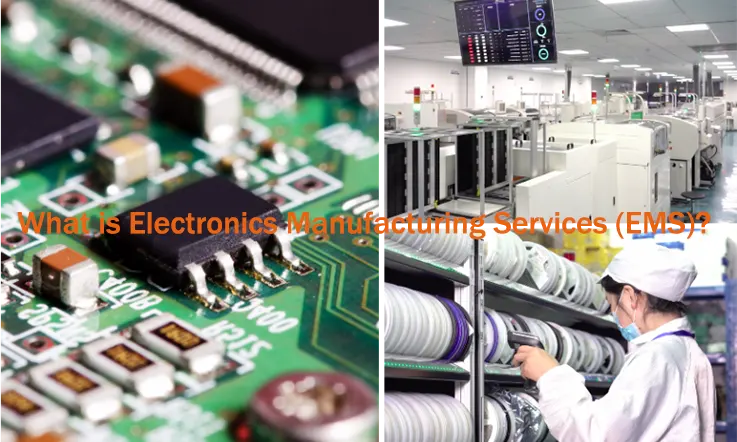
Electronics Manufacturing Services (EMS) power industries ranging from consumer electronics to aerospace, medical devices, and industrial automation. As technology advances, manufacturers are integrating cutting-edge processes such as high-density interconnect (HDI) PCBs, rigid-flex circuits, lead-free soldering, AI-driven quality inspection, and 5G-enabled automation to keep up with evolving market demands.
In EMS, PCB manufacturing involves material selection, signal integrity optimization, and thermal management, while PCB assembly incorporates Surface Mount Technology (SMT) and Through-Hole Technology (THT). High-reliability production requires precise design and strict quality control methods, including In-Circuit Testing (ICT), functional testing, and Environmental Stress Screening (ESS). Additionally, supply chain management plays a central role in global component sourcing, inventory forecasting, and counterfeit component prevention.
This guide delves into the core technologies, cost optimization strategies, and critical factors in selecting the right manufacturing partner, providing OEMs, PCB designers, and manufacturers with a comprehensive industry perspective.
Understanding Electronics Manufacturing Services (EMS) and Its Industry Applications
Electronics Manufacturing Services (EMS) support the design, assembly, testing, and distribution of electronic products across various industries. Companies that rely on EMS providers gain access to advanced manufacturing technologies, streamlined supply chain management, and specialized expertise. From printed circuit board (PCB) assembly to full system integration, EMS providers assist businesses in optimizing production and ensuring product reliability.
Each industry has its own manufacturing needs, regulatory requirements, and production complexities. The right EMS approach depends on factors such as material sourcing strategies, compliance standards, and production volume. A closer look at EMS operations and their role in different sectors provides insight into how companies leverage these services.
What Are Electronics Manufacturing Services (EMS) and Their Core Functions?
EMS providers cover multiple aspects of electronic product development and manufacturing. Their facilities incorporate automated production lines, precision assembly techniques, and quality control systems to handle complex builds. EMS offerings extend beyond manufacturing to include supply chain coordination and post-production support.
Core Functions of EMS Providers-
Function | Description |
PCB Fabrication & Assembly | Production of printed circuit boards using surface mount technology (SMT) and through-hole technology (THT). |
Prototyping & NPI (New Product Introduction) | Small-batch production runs to evaluate design effectiveness and manufacturability. |
Supply Chain Management | Component sourcing, procurement strategies, and inventory control to prevent disruptions. |
Testing & Quality Assurance | Inspection processes, including in-circuit testing (ICT), automated optical inspection (AOI), and functional validation. |
Box Build & Final Assembly | Integration of electronics into enclosures with wiring, firmware installation, and final testing. |
Regulatory Compliance & Certifications | Adherence to industry-specific standards such as IPC-A-610, ISO 9001, RoHS, and ITAR. |
Aftermarket & Repair Services | Maintenance, refurbishment, and troubleshooting support for electronic products. |
Automated equipment and industry best practices improve consistency across these processes. EMS providers structure production workflows to match client specifications while addressing environmental considerations, design complexity, and performance testing.
