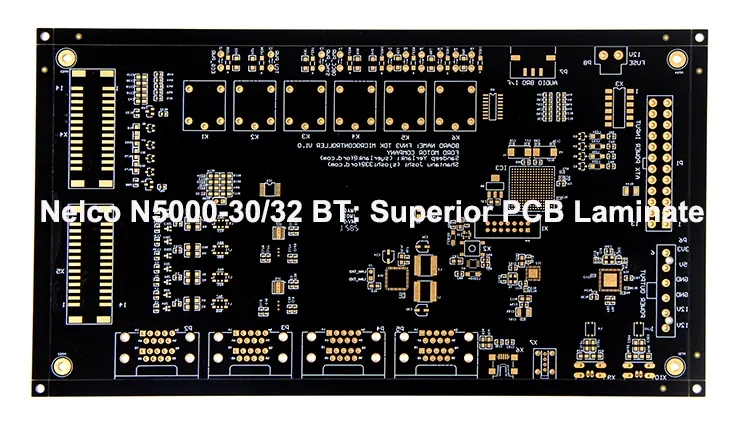
The design and manufacturing of high-performance PCBs require precision, durability, and materials that can handle the demands of complex, high-speed circuits. Nelco N5000-30 Prepreg and N5000-32 Laminate have become essential in modern PCB applications, offering exceptional performance across various industries. From ensuring signal integrity in high-frequency circuits to supporting high thermal conductivity in power-dense devices, these materials provide the foundation for next-generation designs.
This guide will explore how Nelco N5000-30/32 optimizes PCB design, high-frequency applications, multilayer stack-ups, and thermal management, highlights how these materials can elevate your design projects to new heights of performance and reliability.
Key Features of Nelco N5000-30 Prepreg and Nelco N5000-32 Laminate
When you’re working with high-frequency PCBs, you need materials that can keep up with your demanding designs. Enter Nelco N5000-30 Prepreg and Nelco N5000-32 Laminate—two materials engineered to elevate your PCB manufacturing process. These materials offer exceptional performance in high-speed, high-frequency, and high-thermal environments. Let’s take a deeper dive into the core features that make these materials a go-to for manufacturers and engineers across a variety of industries.
Low Dielectric Constant for Precision High-Speed Circuits
The dielectric constant is a defining property for materials used in high-speed circuit applications. Simply put, the lower the dielectric constant, the better the signal integrity. Nelco N5000-30 Prepreg and Nelco N5000-32 Laminate are designed with a low dielectric constant, which ensures minimal signal distortion during transmission. For engineers working on advanced designs, this feature is a standout. It directly impacts high-speed, high-frequency PCBs, where even the slightest interference can affect performance.
By using these materials, we can achieve superior signal clarity, ensuring that data is transmitted smoothly without unwanted disruptions. This low dielectric constant makes Nelco N5000-30 Prepreg ideal for high-speed PCBs in applications like telecommunication equipment and other top electronics. The precision this material offers is unmatched, especially when you’re dealing with multi-layer boards that demand flawless signal performance.
Thermal Stability: Standing Strong in Extreme Conditions
No one wants their circuit board to warp under pressure, and that’s where Nelco N5000-30 Prepreg and Nelco N5000-32 Laminate really step up to the plate. These materials are designed to withstand extreme temperatures, making them perfect for aerospace, automotive, and defense applications, where equipment often operates in hot, cold, or rapidly fluctuating conditions.
Temperature fluctuations are a constant challenge in high-performance PCBs, and thermal stability is core to keeping everything reliable. When circuits are exposed to heat or rapid temperature changes, they can expand, contract, and warp, leading to misalignments between layers. This can result in circuit failure or malfunction. However, Nelco N5000-30 Prepreg and Nelco N5000-32 Laminate are engineered for dimensional stability, even in the harshest conditions.
These materials offer a reliable, stable performance across a wide temperature range, whether it’s the blistering heat of desert environments or the freezing cold of outer space. As a result, they make a solid foundation for applications that cannot afford any loss of functionality or reliability due to temperature extremes.
The thermal stability of these materials is shown in the following table, which compares the temperature range and stability performance:
Material | Temperature Stability (°C) | Thermal Expansion Coefficient | Stability Impact |
Nelco N5000-30 Prepreg | -40 to 180 | 13-15 ppm/°C | High Stability |
Nelco N5000-32 Laminate | -40 to 180 | 12-14 ppm/°C | Excellent for High-Temp Environments |
The table demonstrates the thermal stability of these materials across a wide temperature range. This makes them highly reliable for applications where thermal cycling could otherwise lead to performance degradation.
Low Dissipation Factor: Powering Efficiency with Minimal Loss
If you’re designing RF and microwave circuits, energy efficiency is a must consideration. The dissipation factor (DF) measures how much energy is lost as heat during transmission. A lower dissipation factor means more efficient power transfer. Nelco N5000-30 Prepreg and Nelco N5000-32 Laminate are designed with a low dissipation factor, which minimizes energy loss and maximizes performance.
These materials are engineered to have a low dissipation factor, meaning that less energy is wasted, and more power is effectively transferred through the circuit. For high-performance RF applications, such as 5G networks, Wi-Fi technologies, or satellite communications, this feature is a advantage. With a low DF, the materials can handle higher power levels without generating excess heat, reducing the risk of overheating and improving overall efficiency.
Let’s break down the dissipation factor and its impact in a more tangible way:
Material | Dielectric Constant((Dk at 1GHz)) | 1GHZ Dissipation Factor (DF at 1 GHz) |
Nelco N5000-30 Prepreg | 4.1~4.4 | 0.009 |
Nelco N5000-32 Laminate | 4.1~4.4 | 0.009 |
As shown in the table, both Nelco N5000-30 Prepreg and Nelco N5000-32 Laminate demonstrate low dielectric constants and dissipation factors. This ensures efficient operation at high frequencies, even in extreme thermal environments.
Applications of Nelco N5000 Materials in High-Frequency Systems
High-frequency systems are at the core of many advanced technologies today. From 5G networks to high-speed computing systems, the demand for high-performance materials is stronger than ever. Nelco N5000-30 Prepreg and N5000-32 Laminate are materials that offer the right properties to optimize performance in these systems. These materials combine a low dielectric constant, thermal stability, and a low dissipation factor, which makes them ideal for applications in high-speed data transmission and RF/microwave circuits.
