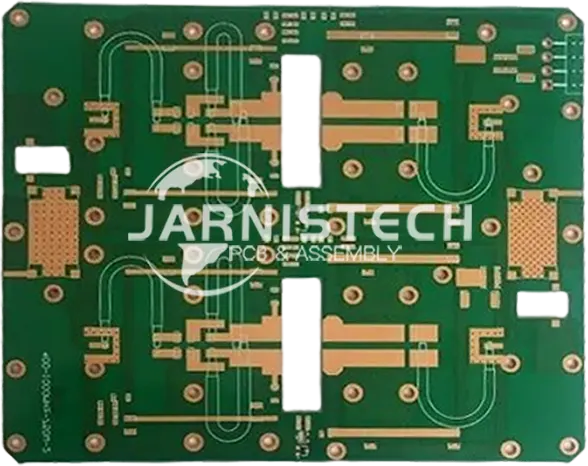
When it comes to PCB manufacturing, Taconic PCBs stand out for their exceptional high-frequency performance, impressive thermal stability, and low dielectric loss. Whether you’re working on RF applications, microwave communication systems, or aerospace technologies, Taconic materials deliver the precision and reliability you need.
At JarnisTech, we specialize in manufacturing Taconic PCBs and providing comprehensive assembly services. With over two decades of experience under our belt, we’re well-equipped to handle a variety of Taconic PCB needs.
We maintain a diverse inventory of Taconic laminates, all available without a minimum order requirement. This flexibility allows you to save both time and money. As an ISO-certified PCB manufacturer, we prioritize quality above all else, ensuring that our products align with your specifications and expectations.
Ready to take your project to the next level? Reach out to us at [email protected] and let’s get started on your Taconic PCB journey!
The Importance of Taconic PCB in High-Frequency Circuit Design
Designing high-frequency circuits is no easy task. These circuits require materials that can tackle everything from maintaining signal integrity to ensuring thermal stability, and that’s where Taconic PCBs come into play. With their PTFE-based substrates, they provide the high-performance characteristics necessary for RF design—without the usual frustrations tied to signal loss or thermal expansion.
Now, let’s break down why Taconic materials are your best bet when working with high-frequency circuits. First off, these materials bring low dielectric constants, which translates into better signal transmission, especially in RF applications where even small interference can lead to big problems.
Choosing the Right Taconic Material for RF Circuits
When it comes to selecting a Taconic material for your RF circuits, there’s no such thing as a one-size-fits-all solution. Taconic’s diverse range of laminates provides specific properties tailored to the unique demands of various high-frequency designs. For example:
RF-35: This is a fan favorite in the PCB design community because of its low dielectric constant and consistent performance across a wide frequency range. It’s particularly useful for applications like radar systems and high-frequency amplifiers where precision is key.
TLX: If your project involves microwave communications or antenna systems, TLX laminates are the way to go. These materials deliver outstanding dimensional stability, even when faced with fluctuating temperatures. This characteristic is essential for high-frequency circuits that generate significant heat.
Let’s say you’re designing a circuit for a 5G base station. You want to minimize signal loss, which makes RF-35 ideal because of its balance between cost and performance. On the other hand, if your design is more temperature-sensitive, such as for aerospace applications, TLX would give you the edge with its better thermal management.
Here’s a quick comparison to help you choose the right laminate:
Taconic Material | Dielectric Constant | Primary Application |
RF-35 | Low | Radar, Amplifiers |
TLX | Medium | Microwave, Antenna |
TLY-5 | Ultra-low | High-Frequency Filters |
How PTFE-Based Substrates Improve High-Frequency Signal Integrity?
PTFE-based substrates are integral to achieving the signal integrity required for high-frequency circuits. Consider PTFE your circuit’s secret weapon against signal loss. These substrates feature low dielectric constants and low dissipation factors, ensuring that energy loss during operation is minimized.
For example, in microwave communications, any slight loss in signal can degrade overall performance. PTFE helps prevent this by providing a stable environment for the signal to pass through without interference. Additionally, the low moisture absorption of Taconic PCBs makes them perfect for environments with fluctuating humidity, where you don’t want moisture affecting your signal integrity.
In high-end applications, like satellite communications, where any signal loss can disrupt communication, the use of Taconic’s PTFE laminates ensures consistent high-frequency performance. These boards are also incredibly effective in environments where thermal expansion would typically create issues with signal degradation over time.
For instance, if you’re working on a satellite receiver design, PTFE’s ability to maintain low dielectric loss under varying environmental conditions means fewer issues down the line. The lower you keep your loss, the more efficient your circuit will be. It’s kind of like having a sports car that doesn’t burn through fuel just to stay at top speed.
