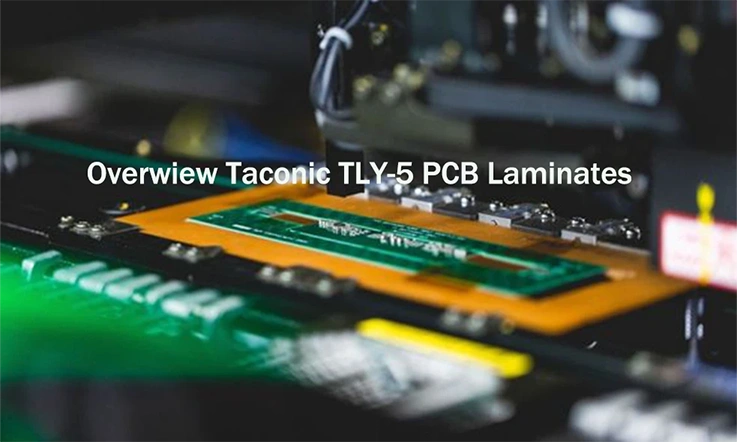
high-frequency PCB design demands precision, reliability, and materials that can handle the rigorous requirements of advanced applications. Enter Taconic TLY-5 PCB Laminates, a go-to choice for us striving for top-notch performance. These laminates have made waves for their low dielectric constant, superior thermal stability, and ability to meet the stringent needs of industries like aerospace, telecommunications, and medical technology.
This article delves into the comprehensive benefits, specifications, and practical applications of Taconic TLY-5, offering actionable insights to engineers and manufacturers. From understanding material properties to mastering design strategies and cost-effective production techniques, we provide an all-encompassing guide to help you harness the full potential of Taconic TLY-5 PCB laminates for your next-generation PCB projects.
The Science Behind Taconic TLY-5 PCB Laminates
When designing high-frequency PCBs, we need materials that won’t buckle under the pressure of high-speed signals and extreme conditions. Taconic TLY-5 PCB Laminates stand out because of their exceptional blend of performance and reliability. Let’s take a deep dive into what makes these laminates the preferred choice for applications ranging from telecommunications to medical devices. The science behind these laminates isn’t just about specs—it’s about crafting materials that perform flawlessly, even when your circuit design is pushed to its limits.
Taconic TLY-5 laminates are known for their consistent and robust properties, thanks to their PTFE (polytetrafluoroethylene) and fiberglass composition. But there’s more than meets the eye when it comes to how these materials are made and what makes them so reliable under pressure.
What Makes TLY-5 Unique?
The uniqueness of Taconic TLY-5 PCB Laminates lies in the advanced combination of PTFE and fiberglass, which is no run-of-the-mill material selection. The PTFE, often associated with its non-stick capabilities, is a robust polymer that offers superior dielectric properties. When you combine PTFE with fiberglass, you’re creating a laminate that has both low loss and high thermal stability. The laminate’s excellent performance at high frequencies is largely due to the material’s low dissipation factor, which ensures that minimal energy is lost during signal transmission.
●PTFE (Polytetrafluoroethylene): Known for its low dielectric constant and low dissipation factor, PTFE contributes to the laminate’s ability to minimize signal loss and heat generation, making it ideal for high-frequency signals. Its chemical inertness further ensures longevity and reliability, even in harsh environments.
●Fiberglass Reinforcement: The fiberglass offers mechanical strength and durability, ensuring the laminate retains its shape and performance over time. This combination creates a product that is not only highly conductive but also extremely resilient, maintaining structural integrity even in high-stress scenarios.
This composition delivers distinct advantages that meet the demands of challenging environments. For instance, PTFE’s superior dielectric properties contribute to the low dielectric constant and low signal loss across a wide range of frequencies. This makes it a go-to choice for RF applications where precision and low distortion are non-negotiable. Let’s unpack the details and see what sets it apart:
●Low Dielectric Constant (Dk): The dielectric constant of TLY-5 is around 2.2, which ensures stable signal propagation at high frequencies. This low Dk is essential when dealing with high-speed communication systems like 5G networks.
●Low Dissipation Factor (Df): When a signal travels through a PCB, some energy is inevitably lost due to resistance in the material. TLY-5 keeps this loss to a minimum, ensuring that your signal remains strong and clear across the entire PCB.
●Thermal Stability: The composition of TLY-5 offers superior heat resistance, making it an ideal choice for power-sensitive applications in aerospace or medical devices, where high performance must be maintained even under fluctuating temperatures.
Breaking Down the Specifications
Understanding Taconic TLY-5’s full potential requires a close look at its technical specifications. When evaluating PCB materials, designers typically refer to metrics such as dielectric constant, dissipation factor, and thermal conductivity. Let’s dive deeper into the numbers that make TLY-5 an industry-leading choice for high-frequency designs.