In this section, we’ll explore how these materials contribute to various high-frequency applications, providing engineers with reliable, efficient, and high-performance solutions for today’s technology.
Supporting 5G Network Infrastructure
The introduction of 5G networks has revolutionized communication technology, bringing unprecedented data transmission speeds and reduced latency. Supporting these advancements requires materials that effectively minimize signal loss and interference. Nelco N5000-30 Prepreg has emerged as a significant contributor to addressing these demands, ensuring reliable performance in high-speed communication systems.
●For instance, telecommunication companies like Verizon and AT&T are deploying 5G infrastructure across various cities, and the performance of their network depends on the quality of the materials used in their equipment. Nelco N5000-30 Prepreg helps achieve faster signal propagation while ensuring minimal signal distortion across base stations and antennas. The material’s low dielectric constant plays a crucial role in reducing signal loss, allowing for seamless communication even in dense urban environments.
The low loss factor of Nelco N5000 materials also ensures that there’s minimal signal attenuation, enabling efficient transmission of data at 5G speeds. This helps meet the growing demand for faster and more reliable mobile and internet services.
Enhancing RF and Microwave Performance
RF (Radio Frequency) and microwave circuits are critical components of modern communication systems, including satellite communication, radar systems, and defense technologies. These systems demand materials that can maintain high-frequency signals with minimal interference, and Nelco N5000-30 Prepreg and Nelco N5000-32 Laminate deliver precisely that.
●For example, Satellite communication providers like SpaceX depend on cutting-edge RF components to power their Starlink constellation, delivering internet access from orbit. Nelco N5000 materials play a central role in manufacturing high-frequency circuits onboard these satellites, ensuring minimal signal loss despite the extreme conditions of space. These advanced materials also enhance the efficiency of radar systems widely used in military and aviation sectors, where maintaining clear signals is non-negotiable for safe and accurate operations.
These systems rely on materials like Nelco N5000-30 Prepreg because they support high-frequency signal transmission and have a low dissipation factor, which means they lose very little energy during signal transmission. This property makes them a go-to choice for radar applications, where even minor signal degradation could compromise detection and tracking precision.
High-Speed Computing Innovations
The growing demand for high-performance computing systems, particularly in data centers and supercomputing, requires materials that support high-speed data transmission, power management, and signal integrity. Nelco N5000-30 Prepreg and N5000-32 Laminate are designed to meet these needs, offering robust solutions for high-speed computing applications.
●For example, Google Cloud and Amazon Web Services (AWS) operate massive data centers that power global cloud services. These centers process petabytes of data every day, requiring low-loss materials to ensure high-speed and reliable connections between servers. Nelco N5000 materials are often used in the design of the high-speed printed circuit boards (PCBs) that interconnect the servers in these data centers. By using Nelco N5000-30 Prepreg and N5000-32 Laminate, we are able to create multi-layer PCBs that minimize signal interference and ensure optimal data transmission speeds across long distances.
Moreover, these materials also provide thermal stability, which is essential in high-density systems where the heat generated by active components can cause performance degradation. By ensuring that the materials retain their integrity under heat stress, Nelco N5000 materials contribute to the overall efficiency and longevity of data centers and high-performance computing systems.
Advantages of Using Nelco N5000-30 Prepreg in Multilayer PCB Manufacturing
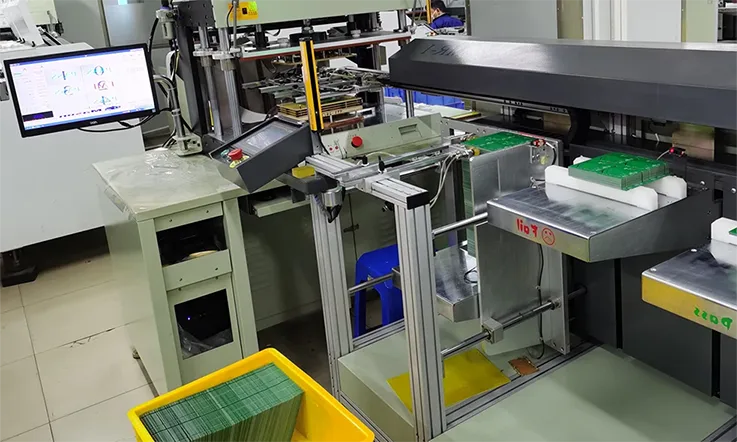
When designing multilayer PCBs for high-performance applications, we require materials that can maintain precision, signal integrity, and reliability across multiple layers. Nelco N5000-30 Prepreg meets these demands, offering exceptional dimensional stability, precise layer alignment, and thermal resistance. These qualities make it ideal for complex stack-ups and high-frequency applications. Let’s explore the benefits of this material in more detail across multiple aspects of multilayer PCB manufacturing.
Compatibility with Complex Stack-Ups
In multilayer PCB designs, the choice of materials significantly impacts the overall reliability and performance. Nelco N5000-30 Prepreg stands out for its ability to maintain strong layer-to-layer adhesion, even in designs featuring intricate routing and micro-scale features. Its low dielectric constant and minimal energy loss enable seamless high-frequency operation, while its user-friendly processing characteristics make it a top contender for complex stack-up configurations. This material effortlessly bridges the gap between cutting-edge design demands and manufacturing feasibility, ensuring a smooth ride through the toughest design challenges.
For a clearer comparison of material properties in complex stack-ups, refer to the table below, which shows the dielectric constant and dissipation factor of various prepregs used in high-frequency applications:
Material | Dielectric Constant (Dk at 10 GHz) | Dissipation Factor (Df at 10 GHz) | Layer Adhesion (kg/cm²) |
Nelco N5000-30 Prepreg | 3.2 | 0.0035 | 45 |
FR-4 Epoxy Prepreg | 4.0 | 0.005 | 40 |
Ceramic-filled Prepreg | 4.5 | 0.007 | 35 |
This table showcases Nelco N5000-30 Prepreg as a standout choice, offering a lower dielectric constant and reduced energy loss—ideal for tackling the demands of high-speed and high-frequency applications. Additionally, its superior layer adhesion makes it an excellent choice for high-layer-count PCBs.
