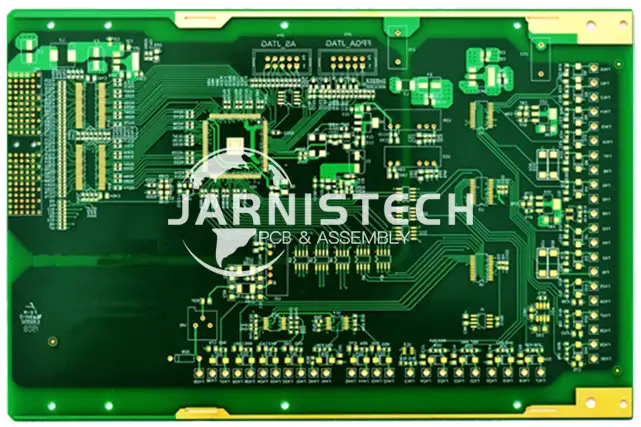
In the electronics manufacturing industry, TUC PCB materials have rapidly gained recognition for their exceptional performance and eco-friendly characteristics. As technology evolves, circuit board designers and procurement teams must rely on these materials to meet the increasing market demands. This article will explore various TUC PCB material series, their high-speed, low-loss properties, thermal stability, and environmental features, providing readers with insights on how to choose the right TUC PCB materials for different applications.
Key TUC PCB Material Series for Performance and Reliability
1. TU-872 TUC PCB Series for High-Speed, Low-Loss Applications
The TU-872 series stands out as an exceptional choice for high-performance circuit boards that prioritize both speed and minimal signal loss. Engineered specifically for high-frequency applications, these materials maintain optimal signal integrity, ensuring data is transmitted accurately and efficiently. They are particularly well-suited for cutting-edge technologies such as 5G communications, where stringent specifications are non-negotiable.
For instance, when designing circuit boards for 5G base stations, engineers rely on the TU-872 series to deliver robust performance even in demanding conditions. The low dielectric loss of this series enhances data throughput, which can make a noticeable difference in high-speed communication systems.
Key Features of TU-872 Series:
Feature | Description |
Dielectric Constant | Low, ensuring reduced signal loss |
Thermal Stability | Maintains performance under varying temps |
Application | Ideal for telecommunications and RF devices |
2. TU-768 TUC PCB for High-Density Interconnects
When it comes to high-density interconnect (HDI) designs, the TU-768 series rises to the challenge. These materials boast superior signal transmission capabilities and a low dielectric constant, making them an ideal fit for multilayer PCB designs where space is at a premium. Whether for smartphones, tablets, or compact gadgets, the TU-768 series delivers outstanding performance in scenarios where every millimeter counts.
Consider the development of a new smartphone model that requires intricate routing and multiple components packed into a small footprint. The TU-768 series helps engineers navigate these tight spaces by allowing for closely spaced vias and traces without compromising on performance.
Advantages of TU-768 Series:
Feature | Description |
Signal Transmission | Excellent performance in dense layouts |
Dielectric Constant | Low, enhancing speed |
Ideal Use | Multilayer designs in consumer electronics |
3. TU-900 and TU-863P TUC PCB for Enhanced Thermal Reliability
The TU-900 and TU-863P materials are designed for applications that face high-temperature challenges. With advanced thermal stability, they excel in environments where heat control is a top priority—think power management systems and automotive electronics. These laminates stay solid under high temperatures, making them a reliable pick for projects where durability and resilience to heat are front and center. Perfect for tough conditions, these materials offer consistent performance, even when the heat gets intense.
In electric vehicle systems, where components have to stay steady under heavy heat, materials like TU-900 and TU-863P offer just what manufacturers are after. These laminates not only handle high temperatures but also add to the durability of the PCB, supporting long-term performance. This stability contributes directly to system reliability—an absolute must for safety in automotive tech. When it comes to EV applications, these materials keep things steady, extending the lifespan of critical components while keeping everything humming along smoothly.
Highlights of TU-900 and TU-863P:
Feature | Description |
Thermal Stability | High Tg for better heat resistance |
Application | Power management and automotive electronics |
Durability | Long-lasting performance under stress |
TU-872 Series: Optimized TUC PCB for High-Speed Applications
1. Signal Integrity of TU-872 TUC PCB in High-Speed Circuits
The TU-872 series shines when it comes to maintaining signal integrity in high-speed circuits. Engineers can leverage smart layout and routing designs to ensure that signals stay crystal clear, even when the data is zipping along at lightning speeds. This attention to detail can drastically reduce errors and keep your devices performing at their peak.
2. High-Frequency Stability in TU-872 TUC PCB Designs
For high-frequency tasks, TU-872 materials are built to handle the job, ensuring low signal loss for smooth, efficient data flow. This makes it a top pick for applications in wireless communications, where clear transmission is everything. Whether it’s for Wi-Fi, IoT devices, or similar tech, TU-872 brings the strength needed to keep data strong and steady. With TU-872, you get materials that help maintain the integrity of every bit, even in challenging high-frequency environments—giving your design the backbone it needs.
