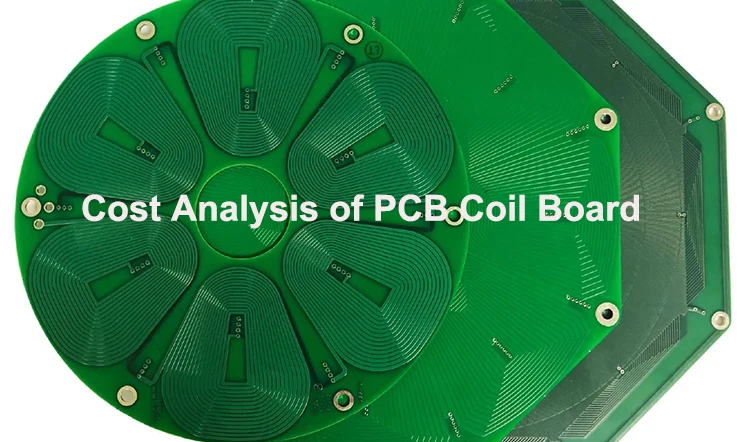
In the competitive realm of electronics manufacturing it is crucial to prioritize cost efficiency in order to secure profitability and stay ahead of the competition. PCB coil boards play a role in a wide range of electronic devices offering various benefits compared to traditional wound coils. Such as smaller size, lighter weight, enhanced performance and reduced expenses. However, the cost of PCB coil board can fluctuate depending on factors. Like materials used, manufacturing method employed and design choices made. In this article, we will provide a comprehensive cost analysis of PCB coil board while exploring effective strategies for cost optimization.
Background and significance of PCB coil boards
PCB coil boards are made circuit boards used in a range of electronic gadgets like inductors, transformers and antennas. They’re crafted by wrapping copper wire around core material, which is then incorporated into the PCB. This process allow for the production of top notch coils, with inductance and other electrical features.
Significance of PCB Coil Boards
The importance of PCB coil boards lies in their benefits when compared to traditional wound coils. Firstly they are smaller and lighter making them very useful in situations where space and weight’re important considerations. Secondly PCB coil boards can achieve inductance and Q factor than wound coils leading to better circuit performance. Additionally these boards can be produced on a scale at a lower cost making them a cost effective choice for applications requiring high volume. Furthermore the flexibility in design of PCB coil boards allows for customization, in terms of shape and size to meet application needs.
Applications of PCB Coil Boards
The use of PCB coil boards is widespread serving purposes. They are commonly used in power supplies for inductance and filtering needs. In RF circuits PCB coil boards play a role in producing inductors and transformers. Additionally these boards are found in antennas to help form circuits. In electronics PCB coil boards are crucial for providing inductance and filtering within power systems and circuits. Lastly the medical sector relies on PCB coil boards to fabricate coils for imaging devices, like MRI machines.
Materials Used in PCB Coil boards
Copper Foil and Prepreg
Copper foil is utilized to create the conductive traces that form the coils on the PCB, offering excellent electrical conductivity and available in various thicknesses. In addition, Prepreg, composed of fiberglass cloth impregnated with uncured epoxy resin, along with laminate, which is the cured form of prepreg, constitute the base material of the PCB, providing both mechanical support and insulation.
Core Material and Adhesive
Core materials, like ferrite powdered iron or air are carefully chosen to support the coils according to the need of the application. On the another, adhesive substances are applied to attach the coils to the core material and PCB ensuring stability and accurate alignment.
Soldermask and Silkscreen
A soldermask, usually crafted from epoxy or liquid photoimageable material (LPI) serves as a safeguarding layer on the PCB to avoid solder connections forming between tracks. Meanwhile the silkscreen layer containing ink helps in labeling components, reference designators, logos and other markings, for component positioning and assembly.
The main materials utilized in PCB coil boards are typically these. Nevertheless based on the design and purpose there might be extra materials included, like more insulation layers for added protection coatings to shield against environmental elements or special materials for high frequency uses. The choice of materials is determined by factors such, as thermal conductivity needs, mechanical durability, cost factors and environmental aspects.
