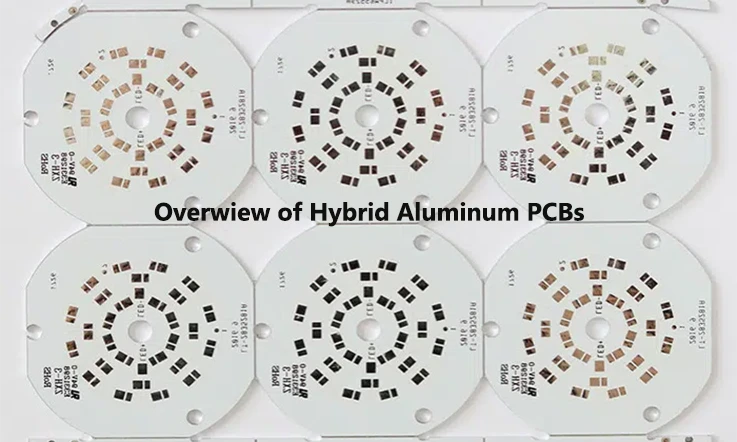
As modern electronic devices continue to become more compact and powerful, thermal management becomes a critical consideration. Hybrid Aluminum PCBs offer a reliable solution by effectively dissipating heat, preventing device overheating, and ensuring optimal performance and reliability. The aluminum base acts as a heat sink, efficiently transferring heat away from heat-generating components, resulting in improved lifespan and operational stability.
What is Hybrid Aluminum PCBs?
Hybrid aluminum PCBs, also known as metal-based PCBs or metal core PCBs, are circuit boards that use an aluminum base instead of the traditional FR4 (fiberglass-reinforced epoxy) material. They are designed to provide enhanced thermal management and improved electrical performance, making them well-suited for applications that require efficient heat dissipation and high-power capabilities.
Construction of a Hybrid Aluminum PCB
The construction of a hybrid aluminum PCB typically consists of three layers:
Aluminum Base Layer: The bottom layer of the PCB is made of aluminum, which acts as a heat sink and provides excellent heat dissipation properties. The aluminum base helps to efficiently transfer heat away from electronic components, preventing overheating and improving the overall thermal management of the PCB.
Dielectric Layer: Above the aluminum base, there is a layer of thermally conductive dielectric material. This layer provides electrical insulation between the aluminum base and the circuit layer while facilitating the transfer of heat from the components to the aluminum base. The dielectric material is designed to have good thermal conductivity to effectively dissipate heat.
Circuit Layer: The top layer of the hybrid aluminum PCB is the circuit layer, which contains the conductive traces, components, and solder mask. The circuit layer is typically made of copper, which is etched to create the desired circuitry. The components are mounted on the circuit layer, and the conductive traces provide electrical connections between them.
Benefits and Drawbacks of Using Hybrid Aluminum PCBs
Using hybrid aluminum PCBs offers some benefits and drawbacks. Let’s explore them:
Benefits of Hybrid Aluminum PCBs:
1. Excellent Thermal Management: The aluminum base of hybrid aluminum PCBs provides superior heat dissipation capabilities compared to traditional FR4 PCBs. This allows for efficient cooling of electronic components, reducing the risk of overheating, and enhancing the overall reliability and lifespan of the devices.
2. High Power Handling: Hybrid aluminum PCBs can handle higher power loads and power densities due to their improved thermal conductivity. They are well-suited for applications that require robust power distribution, such as power converters, motor drives, and high-power LED lighting.
3. Lightweight Design: Aluminum is a lightweight material, making hybrid aluminum PCBs a preferred choice for applications where weight reduction is crucial. Industries like aerospace, automotive, and portable electronics benefit from the lighter weight, leading to improved fuel efficiency, increased payload capacity, and enhanced portability.
4. Thermal Expansion Compatibility: Aluminum has a coefficient of thermal expansion (CTE) that closely matches that of semiconductor materials, like silicon. This compatibility reduces the risk of stress and damage to electronic components due to thermal expansion and contraction during operation, enhancing reliability.
5. Enhanced Electrical Performance: Hybrid aluminum PCBs offer improved electrical performance compared to standard PCBs. The aluminum base acts as a heat sink, reducing the operating temperature of components and minimizing the risk of thermal-induced electrical failures. Additionally, the metal core provides better electromagnetic shielding, reducing electromagnetic interference (EMI) and improving signal integrity.
