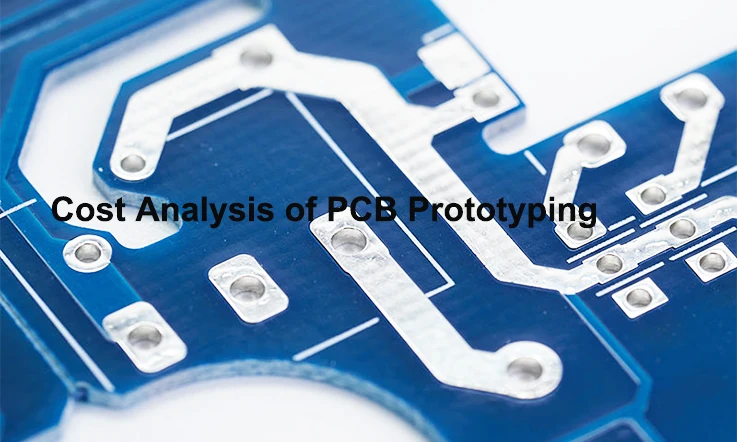
PCB prototyping is a key step in turning an idea into a real, functional product. But if you’ve ever wondered why the cost of these prototypes varies so much, you’re not alone. The factors behind PCB prototyping costs can feel like a maze. In this article, we’ll break down everything you need to know about how these costs are determined. From material choices to design complexity, we’ll dig deep into the nuts and bolts of what you’re paying for—and how you can keep your wallet from getting too light.
Key Factors Influencing PCB Prototyping Cost
Several key factors affect the price of a PCB prototype. Understanding these elements will allow you to make informed decisions during the design and procurement process, ensuring that you get the best value without sacrificing essential performance attributes.
Materials and Their Impact on PCB Prototype Pricing
One of the most significant drivers of PCB prototype costs is the material. The most commonly used substrate is FR-4, a glass-reinforced epoxy laminate, favored for its balance between performance and affordability. However, for designs operating at higher temperatures, high Tg materials or even ceramic-based materials may be required. These higher-performing materials, while essential for specific applications like automotive or aerospace, can significantly increase production costs.
Key Cost Factors in Materials:
●FR-4 is cost-effective but limited in high-temperature environments.
●High Tg materials are necessary for applications with elevated thermal demands but can drive the price up by 20-30%.
●Ceramic substrates or specialized laminates used in RF/microwave designs are even pricier, but often the only solution for high-frequency applications.
PCB Prototype Cost Breakdown by Layer Count and Material
Layer Count | Material (FR-4) | Material (High Tg) | Material (Ceramic) | Estimated Cost | Production Time (Standard) |
2-Layer | $50 | $80 | $150 | $50-100 | 3-5 days |
4-Layer | $100 | $150 | $250 | $150-200 | 5-7 days |
6-Layer | $150 | $200 | $300 | $200-400 | 7-10 days |
8-Layer | $300 | $350 | $500 | $300-600 | 7-12 days |
10-Layer | $400 | $500 | $700 | $500-800 | 10-15 days |
While material choice can seem like a no-brainer, be sure to consider the long-term performance needs of your design. Making compromises here may save money upfront but could lead to costly failures later.
How PCB Design Affects Prototyping Costs?
When it comes to design, complexity is king—and it has a direct impact on pricing. A simple two-layer PCB will cost far less than a 10-layer board with intricate routing and tight tolerances. The more complex the design, the more time and resources it takes to manufacture.
However, design optimization can significantly mitigate these costs. PCB design tools like Altium, KiCad, or Eagle allow for design-for-manufacturing (DFM) checks, helping engineers to reduce unnecessary vias, minimize trace lengths, and avoid costly production errors. Properly leveraging these tools during the design phase can save significant money.
Here’s a quick example: Imagine you’re designing a 6-layer PCB for a high-speed data application. Initially, the design may include unnecessary blind and buried vias, increasing cost by 30%. By using a DFM analysis and simplifying via structures to standard through-hole vias, you could cut that increase by half, saving considerable costs while still meeting performance requirements.
