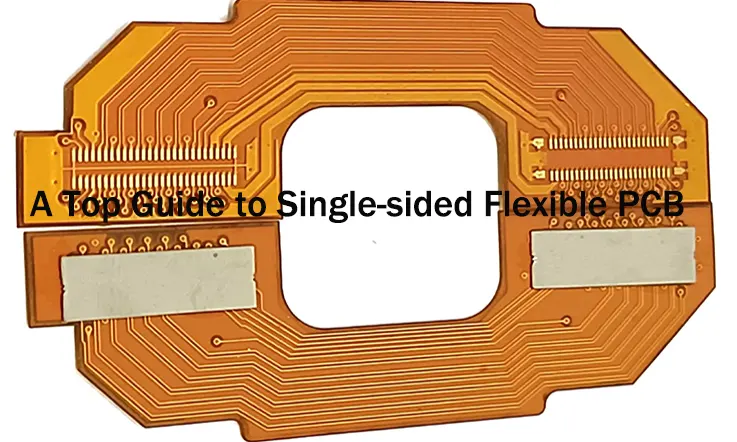
Printed circuit boards serve as the fundamental interconnect infrastructure in electronic devices. Although rigid boards are widely used, flexible PCB offer distinct advantages for applications that demand dynamic flexing, bending, or shaping around structures. Among the various FPCB constructions, single-sided flex circuits with conductors on one side are the most straightforward.
This article aims to explore the concept of single-sided flexible PCB, encompassing their typical applications, associated benefits, materials and construction techniques employed, essential manufacturing capabilities required, and crucial design considerations for implementing single-sided flex circuits.
What is a Single Sided Flex PCB?
A single-layer flexible PCB, utilizing a single-sided polyimide (PI) copper-clad laminate, typically consists of rolled copper foil, chemically etched conductive patterns, and a layer of covering film applied after circuit completion. While it is possible to manufacture a single-sided flexible PCB without a cover layer or protective coating, such layers are often employed to safeguard the circuit, typically positioned as the top layer of the flexible circuit.
The single-sided flexible PCB enables access to component termination functions from only one side, allowing the design of through holes in the base film. These through holes facilitate the passage of electronic component pins, enabling electrical interconnection through soldering.
Prominently employed insulating substrates for the manufacturing of single-sided flexible PCB encompass PCB raw materials such as polyimide, polyethylene terephthalate, aramid cellulose ester and polyvinyl chloride.
To enhance the rigidity of the single-sided flexible circuit, reinforcement ribs can be incorporated in specific areas requiring additional stiffness.
Among flexible circuit boards, the single-sided flexible PCB represents the simplest and most cost-effective manufacturing option. If a single layer layout suffices for an use selecting a single layer flexible PCB is a wise decision.
Consequently, the utilization of a single-sided flexible PCB offers significant cost-effectiveness.
What Materials are Used in Single-sided Flexible PCB?
Common materials utilized in the fabrication of single-sided flexible printed circuit boards include:
Base Dielectric: Polyimide tops the list of preferred materials, applauded for its top-tier flexibility and thermal resistance. On the other hand, options like Liquid Crystal Polymer, Polyethylene Naphthalate, Polyethylene Terephthalate , or Polyurethane (PU) may also serve the purpose.
Conductor: Electrodeposited copper foil is commonly utilized for the conductor layer, typically ranging in thickness from 12 to 35μm. Rolled annealed copper offers optimal performance in terms of flexure.
Bonding Adhesive: Acrylic or epoxy-based adhesive films are employed to attach stiffeners, connectors, or components onto the flexible PCB.
Cover Layer: A cover layer, consisting of either polyimide or adhesive materials, can be optionally added to provide insulation or enhance stiffness.
Stiffeners: In areas of the flexible PCB that require rigid mounting surfaces, selective FR-4 stiffeners can be incorporated.
Finishes: To ensure solderability and durability, immersion tin or silver over nickel finishes are commonly employed.
What is the Structure of a Single-sided Flexible PCB?
Polyimide Substrate/Cover Layer: The main material used for the sided flexible PCB is the polyimide film, which serves as both a base and a protective covering on each side of the circuit board. Polyimide provides flexibility and resistance to high temperatures making it perfect, for the needs of flexible PCB uses.
Copper Circuit Layer: The formation of the copper layer happens via chemical etching of the copper foil, which in turn gives birth to the needed circuit design. This layer operates as the conductive layer for the single-sided flexible PCB. The copper layer is lodged centrally in the PCB, compressed between the polyimide substrate and the adhesive layer.