Optimizing PCB Layout for Taconic Materials
When it comes to designing with Taconic PCBs, an optimized layout can make a world of difference in performance. High-frequency circuits operate on a different level compared to standard designs, and as such, you need to pay extra attention to your layout techniques to ensure everything runs smoothly. Let’s dive into some best practices that can help you harness the full potential of Taconic materials.
Best Practices for High-Frequency Layout with Taconic PCBs
To create a layout that maximizes the benefits of Taconic PCBs, you need to adopt a strategic approach. Here are some best practices that should be on your radar:
Keep Traces Short and Direct: The shorter the traces, the less opportunity for interference. This is particularly true for high-frequency applications where even a small detour can lead to increased inductance and resistance.
Utilize Ground Planes Effectively: Ground planes are not just for aesthetics; they serve a practical purpose in high-frequency designs. Using a solid ground plane can help minimize return path inductance, ensuring your signal stays clean. Make sure to connect all ground points to the plane to create a low-impedance path.
Maintain Consistent Trace Widths: To manage impedance effectively, keeping your trace widths consistent across the board is key. This approach helps maintain a uniform characteristic impedance, reducing reflections and enhancing overall signal integrity.
Avoid Sharp Turns: Keep those corners smooth! Sharp turns can create impedance discontinuities. Instead, use gentle curves to maintain the integrity of the signal as it flows through the PCB.
Implement Via Strategically: Vias can be a necessary evil, but they can also introduce inductance if not used wisely. Use them sparingly, especially in critical signal paths. If you must use vias, consider back-to-back configurations to minimize their impact.
Here’s a quick visual guide to illustrate these practices:
Practice | Description |
Short Traces | Minimize the distance to reduce interference. |
Ground Planes | Solid ground planes enhance signal return paths. |
Consistent Trace Widths | Maintains characteristic impedance and reduces reflections. |
Smooth Turns | Prevents impedance discontinuities. |
Strategic Via Placement | Reduces inductance in critical paths. |
Managing Impedance and Signal Integrity in RF PCB Designs
When you’re fully immersed in RF PCB design, handling impedance and signal integrity is where the action happens. A well-designed PCB won’t do you any good if your signals get all muddled up during transmission. Here are some techniques to keep your signals sharp and clean:
Calculate Characteristic Impedance: Before laying down any traces, use the right formulas to determine the required characteristic impedance for your design. This calculation will guide your trace width and spacing, ensuring you’re on the right track from the get-go.
Controlled Impedance Layers: Consider using controlled impedance layers when working with Taconic materials. This approach involves defining the dielectric thickness and substrate parameters to create a predictable environment for your signals.
Use Termination Techniques: Applying termination resistors at the ends of high-speed signal lines can significantly improve signal integrity. This practice reduces reflections that can occur when the signal encounters impedance mismatches.
Simulation Tools: Don’t skimp on using simulation tools to analyze your layout before production. Tools like HFSS or Sonnet can help visualize how signals travel through your design, highlighting potential issues before they become real problems.
Monitor Signal Integrity: After your PCB is manufactured, using an oscilloscope to monitor signal integrity can provide insights into any anomalies. If you notice irregularities, it may be time to revisit your layout and make necessary adjustments.
Here’s a handy reference table for impedance management:
Technique | Description |
Characteristic Impedance | Calculate and design to meet specific requirements. |
Controlled Impedance Layers | Define dielectric thickness and substrate properties for predictability. |
Termination Techniques | Implement resistors to minimize signal reflections. |
Simulation Tools | Utilize software to visualize and correct signal paths. |
Signal Integrity Monitoring | Check signals post-manufacturing to identify issues. |
A Comparative Overview of Taconic vs. Rogers PCB Materials

In the ever-changing world of high-frequency circuit design, Taconic and Rogers PCB materials frequently steal the spotlight. Each of these materials brings its own set of characteristics tailored to meet the demands of specific applications, especially in RF and microwave settings. In this section, we’ll dive into the performance distinctions between these two materials and uncover how to make smart, cost-effective choices without sacrificing quality.
Performance Differences in RF and Microwave Applications
When evaluating Taconic and Rogers materials for RF and microwave applications, it’s crucial to consider several key performance metrics, including dielectric constant, thermal stability, and signal loss characteristics. Here’s a breakdown of how they stack up against each other:
1. Dielectric Properties
Taconic Materials: Known for their low loss tangent, Taconic substrates typically feature dielectric constants ranging from 2.5 to 3.5, making them suitable for high-frequency designs where minimal signal loss is desired. For example, their TLY series is often chosen for its excellent balance of dielectric properties and cost-effectiveness.