3. Designing with TU-872 TUC PCB for Data Integrity
The TU-872 series is a strong choice for high-speed, high-frequency designs where clear data transmission is a must. By managing trace lengths, it ensures reliable signal flow and keeps data quality intact. This series strikes a balance between performance and efficiency, helping designers build products that don’t just perform well—they stand out. With TU-872, you’re getting a foundation that backs data integrity in even the most demanding tech landscapes. Give your project the edge it deserves with materials that know how to handle high-speed demands.
Feature | Benefit | Key Considerations |
Signal Integrity | Reduces errors and ensures clear transmission | Optimize routing to minimize interference |
High-Frequency Stability | Maintains performance in critical applications | Test under actual operating conditions |
Data Integrity | Enhances reliability in data transmission | Keep trace lengths short to optimize performance |
Ready to elevate your designs? The TU-872 series is not just another option; it’s the ticket to pushing your high-speed applications to new heights. Don’t miss out on the chance to incorporate this technology into your next project!
TU-768 Series: TUC PCB for Multilayer and High-Density Applications
1. Multilayer Stack-Ups Using TU-768 TUC PCB Materials
For complex multilayer PCB designs, the TU-768 series offers robust support, allowing for intricate layer stacking while optimizing space. Think of them as the Swiss Army knife of PCBs—versatile and ready for action! By using TU-768, engineers can stack layers smartly, creating intricate circuits without breaking a sweat. A well-planned stack-up can result in reduced overall size and improved functionality, making it a go-to choice for today’s compact electronic devices.
Design Aspect | Benefits |
Layer Count | Supports high layer counts for dense designs. |
Space Optimization | Reduces footprint while enhancing functionality. |
Thermal Management | Provides effective heat dissipation in complex layouts. |
2. High-Density PCB Solutions with TU-768 TUC PCB
In high-density circuit designs, TU-768 is ready to handle complex layouts with tighter trace routing and smaller vias while delivering solid electrical reliability. This makes it a natural choice for high-tech gear like smartphones and IoT devices. Its sturdy construction means it stands up well under challenging conditions, ensuring consistent device performance over time. By incorporating TU-768, designers can achieve greater functionality in less space, keeping devices compact yet powerful—a perfect match for today’s tech demands.
Features of TU-768 | Benefits |
Tighter trace routing | More components in a smaller space |
Smaller vias | Enhanced connectivity and layout |
Solid electrical performance | Reliable signal integrity |
Durable construction | Long-lasting device performance |
3. Signal Integrity in High-Performance TU-768 TUC PCB
If you’re looking to keep signal clarity high, TU-768 has what it takes. Built for dependable signal integrity, this material helps reduce trace lengths and control signal paths, allowing data to stay steady even at fast speeds. Engineers using TU-768 can design with confidence, knowing that interference is minimized, keeping everything from high-speed communications to precision instruments running smooth and steady. This laminate keeps it clear, no sweat—perfect for any project where clean data flow is a must.
Feature | Benefit |
Signal Integrity Focus | Reliable data flow at high speeds |
Optimized Trace Lengths | Reduced interference, clear signals |
Controlled Signal Path Design | Enhanced precision in performance |
TUC PCB Laminates: A Comprehensive Overview
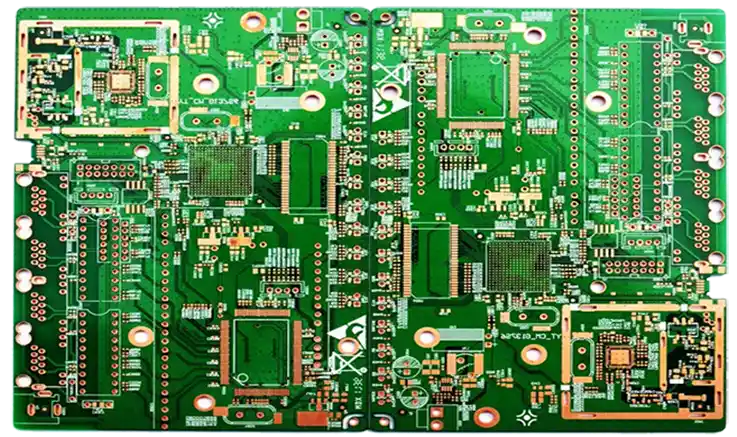
When it comes to picking the right PCB laminate, TUC materials bring top-notch performance across a spectrum of electronics needs. Each classification of TUC laminates offers distinct benefits tailored for specific applications, from low-loss laminates ideal for high-frequency tasks to high-reliability options built for thermal endurance. Whether you’re working with power systems, communications, or IoT designs, there’s a TUC material geared to fit the job. Let’s break down these choices and see what each category brings to the table for today’s advanced electronics projects.
1. Classification of TUC PCB Laminate Materials
Very Low Loss Laminate: TU-901-
●Perfect for high-frequency applications where minimizing signal loss is key.
