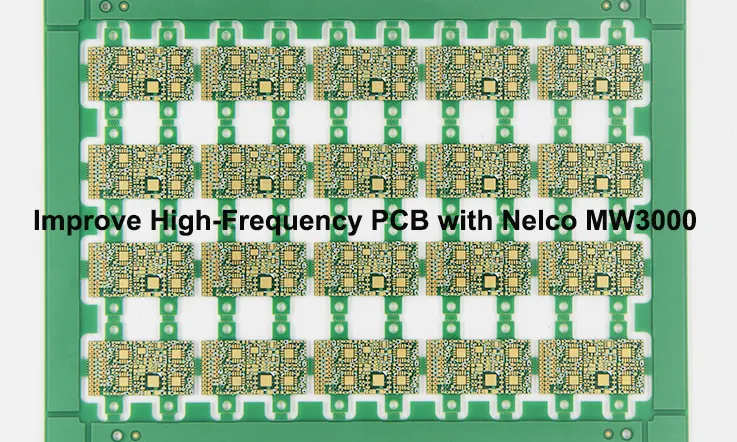
In high-frequency PCB design, choosing the right materials can significantly impact the performance and reliability of your circuits. Nelco MW3000 PCB laminates have gained popularity for their excellent electrical properties and thermal stability, making them suitable for high-speed, high-frequency applications.
This guide provides an in-depth look at Nelco MW3000, covering its core features and the considerations for effectively integrating it into PCB manufacturing. Therefore, whether working on RF circuits, 5G technology, or high-speed data transmission, knowing how to optimize the use of Nelco MW3000 can help you achieve solid results with fewer challenges. At the same time, we will also explore its compatibility with lead-free assembly, how it fits with standard PCB fabrication techniques, and how its high-TG properties aid in efficient production.
Introduction to Nelco MW3000 PCB Laminates
Designing high-frequency PCBs for advanced electronics requires careful selection of materials to ensure the circuit boards perform as expected. Nelco MW3000 PCB Laminates are engineered specifically for this purpose, offering properties that support demanding applications such as 5G technology, supercomputing, and RF/microwave systems. These laminates help ensure designs can manage high-speed data and maintain consistent performance in complex environments.
When designing high-frequency PCBs, choosing the right material helps prevent signal loss and ensures steady performance. Nelco MW3000 is engineered to offer low dielectric loss and solid signal integrity, making it a reliable choice for high-speed applications where precision matters. This material addresses common challenges in high-frequency designs, ensuring stable and consistent performance across the board.
What Are Nelco MW3000 PCB Laminates and Why Are They Valuable?
Nelco MW3000 is a laminate designed for high-frequency PCB applications. It is characterized by a low dielectric constant (Dk) and low loss factor (Df), which reduces signal loss during transmission. These properties make it ideal for applications where high-speed data transfer is a necessity.
In high-frequency designs, even the smallest amount of signal loss can lead to problems such as data errors, inefficient power usage, and interference between signals. Nelco MW3000 is built to handle these concerns effectively, helping to ensure that signals remain clear, strong, and stable across the board.
With its low loss and consistent electrical properties, Nelco MW3000 is an effective solution for applications where maintaining the quality of high-frequency signals is core.
Benefits of Using Nelco MW3000 PCB Laminates in High-Frequency Designs
Using Nelco MW3000 offers several advantages for high-frequency designs:
1.Signal Integrity – The low dielectric constant of Nelco MW3000 ensures signals travel with minimal interference, making it a good match for high-frequency applications that require stable transmission over long distances.
2.Minimal Loss – The low loss factor (Df) ensures that less power is lost during signal transmission, leading to improved energy efficiency and performance in high-speed designs.
3.Thermal Stability – The material performs well under a variety of temperature conditions, maintaining its properties even when subjected to changes in environmental temperature.
4.Manufacturing Flexibility – Nelco MW3000 is compatible with lead-free reflow processes, supporting sustainability efforts while maintaining reliable performance throughout the PCB manufacturing process.
For high-frequency PCB applications, these benefits make Nelco MW3000 a versatile material for creating efficient and long-lasting designs.
Applications of Nelco MW3000 PCB Laminates in Advanced Electronics
The versatility of Nelco MW3000 makes it suitable for a variety of high-frequency applications. Some of the areas where this material excels include:
●5G Infrastructure – With the rapid rollout of 5G technology, Nelco MW3000 offers the stability required for high-speed data transfer in network infrastructure.
