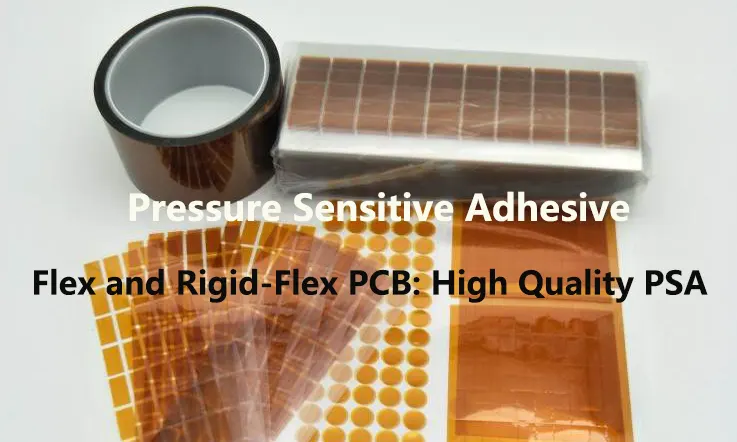
There is a wide variety of pressure-sensitive adhesives (PSA) on the market today, and each of these PSA varieties is ideally suited to perform a distinct circuitry function. These adhesives are often highly flexible and easy to work with, making them a superior choice for the majority of applications due to their characteristics. These adhesives all have higher bond strength, and in some cases, the bond actually gets stronger with time.
PSAs, in contrast to certain adhesives, do not cause problems when they are bonded to particular materials. Because of this, PSAs can be used to adhere flex circuits directly to a substrate or any other material, which further expands their range of applications.
The purpose of this article is to offer the designer or user with information regarding the usage of pressure sensitive adhesives (PSAs) for the assembly of rigid-flex boards and flexible printed circuit boards. This reference offers information on various types of PSAs, as well as their uses, materials, and design considerations for FPC.
Definition of Pressure Sensitive Adhesive (PSA)
One of the main types of adhesive tapes is pressure-sensitive adhesive, often known as PSA or self-stick adhesive. It is a relatively thin, flexible material with a single- or double-sided coating.
When applied with pressure to the majority of clean, dry surfaces, PSA guarantees that adhesive tape will attach to a variety of substrates, including flex and flex rigid PCBs, and various FPC stiffeners, such as PI, FR4, stainless steel, and aluminum, at the slightest touch.
Which Adhesives are Used in PSA Tapes ?
Silicone Adhesives
Silicone polymers were used in the formulation of this adhesive, making it the only one of its kind that can form strong bonds with silicone surfaces. Silicone adhesives are able to tolerate higher temperatures than rubber or acrylic glue, despite the fact that they are considerably more expensive and have a much lower initial tack.
Acrylic Adhesives
In general, Adhesives made with acrylic polymers have, a stronger ability to withstand the effects of long-term aging and a higher level of resistance to the various solvents and environmental variables. Acrylic adhesives are known to produce bonds that are typically stronger than those produced by standard rubber adhesives, and they are also able to withstand higher temperatures.
Rubber Adhesives
Adhesives designed with tackifying resins, oils, and anti-oxidants that are based on natural or synthetic rubbers. Rubber is the most cost-effective PSA material, and it has excellent adhesion speed. Rubber adhesive is not advised for high-temperature applications.
Typically Used PSA Tapes
In flex circuits, the following types of pressure-sensitive adhesive adhesives are most frequently used to bond stiffeners and FR4 frames (which serve as supporting plates and perform a function similar to that of SMT carriers):
● 3M966
● 3M467
● 3M9077
● Tesa 8854
● Tesa 8853
● Other double-sided PSA tape models If need.
PSAs can be obtained in a wide range of different adhesive formulations and thicknesses, allowing them to be tailored to the particular needs of a given design. The companies 3M and TESA are two of the most well-known suppliers. There are literally hundreds of distinct PSA formats to choose from.
PSA (Pressure Sensitive Adhesive) Thickness
PSAs typically range in thickness from 2 to 5 mils and are offered in a variety of adhesive formulations. The type of material to which the flex circuit will be affixed as well as any other environmental concerns determine which adhesive formula should be used. The most widely used pressure sensitive adhesive (PSA) in the business world is called 3M 467MP, and it has a very excellent bond strength to a wide variety of different materials.
Advantegaes of PSA( Pressure Sensitive Adhesive) Tapes
● Reduces assembly time.
● Thinner and lighter material.
● Eliminates the need for surface refinishing.
● Provides vibration dampening and noise reduction.
● Provides uniform thickness and gap filling properties.
● Bonds dissimilar material without incompatibility concerns.
Uses of Pressure-Sensitive Adhesive (PSA) in the Industrial Sector
Pressure-sensitive adhesives are utilized in a variety of industries due to their flexibility, dependability, and adaptability. Tapes, labels, and graphics usually employ pressure-sensitive adhesive material, which is frequently put to objects in order to seal or identify them. In consideration of the importance of skin contact and sensitivity, this sort of skin-safe adhesive is also utilized to manufacture a variety of medical products, such as bandages and wound dressings.