Mid Loss Materials: TU-742 HF-
●Balances performance and cost, suitable for moderate frequency circuits.
Extreme Low Loss Laminate: ThunderClad 4R-
●Designed for applications that demand the absolute lowest signal loss.
Low Loss Laminates: TU-787 LK, TU-872 LK, TU-872 SLK-
●Ideal for general applications needing reliable performance.
Super Low Loss Laminate: ThunderClad 3+, ThunderClad 4N, ThunderClad 3, ThunderClad 2 Sp-
●Exceptional choice for advanced communication systems and high-speed designs.
High Thermal Reliability Laminates: TU-865, TU-862T, TU-862 HF, TU-768, TU-662F, TU-662-
Engineered for high-temperature environments, ensuring reliability over time.
Standard Loss Materials: TU-768F, TU-768, TU-722, TU-668, TU-662F, TU-662-
●Commonly used across standard applications, providing balanced performance.
Non-flow/Mid-flow Prepregs: TU-84P NF, TU-84P MF, TU-863P MF-
●Specialized for layering and assembly processes, offering design flexibility.
TUC PCB Laminates Overview Table
Classification | Material | Applications | Key Features |
Very Low Loss | TU-901 | High-frequency circuits | Minimal signal loss |
Mid Loss | TU-742 HF | Moderate frequency circuits | Good balance of performance and cost |
Extreme Low Loss | ThunderClad 4R | Critical applications | Ultra-low signal loss |
Low Loss | TU-787 LK, TU-872 LK, TU-872 SLK | General applications | Low loss characteristics |
Super Low Loss | ThunderClad 3+, 4N, 3, 2 Sp | Advanced communication systems | Superior performance |
High Thermal Reliability | TU-865, TU-862T, TU-862 HF, TU-768, TU-662F, TU-662 | High thermal stress environments | Long-term stability |
Standard Loss | TU-768F, TU-768, TU-722, TU-668, TU-662F, TU-662 | Various standard applications | Balanced performance |
Non-flow/Mid-flow Prepregs | TU-84P NF, TU-84P MF, TU-863P MF | Layering and assembly processes | Design flexibility |
Ready to kick your projects into high gear? Don’t hesitate—reach out to JarnisTech today! We have a many series TUC PCB laminates to meet your needs, no matter the challenge. Let’s work together to make your next project a success!
How TUC PCB Laminate Differs from Other Laminates?
TUC PCB laminates provide unique benefits compared to standard laminates, making them an excellent choice for various applications. Below is a comparison table highlighting key differences:
Feature | TUC Laminates | Standard Laminates |
Electrical Properties | Excellent performance for high-speed | Variable, often lower than TUC |
Thermal Expansion | Improved Z-axis thermal expansion | Less stable under temperature changes |
Halogen Content | Halogen-free | Often contain halogen |
Dielectric Constant (Dk) | ≤ 4 | Varies widely, typically higher |
Dissipation Factor (Df) | ≤ 0.005 | Typically higher than TUC |
Compatibility | Works with modified FR-4 processes | May not support lead-free processes |
Water Resistance | High | Varies |
Anti-CAF Capability | Excellent | Limited in many cases |
Temperature Stability | Stable across temperature variations | Less consistent performance |
TUC PCB laminates are crafted to deliver dependable electrical performance, support eco-friendly practices, and align smoothly with advanced manufacturing setups. These laminates bring an edge to modern PCB designs, balancing durability and precision in demanding environments. Ready to level up your build quality? With TUC, you’re looking at materials that not only meet today’s standards but also make the whole design process feel a bit smoother. Perfect for projects aiming for efficiency and a long-lasting finish!
Alternative PCB Materials to TUC PCB Laminates Materials
No TUC laminates? No problem! There are plenty of high-performance PCB materials out there that can keep your projects running smoothly and meet rigorous specs. Let’s break down a few top alternatives, each with its own unique strengths:
Material | Type | Key Features |
SH260 | Rigid Polyester | Durable, reliable, suitable for various applications. |
N4000-13-13-SI | High-Speed Epoxy | Multifunctional laminate; excellent for high-speed circuits. |
FR408HR | Performance Laminate | High-temperature resistance; ideal for demanding environments. |
IT-170GRA2 | Rigid PCB | High Tg for stability in fluctuating conditions. |
S7038 | HDR Material | Mid-loss performance; balanced solution for various applications. |
S1600 | Flexible PCB | Conventional F-4; provides flexibility and reliability. |
S1151G | FR-4 Rigid PCB | Widely used, meets standard industry requirements. |
S1170G | Green Rigid PCB | Environmentally friendly, suitable for sustainable projects. |
S1150G | Halogen-free FR-4 | Lead-free compatible; safe for diverse applications. |
S1141 | Traditional FR-4 | Reliable, widely accepted material in PCB fabrication. |
S1000-2 | Lead-Free FR-4 | Eco-conscious design; FR-4.0 and FR-15.0 compatible. |
S1000H | Lead-Free FR-4 | Compatible with FR-4.0 and FR-5.0; maintains performance standards. |
S1000-2M | Lead-Free FR-4 | Compliance with environmental standards; suitable for a range of projects. |
When searching for alternatives to TUC laminates, consider the application needs, performance specifications, and environmental impact. Each of these materials has unique characteristics that can cater to specific requirements in your projects. Don’t hesitate to reach out JarnisTech, we will provide for guidance on the best material selection for your PCB needs!