Adhesive Layer: The bonding of the copper circuit layer and the polyimide substrate is facilitated through the utilization of an adhesive substance. This layer serves to warrant the steadfast fixity of the copper traces to the polyimide film, enhancing the overall structural integrity of the flexible PCB.
Cover Layer Replacement: In contrast to rigid PCB that utilize solder mask to protect the circuitry, single layer flexible PCB employ polyimide as a cover layer to replace the solder mask. The polyimide cover layer provides both protection and insulation for the circuitry while maintaining the flexibility and durability of the PCB.
Stack-up of a Single-sided Flexible PCB
The stack-up of a single layer flex PCB refers to the arrangement of layers and materials employed in its construction. Unlike in multi-layer flexible or rigid PCB, the single layer flex PCB possess conductive paths on merely one side, which simplifies their stack-up.
Stack-up of a single-sided flexible PCB consists of a base dielectric layer, a conductor layer, and optionally, a cover layer. This configuration allows for flexibility, lightweight design, and the ability to withstand dynamic flexing and shape changes required in various applications.
Worth noting is that single-sided flexible PCB encompass only one conductive layer. This implies that both components and trace elements are situated solely on one facet of the board. Consequently, the stack-up formation is significantly uncomplicated in comparison to multilayer flexible PCB, which have multiple conductive layers separated by dielectric materials.
How to Design a Single-sided Flexible PCB?
Within a single sided flexible PCB structure, a lone conductive copper sheet is enclosed by either dual insulating layers or a solitary polyimide insulating layer. The exposed side of the copper sheet is utilized for the single layer flexible PCB design.
Subsequently, the circuit pattern is etched out of the internal copper sheet using a chemical etching technique.
Single-sided flex PCB boards may feature components, cables, pins, and stiffeners. Additionally, certain single-sided flexible PCB incorporate a dual-access mechanism, allowing access to the conductive material from both sides of the circuit.
This design objective necessitates a compact PCB layout and specialized layers to enable access to the single copper layer through the polyimide layer of the base material.
As a result, single-sided flexible PCB offer significant cost-effectiveness while still accommodating the required functionality and design considerations.
Manufacturing Process of Single-sided Flexible PCB
The manufacturing procedure for single-sided flexible PCB involves a series of consecutive stages, extending from design and material choice to fabrication and assembly.
Design and Layout:
Design Specification: Establish the electrical and mechanical requirements of the PCB, including dimensions, component placement and electrical connections.
Schematic Design: Create a schematic diagram of the circuit, specifying the components and their interconnections.
PCB Layout: Utilize PCB design software to develop the layout of the single-sided flexible PCB, encompassing component placement and conductive trace routing.
Material Selection:
Flexible Substrate: Select a suitable flexible substrate material, typically polyimide (PI) or polyester (PET), considering factors such as temperature tolerance, flexibility and cost.
Copper Foil: select for the suitable thickness and category of copper foil to be employed for the conductive traces. Copper is predominantly selected given its superior conductive nature in terms of electricity.
Preparation of Flexible Substrate:
Cleaning and Pre-treatment: Thoroughly clean and pre-treat the flexible substrate material to enhance adhesion and ensure its cleanliness.
Copper Cladding:
Copper Foil Lamination: Laminate the chosen copper foil onto one side of the flexible substrate using an adhesive layer, thereby creating the conductive layer.
Circuit Patterning:
Photoresist Application: Apply a layer of photosensitive material (photoresist) to the copper-clad side of the flexible substrate.
Exposure: Employ a mask and UV light to expose the photoresist, reproducing the PCB layout and delineating the areas where the copper will be etched away.
Etching:
Chemical Etching: Employ an etching solution to chemically remove the exposed copper, leaving behind the desired conductive traces.
Resist Stripping: Eliminate the remaining photoresist, exposing the conductive traces.
Component Placement:
Surface Mount Technology: Utilize automated pick-and-place machines to accurately position surface-mount components onto the PCB. These components are then attached to the conductive traces using solder paste.
Through-Hole Technology: Insert through-hole constituents either manually or with automation into pre-drilled apertures on the PCB, and subsequently secure them via soldering on the opposed facet.
Soldering:
Reflow Soldering: In the case of SMT components, subject the entire PCB to reflow soldering, where it passes through an oven to melt the solder paste and establish secure electrical connections.
Hand Soldering: For THT components, manual soldering may be required.
Insulation Layer:
Cover Layer Application: Apply an insulating cover layer, typically made of polyimide, across the entire PCB to safeguard the conductive traces and components. This layer may include openings to expose specific areas or components.
