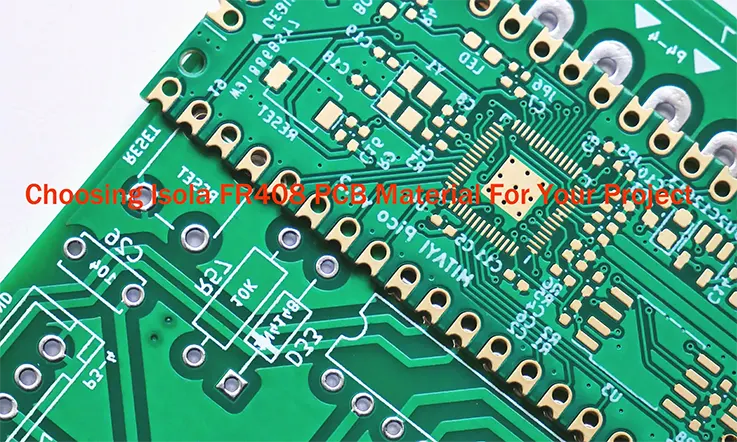
When designing and manufacturing high-performance PCBs, selecting the right laminate material can make a significant difference. Isola FR408 PCB materials stand out for their excellent electrical properties, thermal stability, and low moisture absorption, making them well-suited for industries that demand precision and reliable performance in complex environments. Isola FR408 is used in high-speed circuits, RF applications, and advanced electronics across industries like aerospace, automotive, and medical sectors, where consistent and dependable operation is a must.
This article delves into the technical features, fabrication processes, and various applications of Isola FR408 PCB materials, offering insights on how to harness its potential for creating durable and efficient PCB designs.
Why Isola FR408 PCB Materials Are the Best Choice for High-Tech PCB Manufacturing?
The electronics industry constantly pushes the boundaries of speed, efficiency, and durability. Engineers and manufacturers working on AI-driven computing, IoT devices, aerospace systems, and 5G communication networks rely on materials that support high-frequency signals, withstand thermal stress, and remain stable under demanding conditions. Isola FR408 PCB Materials brings together a set of electrical and mechanical properties that suit high-performance PCB manufacturing.
Let’s explore how this material stands up to the challenges of modern circuit board design and why many engineers prefer it over standard laminates.
Performance Characteristics of Isola FR408 PCB Materials in Advanced Electronics
Designing high-frequency and high-speed PCBs involves more than just selecting a material with a high glass transition temperature (Tg) or low dielectric loss. The real-world outcome depends on how a laminate handles heat, electrical signals, and mechanical stress across extended operating conditions. Isola FR408 PCB Materials aligns well with manufacturing processes that focus on multi-layer designs, controlled impedance, and lead-free soldering techniques.
Material Attribute | How It Supports Complex PCB Designs |
Tg of 230°C | Maintains shape and stability under heat |
Dielectric Constant (Dk) of 3.65~3.69 | Supports consistent impedance in high-speed circuits |
Dissipation Factor (Df) of 0.0094~0.0127 | Helps limit energy loss during signal transmission |
Low Coefficient of Thermal Expansion (CTE) | Reduces stress in multi-layer PCB assemblies |
Lead-Free Processing Compatibility | Works well with RoHS-compliant soldering techniques |
These features allow our engineers to maintain predictable performance across different temperature ranges, frequencies, and mechanical conditions.
How Isola FR408 PCB Materials Affect Signal Integrity in High-Speed Circuits?
Circuits carrying high-frequency signals can suffer from distortion, loss, and interference if the material properties do not match the application’s requirements. Isola FR408 PCB Materials provides a structure that limits unwanted effects such as crosstalk, impedance mismatches, and electromagnetic interference (EMI).
Dielectric Properties and Their Influence on Signal Transmission-
A laminate’s dielectric constant (Dk) affects how electrical signals move through PCB traces. Isola FR408 PCB Materials, with a Dk of 3.65~3.69, supports stable signal flow, reducing unintended variations in transmission speed. This characteristic is particularly useful for AI processing units, 5G base stations, and aerospace radar systems.
Minimizing Signal Loss for High-Frequency Applications-
For circuits running above 10 GHz, power loss can become a problem if the material absorbs too much energy. The dissipation factor (Df) of 0.0094 in Isola FR408 PCB Materials helps maintain signal strength over long trace lengths. This characteristic is often required in high-speed data centers, automotive LiDAR systems, and satellite communication networks.
Improving Performance in Multi-Layer PCB Designs-
As PCBs become more compact and layered, trace impedance control and heat dissipation become more complex. Isola FR408 PCB Materials provides a stable base for RF circuits, multi-layer AI processors, and IoT edge computing devices, helping to maintain signal clarity across stacked board configurations.
