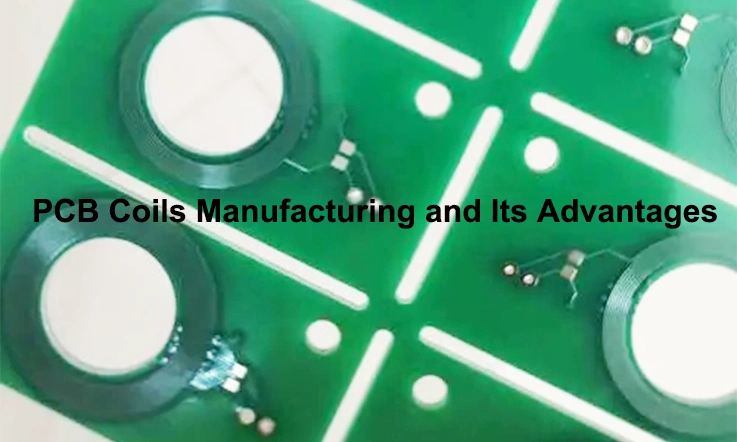
Printed circuit board coils, commonly referred to as PCB coils play a role in various electronic devices. Creating these coils involves combining coil winding methods with PCB manufacturing procedures to produce effective and dependable coils. This post explores the advantages of PCB coil manufacturing and highlights emerging trend shaping the future of this technology.
Importance of PCB Coils in Electronic Devices
PCB coils are components in electronic devices providing various benefits over conventional wire wound inductors. These advantages encompass inductance, compact dimensions, cost efficiency and dependability. The close arrangement of traces within PCB coils allow for greater inductance values compared to similarly sized wire wound coils, and making them well suited for application such as RF circuits and antennas that demand high inductance levels.
The compact size of PCB coils is beneficial for situation where space’s limited, especially in portable electronic device where size and weight are important factors. Additionally, PCB coils can be produced in quantities at a lower cost than wire wound coils making them a cost effective option for application that need high production volumes. Their robust construction and lack of mechanical connections also contribute to their reliability, which is essential for application such as medical device and automotive electronics.
PCB coils are used in electronic devices, like smartphones, laptops, tablets, cameras, GPS system, medical equipment and car electronics. With the increasing need for lighter and affordable device the significance of PCB coils in electronics is set to increase. They are anticipated to remain integral to the development of new and innovative electronic product.
Specific examples of how PCB coils are utilized in electronic devices. Their are used in RF circuits to match impedance filter signals and achieve resonance. They are also found in antennas to connect them effectively to transmission lines. In power supplies PCB coils serve as inductors for filtering and regulating voltage. Furthermore they play a role, in filters by eliminating frequencies. Additionally these coils are utilized in sensors to detect fields and other physical aspects by acting as inductors.
Therefore, PCB coils play a role in electronic devices because of their many benefits compared to traditional wire wound inductors. Their higher inductance, size, cost efficiency and dependability, to making them a popular option for a wide array of uses in the electronics sector.
Manufacturing Process of PCB Coils
In creating PCB coils various important stages are involved, each playing a role, in guaranteeing the effectiveness and high quality of these vital components utilized in electronic devices.
Material selection
Material selection is the initial phase, where careful consideration is given to choosing the appropriate materials for the PCB coils. Copper and aluminum are commonly utilized due to their high electrical conductivity and cost-effectiveness. The determination of the thickness and width of the conductor traces is also paramount, tailored to achieve the desired inductance and current-carrying capacity.
Material selection
Following material selection, the coil winding process takes place, involving the precise winding of the conductor onto a form or mandrel. The winding technique employed is dependent on specific application requirements, with helical winding commonly utilized for high-inductance coils and spiral winding for low-inductance coils. The intricacies of the winding, including the number of turns and spacing, directly impact the inductance of the coil.