Drawbacks of Hybrid Aluminum PCBs:
Cost: Hybrid aluminum PCBs can be more expensive than traditional FR4 PCBs due to the higher cost of aluminum and the additional manufacturing processes involved. This cost factor may be a consideration, particularly for cost-sensitive applications.
Machining Challenges: Aluminum is a relatively soft material compared to FR4, which can present challenges during manufacturing and assembly processes. Machining aluminum PCBs requires specialized tools and techniques to prevent damage or deformation of the aluminum base.
Limited Flexibility: Hybrid aluminum PCBs may have limited flexibility compared to traditional PCBs. The rigidity of the aluminum base restricts bending or flexing of the PCB, making them less suitable for applications that require flexible or bendable circuits.
Insulation Requirements: Since the aluminum base is conductive, additional insulation is required to prevent electrical short circuits. This insulation layer adds complexity to the manufacturing process and may increase overall PCB thickness.
It’s important to weigh the benefits and drawbacks of hybrid aluminum PCBs based on the specific requirements of the application. While they offer significant advantages in thermal management and high-power applications, the cost and manufacturing considerations should be taken into account.
Comparison with traditional PCB materials
The combination of the aluminum base with the dielectric layer and circuit layer creates a PCB that offers improved thermal management capabilities compared to traditional PCBs. The aluminum base acts as a heat sink, efficiently dissipating heat generated by the electronic components. This is particularly beneficial for applications that generate high levels of heat, such as power electronics and high-power LED lighting.
How to design a Hybrid Aluminum PCBs?
Designing a hybrid aluminum PCB requires careful consideration of thermal management, electrical connectivity, and mechanical stability. Here are some key steps to guide you through the design process:
Determine Design Requirements:
Identify the specific requirements of your application, such as thermal dissipation needs, power component placement, electrical connectivity, and mechanical constraints.
Define the form factor, size, and shape of the PCB according to the available space and integration requirements.
Thermal Management Considerations:
Analyze the thermal requirements of your design and identify the heat-generating components that require effective heat dissipation.
Plan the placement of power components and strategically position thermal vias beneath them to enhance the heat transfer from component to the aluminum base.
Optimize the size and shape of copper traces and thermal pads to maximize thermal conductivity throughout the PCB.
Material Selection:
Select the appropriate aluminum base material based on thermal conductivity, mechanical strength, and compatibility with assembly processes.
Choose the dielectric layer material that offers good electrical insulation while providing desired thermal characteristics suitable for your application.
Electrical Connectivity:
Determine the circuit layers and their interconnections to meet the electrical requirements of your design.
Plan the placement of signal, power, and ground planes to optimize signal integrity, power distribution, and noise reduction.
Ensure proper isolation between different circuit layers to prevent electrical interference and short circuits.
Mechanical Stability and Mounting:
Consider the mechanical stability of the hybrid aluminum PCB, especially when mounting heavy or large components.
Design the PCB with appropriate mounting holes, slots, or other mechanical features for secure attachment and structural integrity.
Account for any mechanical stress that may occur due to differential expansion rates between the aluminum base and other substrate materials.
Design for Manufacturability (DFM):
Follow design guidelines provided by the manufacturer or industry standards for hybrid aluminum PCBs.
Ensure proper spacing between components, traces, and pads to comply with manufacturing tolerances and prevent soldering issues.
Verify that the design meets the manufacturability requirements, including minimum drill sizes, aspect ratios, and copper thicknesses.
Prototype and Testing:
Create a prototype of the hybrid aluminum PCB to verify the design’s functionality, thermal performance, and mechanical stability.
Conduct thorough electrical testing, including signal integrity, power distribution, and thermal testing to validate the design’s performance.
Design Iteration and Optimization:
Evaluate the prototype results and make any necessary design modifications to address any identified issues or shortcomings.
Optimize the thermal management, electrical connectivity, and mechanical stability based on the prototype testing results.
Documentation and Gerber Files:
Prepare comprehensive documentation that includes detailed design specifications, layer stack-up, component placement, and routing information.
Generate accurate Gerber files that comply with the manufacturing requirements and standards.
Collaboration with Manufacturer:
Collaborate closely with a reputable hybrid aluminum PCB manufacturer to ensure that the design aligns with their capabilities and manufacturing processes.