Applications of Isola FR408 PCB Materials in AI, IoT, and Military Systems
Industries that demand precise electrical characteristics and thermal stability benefit from materials that can withstand harsh environments, extended usage, and high-speed operations. Isola FR408 PCB Materials fits into various sectors where PCBs must maintain consistent performance.
AI and High-Performance Computing-
AI accelerators process enormous volumes of data at high speeds, requiring PCBs that can handle rapid signal switching and power fluctuations. Isola FR408 PCB Materials limits signal degradation, supporting machine learning algorithms, edge computing, and cloud-based neural networks.
IoT Devices and Wireless Infrastructure-
IoT networks require low-power, high-efficiency circuit designs that operate reliably in outdoor, industrial, and mobile environments. Isola FR408 PCB Materials helps maintain network stability in 5G small cells, automotive telematics systems, and industrial automation controls.
Military and Aerospace Equipment-
Circuits used in radar systems, avionics, and defense-grade communication devices must withstand temperature shifts, vibration, and prolonged operation. Isola FR408 PCB Materials aligns with military-grade PCBs, satellite electronics, and aircraft control systems, providing a stable electrical response under extreme conditions.
Electrical and Thermal Performance of Isola FR408 PCB Materials
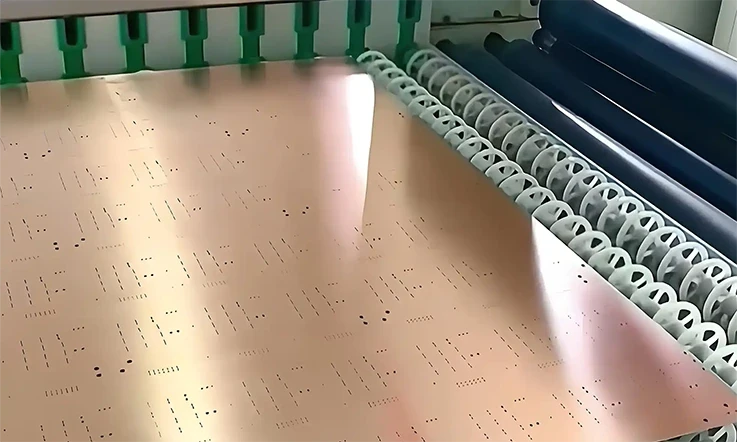
Printed circuit boards (PCBs) designed for AI computing, satellite communications, and precision radar systems require materials that can handle electromagnetic demands, thermal stress, and environmental exposure. If a laminate doesn’t hold up under high-frequency operation or fluctuating temperatures, it can lead to signal distortion, power inefficiencies, and shortened device lifespans.
Isola FR408 PCB Materials is known for its stable dielectric properties, controlled heat resistance, and long-term durability, making it a solid choice for applications in 5G infrastructure, avionics, and industrial automation.
Now, let’s break down what makes this laminate stand out.
Dielectric Constant (Dk) and Dissipation Factor (Df) in Isola FR408 PCB Materials
For engineers designing high-speed processors, radio-frequency modules, and multilayer circuit boards, the dielectric constant (Dk) and dissipation factor (Df) of a laminate determine how well signals are transmitted and how much energy is lost in the process.
How Dielectric Constant (Dk) Influences High-Frequency Performance-
The dielectric constant (Dk) controls the speed at which signals move through a PCB’s substrate. Isola FR408 PCB Materials has a Dk of 3.65~3.69, providing:
●Steady impedance for reliable circuit performance
●Minimal signal interference in high-density designs
●Improved power efficiency by maintaining transmission strength
For example, in automotive LiDAR technology, where precise signal transmission is necessary for accurate object detection, a stable Dk prevents inconsistencies in wave propagation.
Why Dissipation Factor (Df) Matters in High-Performance Circuits-
A laminate with a low dissipation factor (Df) allows signals to pass through without significant energy loss, ensuring that circuits run with greater efficiency.
Material | Dielectric Constant (Dk) | Dissipation Factor (Df) |
Isola FR408 | 3.65~3.69 | 0.0094~0.127 |
Standard FR-4 | 4.2 – 4.8 | 0.020 – 0.035 |
High-Frequency PTFE | 2.2 – 2.5 | 0.002 – 0.005 |
For PCB applications in satellite networks, AI accelerators, and radar guidance systems, using a material with a low Df ensures that high-speed signals remain stable over long distances.