Here’s a breakdown of key metrics:
Specification | TLY-5 Value | Industry Standard (Rogers 5880) |
Dielectric Constant (Dk) | 2.2 | 2.33 |
Dissipation Factor (Df) | 0.0009 | 0.0009 |
Thermal Conductivity | 0.65 W/mK | 0.34 W/mK |
Flammability Rating | UL94-V0 | UL94-V0 |
Taconic TLY-5 outshines competitors like Rogers 5880, especially when it comes to dielectric constant and dissipation factor, ensuring that high-frequency signals travel more efficiently, with less distortion. The thermal conductivity of TLY-5 ensures that heat doesn’t become an issue, keeping your circuit boards from overheating and failing under stress.
These numbers aren’t just on paper—they translate directly into real-world performance. For example, when working on 5G communications, where data rates are sky-high and latency is a concern, these properties ensure that signals travel faster, more efficiently, and without the issues that can otherwise slow down communication.
Role in High-Frequency PCB Manufacturing
Taconic TLY-5 PCBs are specifically engineered to meet the demands of high-frequency circuit designs. In RF and microwave systems, achieving consistent signal performance and minimizing interference is a must. Thanks to its low dielectric constant and reduced dissipation factor, TLY-5 material ensures reliable operation across GHz frequencies.. TLY-5’s low dielectric constant and dissipation factor make it an ideal choice for applications requiring consistent performance in the GHz range, such as:
●Satellite Communication Systems: TLY-5 PCBs are ideal for maintaining signal integrity in satellite transponders and communication equipment.
●Radar Systems: Whether it’s automotive radar systems navigating complex road environments or defense radar applications demanding pinpoint accuracy, Taconic TLY-5’s low-loss properties ensure minimal signal degradation. This material excels in preserving signal clarity, which enhances detection performance and supports seamless operation across a wide range of frequencies.
●Microwave Filters and Amplifiers: In RF filters, amplifiers, and oscillators, Taconic TLY-5 shines by offering exceptional signal clarity and unmatched stability. These properties ensure that devices maintain peak performance, even when faced with challenging environments or demanding conditions. Whether tackling high-frequency ranges or dealing with extreme temperatures, TLY-5 proves to be a rock-solid choice for our PCB engineers striving for reliable and efficient designs.
The laminate’s high-performance capabilities make it particularly suited for precision-driven applications, where signal degradation can cause significant problems, such as system failure or reduced operational efficiency.
From Material to Masterpiece
The journey of Taconic TLY-5 PCB Laminates from raw material to finished product is a testament to precision engineering. While the material properties are impressive, the real magic happens when these materials are processed into high-performance PCBs. High-frequency circuits demand extreme precision, and the manufacturing process is just as important as the material itself.
When working with TLY-5 laminates, we need to focus on several elements:
1.Layer Construction: Designing multilayer PCBs using TLY-5 requires special care when stacking materials. We need to pay attention to the laminate’s thermal expansion and coefficient of thermal expansion (CTE) to ensure that the layers bond correctly and that the PCB can withstand stress over time. Failure to account for these factors can lead to cracks or delamination.
2.Drilling and Etching Precision: PTFE is a tricky material to work with, so drilling and etching processes need to be carried out with precision. Unlike traditional FR4 boards, Taconic TLY-5 requires specialized equipment to drill vias without damaging the surface or introducing defects. For example, laser drilling is often used for precise hole creation without causing material warping.
3.Bonding and Lamination: The combination of PTFE and fiberglass in Taconic TLY-5 requires specific bonding agents and careful control over lamination temperatures. Achieving the right pressure and temperature during the lamination process is necessary to ensure the material’s structure remains consistent and uniform. Any misstep in managing this process could cause the material to lose its performance characteristics, especially when operating in high-frequency conditions, leading to possible signal loss or degradation.If not handled correctly, the material may lose its high-frequency characteristics, leading to signal degradation.
Once processed, Taconic TLY-5 PCB Laminates are ready to be implemented in high-performance applications, such as 5G infrastructure, medical devices, and aerospace electronics, where performance and precision are non-negotiable.
How Many Types of Taconic TLY-5 PCB Laminates Are There?
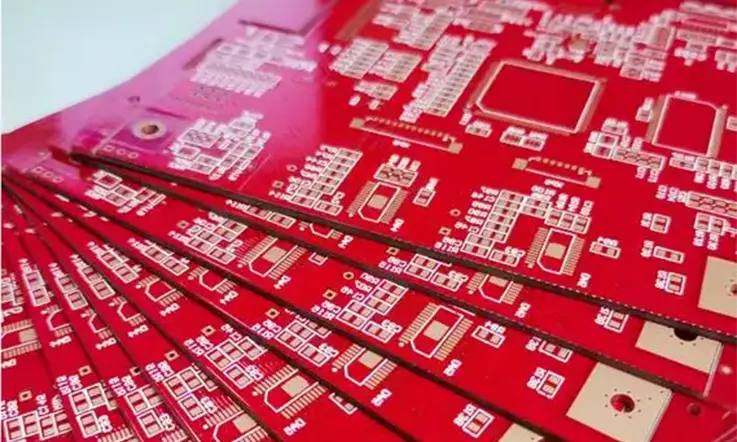
Taconic TLY-5 is widely recognized for its superior performance in high-frequency applications, especially in RF and microwave circuit designs. However, what might be less known is that Taconic offers multiple variations of TLY-5 laminates, each tailored to cater to different needs. Whether you’re developing radar systems, communication devices, or other advanced technology, these different variants allow you to choose the best fit for your specific project. This variety ensures that you can achieve the most reliable and efficient performance for your unique design requirements.