●Supercomputing – Supercomputers demand PCB materials that can handle complex operations and maintain signal integrity. The low loss and stable properties of Nelco MW3000 help meet these requirements.
●RF and Microwave – Applications that involve RF signals or microwave frequencies benefit from Nelco MW3000’s stable performance, especially in designs where clear signal transmission is essential.
●Automotive Electronics – In the development of autonomous vehicles or advanced automotive systems, Nelco MW3000 provides the necessary material properties to support reliable performance under demanding conditions.
The performance characteristics of Nelco MW3000 make it a dependable choice for any high-frequency PCB design, supporting various applications across industries that rely on fast data communication and precision.
Key Features of Nelco MW3000 PCB Laminates
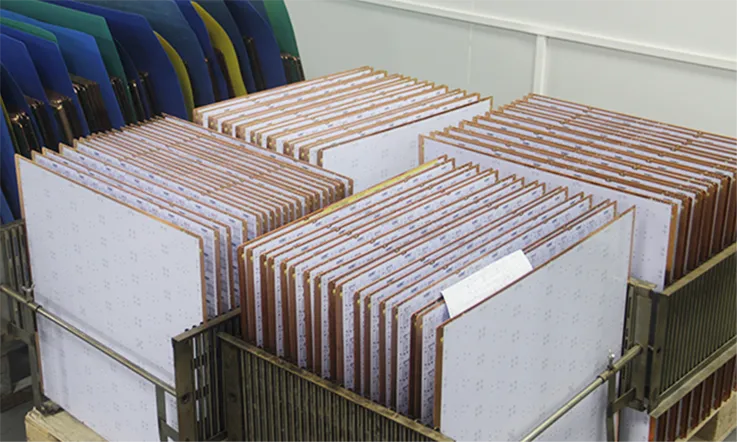
When selecting materials for high-frequency PCB designs, it’s necessary to choose laminates that deliver consistent performance across core attributes. Nelco MW3000 PCB Laminates are known for their excellent electrical properties, strong thermal resistance, and mechanical durability, making them well-suited for high-performance applications. These features ensure reliable performance in a range of environments, from telecommunications to aerospace.
Let’s dive deeper into these features to see how Nelco MW3000 compares in real-world applications.
Low Dielectric Constant (Dk) for Improved Signal Transmission
In high-frequency applications, managing signal speed and clarity is a must. The dielectric constant (Dk) of a laminate directly influences how signals travel through the PCB material. Nelco MW3000 is engineered with a low Dk, helping preserve signal quality and reducing the chances of signal drop-off. This design helps ensure that your circuits perform reliably, so if you’re working on high-speed data transmission or precision RF designs.
The low dielectric constant of Nelco MW3000 minimizes the loss of signal strength and ensures that high-speed signals maintain their integrity, reducing errors in critical data transmission. This property is especially useful for industries such as 5G and high-speed data transfer systems where accurate, fast signal propagation is a must.
The Effect of Dielectric Constant on PCB Design-
In PCB design, a high Dk can cause delays in signal transmission as the material absorbs more energy. With Nelco MW3000, we benefit from faster signal transmission with minimal attenuation, making it good for RF circuits and telecommunications applications.
Comparison with Other Materials-
Material | Dielectric Constant (Dk) | Loss Tangent (Df) | Applications |
Nelco MW3000 | 3.4-3.6 | 0.0031 | 5G, telecom, RF |
Rogers RT/duroid | 2.2-2.55 | 0.002 | Aerospace, RF |
Taconic T-Lam® | 2.5-3.5 | 0.0021 | Industrial, military |
Superior Thermal and Mechanical Stability for Harsh Environments
Nelco MW3000 PCB Laminates are built to handle extreme conditions, offering superior thermal and mechanical stability. With high-TG (glass transition temperature) materials, Nelco MW3000 can withstand high temperatures without compromising its performance. This makes them better for industries where high-frequency applications operate in harsh environments, like automotive, aerospace, and defense, ensuring long-term reliability and precision.
The thermal stability of Nelco MW3000 means it can handle heat fluctuations without significant changes in its properties. Similarly, its mechanical strength ensures that the PCB remains structurally intact under physical stress.