Etching and plating
Subsequently, the etching and plating stage is undertaken to refine the coil. Through the use of chemical etchants, such as ferric chloride, the unwanted copper or aluminum is removed, ensuring the coil’s optimal performance. Subsequent plating with solderable finishes like tin or gold serves to safeguard the coil against corrosion and facilitate seamless integration with other component.
Inspection and testing
The inspection and testing phase serve as the final checkpoint in the manufacturing process of PCB coils. Thorough scrutiny is conducted to detect any defects, such as shorts or opens, guaranteeing the coil’s integrity. Additionally, meticulous testing is carried out to verify that the coil meets the prescribed inductance and current-carrying capacity standards. Utilizing specialized tools like an inductance meter and multimeter, the performance parameters of the PCB coil are meticulously evaluated.
The efficient and budget friendly process of manufacturing PCB coils makes them a favorable option for large scale usage. The careful handling of every stage starting from choosing materials to conducting inspections and tests guarantees that PCB coils provide effective performance across a wide range of electronic devices.
Advantages of PCB Coils
PCB coils provide some of advantages that make them a preferred choice in electronic devices:
● Increased Inductance
● Compact Size
● Cost-Effectiveness
● Reliability
● Versatility
● Automation
● Integration
PCB coils provide a series of advantages, such as including increased inductance, compact size, cost effectiveness, reliability, versatility, automation and integration capabilities. These feature make them essential elements in electronic device.
Future trends in PCB coil manufacturing
Future trend in PCB coil production are anticipated to prioritize improving effectiveness, productivity and size reduction. Some key trends to look out for include:
Integration of advanced materials
Incorporating advanced materials with superior electrical properties. Such as graphene or nanomaterials, can improve the performance and efficiency of PCB coils. These materials provide conductivity, reduced resistance and improved thermal stability ultimately boosting the performance of the coils.
3D printing technology
The adoption of 3D printing technology in PCB coil manufacturing can revolutionize the design and production process. This new method offer opportunities to create coil shapes that were previously unattainable through manufacturing method. Furthermore 3D printing allow for prototyping and customization making it easier to develop unique coil designs suited for particular application.
IoT and wireless power transfer
The rise of Internet of Things (IoT) device and the need for power transfer solution indicate that PCB coils will have a significant role in facilitating effective energy transmission. Potential future direction could include creating PCB coils for wireless charging purposes and incorporating these coils into smaller IoT devices to improve connectivity and energy efficiency.
High-frequency applications
The growing need for frequency uses like 5G communication systems and radar systems will push the advancement of PCB coils that can function at higher frequencies. Potential upcoming developments might focus on creating PCB coils with improved impedance matching, lower parasitic capacitance and better signal integrity to fulfill the needs of frequency circuits.
Industry 4.0 and automation
The incorporation of Industry 4.0 technologies like artificial intelligence, machine learning and robotics, in the manufacturing of PCB coils has the potential to streamline production processes enhance quality control measures and boost overall efficiency. By automating tasks related to coil winding, inspection and testing manufacturers can improve productivity levels. Maintain a high standard of quality during large scale production runs.
In summary the upcoming developments in PCB coil production are set to make use of cutting edge materials printing tech, IoT applications, high frequency designs and Industry 4.0 automation to foster creativity and address the changing requirements of the electronics sector. Embracing these advancements will empower manufacturers to create notch, effective and compact PCB coils that serve a variety of purposes in todays digital era.
Final Thoughts
Manufacturing PCB coils comes with advantages, such as increasing inductance being compact in size cost effective, reliable, versatile, automated and easily integrated. As technology advances in the electronics industry PCB coils are expected to play a role in supporting advanced technologies, like IoT, wireless power transfer and high frequency applications. By adopting materials 3D printing techniques, integrating IoT systems designing for high frequencies and embracing automation through Industry 4.0 practices manufacturers can create innovative PCB coils that cater to the needs of the digital era. With its myriad benefits and promising future, PCB coil manufacturing remains a cornerstone of modern electronics design and production.