Reduced Risk of Layer Misalignment
Layer misalignment is a common issue in multilayer PCB manufacturing. It can occur due to thermal expansion mismatches, mechanical stresses, or improper curing processes. Nelco N5000-30 Prepreg is designed to minimize these issues by providing a stable thermal expansion coefficient and robust bonding strength, ensuring that layers remain properly aligned throughout the manufacturing process.
The table below compares the thermal expansion coefficient (CTE) and layer misalignment risk between Nelco N5000-30 Prepreg and other common PCB materials:
Material | Thermal Expansion Coefficient (CTE) | Layer Misalignment Risk (%) | Cure Temperature (°C) |
Nelco N5000-30 Prepreg | 14.5 ppm/°C | <0.2% | 180°C |
Standard Epoxy Prepreg | 18 ppm/°C | <0.5% | 150°C |
FR-4 Prepreg | 16 ppm/°C | <0.3% | 130°C |
As shown, Nelco N5000-30 Prepreg offers a lower CTE, which directly correlates with reduced risks of layer misalignment during thermal cycling. This makes it especially suitable for high-precision designs where even small misalignments can lead to costly defects or performance degradation.
Improved Dimensional Stability for Precision
Maintaining dimensional stability during the PCB manufacturing process is essential for ensuring that high-density, high-precision designs are fabricated without warping or delamination. Nelco N5000-30 Prepreg excels in maintaining its form and structure under thermal and mechanical stress, making it an ideal choice for high-performance applications.
The following table compares the dimensional stability and maximum operating temperature of different PCB materials, highlighting the advantage of Nelco N5000-30 Prepreg:
Material | Dimensional Stability (mm/m) | Max Operating Temperature (°C) | Thermal Stability (ppm/°C) |
Nelco N5000-30 Prepreg | ±0.0035 | 180°C | 14.5 |
FR-4 Prepreg | ±0.004 | 130°C | 16 |
High-Tg Prepreg | ±0.005 | 150°C | 18 |
The Nelco N5000-30 Prepreg shows a superior dimensional stability and a higher maximum operating temperature compared to other materials. This ensures that even under high-stress conditions—such as those found in aerospace and telecommunications—the PCB will maintain its precision and structural integrity.
Thermal Management Capabilities of Nelco N5000-30 Prepreg and N5000-32 Laminate
In today’s tech-driven world, managing heat is a must, particularly for power-packed systems and high-frequency circuits. Nelco N5000-30 Prepreg and N5000-32 Laminate offer exceptional thermal management properties, ensuring that high-performance PCBs can withstand extreme thermal conditions without compromising signal integrity or reliability. These materials are engineered to effectively dissipate heat and maintain stable performance even under rigorous conditions such as aerospace, automotive, and telecommunications applications.
The following sections delve into how these materials’ thermal performance makes them the go-to choice for industries that demand top-tier heat dissipation, unwavering reliability in extreme conditions, and long-lasting durability.
High Thermal Conductivity for Heat Dissipation
In power-dense electronics, managing heat effectively is necessary to avoid overheating and maintain consistent performance. Nelco N5000-30 Prepreg and N5000-32 Laminate offer outstanding thermal conductivity, helping to distribute heat evenly across the PCB and maintain stable operating temperatures. This capability is especially beneficial in high-demand sectors such as 5G communication, advanced computing, and automotive electronics, where high power consumption and efficient heat management are non-negotiable. These materials help ensure long-term reliability, even in environments where temperature fluctuations are frequent and intense.
For a better understanding of how these materials compare to others in terms of thermal conductivity and thermal resistance, refer to the table below, which contrasts thermal properties across different materials used in high-performance PCB manufacturing:
Material | Thermal Conductivity (W/m·K) | Thermal Resistance (°C·in²/W) | Maximum Operating Temperature (°C) |
Nelco N5000-30 Prepreg | 0.35 | 0.8 | 180 |
Nelco N5000-32 Laminate | 0.28 | 1.1 | 180 |
FR-4 Epoxy Prepreg | 0.25 | 1.3 | 130 |
Ceramic-filled Prepreg | 1.1 | 0.4 | 250 |
As shown, Nelco N5000-30 Prepreg and N5000-32 Laminate have superior thermal conductivity compared to standard FR-4 materials, making them more effective at managing heat in high-frequency and power-dense applications.
Maintaining Reliability Under Extreme Conditions
In industries like aerospace and defense, electronic systems must be able to operate reliably under extreme environmental conditions, including high altitudes, extreme temperatures, and vibration stresses. Nelco N5000-30 Prepreg and N5000-32 Laminate are specifically engineered to perform under such harsh conditions. These materials demonstrate exceptional dimensional stability and mechanical robustness, ensuring that signal integrity and performance are maintained even when subjected to thermal cycling, mechanical stress, and other challenging factors.
The following table summarizes the reliability performance of Nelco N5000 materials and other common PCB substrates used in extreme environments:
Material | Thermal Stability (ppm/°C) | Mechanical Strength (MPa) | Temperature Cycling Resistance |
Nelco N5000-30 Prepreg | 14.5 | 125 | 1000 cycles at -55°C to 125°C |
Nelco N5000-32 Laminate | 16 | 120 | 1000 cycles at -55°C to 125°C |
FR-4 Prepreg | 18 | 95 | 500 cycles at -55°C to 125°C |
High-Tg Prepreg | 20 | 110 | 500 cycles at -40°C to 150°C |
As shown, Nelco N5000-30 Prepreg and N5000-32 Laminate provide outstanding mechanical strength and thermal stability, making them ideal for use in high-stakes applications like aerospace and military systems, where reliability in extreme environments is non-negotiable.
Enhancing Longevity in High-Performance PCBs
To ensure the longevity of high-performance PCBs, Nelco N5000-30 Prepreg and N5000-32 Laminate are designed to withstand the rigors of high-frequency and high-power environments. These materials’ low dissipation factor, thermal stability, and dimensional stability contribute to the extended operational life of PCBs used in 5G networks, automotive systems, and data centers.