How Stability Enhances PCB Durability-
When PCBs are exposed to significant temperature variations, such as those found in aerospace or automotive applications, their performance can degrade. Nelco MW3000 maintains structural integrity even when subjected to thermal stress, ensuring longer-lasting and more reliable performance.
Material Comparison-
Material | Glass Transition Temperature (Tg) | Thermal Resistance | Mechanical Durability |
Nelco MW3000 | 170°C | High | High |
Rogers RT/duroid | 280°C | Very High | High |
Isola I-Tera® | 170°C | Moderate | Moderate |
From the table, we can see that Nelco MW3000 offers excellent thermal and mechanical properties for its intended use in high-frequency applications, competing effectively with other high-performance materials.
Lead-Free Compatibility and RoHS Compliance of Nelco MW3000
As the electronics industry continues to focus on sustainability, the demand for lead-free and RoHS-compliant materials has increased. Nelco MW3000 meets these requirements, ensuring it can be used in environmentally conscious designs while maintaining high performance.
With RoHS compliance, Nelco MW3000 ensures that the final product adheres to international regulations that reduce hazardous substances in electronics manufacturing. This compliance makes it an attractive option for global manufacturers who must meet these standards.
How Compliance Supports Sustainable Manufacturing-
Using RoHS-compliant materials like Nelco MW3000 helps reduce the environmental impact of PCB production. By using sustainable, lead-free materials, we can contribute to a greener future while ensuring their products meet regulatory standards.
RoHS Compliance Overview-
Material | RoHS Compliance | Lead-Free | Sustainability Features | Ideal Applications |
Nelco MW3000 | Yes | Yes | High | 5G, telecom, consumer electronics |
Rogers RT/duroid | Yes | Yes | High | Aerospace, military |
Shengyi S1135 | Yes | Yes | Moderate | Industrial, automotive |
As highlighted, Nelco MW3000 aligns with global sustainability standards while providing performance that meets the needs of high-frequency PCB applications.
The Advantages of Nelco MW3000 PCB Laminates Over Other Materials
In high-frequency PCB design, choosing the right laminate material can significantly influence performance. Nelco MW3000 stands as a superior option for high-frequency applications, providing both electrical efficiency and mechanical robustness. It outperforms many common alternatives by delivering consistent results in signal integrity, low loss, and material stability under demanding conditions.
In this section, we’ll dive into the specific advantages that Nelco MW3000 offers when compared to other high-frequency materials. By exploring its electrical performance, mechanical durability, and cost-efficiency, we’ll uncover why Nelco MW3000 remains a preferred choice for designers looking to optimize their PCB designs.
Comparing Electrical Performance: Nelco MW3000 vs Other High-Frequency Materials
High-frequency PCBs require materials with excellent signal transmission characteristics. When comparing Nelco MW3000 to other high-frequency materials, its electrical performance shines. With a low dielectric constant (Dk) and low dissipation factor (Df), it ensures minimal signal loss and stable electrical behavior over a wide range of frequencies.
Nelco MW3000’s properties make it a strong contender in high-performance fields like 5G, RF circuits, and data centers, where signal integrity is non-negotiable. With its ideal balance of dielectric constant (Dk) and dissipation factor (Df), Nelco MW3000 outperforms other materials such as Rogers RO4003C and Taconic RF-35. While these alternatives are widely used, they tend to exhibit slightly higher loss factors, making Nelco MW3000 the go-to choice for reducing signal degradation.
Electrical Performance Comparison-
Material | Dielectric Constant (Dk) | Dissipation Factor (Df) | Electrical Performance |
Nelco MW3000 | 3.4-3.6 | 0.0021 | Excellent Signal Integrity |
Rogers RO4003C | 3.38± 0.05 | 0.0021-0.0027 | Good, but higher signal loss |
Isola I-Tera | 3.38-3.75 | 0.0028-0.0035 | Decent, higher loss factor |
Taconic RF-35 | 3.5 | 0.0018 | Balanced performance |
As seen in the table above, Nelco MW3000 stands out with a lower dielectric constant and dissipation factor compared to many competitors like Rogers RO4003C or Taconic RF-35. This results in more reliable signal transmission and lower signal loss, which is a significant advantage in high-frequency PCB applications.
Mechanical Strength and Durability Comparison in PCB Manufacturing
Durability is a core factor in choosing PCB materials, especially in high-frequency environments where materials are subject to physical and thermal stress. Nelco MW3000 laminates have been designed to withstand mechanical stresses, including thermal cycling, vibration, and mechanical deformation.
