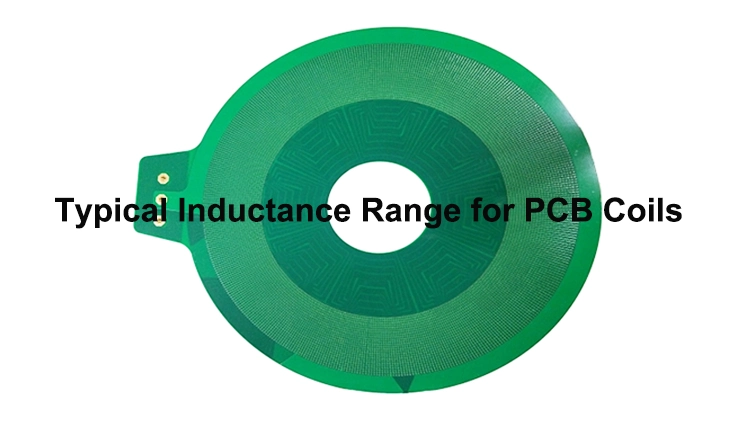
PCB coils are components in many electronic circuits and their inductance values have a significant impact on how well a circuit functions. It’s important for engineer designing and choosing coils to understand the usual inductance ranges and what they mean. This piece gives an overview of the typical inductance levels for different types of PCB coils like spiral, solenoid, toroidal and planar coils. We also discusses the factors that can influence inductance values and provides advice, for coil design considerations.
Overview of PCB Coils and Inductance
PCB coils, commonly referred to as PCB inductors or surface mount inductors are parts utilized in the design of printed circuit board to offer inductance. Inductance is a characteristic of a component, within a circuit that resists alterations in flow and retains energy within a magnetic field.
PCB coils are usually compact parts created through different winding methods and materials. They are crafted to possess an inductance value and are commonly utilized alongside components, like capacitors to construct diverse electronic circuits.
Inductance is typically quantified in henries (H) although in PCB design its more common to refer to units like microhenries (μH) or nanohenries (nH). The inductance rating of a PCB coil is influenced by factors such, as the coils number of turns, physical size and core material. PCB coils are utilized in electronic devices and circuitry for diverse purposes:
● Filtering and Signal Conditioning
● RF and Wireless Applications
● Power Electronics
● Oscillators and Resonant Circuits
● EMI and EMC Protection
PCB coils play a role in numerous electronic circuits. Their ability to provide inductance enables various functions, including filtering, impedance matching, energy storage, and frequency control. Engineers need to assess the application needs and select the right PCB coil to ensure top notch circuit performance.
Role of Inductors in PCB Design
Inductors are crucial in PCB design as they perform vital function. They serve as versatile components with various application in a electronic circuit, and they improve circuit performance and capabilities. Here are the main responsibilities that inductor carry out in PCB design.
Energy Storage and Filtering:
Inductors play a role in electronic circuits as they can store energy in their magnetic fields when electricity passes through them. This stored energy can be released back, into the circuit when required, aiding in power control. Moreover inductors are frequently employed in filters to either permit or restrict frequencies. When combined with capacitors they create LC filters that effectively eliminate frequency elements from signals thereby enhancing signal clarity.
Resonance and Impedance Matching:
By utilizing the characteristics of inductors and capacitors resonant circuits can be designed to have a peak response at a particular frequency. These circuits are essential in applications such as tuned circuits and oscillators, where precise frequency control is critical. Moreover inductors are players, in ensuring impedance matching within circuits. They assist in aligning the impedance of circuits or components enhancing power transfer efficiency and minimizing undesired signal reflections.
Power Conversion and Electromagnetic Interference (EMI) Suppression:
Inductors are components in power conversion systems especially in switch mode power supplies (SMPS). They enable energy storage during the on-time of a switching cycle and release it during the off-time, effectively regulating and stabilizing the output voltage. Moreover inductors are vital for reducing interference (EMI), by creating a pathway for high frequency noise currents to flow with low impedance. This prevents EMI from spreading through the circuit or emitting from the PCB safeguarding the systems integrity.
Therefore, inductors are indispensable components in PCB design, offering a broad range of electronic functions and significantly enhancing circuit performance. Their flexibility and ability to serve purposes are essential for ensuring electronic systems operate at their best. In addition, Inductors come in forms like through hole surface mount and integrated passive components (IPCs). Choosing the type and design of an inductor depends on factors such as the required inductance value, current capacity, frequency response and size restrictions, for a specific application.
Factors Affecting PCB Coil Inductance
● Coil Geometry
● Number of Turns
● Conductor Material and Dimensions
● Distance Between Conductors
● Core Material
● Proximity to Other Magnetic Materials
● Temperature
● Manufacturing Tolerances
When designing or selecting a PCB coil, it is essential to consider all relevant factors to achieve the desired inductance. Utilizing inductance calculators and simulation tool allow for precise determination of inductance based on specific coil design parameter.