Let’s break down the different types of Taconic TLY-5 PCB laminates available, focusing on their unique characteristics and the best scenarios for each. Understanding these variations helps you make informed decisions and optimize your PCB designs for reliability, efficiency, and cost-effectiveness.
1. Standard Taconic TLY-5 Laminate
Taconic’s TLY-5 laminate stands out as the go-to material for a broad range of high-frequency applications, earning its reputation in industries like telecommunications, automotive radar, and aerospace. This standard TLY-5 variant offers remarkable dimensional stability and a low dissipation factor, ensuring minimal signal loss even at high frequencies. It also maintains a consistent dielectric constant, which helps preserve signal integrity in core systems. Whether you’re working on precision communications equipment or cutting-edge radar technology, TLY-5 offers the reliability and performance you need to keep things running smoothly.
Characteristics of Standard TLY-5:
●Dielectric Constant (DK): Typically around 2.2 to 2.5 at 10 GHz, offering great consistency in signal transmission.
●Dissipation Factor (DF): Low dissipation, typically around 0.0019, which minimizes signal loss and heat generation.
●Temperature Range: Typically operates effectively between -55°C and 130°C.
This standard version works beautifully in a wide range of RF and microwave applications, and its consistency makes it the perfect choice for many users starting with high-frequency PCB designs.
2. Taconic TLY-5D Laminate
The TLY-5D version of Taconic laminate is an upgraded variation specifically designed for applications where thermal stability is a top priority. It’s ideal for environments where temperature fluctuations are extreme, like in aerospace or automotive radar systems. The enhanced thermal performance of TLY-5D ensures that the material remains stable even under challenging conditions.
Key Features of TLY-5D:
●Thermal Stability: Performs exceptionally well at both high and low temperatures.
●Enhanced Dissipation Factor (DF): Offers slightly improved thermal properties, making it more suitable for high-power applications.
●Robust Mechanical Strength: Better suited for high-vibration environments.
If your project involves environments with significant thermal challenges, like power amplifiers or low-noise amplifiers (LNAs), TLY-5D ensures that your PCB remains operational without compromising performance.
3. Taconic TLY-5X Laminate
For applications requiring extremely low signal loss at ultra-high frequencies, Taconic’s TLY-5X laminate stands out as the top choice. This version excels in advanced telecommunications and phased array antennas, where handling high-frequency signals without distortion is a must. The TLY-5X is engineered to perform in demanding RF and microwave environments, offering unmatched reliability and performance. If you’re dealing with complex, high-stakes technology that demands peak performance, the TLY-5X laminate is the solution you need to ensure your systems operate with precision and efficiency.
Key Characteristics of TLY-5X:
●Ultra-Low Loss: Exceptional dielectric properties make it perfect for high-frequency circuits up to 40 GHz and beyond.
●Superior Signal Integrity: Enhanced stability at very high frequencies with ultra-low attenuation.
●Stable Dielectric Constant (DK): Extremely consistent dielectric constant across a wide frequency range.
If your project involves cutting-edge RF communication systems or high-precision radar technology, TLY-5X is the ideal choice for your design, providing performance that stands up to the toughest standards.
4. Taconic TLY-5B Laminate
The TLY-5B variant is specifically crafted for high-density interconnects and multi-layer designs. It offers superior peel strength and bonding capabilities, making it the right choice when your design requires excellent adhesion and structural integrity. The TLY-5B laminate is commonly used in high-performance automotive and avionics applications where reliability is non-negotiable.
Unique Attributes of TLY-5B:
●Enhanced Peel Strength: Ensures that your layers stay bonded under stress.
●Multi-Layer Bonding: Excellent bonding properties that help in high-density designs with multiple layers.
●Mechanical Durability: Withstands mechanical stresses while ensuring high-frequency performance.
TLY-5B is great when your application demands more robust structural integrity alongside performance, such as in complex aerospace systems.
5. Taconic TLY-5H Laminate
The TLY-5H laminate is engineered for high-speed digital and microwave applications, focusing on low signal loss to ensure reliable signal transmission. It excels in scenarios where a steady dielectric constant (DK) is required, such as in precision filters and phase shifters used in radar systems. If you need a material that can handle demanding RF designs while keeping your system performing at a high level with minimal interference, TLY-5H stands out as a top choice. Whether you’re working on high-frequency circuits or advanced timing setups, this laminate helps ensure your designs stay on track and deliver consistent results.
