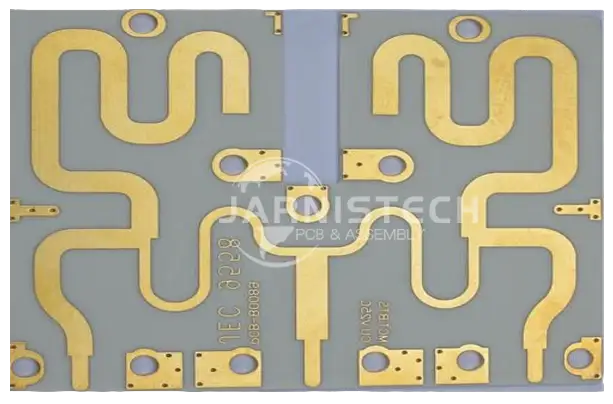
When it comes to handling high-frequency, RF (radio frequency), and microwave applications, Teflon PCBs are nothing short of a breakthrough in the world of circuit board technology. Designed with PTFE (polytetrafluoroethylene) materials, these PCBs go beyond the ordinary, ensuring a smooth and reliable transmission of signals even in the most demanding environments. From telecommunications to aerospace, Teflon PCBs have staked their claim as the backbone of high-frequency applications. Here, we dive into the intricate details of Teflon PCB design, materials, manufacturing techniques, and best practices to bring you a top-notch guide that captures everything you need to know.
What is a Teflon PCB?
An In-Depth Look at High-Frequency and RF Performance
Teflon PCBs are a type of printed circuit board specifically engineered to perform exceptionally well in high-frequency applications, like radio frequency (RF) and microwave systems. Unlike traditional FR4 PCBs, Teflon PCBs are made using Polytetrafluoroethylene (PTFE), which boasts remarkable properties, especially when dealing with signal integrity in high-speed communications. But what exactly makes Teflon so appealing for these applications? Let’s break it down and take a closer look.
The Science Behind Teflon PCB Materials and RF Benefits
Teflon is a synthetic polymer known for its low dielectric constant and low loss tangent—properties that make it an ideal material for high-frequency circuits. These characteristics reduce signal loss and distortion, enabling clean and clear signal transmission even at higher frequencies.
In high-frequency systems, the dielectric constant of the PCB material affects how quickly signals travel through the board. For instance, lower dielectric constants lead to faster signal propagation, which is exactly what you need for RF communication. Teflon, with its low dielectric constant, ensures that your signal quality remains intact, even when dealing with signals in the gigahertz range.
In addition to its electrical properties, Teflon PCBs are known for their resistance to extreme environmental conditions. Whether you’re dealing with high temperatures, humidity, or aggressive chemical environments, Teflon can handle it.For applications like satellite communications or radar systems, where reliability is a must, Teflon’s ability to resist environmental stress makes it a go-to choice. It doesn’t break down, keeping your system in top form no matter the challenge.
Property | Teflon PCB | Impact on RF Performance |
Dielectric Constant | 2.0-2.5 | Lower values allow faster signal propagation |
Loss Tangent | <0.001 | Minimal signal loss over long distances |
Temperature Stability | High | Withstands extreme temperatures without performance drop |
Electrical Performance | Excellent | Ensures integrity of signals even at GHz frequencies |
Teflon’s ability to maintain high-frequency performance with minimal signal degradation allows engineers to push the limits of what’s possible in telecommunications and microwave technologies. Want your design to work flawlessly under extreme conditions? Teflon PCBs can deliver.
Key Electrical Properties of Teflon PCBs for Signal Integrity
To get the most out of Teflon PCBs, it’s all about managing those key electrical properties. Signal integrity is top of mind for engineers, and Teflon doesn’t disappoint. Here’s why:
Low Loss Tangent: Teflon’s low loss tangent helps to minimize energy dissipation, which allows signals to travel further with less attenuation. This feature is especially beneficial in high-speed and high-frequency circuits, where maintaining signal strength over long distances is a priority. Whether you’re dealing with RF designs or fast digital signals, Teflon helps reduce signal degradation, making it an excellent material for demanding applications.
Stable Dielectric Constant: The dielectric constant of a material determines how the material affects the flow of electromagnetic fields. With Teflon, this constant remains stable over a wide range of frequencies, which is a huge advantage in applications like microwave circuits where consistent performance is necessary for signal transmission.
Impedance Control: When working with high-frequency designs, managing impedance is a must. Teflon PCBs make this a whole lot easier thanks to their stable dielectric properties. This consistency means you can control impedance with precision, keeping your signal paths clean and free from reflections or data loss. No need to worry about pesky signal degradation—Teflon’s got your back. So, whether you’re tackling RF circuits or any high-speed application, this material ensures that your signals stay sharp and steady, exactly where you want them.
