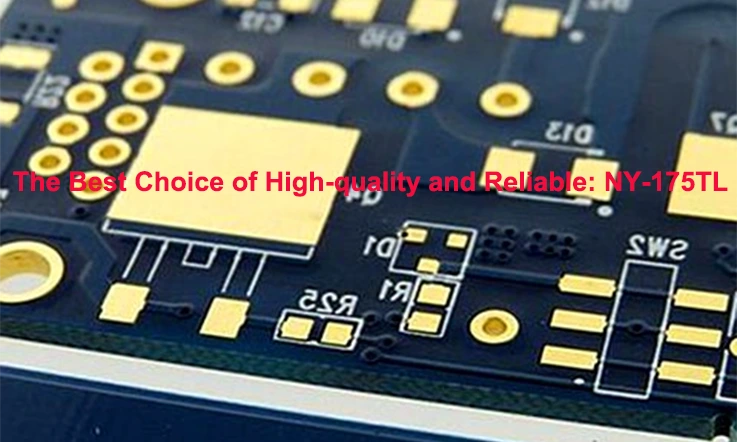
NanYa 175TL PCB materials are a high-quality and reliable choice for circuit board manufacturers. These materials offer exceptional thermal resistance, electrical insulation, flame retardancy, mechanical strength, chemical resistance, low water absorption, and excellent processability. With their superior properties, NanYa 175TL materials provide the necessary foundation for the production of robust and high-performance PCBs.
Therefore, In the ever-evolving electronics industry, finding materials that balance performance, reliability, and cost is like striking gold. NanYa 175TL PCB materials have earned their spot as a go-to choice for creating advanced circuit boards, delivering consistent results across a range of high-performance applications. Whether you’re building for aerospace systems, medical equipment, or 5G devices, this material stands tall in the crowd. Let’s break it all down and uncover what makes NanYa 175TL a true contender for your next big project.
The Evolution of NanYa 175TL PCB Materials
The journey of NanYa 175TL PCB materials begins with the persistent challenges PCB manufacturers faced in creating circuit boards that could handle the demands of modern electronics. As technology evolved, the need for materials that could handle higher temperatures, greater electrical loads, and more complex designs became more urgent. NanYa, with its forward-thinking approach, recognized these gaps in the market and set out to create a material that could not only meet but exceed the expectations of engineers across the globe.
How It All Started?
In the past, PCB manufacturers were stuck between a rock and a hard place. They were trying to craft materials that were durable enough for high-performance devices, but the options available just didn’t hit the mark. Materials lacked thermal stability, they didn’t support high-speed signals well, and they didn’t age well under stress. When these issues piled up, manufacturers were forced to settle for lower performance or pay the price with costly failures.
This is where NanYa’s story takes a turn. Their research and development team were driven by the idea that a better material was possible. Instead of simply following industry trends, NanYa set out to break through limitations and create a material that could adapt to the evolving needs of electronics. The development of NanYa 175TL was the answer. By optimizing its resin systems and selecting the best glass fiber reinforcements, NanYa 175TL was born—a material capable of withstanding the extreme conditions found in high-performance applications.
This innovation was more than just a theoretical breakthrough. It delivered real-world benefits that quickly garnered attention from engineers and manufacturers alike. NanYa 175TL offered exceptional dimensional stability, impressive thermal resistance, and a solid electrical performance profile, enabling it to support the next generation of technologies.
The Science Behind the Material
Understanding what makes NanYa 175TL stand out requires a look under the hood—specifically, the carefully selected materials that go into creating it. The resin system used in NanYa 175TL is optimized for high thermal resistance, which allows the material to maintain its structural integrity even under high thermal stress. This makes it a strong contender for high-temperature applications, such as automotive, aerospace, and power electronics.
But that’s not all. The material’s glass fabric reinforcement enhances its mechanical strength, providing robust durability to withstand the stresses encountered during the manufacturing process. Whether it’s high-frequency signals or extreme temperatures, NanYa 175TL doesn’t just hold its own—it performs at a higher level.
For engineers working on multilayer designs or high-speed circuits, NanYa 175TL is an invaluable material. Its low dielectric loss ensures that signals maintain their integrity, even at high speeds. This makes it the material of choice for industries like telecommunications, where minimizing signal degradation is essential.
Here’s a quick comparison of some properties:
Property | NanYa 175TL | Other PCB Materials |
Glass Transition Temp (Tg) | 170°C | 140°C |
Dielectric Constant (Dk) | 3.20 | 3.50–4.00 |
Thermal Decomposition Temp (Td) | 350°C | 280°C–320°C |
Coefficient of Thermal Expansion (CTE) | 15ppm/°C | 25ppm/°C |
This table shows how NanYa 175TL stacks up against typical PCB materials, and why it’s a preferred choice for high-end applications requiring durability, precision, and reliability.
Why Engineers and Designers Trust It?
For us, reliability is everything. NanYa 175TL doesn’t just talk the talk; it walks the walk. PCB design is already a complex and challenging process. The last thing any human wants is to deal with material failures that throw a wrench in the works. With NanYa 175TL, that worry is a thing of the past.