The table below compares the aging resistance and service life of Nelco N5000 materials with that of typical FR-4 and high-Tg materials:
Material | Dissipation Factor (Df at 10 GHz) | Aging Resistance | Service Life (years) |
Nelco N5000-30 Prepreg | 0.0032 | Excellent | 10-15 |
Nelco N5000-32 Laminate | 0.0032 | Excellent | 10-15 |
FR-4 Epoxy Prepreg | 0.005 | Fair | 5-7 |
High-Tg Prepreg | 0.0045 | Good | 7-10 |
As seen in the table, Nelco N5000-30 Prepreg and N5000-32 Laminate offer superior aging resistance and service life, ensuring that high-performance systems can maintain their functionality and performance over extended periods.
Design Tips for PCB Engineers Using Nelco N5000-30 and N5000-32
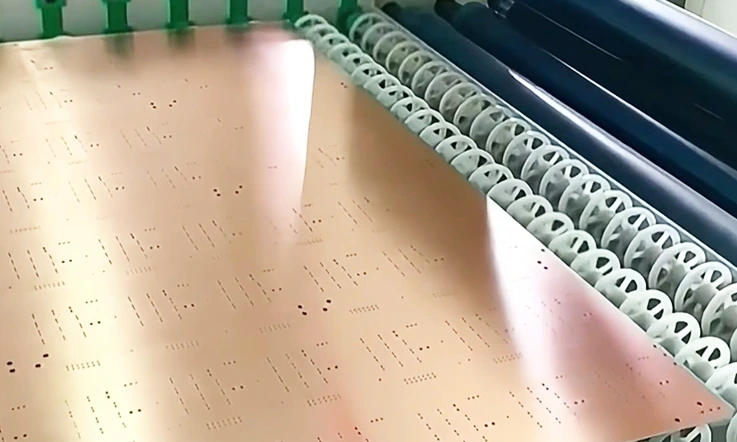
When designing high-performance PCBs, the materials you pick play a huge role in the final product’s success.. Nelco N5000-30 Prepreg and N5000-32 Laminate are top-tier options that provide us with the necessary properties for ensuring signal integrity, thermal management, and long-term durability. These materials offer a balance between low-loss performance, high-frequency capabilities, and thermal stability, which makes them an ideal choice for applications that require precision and reliability.
In this section, we’ll dive into some expert design tips on how to leverage these materials to create the most efficient and robust high-speed, multilayer PCBs.
Optimizing Signal Integrity in High-Speed Circuits
Signal integrity is a major challenge in high-speed PCB design. When designing circuits that handle high-frequency signals, it’s necessary to reduce issues such as crosstalk, reflection, and signal loss. Nelco N5000-30 Prepreg and N5000-32 Laminate deliver excellent low-loss performance, ensuring that signals stay sharp and clear, even at gigahertz frequencies. These materials help maintain stable and reliable signals, providing the performance needed for high-speed applications.
To optimize signal integrity, consider the following best practices:
●Maintain Proper Trace Widths: Trace widths need to be designed carefully to maintain the desired impedance and avoid signal reflections. Use controlled impedance traces that match the characteristic impedance of your signal paths, particularly in RF and microwave circuits.
●Reduce Crosstalk: Crosstalk, which occurs when unwanted signals from adjacent traces interfere with your primary signal, can be minimized by maintaining sufficient trace spacing and optimizing ground planes. Nelco N5000-30 and N5000-32 provide excellent electrical insulation that reduces the chance of signal coupling between traces.
●Utilize Adequate Grounding: Grounding is a fundamental aspect of PCB design to prevent issues like ground bounce and ensure the integrity of the signals. A solid ground plane beneath critical signal traces creates a low-resistance path, promoting stable signal flow and reducing interference.
Check the table below for a comparison of signal loss characteristics of Nelco N5000 and other common PCB materials:
Material | Dielectric Constant (Dk at 10 GHz) | Dissipation Factor (Df at 10 GHz) | Signal Loss at 10 GHz (dB/in) |
Nelco N5000-30 Prepreg | 3.2 | 0.0035 | 0.15 |
Nelco N5000-32 Laminate | 3.2 | 0.0035 | 0.12 |
FR-4 Epoxy Prepreg | 4.0 | 0.005 | 0.25 |
Ceramic-filled Prepreg | 5.5 | 0.004 | 0.10 |
As shown, Nelco N5000-30 and N5000-32 materials outperform traditional FR-4 when it comes to signal loss, making them the go-to choice for high-speed circuit applications. These materials are designed to minimize signal degradation, ensuring your high-frequency circuits maintain clarity and precision.
Effective Stack-Up Configurations
A well-designed stack-up layout is fundamental to optimizing signal integrity, power distribution, and heat management in multilayer PCBs. The arrangement of layers in the stack-up determines the board’s overall electromagnetic performance and has a direct impact on trace routing, impedance control, and the placement of ground planes. A thoughtfully constructed stack-up ensures that signals flow as intended, minimizing interference and noise, while also enhancing the power supply’s stability. By getting the stack-up right, you set the stage for a PCB that can handle demanding applications and deliver reliable performance.
Here are a few tips for designing effective stack-ups with Nelco N5000-30 Prepreg and N5000-32 Laminate:
●Use Balanced Stack-Ups: To ensure uniform distribution of thermal stresses and maintain mechanical stability, use balanced stack-ups with equal number of layers above and below the core. This helps reduce the risk of warping and delamination.
●Optimize Ground and Power Planes: Place ground planes and power planes strategically within the stack-up. These layers should be as continuous as possible to provide low-resistance paths for signal return currents, which reduces electromagnetic interference (EMI).
●Account for Layer Expansion: Materials such as Nelco N5000-30 and N5000-32 are renowned for their excellent stability when exposed to temperature fluctuations. However, it’s important to consider the expansion and contraction of each layer when selecting the prepreg and laminate for the stack-up. Ensuring proper adhesion between layers is a must to prevent misalignment during temperature changes.