Electrical Property | Teflon PCB | Impact on Signal Integrity |
Dielectric Constant | 2.0-2.5 | Helps reduce signal distortion by maintaining consistent signal velocity |
Loss Tangent | <0.001 | Ensures minimal signal loss, leading to reliable data transmission |
Impedance Control | Precise | Facilitates better control of signal impedance, preventing reflections |
Attenuation | Low | Lower attenuation leads to longer-range transmission with reduced noise |
When your design demands signal integrity in applications such as wireless communication, 5G networks, or aerospace electronics, Teflon offers a reliable and efficient solution. In fact, it’s a go-to material for those who need performance that won’t quit, even in the most demanding environments.
Teflon PCB vs. Other High-Frequency Substrates: A Comparison
When it comes to choosing the right PCB material for high-frequency applications, the market offers several options. But Teflon stands out for a variety of reasons. Let’s put it side-by-side with other commonly used substrates like FR4, ceramic PCBs, and PTFE composites to see how it compares.
Material | Dielectric Constant | Loss Tangent | Signal Integrity | Applications |
Teflon (PTFE) | 2.0-2.5 | Very Low | Excellent | RF, Microwave, 5G |
FR4 | 4.0-4.5 | Moderate | Good but prone to signal loss at high frequencies | Consumer electronics, low-frequency circuits |
Ceramic PCBs | 3.0-10.0 | Low to Moderate | Excellent | High-end RF, automotive |
PTFE Composites | 3.0-4.0 | Low | Good | General RF applications |
Teflon beats other materials hands down in RF and microwave circuits, particularly in terms of signal integrity. FR4, while widely used, doesn’t hold up as well at high frequencies because it has a higher dielectric constant and higher loss tangent, leading to signal loss over longer distances.
Ceramic PCBs, on the other hand, are great for precision applications, but they are more expensive and can be harder to process. While PTFE composites are similar to Teflon, the performance can vary depending on the composition. Simply put, if you’re looking for consistent and reliable performance in RF or microwave systems, Teflon takes the cake.
In real-world applications, when you’re working on a 5G system or high-performance radar, Teflon is the material that can handle the task—it’s built to keep signals clean and interference-free, whether in medical imaging devices or telecommunications equipment.
Types of Teflon PCB Laminates for High-Frequency and Microwave Applications
When it comes to high-frequency and microwave applications, the type of Teflon laminate you choose can have a huge impact on the overall performance and reliability of your circuit. These laminates are specifically designed to maintain signal integrity and ensure minimal signal loss, even at high frequencies.
Common Teflon PCB Laminates and Their Frequency Capabilities
Teflon-based laminates are available in various formulations, each with unique properties suited to different high-frequency applications. These laminates include PTFE-based composites, Rogers materials, and other specialized blends. Let’s break down some of the most commonly used Teflon laminates and their specific frequency capabilities.
Laminates | Frequency Range | Applications | Dielectric Constant | Loss Tangent |
Rogers 4003C | Up to 40 GHz | High-speed, RF, Microwave | 3.38 | 0.0025 |
Rogers 4350B | Up to 30 GHz | RF and communications | 3.48 | 0.003 |
Teflon (PTFE) | Up to 100 GHz | Aerospace, 5G, Microwave | 2.65 | 0.0002 |
Rogers RT/duroid 6002 | Up to 60 GHz | Military, radar, and satellite | 2.94 | 0.001 |
As shown in the table, Teflon laminates like PTFE and Rogers RT/duroid are highly effective for applications requiring signal integrity at high frequencies. Rogers 4003C and 4350B are commonly used for RF communications and microwave circuits, providing good performance while balancing cost and reliability.
The higher the frequency range a laminate can handle, the more precision is required in manufacturing and assembly. Rogers and Teflon composites are the go-to choices for engineers who demand optimal performance at GHz-level frequencies.
Differences Between Rogers and Teflon PCB Materials
When deciding between Rogers and Teflon materials, it’s key to understand their unique properties and how they can affect your RF and microwave designs. Rogers materials are well-known in the PCB world for their precision and reliability, but Teflon laminates have their own advantages when it comes to performance at extreme frequencies.
Property | Rogers Materials | Teflon (PTFE) Materials |
Dielectric Constant | 3.0 – 10.0 | 2.0 – 3.0 |
Loss Tangent | 0.002 – 0.003 | 0.0002 |
Frequency Range | Up to 60 GHz | Up to 100 GHz |
Thermal Stability | High | Moderate to High |
Cost | Moderate to High | High |
Here’s the rundown: Rogers materials like 4003C and 4350B are known for their excellent thermal stability and reliability under demanding conditions. They offer a slightly higher dielectric constant and loss tangent compared to Teflon. On the flip side, Teflon laminates stand out due to their extremely low loss tangent, making them perfect for high-performance microwave and 5G applications that require minimal signal loss.
