printed circuit board (PCB), yet it holds immense significance in ensuring the board’s functionality, longevity, and overall performance. Over the years, we alike have learned to appreciate the role it plays in circuit board designs—going far beyond just protection. In this article, we dive deep into the world of PCB soldermask. We’ll explore its evolution, material types, color options, and costs.
A Fresh Look at PCB Soldermask
PCB soldermask is often seen as just a protective layer, but it plays a much deeper role in the overall functionality and performance of a circuit board. At its core, soldermask is a layer of resin that’s applied to a PCB, leaving only the areas meant for component soldering exposed. This coating offers far more than just a protective shield against the environment—it’s an integral part of how your board performs, survives, and thrives in various applications.
Soldermask serves as more than just a shield against moisture, dust, and contaminants. It plays an integral role in ensuring a PCB’s longevity, withstanding various environmental challenges and maintaining peak performance across different applications. Whether it’s for everyday consumer gadgets or sophisticated industrial systems, the proper selection and application of soldermask can greatly enhance the PCB’s resilience and functionality. Think of it as the unsung protector that keeps your circuits in top shape, even under tough conditions.
The Evolution of PCB Soldermask Technology
From its humble beginnings as a simple barrier to prevent solder from bridging, PCB soldermask technology has come a long way. Initially, it was a straightforward liquid applied to the PCB to keep excess solder in check. But with advances in material science and manufacturing techniques, soldermasks have transformed into a multi-functional element that can enhance the electrical and mechanical properties of a PCB.
Early soldermask formulations were relatively simple. Over time, however, the need for more complex boards—such as high-density interconnects (HDI) and flexible PCBs—has pushed the development of more sophisticated materials. Today, we can use advanced formulations that provide high performance in signal integrity, thermal dissipation, and even harsh environmental conditions.
For instance, Liquid Photoimageable (LPI) soldermask technology has allowed for higher precision and more detailed applications. This process uses ultraviolet light to cure the material, ensuring that soldermask is applied precisely where needed, while the areas to be soldered remain exposed. The result? More durable, reliable, and functional circuit boards that can handle complex designs and intricate features.
Why PCB Soldermask is the Backbone of Circuit Board Durability?
Think of soldermask as the protector of your circuit board—a layer that ensures your board remains intact under the harshest conditions. Without it, your PCB would be vulnerable to physical wear, oxidation, moisture, and other contaminants that could cause major failures. Over the years, many manufacturers have perfected soldermask materials and application techniques to offer more than just protection. They enhance your board’s ability to survive, perform, and maintain its integrity through all sorts of challenges.
For instance, take a PCB used in automotive electronics. These boards face extreme temperatures, moisture, and harsh chemicals daily. The right soldermask ensures that these boards continue to perform reliably over the lifespan of the vehicle. Similarly, in medical devices, soldermask protects sensitive components from environmental damage, ensuring that the board remains operational when needed most.
Choosing the right soldermask material and application method can drastically influence the performance and longevity of a PCB, and that’s something us should never overlook.
Surprising Roles PCB Soldermask Plays in Modern Electronics
In high-speed communication devices, soldermask contributes to maintaining signal integrity by preventing unintended signal leakage and ensuring clean signal paths. In power electronics, where components generate significant heat, the soldermask helps manage thermal dissipation, preventing heat from damaging the PCB or interfering with circuit operation. These advanced applications highlight the versatility of soldermask, which is no longer just a “nice-to-have” but a must-have in advanced designs.
Real-Life Example:
A great example of how soldermask plays a role in high-frequency circuits is in the telecommunications industry. For 5G antennas and base station equipment, PCBs are required to handle extremely fast data transmissions without interference. The soldermask used in these PCBs needs to be engineered to resist signal degradation while allowing for high-speed data to flow seamlessly.
Moreover, in the automotive industry, which often demands rugged PCBs for vehicles’ onboard systems, the soldermask prevents oxidation, which could otherwise lead to short-circuiting in harsh outdoor environments. This keeps the board functional under challenging conditions, from freezing temperatures to intense heat in engine compartments.
Understanding PCB Soldermask
PCB soldermask is often viewed simply as a protective layer, but it’s far more complex than that. In the world of printed circuit boards, soldermask is an essential material that serves both protective and performance-enhancing roles. Applied to the surface of a PCB, it isolates conductive areas while ensuring that only the pads for component soldering remain exposed. But soldermask’s job goes beyond just keeping the board clean—it contributes to the durability, signal integrity, and heat management of your entire circuit.
Let’s dive deeper into the functions and significance of soldermask, exploring how it impacts a PCB’s design and performance across various applications.
What is PCB Soldermask?
At the heart of every PCB lies soldermask, a thin layer of polymer material that protects the copper traces beneath. The primary function of soldermask is to isolate these copper traces from external factors—dust, moisture, and other contaminants that might cause damage or short circuits. However, soldermask also contributes to the operational reliability of the circuit board by preventing solder bridges and ensuring that components can be properly soldered.
To give you a clearer understanding, here’s a breakdown of soldermask’s basic functions and the materials used in its production.
Basic Functions and Materials Used in PCB Soldermask-
Function | Description | Common Materials Used |
Protection Against Contaminants | Shields PCB from dust, moisture, and chemical damage. | Epoxy, LPI, Acrylic |
Electrical Isolation | Prevents electrical shorts by covering unwanted areas. | Epoxy, UV-Curable |
Prevents Solder Bridging | Stops solder from connecting adjacent pads. | LPI, Epoxy |
Enhances PCB Reliability | Increases the longevity of the PCB in harsh environments. | UV-Curable, Epoxy |
Key Functions of PCB Soldermask in Circuit Boards
PCB soldermask serves a variety of functions that extend beyond protection. It is a tool that ensures your PCB remains functional and reliable throughout its lifecycle. One of the lesser-known roles of soldermask is its contribution to signal integrity and thermal management. In high-frequency circuits, where even the slightest hiccup can throw off performance, the soldermask steps in to keep signal integrity rock-solid. It’s like having a backstage crew that keeps the show running flawlessly, ensuring your PCB handles the heat—both literally and figuratively—without breaking a sweat.
Here’s a deeper dive into some of soldermask’s functions, including how it helps optimize performance in specific applications.
Key Functions of PCB Soldermask-
Function | Explanation | Importance in PCB Design |
Signal Integrity | Prevents electrical noise and interference. | Ensures reliable performance, especially in high-speed circuits. |
Thermal Management | Aids in dissipating heat generated by components. | Crucial in high-power or high-density applications. |
Chemical Protection | Guards against chemical reactions and corrosion. | Increases the lifespan of the PCB in harsh environments. |
Prevention of Short Circuits | Avoids unwanted electrical connections between traces. | Prevents faults in densely packed circuit boards. |
As you can see, soldermask does much more than provide basic protection. It enhances the PCB’s functionality in ways that improve both performance and longevity.
