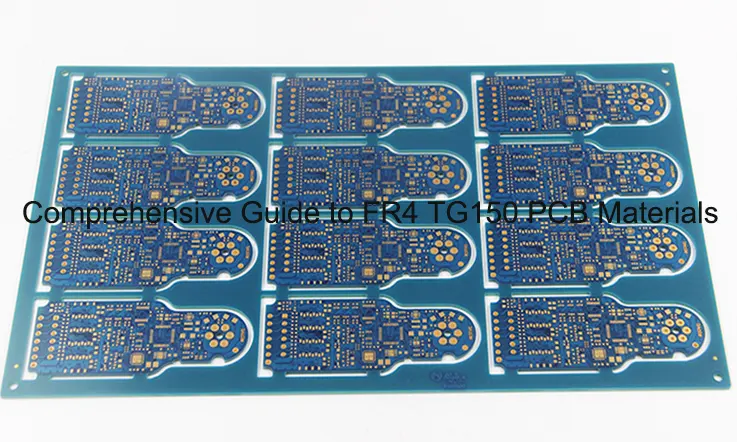
In the rapidly evolving world of electronics, the demand for printed circuit boards (PCBs) that can withstand high thermal and mechanical stress has become increasingly important. One such material that meets these rigorous requirements is the FR4 TG150 PCB. This guide will delve into the intricacies of FR4 TG150 PCBs, exploring their key properties, applications, and why they are an excellent choice for high-thermal environments. We will also compare them with other materials, such as TG140 and TG180, to help engineers and procurement teams make informed decisions when selecting PCBs.
Understanding FR4 TG150 PCB: Key Features and Applications
What is FR4 TG150?
FR4 TG150 refers to a type of PCB material with a glass transition temperature (Tg) of 150°C. The glass transition temperature is the point at which the material changes from a rigid state to a more flexible one under heat. This property is vital for PCBs used in high-temperature environments, as it ensures the board maintains its structural integrity and performance under thermal stress.
FR4 TG150 material is a fiberglass-reinforced epoxy laminate, making it robust, durable, and capable of handling significant thermal loads. Its high Tg rating makes it suitable for applications where heat resistance is a primary concern. The material is particularly favored in industries such as telecommunications, automotive, and industrial electronics, where performance under extreme conditions is non-negotiable.
Glass Transition Temperature and Its Importance in PCB Design
The glass transition temperature (Tg) plays a pivotal role in determining the operational limits of a PCB. When a PCB’s operating temperature exceeds the Tg, the board may become more flexible, leading to potential issues such as warping, delamination, or electrical failure. By choosing a material with a Tg above the expected operating temperature, engineers can ensure the PCB remains stable and reliable.
FR4 TG150 offers an ideal balance between performance and cost, as it provides a higher Tg than standard TG140 PCBs without the premium price associated with TG180 materials. This makes it a popular choice for designs requiring a high degree of thermal stability but not the highest Tg levels available.
Comparison: TG150 PCB vs TG130, TG180 and PTFE PCB
Choosing the right Tg for your PCB depends on the application’s thermal demands. Here’s a comparison between TG150, TG130, and TG180 PCBs:
TG130 PCB: Suitable for low to moderate thermal applications, TG130 is often used in consumer electronics where operating temperatures remain within manageable ranges. However, in high-performance environments, the lower Tg may lead to reliability issues.
Let’s compare them:
Parameter | Fr4 Tg150 | Fr4 Tg130 |
Glass Transition Temperature | Tg>150°C | Tg>130°C & ≤140°C |
Dissipation Factor (DF) | 0.014 (at 1MHz) | 0.017 (at 1MHz) |
Dielectric Constant (Dk) | 4.2 (at 1MHz) | 4.3 (at 1MHz) |
FR4 TG150 offers enhanced mechanical properties and thermal stability compared to FR4 TG130. However, both materials maintain high reliability in their applications.