Regional Differences: PCB Prototyping Cost in the USA and Other Markets
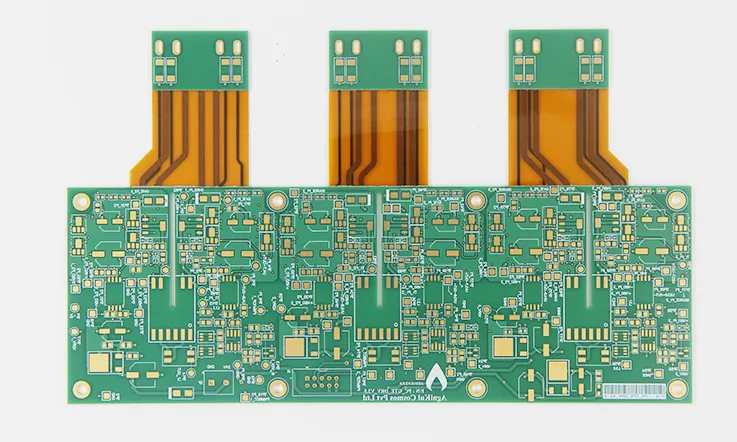
Your choice of manufacturing location can have a dramatic impact on your overall PCB prototype cost. While high-end services in the U.S. might come with premium pricing, opting for overseas suppliers might reduce costs significantly.
PCB Prototyping Cost in the USA
U.S.-based PCB manufacturers are known for high-quality, quick-turnaround services, but they come at a higher cost. This is largely due to labor rates, quality control standards, and quicker shipping times. The upside? U.S. manufacturers often provide engineering support and advanced testing options that help ensure the board functions perfectly right out of the gate.
Comparing International PCB Prototype Prices: China, India, and Beyond
For those looking to cut down costs, regions like China and India offer substantially lower pricing due to reduced labor and overhead costs. Chinese manufacturers, in particular, have perfected mass production, making them ideal for large-volume orders. However, the trade-off might be longer shipping times and occasionally lower quality control, so it’s essential to vet your supplier thoroughly.
For instance, a standard 4-layer PCB prototype produced in China might cost around $100-150, while the same board produced in the U.S. could be upwards of $500-600. The cost difference is significant, but it’s important to weigh the turnaround time and quality control elements in your decision-making process.
Real-World Example of PCB Prototype Cost Management
Let’s walk through a real-world case study where a mid-sized electronics manufacturer reduced PCB prototype costs by optimizing their design and carefully choosing suppliers.
Case Study: Reducing Costs in a High-Speed Data Project
●Initial Situation: The manufacturer initially designed a 12-layer PCB for a high-speed data router. Their first quote from a U.S.-based supplier came in at $1500 per board, with a turnaround time of two weeks.
●Challenges: The cost was too high, and the lead time didn’t meet their needs for a rapid market release.
●Solution: After a DFM review, they reduced the layer count to 8 and simplified the routing, leading to a lower production cost. They then sourced the prototype from a Chinese manufacturer at $450 per board, cutting costs by 70% while maintaining acceptable quality levels.
This example illustrates how early design decisions and global sourcing can profoundly impact the overall PCB prototyping budget.
Quick-Turn PCB Prototypes vs. Standard Prototypes: Cost Differences
Time is a critical factor in prototyping, and it can have a dramatic effect on your costs.
The True Cost of Quick-Turn PCB Prototypes
If you need a prototype fast, quick-turn services will deliver in 24 to 48 hours, but you’re paying a premium. For instance, if a standard prototype costs around $300, a quick-turn service could raise that to $700-1000. This surge is due to the immediate resource allocation and expedited shipping required.
Standard PCB Prototype Pricing Models
On the other hand, standard production timelines typically range from 5-10 days, and the pricing remains much more manageable. These services are ideal if your timeline allows for some flexibility.
Tip: If time isn’t an issue, use standard services to save significantly on costs.