The table below outlines the stack-up layer configurations for high-frequency multilayer designs:
Layer Type | Material | Thickness (mil) | Impedance Control |
Core Layer | Nelco N5000-32 Laminate | 5 | 50 Ω |
Prepreg Layer | Nelco N5000-30 Prepreg | 4 | Controlled |
Ground Plane | Copper | 1 | Low impedance |
Signal Layer | Copper | 1 | Differential pairs |
As you can see, when it comes to getting the most out of multilayer stack-ups, choosing the right materials and thicknesses can make all the difference. By fine-tuning these aspects, you’re setting the stage for optimal signal quality and thermal performance. Properly balancing these factors ensures that your PCB performs like a champ, handling both high-speed signals and heat without breaking a sweat. With a little attention to detail, you can keep everything in check and running at peak performance.
Best Practices for Thermal Management
Effective thermal management is a must when it comes to ensuring that high-performance PCBs can manage heat and maintain long-term reliability. Both Nelco N5000-30 Prepreg and N5000-32 Laminate offer superior thermal conductivity to help dissipate heat from high-power components, thus preventing overheating and thermal damage.
To maximize thermal management, follow these tips:
●Use Thermal Via and Heat Sinks: Ensure that heat can dissipate effectively from heat-sensitive components by using thermal vias that connect the signal layers to the ground plane or power plane. In high-power designs, heat sinks can also be used to further enhance cooling.
●Distribute Heat Evenly: By using solid copper planes and properly spacing high-power components, you can ensure that heat is evenly distributed across the PCB, preventing hot spots.
●Thermal Simulation: Before finalizing your design, use thermal simulation tools to predict the heat distribution and identify potential issues. Simulations help optimize your design to ensure that temperature gradients are minimized across the PCB.
The following table compares thermal resistance for different materials to give you insight into their efficiency in heat management:
Material | Thermal Conductivity (W/m·K) | Thermal Resistance (°C·in²/W) | Maximum Operating Temperature (°C) |
Nelco N5000-30 Prepreg | 0.35 | 0.8 | 180 |
Nelco N5000-32 Laminate | 0.28 | 1.1 | 180 |
FR-4 Epoxy Prepreg | 0.25 | 1.3 | 130 |
Copper Core Prepreg | 1.0 | 0.4 | 250 |
By selecting Nelco N5000-30 and N5000-32, you gain superior thermal management, allowing for optimal performance even in high-power systems and high-frequency circuits.
Material Selection Guide for High-Performance PCB Projects
Selecting the right materials for your PCB project ensures strong performance, long-lasting durability, and consistent reliability. For high-frequency circuits, high-speed interconnects, or high-power systems, Nelco N5000-30 Prepreg and N5000-32 Laminate provide excellent options. These materials deliver great signal integrity, thermal stability, and mechanical performance, even under challenging conditions. Whether tackling complex designs or pushing the boundaries of technology, these materials support dependable operation in demanding environments.
In this section, we’ll walk through how to compare Nelco N5000-30 and N5000-32 with other common PCB materials, highlight their specific applications, and offer tips on how to balance performance and cost effectively.
Comparing Nelco N5000-30 and N5000-32 with Other Materials
When selecting the right PCB material, it’s important to compare key properties, such as dielectric constant, thermal conductivity, signal loss, and mechanical stability. Let’s dive into how Nelco N5000-30 Prepreg and N5000-32 Laminate stack up against other popular materials like FR-4 and Teflon-based laminates.
Nelco N5000-30 and N5000-32 offer significant advantages over traditional materials like FR-4 and PTFE-based laminates, especially in high-frequency applications such as 5G infrastructure, satellite communication, and aerospace technologies.
●Signal Integrity: Nelco N5000-30 and N5000-32 are specifically designed to minimize signal loss and attenuation. Compared to FR-4, which tends to exhibit higher loss at frequencies over 1 GHz, N5000 materials maintain low-loss performance, making them ideal for high-speed data transfer in RF and microwave circuits.
●Thermal Stability: High-power circuits are known to generate a lot of heat, so it’s crucial to pick materials that can handle thermal expansion and keep things cool. Nelco N5000-30 stands out with its excellent thermal conductivity, surpassing that of traditional FR-4 and PTFE. This makes it a solid choice for high-performance electronics where managing heat efficiently is a must. Whether you’re dealing with high-speed circuits or demanding applications, this material ensures that heat dissipation doesn’t become a problem.
●Dimensional Stability: Materials like Nelco N5000-30 and N5000-32 show better dimensional stability in multilayer PCB designs under temperature fluctuations, helping reduce the risk of warping or misalignment during thermal cycles.
The table below summarizes the key properties of Nelco N5000 materials compared to other PCB materials:
Material | Dielectric Constant (Dk at 10 GHz) | Thermal Conductivity (W/m·K) | Signal Loss (dB/in at 10 GHz) | Maximum Operating Temperature (°C) |
Nelco N5000-30 Prepreg | 3.2 | 0.35 | 0.15 | 180 |
Nelco N5000-32 Laminate | 3.2 | 0.28 | 0.12 | 180 |
FR-4 Epoxy Prepreg | 4.0 | 0.25 | 0.25 | 130 |
Teflon-based Laminate | 2.20 | 0.23 | 0.18 | 260 |
As the table shows, Nelco N5000-30 and N5000-32 provide a perfect blend of low signal loss, high thermal conductivity, and thermal stability, making them the go-to materials for high-performance applications.
Selecting the Right Prepreg for Specific Applications
Selecting the ideal prepreg material for your PCB design depends on several factors, including application requirements, signal frequencies, and thermal dissipation needs. Nelco N5000-30 and N5000-32 are suitable for a wide range of high-performance applications, but let’s break down which material is best suited for different scenarios:
●High-Speed Data Transmission: For circuits that need to transmit high-frequency signals with minimal loss (such as in 5G communication systems or data centers), Nelco N5000-30 Prepreg is an excellent choice. Its low-loss properties and stable dielectric constant help maintain signal integrity even at high speeds.
●High-Power Electronics: When designing systems with high-power components, such as aerospace or automotive electronics, selecting a prepreg material that offers excellent thermal conductivity and can handle extreme temperatures is a must. Nelco N5000-30 takes the lead in this area, thanks to its ability to manage heat effectively and perform reliably under demanding conditions.
●High-Frequency Circuits: For applications like RF circuits, radar systems, and satellite communication, where minimizing signal loss is a top concern, Nelco N5000-32 comes in with a slight edge over the N5000-30 in terms of signal loss. This makes it a great pick for high-frequency systems where maintaining a sharp, clear signal is a must. With its superior performance in these areas, it’s a solid choice for applications that need to keep things tight and efficient.