Choosing between Rogers and Teflon boils down to the frequency range and performance needs of your specific application. If you’re aiming for high-frequency performance, Teflon might be the best fit. But if you need a more cost-effective solution that offers reliability in a wide range of applications, Rogers could be the better choice.
Choosing the Right Teflon PCB Laminates for Specific Applications
Selecting the appropriate Teflon PCB laminate depends on the application’s specific needs—whether it’s 5G communications, microwave systems, aerospace, or medical devices. Understanding how different laminates behave at various frequencies and under different conditions will ensure you’re making the right decision.
Application | Recommended Teflon Laminate | Why This Choice | Frequency Range |
5G Communications | Teflon (PTFE), Rogers 4003C | High-speed, low loss, and low dielectric constant | Up to 100 GHz |
Aerospace and Military | Rogers RT/duroid 6002, Teflon | Precision and low loss at extreme conditions | Up to 60 GHz |
Medical Device Circuits | Rogers 4350B, Teflon | Consistent performance in high-performance environments | Up to 30 GHz |
Microwave Circuits | Teflon (PTFE), Rogers 4003C | Excellent signal integrity and high frequency handling | Up to 60 GHz |
In the table, you’ll notice that Teflon laminates like PTFE and Rogers 4003C are the preferred materials for high-frequency communications (such as 5G). For military and aerospace applications, Rogers RT/duroid 6002 provides reliable performance even under harsh conditions. In medical devices, it’s all about signal clarity, and Rogers 4350B or Teflon are often the go-to solutions.
Making the right choice boils down to understanding your specific needs—whether you’re designing for precision or reliability. Don’t settle for less! Get the right material to ensure your design works flawlessly.
Teflon PCB Manufacturing Techniques and Challenges
When it comes to Teflon PCB manufacturing, the techniques used are not your everyday processes. These materials require precision and care, not just because of their unique properties, but also due to the specific challenges they pose. From drilling and etching to lamination and bonding, the whole process demands attention to detail and specialized equipment to ensure top-notch quality.
Drilling and Etching Teflon PCB Materials for Precision
Handling the drilling and etching of Teflon PCBs is anything but straightforward. Thanks to Teflon’s distinct molecular makeup, it doesn’t react the same way as standard PCB materials. When you’re working with high-frequency circuits or microwave systems, dialing in precision for both drilling and etching makes all the difference in keeping signal quality intact. Achieving this level of accuracy means staying on top of every little detail—there’s no cutting corners here if you’re aiming for performance that hits the mark.
Drilling: Standard drills can cause excessive heat, which might lead to cracks or burrs. Teflon PCBs require diamond-coated drills or laser drilling to avoid these issues. The drill speed must be carefully controlled to minimize heat generation and prevent material degradation. High-speed drilling techniques such as laser ablation are often used to ensure precision without causing damage to the laminate.
Etching: Teflon etching requires special attention because the material’s chemical properties make it resistant to most acids used in conventional etching. Plasma etching or laser etching is commonly employed for high-frequency applications, as it ensures the fine features needed for microwave and 5G circuits without compromising signal paths.
Process | Standard PCBs | Teflon PCBs | Challenges |
Drilling | Conventional carbide drills | Diamond-coated drills, lasers | Higher precision required for signal integrity |
Etching | Acid etching | Plasma etching, laser etching | Material resistance to standard acids |
Etching Precision | Standard etching processes | High-precision required | Ensuring accuracy at high frequencies |
As you can see, when working with Teflon PCBs, precision is non-negotiable. One wrong move during the drilling or etching process, and the performance could be compromised. That’s why it’s crucial to choose the right equipment for the job. If you need top-notch performance in your designs, don’t skimp on the details.
Lamination and Bonding in Teflon PCB Manufacturing
Lamination and bonding are key stages in Teflon PCB manufacturing that demand both finesse and patience. Since Teflon is not as easily bonded as traditional materials, manufacturers have to employ specialized techniques to ensure strong, reliable bonds.
Lamination Process: The Teflon PCB laminating process typically involves stacking layers of Teflon film with other reinforcing materials, such as glass fiber or copper foil. The combination of high temperature and pressure ensures the material adheres properly, but you can’t just apply heat and call it a day. The bonding temperature must be precisely controlled to avoid damage to the material.
Bonding Techniques: Teflon PCBs require specialized bonding adhesives that can withstand high temperatures and extreme environments. Acrylic-based adhesives and epoxy resins are commonly used for bonding Teflon layers to the copper and glass layers in the PCB stack-up. The bonding needs to be strong enough to handle the mechanical stress that often accompanies high-frequency circuits.