How PCB Soldermask Enhances PCB Reliability and Performance?
For PCB manufacturers and designers, the goal is always to create PCBs that perform reliably, even under the most demanding conditions. PCB soldermask contributes directly to this by offering durability against environmental challenges. Whether it’s exposure to heat, humidity, or chemicals, the right soldermask ensures the PCB remains operational and effective.
Additionally, soldermask helps in the reliability of high-frequency designs. For instance, signal loss can be reduced by using the correct soldermask formulation.
How PCB Soldermask Affects Performance and Reliability-
Factor | Description | Effect on PCB Design |
Temperature Resistance | Ability to withstand high or low temperatures without degradation. | Protects boards in automotive or aerospace applications. |
Chemical Resistance | Resistance to chemicals like solvents, oils, and acids. | Extends the life of boards exposed to harsh chemicals. |
UV Resistance | Resilience against UV rays, preventing degradation. | Ensures longevity for outdoor and solar applications. |
Longevity | The expected life of the PCB under normal conditions. | Increases the lifespan of the PCB, reducing the need for replacement. |
By choosing the right soldermask material, we can ensure that the PCB stands up to a variety of environmental and operational challenges, providing a higher level of durability and longevity.
Types of PCB Soldermask and Their Applications
When it comes to designing PCBs, one of the most crucial decisions is selecting the appropriate soldermask. While most may assume that it’s a one-size-fits-all solution, the truth is, soldermasks come in various types, each offering unique benefits depending on the application. Whether you’re building a high-speed circuit or a simple consumer product, the soldermask you choose will significantly influence the performance, durability, and reliability of your PCB. Let’s dive into the different types of soldermask and their specific uses across various industries.
Liquid Photoimageable (LPI) PCB Soldermask
Liquid Photoimageable (LPI) soldermask is one of the most commonly used types in PCB manufacturing. This process involves applying a liquid mask to the PCB surface and then exposing it to ultraviolet (UV) light, which hardens the mask where exposed. The unexposed areas are washed away, leaving the desired pattern on the board. This process offers excellent resolution, making it suitable for high-density PCBs.
LPI soldermask is ideal for applications where precise, fine features are required. It’s commonly used in high-frequency electronics, consumer devices, and automotive PCBs.
1.Key Benefits of LPI Soldermask-
●High Precision: Capable of forming fine lines and detailed features on high-density interconnect (HDI) boards.
●Superior Conformance to Traces: Ensures a better match to the underlying copper, reducing the risk of short circuits.
●Flexible: Supports both standard and advanced PCB designs.
2.Advantages of Liquid Photoimageable (LPI) Soldermask-
Feature | LPI Soldermask Characteristics | Applications |
Precision | Forms sharp, clean edges, especially for fine traces. | Ideal for HDI, compact consumer electronics. |
Compatibility with High-Frequency | Excellent for high-speed signals. | Used in RF devices, automotive applications. |
Durability | Provides reliable protection against moisture and contaminants. | Electronics exposed to harsh conditions. |
Customizability | Can be customized for various design requirements. | Ideal for complex circuit designs. |
Peelable PCB Soldermask for Prototyping and Repairs
When it comes to prototyping and repairs, a peelable soldermask is often the solution of choice. This type of soldermask is temporary and can be peeled off once the PCB has been soldered. It’s typically used in situations where the PCB is going through multiple iterations during the prototyping phase or when repairs need to be made to specific areas of the board.
Peelable soldermask is great for flexibility in design iterations, enabling us to modify the board as they test different components. The ability to remove soldermask without damaging the PCB underneath makes it an ideal option for prototyping and low-volume production.
1.Key Benefits of Peelable Soldermask-
●Easy Removal: Peelable soldermask can be removed manually, leaving the PCB underneath intact.
●Cost-Effective for Prototypes: Great for low-volume runs where multiple revisions are expected.
●Perfect for Repairs: Allows for targeted repairs without disrupting the entire PCB design.
2.Benefits and Applications of Peelable Soldermask-
Benefit | Description | Application |
Quick Removal | Peel it off after soldering or testing to make quick fixes. | Used in PCB prototyping, repair, and low-volume production. |
Cost-Effective | Low cost compared to permanent soldermasks. | Perfect for prototype designs or quick-turnaround projects. |
Flexibility | Offers flexibility during design adjustments. | Best used when multiple iterations of the same PCB design are needed. |
UV-Curable and Epoxy-Based PCB Soldermask Options
UV-curable and epoxy-based soldermask options provide a more durable and stable solution compared to LPI and peelable types. These soldermasks are commonly used in high-performance applications where the PCB will be exposed to harsh environments. UV-curable soldermask is applied in liquid form and then cured under UV light, making it ideal for high-volume production. Epoxy-based soldermask, on the other hand, is a more rigid material that’s ideal for applications requiring stronger resistance to heat and chemicals.
Both UV-curable and epoxy-based soldermasks offer excellent protection for PCB components, ensuring long-term functionality and reliability.
1.Key Benefits of UV-Curable and Epoxy-Based Soldermask-
●High Resistance to Chemicals and Heat: These options are ideal for extreme environments like automotive and aerospace.
●Durable: These soldermasks provide robust protection, especially for demanding applications.
●Faster Curing Process: UV-curable soldermasks can be processed quickly, making them a good choice for high-volume production runs.
2.UV-Curable and Epoxy-Based Soldermask Features-
Feature | UV-Curable Soldermask | Epoxy-Based Soldermask |
Cure Process | Cured using UV light for faster processing times. | Cured at high temperatures for stronger bonding. |
Heat Resistance | Good heat resistance, ideal for high-power circuits. | Excellent thermal stability, even under extreme heat. |
Chemical Resistance | Resists corrosion from moisture and chemicals. | Superior chemical resistance, ideal for automotive or industrial applications. |
Durability | Offers long-lasting performance. | Offers strong physical protection and longevity. |
Choosing the Right PCB Soldermask Color for Your Design
When it comes to designing a PCB, the choice of soldermask color may seem like a mere aesthetic decision, but it goes beyond just looks. The color of your soldermask can influence several practical factors, such as visibility, inspection, and even signal integrity. In this section, we’ll dive deep into the different soldermask colors available, how each one impacts your design process, and why you should choose the right one for your application.