Consider a case where a our designer is tasked with creating a circuit board for an electric vehicle (EV). The board must handle high power levels, operate in varying temperatures, and endure constant vibration. With traditional materials, we might encounter issues like delamination or signal distortion due to heat exposure or physical stress. With NanYa 175TL, these problems are minimized, allowing the design process to flow smoothly without the constant fear of material failure.
NanYa 175TL’s excellent thermal stability means that the material can handle the wide range of temperatures an EV might experience, from frigid winters to scorching summers. Its ability to maintain its mechanical integrity even under vibration ensures that the board performs reliably over the long term.
Comprehensive Overview of NanYa 175TL PCB Materials
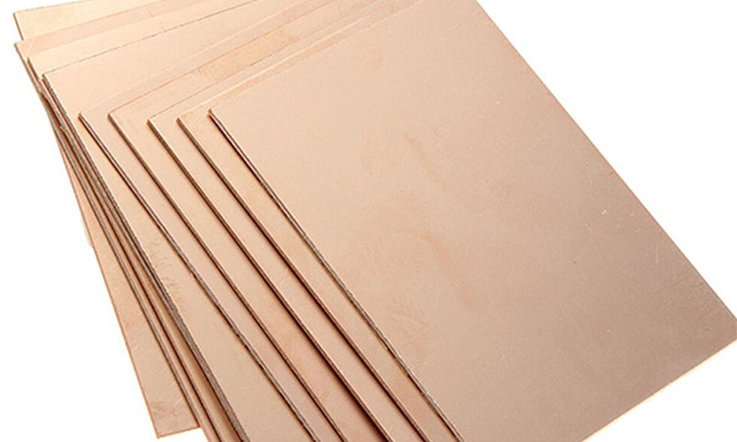
When diving into high-performance PCB designs, selecting the right material is non-negotiable. NanYa 175TL PCB materials offer solutions tailored for industries that demand reliability, efficiency, and innovation. This section explores its unique characteristics, advantages for us, and its established reputation in the electronics sector.
Unique Characteristics of NanYa 175TL PCB Materials
NanYa 175TL is a standout in the PCB material market, specifically engineered to address common challenges like heat management, signal interference, and manufacturing complexity. Below, we delve into its properties that set it apart.
High Thermal Resistance and Durability-
In today’s high-demand industries like automotive, telecommunications, and industrial machinery, maintaining reliable thermal performance is a must. NanYa 175TL is built to handle the heat with a glass transition temperature (Tg) of 175°C, making it a solid performer even in the harshest environments. It’s not just about heat—this material is tough through and through, with the mechanical strength to endure vibrations and thermal cycling, ensuring it keeps going strong over time.
Thermal and Mechanical Properties of NanYa 175TL-
Property | NanYa 175TL | Industry Average |
Glass Transition Temp (Tg) | 175°C | 135–150°C |
Thermal Expansion (Z-Axis) | ≤3.0% | 5–6% |
Peel Strength | ≥1.5 N/mm | 1.0 N/mm |
With these attributes, we can confidently employ NanYa 175TL in high-temperature or multilayer applications without concerns over warping or delamination.
Advanced Electrical Insulation Properties-
Effective electrical performance is essential for applications like 5G, IoT devices, and high-speed computing. NanYa 175TL’s low dielectric constant (Dk = ~4.2) and dissipation factor (Df ≤ 0.018) ensure minimal signal loss, even at higher frequencies.
Electrical Properties of NanYa 175TL-
Parameter | NanYa 175TL | Ideal Range for High-Speed Applications |
Dielectric Constant | ~4.2 | 3.8–4.5 |
Dissipation Factor | ≤0.018 | ≤0.02 |
Volume Resistivity | ≥1×10⁸ Ω·cm | ≥1×10⁷ Ω·cm |
This combination of properties reduces signal degradation and enhances circuit reliability, making it ideal for industries where performance consistency is a must.
Flame-Retardant Compliance with IPC Standards-
For applications requiring compliance with safety and fire-resistance standards, NanYa 175TL exceeds expectations. It meets UL94 V-0 standards and IPC-4101/99, ensuring it’s ready for use in applications like medical devices and industrial machinery.
Key Advantages of NanYa 175TL PCB Materials for Manufacturers
NanYa 175TL offers features that simplify manufacturing and enhance product reliability. Below, we explore its benefits for production and its adaptability to cutting-edge technologies.
Enhanced Dimensional Stability for Complex Designs-
In multilayer PCB designs, precision is a must. Even the slightest misalignment can lead to performance issues. NanYa 175TL excels in this area with its low coefficient of thermal expansion (CTE), ensuring that each layer maintains alignment, even in designs with tight tolerances. Thanks to this high dimensional stability, you can count on consistent performance without the worry of misaligned layers.