This laminate’s superior peel strength and minimal Z-axis expansion ensure that it maintains structural integrity even under harsh conditions. Compared to materials like Rogers RO4350B and Isola FR408HR, Nelco MW3000 delivers exceptional performance in terms of both mechanical strength and reliability, making it an excellent choice for automotive, aerospace, and industrial applications.
Mechanical Strength Comparison-
Material | Z-Axis Expansion (%) | Peel Strength (lb/in) | Durability Performance |
Nelco MW3000 | 0.10% | 6.5 | Excellent durability |
Rogers RO4350B | 0.12% | 6.0 | Good durability |
Isola FR408HR | 0.15% | 5.5 | Moderate durability |
Taconic TLY | 0.14% | 5.8 | Good durability |
Nelco MW3000 laminates show a significant edge in both peel strength and Z-axis expansion control. These characteristics contribute to the material’s overall durability and make it also a reliable choice for high-frequency PCBs in harsh operating environments.
The Cost-Effectiveness of Nelco MW3000 for High-Frequency Designs
Cost is always a consideration when selecting materials for high-frequency PCB manufacturing. Nelco MW3000 delivers an affordable solution without compromising on performance. When compared to other high-performance materials, such as Rogers RT/duroid, Nelco MW3000 provides similar performance characteristics at a more accessible price point.
The cost-effectiveness of Nelco MW3000 makes it a great choice for manufacturers who need to balance high-performance capabilities with budget constraints. As PCB manufacturers face increasing pressure to reduce production costs while maintaining performance, Nelco MW3000 offers an optimized balance between price and performance, ensuring a great return on investment in high-frequency applications.
Cost-Effectiveness in PCB Design-
Material | Price per Square Meter | Performance Score | Applications |
Nelco MW3000 | $100 | High | 5G, RF, Telecom |
Rogers RT/duroid | $150 | Very High | Aerospace, High-Speed |
Tuc PCB | $80 | Moderate | Industrial, Automotive |
From the table, it’s clear that Nelco MW3000 offers a highly competitive price point, making it a suitable choice for high-frequency designs where cost-effectiveness and performance must go hand in hand.
Design Considerations for Nelco MW3000 PCB Laminates
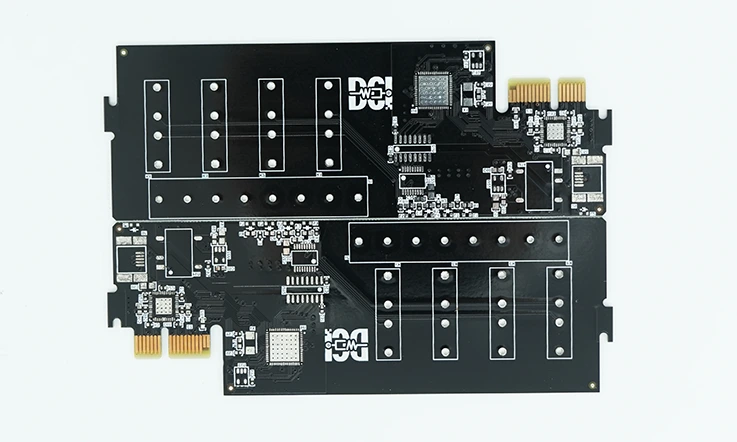
When designing high-frequency PCBs, choosing the right material is only part of the puzzle. Nelco MW3000 PCB laminates, with their excellent electrical properties, allow our engineers to achieve superior signal integrity while ensuring robust and reliable performance in demanding environments. To maximize the benefits of Nelco MW3000 in your designs, a few design considerations should be kept in mind. These involve optimizing the PCB layout, managing signal integrity effectively, and ensuring trace width and spacing are in harmony with the specific high-frequency requirements.
Optimizing PCB Layouts for High-Speed and High-Frequency Applications
PCB layout optimization plays a central role in high-frequency circuit design. The goal is to reduce signal loss, control impedance, and maintain efficient data signal transmission through the PCB. In high-speed data transmission, minimizing signal loss is a must. Nelco MW3000, with its low dielectric constant and low dissipation factor, helps preserve signal integrity across a wide range of frequencies.