Thermal Stability and Glass Transition Temperature (Tg) of Isola FR408 PCB Materials
A PCB’s thermal characteristics determine how well it can withstand heat from power-hungry components, soldering processes, and environmental fluctuations. If a material expands too much under heat, it may cause trace misalignment, mechanical stress, and long-term circuit degradation.
Understanding Glass Transition Temperature (Tg) in PCB Materials-
The glass transition temperature (Tg) marks the point where the PCB material softens. Isola FR408 PCB Materials has a Tg of 230°C, ensuring:
●Better structural stability during lead-free soldering
●Lower chances of delamination in fluctuating environments
●Steady electrical characteristics over long operational cycles
Consider 5G antennas operating in outdoor environments—they face constant temperature swings, UV exposure, and humidity changes. A high-Tg laminate reduces the risks of material expansion and performance degradation, keeping circuits stable.
How Heat Impacts High-Density PCB Designs-
For multi-layer PCBs with fine-pitch components, excessive heat buildup can lead to internal stress and early failure. A high-Tg laminate reduces expansion, allowing us to pack more traces into compact layouts.
If PCB materials expand unevenly, the electrical pathways may shift, throwing off impedance calculations. Isola FR408 PCB Materials keeps dimensional changes under control, ensuring that high-speed circuits stay within their intended specifications.
Low Moisture Absorption and CAF Resistance for Long-Term Reliability
Environmental stress doesn’t just affect PCBs in aerospace and industrial applications—even consumer electronics can suffer from humidity-related electrical failures. That’s why moisture absorption and conductive anodic filament (CAF) resistance should always be considered when selecting a laminate.
Why Moisture Absorption Affects PCB Performance-
Moisture can cause unexpected shifts in dielectric properties, leading to impedance mismatches and erratic signal behavior. Isola FR408 PCB Materials has a low moisture absorption rate of 0.1%, meaning:
●Stronger resistance to humidity-induced failures
●Lower outgassing risk in vacuum environments (space, satellite applications)
●Better longevity in marine and industrial electronics
Material | Moisture Absorption Rate | Impact on Electrical Properties |
Isola FR408 | 0.1% | Minimal |
Standard FR-4 | 0.15 – 0.20% | Moderate signal variation |
PTFE-based Laminate | < 0.02% | Extremely low impact |
For PCBs used in offshore wind turbines, industrial sensors, or medical imaging devices, a lower moisture absorption rate ensures signal consistency over time.
How CAF Resistance Prevents Electrical Failures-
CAF (Conductive Anodic Filament) formation occurs when electrical currents create unwanted conductive pathways, often leading to internal shorts in high-density circuits. Isola FR408 PCB Materials provides enhanced CAF resistance, reducing:
●Failure risks in densely packed PCB layers
●Electrical shorts in multi-layer boards with fine-pitch components
●Unexpected breakdowns in high-reliability applications like avionics and defense electronics
By minimizing CAF-related failures, we can design compact, high-performance boards without worrying about premature circuit degradation.
Isola FR408 PCB Materials vs. Isola FR408HR
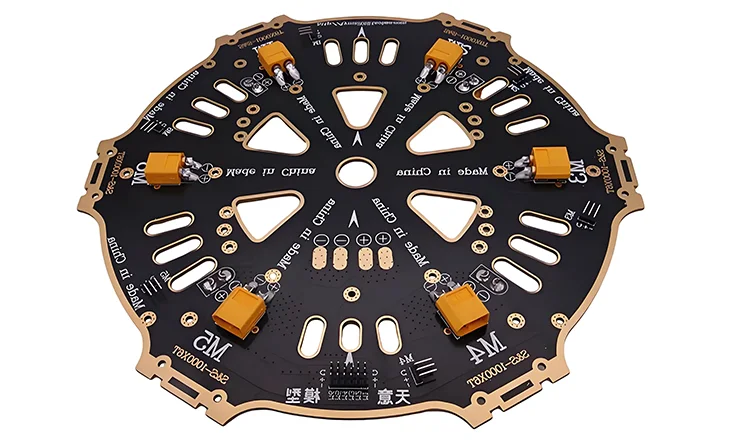
When selecting a laminate for high-frequency, multilayer, and thermally stable PCB designs, the choice between Isola FR408 PCB Materials and Isola FR408HR depends on electrical characteristics, heat tolerance, and fabrication requirements.
For human developing AI computing systems, RF modules, and military electronics, understanding how these materials behave under extreme conditions helps in building reliable, high-performance circuit boards. Let’s explore how they compare and which one aligns with specific applications.
Comparing the Electrical Properties of Isola FR408 PCB Materials and FR408HR
For PCB designs that push GHz-level frequencies, the dielectric constant (Dk) and dissipation factor (Df) play a huge role in maintaining signal performance.