Dimensional Stability Comparison-
Material | CTE (Z-Axis) | Application Layer Count |
NanYa 175TL | ≤50 ppm/°C | 12–20 |
Standard FR4 | ~70 ppm/°C | 6–10 |
This allows us to create complex boards, such as those used in server systems and 5G base stations, with reduced risk of defects.
Cost-Effective Solutions for High-Volume Production-
For high-volume production, minimizing waste and optimizing processes is essential. NanYa 175TL’s compatibility with advanced manufacturing techniques, such as laser drilling and automated lamination, streamlines production and reduces costs.
For example, a telecommunications company reduced material waste by 18% when switching to NanYa 175TL, cutting down on rework and enhancing production efficiency.
Compatibility with Advanced Fabrication Techniques-
NanYa 175TL’s properties make it an excellent choice for innovative fabrication methods. Its thermal stability prevents delamination during high-temperature soldering processes, and its mechanical resilience ensures microvias remain intact during laser drilling.
Industry Recognition of NanYa 175TL PCB Materials
Widely Used in High-Reliability Industries-
NanYa 175TL has become a preferred choice in demanding industries like aerospace, telecommunications, and medical devices. These fields often require materials that can maintain performance under challenging conditions.
For example, in automotive applications, PCBs made with NanYa 175TL successfully passed rigorous vibration and temperature cycling tests, demonstrating long-term reliability.
Certified to Meet Stringent International Standards-
Manufacturers seeking global compliance can rely on NanYa 175TL’s certifications, including UL, IPC, and ISO standards. These credentials make it easier to achieve regulatory approval for products in multiple markets.
Certifications Achieved by NanYa 175TL-
Certification Body | Standard | Application |
UL | UL94 V-0 | Flame retardancy |
IPC | IPC-4101/99 | High-performance laminates |
ISO | ISO 9001 | Quality management systems |
Trusted by Leading Global Electronics Brands-
Top-tier brands in telecommunications, computing, and consumer electronics frequently specify NanYa 175TL for its proven performance. Its widespread adoption is a testament to its reliability in both prototyping and mass production.
Thermal and Electrical Performance of NanYa 175TL PCB Materials
In the world of modern electronics, managing thermal and electrical performance is a major factor in the success of a design. Whether it’s dealing with heat in high-power systems or ensuring clear signals in complex, high-frequency layouts, the choice of PCB materials can make a significant difference. NanYa 175TL offers reliable performance in demanding environments, maintaining stability even under extreme conditions. This section will explore the material’s thermal and electrical properties, with practical examples and data, to illustrate why NanYa 175TL is a solid option for a variety of applications.
Thermal Properties Supporting High-Performance Electronics
Managing thermal challenges is no easy feat, especially in industries like telecommunications, automotive, and aerospace. NanYa 175TL tackles these hurdles with a carefully engineered material composition that prioritizes thermal stability and heat management.
Superior Glass Transition Temperature (Tg)-
With a Tg of 175°C, NanYa 175TL maintains structural integrity even in high-temperature environments. This property ensures that the PCB layers remain well-bonded, reducing the risk of warping or delamination during soldering or operation.
Comparison of Glass Transition Temperatures (Tg)-
PCB Material | Tg (°C) | Recommended Application |
NanYa 175TL | 175 | High-temperature, multilayer designs |
Standard FR4 | 135–150 | General-purpose PCBs |
High-Performance FR4 | 170–180 | High-reliability applications |
Thermal Decomposition Temperature (Td) for Extreme Conditions-
NanYa 175TL boasts a Td exceeding 350°C, making it suitable for applications exposed to extreme thermal cycling or high-power dissipation. This property ensures that the material doesn’t degrade, even in rigorous conditions such as in automotive powertrain systems or 5G base stations.
Effective Heat Dissipation for Optimized Reliability-
Efficient heat dissipation isn’t just about preventing overheating—it’s about safeguarding the lifespan of components. NanYa 175TL’s low thermal resistance aids in managing heat, even in compact designs with densely packed components.
Electrical Performance in Advanced PCB Designs
In high-frequency and high-speed applications, electrical performance is a must. NanYa 175TL provides outstanding results, tackling the demands of advanced technology with ease. It’s designed to handle the complexities of modern systems, ensuring clear signals and minimal interference, even when pushed to the limits. Whether you’re working on telecommunications, automotive, or industrial designs, NanYa 175TL stands out for its ability to maintain consistent performance, no matter how tough the conditions get.
High Dielectric Constant and Low Dissipation Factor-
With a dielectric constant (Dk) of ~4.2 and a dissipation factor (Df) of ≤0.018, NanYa 175TL minimizes signal loss and ensures reliable data transmission across high-speed networks and high-frequency circuits.
Electrical Characteristics of NanYa 175TL-
Parameter | Value | Impact |
Dielectric Constant | ~4.2 | Signal clarity in high-frequency designs |
Dissipation Factor | ≤0.018 | Reduced signal attenuation |
Volume Resistivity | ≥1×10⁸ Ω·cm | Improved insulation for dense circuitry |
Enhanced Signal Integrity for High-Frequency Applications-
High-speed designs, like those in 5G infrastructure and advanced computing, require materials that can handle signal integrity challenges. NanYa 175TL’s consistent Dk and Df values reduce signal skew, allowing for faster, more accurate data transfer.