When laying out high-speed circuits with Nelco MW3000, key layout factors such as trace width, spacing, and routing must be carefully considered to ensure that the signals travel with minimal interference. Moreover, impedance control becomes increasingly important as the data rates increase, particularly for high-speed digital and RF circuits. For example, a well-implemented PCB layout with Nelco MW3000 can reduce signal reflections, preventing issues like signal distortion or data errors.
PCB Layout Optimization Tips:
●Controlled Impedance Routing: Maintaining a constant trace width and spacing to achieve the desired impedance ensures signal quality, especially in high-speed designs.
●Ground Plane Design: A solid ground plane helps reduce electromagnetic interference (EMI) and crosstalk between adjacent traces, which is particularly useful when handling high-frequency signals.
●Minimize Via Use: The fewer vias used in a design, the less the signal will degrade. Vias can add inductance and resistance, impacting the signal’s integrity.
By integrating these best practices and using Nelco MW3000 laminates, you can maximize the performance of high-frequency PCB designs.
Managing Signal Integrity with Nelco MW3000 Materials
Maintaining signal integrity is one of the primary challenges in high-frequency PCB design. The properties of Nelco MW3000 laminates, including their low dielectric constant and low loss factor, provide a strong foundation for signal integrity in high-frequency applications. However, we must also address issues like crosstalk, which can degrade performance by causing interference between adjacent traces.
With its low dissipation factor and low dielectric constant, Nelco MW3000 minimizes signal loss and maintains the quality of the transmitted signal over long distances. This is especially beneficial in applications like high-speed communication systems, RF circuits, and 5G networks, where high data rates demand superior signal clarity.
Additionally, signal integrity can be further enhanced by employing specific design techniques such as controlled impedance traces, differential pairs, and proper grounding. Nelco MW3000, with its precise material properties, helps reduce the risk of signal degradation that can occur due to variations in impedance or signal reflections.
Managing Signal Integrity-
Feature | Impact on Signal Integrity |
Low Dielectric Constant (Dk) | Minimizes signal loss and delays |
Low Dissipation Factor (Df) | Reduces heat generation and signal degradation |
Impedance Control | Prevents signal reflections and distortion |
Proper Grounding | Reduces noise and interference |
By carefully controlling impedance and ensuring the ground plane is continuous with minimal noise, we can further protect signal quality. Proper trace spacing is a practical method for reducing crosstalk and maintaining signal fidelity throughout the PCB. Utilizing the capabilities of Nelco MW3000 laminates to their fullest requires an understanding of the physical properties of the material and its interaction with high-speed signals.
The Role of Trace Width and Spacing in High-Frequency PCB Design
When designing high-frequency circuits, the physical dimensions of the PCB traces—such as their width and spacing—affect impedance matching and help minimize signal loss. Nelco MW3000 offers consistent material properties, supporting precise control over trace impedance, which helps ensure stable data transmission at high speeds.
Trace width and spacing need to be carefully selected based on the required impedance value for the circuit. For instance, high-frequency digital signals typically require a controlled impedance of 50 ohms for signal transmission. The width of the trace and the distance to the ground plane (or other traces) must be calculated based on the laminate’s dielectric constant and the specific design goals.
Moreover, when it comes to high-frequency designs, any deviation in trace width or spacing can cause reflections, signal degradation, or even circuit failure. Therefore, precise layout and material selection like Nelco MW3000 are need to ensure that trace widths and spacing align with the intended impedance.
Trace Width and Spacing Calculation Example:
For a 50-ohm microstrip line on a Nelco MW3000 laminate, the trace width (W) can be calculated using the following formula:
Considerations for Using Nelco MW3000 in PCB Manufacturing
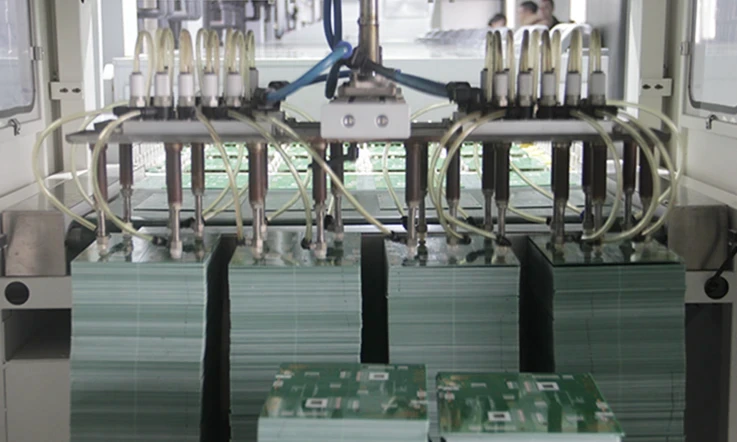
When selecting materials for high-frequency applications, Nelco MW3000 PCB laminates are a top choice due to their exceptional electrical properties and ability to handle high-frequency signals with ease. However, working with specialized materials like Nelco MW3000 does require specific considerations during the PCB manufacturing process. These factors influence both performance and manufacturability, ultimately affecting production costs and timelines.
