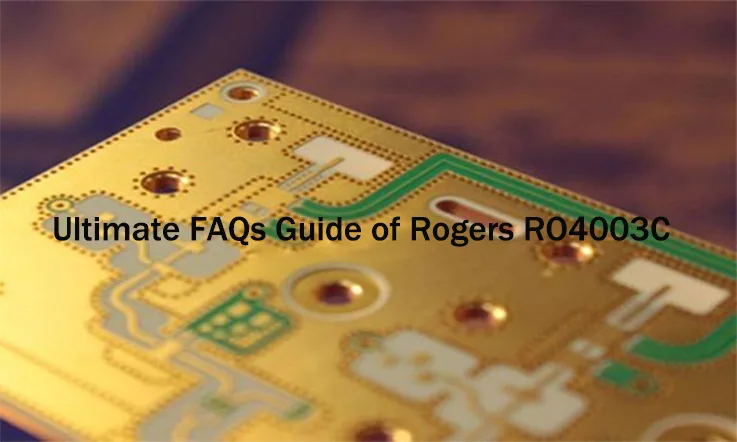
Rogers RO4003C is a series of hydrocarbon laminates that are reinforced with glass. These laminates possess a glass-reinforced surface, which bears resemblance to the traditional epoxy laminates. The material is particularly well-suited for the construction of multi-layer boards.
In terms of processing, Rogers RO4003C shares similarities with FR-4. However, it operates at a significantly lower fabrication rate. These laminates have been specifically developed to cater to high-volume applications that require exceptional performance.
One notable characteristic of Rogers RO4003C is its dissipation factor, which stands at 0.0027 at a frequency of 10 GHz. This factor indicates the material’s ability to dissipate energy and maintain signal integrity. With such desirable properties, Rogers RO4003C can be found in the market at competitive rates.
Exploring further details about Rogers RO4003C will provide valuable insights into its composition, performance, and applications.
What Is Rogers RO4003C?
Rogers RO4003C is a series of high-performance circuit board materials manufactured by Rogers Corporation. It is a glass-reinforced hydrocarbon laminate designed specifically for applications requiring excellent electrical and mechanical properties, particularly in high-frequency and RF (Radio Frequency) applications.
The RO4003C material is known for its low-loss characteristics, making it suitable for high-frequency circuit designs where signal integrity is crucial. It offers efficient signal transmission with minimal signal attenuation, enabling reliable performance in demanding communication systems.
This material is widely used in various industries such as telecommunications, aerospace, automotive, and more. It plays a vital role in the construction of electronic devices including radios, televisions, cell phones, wireless systems, and microwave circuits.
The RO4003C circuit board is constructed using two different types of glass cloth combined with a hydrocarbon resin system. This construction provides the board with superior electrical and mechanical properties while maintaining a low thermal expansion coefficient (Tg). Its standard glass construction also simplifies the manufacturing process, making it easier for electronic designers to work with.
While the RO4003C offers numerous advantages, it is important to note that it is not flame-retardant, which makes it vulnerable to oxidation and potential performance degradation. Additionally, it may not be suitable for high-speed applications that require rapid signal transmission and stringent signal integrity.
Overall, the Rogers RO4003C is a popular choice for high-frequency and RF applications due to its low-loss properties, wide frequency range, and ease of construction. Its performance characteristics make it a valuable material for electronic designers seeking reliable and efficient signal transmission in their circuits.
Rogers RO4003C features and specification in PCB Application
Rogers RO4003C is a high-frequency circuit material widely used in the manufacturing of printed circuit boards (PCBs). It’s well known for its unique blend of electrical and mechanical stability, making it suitable for a variety of applications.
Here are some of the key features and specifications:
Features:
Low Dielectric Constant: The RO4003C has a low dielectric constant of 3.38 ± 0.05 @ 10 GHz. This feature allows it to handle high frequencies with minimal signal loss.
Low Loss Tangent: It features a low loss tangent (0.0027 @ 10 GHz), which makes it suitable for applications that require minimal signal loss.