Minimizing Crosstalk in Densely Packed PCBs-
In tightly packed multilayer PCB designs, managing crosstalk can be a real challenge. NanYa 175TL helps maintain signal clarity by reducing interference between traces, ensuring that your designs perform as expected. This material is engineered to preserve signal integrity, even in complex layouts, so your devices keep running at their best. Whether you’re working on high-speed circuits or high-density boards, NanYa 175TL keeps things crisp and clean, helping you avoid performance hiccups.
Stability Under Mechanical and Thermal Stress
PCB materials must endure mechanical and thermal challenges without compromising performance. NanYa 175TL is specifically designed to withstand demanding conditions, making it a trusted choice for us.
Exceptional Dimensional Stability Under High Temperatures-
NanYa 175TL’s low coefficient of thermal expansion (CTE) ensures that PCBs stay true to their dimensions, even through the heat of soldering and during operational cycles. This stability is especially valuable for multilayer boards, where slight misalignments between layers can lead to performance issues. Thanks to NanYa 175TL, your designs remain well-aligned, reducing the risk of signal loss or failures over time.
Dimensional Stability Metrics-
Material | CTE (Z-Axis) | Recommended Use Case |
NanYa 175TL | ≤50 ppm/°C | Multilayer and high-density PCBs |
General FR4 | ~70 ppm/°C | Standard consumer electronics |
Resistance to Thermal Cycling and Mechanical Stress-
NanYa 175TL is built to endure repeated thermal cycling, making it suitable for automotive applications that experience frequent temperature changes. Additionally, its mechanical resilience prevents cracks or delamination under physical stress, ensuring long-term reliability.
Long-Term Reliability in Demanding Applications-
From aerospace systems to industrial automation, applications that demand longevity rely on materials like NanYa 175TL. Its resistance to environmental factors, combined with superior thermal and electrical properties, guarantees consistent performance.
Consider Factors Use NanYa 175TL in PCB Fabrication

Choosing the right PCB material is a multi-faceted decision that goes beyond just technical performance. For PCB Manufacturer and designers, factors like production efficiency, procurement timelines, material quality, and overall cost-effectiveness play a huge role in driving project success. NanYa 175TL PCB materials strike a balance across all these aspects, making them a dependable choice for high-performance electronics. Let’s break it down.
Production Techniques Streamlined with NanYa 175TL
We are always looking for materials that don’t just perform well but also integrate smoothly into production processes. NanYa 175TL is designed to reduce processing headaches and improve throughput efficiency.
Compatibility with High-Density Interconnects (HDIs)-
NanYa 175TL supports modern HDI technologies, offering excellent layer adhesion during lamination and consistent performance in processes like laser drilling and electroplating. Its mechanical stability means fewer production hiccups, especially in multilayer designs.
Thermal and Chemical Resilience in Fabrication-
During high-temperature soldering or exposure to chemicals in etching and cleaning processes, materials can degrade or warp. NanYa 175TL holds up under these conditions, reducing rework and material waste.
Fabrication Yield Rates with NanYa 175TL-
Process Step | Yield Rate (NanYa 175TL) | Yield Rate (Standard FR4) |
Lamination | 98% | 92% |
Microvia Drilling | 97% | 90% |
Solder Reflow | 96% | 88% |
Procurement Timelines and Supply Chain Flexibility
Time is money in manufacturing, and a reliable supply chain can make or break project deadlines. NanYa’s global network ensures steady material availability, even for large-scale projects.
Shorter Lead Times for Critical Projects-
NanYa 175TL benefits from efficient production cycles at NanYa’s state-of-the-art manufacturing facilities. This translates to reduced lead times compared to competitors, keeping your production line moving without unnecessary delays.
Vendor Support and Customization Options-
For specialized applications, NanYa offers customization services, such as tailored panel sizes or resin modifications, helping customers get exactly what they need without extensive waiting periods.
Case Study: Meeting Urgent Deadlines-
A telecom company needed materials for a high-frequency application within six weeks. By leveraging NanYa’s streamlined supply chain, they received the required 175TL laminates in just four weeks, ensuring their product launch stayed on schedule.
Assured Quality and Performance Standards
When it comes to PCB materials, quality isn’t something you want to leave to chance. NanYa 175TL’s manufacturing processes are subject to stringent controls, delivering consistent results batch after batch.
Certifications That Matter-
NanYa 175TL complies with IPC-4101/126 and UL94 V-0 flame retardancy standards. These certifications ensure that the material can stand up to the demanding safety and performance requirements of industries like aerospace, medical devices, and automotive. This makes it a solid choice for projects where both reliability and safety are non-negotiable.
Defect Reduction and Long-Term Reliability-
Low coefficients of thermal expansion (CTE) and high thermal stability mean fewer defects like delamination, warping, or cracking during fabrication and use. This saves us from costly recalls or product failures down the line.