High-Speed, Low-Loss Capabilities in TUC PCBs for Digital and RF Applications
1. Ensuring Signal Integrity in High-Speed TUC PCBs
When it comes to building high-speed TUC PCBs, ensuring signal integrity is non-negotiable. Designers need to keep their focus sharp, considering routing layouts and selecting suitable materials to guarantee clear signal transmission. This typically involves using low-dielectric-loss materials, which help minimize noise that can disrupt the flow of information. Every little detail matters in the design process; making informed choices can significantly enhance performance and reliability. Stay on target, and you’ll craft outstanding PCBs that meet demanding standards!
For example, think about the rush of data flying through a 5G network—having materials like those from the TU-872 series can make all the difference in keeping things smooth and fast. If signal integrity takes a hit, it’s like driving with a flat tire; you’re not going anywhere fast.
Key Considerations for Signal Integrity:
Consideration | Importance |
Routing Layout | Directly impacts signal path and delay |
Material Selection | Low-loss materials reduce signal degradation |
Vias and Traces | Optimized dimensions help maintain signal quality |
2. Low Dielectric Loss Benefits in TUC PCB RF Circuits
Low dielectric loss? That’s a big win in the RF game! TUC PCBs featuring this property allow manufacturers to run at high frequencies without overheating. This leads to improved performance across various applications, particularly in wireless communication and RF tech. By maintaining optimal signal integrity, TUC materials ensure devices operate reliably and effectively, setting the groundwork for high-performance electronic systems. It’s all about getting the best out of your technology while keeping the data flowing!
Picture this: If you’re designing a top-notch RF amplifier, choosing low-loss TUC materials is a smart move. This selection allows you to boost output while keeping energy consumption in check, creating a solid balance between performance and thermal management. With these materials, you can optimize your amplifier’s efficiency, ensuring it operates effectively without getting too hot under pressure. It’s all about maximizing your setup and delivering the power you need without the hassle of excess heat!
Benefits of Low Dielectric Loss:
Benefit | Explanation |
Enhanced Efficiency | Reduces energy waste and heat generation |
Higher Frequency Operation | Keeps the party going across various RF bands |
Improved Signal Quality | Lower loss leads to clearer signal transmission |
3. Achieving High-Frequency Stability with TUC PCB Laminates
TUC PCB laminates are top performers in high-frequency applications. Built to withstand the heat and demands of complex designs, these materials provide reliable performance even when the pressure is on. With a knack for handling tough conditions, TUC laminates ensure that your circuits maintain their integrity, helping you achieve that perfect balance of efficiency and durability. When you need consistent results, these laminates deliver, making them a go-to choice for engineers tackling challenging projects in the tech world.
This stability shines in situations where dependability is a must, particularly in the busy field of telecommunications. Imagine launching a new router engineered for lightning-fast internet; with TUC laminates, you can count on it to keep delivering solid performance, rain or shine, making users happy as can be. When reliability is on the line, TUC laminates are ready to deliver, ensuring your products meet the demands and keep everything running like a well-oiled machine.
Features of TUC PCB Laminates:
Feature | Benefit |
High-Frequency Tolerance | Handles fast signal transitions like a champ |
Environmental Resilience | Performs well in varying temperature and humidity |
Consistent Performance | Keeps functionality high even under heavy loads |
Thermal Stability and High Tg for Extreme TUC PCB Applications
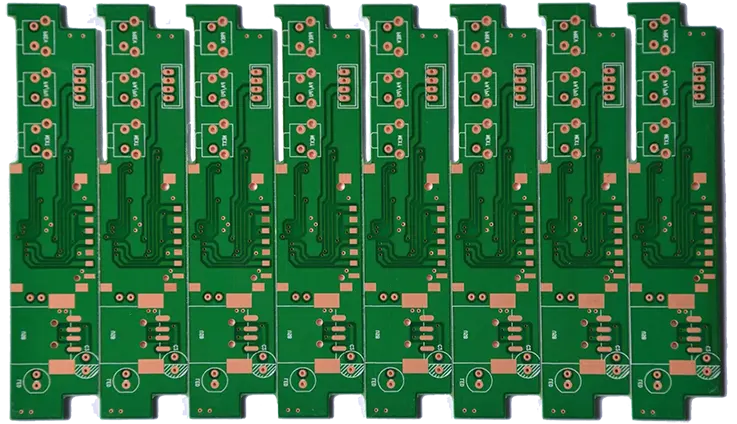
1. High Tg TUC PCB Laminates for Heat Resistance
In high-performance applications, the choice of materials with an elevated glass transition temperature (Tg) is fundamental to ensuring both stability and endurance in thermally demanding environments. TUC PCB laminates such as TU-863P and TU-900 are designed to provide excellent thermal stability with Tg values of 170°C and 185°C respectively. These materials minimize risks associated with thermal expansion and contraction, which can lead to mechanical stress and reduced performance in the PCB structure.