Standard PCB Soldermask Colors and Their Applications
Standard PCB soldermask colors include green, blue, red, and black, with green being the most commonly used. These colors are not just for show; each offers unique advantages depending on the specific needs of the PCB and the end product.
●Green is the most widely used soldermask color due to its historical dominance in the PCB manufacturing industry. It provides good contrast with copper traces, making it easier for operators to visually inspect the PCB during manufacturing. The green color is also associated with more affordable manufacturing and is often the go-to for general consumer electronics and large-volume production.
●Blue and red are commonly used for specialized designs, such as high-end consumer products or military-grade electronics, where color can enhance brand identity or aid in the differentiation of multiple products. These colors tend to have better contrast under certain lighting conditions, which can be advantageous for inspecting fine details during production.
●Black is often chosen for products that require minimal light reflection or where aesthetics matter, such as in premium electronics or wearables. Black soldermask is ideal for environments with high thermal stresses or where a low-reflection surface is needed for applications like high-end computing and high-frequency circuits.
Common Soldermask Colors and Their Applications-
Soldermask Color | Common Applications | Advantages |
Green | Consumer electronics, large-volume production | Widely available, cost-effective, good contrast for visual inspection. |
Blue | High-end consumer electronics, military-grade | Better contrast for visual inspection under certain lighting. |
Red | Custom designs, premium consumer products | Provides good visual contrast for fine trace inspection. |
Black | Wearables, high-end computing, premium electronics | Low reflection, thermal resistance, ideal for high-frequency use. |
How PCB Soldermask Color Impacts Automated Optical Inspection (AOI)?
In Automated Optical Inspection (AOI), the soldermask color is a game-changer for quality control precision. AOI systems depend heavily on visual contrast to spot defects in solder joints, traces, and vias. A high-contrast soldermask enhances the system’s ability to zero in on irregularities, while a poor choice can throw a wrench in the process.
For example, a green soldermask typically provides excellent contrast against the copper, making it easier for AOI machines to spot defects like short circuits, open traces, or insufficient soldering. On the other hand, dark colors such as black may make detection more difficult because they absorb light rather than reflecting it, potentially hiding imperfections under low lighting conditions.
Moreover, specialized soldermask colors such as blue or red are sometimes chosen to optimize the visibility of certain features, especially in high-resolution inspections. These colors may provide better visibility under different lighting conditions, making them suitable for more complex PCBs with smaller traces and pads.
Soldermask Colors and Their Effect on AOI Efficiency-
Soldermask Color | Effect on AOI Detection | Recommended Use Case |
Green | High contrast, ideal for accurate inspection | General consumer electronics, high-volume production. |
Blue | Provides good contrast in specific lighting | Military-grade electronics, precision PCB designs. |
Red | Excellent for high-contrast and detailed inspection | Small form factor designs, low-volume prototyping. |
Black | Poor contrast, may hide defects under certain lighting | High-frequency applications, wearables. |
Custom PCB Soldermask Colors for Specialized Use Cases
For some projects, a custom soldermask color is the only way to go. Whether it’s for branding, specialized industrial needs, or enhanced PCB performance, custom colors allow us to meet specific demands.
●Branding: Custom soldermask colors are frequently used in consumer electronics to enhance brand identity. A unique color can make your product stand out on store shelves, creating a lasting impression. Many high-end gadgets and wearables sport custom soldermask colors as part of their visual appeal.
●Specialized PCB Applications: In industries like aerospace, automotive, and medical devices, specific color choices may be linked to certain functional properties. For example, green soldermask is often the default in medical-grade PCBs due to its balance of cost and performance, while red or blue may be chosen for aerospace applications requiring higher durability or specific light reflectivity.
●Performance Considerations: Sometimes, a unique color can be selected for practical reasons, such as improved heat dissipation or better light reflection in optical systems. Custom colors can be engineered to meet specific thermal or electrical properties for high-power or high-frequency applications.
Custom Soldermask Colors and Their Specialized Applications-
Custom Color | Application | Functionality & Advantage |
Gold | Luxury consumer electronics | Enhances the brand image and appeal for premium products. |
Purple | High-performance computing and wearables | Optimized for better signal reflection and heat dissipation. |
White | Optoelectronics, medical devices | Provides enhanced visibility and is often chosen for optical applications. |
Custom Color | Aerospace, automotive, medical devices | Tailored to meet specific requirements for durability and heat resistance. |
PCB Soldermask Thickness: Guidelines and Impact
Soldermask thickness may not be the first thing you consider in PCB manufacturing, but trust us—getting it right is we need to achieving optimal board performance and long-term reliability. From high-frequency circuits to automotive-grade electronics, the soldermask layer’s thickness directly influences heat dissipation, mechanical stress tolerance, and electrical performance. Let’s explore best practices for soldermask thickness, its impact on design, and how to steer clear of common pitfalls.
Optimal PCB Soldermask Thickness for Various Applications
The ideal soldermask thickness can vary significantly depending on the application of the PCB. Whether you’re working with consumer electronics or high-end industrial machinery, understanding the specific needs of your design will help you choose the right soldermask thickness.
●Standard Consumer Electronics: For typical consumer electronics such as smartphones, laptops, or home appliances, a soldermask thickness between 15 µm and 25 µm is commonly used. This range is thin enough to protect the PCB from environmental factors like dust and moisture while ensuring that the board remains lightweight and cost-effective.
●High-Frequency PCBs: For applications where signal integrity and electrical performance are top priorities, like RF (Radio Frequency) circuits or high-speed digital designs, the soldermask thickness needs to be controlled precisely. Typically, thinner soldermasks between 8 µm and 12 µm are preferred to minimize the inductance and capacitance introduced by the mask. This helps to ensure that signals don’t degrade or interfere with other components.
●Automotive and Aerospace Applications: These sectors require rugged PCBs that can withstand extreme temperatures, vibration, and mechanical stress. A thicker soldermask, generally around 25 µm to 35 µm, is used to improve the board’s thermal resistance and protect it from physical damage.
Recommended Soldermask Thickness by Application-
Application | Recommended Thickness Range | Key Benefits |
Consumer Electronics | 15 µm to 25 µm | Lightweight, cost-effective, sufficient protection. |
High-Frequency PCBs | 8 µm to 12 µm | Reduced signal interference, enhanced electrical performance. |
Automotive & Aerospace | 25 µm to 35 µm | Improved thermal resistance and physical durability. |
Common Issues Related to PCB Soldermask Thickness
Choosing the right soldermask thickness isn’t just about performance—too thin or too thick can lead to a number of common issues that could throw a wrench in your production process.