Quick-Turn vs. Standard PCB Prototyping Costs
Service Type | Typical Turnaround Time | Estimated Cost (2-Layer FR-4) | Estimated Cost (6-Layer FR-4) | Estimated Cost (8-Layer FR-4) |
Standard Service | 5-7 days | $50-100 | $200-300 | $300-500 |
Quick-Turn Service | 24-48 hours | $200-300 | $500-700 | $800-1000 |
Reducing PCB Prototype Prices with Design for Manufacturing (DFM)
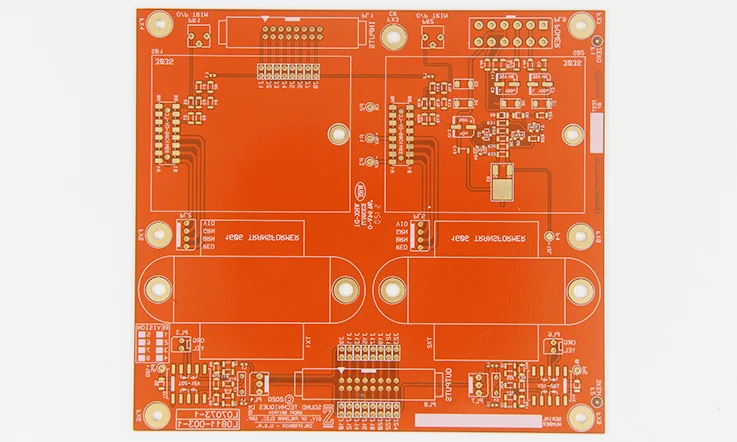
Let’s get into the nitty-gritty of Design for Manufacturing (DFM) and how this approach can seriously cut your costs.
DFM Strategies to Lower PCB Prototyping Cost
By collaborating early with your manufacturer, you can use DFM best practices to streamline your design. This means choosing components that are readily available and ensuring your layout follows standardized manufacturing processes. Small tweaks can result in major savings.
For example:
●Optimizing component placement to avoid unnecessary routing will reduce complexity and lead to fewer errors during production.
●Minimizing via types (blind/buried) can significantly lower your costs.
Common DFM Mistakes That Increase Prototype Costs
Not all DFM strategies are created equal. Here’s a list of common DFM mistakes that could send your costs through the roof:
Over-designing the board, adding unnecessary layers, or using rare components.
Ignoring manufacturing tolerances, leading to production errors and potential reworks.
Avoid these pitfalls by regularly conducting DFM checks during the design phase.
DFM Optimization Savings
DFM Strategy | Cost Before Optimization | Cost After Optimization | Savings |
Minimized Via Usage (Standard Vias) | $400 | $300 | 25% |
Reduced Layer Count (6-Layer to 4) | $500 | $350 | 30% |
Use of Readily Available Materials | $300 | $250 | 15% |
This table shows how DFM practices can help reduce costs in different areas of PCB design, such as the use of vias, material choices, and layer count.
Using Visual Tools and Templates to Optimize PCB Prototype Design
Visual aids play a crucial role in effective PCB design. Use diagrams, tables, and flowcharts to simplify complex design challenges and optimize cost.
●Cost vs. Layer Count Table: Visualizing the cost impact of increasing PCB layers can help you make informed decisions. For example, moving from a 4-layer to an 8-layer board can double your costs, but careful planning could lead to less costly alternatives.
●Material Selection Flowchart: A flowchart that guides you through selecting the best material based on your design’s thermal, mechanical, and cost requirements.
Example:
Layer Count | Material (FR-4) | Material (High Tg) | Cost Impact |
2-Layer | $50 | $80 | Low |
4-Layer | $100 | $150 | Moderate |
6-Layer | $150 | $200 | High |
How to Get Affordable PCB Prototypes Without Sacrificing Quality?
It’s possible to get affordable PCB prototypes without sacrificing quality. Here are some effective strategies.
Choosing Low-Cost PCB Prototyping Options
To stay within budget, leverage local manufacturers, design templates, and bulk ordering where possible. You’ll find that some manufacturers offer discounts for repeat customers or larger order volumes.
Balancing Cost and Quality in PCB Production
Remember, saving money shouldn’t mean sacrificing quality. Strike the right balance by ensuring your design meets DFM standards, choosing appropriate materials, and working with trusted manufacturers. While overseas production might save you a significant amount, always weigh the quality control, communication, and lead-time factors. Consider conducting smaller test runs to assess the manufacturer’s performance before committing to a large-scale production.
Tip: Communicate early and often with your manufacturer to ensure expectations on both sides are aligned. A little upfront effort can save you time and money down the road.