Quality Metrics Comparison-
Metric | NanYa 175TL | Competitor A | Competitor B |
Dimensional Stability (%) | ±0.05 | ±0.08 | ±0.10 |
Solder Mask Adhesion | Excellent | Good | Fair |
Cost-Effectiveness Without Sacrificing Quality
Price considerations are always on the table, but the value comes from balancing cost with performance and yield improvements. NanYa 175TL achieves this balance, making it a budget-friendly option for both small and large-scale production.
Lower Total Cost of Ownership-
While the upfront cost of NanYa 175TL may be marginally higher than generic FR4 materials, its higher yields, reduced defect rates, and longer lifecycle result in lower total production costs.
Bulk Pricing Options-
NanYa’s flexible pricing for bulk orders ensures affordability for high-volume production runs, a big win for us scaling up their operations.
ROI in Real-World Applications-
A consumer electronics manufacturer compared production costs using NanYa 175TL and standard materials. Despite a 10% higher initial cost, the total cost per unit decreased by 15% due to reduced defect rates and higher production yields.
Cost Analysis-
Metric | NanYa 175TL | Standard Material |
Initial Cost (Per Panel) | $12.50 | $11.00 |
Defect Rate | 2% | 8% |
Total Cost per Unit | $12.75 | $13.20 |
Testing and Quality Assurance for NanYa 175TL PCB Materials
In the competitive world of PCB manufacturing, the stakes for reliability and performance are sky-high. PCB materials like NanYa 175TL undergo rigorous testing to meet the demands of advanced applications, from consumer electronics to industrial automation. By integrating stringent quality assurance processes and industry-specific certifications, we can ensure that their products perform as promised. Below, we delve into the testing methods, standards compliance, and quality control techniques that underscore the reliability of NanYa 175TL.
Reliability Testing for Long-Term Performance
Ensuring the long-term performance of PCB materials requires a robust testing framework. NanYa 175TL is subjected to a battery of reliability tests, simulating extreme conditions to guarantee durability and stability.
Through-Hole Reliability Testing-
Through-hole reliability tests measure how well the material withstands repeated thermal cycling. For instance, during wave soldering or reflow processes, the laminate endures rapid temperature changes. NanYa 175TL consistently demonstrates superior resistance to cracking and delamination, even under severe conditions.
Conductive Anodic Filament (CAF) Resistance Testing-
CAF formation is a major concern in densely packed PCBs, as it can cause electrical failures over time. NanYa 175TL laminates are engineered to resist CAF growth, thanks to their advanced resin system and optimized glass weave design. Testing under high humidity and voltage conditions reveals minimal CAF susceptibility.
Dimensional Stability Verification-
Dimensional stability is a must-have for multilayer PCBs, as any misalignment between layers can lead to functionality issues. NanYa 175TL delivers minimal expansion or shrinkage under thermal and mechanical stress, helping maintain precise layer alignment even in challenging conditions.
Comparison of Reliability Metrics-
Test | NanYa 175TL | Standard FR4 |
Through-Hole Reliability | Pass (500 cycles) | Fail (300 cycles) |
CAF Resistance | Excellent | Fair |
Dimensional Stability (%) | ±0.05 | ±0.15 |
Compliance with Industry Standards
NanYa 175TL is designed to meet or exceed the stringent standards that govern PCB materials worldwide. These certifications are not just checkboxes—they ensure compatibility, safety, and environmental responsibility.
Adherence to IPC-4101C/124/129 Specifications-
NanYa 175TL conforms to IPC-4101 standards, ensuring solid electrical insulation, mechanical durability, and strong thermal performance. These specifications are standard for industries like aerospace and medical devices, where product reliability and performance are non-negotiable. With NanYa 175TL, we can be confident that our materials will hold up under demanding conditions and deliver the consistency needed in high-reliability sectors.
Global Flame-Retardant and Environmental Compliance-
The material meets UL94 V-0 flame retardancy, ensuring that it does not contribute to the spread of fire. Additionally, it complies with RoHS and REACH directives, reflecting its environmentally responsible composition.
Case Study: Achieving Compliance for Automotive Applications-
An automotive electronics manufacturer chose NanYa 175TL to meet strict EU safety and environmental standards. The material’s consistent performance during flame and chemical resistance testing allowed the company to pass audits with flying colors, securing a lucrative contract.
Advanced Quality Control in PCB Production
Beyond material testing, quality control during production ensures that PCBs made with NanYa 175TL maintain their performance across varying applications. Sophisticated techniques are used to catch potential issues before we leave the factory floor.
Signal Integrity and EMC Tests-
Signal integrity testing ensures that high-speed signals are transmitted without distortion. NanYa 175TL’s low dissipation factor and stable dielectric constant make it ideal for high-frequency PCBs. Electromagnetic compatibility (EMC) testing further verifies that the material minimizes interference in densely packed circuits.