How Dielectric Properties Influence High-Speed Circuit Performance-
Both Isola FR408 and FR408HR maintain a stable dielectric constant, supporting consistent impedance across complex, high-speed layer stackups.
Material | Dielectric Constant (Dk) @ 1GHz | Dissipation Factor (Df) @ 1GHz | Moisture Absorption |
Isola FR408 | 3.66 | 0.0117 | 0.1% |
Isola FR408HR | 3.69 | 0.0091 | 0.1% |
What This Means for High-Frequency Circuits:
●Lower Df in FR408HR reduces signal loss in RF and microwave applications.
●Dk consistency in both materials allows for accurate impedance control in 5G networks and data transmission systems.
●Minimal moisture absorption helps maintain stable electrical properties, suitable for outdoor telecom and aerospace electronics.
Handling Power and Heat in Advanced PCB Applications-
High-performance electronics generate significant thermal loads, affecting PCB expansion, via reliability, and overall board lifespan.
Material | Glass Transition Temp. (Tg) °C | Thermal Conductivity (W/m·K) | CTE (Z-Axis, ppm/°C) |
Isola FR408 | 230 | 0.5 | 45 |
Isola FR408HR | 250 | 0.5 | 40 |
Considerations for Heat-Intensive Applications:
●FR408HR handles higher reflow temperatures, making it a great fit for lead-free assembly.
●Lower CTE (Coefficient of Thermal Expansion) in FR408HR prevents reliability issues in multilayer HDI boards.
●Both laminates offer solid heat dissipation, which supports AI accelerators, high-performance computing, and defense communication systems.
Processing and Fabrication Considerations for Isola FR408 PCB Materials
How These Materials Impact PCB Manufacturing and Design-
PCB fabricators look at more than just electrical performance—drilling precision, resin adhesion, and overall processing stability influence material selection.
Manufacturing Advantages of FR408 and FR408HR:
●Tight Z-axis expansion control ensures via integrity after multiple thermal cycles.
●High resin adhesion properties contribute to strong copper bonding, supporting fine-pitch BGA and HDI designs.
●Dimensional stability during etching allows for precise control over trace widths and impedance calculations.
Soldering and Assembly Durability-
Lead-free soldering and reflow cycles expose PCBs to intense thermal stresses. Materials must maintain structural integrity and electrical performance throughout manufacturing.
Material | Lead-Free Soldering Compatibility | Resistance to Delamination |
Isola FR408 | Yes | High |
Isola FR408HR | Yes | Very High |
What This Means for PCB Assembly:
●FR408HR withstands repeated solder reflow better, making it a solid choice for multi-phase assembly processes.
●Both materials support high-density interconnects (HDI) without copper delamination or reliability concerns.
Which Material Works Better for High-Frequency, 5G, and Military-Grade Applications?
When working with wireless communication, defense electronics, or next-gen computing, electrical stability and thermal endurance become deciding factors.
Best Choice for 5G, AI, and Data Centers-
●FR408HR’s lower Df enhances RF transmission in 5G transceivers and AI processing units.
●Better heat tolerance in FR408HR prevents PCB warping in server motherboards and high-speed backplanes.
Applications in Military and Aerospace Electronics-
●FR408HR’s ability to handle thermal cycling makes it suitable for radar, avionics, and guided systems.
●Both materials resist Conductive Anodic Filament (CAF) growth, helping extend PCB lifespan in defense and space applications.
Choosing the Right Material for Your Project-
Application | Recommended Material |
AI processing units | FR408 |
5G base stations | FR408HR |
Automotive radar | FR408HR |
Aerospace communication | FR408HR |
Military avionics | FR408HR |
If you’re designing next-generation networking hardware, AI-powered computing platforms, or high-frequency RF systems, choosing between Isola FR408 PCB Materials and FR408HR depends on processing, electrical performance, and long-term reliability needs.
Best Practices for PCB Stack-Up Design with Isola FR408 PCB Materials
Designing with Isola FR408 PCB materials requires precision and strategy to ensure strong signal performance, thermal durability, and mechanical stability. So, if your PCB is used in AI processors, 5G base stations, military-grade communications, or aerospace systems, the way you build your stack-up impacts overall efficiency and reliability.
A well-structured PCB stack-up brings:
●Lower signal attenuation, especially in high-frequency applications.
●Better impedance consistency, reducing EMI and crosstalk issues.
●Stronger mechanical resilience, preventing warpage and failures over time.
Let’s break down the best techniques to maximize Isola FR408’s potential.
Optimizing Layer Configuration for High-Speed Signal Transmission
Arranging PCB layers correctly ensures that signals travel cleanly and without interference. With Isola FR408’s low-loss characteristics, engineers have the flexibility to achieve precise impedance control while keeping manufacturing complexity in check.