Rogers Materials: Rogers substrates, such as RO4000 and RO3000 series, offer a wider range of dielectric constants (from 2.2 to 10.2). This flexibility allows designers to select a material that closely matches their specific impedance requirements, which is particularly beneficial in microwave applications.
2. Thermal Stability
Taconic: Generally exhibits good thermal stability, making it suitable for environments that experience significant temperature fluctuations. The thermal performance of Taconic materials is often highlighted in applications where heat dissipation is a concern.
Rogers: Rogers materials excel in high-temperature applications, maintaining performance even under harsh conditions. This makes them ideal for aerospace and military applications where reliability is non-negotiable.
3. Signal Loss Characteristics
Taconic: With a lower loss tangent, Taconic materials tend to demonstrate reduced signal degradation over distance, making them advantageous for long-range communications.
Rogers: While Rogers materials may exhibit slightly higher loss in some configurations, they compensate with superior performance in high-frequency ranges, especially in applications requiring complex multi-layer designs.
Here’s a quick comparison table to visualize these differences:
Property | Taconic | Rogers |
Dielectric Constant Range | 2.5 to 3.5 | 2.2 to 10.2 |
Thermal Stability | Good | Excellent |
Signal Loss Characteristics | Low Loss Tangent | Varies by series, generally good |
Typical Applications | Cost-sensitive RF applications | Aerospace, military, high-end RF |
Cost-Effective Material Choices for High-Frequency Designs
Choosing the right PCB material doesn’t have to put a dent in your wallet. Both Taconic and Rogers provide options that strike a solid balance between performance and cost. Here are some tips to help you make informed material selections without compromising on quality:
1. Evaluate Project Requirements
Understanding the specific needs of your project is key. If your application demands high performance while keeping an eye on the budget, Taconic materials like the TLY series can provide impressive capabilities at a more affordable price compared to Rogers products.
2. Consider Layer Count and Complexity
For multi-layer designs, the choice of material can significantly affect manufacturing costs. Using Taconic for outer layers and a more affordable option for inner layers can help maintain a balance between performance and cost.
3. Long-Term Reliability vs. Short-Term Savings
While it might be tempting to choose the cheaper option, consider the long-term implications. Rogers materials, while often pricier, may offer enhanced durability and performance that could save money on replacements and repairs down the line.
4. Quantity Discounts
Don’t overlook the benefits of bulk purchasing. Many suppliers offer discounts on large orders, allowing you to save on both Taconic and Rogers materials when planning for larger projects.
5. Consulting with Manufacturers
Reaching out to manufacturers can provide valuable insights into the best material choices for your specific application. They often have experience with various materials and can guide you in making the most cost-effective decision.
Here’s a handy reference for evaluating your material choices:
Factor | Consideration |
Project Requirements | Assess if performance or cost is a priority. |
Layer Count | Choose materials wisely for outer vs. inner layers. |
Long-Term Reliability | Evaluate the potential savings on replacements. |
Quantity Discounts | Take advantage of bulk order discounts. |
Manufacturer Consultations | Gain insights from experts in the field. |
Popular Taconic PCB Laminates for High-Performance Applications
When it comes to high-performance applications in the electronics industry, Taconic PCB laminates are a go-to choice for engineers and designers. They deliver reliable performance across a range of environments, particularly in RF and microwave applications. Let’s dive into two of the most popular laminates: RF-35 and TLY-5, exploring their properties, use cases, and how to select the right one for your needs.
Properties and Use Cases of Taconic RF-35 and TLY-5 Laminates
1. Taconic RF-35
Overview: RF-35 is a popular choice among designers for its excellent thermal stability and low loss characteristics. This laminate is constructed from a PTFE (polytetrafluoroethylene) base, which is a preferred material for high-frequency applications.
Properties:
●Dielectric Constant: 3.5
●Loss Tangent: 0.0021 at 10 GHz
●Thermal Stability: Can operate up to 260°C, making it suitable for demanding environments.
●Moisture Absorption: Minimal, ensuring consistent performance even in humid conditions.
Use Cases:
●Aerospace and Defense: Due to its robust thermal stability, RF-35 is ideal for applications in aerospace where equipment is subjected to extreme temperatures.
●Telecommunications: Its low loss characteristics make it a great fit for RF signal transmission, helping to maintain signal integrity over long distances.