Wrapping Up
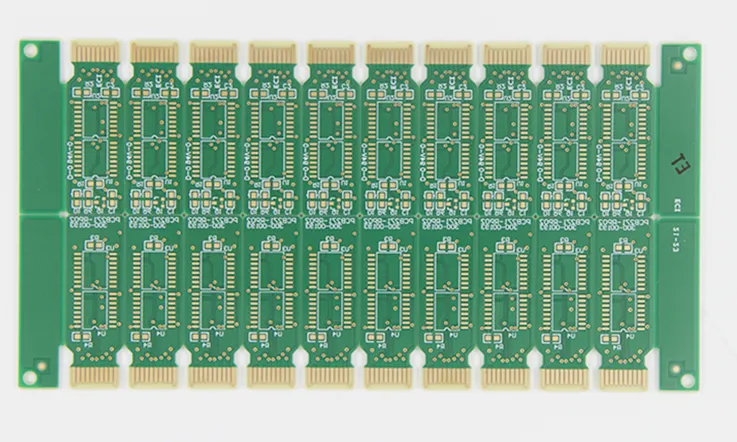
Finding the Right Balance in PCB Prototyping Costs
When it comes to PCB prototyping costs, it’s not just about cutting corners to save money. Instead, it’s about understanding the levers you can pull to optimize costs without compromising on the critical aspects of your design. Whether you’re a junior engineer just starting in the field, a PCB buyer juggling multiple suppliers, or a seasoned electronics manufacturer, knowing where to focus your attention—materials, design complexity, or manufacturing location—can make all the difference.
By using DFM strategies, optimizing your design, and carefully selecting materials and suppliers, you can significantly reduce costs while ensuring your product performs as expected. Keep in mind that investing in a quality prototype can pay dividends in the long run by avoiding costly errors and ensuring a smoother transition to full production.
So, as you prepare to get your next prototype off the ground, think about the trade-offs and make sure you’re focusing on what really matters. And if you’re ever stuck in a design quandary, don’t be afraid to consult your manufacturer—they’ve likely seen it all and can help you avoid common pitfalls.
Get Your PCB Prototype Cost Estimate Today
Looking to get started with your next prototype? Whether you need a quick-turn or cost-effective standard service, request a custom quote now. You can also upload your PCB design for a free DFM review to help you spot cost-saving opportunities. Don’t wait—get your PCB to market faster and smarter with expert help from top suppliers – JarnisTech.
Frequently Asked Questions (FAQ)
1.What is the average cost of a PCB prototype?
The cost of a PCB prototype can vary greatly based on several factors like material, layer count, and manufacturer location. In general, a two-layer PCB prototype can cost around $50-100, while a six-layer board can range from $200-400. Quick-turn services can cost up to three times more than standard production timelines.
2.How does the layer count affect the cost of a PCB prototype?
Each additional layer adds complexity and increases manufacturing costs. For instance, a two-layer board might cost $50-100, while a four-layer board could cost $150-200, and an eight-layer board may go up to $300-600 or more, depending on the materials used.
3.Are overseas manufacturers always cheaper for PCB prototypes?
While overseas manufacturers, particularly in China and India, tend to offer lower prices, it’s essential to consider factors such as quality control, lead time, and shipping costs. These can offset the savings in some cases, especially if the prototype requires high precision or quick delivery.
4.How can I reduce the cost of my PCB prototype?
The most effective ways to reduce costs are by optimizing your design through DFM strategies, selecting readily available materials, and avoiding unnecessary features like blind or buried vias. Additionally, consider ordering in bulk and exploring local suppliers for shorter lead times and better communication.
5.How do quick-turn PCB services impact cost?
Quick-turn services are designed to expedite the production process, often delivering prototypes within 24-48 hours. However, this convenience comes at a premium, typically doubling or tripling the cost of a standard prototype order. If time permits, opting for a standard timeline can offer substantial savings.
6.Is it better to use FR-4 or High Tg materials for my PCB prototype?
The choice depends on your design’s thermal requirements. FR-4 is cost-effective and sufficient for most standard applications, but high Tg materials are recommended if your PCB will operate in high-temperature environments. While high Tg materials are more expensive, they prevent performance degradation in high-stress conditions.
7.What is DFM, and how can it help me save money?
DFM (Design for Manufacturing) is a set of practices aimed at making a design easier and more cost-efficient to manufacture. By following DFM principles—such as simplifying the board layout, minimizing the number of layers, and avoiding complex via structures—you can reduce prototyping and production costs.