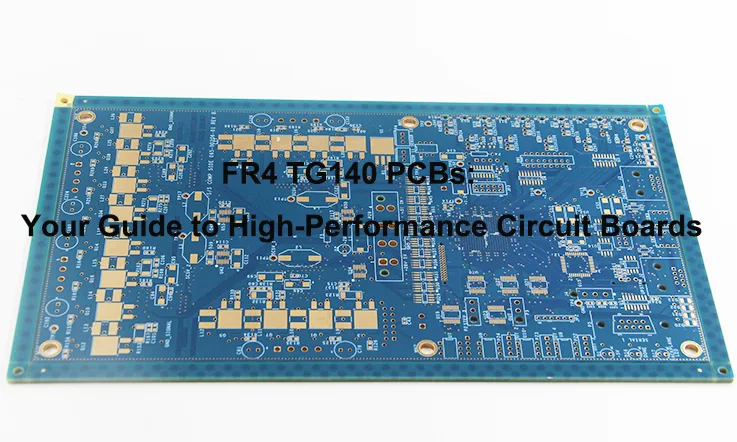
In the fast-evolving world of electronics, the quest for high-performance materials has never been more critical. Imagine a cutting-edge consumer electronics device that experiences unexpected failures during high-speed data transmission or a sophisticated automotive control system that suffers from heat-induced malfunctions. These real-world scenarios underscore the importance of selecting the right PCB materials to meet the demanding requirements of modern technology.
As electronics become increasingly complex and performance-driven, the demand for materials that can reliably handle extreme conditions is soaring. FR4 TG140 has emerged as a leading choice in this arena, providing a compelling blend of thermal stability, cost-effectiveness, and robust performance. This material’s ability to maintain integrity under higher temperatures makes it indispensable for applications where precision and reliability are non-negotiable.
For design engineers, understanding the nuances of FR4 TG140 is crucial. It’s not just about choosing a material; it’s about leveraging its properties to address specific challenges in your designs. Whether you’re developing high-speed communication circuits or intricate automotive electronics, mastering advanced design techniques such as impedance matching and thermal management can significantly enhance your PCB’s performance and durability.
But what exactly is FR4 TG140 PCB, and why is it an essential consideration for your next project? Let’s explore its features, benefits, and how it compares with other materials to help you make the best decision for your designs.
What is FR4 TG140 PCB and Why It Matters in Modern Electronics?
Understanding TG140 in PCB Materials
When you hear about TG140 in PCB materials, the “TG” refers to the glass transition temperature—a critical factor in determining how a material behaves under heat. For FR4 TG140, the glass transition temperature is 140°C, meaning this is the point where the material transitions from a hard, glassy state to a softer, more pliable one. This property is particularly important in applications where the circuit board is exposed to high temperatures for prolonged periods.
FR4 TG140: The Foundation of High-Temperature PCBs
FR4 TG140 isn’t just any material; it’s the backbone of high-temperature PCBs. Built from a woven glass fabric impregnated with epoxy resin, this material offers excellent thermal stability, making it suitable for environments where consistent thermal performance is required. The ability to withstand heat without compromising performance is why FR4 TG140 is chosen for products like automotive electronics, industrial controls, and consumer devices.
How TG Value Affects PCB Performance?
The TG value plays a pivotal role in determining the thermal and mechanical performance of a PCB. A TG140 PCB can handle moderate thermal cycling without showing significant degradation. As electronic components generate heat, especially in high-performance applications, the ability to maintain stability at higher temperatures becomes more vital. Using materials with a TG value that matches the demands of your design can significantly improve the overall lifespan and reliability of the product.
Why Choose FR4 TG140 PCB for Your Design?
Striking the Balance: Affordability and Performance-
Every design engineer and procurement team faces the challenge of selecting the right material that doesn’t just meet performance specifications but also aligns with budgetary constraints. This is where FR4 TG140 PCBs shine.
Cost-Effective Solutions for Mid-Range Applications-
One of the standout features of FR4 TG140 is that it provides a reliable performance profile at a cost that fits within most budgets. Whether you’re working on consumer electronics like smartphones and tablets or even automotive components, this material offers the heat resistance you need without escalating production costs. In markets where cost margins are thin, FR4 TG140 is a material that offers great value for the investment, making it an excellent option for mass production.
Thermal and Mechanical Stability-
Unlike cheaper alternatives, FR4 TG140 brings stability in both its thermal and mechanical characteristics. When exposed to varying temperatures, FR4 TG140 PCBs maintain their integrity, resisting warping, bending, or cracking. This level of durability is especially valuable in environments where boards may experience fluctuating temperatures, such as automotive and industrial electronics.