●Too Thin: When the soldermask is too thin, it can compromise the protection of the PCB. The thinner layer may not provide adequate resistance to moisture, chemicals, or physical abrasion, leaving the underlying traces exposed to damage. Additionally, thinner soldermasks can cause issues with solder bridging, where excess solder flows into unintended areas.
●Too Thick: On the flip side, an overly thick soldermask can introduce unwanted electrical resistance. This can affect signal integrity, particularly in high-frequency applications, leading to signal distortion and increased heat generation. Thicker soldermasks may also delay the curing process, which can lead to defects or inconsistent coating.
●Uneven Thickness: Uneven soldermask application can result in inconsistent board performance, with certain areas being overexposed to external contaminants while others are left inadequately protected. This can affect automated inspection processes, leading to costly errors or scrapped boards.
Common Issues with PCB Soldermask Thickness-
Issue | Cause | Impact on PCB Performance |
Too Thin | Inadequate coverage or application | Increased susceptibility to damage, poor protection. |
Too Thick | Over-application or improper curing | Electrical interference, heat issues, slow curing. |
Uneven Thickness | Inconsistent application process | Irregular protection, inspection difficulties. |
How to Measure and Ensure Consistent PCB Soldermask Thickness?
Ensuring that the soldermask thickness remains consistent across the entire PCB is a critical step in the manufacturing process. Here’s how you can effectively measure and control soldermask thickness.
●Contact Method Measurement: One of the most common methods for measuring soldermask thickness is through a contact profilometer, which uses a stylus to physically touch the surface of the PCB and measure the thickness at different points. While this method is highly accurate, it may not be suitable for complex shapes or high-volume production.
●Non-Contact Methods: For high-speed manufacturing, laser-based or X-ray technologies are used to measure soldermask thickness. These methods are non-destructive and allow for high-throughput measurements, making them ideal for mass production of PCBs.
●Inspection Tools: To ensure consistent thickness during the application process, automated inspection tools can be used to monitor the soldermask as it is applied to the board. These tools provide real-time feedback to operators, allowing for quick adjustments if the thickness strays from the desired range.
Methods for Measuring Soldermask Thickness-
Measurement Method | Description | Advantages |
Contact Profilometer | Stylus physically touches the surface to measure thickness | High accuracy, effective for small batches. |
Laser-Based Measurement | Uses laser to scan the surface for thickness | Non-destructive, high throughput, ideal for mass production. |
X-ray Inspection | Uses X-ray technology to analyze soldermask thickness | Non-contact, effective for complex geometries. |
The PCB Soldermask Application Process: Step-by-Step Guide
When manufacturing PCBs, achieving the highest quality soldermask application isn’t just about covering traces and pads—it’s a fine-tuned process that ensures your circuit board will perform under the toughest conditions. PCB soldermask plays a pivotal role in protecting components, improving durability, and even enhancing performance. Let’s break down this process step by step, focusing on the intricate techniques that drive efficiency and reliability in PCB production.
Surface Preparation Before Applying PCB Soldermask
Before any soldermask is applied, preparing the PCB surface is a step that can’t be overlooked. A clean, smooth, and properly prepped surface is the foundation of a successful soldermask layer, which ultimately impacts the adhesion and functionality of the soldermask.
1.Cleaning and Degreasing: The first step is to remove any dirt, oils, or residues that could prevent the soldermask from adhering properly. This step often involves chemical cleaning solutions and solvent baths. Depending on the application, manufacturers may also use ultrasonic cleaning to remove any hard-to-reach contaminants from the board’s surface.
2.Etching the Surface: To promote better adhesion of the soldermask, the copper pads on the PCB are often etched. This involves using a mild acid solution to slightly roughen the copper surface, which enhances mechanical bonding for a more durable soldermask layer.
3.Drying the PCB: Any moisture left on the PCB after cleaning and etching can cause problems during the application of soldermask, such as bubbling or delamination. The drying process is typically conducted in an oven or vacuum chamber, ensuring a completely dry, contaminant-free surface before the soldermask is applied.
Surface Preparation Process-
Step | Description | Purpose |
Cleaning & Degreasing | Remove all surface contaminants using solvents. | Prevents contamination that could affect adhesion. |
Etching | Roughen copper pads using mild acid solutions. | Improves mechanical bond between soldermask and PCB. |
Drying | Use heat or vacuum to dry the PCB. | Ensures moisture-free surface for better adhesion. |
Imaging and Curing Techniques for PCB Soldermask
Once your PCB is prepared, it’s time to apply the soldermask itself. This step involves a precise and systematic application that involves imaging, curing, and hardening the soldermask to ensure it properly covers all the desired areas while leaving pads and traces exposed.
1.Applying the Soldermask Layer: The soldermask material, often in a liquid form, is applied across the entire PCB using screen printing or soldermask lamination techniques. After applying the initial layer, the board is ready for imaging.
2.Imaging the Soldermask: Here, a photomask or negative film with patterns representing the exposed copper pads is applied over the PCB. UV light is then projected through the mask, causing the photopolymer in the soldermask to harden in the areas exposed to light, while the areas under the mask remain uncured. This creates the precise patterns necessary for the final product.
3.Curing the Soldermask: After imaging, the board undergoes a curing process—either UV curing or thermal curing—which hardens the soldermask, ensuring that it can withstand heat and other stress factors during the PCB’s lifecycle. The UV curing method is most common due to its fast processing time, but for thicker layers or certain conditions, thermal curing may be used.
Imaging and Curing Process-
Step | Description | Purpose |
Applying the Soldermask | Screen printing or lamination of liquid soldermask. | Covers the PCB and prepares it for imaging. |
Imaging | Expose the soldermask to UV light through a photomask. | Creates patterns for copper exposure. |
Curing | Expose the soldermask to UV or heat to harden it. | Ensures durability and thermal resistance. |
Final Inspection and Quality Control of PCB Soldermask Layers
Once the soldermask has been applied and cured, it’s time for the final inspection and quality control. This step ensures that the PCB meets strict quality standards and is free from defects, ensuring long-term reliability.
1.Automated Optical Inspection (AOI): Using high-resolution cameras, AOI can detect imperfections such as soldermask voids, misalignment, or defective curing. This process allows manufacturers to inspect the boards quickly and accurately.
2.Thickness Measurement: The thickness of the soldermask must be consistent throughout the PCB to avoid performance issues. Laser micrometers and other precision instruments are used to measure the soldermask thickness, ensuring it falls within the required range for specific applications.