Real-Time Monitoring During Fabrication-
Manufacturing environments can introduce variability, but NanYa’s advanced process controls mitigate risks. Real-time monitoring tools check parameters like lamination pressure, temperature, and etching quality to maintain consistency.
Stringent Quality Assurance Protocols-
Final inspection protocols include cross-sectional analysis, solder mask adhesion tests, and surface cleanliness checks. These measures ensure that each PCB meets or exceeds the performance benchmarks set during design.
Quality Metrics for NanYa 175TL Production-
Quality Control Test | Result (NanYa 175TL) | Industry Benchmark |
Signal Integrity (GHz) | 10+ | 8-10 |
EMC Compliance | Pass | Pass |
Lamination Defect Rate (%) | <1 | 2 |
NanYa 175TL Comparison with Other High-Performance PCB Materials
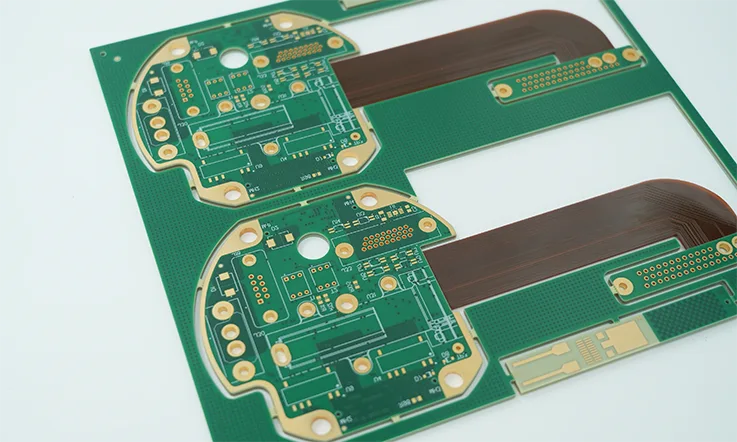
Choosing the right PCB material is a first step in ensuring optimal performance, cost-efficiency, and reliability in electronic designs. From telecommunication systems to automotive applications, each industry demands materials with specific characteristics. This comparison explores NanYa 175TL alongside other high-performance PCB materials, focusing on performance, specifications, cost, and application suitability.
Performance Comparison: Thermal, Electrical, and Mechanical Properties
Thermal Performance-
NanYa 175TL demonstrates impressive thermal stability, with a high glass transition temperature (Tg) and thermal decomposition temperature (Td), making it ideal for high-power and high-temperature environments. While Rogers materials excel in RF and microwave applications due to their low dielectric loss, they may not perform as well in mechanically demanding conditions.
Material | Tg (°C) | Td (°C) | Thermal Conductivity (W/mK) | Thermal Expansion (ppm/°C) |
NanYa 175TL | 175 | 340 | 0.35 | 13 |
Rogers RO4003C | 280 | 390 | 0.66 | 17 |
Isola Astra MT77 | 200 | 360 | 0.45 | 15 |
Shengyi S1170GFR | 170 | 300 | 0.28 | 18 |
Electrical Properties-
NanYa 175TL delivers reliable signal integrity and low dielectric loss, making it suitable for complex multilayer PCBs and mid-to-high frequency designs. In contrast, Teflon-based materials, such as Taconic TLY-5A, are preferred for ultra-high-frequency applications but come with a higher price tag.
Material | Dk @ 10GHz | Df @ 10GHz | Application |
NanYa 175TL | 4.2 | 0.017 | Mid-frequency multilayer PCBs |
Taconic TLY-5A | 2.20 | 0.0019 | Ultra-high-frequency RF boards |
Rogers RO3003 | 3.0 | 0.0021 | Microwave and radar systems |
Shengyi S1000-2 | 4.6 | 0.018 | Consumer electronics |
NanYa 175TL is recognized for its exceptional mechanical strength and dimensional stability under thermal and mechanical stress, making it suitable for automotive and industrial control applications. Ventec VT-4B5, while more expensive, offers enhanced mechanical robustness and delamination resistance.
Specifications and Customization Options
NanYa 175TL provides a wide range of thicknesses and copper weights, catering to diverse design needs. While Rogers and Isola offer more high-end customization options, they come with significantly higher costs.
Material | Available Thickness (mm) | Copper Weight (oz) | Customization Flexibility |
NanYa 175TL | 0.2 – 3.2 | 0.5 – 3.0 | Medium to high |
Rogers RO4350B | 0.1 – 3.0 | 0.5 – 4.0 | High |
Ventec VT-4B5 | 0.2 – 2.5 | 0.5 – 3.5 | Medium |
Cost Analysis: Balancing Budget and Performance
Cost-Performance Ratio-
NanYa 175TL strikes a balance between cost and performance, making it an attractive option for high-volume production. For budget-conscious projects like consumer electronics or industrial applications, it delivers reliable quality at a competitive price. High-end materials like Rogers and Taconic cater to niche, high-frequency, and aerospace markets but are considerably more expensive.