Highlights of TLY-5H:
●High-Speed Digital Performance: Ideal for circuits requiring high-speed signal processing.
●Consistency in High-Frequency Applications: Stable properties across a wide range of frequencies, ideal for precision instrumentation.
●Low Loss: Ensures minimal energy loss, even in the most demanding applications.
If your design focuses on high-speed digital systems and precision microwave applications, TLY-5H provides the stability and performance you need for a flawless signal.
Advantages of Taconic TLY-5 PCB Laminates
In the world of high-performance PCB design, materials can either make or break your project. Taconic TLY-5 PCB Laminates offer an unmatched combination of reliability, precision, and cost-effectiveness for applications requiring top-notch performance. Let’s explore their standout benefits, from maintaining pristine signal quality to thriving in demanding environments, and even saving you a buck or two along the way.
Unmatched Signal Integrity for High-Frequency Applications
When it comes to high-frequency designs, even the tiniest signal loss can throw a wrench in the works. Taconic TLY-5 PCB Laminates ensure that your signals stay strong and stable, thanks to their low dielectric loss and consistent electrical performance.
Imagine a telecommunications network that spans continents, relying on seamless RF communication between nodes. Even a fractional signal loss could compromise connectivity. TLY-5 laminates excel in these scenarios, whether in 5G base stations or satellite communication systems.
Here’s a comparison to highlight how Taconic TLY-5 stands up against its competitors:
Material | Dielectric Constant (Dk) | Dissipation Factor (Df) | Ideal Applications |
Taconic TLY-5 | 2.2 | 0.0009 | RF antennas, 5G networks |
Rogers RO5880 | 2.2 | 0.0009 | Microwave circuits, satellite systems |
Rogers RO4003C | 3.38 | 0.0021 | RF circuits, automotive radar |
Isola Astra MT77 | 3.00 | 0.0017 | Aerospace, satellite systems |
Panasonic R-5515 | 2.1 | 0.001 | Communication satellite, radar |
Arlon AD255C | 2.52 | 0.0013 | Microwave circuit, radio frequency amplifier |
Exceptional Thermal and Mechanical Reliability
Let’s face it: high-performance PCBs often operate in some pretty unforgiving conditions. Whether it’s the blistering heat of a jet engine compartment or the frigid vacuum of space, Taconic TLY-5 PCB Laminates are designed to hold their own. Their unique combination of PTFE and fiberglass ensures excellent thermal and mechanical durability, making them a reliable choice for aerospace and defense applications.
Here’s what sets them apart:
●High Thermal Conductivity: With a thermal conductivity of 0.65 W/mK, TLY-5 laminates dissipate heat effectively, preventing hotspots and maintaining performance even under heavy loads.
●Dimensional Stability: These laminates resist warping and maintain their integrity under varying temperatures, ensuring that multilayer designs remain perfectly aligned.
Cost-Effective Solutions for OEMs and Manufacturers
Balancing performance and cost is always a challenge, but Taconic TLY-5 PCB Laminates strike that balance beautifully. Their durability and consistent performance lead to reduced long-term maintenance and higher yields in production—saving money without cutting corners.
Here’s how TLY-5 helps manufacturers and OEMs keep costs in check:
1.Reduced Scrap Rates: The precision engineering behind TLY-5 ensures fewer defects during manufacturing, leading to less material waste.
2.Long Lifespan: With superior thermal and mechanical properties, these laminates deliver reliable performance over time, minimizing the need for replacements.
3.Streamlined Processing: TLY-5 laminates are compatible with a wide range of standard manufacturing processes, saving both time and resources.
So, we can Imagine a high-volume production line for IoT devices. Switching to TLY-5 could reduce your defect rates by 20%, leading to significant cost savings over time. Plus, the material’s resilience means fewer returns and happier customers.
Comparing Taconic TLY-5 PCB Laminates with Alternative Materials
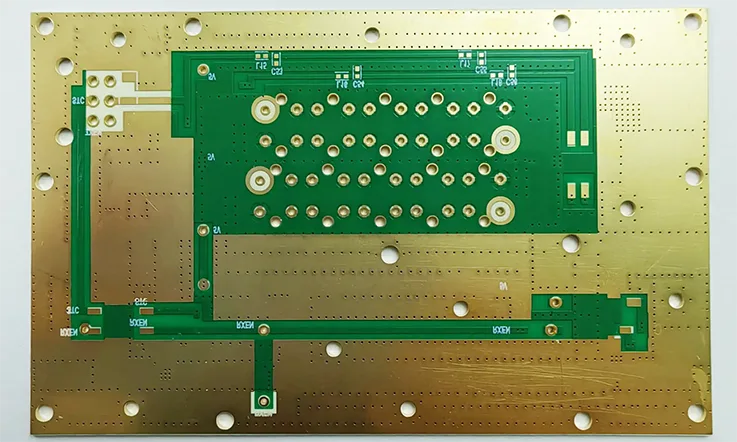
When designing high-frequency PCBs, selecting the right PCB substrate material is a make-or-break decision. Taconic TLY-5 laminates have carved out a solid reputation for their stellar performance in RF and microwave applications. However, they are not alone in the marketplace. Competitors like Rogers 5880 and standard FR4 laminates also vie for attention, each bringing unique traits to the table. Here, we’ll delve into a side-by-side comparison to help designers and OEMs make informed choices.