Selecting the appropriate PCB material for your project requires careful consideration of each material’s specifications. It is important to match these specifications with the specific requirements of your application. While FR4 TG150 provides robustness, PTFE PCBs offer unique characteristics, such as a low-friction surface, making them suitable for specialized uses.
TG150 PCB: A mid-range solution, TG150 offers enhanced thermal performance without significantly increasing costs. It is ideal for applications that face occasional high temperatures or require more robust thermal management.
TG180 PCB: For applications that consistently operate in extreme thermal conditions, TG180 is the go-to material. However, the higher cost and processing complexities can make it less practical for some projects.
PTFE PCB: FR4 Tg150 is ideal for high-speed circuit applications, while PTFE PCB materials excel in low loss tangent and high-frequency tasks. When looking at the features of Fr4 Tg150 and PTFE PCB materials, they are quite different. The table below explains the distinctions between the two.
Properties | Fr4 Tg150 | PTFE |
Dielectric Constant | 4.5-5.5 | 1.8-2.2 |
Dissipation Factor (at 1MHz) | 0.015-0.025 | 0.002-0.008 |
Thermal Coefficient of Expansion (CTE) | 16-18 ppm/°C | 12-17 ppm/°C |
Thermal Conductivity | 0.3 W/m•K | 0.3-0.4 W/m•K |
Typical Applications of FR4 TG150 in High-Temperature Environments
FR4 TG150 PCBs are widely used across various industries due to their ability to maintain performance under high thermal loads. Common applications include:
Telecommunication Equipment: High-speed data processing and signal transmission generate considerable heat, making FR4 TG150 a reliable choice.
Automotive Electronics: With the increasing integration of electronics in modern vehicles, heat resistance is essential to ensure reliability in harsh environments.
Industrial and Aerospace Equipment: Systems operating in extreme or variable temperatures benefit from the thermal stability of FR4 TG150 materials.
Key Properties and Performance of FR4 TG150 Material
High-Tg and Thermal Resistance in FR4 TG150
The primary advantage of FR4 TG150 material is its enhanced thermal resistance. The Tg rating of 150°C ensures that the PCB can endure higher operational temperatures without softening or losing mechanical strength. This feature makes it suitable for applications where temperature fluctuations or extended high-temperature operation are frequent.
In addition to its thermal resistance, FR4 TG150 also offers excellent resistance to thermal cycling—a process in which the PCB is repeatedly heated and cooled. This property is crucial for applications where the PCB must maintain its integrity over multiple heating and cooling cycles, such as in automotive and industrial applications.
Please check the thermal conductivity of FR4 TG150 in comparison to other standard PCB materials:
Material | Thermal Conductivity (W/mK) |
Fr4 Tg150 | 0.3-0.35 |
Aluminum | 200-250 |
Copper | 385 |
Ceramic | 20-70 |
Thermal Conductivity Comparison: While FR4 Tg150 has lower thermal conductivity compared to metals, it surpasses ceramics in performance. This balance between cost-effectiveness and thermal management makes it a versatile choice for complex PCB designs.
Application Tip: To maximize the thermal performance of FR4 Tg150, incorporate effective cooling techniques such as heat sinks or fans in your PCB designs, and optimize component density and placement for optimal heat dissipation.
All in all, FR4 TG150 is an excellent option for applications requiring high thermal performance, cost efficiency, and reliability.
Impact of Glass Transition Temperature on PCB Durability
A PCB’s durability is closely linked to its Tg rating. When the operating temperature approaches or exceeds the Tg, the material begins to transition from a glassy, rigid state to a more elastic, rubbery state. This shift can lead to mechanical stress, warping, and in severe cases, delamination or cracking of the PCB.
FR4 TG150’s higher Tg allows it to resist these transitions better than materials with a lower Tg, such as FR4 TG140. This results in improved durability and longer operational lifespans, especially in environments where high temperatures are a consistent factor.