Temperature Stability: RO4003C has a good thermal coefficient of dielectric constant, making it stable under varying temperature conditions.
Low Moisture Absorption: This material has a very low moisture absorption rate, reducing performance variability in humid environments.
Mechanical Durability: It maintains its physical properties even under stress, making it suitable for use in rugged environments.
Specifications:
● Dielectric Constant (Dk): 3.38 ± 0.05 @ 10 GHz
● Dielectric Loss (Df): 0.0027 @ 10 GHz
● Thermal Coefficient of Dk: -3 ppm/°C
● Z-Axis Thermal Expansion (50-260°C): 24 ppm/°C
● T288: >60 minutes
● Moisture Absorption: <0.05% ● Peel Strength: >8 lbs./in.
● Volume Resistivity: >10^6 MΩ.cm
● Surface Resistivity: >10^6 MΩ
Applications in PCB:
Rogers RO4003C is extensively used in a variety of PCB applications, including:
Microwave and RF applications: Due to its low dielectric constant and low loss factor, RO4003C is ideal for use in microwave and RF applications.
Automotive Radar Systems: The RO4003C is used for manufacturing PCBs used in automotive radar systems.
Cellular Base Station Antennas: This material is also used in the production of PCBs for cellular base station antennas.
Power Amplifiers and Filters: Due to its thermal stability and low signal loss, RO4003C is often used in power amplifiers and filters.
Please note that the selection of PCB materials is a critical decision based on the specific needs of your application, and you should consult with a PCB design and manufacturing expert to make the best choice.
The Benefits and Drawbacks of Rogers RO4003C
The Rogers RO4003C offers several benefits that make it a desirable choice for various applications:
Benefits:
Low Loss: The RO4003C is known for its low-loss characteristics, making it suitable for high-frequency applications. It provides efficient signal transmission with minimal signal attenuation.
Wide Frequency Range: This circuit board can handle a wide frequency range, making it ideal for RF and microwave applications. It is capable of supporting frequencies up to 300MHz, enabling reliable performance in demanding communication systems.
Superior Electrical and Mechanical Properties: The RO4003C exhibits excellent electrical and mechanical properties, thanks to its glass-reinforced hydrocarbon laminate construction. It offers stability, reliability, and high-performance capabilities.
Ease of Construction: With its standard glass construction, the RO4003C facilitates an easier construction process compared to other materials. This makes it more convenient for electronic designers to work with and manufacture circuits.
Cost-Effective: The RO4003C is a cost-effective option, providing high performance at a reasonable price. This makes it more accessible for mass-market applications and helps reduce overall project costs.
However, the Rogers RO4003C also has a few drawbacks to consider:
Drawbacks:
Lack of Flame Retardancy: One significant drawback of the RO4003C is its vulnerability to oxidation and reduced performance due to its non-flame-retardant construction. This limits its suitability for applications where fire safety is a critical concern.
Not Suitable for High-Speed Applications: The RO4003C may not be the best choice for high-speed applications that require rapid signal transmission and stringent signal integrity. Other materials with specific characteristics may be more suitable for such applications.
While the benefits of the RO4003C, such as low loss, wide frequency range, and ease of construction, make it highly desirable, it is essential to consider its drawbacks, particularly the lack of flame retardancy and limitations in high-speed applications, when selecting this material for a specific project.
Parameters affecting radiation losses in RO4003C laminates
Dielectric Constant (Dk): The dielectric constant of RO4003C influences the propagation velocity of signals on the laminate. Higher dielectric constant can lead to increased radiation losses. Therefore, selecting a laminate with a lower dielectric constant can help minimize radiation losses.
Copper Roughness: The roughness of the copper surface on the laminate can contribute to radiation losses. Higher roughness can lead to increased energy dissipation and radiation. Ensuring a smooth copper surface by using appropriate copper foil and surface treatments can help reduce radiation losses.
Copper Thickness: The thickness of the copper conductor on the laminate can affect radiation losses. Thicker copper conductors tend to exhibit lower radiation losses compared to thinner conductors. Optimizing the copper thickness for the specific application can help minimize radiation losses.