Material | Approx. Cost ($ per sq. ft.) | Applications |
NanYa 175TL | 5 – 8 | Automotive, Industrial, Consumer PCBs |
Rogers RO4003C | 12 – 20 | 5G, Aerospace, Microwave Systems |
Shengyi S1000-2 | 4 – 7 | Consumer Electronics |
Applications: Tailored for Industry Needs
Telecommunications-
●NanYa 175TL: Reliable in mid-frequency base station circuit boards with excellent thermal management and signal integrity.
●Rogers RO4350B: Ideal for 5G base stations and radar systems with ultra-low dielectric loss.
Automotive Electronics-
●NanYa 175TL: Widely used in automotive ECU boards for its high-temperature resistance and vibration tolerance.
●Ventec VT-4B5: Favored in EV control boards for superior mechanical strength and heat dissipation.
Consumer Electronics-
●NanYa 175TL: A cost-effective and reliable choice for large-scale consumer electronics.
●Shengyi S1170GFR: Lower-cost option for non-critical applications in consumer devices.
Handling and Storage Recommendations for NanYa 175TL PCB Materials
Ensuring the long-term performance and reliability of NanYa 175TL PCB materials starts with proper handling and storage practices. These materials are engineered to meet the highest industry standards, but their performance hinges on how they are managed before fabrication. In this section, we provide a guide to maintaining the integrity of NanYa 175TL through meticulous handling and optimal storage conditions.
Handling Guidelines: Protecting Material Integrity During Processing
Careful handling safeguards NanYa 175TL PCB materials from contamination, damage, and mechanical stress. Follow these best practices to maintain their pristine condition:
Cleanliness and Contamination Prevention-
●Always handle materials with clean, dry hands or wear non-contaminating gloves to avoid oil, dirt, and moisture transfer.
●Use anti-static mats or workstations to prevent static discharge, which could affect sensitive copper laminates.
Mechanical Stress and Damage Control-
●Avoid bending or flexing the sheets excessively, as this can lead to microcracks or stress fractures. For instance, improper handling in high-volume production environments has led to a 5% rejection rate in some cases.
●Employ precision cutting, drilling, and shaping tools to ensure clean edges and prevent delamination during processing.
Tool and Equipment Compatibility-
●Use carbide or diamond-coated bits for drilling and shaping to reduce material stress.
●Keep tools sharp and clean to minimize debris and rough edges.
Storage Recommendations: Maintaining Material Quality Over Time
Storing NanYa 175TL PCB materials correctly helps maintain their performance over time. Factors such as temperature, humidity, and contamination can affect the material’s durability and overall reliability. To preserve these high-performance materials, it’s best to keep them in a controlled environment that reduces these potential risks.
Temperature and Humidity Control-
●Store materials in a controlled environment between 20°C and 25°C (68°F to 77°F) with a relative humidity of 50%.
●Avoid rapid temperature changes or prolonged exposure to high humidity, which can warp laminates or degrade copper adhesion.
Protection from Contaminants-
●Keep materials in their original, sealed packaging to shield them from dust, moisture, and foreign particles.
●If repackaging is necessary, use vacuum-sealed bags with desiccants to absorb residual moisture.
Light and UV Protection-
●Direct sunlight and UV exposure can degrade solder mask layers and compromise the dielectric properties of the laminates. Always store materials in shaded or enclosed storage spaces.
Storage Parameter | Recommended Condition | Potential Risk If Ignored |
Temperature | 20°C – 25°C (68°F – 77°F) | Material warping, reduced Tg performance |
Humidity | 50% RH | Copper oxidation, laminate degradation |
Packaging | Original or vacuum-sealed | Contamination, moisture ingress |
Precautions During Long-Term Storage
When storing NanYa 175TL for extended periods, regular inspections can help identify early signs of degradation:
●Visual Checks: Inspect for discoloration, oxidation on copper layers, or moisture accumulation.
●Dimensional Stability Tests: Verify that the material remains flat and free from warping or bowing.
Handling Precautions: Protecting Surface and Structural Integrity
Surface damage or exposure to chemicals can compromise the material’s functionality. Implement these precautions to avoid issues:
Scratch and Surface Protection-
●Stack multiple sheets with soft separators or protective films to avoid abrasions.
●When transporting, secure sheets in rigid carriers to prevent mechanical shock.
Chemical Exposure-
●Avoid contact with solvents, acids, or cleaning agents unless verified to be compatible with the material. Prolonged exposure to incompatible chemicals can weaken dielectric properties and cause delamination.
Why Choose Us for Manufacturing Your High-Performance PCB Project?