Construction of a Typical Pressure Sensitive Adhesive Tape
Self Wound: A carrier that has a PSA coating applied to one side and a release coating applied to the opposite side. When it comes to products of this nature, there is no release liner. Self-wound tapes can be used for a wide variety of applications, including masking, duct sealing, and carton sealing.
Double Coated: A PSA coating is applied to both sides of a carrier. The carrier for the adhesive can be made of a wide variety of materials, including plastic films, tissue, nonwovens, and so on. Laminates and carpet tape are two common applications for this material.
Transfer Tape: An unsupported mass of adhesive film coated on a release liner with a release coat on both sides. Transfer tapes have excellent conformability to curved or otherwise non-flat surfaces.
Single Coated: A substance with an adhesive coating on just one side of it (Facestock). The silicone-coated release liner serves as a barrier to protect the adhesive.
Design Considerations for Flex Circuits Used in PSAs
PSAs have design requirements that originate from how the PSA sections are manufactured and mounted onto the flex circuit. These requirements, which need to be addressed, must be met. In most cases, the PSAs are cut to shape as independent entities, and after that, they are manually positioned and attached to the flex circuit.
For PSA outline, Either a punch and die set or a laser cutting machine can be used, depending on the amount of PSAs that need to be cut out. Laser cutting is used for smaller quantities. The magnitude of the PSA is going to be the limiting factor in this situation. Producing very small PSA pieces that are also easy to handle and position during installation might be challenging, if not impossible, in some cases. It is vital for the supplier of flex circuits to go over the specific PSA requirements and make any necessary adjustments. As a result of the heat generated during the process of cutting, laser cutting may also leave a very little darkening at the very edge of the PSA. This is due to the fact that laser cutting uses light rather than an electric current.
It is recommended to include the outline of the PSA sections to the silkscreen layers of the design in order to assist in the exact placement of the PSAs. This will help ensure that the PSAs are positioned in the correct locations. If the PSA is going to be used to attach a stiffener, it will first be added to the material that makes up the stiffener, and then a routing operation will be utilized to cut out both the PSA and the contour of the stiffener at the same time.
Because of the high temperature involved in the reflow process, the type of PSA that can be utilized for designs that call for automated component assembly and reflow will be restricted. There are only a few PSAs that have the rating to resist the temperatures required for RoHS reflow. These PSAs are only for use as mechanical attachments in various applications. There is not a single thermally or electrically conductive PSA that has a reflow temperature rating that we are aware of. In the event that they are required, these PSAs will have to be attached to the flex circuit after the process of component assembly has been completed.
FPC Adhesive (Bonding Sheet) vs. PSA
One of the last steps in the fabrication process is the addition of stiffeners to the flexible circuit. These stiffeners can be attached using either a layer of pressure sensitive adhesive or a layer of thermal setting glue referred to as Bonding Sheet. When considering cost, the PSA application is almost always going to be significantly less expensive than its counterpart. Thermal setting on-flow adhesive requires the flex PCB to be placed back in the lamination press to apply the heat and pressure needed to cure the adhesive. The adhesive also needs to be pre-cut to the specific shape of the stiffener itself by either laser cutting or die punching. This can be done to ensure that the adhesive adheres properly.
The configuration and/or position of stiffeners will also determine the type of glue used. For instance, if a stiffener does not reach to the circuit outline, it will typically necessitate a PSA attachment and an additional stiffener outline to be added to the silkscreen for proper placement.
● The preferred approach for thermally bonding stiffeners to the circuit with the same flexible glue used to connect the coverlay is to use heat and pressure, which will result in a very strong, permanent stiffener bond.
● If the design prohibits the use of flexible adhesive, PSA can also be used to bond stiffeners solely through the application of pressure. The particular PSA will depend on whether or not the flex PCB will undergo an automated reflow cycle and/or what material it will be bonded to.
Summary
The addition of PSAs to the design of a flexible circuit board gives new capabilities that can handle a variety of design difficulties, including mechanical mounting, heat dissipation, electrical grounding, and prospects for cost reduction.
We strongly encourage you to get in touch with us so that we can discuss the specific requirements of your project and so that we can provide design support to make sure that the project is a success. Because we are a PCB Fabrication and assembly factory, there is such a vast selection of options available, both in terms of the application and the materials.
Related Posts:
1. Selecting PCB Laminate Materials: A Comprehensive Overview
2. PCB Copper Trace Width and Space: Everything You Need to Know About Them
3. Which Types are Most Commonly Used in PCB Substrates?
4. What Is Fiberglass PCB and Why Fiberglass Used in PCB Manufacturing?
5. Standard PCB Thickness-Choosing the Correct Thickness for PCB