In this section, we’ll explore the practical aspects of using Nelco MW3000 in PCB production. We’ll cover processing considerations, how the material interacts with standard fabrication techniques, and how lead-free assembly can affect manufacturing efficiency. Understanding these points will help ensure that Nelco MW3000 is used to its fullest potential while minimizing production issues.
Easy Processing with High-TG Materials for Efficient PCB Production
Nelco MW3000 features a high glass transition temperature (TG), making it a solid choice for high-frequency circuit applications. This high TG allows the material to withstand higher temperatures during the lamination process, meeting the thermal demands of modern PCB manufacturing. As technology advances, materials like Nelco MW3000 offer the necessary durability and thermal stability for a variety of designs.
During the lamination process, Nelco MW3000 offers excellent control over material bonding, ensuring that each layer adheres securely without the risk of delamination or warping, even when exposed to high temperatures. This capability is especially useful in high-frequency circuits where signal performance depends on consistent material quality.
Process Step | Nelco MW3000 vs Other Laminates | Benefits |
Lamination | Stable bonding under heat | Reduces risk of delamination |
Thermal Cycling | Excellent resistance to thermal stress | Suitable for demanding environments |
Signal Integrity | Low loss, precise dielectric properties | Minimizes signal loss |
By incorporating high-TG materials like Nelco MW3000, we can improve both the speed and consistency of production processes, ultimately reducing the chance of defects and enhancing overall production efficiency.
Lead-Free Assembly and Its Impact on the Manufacturing Process
With increasing attention on environmental sustainability, many manufacturers have switched to lead-free assembly processes. Nelco MW3000 laminates are fully RoHS-compliant, meaning they meet the European Union’s standards for restricting hazardous substances like lead and mercury.
The transition to lead-free assembly has had a significant impact on the reflow process, requiring higher temperatures to melt the solder without compromising the integrity of the materials. High-TG materials like Nelco MW3000 are particularly well-suited for this transition, as they can endure the higher temperatures without losing their strength or performance characteristics.
In addition to meeting environmental regulations, using lead-free materials like Nelco MW3000 helps improve the manufacturing process by reducing the likelihood of defects. The stable properties under higher temperatures allow manufacturers to proceed with the reflow process more smoothly and without worrying about damage to the laminate.
Consideration | Lead-Free Assembly with Nelco MW3000 | Traditional Lead-Based Materials |
Soldering Temperature | Stable under higher temperatures | More temperature-sensitive |
Environmental Impact | Meets RoHS standards, eco-friendly | Contains restricted substances |
Manufacturing Process | Reliable performance in lead-free assembly | More prone to soldering issues |
By utilizing Nelco MW3000, PCB manufacturers can ensure compliance with global environmental standards while maintaining the reliability of their products.
Compatibility with Standard PCB Fabrication Techniques
Nelco MW3000 is designed to integrate seamlessly into standard PCB fabrication processes. It works with conventional techniques such as lamination, drilling, plating, and etching without the need for specialized equipment or changes to existing workflows.
In lamination, Nelco MW3000’s uniform properties make it easy to bond with other layers, creating strong and reliable connections. During drilling, the laminate’s consistent material properties reduce tool wear, making the process more efficient and cost-effective. In plating, Nelco MW3000 offers excellent adhesion to copper layers, ensuring durable electrical connections. Etching with Nelco MW3000 is also consistent, allowing for the precise definition of intricate circuit patterns.