In automotive electronics, where temperatures can swing wildly, TU-863P offers stable glass transition temperature (Tg), which helps maintain structural strength and minimizes the chances of delamination, ultimately boosting the lifespan of devices. On the other hand, TU-900’s elevated Tg properties make it a solid pick for industrial control applications, where keeping the Coefficient of Thermal Expansion (CTE) low at high temperatures is key to ensuring reliable signal transmission across multiple layers.These materials tackle thermal challenges head-on, keeping your devices performing at their best!
Material Series | Tg (°C) | Recommended Applications |
TU-863P | 170°C | Automotive, Power Electronics |
TU-900 | 185°C | Industrial Controls, Aerospace |
2. Thermal Management in High-Power TUC PCB Designs
High-power PCB designs require sophisticated thermal management strategies to prevent overheating, which can lead to reliability issues and shorten device lifespans. Thermal dissipation can be optimized through careful design choices, such as the integration of thermal vias and high thermal conductivity materials. By combining TU-768’s low dielectric loss with heat sinks and copper-filled thermal vias, engineers can effectively manage the heat generated by high-power circuits.
For example, in power amplifiers where thermal buildup is a critical concern, implementing TU-768 paired with strategic cooling elements can enhance the performance and longevity of the PCB. This is especially relevant in space-constrained designs for portable electronics, where thermal management directly impacts device durability.
Thermal Design Strategies to Enhance TUC PCB Performance:
●Thermal Vias: Copper-filled vias improve heat transfer between layers.
●High Conductivity Materials: Employing substrates with high thermal conductivity, such as copper or silver, promotes even heat spread across the board.
●Balanced Layouts: Uniform component placement to reduce localized heat spots.
3. Reliable TUC PCB Performance in High-Temperature Conditions
For devices operating under extreme temperatures, opting for TUC PCB materials engineered for high-temperature resilience ensures dependable performance. The TU-900 series, for instance, is designed to endure harsh environments without sacrificing electrical performance or mechanical integrity. This advantage is particularly useful in sectors like automotive electronics and industrial machinery, where the ability to withstand heat directly impacts device stability and functionality. So, when the heat is on, you can trust these materials to keep your systems running strong!
Using high-temperature TUC PCBs also minimizes potential issues such as warping and delamination under thermal stress. For applications where extended temperature ranges are a requirement, these materials provide a robust foundation that enhances device reliability, ultimately lowering maintenance and replacement costs.
Key Benefits of High Tg TUC PCBs:
●Extended Operational Lifespan: Higher resistance to thermal degradation.
●Enhanced Structural Integrity: Reduced risk of mechanical stress under temperature fluctuations.
●Optimized for High-Temperature Applications: Ideal for automotive, aerospace, and power management systems.
Environmentally Friendly, Halogen-Free, and Lead-Free TUC PCB Materials
1. Benefits of Eco-Friendly TUC PCB Manufacturing
Shifting to eco-friendly TUC PCB production isn’t just a trend—it’s a commitment to sustainability. Manufacturers increasingly choose materials that are low-emission, halogen-free, and lead-free to reduce environmental impact and comply with regulatory standards. Beyond meeting industry norms, these choices make a difference in minimizing the carbon footprint. In fact, adopting these green practices can cut hazardous waste and reduce volatile organic compound (VOC) emissions by up to 60%.
Think of it as hitting two birds with one stone: manufacturers can protect the environment and future-proof their products against stricter regulations. Below is a comparison table showing environmental and cost benefits for eco-friendly and traditional materials:
Feature | Eco-Friendly TUC Materials | Traditional PCB Materials |
VOC Emissions | 40-60% lower | Higher |
Regulatory Compliance (RoHS) | Fully compliant | Partial compliance |
Cost-Effectiveness | High long-term savings | Lower initial costs |
2. Lead-Free TUC PCB Materials for Sustainable Production
Going lead-free in PCB manufacturing isn’t a walk in the park, but it’s a meaningful choice with solid payback. Lead-free TUC materials meet environmental standards like RoHS, making them attractive to a global market looking for safer, greener options. What’s more, these materials perform consistently in high-power applications without compromising quality—a huge plus for industries like automotive and medical electronics where safety is a non-negotiable.
The payoff? Products that resonate with eco-conscious consumers and align with global sustainability goals. More and more OEMs are jumping on board, seeing it as a long-term investment that appeals to modern consumers who are looking for safer electronics.
3. Choosing Halogen-Free TUC PCB for Green Electronics
Choosing halogen-free TUC materials is a smart choice, especially if there’s any risk of high heat or fire. Halogen-free options release fewer toxic gases and produce less smoke, which not only enhances safety but also makes a greener footprint. These materials are popular among designers of consumer electronics and automotive components, where durability meets environmental responsibility.