Designing with FR4 TG140: What You Need to Know?
Material Properties and Stack-Up Design-
Choosing the Right PCB Stack-Up for Your Project
Designing with FR4 TG140 requires an understanding of its material properties, especially when considering the stack-up design. A well-planned PCB stack-up is essential for optimizing signal transmission, managing impedance, and ensuring overall circuit performance. When working with FR4 TG140, you should focus on factors like copper thickness, trace width, and the number of layers in the design. Proper material selection ensures that the PCB performs well, even under electrical and thermal stress.
Ensuring Optimal Signal Integrity with FR4 TG140
Signal integrity is a major concern in high-speed applications, where any deviation in signal transmission can lead to performance issues. FR4 TG140 allows for excellent impedance control, which is vital for minimizing signal loss and maintaining clean data transmission. When designing multilayer boards, pay close attention to layer arrangement and the dielectric constant of the materials to ensure that signal paths remain stable.
Advanced Design Considerations for FR4 TG140 PCBs
Designing with FR4 TG140 requires a nuanced understanding of its properties and how they interact with various design parameters. To optimize performance, engineers must employ advanced design techniques and best practices. This section delves into critical aspects such as impedance matching and thermal management strategies to enhance the functionality and reliability of FR4 TG140 PCBs.
Impedance Matching: Ensuring Signal Integrity-
Understanding Impedance in PCB Design
Impedance matching is crucial in high-speed PCB designs to ensure signal integrity. Impedance mismatches can lead to signal reflections, increased noise, and degraded performance. FR4 TG140, with its specific dielectric properties, affects impedance calculations and, consequently, the performance of high-frequency circuits.
Techniques for Impedance Matching
1)Controlled Impedance Trace Design-
Trace Width and Spacing: To achieve controlled impedance, the width of the signal traces and the spacing between traces and reference planes must be meticulously calculated. For FR4 TG140, the dielectric constant (Dk) of approximately 4.5 plays a critical role in these calculations. Use impedance calculators or simulation tools to determine the correct trace width and spacing based on your board’s specific stack-up and the desired impedance.
2)Multi-Layer Stack-Up Optimization-
Layer Arrangement: Optimize the PCB stack-up by strategically placing signal layers, power planes, and ground planes. For FR4 TG140, ensure that high-speed signal layers are positioned between ground planes to minimize noise and crosstalk. This configuration helps maintain signal integrity and minimizes impedance variations.
3)Simulation and Modeling-
Use of CAD Tools: Employ advanced CAD tools to simulate signal behavior and impedance characteristics. Tools such as HyperLynx or Ansys SI can model signal propagation and impedance changes, allowing for fine-tuning of trace geometries and layer configurations.
Thermal Management: Enhancing Reliability and Performance-
Importance of Thermal Management
Effective thermal management is essential to ensure that FR4 TG140 PCBs perform reliably under varying temperature conditions. High operating temperatures can affect the material’s properties and lead to performance degradation or failure. Proper thermal management strategies help dissipate heat efficiently and maintain PCB integrity.
Advanced Thermal Management Techniques
1)Thermal Via Design
Heat Dissipation: Implement thermal vias to transfer heat from the surface of the PCB to internal layers or heat sinks. Place thermal vias strategically around high-power components and heat-generating areas to facilitate efficient heat dissipation. Ensure that the via diameters and pad sizes are optimized to handle the expected thermal load.
2)Copper Pour and Heat Spreading
Copper Pour Areas: Use large copper pours or planes to spread heat away from critical components. In FR4 TG140 designs, adding copper pours around power components can effectively distribute heat and reduce localized temperature rises. Ensure that these pours are properly connected to thermal vias or heat sinks.
3)Heat Sinks and Thermal Pads
Component Cooling: Attach heat sinks or thermal pads to high-power components to enhance heat dissipation. These additional cooling mechanisms help lower the operating temperature of components and prevent overheating. Ensure that the thermal interface materials used have low thermal resistance to maximize heat transfer.
4)Board Layout Considerations
Component Placement: Position heat-sensitive components away from high-power areas and ensure adequate spacing between components to prevent heat accumulation. Proper layout can mitigate heat concentration and improve overall thermal management.
5)Simulation and Testing
Thermal Simulation: Use thermal simulation tools to model heat distribution across the PCB. Tools such as FloTHERM or COMSOL Multiphysics can simulate thermal behavior and predict temperature rise under various operating conditions. Conduct thermal stress tests to validate your design and make necessary adjustments based on simulation results.