Fabrication Process | Nelco MW3000 Compatibility | Other Materials |
Lamination | Easy, stable bonding | Requires more careful control |
Drilling | Reduced tool wear, uniform material | Can cause tool wear, less consistent |
Plating | Strong adhesion, reliable performance | May cause adhesion problems |
Etching | High precision, uniform etching | May lead to inconsistent etching |
This compatibility with existing fabrication techniques means that manufacturers can continue using their standard equipment while benefiting from the performance advantages of Nelco MW3000.
Why Choose Us as Your High-Quality PCB Supplier?
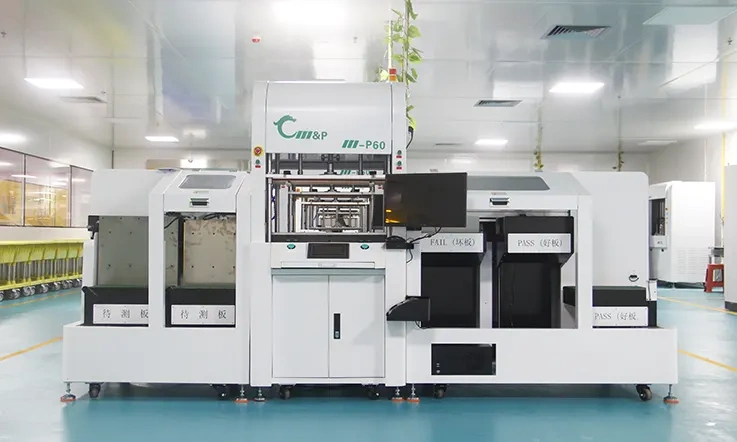
When it comes to selecting a dependable partner for high-quality PCBs, you want to work with a team that not only provides top-grade materials but also brings solid industry experience, state-of-the-art technology, and a strong support structure. Here’s why teaming up with us makes sense:
1.Industry Expertise & Experience:
With years of experience in the PCB manufacturing industry, our team understands the intricacies of producing high-performance boards for various applications, from RF circuits to 5G and high-speed data transmission systems. We’ve built our reputation by providing solutions that meet even the most stringent standards in the field of high-frequency PCB design.
2.Advanced Technology & Equipment:
We leverage the latest in PCB manufacturing technology, ensuring precision, consistency, and quality across every batch. Our state-of-the-art equipment and automated processes reduce production errors and increase efficiency, allowing us to deliver high-frequency PCBs with unmatched reliability.
3.Skilled Engineering Team:
Our engineering team is made up of professionals with deep technical knowledge and hands-on experience in high-TG materials and PCB design. From layout optimization to signal integrity management, they work tirelessly to ensure every design is realized to its fullest potential, ensuring your projects succeed without compromise.
4.Commitment to Quality Assurance:
Quality is at the heart of everything we do. We maintain rigorous quality control processes throughout the production cycle, ensuring that every PCB meets international standards for performance, durability, and safety. Our use of Nelco MW3000 materials, known for their superior electrical and thermal properties, ensures your boards will perform reliably under demanding conditions.
5.Comprehensive After-Sales Support:
Our commitment to customer satisfaction doesn’t end with delivery. We provide robust after-sales support to help with any questions or issues that arise during the implementation of your PCBs. Whether you need assistance with troubleshooting or advice on design optimizations, our team is always available to provide expert guidance.
6.One-Stop Services from Manufacturing to Assembly
At our company, we don’t just stop at manufacturing. We use top-quality PCB laminates from leading brands, such as Nelco MW3000, to ensure your circuit boards are built to meet the highest standards of performance. Additionally, we provide a comprehensive, one-stop service that covers everything from PCB production and component sourcing to final circuit board assembly, ensuring you have a seamless experience from start to finish
Contact Us Today:
Choosing us as your PCB supplier means you’re partnering with a team that offers not only advanced technology and materials but also personalized support throughout your project lifecycle. Now, please send your PCB Gerber and BOM files to Us, let’s talk with you about Your PCB project Detail!
FAQs related to Nelco MW3000 PCB Laminates:
1. What’s the maximum operating temperature for Nelco MW3000?
It can withstand temperatures up to 170°C, suitable for high-temperature environments.
2. Is Nelco MW3000 suitable for RF circuits?
Yes, it’s an excellent choice for RF designs due to low signal loss and high-frequency performance.
3. Does Nelco MW3000 offer impedance control?
Yes, it provides reliable impedance control for stable signal transmission.
4. Which PCB fabrication processes work with Nelco MW3000?
It’s compatible with lamination, drilling, plating, and etching processes.