Lamination Technique | Traditional PCB | Teflon PCB | Challenges |
Bonding Materials | Standard epoxies, resins | Acrylic-based adhesives, epoxies | Difficulty achieving strong bonds with Teflon |
Lamination Process | Pressed at standard temps | Higher temperatures required | Material sensitivity to heat |
Pressure and Temperature | Standard heat and pressure | Precise control needed | Preventing delamination and damage |
When working with Teflon PCBs, you’re dealing with a process that goes beyond standard lamination. Achieving a solid and dependable final product means using the right bonding agents and keeping temperature control in check. Skimp on either, and you might end up with weak spots that can compromise your circuit’s overall performance. Teflon’s unique characteristics demand attention to these finer details if you’re looking for a result that’ll stand up to the demands of high-frequency applications.
Handling and Processing Challenges of Teflon PCBs
Processing Teflon PCBs comes with its fair share of challenges. This material requires a more meticulous approach, not only in the manufacturing process but also in storage and handling. Whether you’re dealing with small-scale prototypes or large-volume production, ensuring the material stays in top condition is a must.
Handling Teflon PCBs: Teflon is notoriously sensitive to moisture and temperature. Improper handling can cause delamination or affect the overall signal integrity. For this reason, Teflon PCBs should be kept in controlled environments with low humidity and constant temperature. The material should also be handled with care to avoid physical damage during the manufacturing process.
Processing Challenges: One of the major challenges is the thermal mismatch between Teflon PCBs and standard copper traces. Teflon and copper have different thermal expansion rates, which can lead to stress on the board during high-temperature operations. Special care is needed to match expansion rates and ensure that the copper traces don’t peel off or crack during use.
Challenge | Standard PCBs | Teflon PCBs | Solution |
Handling Sensitivity | Easy to handle | Sensitive to moisture & temp | Store in low-humidity, controlled environments |
Thermal Mismatch | Minimal concerns | Significant expansion difference | Use materials with matched thermal expansion rates |
Physical Damage | Robust | Brittle, prone to cracking | Handle with care, avoid bending or warping |
These challenges highlight the need for a careful, precise approach when working with Teflon materials. Attention to detail during both the handling and processing stages can make the difference between a successful project and a costly failure. So, don’t cut corners—be methodical in your approach.
How to Design Teflon PCBs for Optimal High-Frequency Performance?
Designing Teflon PCBs for high-frequency applications calls for a methodical approach, one where every decision affects signal clarity and overall performance. To get the most out of these specialized boards, you’ll want to focus on carefully selecting materials, setting up the right layer stack-up, and dialing in impedance control. Each step in the process—from planning through execution—requires precision. Let’s dive into some top strategies for optimizing Teflon PCB designs to deliver peak performance.
Best Practices for Signal Integrity in Teflon PCB Designs
When designing Teflon PCBs, maintaining signal integrity is a top priority, especially in high-frequency environments like 5G, satellite communication, and military applications. The signal integrity of a PCB directly affects its performance, so you need to approach the design with a strategy that minimizes interference and maintains strong signals over long distances.
1. Minimizing Crosstalk: Crosstalk between traces can create signal degradation, especially at microwave frequencies. To keep your design clean, use wide spacing between traces and layer separation. Keep sensitive traces away from high-power signals and ensure that return paths are well-defined to avoid unwanted coupling.
2. Grounding and Power Planes: A strong ground plane is a must. In Teflon PCB designs, having a continuous ground plane beneath the signal traces will help maintain signal integrity by providing a clear, low-resistance path for return currents. Implementing separate power planes for different voltage levels can also help avoid noise coupling from high-frequency signals.
3. Via Technology: When placing vias, keep them as short and as few as possible. Longer vias introduce inductance and capacitance, which can negatively affect signal integrity. Blind and buried vias are preferred in high-frequency designs for minimizing these effects.
Technique | Traditional PCB Design | Teflon PCB Design | Why It Matters |
Crosstalk Reduction | Wide spacing, trace shielding | More rigorous trace spacing | Keeps high-frequency signals from interfering |
Grounding | Basic ground planes | Continuous, solid ground planes | Low-resistance return paths enhance signal quality |
Via Minimization | Regular through vias | Short, minimal via usage | Reduces signal loss and electromagnetic interference |
Layer Stack-Up Considerations for Teflon PCB High-Frequency Use
When working with Teflon PCBs for high-frequency applications, the layer stack-up is a core factor that impacts how well signals move through the board. The layout of conductive layers, dielectrics, and ground planes shapes signal integrity and allows for effective impedance management. Let’s dive into the top factors to keep in mind when setting up the layer stack for Teflon PCBs, making sure each choice keeps your board performance on point.
1. Dielectric Material Choice: The dielectric constant (Dk) of the material plays a significant role in signal propagation speed. Teflon typically has a low Dk compared to traditional materials, which makes it a good choice for high-frequency designs as it reduces signal loss. Be mindful of the Dk values across all layers to ensure consistency in signal behavior.
2. Minimizing Signal Loss: For high-speed designs, the thickness of the dielectric layer between signal traces is another crucial factor. In Teflon PCBs, thinner dielectric layers help maintain signal strength, reducing losses due to longer transmission paths. However, be careful not to compromise the mechanical stability of the board by making these layers too thin.