2. Taconic TLY-5
Overview: TLY-5 is designed for high-frequency applications that demand excellent electrical performance and mechanical reliability. It’s particularly favored for its balance of cost and performance.
Properties:
●Dielectric Constant: 2.2
●Loss Tangent: 0.0011 at 10 GHz
●Thermal Stability: Operates well at temperatures up to 180°C.
●Surface Finish: Smooth surface, enhancing solder adhesion and facilitating better signal performance.
Use Cases:
●RF Amplifiers: The low loss characteristics of TLY-5 make it a perfect choice for RF amplifiers in consumer electronics.
●Antenna Applications: Its lightweight nature and excellent dielectric properties allow for effective antenna designs in wireless communications.
Comparison Table of Taconic RF-35 and TLY-5 Laminates
Property | Taconic RF-35 | Taconic TLY-5 |
Dielectric Constant | 3.5 | 2.2 |
Loss Tangent | 0.0021 at 10 GHz | 0.0011 at 10 GHz |
Thermal Stability | Up to 260°C | Up to 180°C |
Moisture Absorption | Minimal | Low |
Typical Applications | Aerospace, Telecommunications | RF Amplifiers, Antennas |
How to Select the Right Taconic Laminate for RF and Microwave Applications?
Choosing the right Taconic laminate for your RF and microwave applications can be a bit of a puzzle, but with a few handy tips, you’ll be navigating this process like a pro!
1. Assess Application Requirements
Begin by evaluating the specific requirements of your project. Are you working in a high-temperature environment? If so, RF-35 might be your best bet due to its superior thermal stability. On the other hand, if your focus is on low-loss performance for RF amplifiers, then TLY-5 could be the way to go.
2. Consider Frequency and Impedance Needs
Understanding the frequency at which your circuit will operate is crucial. Taconic laminates provide various dielectric constants, allowing you to choose the best match for your design’s impedance. For instance, the TLY-5’s lower dielectric constant makes it suitable for high-frequency applications, while the RF-35’s higher constant is better for moderate frequencies.
3. Evaluate Cost and Availability
Budget considerations can significantly influence your decision. While RF-35 offers outstanding performance, TLY-5 often presents a more cost-effective solution for projects where extreme performance isn’t necessary. Comparing costs from different suppliers can also yield savings without sacrificing quality.
4. Consult with Experts
Don’t hesitate to reach out to Taconic representatives or experienced colleagues for guidance. Their insights can provide invaluable information that can help steer your decision in the right direction.
Taconic PCB Manufacturing Processes: Key Considerations for High-Precision Circuits
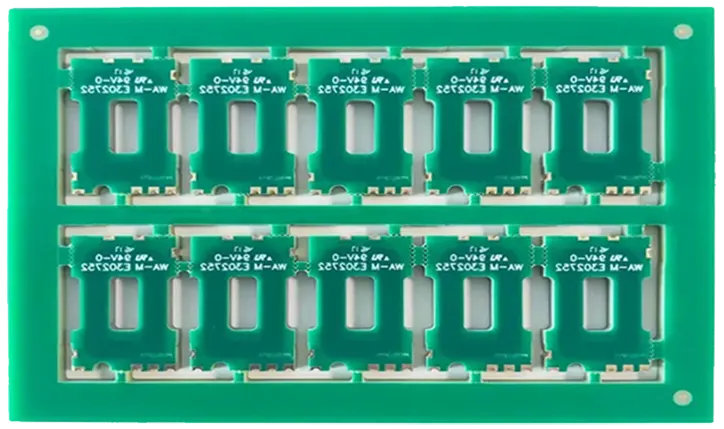
In high-precision circuit design, understanding the manufacturing processes for Taconic PCBs is fundamental. PTFE-based materials present unique challenges and opportunities, requiring specific strategies to ensure top performance. This section will explore the specialized handling techniques needed for PTFE and offer practical tips for engineers aiming to minimize material expansion and warping during manufacturing.
Handling and Machining Taconic PTFE-Based Materials in PCB Production
When working with PTFE (polytetrafluoroethylene) materials, it’s essential to recognize that their unique properties necessitate specialized handling techniques. Unlike traditional PCB materials, PTFE offers exceptional dielectric performance but can also be more sensitive to temperature changes and mechanical stress.
1. Unique Properties of PTFE
●Low Friction: PTFE is known for its low friction properties, which can be a double-edged sword during machining. While it allows for smoother machining, it also means that tools can slip if not properly calibrated.
●Thermal Expansion: PTFE has a higher thermal expansion coefficient compared to other PCB materials. This means that dimensional accuracy can be affected during machining, requiring precise temperature controls.