How EMS Supports Consumer Electronics, Aerospace, and Medical Device Industries?
EMS providers work with companies across multiple sectors, each with distinct production requirements. Their ability to handle precision manufacturing, compliance mandates, and efficient logistics makes them valuable partners in delivering high-quality electronic products.
Consumer Electronics: High-Volume Manufacturing and Rapid Production Cycles-
Consumer electronics manufacturing prioritizes efficiency, cost management, and fast turnaround times. Devices such as smartphones, gaming consoles, and home automation systems require streamlined production to keep pace with shifting market trends. EMS providers implement automated assembly lines and design-for-manufacturability (DFM) strategies to support these projects.
Key Considerations in Consumer Electronics EMS:
●High-speed SMT placement for miniaturized components.
●Flexible production scaling to accommodate demand fluctuations.
●Efficient prototyping and rapid validation of new designs.
Aerospace & Defense: Compliance and High-Reliability Manufacturing-
Electronics used in aerospace and defense applications must endure harsh environments, extreme temperatures, and electromagnetic interference. EMS providers in this sector follow strict manufacturing guidelines and conduct extensive testing to validate product performance under stress conditions.
Core Considerations in Aerospace & Defense EMS:
●Conformal coating and thermal management solutions for extended durability.
●Multi-stage inspection and quality verification processes.
●Secure supply chain oversight for controlled component sourcing.
Medical Devices: Regulatory Adherence and Precision Assembly-
The medical industry enforces strict regulations to ensure the safety and effectiveness of electronic equipment. EMS providers working in this sector must document every stage of production, maintain cleanroom assembly environments, and comply with international medical standards.
Main Considerations in Medical Device EMS:
●ISO 13485 certification and adherence to FDA guidelines.
●Comprehensive traceability systems for material tracking.
●Electrostatic discharge (ESD) protection measures to prevent component failures.
Each of these industries depends on EMS providers to meet specific production challenges. The choice of an EMS partner should align with the regulatory, technological, and logistical demands of the sector.
Differences Between EMS, ODM, and OEM in Electronics Production
EMS, ODM (Original Design Manufacturer), and OEM (Original Equipment Manufacturer) represent different approaches to electronics production. Understanding their distinctions helps businesses determine the best outsourcing strategy for their needs.
Model | Description |
EMS (Electronics Manufacturing Services) | Provides contract manufacturing, PCB assembly, testing, and logistics for various clients. |
ODM (Original Design Manufacturer) | Designs and produces electronic products, which other brands can customize and resell. |
OEM (Original Equipment Manufacturer) | Develops and markets electronic products under its own brand but outsources production. |
Choosing the Right Model for Production Needs-
●EMS providers handle manufacturing without contributing to product design. Companies looking for reliable assembly, testing, and supply chain services benefit from this model.
●ODM companies offer pre-designed solutions that can be modified based on customer requirements. This option is suitable for businesses that want to introduce products with minimal design investment.
●OEMs maintain control over the design and branding of their products while relying on external manufacturing partners for production scalability.
Selecting the appropriate approach depends on production goals, cost considerations, and the level of design involvement required. EMS remains a solution for companies seeking specialized manufacturing support without investing in in-house production infrastructure.