3.Environmental Testing: For certain applications, especially those in harsh environments (e.g., automotive, aerospace, medical), environmental testing is performed to verify the soldermask’s ability to withstand thermal cycling, humidity, and UV exposure. These tests simulate real-world conditions and ensure the board can survive over time.
Quality Control and Inspection Process-
Step | Description | Purpose |
Automated Optical Inspection (AOI) | Use cameras and software to inspect the soldermask layer. | Detect defects such as misalignment or voids. |
Thickness Measurement | Use laser or micrometers to measure soldermask thickness. | Ensure uniform thickness for durability. |
Environmental Testing | Subject the board to extreme conditions. | Verify the soldermask’s performance under stress. |
●Pro Tip: Inspections and quality control aren’t just about catching defects; they’re about ensuring the performance and longevity of your PCB design. Testing early and often will save you from costly repairs and reworks later.
Advanced Applications of PCB Soldermask in HDI and Flex PCBs
As the demand for advanced electronic devices continues to rise, PCB soldermask has evolved to meet the requirements of High-Density Interconnect boards and flexible PCBs. These specialized PCBs are integral to high-performance and compact applications, ranging from smartphones to medical devices. In this section, we’ll dive into how soldermask plays a role in these advanced PCBs, addressing challenges and offering insights into optimizing soldermask performance for these specific types.
PCB Soldermask for High-Density Interconnect (HDI) Boards
HDI boards are designed to handle high-performance tasks, making them ideal for smartphones, wearables, 5G devices, and high-speed circuits. These boards are characterized by their tiny vias, fine-pitch traces, and multiple layers that allow for superior electrical performance in a compact form factor. When it comes to PCB soldermask for HDI boards, several factors need to be considered to ensure both quality and efficiency.
1.Material Selection: For HDI boards, liquid LPI soldermask stands out as the preferred choice due to its exceptional precision and adaptability. This material provides the high-definition resolution required for accurately coating the intricate fine-pitch traces and minuscule vias characteristic of HDI layouts. Its capability to detail small features without compromising durability ensures the board’s reliability and consistent performance in demanding applications.
2.Application Precision: HDI boards require high-precision soldermask application. The small dimensions of HDI boards make them prone to misalignment during the soldermask coating process. Advanced imaging systems and automated application processes help ensure that the soldermask is evenly applied to the small, intricate features of the board.
3.Thermal Considerations: HDI boards often face high thermal stress due to their small size and high-density interconnects. Therefore, the soldermask must offer excellent thermal resistance. High-performance epoxy-based soldermask is commonly used in this scenario, as it provides exceptional resistance to heat while maintaining its integrity under extreme conditions.
Key Characteristics of Soldermask for HDI Boards-
Feature | LPI Soldermask | Epoxy-based Soldermask |
Resolution | High (ideal for fine-pitch traces) | Moderate (best for less intricate designs) |
Thermal Resistance | Moderate | High (withstands higher temperatures) |
Application Method | Automated, precise | Requires careful handling |
Durability | Good | Excellent, especially in extreme conditions |
Common Use Case | High-speed circuits, compact electronics | Military, aerospace, automotive |
Challenges of Applying PCB Soldermask on Flexible PCBs
Flexible PCBs are becoming more prevalent due to their ability to bend and fold, making them ideal for wearables, medical devices, and flexible displays. However, applying PCB soldermask to these types of boards presents unique challenges due to their physical properties and design requirements.
1.Material Flexibility: Unlike rigid PCBs, flexible boards must be coated with soldermask materials that can handle dynamic stress. The soldermask used must not crack, chip, or delaminate when the board is bent. Flexible soldermask materials, like UV-cured soldermask, are often used in this application because they retain their flexibility and adhesion even after multiple cycles of bending.
2.Uniform Coating Application: One of the major challenges with flexible PCBs is ensuring that the soldermask is applied uniformly across the entire board, including the bends and corners. Traditional spray coating or immersion methods may not be suitable for these designs. Specialized techniques like vacuum lamination or precision application are often necessary to ensure that the soldermask adheres properly to the flexible material.
3.Environmental Factors: Flexible PCBs are often exposed to extreme environmental conditions such as high humidity, extreme temperatures, or exposure to chemicals. This makes it essential for the soldermask to be chemically resistant and durable. Epoxy-based soldermask is particularly effective in these applications because of its superior chemical resistance and high bonding strength.
Challenges and Solutions for Flexible PCB Soldermask-
Challenge | Solution | Why It Works |
Material Flexibility | Use UV-cured or flexible soldermask | Maintains flexibility and adhesion after bending |
Uniform Coating | Employ precision coating techniques | Ensures even coverage across flexible surfaces |
Environmental Resistance | Choose epoxy-based soldermask | Offers superior resistance to chemicals and temperature variations |
Bending Stress | Laminate or use flexible soldermask materials | Prevents cracking or peeling during bending cycles |
PCB Soldermask Compatibility with Surface Finishes
When it comes to designing high-quality PCBs, ensuring that your soldermask is compatible with your chosen surface finish is a fundamental step. The interaction between soldermask and surface finishes, like ENIG (Electroless Nickel Immersion Gold), HASL (Hot Air Solder Leveling), and OSP (Organic Solderability Preservative), has a direct impact on the performance and durability of your PCB. Let’s dive into how these finishes interact with soldermask layers and explore best practices for achieving the best results.
Interaction of PCB Soldermask with ENIG, HASL, and OSP
Different surface finishes each bring unique characteristics when combined with PCB soldermask. Understanding how these finishes interact helps prevent issues like poor adhesion, soldermask defects, or even PCB failure in special applications.
1.ENIG (Electroless Nickel Immersion Gold): ENIG is a highly popular surface finish that offers a smooth, flat surface, making it ideal for high-density interconnects. However, ENIG can present challenges when bonding with soldermask. Since ENIG surfaces tend to be very smooth and have minimal roughness, ensuring a strong bond with the soldermask can be tricky. To improve this, we may employ surface activation treatments like plasma treatment or micro-etching to create a rougher texture for better adhesion.
2.HASL (Hot Air Solder Leveling): HASL is a widely used finish, known for its cost-effectiveness and compatibility with a variety of components. When combined with soldermask, HASL can create issues if the soldermask is not adequately applied, leading to inconsistent coverage or delamination at the edges. This is due to HASL’s solder residue, which can affect the soldermask’s adhesion properties. To prevent this, ensure that HASL layers are properly cleaned and that the soldermask is cured properly.
3.OSP (Organic Solderability Preservative): OSP finishes provide a thin layer of organic material that preserves copper surfaces, which is ideal for lead-free applications. While OSP does offer excellent adhesion with soldermask, there is a risk of degradation over time when exposed to heat. The interaction of OSP with soldermask is largely dependent on environmental conditions, so special attention is required to prevent delamination or oxidation during the application process.