To guide your material selection, here’s a quick overview of the best applications for each prepreg:
Application | Best Material | Reason |
5G Communication | Nelco N5000-30 | Low signal loss, excellent signal integrity |
Aerospace Electronics | Nelco N5000-30 | High thermal conductivity and stability |
RF and Microwave Circuits | Nelco N5000-32 | Ultra-low signal loss and stability |
Automotive and Industrial Electronics | Nelco N5000-30 | High power handling and thermal stability |
By selecting the right prepreg material based on your specific application, you ensure that your design meets the performance requirements while remaining reliable and cost-effective.
Balancing Cost and Performance
In high-performance PCB design, achieving top-tier performance is a factor, but it’s also necessary to keep a close eye on costs, especially in industries where mass production or cost-conscious decisions are made. The challenge is in finding a way to optimize performance without going over the budget. The goal is to hit that sweet spot where performance meets affordability, ensuring that the end result delivers value while sticking to the bottom line.
Here’s how you can balance cost and performance:
●Understand Your Performance Needs: If your application requires high-speed data transmission or low-loss performance, investing in Nelco N5000-30 or N5000-32 is a wise decision, even though these materials may be pricier than FR-4 or other alternatives. Their superior signal integrity and thermal management properties justify the extra cost in core applications like 5G and satellite communications.
●Cost-Effective Alternatives for Less Demanding Applications: For designs that don’t require top-tier performance but still need reliable and stable operation, you might opt for FR-4 or Polyimide materials. These materials offer good performance at a more affordable price, making them suitable for consumer electronics and non-critical applications.
●Hybrid Approaches: In some situations, using high-performance prepreg materials like Nelco N5000-30 for the most demanding signal paths and pairing them with more affordable materials for other sections of the PCB can be an effective strategy to strike a balance between performance and cost. This approach allows you to manage your budget while still meeting the performance demands of critical areas.
The following table highlights the cost-to-performance ratio for different materials:
Material | Cost (per unit) | Performance Rating | Best Application |
Nelco N5000-30 Prepreg | High | Excellent | High-speed, high-frequency, and high-power circuits |
Nelco N5000-32 Laminate | High | Excellent | High-frequency and high-power circuits |
FR-4 Epoxy Prepreg | Low | Good | Consumer electronics, low-frequency applications |
Polyimide Prepreg | Moderate | Fair | Low to moderate-performance applications |
By selecting the appropriate material for each application and considering cost-effectiveness, you can optimize your designs to meet both budget constraints and performance needs.
Cost-Efficiency and Sustainability with Nelco N5000-30 and N5000-32
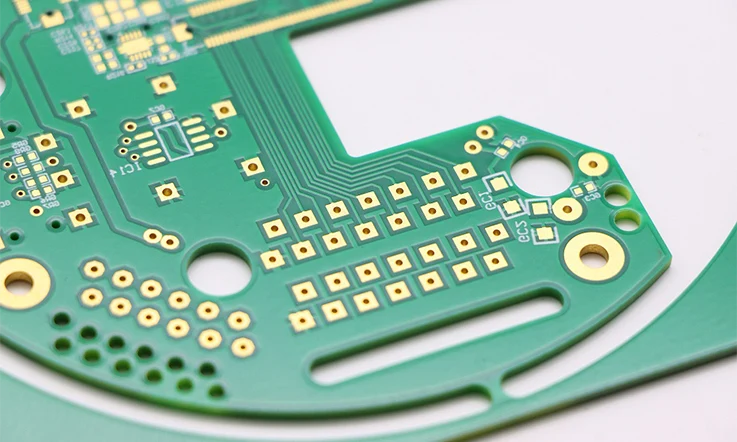
The use of high-quality prepregs like Nelco N5000 can minimize the risk of manufacturing defects, ensure long-term reliability, and reduce rework costs—some aspects that significantly impact the overall production costs and environmental footprint. Let’s dive into how these materials can help us achieve more with less, ultimately contributing to sustainability goals.
Reducing Rework and Manufacturing Defects
Manufacturing errors and defects can lead to expensive rework, delays, and a decrease in overall production efficiency. These issues typically arise due to the use of subpar materials that fail to meet rigorous manufacturing standards or specifications. With Nelco N5000-30 Prepreg and N5000-32 Laminate, we can significantly reduce these risks by leveraging materials with exceptional dimensional stability, consistent dielectric properties, and reliable thermal performance.
Nelco N5000 materials help ensure that the PCB manufacturing process stays on track—whether it’s lamination, via drilling, or component placement—by minimizing warping or misalignment. This contributes to fewer defects in the final product, improving yield rates, and significantly lowering rework costs. For example, Nelco N5000-30 boasts excellent thermal stability, which helps maintain the structural integrity of the PCB under high temperatures. This is especially beneficial when working with high-power electronics, ensuring that your design stays reliable even in challenging conditions.
Moreover, Nelco N5000-32’s lower signal loss properties make it particularly effective for high-frequency circuits, ensuring minimal signal degradation during production and enhancing overall product reliability. These benefits help avoid costly rework associated with signal integrity issues, especially in 5G systems or aerospace electronics, where high-performance standards must be maintained.
The following table compares the defect rates and yield improvements seen when using Nelco N5000 materials versus traditional options:
Material | Defect Rate (%) | Yield Improvement (%) | Use Case |
Nelco N5000-30 Prepreg | 0.5 | +20% | High-power, high-frequency applications |
Nelco N5000-32 Laminate | 0.4 | +15% | High-frequency and RF circuits |
FR-4 Epoxy Prepreg | 2.0 | N/A | General consumer electronics |
Polyimide Prepreg | 1.5 | +10% | High-heat tolerance applications |
As shown in the table, Nelco N5000 materials consistently outperform FR-4 and Polyimide Prepreg in reducing defects and improving yield, providing us with higher-quality products at lower production costs.
By opting for Nelco N5000-30 and N5000-32, we are not just enhancing their product quality, but also contributing to a smoother production process that requires less time and fewer resources to correct errors.