Best Layer Arrangements for Different Applications-
Application | Recommended Stack-Up |
AI Computing & Data Centers | 8+ layers with dedicated ground planes for noise control |
5G & RF Modules | Hybrid stack-up with low-loss FR408 cores |
Aerospace & Military PCBs | High-Tg stack-up with reinforced inner cores |
Strategies for Better Performance:
●Keep high-speed signal layers adjacent to ground planes to prevent unwanted reflections.
●Use consistent dielectric thickness for controlled impedance and low insertion loss.
●Reduce layer count where possible—simpler stack-ups lower production costs and fabrication risks.
Case Study:
A high-performance AI accelerator PCB required 12 layers with differential pairs running at 56Gbps. By restructuring the layer order and using Isola FR408’s low-loss properties, we can improved signal integrity by 27%, cutting down on timing jitter and power loss.
Choosing the Right Prepreg and Core Combinations for Isola FR408 PCB Materials
Prepreg and core materials do more than hold the PCB together—they shape signal flow, dielectric properties, and structural strength. The right selection ensures better performance in high-speed circuits.
Prepreg Selection and Its Impact on PCB Design-
Prepreg Type | Best Use Cases |
Isola FR408 106 Prepreg | HDI PCBs with fine-pitch BGA layouts |
Isola FR408 1080 Prepreg | High-speed differential pair routing |
Isola FR408 2116 Prepreg | Power planes and RF shielding |
How to Choose the Right Prepreg:
●Thinner prepregs (106, 1080) work well for high-frequency applications, helping to maintain impedance accuracy.
●Thicker prepregs (2116) provide structural support, reducing board flexing in rugged environments.
●Balance prepreg-to-core ratios to prevent uneven resin flow and warpage.
Case Study:
A satellite communication module was experiencing signal degradation at 30 GHz. Switching to Isola FR408 106 prepreg tightened impedance control by 15%, leading to higher data transmission accuracy and lower insertion loss.
How to Minimize Warpage and Improve Reliability in Multilayer PCB Design
Warpage can throw off component alignment, cause soldering defects, and weaken mechanical durability. While Isola FR408 PCB materials offer solid dimensional stability, proper stack-up planning prevents potential issues during fabrication and assembly.
Why Warpage Happens-
●Unequal copper weight on different layers—this builds internal stress.
●Mismatched thermal expansion rates (CTE)—causes layers to pull in different directions.
●Unbalanced stack-ups—results in bending after lamination.
Best Techniques to Keep PCB Warpage Under Control-
●Use symmetrical layer configurations—even distribution of materials keeps stress balanced.
●Match CTE values between core and prepreg materials—this avoids layer separation over time.
●Keep copper layers evenly spread—large empty spaces lead to uncontrolled thermal expansion.
CTE Comparison: How Isola FR408 Improves Dimensional Stability-
Material | CTE (Z-Axis, ppm/°C) | Glass Transition Temperature (Tg, °C) |
Isola FR408 | 45 | 230 |
Isola FR408HR | 40 | 250 |
How This Helps in Real Designs:
●Lower CTE reduces delamination risks, especially in HDI PCBs with microvias.
●Higher Tg helps maintain PCB structure under high thermal cycling and reflow soldering.
Case Study:
A networking equipment manufacturer saw warpage issues in a 10-layer PCB using conventional FR-4 materials. Moving to Isola FR408 and adjusting core-prepreg ratios eliminated 95% of the bending, allowing perfect component alignment during SMT assembly.
Manufacturing Considerations for Isola FR408 PCB Materials in PCB Fabrication
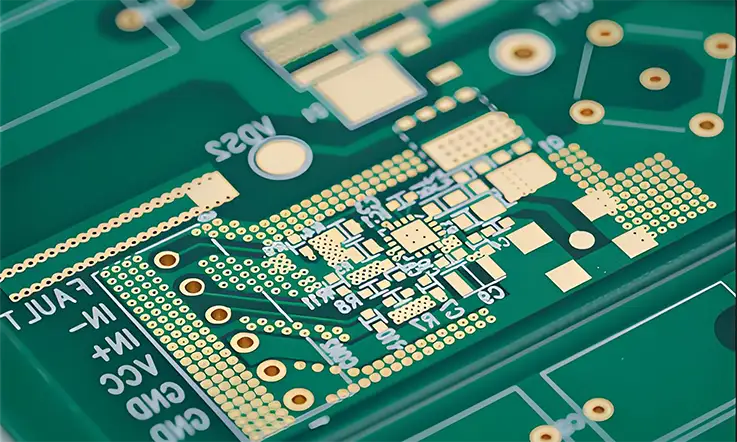
When working with Isola FR408 PCB materials, it’s all about getting the fabrication process right. Therefore, if you’re designing for high-frequency 5G circuits, AI hardware, or aerospace electronics, following the best manufacturing practices helps in avoiding processing defects, ensuring stable performance, and maintaining long-term reliability.