3. Impedance Consistency: Maintaining impedance consistency across different layers is must make to ensure that signals pass through without reflections or losses. The stack-up should be optimized to ensure controlled impedance on the trace, especially for high-speed signals like those in 5G or microwave circuits.
Layer Consideration | Traditional PCB | Teflon PCB | Why It Matters |
Dielectric Material | Standard FR4 | Low-Dk Teflon | Reduces signal loss at high frequencies |
Layer Thickness | Standard thickness | Optimized for signal integrity | Ensures lower signal loss and better performance |
Impedance Control | Standard trace width | Precisely controlled traces | Maintains impedance consistency, crucial for high-speed signals |
Impedance Control Techniques in Teflon PCB Layouts
Impedance control is a critical component of any high-frequency PCB design, and it’s even more so in Teflon PCBs. Impedance mismatches can lead to signal reflections, data loss, or even failure of your system. Implementing effective impedance control techniques ensures that the high-speed signals in your Teflon PCB design flow without interference or degradation.
1. Use of Controlled Impedance Traces: The impedance of a signal trace on Teflon PCBs isn’t just about one factor—it’s a mix of trace width, dielectric thickness, and the spacing to the reference plane. For high-frequency designs, nailing down the right trace width and dielectric thickness is what gets you to target impedances like 50 ohms for single-ended signals or 100 ohms for differential pairs. Each adjustment counts, so every tweak in those values helps you stay dialed in on the ideal impedance, keeping signal quality sharp and interference low.
2. Simulation and Testing: Signal simulations using electromagnetic field solvers can be a lifesaver when designing Teflon PCBs for high-frequency applications. Simulating your impedance characteristics helps you pinpoint potential issues before the actual manufacturing begins. It’s an efficient way to ensure optimized layout and prevent costly revisions during the prototyping phase.
3. Differential Pair Routing: When working with differential pairs, achieving stable impedance is all about precision. You’ve got to keep the spacing between the traces tight and the widths just right so both traces move at the same pace and maintain matching impedance. This balance prevents any hiccups in signal quality, which is especially key in high-frequency setups where even minor variations can cause delays or distortions. In short, attention to every last detail in spacing and width is what keeps your signals cruising smooth and interference-free.
Impedance Control Method | Traditional PCB Layout | Teflon PCB Layout | Why It’s Necessary |
Trace Width Control | Standard width | Fine-tuned for precision | Ensures consistent impedance, crucial for signal integrity |
Simulation | Limited testing | Full electromagnetic simulation | Helps optimize design before manufacturing |
Differential Pair Routing | Standard pair routing | Precisely matched pairs | Maintains balanced impedance and signal speed |
Applications of Teflon PCBs in High-Frequency, RF, and Microwave Technologies
Teflon PCBs have become a go-to material for applications that demand high-frequency and microwave performance. The unique properties of Teflon—such as its low dielectric constant (Dk) and high thermal stability—make it the ideal choice for circuits that deal with RF signals and operate in the microwave spectrum. These properties are particularly important in industries like aerospace, telecommunications, and medical technology, where performance and precision are non-negotiable. Let’s dive into some of the most prominent Teflon PCB applications across these high-tech sectors.
Teflon PCB Usage in Aerospace and Defense Systems
In the aerospace and defense industries, the demand for high-performance PCBs is off the charts. These industries rely on Teflon PCBs due to their exceptional ability to handle microwave frequencies and perform under extreme conditions.
1. Radar Systems: Teflon PCBs are often used in radar equipment that operates at high frequencies. The material’s low signal loss and low dielectric constant help maintain signal clarity even in demanding environments. For example, airborne radar systems use Teflon PCBs to enhance signal transmission and detection capabilities in high-speed aircraft.
2. Communication Systems: Military and defense organizations depend on secure communication systems that operate at microwave frequencies. Teflon PCBs are designed to handle the demanding performance required in these high-frequency circuits, such as military satellites and secure military radios. These systems need to transmit and receive clear, reliable signals under harsh conditions, and Teflon’s dielectric properties are key to achieving that performance.
3. Space Exploration: Spacecraft and satellites are another area where Teflon PCBs shine. The extreme thermal environments and high-frequency demands of space communication systems require PCBs that won’t fail under pressure. Teflon’s thermal stability and low loss make it a perfect fit for space exploration applications, ensuring reliable performance for systems that may be light-years away from Earth.
Application | Typical Usage | Why Teflon Works |
Radar Systems | Airborne radar, military radar equipment | Low loss at high frequencies, stable under temperature extremes |
Military Communication | Military radios, secure satellite communications | Low signal loss, high dielectric strength |
Space Exploration | Satellite communication, deep-space systems | Excellent thermal stability, high-frequency operation |
Telecommunications and 5G Applications with Teflon PCBs
The telecommunications industry, especially with the rollout of 5G technology, is pushing the envelope on signal speeds and data transfer. For applications like 5G base stations, satellite communications, and Wi-Fi systems, Teflon PCBs are often the go-to material. Thanks to their minimal signal loss and high-frequency capabilities, these boards help keep data moving with top-notch precision, making sure signals stay strong and sharp across long distances.