Typical Inductance Range for PCB Coils
The range of inductance in PCB coils may differ based on the design and intended use. Nevertheless the usual ranges, for types of PCB coils are as outlined below.
● Spiral inductors: 1 nanohenry (nH) ~ 100 microhenries (µH).
● Solenoid inductors: 1 microhenry (µH) ~ 100 millihenries (mH).
● Toroidal inductors: 1 microhenry (µH) ~ 100 millihenries (mH).
● Planar inductors: 1 nanohenry (nH) ~ 10 microhenries (µH).
These ranges are estimates and can differ based on various factors, like the number of turns, type of conductor, core material (if any) and coil shape. Generally coils with turns or larger core materials tend to show higher inductance values.
When choosing PCB coils it’s important to take into account the needs of the application. This include the desired inductance value as well as factor. Such as the coil’s current carrying capacity, physical size limitations and manufacturing tolerances.
Impact of PCB Coil Inductance on Circuit Performance
The inductance of PCB coils play a significant role in determining the performance characteristics of electronic circuits. Various important factor come into play because of the presence of inductance.
Resonance:
Printed circuit board coils, in conjunction with capacitors, can form resonant circuits that exhibit peak responses at specific frequencies. This characteristic is used in applications, like tuned circuits and oscillators. Nonetheless if not managed correctly resonance could result in oscillations or distortion of signals.
Impedance Matching:
PCB coils are employed to match the impedance of one circuit or component to another. This facilitates optimal power transfer and minimizes reflections. Impedance matching plays a role in RF circuits and antenna systems.
Filtering:
PCB coils, when paired with capacitors can act as filters to either block or allow frequency part. These combinations form LC filters, which effectively remove unwanted noise or interference from signal.
Energy Storage:
PCB coils store energy in their magnetic field when current flows through them. This stored energy can be subsequently released back into the circuit as required. PCB coils find application in power supplier and other systems where energy storage is essential.
Power Conversion:
PCB coils play a role in power conversion circuits like switch mode power supplies (SMPS). They help store energy at one stage of the switching process and release it at another stage contributing to maintaining the output voltage stable.
Transient Protection:
PCB coils can provide transient protection by limiting the rate of change of current in a circuit. Which in turn safeguards delicate components from voltage spikes and other sudden occurrences.
Practical Considerations for PCB Coil Design
In addition to the theoretical aspects of PCB coil design, but also consider practical factor to make sure the coils can be manufactured effectively are reliable and perform at their best.
Current Carrying Capacity:
The coils design needs to consider the projected current levels to avoid overheating or saturation. It’s important to take into like the type of conductor material, sectional area and effective heat management in order to make sure that the coil can manage the expected current without any problems.
Physical Size Constraints:
The coils size is limited by the space, on the PCB. Designers frequently have to balance obtaining the desired inductance and staying within the designated space. Creating compact coil designs involves optimizing its shape and choosing materials thoughtfully.
Manufacturing Tolerances:
Differences in how the productsre made may lead to small changes in the inductance levels of PCB coils. Designers need to consider these differences to make sure the coils always fall within the expected inductance range. By being aware of the restrictions, in manufacturing and collaborating closely with manufacturers designers can attain uniform results.
Thermal Effects:
Temperature variations can impact the inductance of the coil. This factor becomes crucial in situations where maintaining a temperature stability is vital. It is important for designer to choose material and construction method that can endure the temperature fluctuations without causing notable alterations in inductance.
Magnetic Interference:
PCB coils produce fields that may disrupt nearby components. To reduce magnetic interference it is important to use effective shielding methods or place the coil strategically in relation to other components. This ensures the circuits stability. Prevents unintended coupling effects.
Cost and Manufacturability:
The cost and feasibility of the coil design need evaluation. Elements like material accessibility, manufacturing intricacy and assembly procedures can greatly affect both the cost and production simplicity. Choosing accessible budget friendly materials and refining the design for streamlined manufacturing methods are crucial tactics, for cutting down on production costs.
Testing and Validation:
Testing and validating the coils thoroughly is crucial to make sure they meet the required standards. Important tasks involve measuring inductance carrying out tests and assessing performance to confirm that the coils function as planned. This procedure is important, for identifying any design or production issues that might affect the coils efficiency and dependability.
Final Thoughts
The range of inductance in PCB coils plays a role in how they are designed and perform within electronic circuits. Engineers can enhance the performance of these coils by considering factors such as current carrying capacity, size limitations, manufacturing precision, thermal impact, magnetic interference, cost implications and testing procedures. This understanding enables engineers to tailor PCB coil designs to meet the needs of their applications resulting in optimized circuit performance and reliable system integration. By staying up to date on coil technology advancements and utilizing simulation tools effectively engineers can drive innovation, explore new possibilities in electronics design.