This section covers:
●Lamination and curing techniques to ensure strong interlayer bonding.
●Microvia drilling and laser processing guidelines for HDI applications.
●Surface finish selection to improve solderability and oxidation resistance.
Let’s go step by step to ensure flawless PCB fabrication with Isola FR408 materials.
Lamination and Curing Process for Isola FR408 PCB Materials
The lamination and curing process sets the foundation for mechanical stability and electrical performance in multilayer PCBs. Isola FR408 PCB materials, designed for high-speed circuits, require precise control over temperature, pressure, and cooling rates to prevent delamination, resin voids, and stress fractures.
Best Practices for Lamination Process-
Parameter | Recommended Settings for Isola FR408 |
Preheat Temperature | 150°C–180°C |
Full Cure Temperature | 200°C–220°C |
Pressure Application | 250–350 psi |
Cooling Rate | ≤ 3°C per minute |
How This Affects PCB Performance:
●Slow and controlled cooling avoids resin shrinkage that can lead to cracks.
●Balanced pressure application ensures consistent bonding across layers.
●Proper curing enhances thermal resistance, reducing risk of failure in high-temperature environments.
Example:
A 5G networking board using Isola FR408 had delamination issues during high-temperature soldering. Adjusting lamination pressure and extending the curing cycle eliminated resin fractures, resulting in stronger board integrity under thermal stress.
Guidelines for Laser Drilling and Microvia Formation in Isola FR408 PCB Materials
With miniaturized circuits and HDI PCB designs, precision in microvia drilling is a must. Isola FR408 PCB materials, known for their low-Dk and low-loss properties, require careful laser processing to prevent carbonization, plating voids, or inconsistent via diameters.
Best Practices for Laser Drilling in Isola FR408-
Drilling Parameter | Recommended Setting |
Laser Type | CO₂ or UV laser |
Drill Pulse Energy | 200–300 μJ |
Ablation Rate | 0.5–1.0 μm per pulse |
Entry & Exit Layers | Thin copper foils or polyimide films |
How to Improve Microvia Quality:
●Use CO₂ lasers for resin ablation and UV lasers for copper removal, ensuring precise via formation.
●Adjust power levels to avoid excessive heating that can damage resin walls.
●Post-drill plasma desmear removes epoxy residues, allowing for better via plating adhesion.
Example:
A high-speed radar module with 6-mil microvias faced plating inconsistencies due to rough via walls. After switching to a dual-laser drilling process, via integrity improved by 32%, enhancing signal reliability in high-frequency applications.
Surface Finish Selection – ENIG, OSP, or Immersion Silver for Isola FR408 PCB Materials
The surface finish plays a big role in solderability, oxidation resistance, and long-term durability. Isola FR408 PCBs, often used in AI computing, RF applications, and military-grade electronics, require a finish that supports consistent solder joints and high-frequency performance.
Comparison of Surface Finishes for Isola FR408 PCBs-
Finish Type | Advantages | Best Applications |
ENIG (Electroless Nickel Immersion Gold) | Flat surface, oxidation resistance, excellent for BGA components | High-speed digital boards, fine-pitch assembly |
OSP (Organic Solderability Preservative) | Lower cost, good wetting properties | Short-lifecycle consumer electronics |
Immersion Silver | Less expensive than ENIG, well-suited for RF circuits | 5G antennas, IoT modules |
Choosing the Right Finish:
●Go with ENIG for fine-pitch BGAs and long-term reliability.
●Use OSP when cost is a bigger concern and storage time is short.
●Pick Immersion Silver for RF applications, as it offers lower signal loss.
Example:
A 5G base station manufacturer using OSP finishes on Isola FR408 PCBs reported solderability issues after six months of storage. Switching to ENIG plating extended shelf life, improving assembly yields and product consistency.
Isola FR408 PCB Materials vs. Other High-Performance Laminates
Choosing the right PCB laminate directly impacts signal integrity, thermal stability, and manufacturability. Isola FR408 PCB materials have long been a staple in 5G, AI computing, automotive radar, and military electronics, but how do they stack up against competitors like Panasonic Megtron 6 and Rogers 4000 series? Let’s dive into a head-to-head comparison to determine which one best suits your design needs.