Interaction of Surface Finishes with PCB Soldermask-
Surface Finish | Characteristics | Soldermask Compatibility | Best Practices |
ENIG | Smooth, ideal for HDI | Potential for poor adhesion unless treated | Use plasma or micro-etching for better adhesion |
HASL | Cost-effective, widely used | Can cause delamination if solder residues remain | Ensure thorough cleaning and curing of soldermask |
OSP | Thin organic layer, great for lead-free | Excellent adhesion but prone to heat degradation | Apply soldermask in a controlled environment |
Preventing Defects When Combining PCB Soldermask and Finishes
While surface finishes provide essential benefits, combining them with the wrong soldermask process can lead to defects. Preventing these issues requires careful planning and attention to detail.
1.Defects Due to Misapplication: One of the most common issues when applying soldermask over surface finishes is misalignment. Misaligned soldermask during the imaging process can lead to exposed copper pads or improperly protected areas. This can cause shorts, overheating, or signal interference in high-frequency applications.
2.Inconsistent Coating: Surface finishes like HASL can cause the soldermask to form inconsistent coatings, especially at areas where the finish has been unevenly applied. This can be problematic when fine traces are involved, leading to potential failures in electrical performance.
3.Chemical Reactions: Chemical incompatibilities between the soldermask and the surface finish can cause issues during the curing process. Some finishes, like OSP, are particularly susceptible to oxidation, which can affect how well the soldermask bonds to the board.
Common Defects and Preventive Measures-
Defect Type | Cause | Preventive Measures |
Misalignment | Soldermask applied incorrectly during imaging. | Use automated imaging systems to ensure alignment. |
Inconsistent Coating | Uneven finish application on the surface. | Ensure uniform application and curing of finishes. |
Chemical Reactions | Incompatible chemical processes. | Test for compatibility before proceeding with full application. |
●Pro Tip: Pay close attention to curing temperatures—especially with HASL and OSP—as these finishes can react differently to heat, impacting the soldermask application.
Enhancing Adhesion Between PCB Soldermask and Surface Layers
A durable and strong bond between the soldermask and the surface finish is fundamental to ensuring the PCB’s long-term performance. There are several strategies to enhance adhesion, even with challenging surface finishes like ENIG or HASL.
1.Surface Treatment: Utilizing techniques like plasma treatment or micro-etching can significantly improve soldermask adhesion to smoother finishes like ENIG. These methods increase the roughness of the surface, providing the soldermask with more to adhere to.
2.Optimizing Curing Conditions: Proper curing of the soldermask is necessary to ensure a durable bond with the surface finish. Using precise temperature control during the curing process can avoid issues such as under-curing or over-curing, both of which can weaken the bond.
3.Choosing the Right Soldermask: Different types of soldermask are better suited to certain finishes. For instance, liquid photoimageable (LPI) soldermask typically works well with a wide range of surface finishes. However, if you’re dealing with HASL, consider using a thicker soldermask layer to account for surface inconsistencies.
Enhancing Adhesion Between Soldermask and Surface Finishes-
Surface Finish | Adhesion Enhancement Technique | Optimal Soldermask Type |
ENIG | Plasma treatment, micro-etching | LPI soldermask |
HASL | Ensure proper cleaning, apply thicker soldermask | Thicker soldermask to compensate for surface roughness |
OSP | Apply soldermask in a controlled environment | Use medium-thickness soldermask to prevent oxidation |
●Pro Tip: Plasma treatment isn’t just for ENIG—it’s a useful technique for improving soldermask adhesion to nearly all surface finishes. Don’t overlook this simple yet effective method.
Common Defects in PCB Soldermask and How to Fix Them
When it comes to PCB soldermask, defects are more than just an eyesore—they can directly impact the functionality and durability of your PCB. The soldermask layer acts as a protective shield, and if it’s not applied correctly, it can lead to significant issues in your final product. This section will walk you through the most common soldermask defects, how to identify them, and the best ways to tackle these problems head-on.
Identifying Common PCB Soldermask Defects
The soldermask layer is meant to protect the copper traces on a PCB, but even the best soldermask can develop defects during the manufacturing process. Here are some of the most common issues you might encounter:
1.Bubbles: Bubbles in the soldermask layer occur when air pockets get trapped during the application or curing process. These can lead to poor adhesion and can potentially expose the copper underneath, creating weak points on your PCB.
2.Cracks: Cracks in the soldermask are typically a result of thermal stress, which occurs when the PCB is subjected to high temperatures during the soldering process or due to improper curing. These cracks can compromise the integrity of the PCB, leading to potential circuit failure.
3.Discoloration: A soldermask’s color may fade or change, often due to heat exposure or UV degradation. This discoloration doesn’t just affect the appearance—it could be a sign of underlying damage or improper curing that weakens the soldermask.
Common Soldermask Defects and Indicators-
Defect Type | Description | Indicator Signs | Potential Causes |
Bubbles | Air pockets trapped in soldermask during application or curing. | Visible blisters on the surface. | Inadequate degassing, improper curing conditions. |
Cracks | Fractures in the soldermask layer. | Thin cracks or fractures on the surface. | Thermal stress during soldering or improper curing. |
Discoloration | Changes in color of the soldermask. | Faded or yellowed soldermask. | Exposure to high temperatures or UV degradation. |
●Pro Tip: Always check the curing process to ensure that bubbles or cracks don’t form during the application. The right temperature and controlled curing times can make all the difference.
Root Causes of PCB Soldermask Bubbles, Cracks, and Discoloration
To prevent soldermask defects, it’s important to dig into the root causes. Issues like bubbles, cracks, or discoloration don’t just appear out of nowhere – each one has its own set of reasons tied to the application or curing process.
1.Bubbles: Air bubbles can form when the soldermask is applied too thickly or when there is insufficient degassing before the layer is cured. If the soldermask material isn’t allowed to properly off-gas, air will become trapped under the surface, leading to the formation of bubbles.
2.Cracks: The primary cause of cracks is thermal expansion and contraction. When a PCB goes through the soldering process, the temperature fluctuations can cause the soldermask to expand and contract, leading to fractures. Improper circuit board handling during the reflow soldering process can exacerbate this issue, causing the soldermask to break under stress.
3.Discoloration: Overexposure to UV light or excessive heat can cause the soldermask material to degrade, resulting in discoloration. Heat exposure during the curing process or the soldering process can weaken the material’s integrity, while UV light degradation leads to fading over time. If the soldermask is not cured under appropriate UV light conditions, discoloration may occur.