Seek their expert guidance throughout the design process and leverage their knowledge and experience to optimize the design for manufacturability and reliability.
By following these steps and considering the specific requirements of thermal management, electrical connectivity, and mechanical stability, you can design a high-quality hybrid aluminum PCB that meets the needs of your application.
Precautions for the production of Hybrid Aluminum PCBs
When producing hybrid aluminum PCBs, it is important to take several precautions to ensure the manufacturing process goes smoothly and the final products meet the desired standards. Here are some precautions to consider:
Material Selection:
Choose appropriate aluminum substrate materials with adequate thermal conductivity, mechanical strength, and compatibility with the application requirements.
Ensure the dielectric layer materials are compatible with both the aluminum base and the other substrate materials used in the hybrid assembly.
Design Considerations:
Pay attention to thermal management aspects during the design phase to ensure proper heat dissipation and minimize thermal stresses.
Consider the differential expansion rates between the aluminum base and other substrate materials. Adjust the design to accommodate for potential differences in CTE (Coefficient of Thermal Expansion).
Manufacturing Processes:
Implement precise and reliable drilling techniques to achieve accurate hole placement and prevent misalignment.
Optimize the soldering process parameters, such as temperature, time, and flux selection, taking into account the specific requirements of the aluminum PCBs.
Utilize appropriate soldering techniques, such as selective soldering or reflow soldering, based on the specific needs and component types being used.
Implement proper cleanliness and surface preparation techniques to ensure good solder wetting and reliable solder joints on the aluminum substrate.
Handling and Assembly:
Take precautions to prevent contamination of the aluminum surface, such as wearing gloves and using clean handling procedures.
Ensure proper electrical grounding during handling and assembly to avoid electrostatic discharge (ESD) damage to sensitive components and the aluminum substrate.
Implement proper handling and fixturing techniques to prevent damage to the delicate aluminum PCB during assembly processes.
Testing and Quality Control:
Implement rigorous quality control measures to check for any defects and ensure the assembled hybrid aluminum PCBs meet the desired specifications.
Perform thorough electrical and functional testing to verify the performance and reliability of the assembled PCBs before deployment.
Documentation and Traceability:
Maintain comprehensive documentation throughout the production process, including design files, assembly instructions, process parameters, and test records.
Establish a traceability system to track and identify each hybrid aluminum PCB, enabling effective troubleshooting, quality control, and future reference.
Continuous Improvement:
Regularly review and evaluate the manufacturing processes, identifying areas for improvement to enhance the quality, efficiency, and consistency of hybrid aluminum PCB production.
Encourage collaboration and feedback between different stakeholders, such as the design team, manufacturing team, and customers, to identify and address any potential issues or challenges early on.
Implementing these precautions will help ensure the successful manufacturing of hybrid aluminum PCBs while maintaining high standards of quality, reliability, and functionality in the final products.
How To Find a Reliable Hybrid Aluminum PCBs Maker?
To find a reliable hybrid aluminum PCB manufacturer, consider the following steps:
Research and Referrals:
Start by researching and compiling a list of potential manufacturers who specialize in hybrid aluminum PCBs. Look for manufacturers with a solid reputation and experience in producing high-quality aluminum PCBs.
Seek recommendations from industry peers, colleagues, or professional networks who have previously worked with reliable hybrid aluminum PCB manufacturers.
Evaluate Manufacturing Capabilities:
Visit the manufacturers’ websites or reach out to their sales or customer service teams to gather information about their manufacturing capabilities. Pay attention to their experience in hybrid aluminum PCBs, equipment quality, certifications, and product quality control processes.
Quality Standards and Certifications:
Assess whether the manufacturer adheres to internationally recognized quality standards, such as ISO 9001, ISO 14001, or IATF 16949 for automotive applications. Recognized certifications are indicative of a manufacturer’s commitment to quality and process control.
Samples and Prototyping:
Request samples or prototyping services from shortlisted manufacturers to evaluate their manufacturing quality and capabilities. This will allow you to assess their attention to detail, accuracy, and adherence to specifications.
Technical Expertise and Support:
Evaluate the technical expertise and customer support provided by the manufacturer. Do they have knowledgeable engineers who can provide guidance and support throughout your project? Clear communication channels and responsive customer service are vital for a successful partnership.