1. 5G Networks: With the demand for 5G connectivity soaring, the materials used in 5G equipment must support millimeter-wave frequencies without compromising on performance. Teflon PCBs are widely used in 5G antennas, base stations, and backhaul systems due to their ability to maintain signal strength over longer distances, providing reliable data transmission across cities and countries.
2. Satellite Communication: For satellite communications, Teflon PCBs bring standout performance in electromagnetic compatibility (EMC) and minimal signal loss—qualities that become must-haves when managing signals over long distances. Teflon’s stability in high-frequency ranges supports consistent signal strength, even in satellite payload systems. When you’re working with Teflon, you’re building a buffer against the risk of signal interference and degradation, which can cause communication disruptions. This PCB material keeps things steady, making sure high-frequency signals stay intact across vast reaches, even where the slightest hiccup can impact the whole transmission.
3. Wi-Fi and Cellular Networks: With the growing need for Wi-Fi and cellular data, Teflon PCBs make sure these systems deliver smooth and fast connections. Designed for high-speed data transfer at microwave frequencies, Teflon PCBs power up 5G antennas and network interface devices, helping maintain seamless connectivity for users. Thanks to their low-loss and high-frequency capabilities, these PCBs support the demand for lightning-fast, reliable connections, keeping everyone online without a hitch. So whether it’s streaming or working remotely, Teflon-based PCBs help these systems handle the pressure, meeting the demands of our connected lives.
Application | Typical Usage | Why Teflon Works |
5G Networks | Base stations, antennas, backhaul systems | Low loss, high-frequency capability, durability |
Satellite Communication | Satellite payloads, antennas, communication equipment | Low signal attenuation, high stability at long distances |
Wi-Fi and Cellular | Wi-Fi routers, mobile network infrastructure | High-frequency performance, low signal degradation |
Medical Imaging and Diagnostic Equipment Using Teflon PCBs
In the medical tech field, precision and reliability are non-negotiable. That’s why Teflon PCBs are commonly used in high-stakes equipment like MRI machines, CT scanners, and ultrasound systems. These devices require flawless signal integrity and the ability to handle high frequencies. Teflon’s low-loss properties and solid performance in these conditions make it the go-to choice, ensuring that sensitive medical equipment operates smoothly, delivering accurate results when every second counts. Whether it’s capturing detailed images or processing data, Teflon PCBs are in the thick of it, helping healthcare professionals make informed decisions.
1. MRI Machines: Magnetic Resonance Imaging (MRI) uses high-frequency signals and requires materials that won’t interfere with the magnetic fields. Teflon PCBs are used in MRI systems for their low loss and non-interference with high-frequency electromagnetic fields, which ensures clear imaging and accurate diagnostics.
2. CT Scanners and Ultrasound Equipment: Teflon PCBs are also found in CT scanners and ultrasound devices, where microwave frequencies are used to capture detailed images of the human body. The high-frequency performance of Teflon ensures that the electrical components can function correctly without affecting the imaging results, providing doctors with clear and precise scans.
3. Wearable Medical Devices: As wearable medical devices become more advanced, the need for high-frequency electronics increases. Teflon PCBs are used in these devices to ensure stable performance, even in wireless communication between the device and the medical network.
Application | Typical Usage | Why Teflon Works |
MRI Machines | Imaging systems, diagnostics | Low signal loss, non-interference with magnetic fields |
CT Scanners & Ultrasound | Medical imaging systems, real-time diagnostics | Low loss at high frequencies, reliable data transfer |
Wearable Devices | Health monitoring systems, diagnostic wearables | Excellent signal integrity, reliable long-range communication |
Procurement Guide for OEMs and Buyers Looking for Teflon PCBs
When you’re out there sourcing Teflon PCBs for high-frequency projects, it can feel like you’re navigating a maze. With so many choices available, understanding exactly what to focus on is your ticket to securing top-notch performance and value. Whether you’re working on 5G networks, medical gadgets, or aerospace tech, being in the know about Teflon PCB procurement can help you land the right match for your business needs. Don’t get lost in the options – knowing the ins and outs will make sure you’re not just getting by, but getting the best bang for your buck.
Tips for Sourcing Teflon PCBs in High-Frequency Applications
When it comes to sourcing Teflon PCBs for high-frequency applications, the stakes are high—these circuits handle the most demanding signals, so you need materials that hold up under pressure. Here’s a guide to nailing your procurement:
Understand Material Specifications: The dielectric constant (Dk) and dissipation factor (Df) are the most important specs to watch. For RF and microwave applications, Teflon’s low Dk ensures minimal signal loss, making it the go-to for circuits that demand precision. Always ask your supplier for exact Dk values for your frequency range to ensure they match your needs.