The table below illustrates key advantages of halogen-free versus halogenated materials in TUC PCBs, specifically in high-risk and high-temperature applications:
Feature | Halogen-Free TUC Materials | Halogenated Materials |
Smoke Emission | Minimal | High |
Suitability for High Temp | Excellent | Moderate |
Environmental Impact | Lower emissions | Higher impact |
TUC PCB Design Considerations for High-Density Interconnects
1. Designing High-Density PCBs with TUC PCB Materials
Creating compact, high-density interconnect (HDI) PCBs calls for precision and a savvy material choice, and TUC’s PCB materials fit the bill. Designed to accommodate tightly packed layers without compromising signal integrity, they’re ideal for cutting-edge devices like smartphones and high-speed computing components. By choosing TUC materials, engineers can create tighter layouts that not only enhance performance but also boost the durability of the final product, keeping things running at peak efficiency!
Consider this: An HDI PCB layout utilizing TUC materials enables designers to minimize board size while keeping signal integrity intact. This capability is particularly advantageous in consumer electronics, where space is at a premium. Below is a quick comparison table showcasing the compatibility of TUC materials with HDI applications, highlighting their performance benefits and adaptability for compact designs. By leveraging these materials, engineers can create efficient and effective solutions that fit the demands of modern technology without compromising quality.
Feature | TUC PCB Materials | Standard PCB Materials |
Signal Integrity | High | Moderate |
Layer Compatibility | Excellent | Limited |
Density Support | Ideal for HDI | Moderate |
2. Optimizing Signal Integrity in TUC PCB Layouts
When designing a layout that will pass data at high speeds, maintaining signal integrity is everything. TUC PCB materials lend themselves well to maintaining this clarity. Proper routing, together with these materials, ensures that signals travel with minimal interference and loss. This keeps the device’s operations stable, even as data rates go up.
To paint a picture, imagine laying out a multi-layer PCB for a 5G application: using TUC materials, you can space traces tightly while preserving clear signals between layers. A few design tips for optimal signal integrity include:
●Avoid sharp corners in traces: Helps prevent reflection and maintain a stable signal.
●Use uniform trace widths: Assures consistency across the entire layout.
●Consider impedance matching: TUC’s low dielectric materials make this a smoother process.
3. TUC PCB Solutions for High-Frequency Applications
High-frequency applications call for materials that can handle rapid signal transitions without a hitch, and TUC’s PCB laminates rise to the occasion. These materials keep signal loss in check, essential for applications like RF and microwave circuits where every little interference can compromise performance.
For instance, when designing a PCB for radar systems or high-speed data channels, TUC’s high-frequency laminates provide the needed stability. These materials exhibit low dielectric loss, which reduces heat and energy waste. As a result, devices run more efficiently and with a longer lifespan. Below is a table comparing the attributes of TUC high-frequency materials to typical materials used in high-speed PCB applications:
Attribute | TUC High-Frequency Materials | Standard PCB Materials |
Dielectric Loss | Low | Higher |
Thermal Stability | Excellent | Moderate |
High-Frequency Suitability | Ideal for RF/microwave | Limited |
Manufacturing Advantages of TUC PCB Laminates in High-Performance Applications
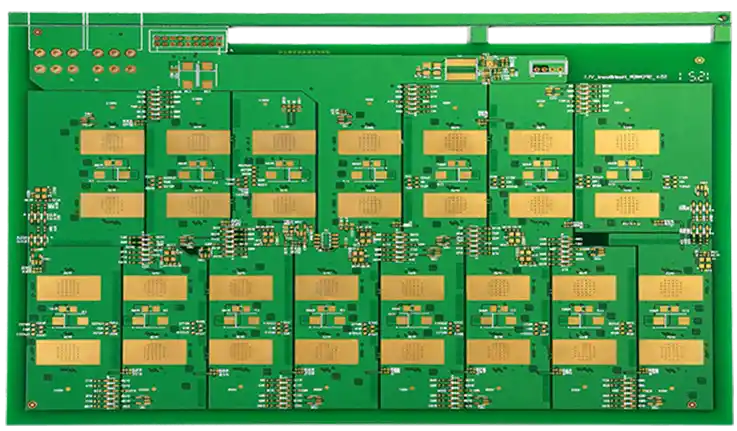
1. Multilayer and HDI Capabilities with TUC PCB Materials
Designing for high-density interconnects (HDI) and multilayer configurations is all about packing robust functionality into compact spaces, especially as device complexity grows. TUC PCB materials stand out in these applications, allowing for intricate layer designs and high-density connections without sacrificing signal performance. This capability meets the demands of modern electronics—think 5G devices, high-speed computing, and IoT devices—where compact yet high-functioning components are essential. The controlled impedance and thermal management properties of TUC’s HDI materials also mean fewer design trade-offs, giving engineers a broader canvas for innovation.