2. Specialized Handling Techniques
●Controlled Environment: Maintain a stable temperature and humidity in the manufacturing facility. Fluctuations can lead to expansion or contraction of PTFE, impacting the integrity of the PCB.
●Custom Tooling: Utilize specialized tooling designed for PTFE machining. This includes sharp, durable cutters that can handle the material’s unique properties without generating excessive heat.
Example Tooling Specification Table:
Tool Type | Material | Recommended Specifications |
Cutting Tools | Carbide or Cobalt | Sharp edges, low friction coatings |
Drill Bits | High-Speed Steel | Designed for PTFE with minimal chipping |
End Mills | Solid Carbide | High helix angle for efficient cutting |
Tips for Minimizing Material Expansion and Warping During Manufacturing
Ensuring dimensional stability in Taconic PCBs is a must, especially in high-frequency applications where precision is non-negotiable. Here are some practical tips for engineers aiming to tackle expansion and warping challenges during the manufacturing process:
1. Pre-Production Material Conditioning
●Thermal Stabilization: Allow the PTFE material to acclimate to the production environment before machining. This process can help minimize internal stresses and reduce the risk of warping.
2. Precision Machining Techniques
●Cutting Parameters: Adjust cutting speeds and feed rates to minimize heat generation. A slower feed rate can reduce friction, which in turn lowers the chances of heat-induced warping.
●Cooling Techniques: Implementing cooling techniques during machining, such as mist coolant systems, can help keep the temperature stable and prevent thermal expansion.
3. Post-Processing Considerations
●Stress Relief: After machining, allow the PCBs to undergo a stress relief process, which can help mitigate any internal stresses developed during the cutting process.
●Quality Control: Utilize precision measurement tools to verify the dimensions of the finished product, ensuring that any warping is detected and corrected before the final assembly.
Best Practices for Assembling High-Frequency Taconic PCBs
Assembling Taconic PCBs for high-frequency applications requires a keen understanding of the unique characteristics of low-loss materials. By following best practices during assembly, you can optimize performance and minimize issues down the line. Let’s explore some techniques and tips to ensure your assembly process is as smooth as a well-oiled machine.
Optimizing Assembly Processes for Low-Loss Materials in Taconic PCBs
The assembly of high-frequency Taconic PCBs involves specific techniques tailored for low-loss materials. Ensuring that every step in the assembly process aligns with the unique requirements of these materials can significantly impact the overall performance of the circuit.
1. Soldering Techniques for High-Frequency Circuits
Lead-Free Soldering: Choosing for lead-free solder to minimize thermal stress on PTFE substrates. This choice also aligns with environmental standards while ensuring a reliable bond.
Controlled Heat Application: Use soldering techniques that apply controlled heat, such as hot air rework or infrared soldering. These methods help prevent thermal shock to the delicate materials of Taconic PCBs.
Soldering Temperature Guidelines:
Solder Type | Temperature Range (°C) | Application Method |
Lead-Free Solder | 230 – 250 | Hot Air Rework, Infrared |
Tin-Lead Solder | 180 – 210 | Wave Soldering |
2. Handling Techniques
Static Control: High-frequency circuits are sensitive to electrostatic discharge (ESD). Implement ESD control measures during handling and assembly, such as wearing grounded wrist straps and using anti-static mats.
Gentle Touch: When placing components, use non-abrasive tools to prevent damage to the surface of the Taconic PCB. A gentle touch goes a long way in preserving the integrity of the materials.
Common Challenges in Assembling Taconic RF Circuits and How to Overcome Them?
Even the most seasoned engineers face challenges when assembling Taconic RF circuits. Identifying these common issues and implementing effective solutions can lead to a successful assembly process.
1. Delamination Concerns
Problem: Delamination can occur if there’s too much heat applied during soldering or if moisture is present in the materials.
Solution: Ensure thorough drying of the PCBs before assembly and use controlled soldering processes that minimize thermal exposure.
2. Impedance Mismatches
Problem: Mismatched impedance can lead to signal integrity issues, affecting overall performance.
Solution: Verify the layout design to ensure that trace widths match the required impedance levels. Use simulation tools to analyze and confirm that the design meets RF specifications.
3. Component Placement Accuracy
Problem: Inaccurate placement of components can lead to inefficiencies and performance degradation.
Solution: Implement automated pick-and-place machines with high precision. Regular calibration and maintenance of these machines can ensure consistent accuracy.
Ensuring Thermal Management and Reliability in Taconic PCB Designs
In high-frequency applications, managing thermal performance and reliability is non-negotiable. The unique properties of Taconic PCBs make them suitable for handling the challenges of heat dissipation, but proper design and assembly practices are key to unlocking their full potential.