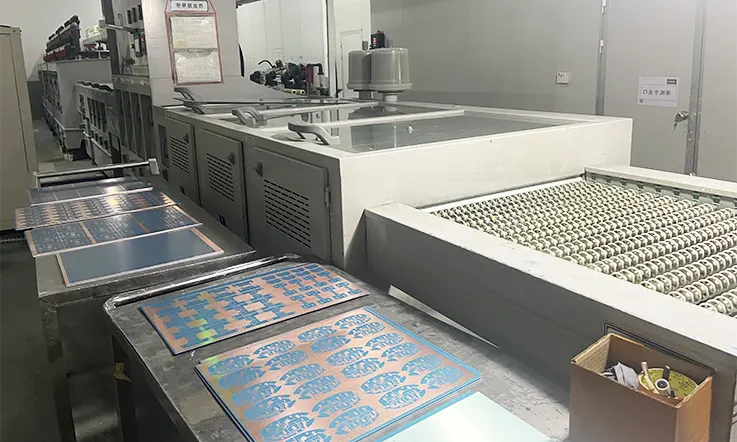
When it comes to high-performance PCB projects, selecting the right PCB manufacturer is key to ensuring the quality, reliability, and efficiency of your final product. At JarnisTech, we combine state-of-the-art manufacturing equipment, cutting-edge production technologies, a team of professional engineers, round-the-clock customer service, and a comprehensive one-stop solution to meet all your PCB needs. Here’s why we stand out as the best choice for your next project:
1. Custom PCB Solutions with Special Materials: Serving All Your Needs
At our company, we understand that every PCB project is unique, and some designs require specialized materials to meet specific performance, durability, or environmental requirements. That’s why we offer a wide range of custom PCB services utilizing advanced materials from leading brands. Whether you need high-frequency PCBs, flexible substrates, or flame-retardant options, we have the expertise and resources to deliver top-notch solutions tailored to your project’s specific needs.
We offer special PCB materials from renowned brands such as:
●Rogers: Known for high-frequency applications with exceptional dielectric properties.
●Taconic: Offers low-loss, high-speed materials perfect for RF and microwave circuits.
●Isola: Provides materials with excellent thermal performance and durability for harsh environments.
●Nelco: Specializes in high-performance laminate materials for automotive and industrial applications.
●Panasonic: Renowned for advanced materials that excel in high-temperature and high-performance environments.
●Arlon: Provides exceptional material solutions for high-speed signal transmission.
●Shengyi: Offers cost-effective, high-reliability options for various applications.
●ITEQ: Provides low-loss materials that are ideal for high-frequency and high-speed applications.
●Teflon (PTFE): Offers excellent electrical properties and is used in high-frequency and high-power applications.
●Ventec: Specializes in high-performance laminates and copper clad materials for demanding applications.
Our custom PCB solutions are crafted with these special materials to meet your design’s exact specifications. We take pride in sourcing and working with high-quality materials to provide PCBs that perform reliably, even under the most extreme conditions.
2. Advanced Manufacturing Equipment: Precision Meets Innovation
Our facility is equipped with the latest and most advanced PCB manufacturing equipment, ensuring precision and consistency at every stage of production. We use high-end machinery for automated drilling, plating, lamination, and inspection, all of which allow us to deliver exceptional quality at high volumes. This equipment is specifically designed to handle complex, high-performance PCB materials like NanYa 175TL, ensuring that your project meets even the strictest specifications.
3. Cutting-Edge Production Technology: Pushing Boundaries of Possibility
We don’t just keep up with industry standards—we set them. By continuously integrating the latest technologies into our production process, we are able to offer cutting-edge solutions that push the boundaries of what’s possible in PCB manufacturing. From high-frequency applications to advanced signal integrity requirements, our technology ensures that your PCBs are optimized for performance, durability, and reliability. Whether you’re dealing with complex multilayer designs or specialized materials, our technology handles it all seamlessly.
4. Professional Engineering Team: Expertise You Can Trust
At JarnisTech, we pride ourselves on our team of highly skilled engineers who bring years of experience in PCB design and manufacturing. Our engineers work closely with clients from the initial design phase through to final production, providing valuable insights and troubleshooting advice along the way. Whether you’re looking for a custom solution or need to ensure that your design is optimized for manufacturing, our team is here to make it happen. Our expertise is one of the factors that sets us apart from competitors.
5. 24/7 Customer Support: Always There When You Need Us
We know that deadlines and unexpected challenges can pop up at any moment in the high-performance PCB field. That’s why we offer round-the-clock customer support. Whether you’re facing tight timelines, need help troubleshooting, or require last-minute adjustments, our team is always here for you. You can rely on us to keep things moving forward and ensure your project stays on track without unnecessary hold-ups.
6. One-Stop Solution: Comprehensive Service from Start to Finish
At JarnisTech, we offer a one-stop solution for all your PCB manufacturing needs. From design consultation, material selection, and prototyping, to full-scale production, testing, and quality assurance, we handle every step of the process. Our clients benefit from seamless integration across each phase of production, ensuring that every detail is addressed and that the final product exceeds expectations. No matter how complex your project is, we have the tools, technology, and expertise to deliver it on time and within budget.
Why Wait? Get Your High-Performance PCB Project Done Right!
With our advanced technology, professional team, and comprehensive service offerings, we are the ideal partner for your next high-performance PCB project. Ready to get started? Contact us today and experience the difference of working with the best in the industry!