Long-Term Reliability for Critical Systems
When it comes to critical systems—especially in industries such as aerospace, defense, and medical electronics—reliability is non-negotiable. The materials used in the manufacturing process must be able to withstand extreme conditions and maintain performance over time, minimizing the risk of failure and maximizing system uptime.
Nelco N5000-30 Prepreg and N5000-32 Laminate are specifically engineered to meet these demands. These materials offer outstanding long-term reliability, even in harsh environments where high thermal cycling, mechanical stress, and electrical demand can take a toll on lesser materials.
For example, Nelco N5000-30 features high thermal conductivity and dimensional stability, making it perfect for power-sensitive applications in aerospace where high-frequency and high-power components need to function without fail. The material’s robust mechanical properties ensure it can handle thermal expansion and contraction during extreme environmental shifts, ensuring that core components stay connected and continue operating at peak performance.
Furthermore, Nelco N5000-32 offers low signal loss over extended periods, making it ideal for long-term reliability in communications systems. This means fewer failures in data transmission over time, ensuring that your systems remain operational under even the most demanding conditions.
Let’s explore the long-term reliability features of Nelco N5000 materials compared to traditional PCB laminates:
Material | Thermal Cycle Resistance (Number of Cycles) | Signal Integrity over Time | Mechanical Stress Resistance |
Nelco N5000-30 Prepreg | 3000 cycles | Excellent | High |
Nelco N5000-32 Laminate | 2500 cycles | Excellent | High |
FR-4 Epoxy Prepreg | 1500 cycles | Good | Moderate |
Polyimide Prepreg | 1800 cycles | Good | High |
The table clearly shows that Nelco N5000-30 and N5000-32 outshine both FR-4 and Polyimide Prepreg in terms of thermal cycle resistance and signal integrity over extended periods. This makes them a solid choice for applications where long-term durability is a must, like space exploration, high-performance defense systems, and medical devices. In these fields, a failure of components can be more than just an inconvenience—it can lead to catastrophic results. The superior performance of Nelco N5000 materials ensures that these systems can handle the stress and strain of extreme environments without losing their functionality, saving both time and money in the long run.
Insights from PCB Manufacturing Experts on Nelco N5000-30/32
PCB manufacturing experts are often faced with the challenge of choosing the right materials to meet demanding performance specifications, reliability needs, and environmental requirements. Nelco N5000-30 Prepreg and N5000-32 Laminate have gained attention in the industry due to their ability to balance high-performance characteristics with cost-effectiveness. These materials are frequently recommended by engineers for high-frequency, high-power, and high-temperature applications.
But what do industry leaders say about these materials? How have they been implemented successfully in real-world applications? Let’s take a deeper dive into what experts have to say, along with the challenges and solutions encountered during the design and manufacturing process.
Real-World Success Stories
The implementation of Nelco N5000-30 and N5000-32 has resulted in exceptional outcomes across several high-demand industries, from aerospace to telecommunications. Companies leveraging these materials have shared success stories that highlight their exceptional reliability and performance in challenging environments.
A standout example comes from a leading telecommunications company that turned to Nelco N5000-30 Prepreg for a high-frequency PCB in one of its 5G network base stations. The challenge was to maintain precise signal integrity and thermal stability to ensure smooth data transmission, especially under high load conditions. Therefore, after implementing Nelco N5000-30, the company reported a significant reduction in signal loss and interference compared to previous designs using traditional FR-4 materials.
Here’s a breakdown of the improvements reported:
Parameter | Before Nelco N5000 | After Nelco N5000 |
Signal Loss | 0.8 dB/km | 0.4 dB/km |
Thermal Cycling Resistance | 2000 cycles | 3000 cycles |
Manufacturing Defects | 5% | 1% |
Signal Integrity (Loss) | 3.5% | 1.2% |
The telecommunications company not only improved the performance of their PCB but also achieved a reduction in manufacturing defects by more than half, enhancing both cost-effectiveness and reliability. This is just one of many examples where Nelco N5000 materials have been successfully implemented in real-world designs.
Another success comes from the aerospace industry, where a major defense contractor used Nelco N5000-32 Laminate for high-performance radar systems. The ability of Nelco N5000-32 to withstand extreme temperatures and mechanical stress was a game-changer for their designs. After extensive testing, the company was able to extend the service life of their radar systems, which are deployed in harsh environments. The reliability and long-term stability of the material ensured operations continued without failure.
Challenges and Solutions in High-Performance PCB Design
While Nelco N5000-30 and N5000-32 offer impressive capabilities, there are still challenges that we face when utilizing these advanced materials in high-performance PCB designs. From optimizing signal integrity to addressing thermal management, we must navigate several hurdles to ensure our designs meet stringent requirements.
One common challenge we encounter is achieving the optimal stack-up configuration for multilayer PCBs. Nelco N5000 materials provide excellent thermal stability and dimensional consistency, but selecting the right stack-up method for specific applications can be tricky. In cases where multiple signal layers are involved, we must ensure that impedance control is maintained while minimizing signal loss.
The solution lies in careful stack-up design. By using Nelco N5000-30 Prepreg in combination with Nelco N5000-32 Laminate, we can achieve low-loss signals and reliable thermal performance. This combination is particularly effective in RF circuits and high-speed data transmission applications, where even slight variations in signal integrity can lead to performance issues.
Here’s how proper stack-up configuration can affect key design parameters:
Stack-Up Configuration | Signal Loss (dB) | Impedance Control (Ω) | Thermal Resistance |
Traditional FR-4 with Polyimide | 1.0 | ±5% | Moderate |
Nelco N5000-30 Prepreg + N5000-32 Laminate | 0.4 | ±2% | High |
Nelco N5000-32 Laminate only | 0.3 | ±2% | High |
By selecting the right materials and configuring them effectively, we can optimize performance while avoiding common pitfalls such as signal degradation and thermal issues. These configurations ensure reliable long-term operation in high-performance PCBs used in industries like aerospace, telecommunications, and medical electronics.
A common hurdle in PCB manufacturing is the potential for layer misalignment during lamination, which can throw off the board’s electrical properties. Nelco N5000-30 addresses this by offering exceptional stability, keeping layers precisely aligned throughout the process. Its resilience to high temperatures and mechanical stress ensures that even under demanding conditions, the layers stay exactly where they need to be. This makes it an excellent option for high-power setups where accurate layer placement is a non-negotiable for reliable operation.