Addressing Heat Dissipation Challenges in High-Frequency PCB Designs
When it comes to high-frequency PCBs, heat dissipation can be a thorn in the side. Excess heat not only affects performance but can also lead to failure if left unaddressed. Here are some practical tips for managing thermal expansion and optimizing cooling strategies.
1. Implementing Effective Heat Sinks
Why They Matter: Heat sinks increase the surface area available for heat dissipation, allowing components to cool more efficiently.
Tip: Consider integrating aluminum or copper heat sinks into your design. These materials have excellent thermal conductivity, which helps draw heat away from sensitive components.
2. Thermal Via Usage
What They Do: Thermal vias allow heat to pass through the PCB layers, facilitating better heat distribution.
Implementation: Strategically place thermal vias near high-heat-generating components to enhance thermal conductivity. For instance, using larger vias can improve heat transfer rates significantly.
Example of Thermal Via Arrangement:
Component | Via Size | Heat Transfer Efficiency |
Power Amplifier | 0.3 mm | Moderate |
Voltage Regulator | 0.5 mm | High |
Microprocessor | 0.4 mm | High |
3. Choosing the Right Layout
Heat Flow Design: Designing your PCB layout to allow for natural heat flow can greatly enhance thermal management. Aim for a layout that positions high-heat components away from heat-sensitive areas.
Tip: Avoid routing traces that can trap heat in corners. Instead, aim for more open pathways that encourage airflow, even within the PCB.
Material Properties that Help Improve Thermal Stability in Taconic PCBs
Selecting the right materials can make all the difference when it comes to thermal stability in your Taconic PCB designs. Understanding the material properties that enhance thermal management will set you on the right path.
1. PTFE-Based Substrates
Heat Resistance: PTFE (Polytetrafluoroethylene) substrates exhibit excellent thermal resistance, allowing them to maintain performance even under high-temperature conditions.
Benefit: Their low thermal expansion coefficient helps maintain dimensional stability during temperature fluctuations, reducing the risk of warping or delamination.
2. Enhanced Thermal Conductivity
Comparison of Materials: When evaluating materials, consider those with high thermal conductivity ratings, like certain Taconic laminates that incorporate metal-filled composites.
Thermal Conductivity Comparison:
Material | Thermal Conductivity (W/mK) | Ideal Applications |
Taconic RF-35 | 0.5 | RF Circuits |
TLY-5 | 0.6 | Microwave Applications |
Rogers RO4350B | 0.3 | High-Frequency Circuits |
3. Coefficient of Thermal Expansion (CTE)
Significance: A low coefficient of thermal expansion (CTE) plays a significant part in preserving the integrity of solder joints, helping to keep connections stable over time. When materials expand and contract at different rates due to temperature changes, it can lead to weakened joints and potential failures.
Taconic Advantage: Many Taconic materials are engineered to have a low CTE, which aids in the durability of the PCB under varying temperatures.
Quality Control and Testing for Taconic PCBs in High-End Applications
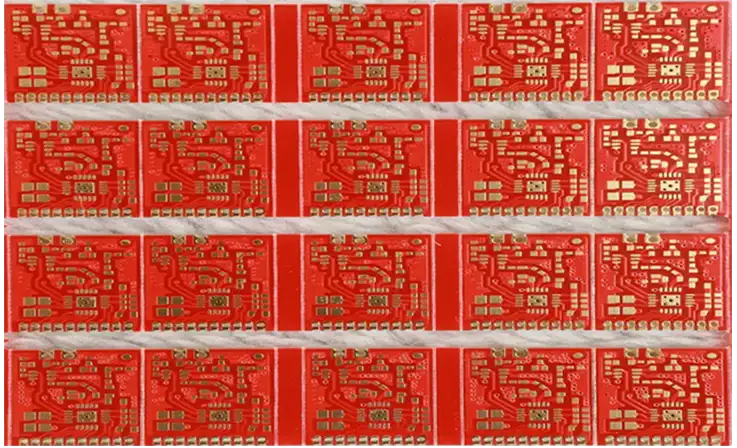
In the competitive landscape of high-end electronics, ensuring the quality and reliability of Taconic PCBs is non-negotiable. Rigorous testing and stringent quality control measures are the cornerstones of delivering exceptional performance, especially in applications demanding precise RF functionality. Let’s explore the critical testing methods and quality assurance steps that pave the way for reliable Taconic PCB designs.