In addition, FR4 Tg150 PCB materials are highly resistant to chemicals, making them suitable for use in harsh environments where exposure to corrosive substances is a concern. This chemical resilience is a significant advantage for industries such as aerospace and medical equipment, where reliability is paramount.
For instance, FR4-TG150 exhibits enhanced chemical resistance compared to other materials. A comparison table highlights its advantages in chemical resistance, stability, and durability.
Material | Chemical Resistance | Impact Strength | Moisture Absorption |
FR4-TG150 | High | Excellent | Low |
CEM-1 | Moderate | Good | High |
CEM-3 | Low | Average | Moderate |
Comparison with Other Materials: FR4 Tg150 surpasses other PCB materials in terms of chemical resistance, stability, and durability, consistently exceeding IPC and industry-specific standards.
Don’t miss out on the reliable solution with amazing chemical resistance. Contact us to procure the appropriate PCB material for your project. Obtain FR4-TG150 at a competitive price—offering high performance at a cost-effective rate.
Electrical and Mechanical Properties of FR4 TG150
In addition to its thermal properties, FR4 TG150 also boasts excellent electrical insulation characteristics. This makes it a reliable choice for high-frequency applications, where signal integrity is paramount. The material’s low dielectric constant and loss tangent contribute to maintaining signal quality, even in demanding operating conditions.
Mechanically, FR4 TG150 provides the necessary rigidity and strength to support multilayer designs, which are common in advanced electronics. Its ability to resist mechanical stress and maintain its structure under high temperatures is a significant advantage in applications where vibration or mechanical shock is a concern.
PCB Thermal Expansion and Cycling Endurance
Thermal expansion is a critical factor in PCB design, particularly in high-temperature environments. As PCBs heat up, they expand, which can lead to stress between the layers of the board and potentially cause delamination. FR4 TG150 offers a lower coefficient of thermal expansion (CTE) compared to materials with a lower Tg, which means it expands less under heat, reducing the risk of structural failure.
The material’s endurance under thermal cycling—repeated heating and cooling—is also a key consideration for applications that undergo frequent temperature changes. FR4 TG150’s ability to handle these cycles without degradation further enhances its reliability and longevity.
Manufacturing and Design Considerations for FR4 TG150 PCB
Selecting the Right PCB Laminate for High-Thermal Applications
Choosing the appropriate PCB laminate is critical for ensuring the board’s performance in high-temperature environments. FR4 TG150 offers an excellent balance between thermal resistance, mechanical strength, and cost, making it a versatile choice for many applications. Its Tg rating of 150°C allows it to withstand higher operational temperatures than standard FR4 materials, making it suitable for both mid-range and high-end applications.
When selecting a laminate, it’s essential to consider the operating environment, the thermal load, and the board’s required lifespan. FR4 TG150 is particularly effective in environments where temperatures fluctuate or consistently exceed the limits of TG140 PCBs.
FR4 TG150 in Multilayer PCB Fabrication
Multilayer PCBs are a common feature in advanced electronics, as they allow for more complex circuitry in a compact form. FR4 TG150 is well-suited for multilayer designs due to its excellent mechanical strength and low thermal expansion. These properties help ensure that the layers remain securely bonded, even under thermal stress.
The material’s thermal resistance also ensures that the multiple layers of copper and laminate in the PCB remain stable during both the manufacturing process and operation. This makes FR4 TG150 an excellent choice for applications where space is limited but performance cannot be compromised.
Ensuring PCB Reliability with TG150 Laminate
To maximize the reliability of a PCB using FR4 TG150 laminate, engineers must account for the board’s thermal and mechanical requirements during the design phase. Proper layer stacking, careful selection of components, and attention to thermal management can all help ensure that the board performs optimally under high-thermal loads.
FR4 TG150’s robustness under temperature stress also contributes to reducing failure rates in critical applications, which is particularly valuable in industries where downtime or malfunction could have severe consequences.