Causes of Soldermask Defects-
Defect Type | Root Cause | Solution |
Bubbles | Trapped air due to improper degassing or over-thick application. | Use proper degassing techniques and ensure even application of soldermask. |
Cracks | Thermal stress from improper soldering temperature control. | Monitor and regulate temperature during reflow and soldering process. |
Discoloration | Exposure to high temperatures or UV light degradation. | Control curing temperatures and UV light exposure for optimal results. |
●Pro Tip: To prevent cracks, make sure your reflow soldering process is precise and controlled. Also, try reducing soldermask thickness in areas that experience the highest thermal stresses.
Best Practices for Troubleshooting PCB Soldermask Issues
Troubleshooting soldermask issues can be tricky, but with the right techniques and best practices, you can quickly get to the root of the problem and fix it. Here are the best practices to follow:
1.Perform Visual Inspections: Start by doing a thorough visual inspection of your PCB for visible defects such as bubbles, cracks, or discoloration. Utilize high-powered magnification to check for small defects that could cause long-term damage.
2.Check Curing Parameters: Ensure that the soldermask is properly cured during the manufacturing process. Both under-curing and over-curing can lead to defects. Use precise temperature controls to avoid these issues.
3.Use a Quality Soldermask: Choose a high-quality soldermask that is designed for the type of PCB you are working on. Resilient soldermask materials can withstand higher temperatures and UV exposure without cracking or discoloring.
4.Monitor Environmental Conditions: Make sure your manufacturing environment is stable, especially regarding humidity and temperature, as both can impact the soldermask curing process.
5.Clean and Degas: Proper cleaning and degassing of the board before applying soldermask are essential steps in preventing defects like bubbles. Make sure that the board is free from dust and debris before application.
Best Practices for Preventing Soldermask Defects-
Practice | Description | Benefits |
Visual Inspections | Use magnification to inspect for defects. | Early identification of issues like cracks or bubbles. |
Proper Curing | Ensure soldermask is cured under optimal conditions. | Avoid under or over-curing defects. |
Use Quality Soldermask | Select high-quality, durable soldermask. | Ensures resilience against thermal and UV stress. |
Environmental Control | Control temperature and humidity during manufacturing. | Prevents issues caused by environmental variations. |
Cleaning and Degassing | Thoroughly clean and degas the PCB before application. | Prevents air bubbles and ensures even soldermask coverage. |
PCB Soldermask for High-Frequency and High-Speed Designs
As electronic devices become more complex and faster, the need for high-speed and high-frequency circuit boards has increased significantly. PCB soldermask helps to ensure signal integrity, manage heat, and maintain reliability in systems where top performance is a must. In this section, we will explore how soldermask contributes to improving these aspects for high-frequency and high-speed PCB applications, ensuring that your designs meet the ever-growing demands.
How PCB Soldermask Affects Signal Integrity?
1.Impedance Matching: Soldermask helps maintain the correct impedance of PCB traces, which is particularly noticeable in high-frequency designs.. If the soldermask isn’t applied evenly, it can cause impedance mismatch, leading to signal reflections and loss of high-frequency signals. This is particularly true for microstrip and stripline configurations, where the soldermask acts as an insulating layer between the conductive traces and the environment.
2.Thickness and Consistency: The thickness and uniformity of the soldermask layer also play a role in minimizing signal loss. For high-speed circuits, a thinner and more consistent soldermask layer reduces the risk of signal distortion. A soldermask that’s too thick can distort the high-frequency signals, leading to attenuation.
●Practical Tip: When designing for high-frequency applications, always opt for a low-loss, high-performance soldermask material. Consider using liquid photoimageable (LPI) soldermask for better precision and signal integrity.
Impact of Soldermask Thickness on Signal Integrity-
Soldermask Thickness | Effect on Signal Integrity | Recommended Application |
Thin (< 25µm) | Reduces signal loss, improves performance | High-speed and RF applications |
Medium (25–50µm) | Moderate signal loss, good for standard circuits | General high-frequency designs |
Thick (> 50µm) | Increased signal attenuation | Not recommended for high-speed applications |
Managing Thermal Performance with PCB Soldermask
Thermal management is another challenge for high-speed and high-frequency PCBs. With faster signal transmission, heat dissipation becomes more critical. The soldermask material you choose can have a direct impact on the board’s ability to handle heat. Here’s how:
1.Thermal Conductivity: The soldermask plays a role in protecting the PCB against overheating. For high-frequency designs, it’s essential to use soldermask materials that have low thermal resistance. Materials like epoxy-based soldermask tend to perform well under higher temperatures. This helps in dissipating heat from the components without damaging the PCB or the solder joints.
2.Heat Dissipation: As signals move at high speeds, they generate heat that needs to be efficiently dissipated to prevent thermal damage. Soldermask helps protect sensitive components by acting as an insulator, but it also plays a role in directing heat away from critical areas. In high-frequency circuits, managing excess heat is necessary to prevent the degradation of performance due to thermal buildup. The soldermask’s function isn’t just about protection—it also helps in regulating heat and ensuring stable operation.
●Practical Tip: For high-performance applications, select thermally conductive soldermask materials. These will help manage heat better and avoid potential thermal problems down the line.
Thermal Performance of Different Soldermask Materials-
Soldermask Material | Thermal Conductivity | Ideal Application |
Epoxy-based | Moderate | High-frequency, general use |
Polyimide-based | High | High-temperature, aerospace |
Liquid Photoimageable (LPI) | Low to Moderate | Standard high-speed designs |
Cost and Optimization Strategies for PCB Soldermask
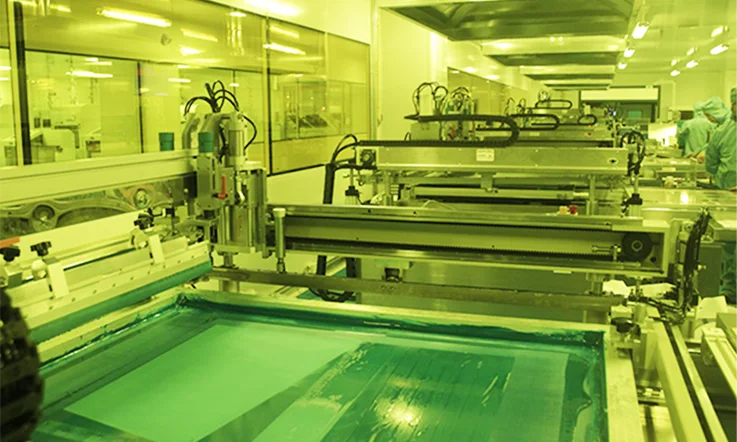
When working with PCB soldermask, understanding the cost structure and how to optimize it can help keep production expenses in line without sacrificing quality. Whether you’re handling mass production or creating just a few prototypes, managing costs wisely becomes a major factor. In this section, we’ll walk you through the factors that influence soldermask costs and how to strike the perfect balance between cost-efficiency and performance.