Ensuring Signal Integrity and Reliability Through Rigorous Testing
Ensuring signal integrity is a top priority in high-frequency applications. Even the smallest glitch can cause performance issues, affecting the entire system’s functionality. Here’s a rundown of essential testing methods designed to ensure optimal RF performance in your Taconic PCBs.
1. Time Domain Reflectometry (TDR)
Purpose: TDR is utilized to identify impedance mismatches and discontinuities within the PCB traces.
Process: By sending a fast pulse down a transmission line and measuring reflections, engineers can pinpoint problems that could lead to signal loss.
Example of TDR Results:
Parameter | Expected Value | Measured Value | Action Needed |
Impedance (Ω) | 50 | 48 | Adjust trace widths |
Reflection Coefficient | < -10 dB | -12 dB | Acceptable |
2. In-Circuit Testing (ICT)
Description: ICT checks the functionality of each component on the PCB while still on the assembly line.
Benefit: This method helps catch defects early, reducing the cost and time associated with post-assembly troubleshooting.
3. High-Frequency Testing
Objective: Conducting tests at the specific frequencies your PCB is designed to operate is key to grasping how the circuit performs in real-world scenarios. This approach allows you to simulate actual operating conditions, providing insights into the circuit’s behavior under typical loads.
Example: For Taconic RF circuits, measuring insertion loss at 5 GHz can reveal how well the PCB will perform in its intended application.
Quality Control Steps to Ensure Long-Term Durability in Taconic RF PCBs
Quality control is not just a checklist—it’s a mindset that influences the entire production process. Implementing robust quality control steps ensures long-term durability and performance of your Taconic RF PCBs.
1. Material Inspection
Why It Matters: Quality starts with the materials. Inspecting raw Taconic laminates for defects ensures that any issues are addressed before they reach production.
Tip: Use a systematic approach to evaluate the thickness, dielectric constant, and thermal properties of the materials.
2. Process Control
Best Practices: Monitor temperature and humidity during the manufacturing process to maintain optimal conditions. Fluctuations can lead to warping or delamination of materials.
Example of Environmental Conditions:
Parameter | Optimal Range | Measured Range | Adjustment Needed |
Temperature (°C) | 20-25 | 18-30 | Adjust HVAC settings |
Humidity (%) | 40-60 | 35-65 | Use dehumidifiers |
3. End-of-Line Testing
Purpose: Conduct final inspections and testing to ensure the finished product meets all specifications before shipment.
Methods: Use automated optical inspection (AOI) and functional testing to verify that each PCB operates as intended.
Sourcing and Supply Chain Considerations for Taconic PCB Materials
In the competitive landscape of electronics manufacturing, sourcing high-performance Taconic PCB materials can significantly impact production efficiency and product quality. A strategic approach to supply chain management ensures that OEMs and electronics manufacturers maintain a steady flow of materials, enabling them to meet project deadlines without compromising quality.
Managing the Supply Chain for High-Performance PCB Materials
Securing a stable supply of Taconic materials requires careful planning and proactive management. Here are some tried-and-true tips for navigating the complexities of the supply chain:
1. Build Strong Relationships with Suppliers
Cultivating relationships with multiple suppliers can mitigate risks associated with material shortages. Engage in regular communication to understand their capacity, lead times, and inventory levels.
2. Monitor Market Trends
Stay abreast of market trends that could affect material availability. For instance, fluctuations in demand for high-frequency applications may lead to temporary shortages. By forecasting trends, you can adjust your procurement strategy accordingly.
3. Diversify Your Supply Base
Relying on a single source can be a gamble. Diversifying your supplier base helps protect against disruptions. For example, if one supplier faces production issues, having alternatives can keep your operations running smoothly.
4. Leverage Technology for Supply Chain Management
Implement software solutions that provide real-time data on inventory levels, supplier performance, and order statuses. This transparency can streamline operations and improve responsiveness to changing demands.
Example of Supplier Evaluation Criteria:
Criteria | Weight (%) | Rating Scale (1-5) | Total Score |
Quality Assurance | 30% | / | / |
Delivery Timeliness | 25% | / | / |
Cost Competitiveness | 20% | / | / |
Customer Support | 15% | / | / |
Flexibility | 10% | / | / |
Evaluating Vendors for Consistent Quality in Taconic PCB Production
Choosing the right vendors is fundamental to ensuring the quality and reliability of Taconic PCB production. Here’s how to effectively assess possible suppliers:
1. Assess Quality Management Systems
Inquire about the vendor’s quality management systems (QMS). A robust QMS that adheres to industry standards (like ISO 9001) indicates a commitment to maintaining high quality throughout the production process.