TLY-5 vs. Rogers 5880
Both Taconic TLY-5 and Rogers 5880 are preferred choices for high-frequency applications, but their subtle differences cater to varying design priorities.
1.Dielectric Properties-
TLY-5 boasts a dielectric constant (Dk) of ~2.2, offering outstanding stability across a wide frequency range. In contrast, Rogers 5880 features an ultra-low Dk of ~2.1, making it slightly better suited for certain microwave and radar designs.
Comparison Table:
Property | Taconic TLY-5 | Rogers 5880 |
Dielectric Constant | ~2.2 | ~2.1 |
Loss Tangent | 0.0009 | 0.0009 |
Thermal Conductivity | ~0.25 W/m·K | ~0.20 W/m·K |
Cost Efficiency | Moderate | High |
2.Mechanical Strength-
TLY-5 is reinforced with PTFE fiberglass, giving it superior mechanical stability. we handling rigorous applications, such as military systems, often lean toward TLY-5 for its robustness under extreme conditions.
3.Ease of Processing-
Both laminates demand precision during fabrication due to their PTFE base, but Taconic TLY-5’s slightly higher thermal conductivity simplifies heat management during drilling and plating processes.
Takeaway: Whether you choose TLY-5 or Rogers 5880 depends on your project’s unique demands. For rugged applications, TLY-5 is a trusted ally, while Rogers 5880 may edge ahead for ultra-high-frequency systems.
Advantages Over Standard FR4 Laminates
FR4 laminates are the workhorses of the PCB world, but when frequencies rise above a few GHz, their limitations start showing. Taconic TLY-5 offers a lifeline for us looking to push boundaries.
1.Dielectric Loss and Signal Integrity-
FR4’s high dielectric loss leads to substantial signal attenuation, making it unsuitable for high-frequency designs. TLY-5, with a loss tangent of just 0.0009, ensures that signals maintain their strength over long transmission paths.
2.Thermal Performance-
FR4 materials can struggle with heat dissipation, especially in densely populated PCBs. TLY-5’s improved thermal properties allow it to perform reliably in applications like phased-array antennas and 5G base stations.
3.Application Examples-
Example 1: A telecommunications firm designing a 5G transmitter faced significant signal degradation with FR4. Switching to TLY-5 reduced signal losses by 60%, leading to a noticeable improvement in overall system performance.
Example 2: In an aerospace navigation system, TLY-5’s stability across temperature fluctuations provided the consistent performance FR4 couldn’t deliver, ensuring uninterrupted operation.
Cost vs. Performance Analysis for OEMs
For OEMs and manufacturers, balancing performance and cost is always a juggling act. Taconic TLY-5 laminates provide an attractive combination of high performance and manageable costs, particularly for RF and microwave designs.
1.Material Costs-
While TLY-5 laminates come at a premium compared to FR4, they are often more economical than Rogers 5880 for similar performance metrics. This cost advantage can make TLY-5 the material of choice for mid-to-high-end RF designs.
2.Longevity and ROI-
TLY-5’s durability means fewer replacements and less maintenance, providing great long-term value for high-stakes applications. Its reliable performance translates into reduced operational costs over time.
3.Value Proposition for OEMs-
Metric | Taconic TLY-5 | Standard FR4 | Rogers 5880 |
Upfront Cost | Moderate | Low | High |
Frequency Performance | Excellent | Limited | Excellent |
Durability | High | Moderate | Moderate |
Processing Ease | Moderate | Easy | Moderate |
How to Design High-Performance PCBs Using Taconic TLY-5 PCB Laminates?
Designing high-frequency PCBs is a nuanced process that requires not only top-tier materials like Taconic TLY-5 but also precise techniques to extract the maximum potential from their unique properties. TLY-5 laminates are engineered for exceptional performance in RF and microwave applications, but achieving optimal results requires a deep understanding of impedance control, stack-up configuration, and thermal management. Below, we’ll dive into advanced strategies and methodologies tailored for professionals in telecommunications, aerospace, and high-tech industries.
Impedance Control Techniques
Impedance control is at the heart of high-frequency PCB design, especially when working with RF signals that demand consistent transmission characteristics. Taconic TLY-5 laminates, with their stable dielectric properties and low loss tangent, provide the perfect canvas for achieving precise impedance.
1.Understanding the Basics of Impedance Control-
Impedance is the opposition that a transmission line offers to signal flow. It’s influenced by the trace width, spacing, and the dielectric constant (Dk) of the substrate. With TLY-5’s Dk of ~2.2, designers can achieve predictable impedance levels, minimizing signal distortion.