Check Certifications: Make sure the supplier provides certified materials, especially if you’re working in aerospace, military, or medical industries. Certifications such as ISO 9001 and UL approval can help guarantee that your Teflon PCBs are built to exacting standards.
Performance Under Extreme Conditions: In fields like aerospace and telecommunications, the environment can be pretty harsh, with extreme temperatures being a real challenge. That’s where Teflon PCBs shine, offering solid thermal stability that keeps your design running smoothly whether you’re facing the heat or the cold. When shopping around for suppliers, make sure they’ve got data sheets that cover thermal cycling and performance at high frequencies across various temperatures. You don’t want to miss out on this info—it’ll help you ensure your system stays in top shape no matter the conditions.
Get Samples: Before placing a bulk order, ask for sample PCBs to test in your applications. It’s a good way to confirm the quality and fit of the material, as well as evaluate its signal integrity.
Tip | Details | Why It Matters |
Understand Specifications | Check Dk and Df values | Ensures low loss and reliable signal transmission at high frequencies |
Check Certifications | Look for ISO 9001 or UL approval | Guarantees quality and industry compliance |
Test Performance | Request sample PCBs for real-world testing | Validates the material’s high-frequency and thermal stability |
Evaluating Cost-Effectiveness and Performance of Teflon PCBs
When sourcing Teflon PCBs, it’s not just about getting the lowest price—it’s about balancing cost-effectiveness with the performance you need. Here’s how to evaluate the right material for the right price:
Assess Your Application Needs: The performance requirements of your application will impact the material choice. For example, if you’re working on 5G circuits, a lower Dk is key, but you’ll also need a material that can handle high-speed data transfer and low loss. Teflon’s superior dielectric properties make it ideal, but it can be pricey, so consider the trade-off between performance and cost.
Compare Suppliers: Prices can vary depending on the supplier’s location and manufacturing processes. Get quotes from multiple suppliers, and make sure to compare prices for the same specifications. But don’t let price be the sole deciding factor—ensure that the supplier provides consistent quality over time.
Consider Long-Term Costs: The lifetime of your Teflon PCB can affect the total cost. Higher-quality Teflon PCBs may have a higher upfront cost, but they tend to be more durable and resistant to wear and tear, which can save money in the long run by reducing the need for replacements.
Quality Control: Always ask about the supplier’s quality control procedures. Reliable suppliers will perform tests like thermal stress, electrical performance, and visual inspections. These tests help ensure you’re not just getting a cheap product but one that performs consistently and meets your specifications.
Factor | Details | Why It Matters |
Performance vs. Price | Match Dk and Df with your application needs | Achieve high signal integrity without overspending |
Compare Suppliers | Request multiple quotes, compare quality and price | Ensures best deal with consistent performance |
Consider Long-Term Costs | Factor in durability, lifespan, and reliability | Avoid costly replacements by investing in quality |
Quality Control | Ensure the supplier uses comprehensive testing | Guarantees consistent quality and reliable performance |
Custom Teflon PCB Options for Specialized RF Needs
When off-the-shelf Teflon PCBs don’t cut it for your unique design needs, custom solutions are the way to go. Many OEMs and electronics manufacturers choose for custom Teflon PCBs to meet the specific needs of their high-frequency applications. Here’s how to get the best custom solution for your specialized needs:
Custom Layer Stacks: For complex RF systems, a custom layer stack-up may be required to optimize the signal integrity and minimize interference. Work with suppliers who can provide customized laminates and dielectric materials based on your unique performance criteria, such as layer thickness and stack-up configuration.
Impedance Control: For RF designs, impedance control is a must to ensure signal transmission without reflections. Suppliers that specialize in custom Teflon PCBs should be able to handle precise impedance matching, ensuring that your microwave signals transmit with minimal loss and reflection.
Prototyping and Testing: Custom designs often require prototyping before mass production. A good supplier will be able to provide quick turnaround times for prototypes, allowing you to test the PCB under actual operating conditions before committing to a full production run.
Material Selection: If your application requires materials with specific thermal, mechanical, or electrical properties, make sure the supplier can meet those specifications. Custom Teflon PCB options can be tailored to meet unique RF needs, from specialized dielectric materials to multi-layer structures.
Custom Option | Details | Why It Matters |
Custom Layer Stacks | Tailor the stack-up to meet signal integrity | Optimize RF performance by adjusting layer thicknesses and material choices |
Impedance Control | Provide precise impedance matching | Minimize signal loss and interference in microwave systems |
Prototyping and Testing | Request rapid prototyping for real-world testing | Quickly validate custom designs and ensure reliability |
Material Selection | Customize dielectric properties for your needs | Get materials that meet exact RF requirements |
Why Choose Us?