Feature | TUC PCB Multilayer Materials | Standard PCB Materials |
High-Frequency Stability | Excellent in HDI setups | Limited in dense designs |
Thermal Durability | Maintains performance | Less resilient under stress |
Signal Clarity | Optimized for dense designs | Variable |
This table highlights how TUC PCB materials bring stability and clarity, even in tightly packed, multi-layered designs. For engineers, it’s like having the freedom to create without constant compromises on performance.
2. Low-Flow Prepregs in TUC PCB Manufacturing
For those aiming for consistent manufacturing processes, low-flow prepregs from TUC offer stability and simplify production. In high-density PCBs, these low-flow materials guarantee solid layer bonding, even under high heat and pressure. This advantage is particularly significant in power electronics and automotive applications, where delamination can lead to serious failures. The outcome? PCBs that endure harsh conditions while preserving both electrical and mechanical reliability. With TUC materials, you can keep your projects running smoothly, no matter the challenge.
Here’s a look at how TUC’s low-flow prepregs outperform traditional materials:
Prepreg Type | Interlayer Bonding | Thermal Resistance | Application Suitability |
TUC Low-Flow Prepreg | High | Excellent | High-density, high-temperature |
Standard Prepreg | Moderate | Limited | General use |
Using TUC’s low-flow prepregs, manufacturers can confidently tackle high-density projects with fewer production risks, ensuring that their circuits can handle the heat—literally!
3. Process Control with High Tg TUC PCB Laminates
High Tg laminates from TUC offer a critical advantage in ensuring stable production. During high-temperature processes, materials with high glass transition temperatures resist structural warping, maintaining dimensional stability. This quality is essential for applications like aerospace and telecommunications where consistent, reliable performance under variable conditions is non-negotiable. High Tg TUC PCB laminates improve product longevity and reduce the risk of failure, making them a preferred choice for complex, high-power applications.
Lamination Type | Glass Transition (Tg) | Warp Resistance | Use Case |
High Tg TUC Laminate | 170°C – 200°C | Excellent | High-power, critical use |
Standard Laminate | 130°C – 150°C | Moderate | General applications |
These materials give manufacturers the stability they need, ensuring that every stage, from production to field deployment, remains as hassle-free as possible.
Cost-Effectiveness and Longevity of TUC PCB Materials in Production
1. Balancing Cost and Performance in TUC PCB Selection
Selecting the right TUC PCB materials requires finding that sweet spot between cost savings and top-notch performance. Engineers choosing these materials can minimize production expenses while ensuring the product maintains a competitive edge. High-grade TUC options allow for functional optimization without sacrificing quality, making them a practical choice in consumer electronics, automotive applications, and other industries where balancing cost and performance directly affects profitability.
Material Feature | Standard PCB | TUC PCB Materials |
Cost Efficiency | Moderate savings | High, with better yield |
Performance Consistency | Varied | High across applications |
Application Flexibility | Limited | Broad, for HDI and more |
2. Long-Term Reliability of TUC PCB Laminates
When it comes to durability, TUC PCB laminates bring peace of mind. Their advanced material properties reduce wear and tear, keeping PCBs intact even under challenging conditions. This makes them popular in applications where longevity is a must, such as industrial automation and power electronics. By choosing TUC laminates, manufacturers ensure that end products can hold up over time, reducing the need for frequent repairs or replacements.
3. Reducing Total Costs with Durable TUC PCB Solutions
Durability directly impacts overall costs, especially for large-scale production runs. TUC PCB materials, known for their resilience, contribute to reducing long-term expenses associated with maintenance and replacements. With fewer defects and longer product lifespans, these materials lower overall production costs, positively impacting bottom-line profitability. Durable TUC solutions are more than a smart choice—they’re an investment in a product’s future that pays off for manufacturers and consumers alike.
Feature | TUC PCB Advantage | Benefits for Manufacturers |
Cost Efficiency | Optimized for diverse applications | Lowered production and lifecycle expenses |
Reliability in Harsh Conditions | Consistent thermal and mechanical stability | Reduces downtime and maintenance requirements |
Durability | High resistance to environmental stresses | Increases product longevity and operational uptime |
Get on board with TUC PCB materials—where durability and efficiency meet head-on to drive your project’s success!
Material Selection Guide for TUC PCB Procurement Teams
1. Key Factors for Selecting TUC PCB Materials
For procurement teams, selecting the right TUC PCB materials means assessing a combination of performance, environmental impact, and cost. These considerations shape the quality, reliability, and market acceptance of the final product. High-frequency applications may need specific laminates, while thermal requirements might call for materials with a high Tg rating. A comprehensive comparison chart between these material properties can streamline decision-making, ensuring the chosen PCB aligns with project needs.
2. Ensuring Electrical Performance in TUC PCB Choices
Electrical stability under varying loads is a priority in TUC PCB material choices. Procurement teams should aim for materials that maintain consistent signal integrity, especially for sensitive circuits. For example, multi-layer boards benefit from TUC materials that minimize dielectric loss, enhancing signal clarity across layers. By aligning materials with the intended electrical characteristics, teams can ensure durability and minimize potential failures, even in high-stress environments.