Substrate Thickness: The thickness of the RO4003C substrate can impact radiation losses. Thicker substrates generally result in lower radiation losses due to increased shielding provided by the additional material. However, the trade-off is increased cost and size. Careful consideration of the substrate thickness is necessary to balance performance requirements and practical constraints.
Trace Geometry and Layout: The geometry and layout of the traces on the laminate can influence radiation losses. Factors such as trace width, spacing, and termination techniques can affect the impedance and radiation characteristics. Proper design techniques, such as impedance control and appropriate termination, can help mitigate radiation losses.
Signal Frequency: The frequency of the signals being transmitted on the laminate can impact radiation losses. Higher frequencies tend to result in increased radiation losses due to the shorter wavelengths involved. Mitigating techniques such as controlled impedance design, proper shielding, and optimized layout become more critical at higher frequencies.
Are RO4003C Flame Retardant PCB Materials?
RO4003C is not inherently flame retardant. It is a high-frequency laminate material developed by Rogers Corporation primarily for its electrical performance characteristics. However, RO4003C can be used in flame-retardant printed circuit board (PCB) constructions when combined with appropriate flame-retardant materials.
To meet flame retardancy requirements, PCB manufacturers often employ additional measures such as incorporating flame-retardant additives or using flame-retardant coatings or laminates in combination with RO4003C. These additional measures help ensure that the final PCB assembly meets the desired flame retardancy standards.
When designing a PCB using RO4003C, it is essential to consider the overall system requirements, including any specific flame retardancy requirements. Collaborating with PCB fabricators and adhering to industry standards and regulations, such as UL 94, can help ensure the appropriate flame retardant properties are achieved in the final PCB assembly.
How Does Insertion Loss in RO4003C Compare to Other Rogers laminates?
The insertion loss in RO4003C high-frequency material is generally lower compared to other Rogers laminates. RO4003C is known for its excellent electrical properties, including low loss and low dielectric constant, which contribute to reduced insertion loss.
Rogers offers a range of laminates designed for high-frequency applications, each with its own unique characteristics. While the specific insertion loss values may vary depending on the frequency and design considerations, RO4003C is typically regarded as one of the lower loss laminates within the Rogers product lineup.
It’s important to note that different laminates within the Rogers family are optimized for specific performance requirements. For example, RO4350B is another popular high-frequency laminate from Rogers that provides excellent stability and lower dielectric loss. However, it may have slightly higher insertion loss compared to RO4003C.
The choice of the appropriate Rogers laminate depends on the specific application requirements, such as operating frequency, signal integrity considerations, and desired performance levels. Consulting the datasheets and technical specifications provided by Rogers Corporation can offer more detailed and accurate information on the insertion loss characteristics of their various laminates.
RO4003C vs FR-4: Which has lower moisture absorption?
Between RO4003C and FR-4, FR-4 is generally known to have higher moisture absorption compared to RO4003C. FR-4 is a widely used standard PCB material based on a woven glass fabric reinforced epoxy laminate. While FR-4 offers good electrical and mechanical properties, it is more susceptible to moisture absorption.
Moisture absorption in PCB materials can lead to various issues, including changes in electrical properties, dimensional instability, and reduced reliability. When exposed to moisture, FR-4 can experience changes in dielectric constant and loss tangent, which can impact signal integrity and performance.
RO4003C, on the other hand, is a hydrocarbon laminate reinforced with glass. It is designed to have lower moisture absorption compared to traditional FR-4 laminates. The hydrocarbon composition of RO4003C reduces its affinity for moisture, making it more resistant to absorption and minimizing the associated negative effects on electrical performance.
In applications where moisture sensitivity is a concern, such as in high-humidity environments or applications exposed to moisture ingress, RO4003C can be a favorable choice due to its lower moisture absorption characteristics. However, it’s important to note that even though RO4003C has lower moisture absorption, it is still essential to follow best practices for PCB assembly and protection to prevent moisture-related issues.