Manufacturing Facility Visit:
Arrange a visit to the manufacturing facility, if possible, to view their production capabilities firsthand. This will allow you to assess their equipment, production processes, quality control measures, and overall manufacturing environment.
Customer References and Reviews:
Ask the manufacturer for customer references or seek out independent reviews and testimonials from other clients. Feedback from existing customers can provide valuable insights into the manufacturer’s reliability, timeliness, and customer satisfaction levels.
Pricing and Lead Times:
Obtain detailed quotes from multiple manufacturers, considering factors such as pricing, lead times, and delivery terms. Be cautious of extremely low prices, as they may indicate compromise in quality or service.
Flexibility and Customization:
Determine if the manufacturer can accommodate your specific hybrid aluminum PCB requirements, such as customized designs, specifications, or special considerations. A reliable manufacturer will be adaptable and flexible to meet your specific needs.
Continuous Improvement and Long-Term Partnership:
Inquire about the manufacturer’s commitment to continuous improvement and their willingness to establish a long-term partnership. A reliable manufacturer should be focused on building strong customer relationships and continuously improving their processes.
By following these steps and conducting thorough due diligence, you can find a reliable hybrid aluminum PCB maker that meets your requirements and delivers high-quality products.
Future Trends and Developments of Hybrid Aluminum PCBs
The future trends and developments of hybrid aluminum PCBs are driven by the growing demand for advanced thermal management and high-power electronic applications. Here are some potential areas of development for hybrid aluminum PCBs:
Improved Thermal Conductivity: Researchers and manufacturers are constantly exploring ways to enhance the thermal conductivity of hybrid aluminum PCBs. This includes the development of new dielectric materials with higher thermal conductivity to further improve heat dissipation and thermal management capabilities.
Miniaturization and Higher Component Density: Future developments may focus on achieving higher component density and miniaturization while maintaining efficient heat dissipation. This could involve advancements in circuit design, materials, and manufacturing techniques to accommodate smaller and more densely packed electronic components.
Integration of Advanced Technologies: Hybrid aluminum PCBs may incorporate advanced technologies to enhance their functionalities. For example, the integration of embedded heat pipes or vapor chambers within the PCB structure could provide even more effective heat transfer and cooling.
Flexible Hybrid Aluminum PCBs: Currently, hybrid aluminum PCBs are primarily rigid due to the aluminum base. However, future developments may explore the integration of flexible materials and techniques to create hybrid aluminum PCBs that offer both thermal management benefits and flexibility for applications that require bendable circuits.
Advanced Manufacturing Techniques: The development of innovative manufacturing techniques, such as additive manufacturing (3D printing) or advanced etching methods, could enable more complex designs and customized hybrid aluminum PCBs. These techniques may also contribute to cost reduction and faster production processes.
Integration of Smart Features: With the rise of the Internet of Things (IoT) and smart devices, hybrid aluminum PCBs may incorporate smart features such as embedded sensors for temperature monitoring, adaptive thermal management, and self-diagnostic capabilities. These features could enhance the functionality, reliability, and overall performance of electronic systems.
Sustainability and Environmental Concerns: Future developments may focus on making hybrid aluminum PCBs more environmentally friendly. This could involve using recycled aluminum materials, exploring greener manufacturing processes, and ensuring proper disposal and recycling methods for end-of-life PCBs.
It’s important to note that these trends and developments are speculative and based on the current trajectory of electronics and PCB technology. The actual future advancements in hybrid aluminum PCBs will depend on ongoing research, technological breakthroughs, market demands, and industry collaborations.
Conclusion
Hybrid aluminum PCBs have revolutionized the field of electronics by providing an effective solution for thermal management and high-power applications. Their ability to dissipate heat efficiently, handle high-power loads, and offer lightweight design makes them indispensable in numerous industries.
As technology continues to advance, the future of hybrid aluminum PCBs holds promising developments such as improved thermal conductivity, miniaturization, flexibility, integration of advanced technologies, and sustainable manufacturing practices. These advancements will further enhance the performance, reliability, and versatility of hybrid aluminum PCBs, catering to the evolving needs of the electronics industry. With their continued innovation and adoption, hybrid aluminum PCBs are set to play a vital role in enabling the next generation of high-performance electronic devices.