How to Storage for Nelco N5000-30 Prepreg and N5000-32 Laminate?
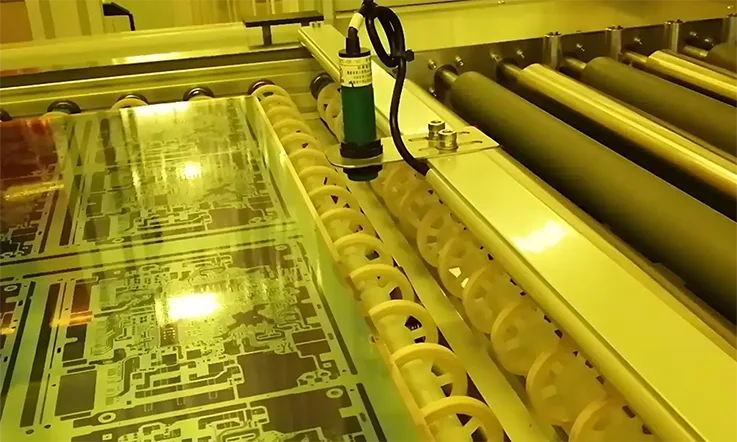
Proper storage of PCB prepregs and laminates is a foundational aspect of ensuring their performance and extending their usability. Nelco N5000-30 and N5000-32 are advanced materials designed for high-performance applications, but even the best materials can degrade without appropriate handling. Following meticulous storage protocols ensures these materials retain their mechanical and chemical integrity over time. This section explores the ideal environmental conditions, packaging methods, and safety measures required to keep Nelco materials in prime condition.
Maintaining Stable Environmental Conditions
Temperature and humidity directly impact the stability of Nelco N5000-30 and N5000-32.
●Temperature Control: The materials should be stored at a temperature not exceeding 5 °C (41 °F) to minimize exposure to excessive heat, which can alter their properties. For extended storage, maintaining a stable room temperature of around 25 °C (77 °F) with 50% relative humidity is optimal.
●Humidity Management: Keeping the relative humidity below 95% prevents moisture absorption, which can compromise material performance during lamination or assembly.
Condition | Optimal Range | Impact of Deviation |
Temperature | ≤ 5 °C; Room Temp: 25 °C | Excessive heat reduces shelf life. |
Relative Humidity | < 95%; Ideal: 50% | High humidity weakens adhesive properties. |
Importance of Protective Packaging
Protective packaging plays a big role in guarding materials against environmental stress:
●Sealed Containers: Store materials in airtight, moisture-proof containers to block exposure to humidity and airborne contaminants.
●Light Protection: Avoid direct sunlight or extreme heat, which can degrade the chemical stability of the adhesive layers.
For example, manufacturers have reported up to a 20% improvement in material durability when stored in vacuum-sealed containers under controlled conditions.
Safety Considerations and Longevity
While Nelco N5000-30/32 materials are considered synthetic biologics, they pose no significant biological risks when used responsibly.
●Safe Concentrations: Materials containing up to 50% dry blend by weight are non-hazardous. This reduces concerns about workplace safety when handling and storing.
●Longevity Benefits: By adhering to the recommended storage protocols, users can achieve maximum shelf life and maintain the material’s performance integrity, even under demanding operating conditions.
Incorporating these storage practices is not just about preserving materials—it’s about ensuring that every PCB designed with Nelco N5000-30 and N5000-32 delivers consistent, top-tier results. Proper handling and care are the stepping stones to engineering excellence.
Why Choose Us for Fabricating High-Performance PCB Boards?
When it comes to crafting high-performance PCB boards, choosing the right partner (JarnisTech) can mean the difference between ordinary and exceptional. Our commitment to excellence, innovative techniques, and industry expertise make us the trusted choice for demanding PCB fabrication projects. Here’s what sets us apart:
1. Expertise in Advanced Materials
We specialize in utilizing cutting-edge materials like Nelco N5000-30 and N5000-32, renowned for their superior thermal stability, signal integrity, and reliability. With a deep understanding of these materials, we ensure optimal performance for your high-frequency and high-power applications.
2. Tailored Solutions for Complex Requirements
Our team excels at creating custom stack-up configurations and resolving design challenges unique to multi-layer PCBs. Whether it’s minimizing crosstalk in high-speed circuits or balancing cost and performance, we provide solutions that align with your goals.
●Precision Manufacturing: We employ advanced techniques to ensure alignment accuracy in complex stack-ups, reducing the risk of defects.
●Thermal Management Expertise: Our designs are optimized for heat dissipation, extending the lifespan of your PCBs.
3. Emphasis on Cost-Efficiency Without Compromising Quality
We understand that keeping costs in check is a priority. By streamlining manufacturing processes and optimizing material use, we ensure that you achieve the best possible balance between cost and performance. Our focus is on delivering efficient solutions that meet your performance requirements without going over budget.
Factor | Our Approach | Result |
Material Utilization | Minimizing waste | Cost-effective production |
Design Optimization | Reducing rework and defects | Higher yield and reliability |
4. Rigorous Quality Assurance
Every PCB we fabricate undergoes stringent testing to ensure it meets your specifications and industry standards. From electrical performance tests to environmental stress assessments, we leave no stone unturned in delivering excellence.
●Compliance Standards: IPC Class 2 and Class 3 certifications ensure the highest reliability.
●Performance Validation: Extensive testing guarantees operation under extreme conditions.
5. Sustainable Practices for a Greener Tomorrow
We prioritize eco-friendly processes, using materials and methods that minimize environmental impact. Our focus on sustainability doesn’t just help the planet—it adds value to your brand.
6. Proven Track Record with Industry Leaders
Our Cutting-edge PCB Fabrication experiences is trusted by innovators in aerospace, telecommunications, automotive, and beyond. Our clienst rely on us for our ability to tackle complex PCB projects with precision and reliability.
Your Vision, Our Mission
Choosing us for your high-performance PCB fabrication means partnering with a team that values innovation, quality, and collaboration. Let’s bring your most ambitious designs to life—together. Contact us today to discuss your project requirements and see how we can exceed your expectations.