Ultimately, the choice of the best PCB material in terms of moisture absorption depends on the specific application requirements, environmental conditions, and the desired level of moisture resistance needed for reliable and consistent performance.
Factors to Consider when Selecting RO4003C Laminate?
When selecting RO4003C laminate for a particular application, several factors should be considered:
Frequency Performance: RO4003C is designed for high-frequency applications, so it is crucial to assess its performance at the desired frequency range. Consider factors such as dielectric constant, loss tangent, and insertion loss to ensure they meet the requirements of your application.
Signal Integrity: Evaluate the laminate’s ability to maintain signal integrity, especially in terms of impedance control, signal attenuation, and skew. RO4003C is known for its stable electrical properties, which contribute to good signal integrity.
Thermal Performance: Consider the operating temperature range of your application and ensure that RO4003C can withstand the desired temperature conditions without significant degradation in its electrical and mechanical properties.
Manufacturing Compatibility: Assess the compatibility of RO4003C with your preferred fabrication processes, including drilling, plating, etching, and soldering. Ensure that the laminate can be easily processed and integrated into your manufacturing workflow.
Material Thickness: RO4003C is available in various thicknesses. Select the appropriate thickness based on the specific requirements of your design, including stack-up considerations and mechanical constraints.
Environmental Considerations: Determine whether your application requires any specific environmental resistance, such as moisture resistance, chemical resistance, or resistance to thermal cycling. Evaluate whether RO4003C meets those requirements.
Cost: Consider the cost implications of using RO4003C for your application, including material costs, fabrication costs, and any additional processing requirements.
Standards and Certifications: Verify if the laminate meets any industry standards or certifications necessary for your application, such as IPC standards or UL recognition.
By thoroughly evaluating these factors, you can make an informed decision when selecting RO4003C laminate that aligns with your application’s requirements and ensures optimal performance and reliability.
When is Controlled Impedance Critical in RO4003C Laminate?
Controlled impedance is essential in RO4003C laminate when the application involves high-frequency signals and requires precise signal integrity. Here are some scenarios where controlled impedance becomes crucial:
High-Speed Digital Applications: In high-speed digital designs, such as high-speed data communication systems or high-speed memory interfaces, controlled impedance is vital to minimize signal reflections, maintain signal integrity, and prevent data errors. RO4003C’s controlled impedance capabilities help ensure consistent and accurate signal transmission.
RF and Microwave Applications: RO4003C is commonly used in RF and microwave circuits, where precise impedance matching is critical. Controlled impedance enables efficient power transfer, reduced signal loss, and maximum power transfer between components, such as amplifiers, filters, antennas, and transmission lines.
Transmission Lines and Stripline Structures: RO4003C is often employed in transmission lines and stripline structures, where controlled impedance is necessary to maintain consistent characteristic impedance throughout the circuit. This helps prevent signal distortion, reflections, and crosstalk, ensuring optimal performance in high-frequency applications.
High-Frequency Analog Circuits: Controlled impedance is crucial in high-frequency analog circuits, such as mixers, oscillators, and amplifiers. It helps maintain the desired impedance values, minimize signal degradation, and preserve signal quality, resulting in accurate and reliable analog signal processing.
High-Frequency Test and Measurement Equipment: In applications involving high-frequency test and measurement equipment, controlled impedance is vital to ensure accurate measurements and reliable signal transmission. RO4003C’s controlled impedance characteristics support precise impedance matching and minimize measurement errors.
In all these scenarios, using RO4003C with controlled impedance design techniques helps optimize performance, reduce signal loss, and maintain signal integrity, ultimately leading to reliable operation of high-frequency circuits and systems.
Which are the Main Circuit Technologies Used in RO4003C Substrates?
RO4003C substrates are compatible with various circuit technologies commonly used in high-frequency applications. The main circuit technologies used with RO4003C include:
Microstrip: Microstrip is a widely used circuit technology in which the signal conductor is placed on the top layer of the substrate, while the ground plane is situated on the bottom layer. The dielectric properties of RO4003C contribute to maintaining controlled impedance in microstrip designs.