2. Request Sample Materials
Before finalizing a partnership, request samples of the Taconic materials. This hands-on evaluation allows you to assess their quality, consistency, and suitability for your specific applications.
3. Evaluate Manufacturing Capabilities
Understanding a vendor’s manufacturing capabilities is key. Ensure they have the necessary equipment and technology to handle your specifications. For instance, some applications may require high-frequency testing capabilities that not all suppliers possess.
4. Conduct Site Visits
If possible, conduct site visits to prospective vendors. This firsthand experience provides insights into their operational processes, cleanliness, and adherence to safety protocols.
High-Frequency PCB Assembly Techniques for OEMs Using Taconic Materials

In today’s competitive electronics market, the assembly of high-frequency Taconic PCBs demands precision and efficiency. OEMs need to implement effective techniques that ensure quality while optimizing manufacturing processes.
How OEMs Can Optimize PCB Assembly with Taconic Laminates?
1. Utilize Advanced Soldering Techniques
High-frequency applications often involve specific soldering methods. Consider using low-temperature solders or solder paste tailored for high-frequency performance. These options can improve joint reliability while minimizing thermal stress on Taconic materials.
2. Implement Automated Assembly Solutions
Automation can enhance precision and reduce assembly time. Machines equipped with vision systems can ensure accurate placement of components, reducing the chances of misalignment. For example, surface-mount technology (SMT) machines can effectively handle small, delicate components, ensuring they are positioned accurately on Taconic PCBs.
3. Optimize Layout Design
Effective layout design is fundamental. Make sure that trace widths and spacing comply with guidelines specific to high-frequency applications. Leveraging computer-aided design (CAD) tools can streamline the layout process and optimize assembly for signal integrity.
Technique | Description | Benefits |
Advanced Soldering | Use low-temperature solders or specialized solder paste | Improved reliability, reduced thermal stress |
Automated Assembly | Utilize machines with vision systems for precise placement | Increased speed and accuracy |
CAD Layout Optimization | Design for high-frequency specifications | Enhanced signal integrity |
Improving Efficiency and Yield in High-Volume Taconic PCB Assembly
Maximizing efficiency and yield in high-volume production can significantly impact profitability. Here are some strategies to help achieve those goals:
1. Standardize Processes
Creating standardized assembly procedures can streamline operations. Documenting every step—from material handling to soldering techniques—ensures consistency across production batches. This approach not only improves efficiency but also enhances quality control.
2. Implement Continuous Training
Investing in training for assembly staff is key. Regular workshops and hands-on sessions focused on the unique properties of Taconic materials and high-frequency assembly techniques keep the team sharp and aware of the best practices.
3. Monitor and Analyze Yield Rates
Keep a close eye on yield rates. Implement real-time monitoring systems to track production metrics and identify bottlenecks in the assembly process. Analyzing this data can help you make informed decisions to improve overall efficiency.
Wrapping Up
In the landscape of high-frequency applications, Taconic PCBs have emerged as a top contender, offering manufacturers a range of benefits that cater to their specific needs. From telecommunications to aerospace, these materials prove their worth across various sectors.
As you look to enhance your high-frequency applications, consider the benefits of Taconic PCBs. They deliver performance and reliability that can set your products apart in a competitive market. Don’t miss out on the opportunity to elevate your designs—make the switch to JarnisTech today!
Frequently Asked Questions (FAQ)
What is the ideal Taconic material for high-frequency circuits?
For most high-frequency applications, Taconic RF-35 is a solid choice due to its low dielectric constant and stable RF performance. It’s widely used in antenna systems and satellite communication.
How do Taconic PCBs compare to Rogers materials in RF applications?
While Rogers materials offer excellent thermal management, Taconic materials often provide a better price-to-performance ratio for high-frequency circuits, especially in cost-sensitive projects.
What are the challenges in assembling high-frequency Taconic PCBs?
The PTFE base of Taconic PCBs makes them sensitive to high temperatures during soldering. Proper temperature control and specialized assembly techniques are needed to avoid damage.
Can Taconic PCBs handle extreme temperatures?
Yes, Taconic PCBs are known for their thermal stability and can handle extreme environments, making them suitable for aerospace and military applications.
What are the common applications for Taconic laminates?
Taconic laminates are commonly used in RF circuit boards, antenna systems, military radars, satellite communication systems, and 5G technology.
How do I ensure high-quality Taconic PCB manufacturing?
Partner with manufacturers experienced in high-frequency PCB fabrication and ensure that proper testing and quality control procedures are followed throughout production.