Key Equations:
2.Advanced Techniques for TLY-5 Laminates-
●Controlled Trace Dimensions: High-frequency circuits are highly sensitive to small variations in trace width and spacing. Laser etching ensures the accuracy and consistency needed for TLY-5-based designs.
●Ground Plane Proximity: Closer placement of ground planes to signal traces reduces impedance variability. This is especially useful for multi-layer PCBs.
3.Validation Through Simulation and Testing-
Tools like Ansys HFSS, CST Studio Suite, and ADS provide accurate modeling of TLY-5’s performance under various configurations. Physical testing with a time-domain reflectometer (TDR) confirms that real-world designs align with theoretical models.
Tip: Incorporate test coupons into your PCB to validate impedance during the manufacturing process.
Best Practices for PCB Stack-Up Design
Layered PCB designs benefit significantly from a well-thought-out stack-up configuration, particularly when Taconic TLY-5 laminates are involved. The stack-up determines the electrical and thermal behavior of the PCB, directly impacting signal integrity, noise isolation, and thermal management.
1.Material Selection and Layer Arrangement-
In a multi-layer design, TLY-5 laminates should be used for high-speed signal layers, with lower-frequency signals routed on standard FR-4 substrates to optimize cost without sacrificing performance.
Example Stack-Up Design:
Layer | Material | Purpose |
Signal Layer 1 | TLY-5 | High-speed RF signals |
Ground Plane | Copper | Signal isolation |
Signal Layer 2 | TLY-5 | Secondary RF routing |
Power Plane | FR-4 | Power distribution |
2.Signal Isolation Strategies-
●Introduce dedicated ground planes to act as shields between signal layers.
●Use differential signaling to mitigate the effects of crosstalk.
3.Matching Impedance Across Layers-
By ensuring impedance uniformity between layers, you prevent reflections and maintain signal quality. Advanced simulation software can assist in verifying layer-to-layer compatibility.
Thermal Management in High-Frequency Applications
Heat can quietly undermine performance in high-frequency applications.. While Taconic TLY-5 laminates are designed to handle thermal stress, improper management can compromise their longevity and functionality.
1.Understanding Thermal Properties-
TLY-5 laminates have a low coefficient of thermal expansion (CTE), making them resistant to mechanical stress caused by temperature fluctuations. However, their inherent low thermal conductivity (~0.25 W/m·K) requires external heat dissipation measures.
2.Effective Heat Dissipation Techniques-
●Thermal Vias: Place copper-plated vias directly beneath heat-generating components to transfer heat to a heat sink or ground plane.
●Integrated Heat Spreaders: Use metal cores or thermal pads for applications involving power amplifiers or high-energy RF circuits.
●Active Cooling Systems: In scenarios like satellite or aerospace systems, consider pairing TLY-5 PCBs with heat sinks or liquid cooling systems for sustained operation.
Case Study:
A defense contractor designing a radar system faced overheating issues. By introducing thermal vias and a copper heat spreader to their Taconic TLY-5 design, they reduced operating temperatures by 20%, ensuring reliable performance under extreme conditions.
3.Simulation and Testing-
Thermal analysis tools such as COMSOL Multiphysics and SolidWorks Simulation can model heat flow and identify potential hotspots, enabling preemptive design corrections.
Challenges and Solutions in Manufacturing PCB with Taconic TLY-5 Laminates
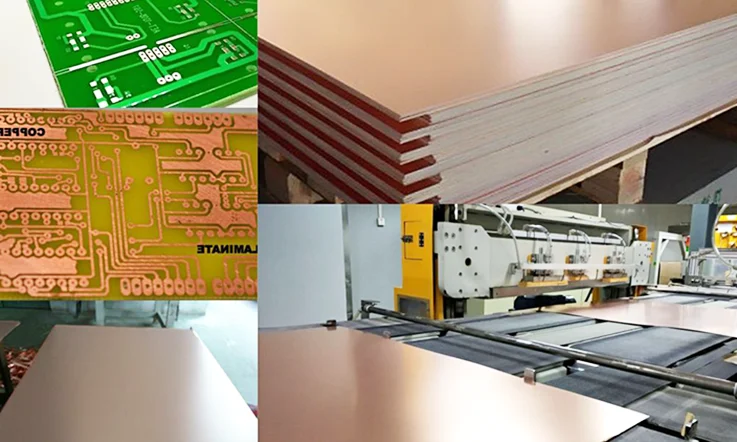
Manufacturing PCBs with Taconic TLY-5 laminates demands precision and care. These advanced materials offer several unique benefits, but their PTFE makeup and performance traits require a thoughtful approach. For manufacturers and designers looking to make the most of TLY-5, being aware of potential challenges and navigating them effectively can ensure a smooth production process. Below, we outline common difficulties and practical solutions for working with this high-performance laminate.
PTFE Processing Challenges
Polytetrafluoroethylene (PTFE), the primary component in Taconic TLY-5 laminates, offers outstanding electrical properties but can be challenging to process due to its non-reactive and soft nature.