Stripline: Stripline technology involves placing the signal conductor between two ground planes, typically on inner layers of a multilayer PCB. RO4003C laminates can be used as the dielectric material in stripline designs, providing controlled impedance and shielding for the signal traces.
Coplanar Waveguide (CPW): CPW is a configuration where the signal conductor is sandwiched between two ground planes, with the signal trace exposed on the top layer and ground planes on the bottom layer and sides. RO4003C can be used as the substrate material for CPW structures, enabling controlled impedance and good isolation between the signal and ground.
Embedded Microstrip: Embedded microstrip combines the advantages of microstrip and stripline technologies. It involves embedding the signal trace within the PCB substrate, surrounded by ground planes. RO4003C can serve as the dielectric material for embedded microstrip designs, offering controlled impedance and enhanced electromagnetic shielding.
Differential Pair: Differential signaling is used for high-speed data transmission, where two complementary signals, with equal amplitude but opposite polarity, are transmitted on parallel traces. RO4003C laminates can be utilized for differential pair designs, ensuring controlled impedance and consistent signal integrity for the differential signals.
These circuit technologies, when implemented with RO4003C substrates, provide controlled impedance, low loss, and excellent high-frequency performance. The choice of circuit technology depends on the specific application requirements, board layout considerations, and desired performance objectives.
Significance of RO4003C’s thermal coefficient of dielectric constant
The thermal coefficient of the dielectric constant (TCDk) of RO4003C is an important parameter because it characterizes how the dielectric constant of the material changes with temperature. It provides information about the material’s thermal stability and the potential impact of temperature variations on the electrical performance of the circuit.
Here’s why the TCDk of RO4003C is significant:
Impedance Control: In high-frequency circuits, maintaining controlled impedance is crucial for signal integrity. The dielectric constant affects the characteristic impedance of transmission lines and matching networks. If the dielectric constant changes with temperature, the impedance of the circuit can deviate from the desired value, leading to signal distortion, reflections, and degraded performance. Understanding the TCDk helps in accurately predicting and compensating for these changes.
Design Predictability: The TCDk value allows designers to account for the thermal effects on the dielectric constant during the design phase. By knowing how the dielectric constant varies with temperature, designers can better estimate the behavior of the circuit under different operating conditions and make informed design decisions.
Temperature Compensation: In some applications, precise control of the dielectric constant over a wide temperature range is critical. The TCDk value helps in designing compensation techniques to mitigate the temperature-induced variations in the dielectric constant. By incorporating temperature compensation strategies, the circuit’s performance can be maintained within the desired specifications across different temperature conditions.
Reliability and Thermal Management: Understanding the TCDk is important for assessing the thermal stability and reliability of the circuit. Temperature variations can cause expansion and contraction of materials, leading to mechanical stress and potential reliability issues. By considering the TCDk, designers can select appropriate materials and develop effective thermal management strategies to minimize the impact of temperature cycling on the performance and longevity of the circuit.
By considering the TCDk of RO4003C, designers and engineers can account for the thermal effects and design more robust and reliable high-frequency circuits that maintain consistent performance over a range of operating temperatures.
Summary
The thermal conductivity (TC) of the Rogers RO4003 circuit board proves to be highly advantageous for high-frequency applications. Its wide frequency range makes it a preferred choice among RF microwave circuit designers, playing a vital role in industries such as automotive, aerospace, and telecommunications. To achieve success in creating an integrated circuit (IC) utilizing this device, it is imperative for an expert electronic designer to invest time in familiarizing themselves with its construction and the benefits it offers.
While the Rogers RO4003C boasts excellent performance, it does possess a few limitations. Its construction lacks flame-retardant properties, rendering it susceptible to oxidation and subsequent degradation in performance. Furthermore, the absence of a flame-retardant component increases the risk of fire incidents. Consequently, the Rogers RO4003C is not suitable for high-speed applications.
Our services
Rogers PCB Laminates & Series