3. Prioritizing Environmental Standards in TUC PCB Procurement
As eco-conscious production becomes a market demand, TUC PCB materials offer sustainable choices that comply with international regulations. Teams looking to balance performance with sustainability can choose lead-free and halogen-free options that lower environmental impact. Selecting these materials not only meets environmental compliance but also resonates with consumers focused on greener products. A side-by-side breakdown of materials with eco-friendly certifications could help guide teams toward optimal choices.
Factor | Material Impact | Considerations |
Performance Requirements | Stable signal, low dielectric loss | High-frequency applications |
Environmental Compliance | Lead-free, halogen-free options | Meets eco-friendly regulations |
Cost Management | Cost-effective materials | Balances budget with required specs |
Why Choose JarnisTech for TUC PCB Manufacturing?
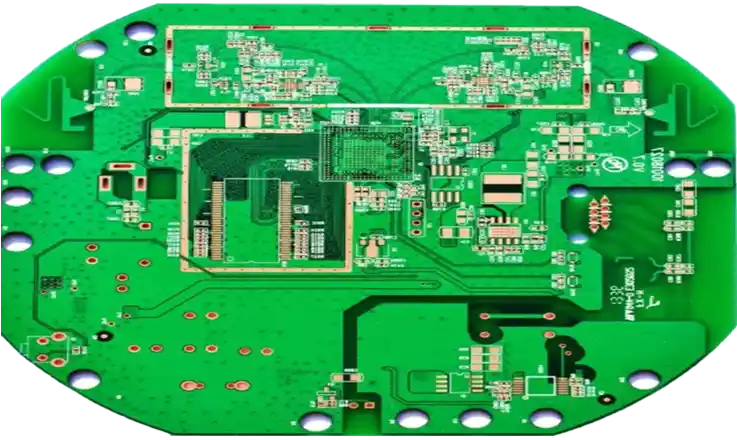
JarnisTech: Your Go-To Source for TUC Laminates in China
When it comes to TUC PCB circuit boards, JarnisTech truly delivers! We take pride in being a leading manufacturer specializing in TUC PCB Boards customized to meet your specific project needs. We manufacturing TUC PCB circuit boards excel in providing environmental protection and seamlessly integrate with lead-free and FR-4 processes. With us, you’re not just getting products; you’re partnering with experts who understand the importance of quality and reliability in every layer. Let’s work together to bring your projects to life!
What We Offer:
●TUC TU-883
●TUC TU-993
●TUC TU-768
●TUC TU-662
●TUC TU-872
We offer a comprehensive range of TUC PCB fabrication services tailored for diverse applications. Our products are made from top-notch raw materials and utilize state-of-the-art technology to ensure quality and reliability. With a focus on excellence, we’re committed to providing solutions that meet your unique needs, no matter the complexity of your project. Partner with us to experience the difference—where quality meets innovation, and your vision becomes a reality!
At JarnisTech, we’re not just about selling PCB manufacturing and assembly services; we’re about building relationships. Our team is dedicated to helping you find the right solution, whether you’re stocking up for a big project or just need a few pieces to complete your work. When you choose us, you’re not just a customer—you’re part of the family!
Check Out Our Comparison Table for TUC Laminates
TUC Laminate | Material Type | Application Suitability | Special Features |
TU-883 | Rigid | General Electronics | High thermal stability |
TU-993 | Rigid | High-Frequency Applications | Excellent dielectric properties |
TU-768 | Multilayer | Dense, complex circuits | Low water absorption |
TU-662 | Rigid | Automotive, Aerospace | High mechanical strength |
TU-872 | Rigid | Telecommunications | Outstanding signal integrity |
Why Settle for Less? Don’t miss out on the opportunity to get the best TUC laminates on the market. Reach out to us today and let’s get your project rolling!
FAQ
Are TUC PCBs environmentally friendly?
Many TUC PCB materials are halogen-free and lead-free, complying with modern environmental standards, making them a suitable choice for sustainable manufacturing practices.
What are the benefits of using high-speed TUC PCBs?
High-speed TUC PCBs excel at facilitating elevated data transfer rates while preserving signal integrity. This makes them a top choice for cutting-edge applications in telecommunications and advanced computing systems.
How do TUC PCBs improve signal integrity?
TUC PCBs enhance signal integrity by utilizing low-loss materials and optimized routing designs, which reduce signal degradation and electromagnetic interference.
What makes TUC PCBs suitable for high-density interconnects?
TUC PCBs are designed to support high-density interconnects due to their compact layout and excellent electrical performance, catering to the needs of modern electronic devices.
Can TUC PCBs withstand high temperatures?
Yes, high Tg TUC PCB materials are engineered to withstand high temperatures, making them ideal for applications that experience thermal stress.
What industries benefit from TUC PCB materials?
TUC PCB materials find applications in a variety of industries, including consumer electronics, automotive, industrial equipment, telecommunications, and medical devices.
Our special materials
PCB Fabrication
TUC PCB Laminate & Materials Series