Cost Considerations of TG150 PCBs vs Other Tg Materials
While TG180 materials offer even greater thermal performance, they come at a higher cost. FR4 TG150 strikes a balance between cost and performance, making it a more economical option for projects that require moderate to high thermal resistance. By selecting FR4 TG150, engineers can achieve the desired thermal performance without the significant price increase associated with TG180 materials.
Manufacturing Process and Technical Details for FR4 TG150 PCBs
Material Preparation and Lamination
The manufacturing process for FR4 TG150 PCBs begins with the preparation of the base laminate. The material is composed of woven fiberglass fabric impregnated with epoxy resin. The lamination process involves layering these sheets and applying heat and pressure to create a robust, thermally stable PCB. The high Tg of the material ensures that it maintains its structural integrity under elevated temperatures.
Key Considerations: Material thickness, layer counts, and compatibility with the intended application are essential factors to evaluate during the preparation phase.
Below is a table of the key considerations and processes:
Consideration | Process |
Thermal Stability | Laminate with heat-resistant material |
Mechanical Strength | Reinforce with fiberglass material |
Electrical Properties | Copper-clad with advanced technology |
Additionally, thickness and layer count must be carefully evaluated when selecting and preparing materials. Incorrect choices or preparation can result in severe issues during manufacturing. For example, materials lacking sufficient stability may lead to delamination during the lamination process, potentially causing PCB layout distortion or stress on components.
In one case, poor material selection led to widespread faults in wearable technology, severely damaging the manufacturer’s reputation. Therefore, it is critical to ensure accurate material selection from the outset.
The complexity of PCB manufacturing requires meticulous attention to these details.
Drilling and Plating Techniques
Once laminated, the PCBs are drilled to create vias and holes for component placement. Precision drilling equipment is used to ensure accuracy and avoid damage to the PCB. Following drilling, the boards undergo plating, where conductive materials are deposited onto the drilled holes to establish electrical connections. Advanced plating techniques, such as electroplating, are employed to ensure high-quality electrical performance. Precision in these steps ensures the reliability and performance of the final product. A table highlights the specific steps:
Step | Description |
1 | Drilling small holes on the PCB |
2 | Cleaning holes to remove debris |
3 | Electroless deposition of a thin copper coat |
4 | Plating additional copper layers |
Critical Parameters: Accuracy in drilling and uniformity in copper plating are vital to prevent issues like roughness, tilt angle deviation, and delamination.
During this stage, challenges such as roughness, tilt angle deviation, and delamination are commonly encountered. The process is completed by etching away excess copper, which refines the PCB’s design and results in a smooth finish.
Quality Control and Testing Procedures
Quality control is crucial for FR4 TG150 PCBs to ensure they meet the required performance standards. Testing includes thermal cycling tests to assess the PCB’s ability to withstand temperature fluctuations, electrical insulation resistance tests to verify electrical properties, and mechanical stress tests to evaluate durability. Rigorous quality control procedures are implemented throughout the manufacturing process to maintain high standards and reliability.
Design Tips and Best Practices for FR4 TG150 PCBs
Optimizing Thermal Management
Effective thermal management is essential when using FR4 TG150 PCBs. Design strategies such as incorporating heat sinks, optimizing component placement, and using thermal vias can enhance heat dissipation. Ensuring that the PCB layout allows for efficient heat flow and reducing thermal hotspots will improve the board’s overall performance and reliability.
Designing for Thermal Expansion
Thermal expansion can lead to mechanical stress and potential failure in PCBs. To mitigate these issues, consider using design features such as reinforced vias and adequate spacing between components. Additionally, selecting a PCB layout that accommodates thermal expansion and contraction will help maintain the board’s integrity under varying temperature conditions.
Applications and Benefits of TG150 PCBs in Different Industries
Consumer Electronics and High-Temperature Devices
In consumer electronics, such as smartphones, tablets, and wearables, the need for compact designs often results in higher heat densities. FR4 TG150 PCBs offer the necessary thermal resistance to ensure these devices perform reliably, even in high-temperature conditions. This material’s durability and resistance to thermal cycling make it a solid choice for devices that must endure frequent heat fluctuations during use.