High-Precision PCB Manufacturing in Electronics Manufacturing Services (EMS)
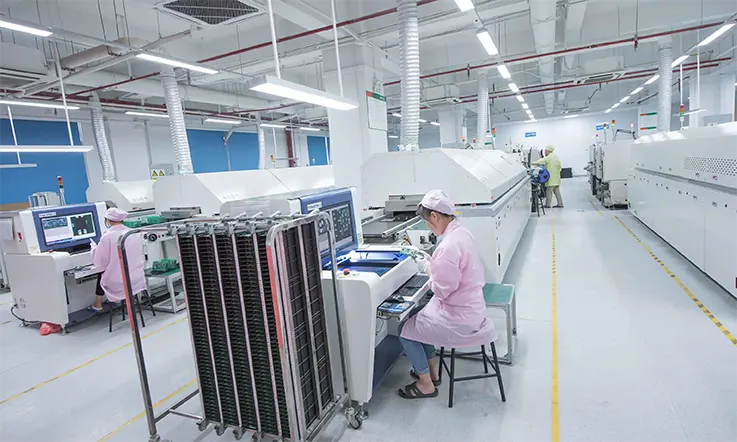
Printed circuit boards are at the center of electronic manufacturing, providing the structural and electrical foundation for everything from everyday consumer gadgets to high-performance aerospace and medical devices. The demand for smaller, more efficient, and more complex circuit boards has led to advancements in fabrication methods, material selection, and quality assurance. EMS providers apply specialized manufacturing techniques to ensure that PCBs meet electrical, mechanical, and environmental requirements while keeping production scalable and cost-effective.
This section explores how EMS companies handle PCB fabrication, the materials used to optimize performance, and the industry standards that define manufacturing quality.
Advanced PCB Fabrication Techniques: HDI, Rigid-Flex, and Multilayer Boards
The push for high-performance electronics has driven PCB manufacturing to evolve beyond standard two-layer designs. Depending on the application, manufacturers incorporate high-density interconnect (HDI) designs, rigid-flex configurations, or multilayer structures to maximize space utilization, improve signal integrity, and enhance durability.
HDI (High-Density Interconnect) PCB Fabrication-
HDI boards allow for finer trace patterns, smaller vias, and increased wiring density, making them suitable for compact and high-speed applications such as telecommunications equipment and advanced computing systems.
Characteristics of HDI PCBs:
●Microvias and laser-drilled holes for compact circuit routing.
●Sequential lamination for high layer count and signal efficiency.
●Optimized stack-ups that reduce electromagnetic interference (EMI).
Rigid-Flex PCB Manufacturing-
Rigid-flex PCBs combine the durability of rigid circuits with the adaptability of flexible substrates. These designs eliminate the need for connectors between different sections of a board, reducing potential failure points and saving space.
Manufacturing considerations for rigid-flex PCBs:
●Layer stacking to balance mechanical flexibility and electrical performance.
●Controlled impedance routing to support high-speed data transmission.
●Precision laser cutting and drilling for clean flex section transitions.
Multilayer PCB Production-
For applications requiring complex signal distribution and power management, multilayer PCBs provide a way to incorporate multiple circuits within a compact design.
Factors influencing multilayer PCB fabrication:
●Material selection for dielectric layers to maintain consistent electrical properties.
●Advanced lamination techniques to prevent internal delamination.
●Copper thickness optimization for efficient current flow.
EMS providers select the appropriate PCB fabrication approach based on product requirements, ensuring durability, efficiency, and manufacturability at scale.
Material Selection for High-Reliability PCBs: FR4, Rogers, and Ceramic Substrates
The materials used in PCB construction affect electrical performance, heat dissipation, and mechanical strength. EMS providers work with a range of substrates to match the needs of specific applications, balancing factors such as frequency stability, thermal resistance, and cost efficiency.
FR4: Standard for General-Purpose PCBs-
FR4 is the most widely used PCB material, offering a combination of electrical insulation, mechanical strength, and affordability. It is commonly found in industrial automation, consumer electronics, and automotive applications.
FR4 Properties | Typical Value |
Dielectric Constant (Dk) | ~4.2 – 4.8 |
Thermal Conductivity | ~0.25 W/m·K |
Glass Transition Temperature (Tg) | 130°C – 180°C |
Rogers Materials: Designed for High-Frequency Electronics-
For applications requiring low signal loss and improved thermal stability, Rogers laminates provide better electrical performance than traditional FR4. These materials are frequently used in 5G networks, aerospace radar systems, and RF communication devices.
Advantages of Rogers PCB Materials:
●Low loss tangent for reduced signal degradation.
●Stable dielectric constant across temperature variations.