Comparing FR4 TG140 with TG150, TG170, and TG180
Not all PCBs are created equal, and as technology advances, the need for more specialized materials becomes apparent. While FR4 TG140 offers excellent performance for many applications, higher TG-rated materials like TG150, TG170, and TG180 are designed for more demanding environments. Understanding when to choose one over the other can make a big difference in your design’s success.
When to Use Each TG Rating?
TG140: Best for General-Purpose and Consumer Electronics
TG140 is well-suited for general-purpose PCBs and consumer electronics that require reliable performance without the need for extreme temperature resistance. It’s the go-to material for products that operate within standard temperature ranges but still need a degree of thermal resilience. Think of smartphones, gaming consoles, and household appliances—these are areas where FR4 TG140 PCBs excel.
TG150 and Beyond: For High-Performance Demands
When dealing with high-stress environments, TG150, TG170, and TG180 offer higher thermal resistance, making them ideal for industries like telecommunications, aerospace, and high-end computing. These materials can handle higher operating temperatures and more extreme thermal cycling without losing their mechanical properties. However, with these higher TG materials comes a cost, both in terms of price and potential challenges in manufacturing.
TG170 and TG180 for High-Stress Environments
If your design is for high-performance computing, telecommunication devices, or aerospace components, you may need to consider TG150 or TG170. These materials can withstand higher temperatures without mechanical deformation, making them ideal for advanced applications.
Comparison Table:
Materials | TG Value | Applications | Key Benefits |
FR4 TG140 | 140°C | Consumer electronics, automotive, industrial | Cost-effective, reliable in moderate heat |
TG150 | 150°C | Telecommunications, high-speed circuits | Higher heat resistance, better signal integrity |
TG170 | 170°C | Aerospace, advanced computing | Ideal for extreme environments |
TG180 | 180°C | High-end telecom, RF/microwave applications | Excellent thermal stability, reduced warping |
While FR4 TG140 serves well in general-purpose applications, understanding its limitations relative to higher TG materials is crucial. For instance, TG150’s enhanced thermal resistance makes it ideal for high-speed data circuits where signal integrity is paramount, whereas TG180’s exceptional stability is indispensable in aerospace applications where extreme conditions are the norm.
Real-World Applications of FR4 TG140: Case Studies and Success Stories
FR4 TG140 has proven its value across various industries by meeting the demands of high-performance electronics. Here are several case studies that illustrate its successful application, highlighting the unique challenges and benefits encountered:
1.Automotive Control Systems
Case Study: Advanced Engine Control Units (ECUs)
Background: In the automotive industry, Engine Control Units (ECUs) are pivotal for managing engine performance and emissions. These units must endure harsh operating conditions, including high temperatures and vibrations.
Application of FR4 TG140: An automotive manufacturer utilized FR4 TG140 for their ECU PCBs to handle the high thermal stresses associated with engine environments. The TG140 material was selected for its superior thermal stability, allowing the PCB to maintain performance and reliability despite temperature fluctuations.
Challenges and Benefits:
Challenge: The primary challenge was to ensure that the PCB could withstand prolonged exposure to elevated temperatures without degrading.
Benefit: FR4 TG140’s high glass transition temperature (140°C) ensured that the PCBs remained structurally intact and functioned reliably, even under the intense thermal conditions of engine compartments. This led to improved durability and reduced failure rates.
2.Consumer Electronics
Case Study: High-Speed Communication Devices
Background: Consumer electronics, such as smartphones and tablets, require PCBs that can support high-speed data transmission while remaining cost-effective. The compact design and efficient thermal management are crucial for these devices.
Application of FR4 TG140: FR4 TG140 was employed in the design of PCBs for high-speed communication devices, where its thermal stability and good dielectric properties were advantageous. The material’s balance of performance and cost made it ideal for mass production of consumer electronics.
Challenges and Benefits:
Challenge: Managing signal integrity and impedance control in high-speed circuits while maintaining affordable production costs.
Benefit: FR4 TG140 provided a stable dielectric constant that helped in maintaining signal integrity and minimizing signal loss. Its cost-effectiveness made it suitable for large-scale production without compromising performance.
3.Industrial Control Systems
Case Study: Industrial Sensor Networks
Background: Industrial sensor networks often operate in environments with significant thermal and mechanical stresses. These sensors need reliable PCBs that can handle varying temperatures and vibrations over long periods.
Application of FR4 TG140: FR4 TG140 was chosen for the PCBs in industrial sensor networks due to its robust thermal and mechanical properties. The material’s ability to withstand thermal cycling and mechanical stress ensured that the sensors operated reliably in demanding industrial environments.
Challenges and Benefits:
Challenge: Ensuring that the PCB could endure frequent temperature changes and physical vibrations without degrading.