The table below illustrates various applications of FR4 TG150 PCB materials across different electronic devices:
Electronic Device | Application |
Smartphones | Battery management sys., power amplifiers, battery chargers |
Tablets | WiFi & Bluetooth accessories, display backlight |
Laptops | Storage devices, CPU power supplies |
Wearable Devices | Fitness monitoring sensors, GPS modules |
FR4 TG150 materials are well-suited for environments that experience high thermal loads and vibrations. They are also effective in complex, multilayer circuit boards.
Pro Tip: When incorporating FR4 TG150 materials in consumer electronics, ensure they are handled and stored correctly, as they can be susceptible to damage from moisture or physical stress. These materials also perform exceptionally well in the aerospace industry.
Telecommunication Equipment and Networking Hardware
Telecommunication equipment operates continuously, often generating significant heat. For this reason, materials with a higher Tg, such as FR4 TG150, are preferred for the PCBs used in these devices. The material’s ability to maintain performance under thermal stress ensures that communication signals remain stable, and the equipment operates without interruption.
Automotive and Aerospace Electronics
The automotive and aerospace industries place unique demands on PCBs, as they are often subjected to extreme environmental conditions, including high temperatures and vibration. FR4 TG150 is an excellent material for these applications due to its ability to withstand thermal cycling and mechanical stress.
In automotive electronics, for instance, FR4 TG150 is used in engine control units, power management systems, and other high-temperature components. Its thermal stability and mechanical strength make it an ideal choice for these demanding environments.
Industrial Electronics and Environmental Reliability
Industrial electronics, which are used in machinery and equipment operating in harsh environments, benefit greatly from FR4 TG150’s durability. The material’s ability to perform reliably under fluctuating temperatures and its resistance to mechanical stress ensure that industrial PCBs continue to function effectively over time, even in challenging conditions.
Choosing the Right PCB Manufacturer for FR4 TG150 PCB
Key Factors in Selecting a Reliable TG150 PCB Manufacturer
When selecting a manufacturer for FR4 TG150 PCBs, several factors should be considered to ensure the boards meet the desired specifications and performance standards. These factors include the manufacturer’s experience with high-Tg materials, their quality control processes, and their ability to deliver consistent results.
A reliable manufacturer will have a proven track record of producing high-quality TG150 PCBs and will be able to provide detailed information about their manufacturing processes, including lamination, drilling, and plating techniques.
Lead-Free and RoHS Compliance for FR4 TG150 PCBs
Compliance with environmental regulations is essential for modern PCB manufacturing. FR4 TG150 PCBs should meet RoHS (Restriction of Hazardous Substances) standards, which restrict the use of certain hazardous materials in electronics. Additionally, lead-free soldering processes are commonly used to align with these regulations, ensuring that the final product is safe for both consumers and the environment.
Testing and Quality Control for High-Performance PCBs
Testing and quality control are critical steps in the PCB manufacturing process. For FR4 TG150 PCBs, manufacturers should conduct thorough testing to verify thermal performance, electrical characteristics, and mechanical integrity. This includes thermal cycling tests, electrical insulation resistance tests, and mechanical stress tests to ensure the boards meet the required specifications and will perform reliably in their intended applications.
Market Trends and Future Outlook for FR4 TG150 PCBs
Current Demand and Growth Projections
The demand for FR4 TG150 PCBs is experiencing notable growth due to the increasing complexity and thermal requirements of modern electronic devices. As industries such as telecommunications, automotive, and aerospace continue to advance, the need for reliable, high-performance PCBs that can handle elevated temperatures is rising. Market research indicates that the FR4 TG150 segment is expected to see a compound annual growth rate (CAGR) of approximately X% over the next five years. This growth is driven by the proliferation of high-performance electronics and the push towards more robust, durable PCB solutions.