1.Material Handling-
PTFE’s low surface energy makes it resistant to adhesives, complicating bonding processes. PCB Manufacturers must utilize specialized surface treatments like plasma etching or sodium etching to enhance adhesion properties before multilayer lamination.
2.Thermal Expansion-
Compared to traditional FR4 materials, PTFE laminates like TLY-5 exhibit higher thermal expansion coefficients. This can cause misalignment during high-temperature processes, such as reflow soldering. To mitigate this, employing low-stress mechanical fixturing and gradual temperature ramps during manufacturing can help maintain alignment.
3.Fabrication Tips-
●Use sharp, carbide-tipped tools for clean cuts without delamination.
●Minimize tool vibrations to prevent micro-fractures.
Example: A manufacturer transitioning from FR4 to TLY-5 for an aerospace application faced bonding failures during initial trials. By integrating sodium-etched PTFE sheets into their workflow, they achieved a 30% improvement in yield rates.
Precision Drilling and Bonding Techniques
Creating precise vias and strong layer bonds is a must for ensuring the long-term performance and reliability of Taconic TLY-5-based PCBs, particularly in demanding high-frequency applications. Achieving this requires attention to detail, as these designs need to withstand the stresses of high-speed signals. Getting the vias right and making sure the layers are securely bonded are fundamental steps in making sure everything stays on track.
1.Drilling-
●PTFE’s softness can lead to burrs and smear during drilling. To combat this, we often freeze the material before drilling, increasing its rigidity temporarily.
●Incorporating entry and backer materials during drilling reduces drill wander and ensures consistent hole diameters.
Drill Speed and Feed Rate Recommendations:
Drill Bit Size | Speed (RPM) | Feed Rate (Inches/Minute) |
≤0.5 mm | 80,000 | 3.0 |
>0.5 mm | 60,000 | 2.5 |
2.Bonding Techniques-
TLY-5 laminates require specialized bonding films to ensure multilayer PCB stability. Thermoplastic films with low dielectric loss are ideal for maintaining electrical integrity.
3.Surface Preparation-
Thorough cleaning and roughening of copper surfaces before lamination can significantly improve bond strength.
Partnering with Experienced PCB Fabricators
When dealing with complex materials like Taconic TLY-5, expertise is everything. Partnering with fabricators (JarnisTech) experienced in high-frequency PCB manufacturing ensures efficient production while avoiding costly mistakes.
1.Proven Track Records-
PCB Manufacturer (JarnisTech) familiar with TLY-5’s unique properties understand how to optimize drilling, bonding, and finishing processes. Our hands-on experience can save months of trial and error for OEMs.
2.Advanced Equipment-
State-of-the-art equipment, such as laser direct imaging (LDI) systems and automated bonding stations, ensures precise manufacturing with minimal variation.
3.Collaborative Design Reviews-
Engaging fabricators (JarnisTech) early in the design phase allows for collaborative problem-solving, ensuring manufacturability without sacrificing performance.
Why Choose JarnisTech Fabrication for Taconic TLY-5 PCB Circuit Boards?
When it comes to advanced PCB manufacturing, the material and expertise behind the product make all the difference. At JarnisTech, we specialize in fabricating Taconic TLY-5 PCB circuit boards, renowned for their exceptional performance in high-frequency and high-reliability applications. Our tailored manufacturing processes and cutting-edge technology ensure that your designs meet the most demanding industry standards.
With properties like superior dimensional stability, minimal dissipation factor (DF), consistent dielectric constant (DK), and high peel strength, Taconic TLY-5 PCBs shine in applications where precision and durability are non-negotiable. Whether you’re designing for aerospace, telecommunications, or automotive systems, our TLY-5 circuit boards deliver unmatched results.
Why Partner with JarnisTech?
At JarnisTech, we take pride in being a leading PCB manufacturer in China, with a proven track record in fabricating Taconic TLY-5 PCB circuit boards. Here’s what sets us apart:
1.Precision Manufacturing-
●Advanced processing techniques tailored for PTFE-based laminates.
●High-precision laser drilling and etching capabilities.
2.Rigorous Quality Assurance-
●In-depth testing, including impedance control and thermal reliability.
●ISO-certified processes to ensure consistent quality in every batch.
3.Customization Options-
●Support for multilayer designs and unique configurations.
●Expertise in integrating TLY-5 materials into complex, high-frequency PCBs.