Factors That Influence PCB Soldermask Costs
The cost of applying soldermask to a PCB can vary significantly depending on several key factors. Here’s a breakdown of the most common elements that influence soldermask pricing:
1.Material Type: Different soldermask materials come at different price points. For example, liquid photoimageable soldermask is typically more affordable than other high-performance options, but it may not offer the same level of durability. Epoxy-based or UV-cured soldermask often come at a premium because of their superior chemical resistance and better performance in harsh environments.
2.Board Size and Thickness: Larger or more complex PCBs require more soldermask material and a more intricate application process, which can increase the cost. Similarly, thicker boards with more layers demand more time and effort during application, raising the cost per unit.
3.Manufacturing Complexity: The complexity of the PCB design can affect the cost. If the design includes fine traces, multiple layers, or high-density interconnects, the process becomes more labor-intensive, requiring precise application techniques and more expensive equipment.
4.Quantity of Units: The more units you order, the lower the cost per PCB. Large batch runs often result in reduced material costs and economies of scale, allowing you to save on soldermask application. On the other hand, smaller quantities or prototypes may see higher per-unit costs due to setup fees and labor time.
5.Environmental Considerations: If you’re producing PCBs that need to meet specific environmental standards (such as RoHS compliance or low-halogen materials), this can add to the overall cost. These materials are often more expensive to manufacture and require specialized processes.
Factors Influencing PCB Soldermask Costs-
Factor | Impact on Cost | Explanation |
Material Type | Varies depending on the performance and durability | LPI is cheaper, while epoxy-based or UV-cured materials cost more. |
Board Size & Thickness | Larger/thicker boards cost more | More material and application time required. |
Manufacturing Complexity | Higher complexity increases costs | Fine traces, HDI, and multi-layer boards need more intricate work. |
Quantity | Higher quantity lowers per-unit cost | Bulk production allows for better cost efficiency. |
Environmental Considerations | Eco-friendly materials increase cost | Compliance with environmental regulations raises the cost. |
Balancing Cost and Quality in PCB Soldermask Selection
Finding the right balance between cost and quality in your soldermask selection is a delicate balancing act. It’s tempting to go for the cheapest option, but remember that compromising too much on quality can result in long-term performance issues, increased defects, and costly repairs down the road. Here’s how to strike that perfect balance:
1.Prioritize Function Over Flash: Not all PCBs require the highest quality soldermask. If your project is for basic applications or prototypes, opting for a less expensive material like LPI soldermask might make sense. However, for high-performance applications or boards exposed to harsh conditions, UV-cured or epoxy-based soldermask may be worth the extra cost due to their higher durability and better adhesion.
2.Standardize Material Choices: If you’re producing in bulk, standardizing your soldermask material can help streamline your production process and reduce costs. Using the same material for all your PCBs simplifies the setup process, reduces material waste, and allows you to negotiate better pricing with suppliers.
3.Factor in Long-Term Costs: While a cheaper soldermask might seem like a cost-saver upfront, it may result in higher long-term expenses. For instance, if you use a soldermask that wears out quickly or discolors, you could face issues down the road with component failures or repair needs. On the flip side, a more durable soldermask might have a higher upfront cost, but it could save you money in repairs, replacements, and product failures.
4.Evaluate Application Requirements: Not all projects demand premium soldermask. If the design is low-density and will not face harsh conditions, you can likely choose for a more affordable soldermask material. However, for applications like high-speed circuits or boards exposed to extreme temperatures or chemicals, it’s wise to invest in a higher-quality soldermask to ensure reliability and performance.
Cost vs. Quality in PCB Soldermask Selection-
Selection Criteria | High-Quality Soldermask | Cost-Effective Soldermask |
Performance | Higher durability, better adhesion, UV resistance | Lower durability, adequate for low-stress applications |
Applications | High-performance, extreme conditions | Prototypes, basic or low-density designs |
Material Type | Epoxy-based, UV-cured | LPI or standard soldermask |
Long-Term Value | Lower risk of defects, fewer repairs | May lead to higher long-term repair costs |
Upfront Cost | Higher cost per unit | Lower cost per unit |
Note: Consider the application-specific needs of your PCB. If you’re working with low-cost products or prototypes, go with an affordable soldermask option. But, if you’re designing for demanding industries like aerospace or medical devices, the extra investment in quality materials is a no-brainer.
Why Choose Us?
China’s Leading PCB Manufacturer – JarnisTech: Your Trusted Partner for High-Quality Circuit Boards
At JarnisTech, we pride ourselves on being at the forefront of PCB manufacturing, offering cutting-edge solutions that meet the demands of today’s innovative electronics industry. Our team of experienced production engineers has handled a diverse range of soldermask colors and surface finishes, ensuring that your PCBs not only meet functional requirements but also stand out with a touch of customization. Whether you’re looking to differentiate your product in the market or make a striking impression during a presentation, we’ve got your back.
JarnisTech’s PCB Solder Mask Manufacturing Capability
Attribute | Details |
PCB Solder Mask Brands | – KSM-S6189: Green, Black, Yellow, Red, Blue, Matte Green, Matte Black |
– Taiyo PSR-4000 G23K: Green | |
– ABQ RS-2000 V-5: Purple | |
PCB Solder Mask Colors | Green, Yellow, Black, Blue, Red, White, Orange, Purple, Pink, Matte Green, Matte Black, etc.. |
PCB Solder Mask Cover Trace | 2 mil (allows partially down to 1.5 mil) |
Solder Mask Dam | – Finish Copper ≤ 1oz: 4 mil (Green) |
– Finish Copper ≤ 1oz: 5 mil (Other Colors) | |
PCB Solder Mask Thickness | Maximum: 25 µm (Printed Twice) |
Standard (Printed Once): | |
– Copper Plane Area: 10–18 µm | |
– Via Edge: ≥ 5 µm | |
– Copper Trace Edge: ≥ 5 µm | |
Max Via Size for Plugging | 0.5 mm |
Talk to Us Today
Ready to bring your PCB design to the next level? Don’t settle for generic solutions when you can create something truly exceptional. Contact us today and discover how our expertise in custom soldermask colors and cutting-edge manufacturing techniques can elevate your next project.