Emerging Applications and Innovations
FR4 TG150 PCBs are finding new applications in various emerging technologies. For instance, their robustness is becoming essential in advanced driver assistance systems (ADAS) in automotive electronics and high-frequency signal processing in telecommunications. Innovations in material science are also enhancing the performance of TG150 PCBs, such as the integration of improved thermal management techniques and advancements in laminate technology that further extend their operational limits.
Case Studies and Real-World Applications of FR4 TG150 PCBs
Case Study 1: Telecommunication Equipment
In the telecommunications sector, FR4 TG150 PCBs are used in high-speed data processing units. A leading telecom company employed FR4 TG150 to ensure the reliability of their data routers under high thermal conditions. The use of TG150 material helped reduce signal degradation and enhanced the longevity of the equipment, even during periods of peak operational demand.
Case Study 2: Automotive Electronics
FR4 TG150 PCBs are critical in automotive electronics, particularly in engine control units (ECUs) and power management systems. An automotive manufacturer integrated TG150 PCBs in their latest vehicle models to handle the extreme temperatures generated by high-performance engines. The material’s superior thermal stability and mechanical strength ensured that the PCBs maintained their functionality and integrity throughout the vehicle’s operational lifespan.
Case Study 3: Industrial Machinery
For industrial machinery operating in harsh environments, FR4 TG150 PCBs offer significant advantages. A manufacturing plant using automated machinery adopted TG150 PCBs for their control systems. The high Tg of the material helped the PCBs withstand the fluctuating temperatures and mechanical stress encountered during operation, resulting in fewer failures and reduced maintenance costs.
User Feedback and Expert Opinions on FR4 TG150 PCBs
Insights from Industry Professionals
Industry experts value FR4 TG150 for its performance and cost-effectiveness. According to a leading electronics engineer, “FR4 TG150 offers excellent thermal performance at a reasonable price point, making it a preferred choice for many high-thermal applications.”
User Reviews and Experiences
Users report high satisfaction with FR4 TG150 PCBs in demanding applications. Feedback highlights the material’s reliability under high temperatures and resilience in harsh environments. One user noted, “We’ve experienced fewer failures and reduced maintenance costs since switching to FR4 TG150 for our industrial equipment.”
Wrapping Up: FR4 TG150 PCB as the Optimal Solution for High-Thermal Designs
Advantages of TG150 PCBs Over Lower-Tg Materials
FR4 TG150 offers several advantages over lower-Tg materials, such as TG140. Its higher Tg provides better thermal stability, which helps prevent issues like warping, delamination, and reduced mechanical strength under high-temperature conditions. This makes FR4 TG150 a more reliable choice for applications that experience elevated temperatures.
Thermal Management and Long-Term Reliability with FR4 TG150
Effective thermal management is essential for ensuring the long-term reliability of PCBs. FR4 TG150’s ability to maintain performance under thermal stress helps to manage heat effectively and extend the operational lifespan of the PCB. This is particularly valuable in applications where consistent performance and durability are critical.
How to Decide Between TG150 and Other Tg Ratings for Your Project
Choosing the right Tg material for your PCB depends on various factors, including the operating temperature, the thermal load, and the specific requirements of your application. FR4 TG150 provides a balanced solution for many high-thermal applications, offering both performance and cost-effectiveness. However, for extreme conditions, materials with a higher Tg, such as TG180, may be necessary. Evaluating your project’s needs and consulting with experienced PCB manufacturers can help ensure you select the most suitable material for your design.
Frequently Asked Questions (FAQ) About FR4 TG150 PCBs
Q: What are the main benefits of using FR4 TG150 over TG140?
A: FR4 TG150 provides better thermal stability and durability compared to TG140, making it suitable for higher thermal demands.
Q: How does FR4 TG150 compare in terms of cost?
A: FR4 TG150 is generally more cost-effective than higher Tg materials like TG180 while offering adequate thermal performance for many applications.
Q: What should I consider when designing a PCB with FR4 TG150?
A: Consider effective thermal management, thermal expansion, and ensuring the PCB layout supports high-temperature operation.