Testing and Inspection:
Conduct electrical testing of the completed single-sided flexible PCB to ensure proper functionality and connectivity.
Perform visual inspection to identify any defects, such as solder bridges or component misalignment.
Cutting and Forming:
Cut and shape the single-sided flexible PCB according to the desired configuration or enclosure requirements, enabling it to conform to specific shapes or fit within designated enclosures.
Final Testing:
Retest the PCB after cutting and forming to verify its correct functioning in its final shape.
Packaging and Shipping:
Package the finished single-sided flexible PCB and make necessary preparations for shipment to customers or further assembly stages.
It’s pertinent to acknowledge that the exact specifics of the product manufacturing procedure can undergo varied adjustments depending on the manufacturer, intricacy of the PCB layout and equipment employed. Nonetheless, the aforementioned general steps provide an overview of the typical process involved in manufacturing single-sided flexible PCB.
Benefits of Single Sided Flexible PCB
Single-sided flexible circuits offer several key advantages over rigid boards:
Dynamic Flexing:
Single-sided flex circuits can endure extensive flexing and shape changes required in motion applications, making them highly suitable for applications that involve frequent movement and bending.
Lightweight:
These circuits weigh significantly less, typically 60-80% less, than equivalent rigid boards. This lightweight characteristic is beneficial in weight-sensitive applications, such as portable electronics or aerospace systems.
Thin Profile:
With flex layers as thin as 25μm, single-sided flex circuits allow for tight installations and stacking. Their thin profile enables compact designs and facilitates integration into space-constrained devices.
High Density:
Single-sided flex circuits offer the advantage of finer lines and spaces, allowing for dense interconnections within limited areas. This high-density capability is particularly advantageous in miniaturized electronic devices where space is at a premium.
Three-Dimensional Flexibility:
Unlike rigid boards, single-sided flex circuits have the ability to bend and conform to three-dimensional surface shapes. This flexibility enables their usage in curved or irregularly shaped products and facilitates design versatility.
Embedded Passives:
Single-sided flex circuits can incorporate embedded passive components such as capacitors and resistors. This integration of passive elements directly onto the circuit board enhances compactness and enables space-saving designs.
Cost Efficiency:
By eliminating the need for additional components and connectors, single-sided flex circuits simplify assembly processes and reduce overall manufacturing costs. Their streamlined design and simplified assembly contribute to cost savings.
High-Frequency Performance:
Single sided flex circuits can maintain controlled impedance and transmit unattenuated signals at high frequencies. This feature makes them well-suited for applications that require reliable signal integrity and high-frequency performance, such as telecommunications or high-speed data transmission.
Durability:
Polyimide materials commonly used in single-sided flex circuits exhibit excellent durability, withstanding millions of flex cycles without compromising their performance. This durability ensures long-lasting functionality and reliability in applications that involve repetitive bending or flexing.
Aesthetics:
Single-sided flex circuits offer the advantage of producing stylish, low-profile products. Their thin and flexible nature allows for sleek and visually appealing designs, enhancing the overall aesthetics of the end products.
Single-Sided Flexible PCB Vs. Single-Sided Rigid PCB
Single-sided flexible circuit boards present a highly advantageous alternative to rigid PCB, offering numerous benefits over their inflexible counterparts.
Single-sided flexible circuit boards are manufacturing use a thin plastic sheet, which is laminated with copper foil before being finished with an epoxy resin coat. Their notable flexibility enables their application as either the upper layer in double-sided board frameworks or the under layer in multi-layer configurations. This innate flexibility bestows numerous benefits, encompassing boosted durability, escalated portability, and amplified user accessibility for clients.
In contrast, rigid circuit boards are composed of metal sheets etched with circuits and interconnected by minuscule metal wires, commonly known as “traces.” Their rigid nature makes them particularly suitable for applications like computer cases, where robustness and durability are paramount considerations.
Conclusion
A single-sided flexible PCB represents the fundamental configuration of a flexible circuit. Within the realm of single-sided flex PCB boards, it is possible to incorporate components, wires, adhesive materials, and stiffeners. The application of flexible circuits spans across diverse products, with medical equipment being a particularly notable beneficiary.
In contrast to conventional cabling and rigid PCB, single-sided flexible PCB present several advantages, including diminished occurrences of cabling and wiring defects, minimized size and weight, enhanced reliability, and increased durability. These benefits contribute to the overall enhancement of the electronic system’s performance and functionality.