Expert Recommendations for Using Taconic TLY-5 PCB Laminates
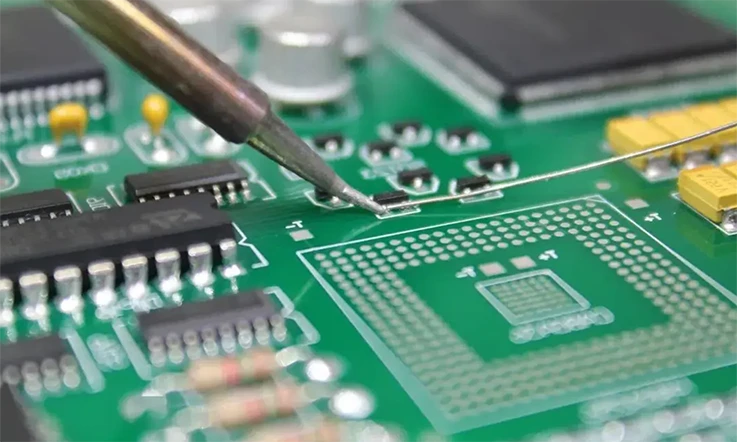
Taconic TLY-5 PCB laminates are revered for their ability to deliver top-notch performance in high-frequency applications. However, achieving consistent results requires an understanding of their specific properties and adopting tailored manufacturing practices. Below, we present expert guidance to help engineers, manufacturers, and designers optimize their use of TLY-5 materials. Whether you’re navigating RF circuit design or ensuring quality in production, these insights will empower you to achieve exceptional outcomes.
Ensuring Optimal Signal Integrity in RF Circuits
High-frequency circuit design demands precision to maintain signal clarity and minimize losses. Taconic TLY-5 laminates offer a low dielectric constant and minimal loss tangent, making them ideal for RF circuits. Here’s how to maximize their potential:
1.Accurate Impedance Matching-
Impedance mismatches can result in signal reflection and degradation. We should calculate and match the impedance of transmission lines and terminations. Utilizing high-frequency simulation tools, such as Ansys HFSS or Keysight ADS, ensures accurate designs tailored to TLY-5’s properties.
Therefore, Proper impedance matching minimizes signal reflection and loss, ensuring efficient energy transfer. Use precise simulation tools to calculate trace widths and spacing based on the dielectric constant (DK) of TLY-5 laminates. For example, a controlled 50-ohm impedance trace can be achieved by carefully adjusting the PCB’s trace width and height relative to the substrate thickness.
Parameter | Example Value |
Dielectric Constant (DK) | 2.20 (TLY-5 Standard) |
Trace Width | 0.35 mm (adjustable) |
Substrate Thickness | 1.6 mm (varies by layer count) |
2.Consistent Trace Widths and Spacings-
Maintaining consistent trace widths and spacings is a must when working with TLY-5, thanks to its stable dielectric properties. Any variations in these aspects can lead to unwanted parasitic effects, which can mess with your signals, especially in circuits running at GHz frequencies. Getting the dimensions just right ensures that the performance stays sharp and free from interference, giving your design a solid shot at long-term reliability. Think of it like keeping your car tuned—every little bit matters to keep things running like a well-oiled machine.
3.Controlled Environments-
Environmental factors, such as humidity and temperature, can influence the dielectric performance of laminates. For RF circuits, manufacturing in clean, temperature-controlled environments is recommended to maintain material integrity.
Example Case: A satellite communication project utilizing TLY-5 achieved a 25% increase in signal-to-noise ratio after fine-tuning the PCB layout for impedance control and adopting microstrip line structures tailored to the material’s dielectric properties.
Testing and Quality Assurance Best Practices
When it comes to high-frequency PCBs used in industries like aerospace, telecommunications, or medical devices, consistency in performance is a must. Any deviation in quality could spell trouble down the line. To ensure reliability across production batches, you need to implement strict testing and quality control protocols. Think of it as a pre-flight check—every part has to meet the highest standards before takeoff. With this approach, you’re not just getting a piece that works, you’re getting one that’s built to last, no matter the conditions.
1.Electrical Testing-
●Perform time-domain reflectometry (TDR) to verify impedance continuity in transmission lines.
●Conduct high-frequency S-parameter measurements to evaluate insertion loss and return loss performance.
2.Thermal Cycling Tests-
TLY-5 laminates must endure temperature fluctuations without delaminating or experiencing dielectric degradation. Testing for thermal shock and cycling simulates real-world conditions and ensures durability.
3.Layer Registration Accuracy-
Multilayer PCBs require perfect layer alignment to avoid impedance mismatches or signal distortion. Advanced automated optical inspection (AOI) systems should be employed to detect misalignments down to a micron level.
Pro Tip: Establish a production baseline by fabricating a small batch for testing before moving to full-scale production. Analyze the results to fine-tune manufacturing parameters and prevent costly rework later.
FAQs About Taconic TLY-5 PCB Laminates
Are Taconic TLY-5 laminates compatible with standard PCB manufacturing processes?
Yes, but specialized techniques for drilling, bonding, and processing PTFE materials are recommended for optimal results.
What are the available thickness options for Taconic TLY-5 laminates?
Taconic TLY-5 comes in a variety of thicknesses, allowing customization for specific design requirements.
Can Taconic TLY-5 laminates handle extreme environmental conditions?
Yes, they exhibit excellent thermal stability and low moisture absorption, making them reliable in harsh environments.
What surface treatments are required for Taconic TLY-5 laminates?
Surface roughening or plasma treatment may be necessary to ensure strong bonding during the PCB fabrication process.