●High-frequency compatibility for microwave and millimeter-wave circuits.
Ceramic Substrates: Thermal Stability and Durability-
Ceramic-based PCBs handle extreme temperature conditions and provide excellent thermal conductivity, making them reliable for power electronics, automotive engine controls, and high-reliability aerospace components.
Why Ceramic Substrates Are Used:
●High resistance to oxidation and moisture exposure.
●Efficient heat dissipation for high-power circuits.
●Low expansion rates, reducing stress on solder joints.
Each material offers unique properties that determine its suitability for different PCB applications. EMS providers assess operating conditions, signal requirements, and production scale to select the best material for a given design.
How EMS Ensures PCB Manufacturing Meets Industry Standards?
PCB manufacturing follows strict guidelines to ensure that boards function correctly and maintain consistency across production batches. EMS providers integrate industry-recognized quality standards and inspection methods to verify that every PCB meets performance expectations before final assembly.
IPC Standards in PCB Manufacturing-
The IPC (Institute for Printed Circuits) establishes globally accepted benchmarks for PCB design, fabrication, and testing. Compliance with IPC standards reduces variability and ensures that manufacturers follow best practices.
IPC Standard | Purpose |
IPC-6012 | Qualification and performance for rigid PCBs |
IPC-2221 | Generic design standards for printed circuits |
IPC-A-600 | Acceptability of printed boards |
Testing and Quality Control in PCB Production-
EMS providers conduct multiple rounds of testing to detect defects and confirm that boards function as intended.
●Automated Optical Inspection (AOI): Uses high-resolution cameras to identify issues such as solder bridging and misaligned components.
●In-Circuit Testing (ICT): Checks continuity and component values to verify electrical correctness.
●X-Ray Inspection: Analyzes hidden solder joints, particularly for ball grid arrays (BGAs) and multilayer PCBs.
●Thermal Cycling & Burn-In Testing: Simulates real-world operating conditions to evaluate long-term reliability.
Regulatory Compliance for Industry-Specific Applications-
Different industries require additional certifications to meet product safety and performance regulations.
●ISO 13485: Required for medical electronics manufacturing.
●IATF 16949: Ensures compliance with automotive industry production standards.
●ITAR Compliance: Necessary for defense and aerospace applications.
PCB Assembly Processes in Electronics Manufacturing Services (EMS)
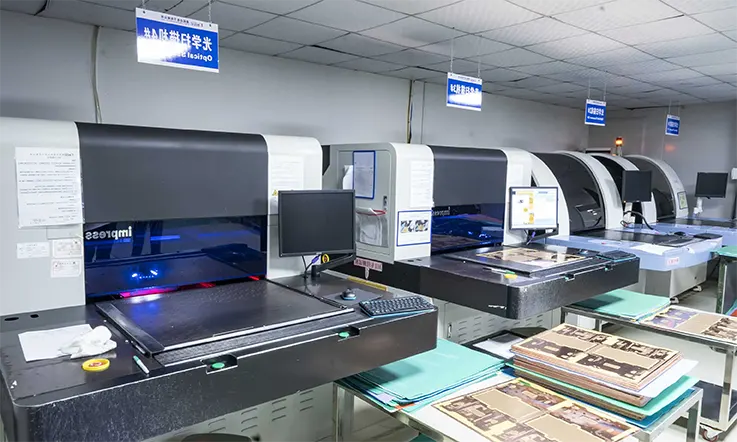
Building a circuit board is more than just placing components onto a substrate. Every step in the assembly process impacts how well the final product operates in real-world conditions. EMS providers bring together advanced automation, skilled technicians, and strict quality control measures to deliver reliable PCBs for industries such as consumer electronics, aerospace, and medical technology.
Choosing the right assembly method, soldering techniques, and inspection processes ensures that boards can handle high-performance demands while meeting regulatory standards. Let’s break down the most widely used PCB assembly techniques, lead-free soldering advancements, and quality assurance methods that keep production in check.