Benefit: The thermal stability of FR4 TG140 helped maintain the performance of the PCBs, preventing issues such as warping or cracking. This reliability translated into enhanced performance and reduced maintenance needs for the sensor systems.
4.Telecommunications Equipment
Case Study: Base Station Transceivers
Background: Base station transceivers for telecommunications equipment must manage high power levels and operate efficiently in varying thermal conditions. High thermal performance and signal integrity are critical for these components.
Application of FR4 TG140: In base station transceivers, FR4 TG140 was used to ensure that the PCBs could handle the high power dissipation and thermal cycling associated with base station operations. The material’s thermal properties contributed to effective heat dissipation and overall device performance.
Challenges and Benefits:
Challenge: Managing heat dissipation while maintaining signal integrity and reliability in high-power applications.
Benefit: FR4 TG140’s excellent thermal performance allowed for efficient heat management, reducing the risk of overheating. Its dielectric stability helped maintain signal integrity, which is essential for reliable telecommunications performance.
PCB Manufacturing Process with FR4 TG140
From Lamination to Final Testing: The Journey of a PCB-
Manufacturing a FR4 TG140 PCB is a detailed process that requires careful handling at every step. From the initial lamination to the final round of testing, ensuring that the material maintains its properties is key to producing high-quality boards.
The Lamination Process for TG140-Based PCBs-
Lamination is one of the most critical stages in PCB production. For FR4 TG140-based PCBs, maintaining a controlled temperature during lamination ensures that the material’s properties aren’t compromised. During this process, the resin softens and bonds the copper layers to the dielectric material, creating a robust structure that can handle high-temperature operation.
Quality Control and Reliability Testing for FR4 TG140 PCBs-
After the fabrication process is complete, FR4 TG140 PCBs undergo rigorous testing to ensure reliability. Thermal stress tests are conducted to confirm the board’s durability under high-temperature conditions. Additionally, mechanical stress testing ensures that the boards can withstand vibrations and shocks without cracking or delaminating.
How to Choose a Manufacturer for FR4 TG140 PCBs?
What to Look for in a Trusted PCB Supplier?
Selecting a PCB manufacturer that understands the intricacies of working with FR4 TG140 is crucial to the success of your project.
Experience with High-Temperature PCBs
Experience matters when it comes to manufacturing high-temperature PCBs. Look for a supplier with a proven track record in producing FR4 TG140-based boards, especially for applications that require consistent performance under thermal stress.
Certifications and Standards for PCB Fabrication
Industry certifications, like ISO and IPC standards, are critical markers of quality. A manufacturer with these certifications has established processes in place that ensure consistency in every batch of PCBs they produce. This gives you confidence that your boards will meet both design and performance specifications.
Future Trends: Will FR4 TG140 Remain a Popular Choice?
Adapting to New Technologies and Applications-
As technology evolves, so do the requirements for PCB materials. However, FR4 TG140 remains a reliable choice for a wide range of applications, particularly in consumer electronics and automotive industries.
The Evolution of High-Temperature PCB Materials-
While higher TG materials like TG150 and TG170 are becoming more popular in advanced electronics, FR4 TG140 continues to be favored for its balance of performance and cost. As new technologies like 5G, IoT, and autonomous vehicles emerge, there may be a shift toward materials with even higher temperature tolerances. However, FR4 TG140 will likely remain a staple in industries where moderate heat resistance is sufficient.
Where Does TG140 Fit in the Next Generation of Electronics?
The future of electronics may require even more durable and high-performance materials, but FR4 TG140 will continue to serve as a trusted option for mainstream applications. Its ability to offer stable thermal performance without significant cost increases ensures that it will remain a popular choice for PCB manufacturers and designers alike.
Wrapping Up
As you embark on your next PCB design project, the choice of material can significantly influence the performance, reliability, and cost-effectiveness of your final product. FR4 TG140 stands out as a versatile option that strikes an optimal balance between performance and cost, making it a compelling choice for a wide range of applications.
Whether you are designing advanced automotive control systems, high-speed communication devices, or robust industrial control systems, FR4 TG140’s superior thermal stability and reliable mechanical properties can meet your specific requirements without escalating production costs. Its proven track record across various industries underscores its capability to deliver dependable performance under demanding conditions.
For further guidance, we invite you to delve into our comprehensive design resources, which offer in-depth insights and practical advice on leveraging FR4 TG140 effectively. Stay abreast of the latest industry trends and advancements to ensure that your designs not only meet current standards but also lead the way in technological innovation.
By staying informed and applying best practices, you can ensure that your designs remain at the forefront of technology, harnessing the full potential of FR4 TG140 to achieve exceptional results in your projects.