Costs involved in PCB coil board production
The expenses linked to manufacturing PCB coil boards can be divided into several key areas although the specific breakdown of costs might differ depending on variables, like design intricacy, manufacturing methods, production scale and location. Here is a broad summary of the associated expenses.
Cost of materials for PCB coil boards
The prices of materials for PCB coil boards like copper foil, prepreg and laminate can change depending on factors. The cost of copper foil is impacted by its thickness, where thicker foils tend to be pricier. Similarly the quality of prepreg and laminate affects their prices as higher quality materials come with a price expensive. Additionally the quantity of materials ordered matters as larger orders usually lead to lower costs per unit.
Manufacturing costs of PCB
The costs of creating PCB coil boards can differ based on factors. The expenses for winding the coils depend on factors like the type of equipment used and the intricacy of the coils being made. Similarly the costs linked to producing PCBs are affected by aspects. Such as the number of layer, board size and design complexity. Furthermore assembly and inspection expenses may vary based on the number of components, on the board and the level of testing required.
Overhead Costs
Facility costs, including rent, utilities, maintenance, and equipment depreciation, are integral to the manufacturing process. Labor expenses account for the wages and benefits of employees involved in coil winding PCB fabrication, assembly and testing. Moreover administrative expenditures, like management salaries, administrative personnel costs and other overhead expenses also factor into the cost.
Miscellaneous Costs
Quality control measures like inspections, testing tools and staff are crucial for guaranteeing the dependability and performance of PCB coil boards impacting the production expenses. Moreover costs related to packaging and delivery encompassing materials, labeling and transportation also have an impact on the total production expenditure.
How to Cost Optimization Strategies for PCB Coil?
Material Substitution: Evaluate materials that meet the necessary standards but are more budget friendly. For instance think about utilizing copper foil or lower quality prepreg without compromising on performance.
Design for Manufacturability: Optimize the design of the PCB coil board design for manufacturing, less waste and fewer errors. Factors to consider are component placement, trace routing and reducing the number of layers.
Supplier Negotiation: Collaborate with supplier and manufacturers to discuss pricing volume discount and improved contractual terms. Building strong relationship with supplier can lead to cost saving in the long run.
Process Optimization: Streamline manufacturing procedures boosting effectiveness and cutting down on production time are goals. This may entail implementing automation, optimizing workflow layouts, and removing obstacles to enhance output and minimize labor expenses.
Volume and Economies of Scale: Increasing the level of output might bring about economies of scale leading to reduced per unit expenses. It is advisable to factor, in demand and strategize production accordingly to capitalize on these cost advantages.
Quality Control and Rework Reduction: Implement robust quality control measures to minimize rework and scrap. This involves purchasing automated inspection tools performing testing and putting in place process controls to lower mistakes and flaws.
Continuous Improvement: Foster a culture of continuous improvement within the organization. Inspire team members to discover and execute money saving strategies support efficiency programs and consistently review and enhance procedures.
Value Engineering: Analyze the design, materials and production method to pinpoint areas, for cost reduction without sacrificing functionality or quality. Look for opportunities to simplify the design or eliminate unnecessary feature or components.
Supply Chain Optimization: Enhance the efficiency of the supply chain by cutting down on lead times efficiently handling inventory and pinpointing chances for cost reduction through sourcing and managing logistics.
Lifecycle Cost Analysis: Consider the lifecycle costs of the PCB coil boards, it’s important to factor in maintenance, repairs and replacing components. Prioritizing reliability and durability in the design can lead to savings in the run.
Sum Up
With the increasing need for PCB coil boards it’s essential for manufacturers to focus on cost optimization. This piece explores the analysis of PCB coil board expenses, emphasizing elements and opportunities for cost efficiency. Through tactics like using materials designing for easier manufacturing optimizing processes and negotiating with suppliers manufacturers can save costs while maintaining quality. By continuously evaluating and improving cost-related factors, manufacturers can enhance their competitiveness, profitability, and customer satisfaction in the dynamic electronics industry.