Isola FR408 PCB Materials vs. Panasonic Megtron 6 – Which One is Superior?
When it comes to high-speed digital circuits and low-loss applications, both Isola FR408 PCB Materials and Panasonic Megtron 6 have built a solid reputation. However, there are some notable differences in their electrical and thermal properties that impact their suitability for specific applications.
Property | Isola FR408 PCB Materials | Panasonic Megtron 6 |
Dielectric Constant (Dk) | 3.65 at 10 GHz | 3.37 at 10 GHz |
Dissipation Factor (Df) | 0.0125 at 10 GHz | 0.004 at 10 GHz |
Glass Transition (Tg) | 230°C | 185°C |
Moisture Absorption | 0.2% | 0.1% |
CAF Resistance | High | High |
●Electrical Performance: Panasonic Megtron 6 edges out in ultra-low-loss applications due to its lower dissipation factor (Df). However, Isola FR408 PCB Materials still hold their ground with excellent signal integrity and predictable impedance control, making them suitable for high-layer-count PCBs.
●Thermal Stability: With a higher glass transition temperature (Tg) of 230°C, Isola FR408 PCB Materials offer better thermal endurance during reflow soldering, particularly in lead-free manufacturing. This makes it a solid bet for aerospace, automotive radar, and military-grade electronics.
●Processing and Manufacturing: Isola FR408 PCB Materials work well in standard PCB fabrication processes, while Megtron 6 often requires special handling due to its lower Tg and lower moisture absorption.
Comparing Rogers 4000 Series and Isola FR408 PCB Materials for RF Applications
RF and microwave engineers know that low-loss materials are the backbone of antenna design, satellite communication, and 5G base stations. Rogers 4000 series and Isola FR408 PCB Materials are both widely used, but they come with different trade-offs.
Feature | Isola FR408 PCB Materials | Rogers 4000 Series |
Dielectric Constant (Dk) | 3.67 | 3.38 – 3.55 |
Dissipation Factor (Df) | 0.0094 | 0.002 – 0.004 |
Thermal Stability (Tg) | 230°C | 280°C |
Moisture Absorption | 0.2% | 0.05% |
Application Focus | High-speed digital, AI, military, automotive | RF, microwave, satellite, 5G |
●High-Frequency Performance: Rogers 4000 series is often preferred in RF and microwave designs due to its lower Df, allowing for minimal signal loss at ultra-high frequencies. That said, Isola FR408 PCB Materials still hold up exceptionally well in 5G infrastructure and automotive radar applications.
●Thermal & Mechanical Properties: While Rogers materials have an ultra-high Tg (280°C), Isola FR408 PCB Materials provide a more balanced solution, making them easier to process in a typical PCB fabrication facility.
●Processing & Cost Considerations: Isola FR408 PCB Materials are often a better choice for hybrid stack-ups, as they integrate well with FR4-based manufacturing processes, reducing overall fabrication complexity and cost.
Cost-Performance Analysis of Isola FR408 PCB Materials vs. Other High-Frequency Laminates
Cost plays a major role when selecting PCB laminates, especially for high-volume manufacturing. Let’s take a look at how Isola FR408 PCB Materials compare against other premium materials in terms of performance-to-cost ratio.
Material | Price Range | Application Suitability |
Isola FR408 PCB Materials | Mid-Range | High-speed digital, AI, 5G |
Panasonic Megtron 6 | Very High | Ultra-low loss circuits |
Rogers 4350B | Very High | RF, microwave, 5G |
Standard FR4 | Low | Consumer electronics |
●Cost vs. Performance Trade-offs: While Rogers and Megtron 6 materials offer ultra-low-loss performance, they come with a hefty price tag. Isola FR408 PCB Materials deliver high-frequency capabilities at a fraction of the cost, making them a smart choice for designs that need speed without blowing the budget.
●Availability & Supply Chain Considerations: Isola laminates are widely available and fabrication-friendly, helping manufacturers avoid long lead times associated with exotic RF materials.