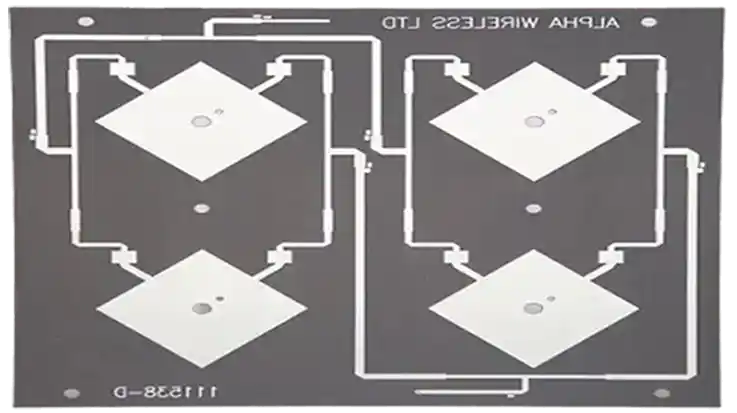
20+ Years Experiences – Trusted Top Teflon PCB Circuit Boards Manufacturer In China – JarnisTech!
Teflon’s unique properties make it one of the top picks for high-performance printed circuit boards. However, working with Teflon isn’t something just any PCB manufacturer can handle. The material requires specialized equipment and precise procedures, which not all PCB manufacturers have in place. So, when you’re searching for a Teflon PCB manufacturer, make sure you’re teaming up with a company that knows their stuff—one that has the experience and the know-how to work with Teflon and take on the challenges that come with it.
At JarnisTech, we’ve got the expertise to handle PTFE (Teflon) PCBs like no one else. Teflon is used extensively in high-frequency PCB applications, and we’ve mastered the art of manufacturing Teflon-based PCBs for demanding environments. From rapid prototype development to industry-leading quality standards, we offer a one-stop solution for all your Teflon PCB needs.
We don’t just deliver Teflon PCBs—we deliver them fast. Need a prototype? We’ve got your back with quick turnaround times that won’t compromise quality. Whether it’s a simple prototype or a complex high-frequency board, we’re all in, ready to get the job done. Top-tier quality? Always. We don’t cut corners when it comes to making sure our boards meet the highest standards in the industry.
But that’s not all. With JarnisTech, you’re working with a company that has extensive experience in high-frequency circuit board manufacturing. From Ceramic PCBs to Rogers, Taconic, and Arlon PCBs, we’ve got the RF components in stock to keep your project moving without delays. With our ability to source a variety of materials on hand, we’re ready to tackle whatever your project demands.
FAQ
What is Teflon PCB and why is it used in circuit boards?
Teflon PCB is a type of printed circuit board that uses PTFE (Polytetrafluoroethylene) as its laminate material. It’s primarily used in high-frequency applications where low signal loss, high dielectric stability, and excellent thermal resistance are needed. It’s ideal for RF (radio frequency), microwave, and aerospace circuits, ensuring reliable performance even in harsh conditions.
What are the benefits of using Teflon PCBs in high-frequency applications?
Teflon PCBs offer low dielectric loss and low dissipation factor, making them highly effective for high-frequency signal transmission. They also exhibit superior thermal stability and chemical resistance, ensuring long-lasting performance in demanding environments, such as telecommunications and aerospace systems.
Can any PCB manufacturer produce Teflon PCBs?
Not all PCB manufacturers have the specialized equipment and expertise required to handle Teflon materials. Teflon requires specific lamination, drilling, and etching processes to ensure the board performs at its best. When looking for a Teflon PCB supplier, ensure they have experience in working with high-frequency circuit boards and possess the necessary capabilities.
What industries use Teflon PCBs?
Teflon PCBs are widely used in industries that demand high-performance, high-frequency electronics. These industries include aerospace, defense, telecommunications, medical imaging, and 5G communications. Teflon’s low signal loss and stable properties make it a top choice for these applications.
Is Teflon PCB suitable for prototype manufacturing?
Yes, Teflon PCBs can be used for prototypes. Many PCB manufacturers offer rapid prototyping services for Teflon-based designs. It’s important to work with a manufacturer experienced in handling Teflon materials to ensure quick turnaround times without compromising on quality.
What is the cost of Teflon PCBs compared to other materials?
Teflon PCBs are generally more expensive than standard FR4 boards or even some other high-frequency materials like Rogers PCBs. The cost is influenced by the complexity of the design, the number of layers, and the specific processes required to handle the material. However, the price is justified for high-performance applications that demand reliable signal integrity and long-term durability.
Can Teflon PCBs be used in high-temperature environments?
Yes, Teflon PCBs are well-suited for high-temperature environments. Teflon’s high thermal resistance allows it to function in extreme temperature conditions, making it ideal for use in industries like aerospace and automotive, where components are exposed to high heat levels.