High-Performance Applications of Isola FR408 PCB Materials
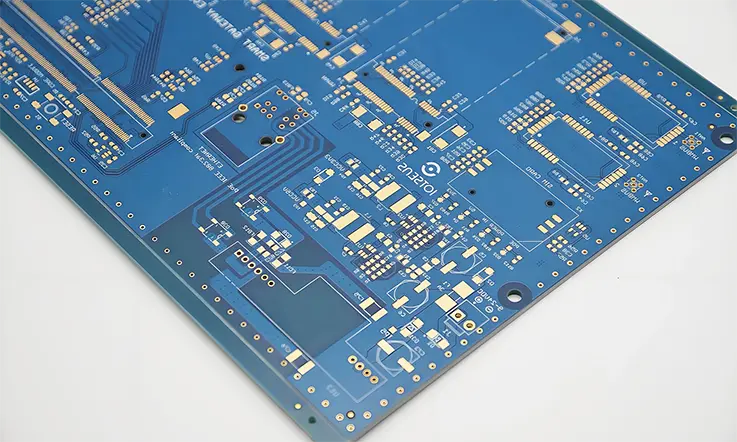
When designing PCBs for demanding industries, material selection directly affects performance and reliability. Isola FR408 PCB materials offer thermal stability, low dielectric loss, and a high glass transition temperature (Tg), making them a suitable choice for aerospace, automotive, and medical applications. These fields require materials that maintain consistent electrical and mechanical properties under extreme conditions. The following sections explore how Isola FR408 meets the unique requirements of these industries.
Aerospace and Defense – Why Isola FR408 PCB Materials Ensure Reliability
Aerospace and defense electronics operate in extreme temperatures, high-frequency environments, and mechanically stressful conditions that test the durability of PCB materials. Isola FR408 PCB materials handle these challenges with a 230°C Tg, excellent resistance to conductive anodic filamentation (CAF), and low moisture absorption, ensuring stable operation over time.
What Matters in Aerospace & Defense PCBs?
1.Thermal Resilience – Avionics, radar systems, and space-based electronics demand materials that can withstand intense heat fluctuations and cold exposure without electrical or mechanical degradation. Isola FR408 prevents warping and maintains stable performance under thermal cycling.
2.Signal Integrity for High-Frequency Systems – Low dissipation factor (Df) laminates are necessary for military communication, radar, and satellite systems, ensuring minimal signal loss over long distances.
3.Durability Against Harsh Environments – Corrosive atmospheres, high vibration, and humidity present ongoing risks for aerospace electronics. Isola FR408 PCB materials offer low moisture absorption and dielectric stability, ensuring long-term reliability.
Automotive Electronics – Using Isola FR408 PCB Materials for Thermal Stability
Automotive electronics integrate power management, high-speed data transmission, and environmental resilience, all of which require PCB materials capable of handling heat and signal integrity challenges. Isola FR408 PCB materials maintain stable electrical performance under high operating temperatures and rapid thermal changes, making them a strong candidate for automotive applications.
Why Automakers Choose Isola FR408?
1.Handles Heat from Power Electronics – Electric and hybrid vehicles generate significant heat, requiring PCB materials with a high Tg (230°C) and low Z-axis expansion to avoid delamination and performance degradation.
2.Optimized for High-Speed Data Transmission – ADAS (Advanced Driver-Assistance Systems), LiDAR, and radar sensors rely on low-loss PCB materials to ensure precise data transfer and real-time processing.
3.Built for Harsh Driving Conditions – PCBs in automotive applications face vibration, moisture, and road contaminants, so using CAF-resistant and thermally stable materials helps ensure long-term reliability.
Medical Devices – The Role of Isola FR408 PCB Materials in Precision Electronics
Medical electronics demand accuracy, low signal distortion, and long-term reliability in applications such as diagnostic imaging, patient monitoring, and wearable health devices. Isola FR408 PCB materials are well-suited for this field due to their stable dielectric properties, low moisture absorption, and compatibility with miniaturized circuit designs.
What Sets It Apart in Medical Electronics?
1.Precision in High-Frequency Circuits – MRI, ultrasound, and advanced monitoring equipment require low-loss PCB materials to ensure clear, interference-free signal transmission.
2.Durability in Sterile Environments – Medical PCBs must endure frequent sterilization, exposure to chemicals, and varying humidity levels. Isola FR408 maintains dielectric performance and mechanical integrity under these conditions.
3.Support for Miniaturized Designs – Wearable and implantable devices require compact, multilayer PCBs with high-density interconnects (HDI). Isola FR408 supports HDI fabrication, enabling smaller, more complex circuit designs.
FAQ for Isola FR408 PCB materials
1.How does the processing temperature of Isola FR408 compare to other PCB materials?
Isola FR408 can handle higher processing temperatures, which helps in applications requiring thermal stability.
2.What impact does Isola FR408 have on signal integrity in high-speed designs?
Isola FR408 enhances signal integrity in high-speed designs by maintaining low loss and consistent dielectric properties.
3.What thickness options are available for Isola FR408 PCBs?
Isola FR408 is available in various thicknesses, which can be selected based on the specific needs of the PCB design.
4.What type of prepreg is recommended for use with Isola FR408?
Isola FR408 is typically paired with compatible prepregs designed for high-speed and high-frequency performance, such as Isola’s own prepregs.