Surface Mount Technology (SMT) vs. Through-Hole Technology (THT) in EMS
Every PCB design calls for an assembly method that aligns with its application. Two widely used techniques—Surface Mount Technology (SMT) and Through-Hole Technology (THT)—offer different benefits based on factors such as board complexity, durability requirements, and manufacturing scale.
Surface Mount Technology (SMT) Assembly-
SMT has transformed PCB production by allowing smaller, lightweight components to be placed directly onto the surface of the board. With automated pick-and-place machines and reflow soldering, this method supports high-speed manufacturing while keeping costs manageable.
Advantages of SMT in EMS Manufacturing:
●Supports compact, lightweight designs for modern electronics.
●Enables faster, high-volume production through automation.
●Enhances electrical performance by reducing lead length.
SMT Assembly Process in EMS:
Step | Description |
Solder Paste Application | A stencil applies solder paste onto PCB pads. |
Component Placement | Automated machines precisely position components. |
Reflow Soldering | Controlled heat bonds components securely. |
Inspection & Testing | AOI and functional tests ensure proper assembly. |
Through-Hole Technology (THT) Assembly-
While SMT dominates modern electronics, THT still plays a strong role in applications that demand durable mechanical connections, such as industrial controls and aerospace systems.
When THT Makes Sense:
●Ideal for components handling high currents and voltages.
●Strengthens solder joints for vibration-heavy environments.
●Simplifies repairs and modifications in certain designs.
Common THT Soldering Methods:
Method | How It Works |
Wave Soldering | A molten solder wave bonds components efficiently. |
Hand Soldering | Used for repairs, prototypes, and specialty components. |
Selective Soldering | A precise alternative for mixed-technology boards. |
Many EMS providers combine SMT and THT in hybrid PCB designs to balance speed, durability, and cost.
Lead-Free and RoHS-Compliant Soldering Techniques for EMS Manufacturing
Shifting away from traditional lead-based solder has become a priority in electronics manufacturing. With Restriction of Hazardous Substances (RoHS) compliance required in many regions, EMS companies now rely on lead-free solder alloys that meet environmental and performance standards.
Popular RoHS-Compliant Soldering Alloys-
Lead-free soldering brings challenges, such as higher melting points and different wetting properties. The table below highlights commonly used alternatives.
Solder Alloy | Composition | Melting Point (°C) | Why It’s Used |
SAC305 | Sn96.5/Ag3.0/Cu0.5 | 217-220 | Reliable for most applications. |
Sn100C | Sn99.3/Cu0.7 | 227 | Reduces oxidation risks. |
Bi57Sn42Ag1 | Bi57/Sn42/Ag1 | 138 | Low-temperature option for sensitive components. |
How EMS Providers Handle Lead-Free Soldering Challenges-
●Higher Heat Requirements: Adjusted reflow profiles prevent thermal stress.
●Oxidation Risks: Nitrogen reflow ovens reduce defect rates.
●Solder Joint Durability: Flux and pad design modifications improve bonding.
As lead-free technology continues evolving, EMS manufacturers refine their processes to meet industry expectations without compromising reliability.
The Role of Automated Optical Inspection (AOI) in EMS PCB Assembly
No matter how advanced a manufacturing process is, errors can still occur. A single misplaced component or poor solder joint can lead to performance issues, product recalls, or safety risks. Automated Optical Inspection (AOI) systems step in to catch these issues before they become bigger problems.
How AOI Works in PCB Manufacturing-
AOI relies on high-resolution cameras, pattern recognition, and machine learning algorithms to inspect every PCB that comes off the assembly line.
Inspection Method | What It Detects |
2D AOI | Surface defects, missing components, solder misalignment. |
3D AOI | Solder volume, height variations, coplanarity issues. |
X-Ray AOI | Hidden solder defects (e.g., BGAs, QFNs). |
Why EMS Providers Use AOI in PCB Assembly-
●Fast Detection: Finds errors immediately, reducing rework time.
●Handles High-Speed Production: Keeps up with automated lines.
●Supports Complex PCB Designs: Inspects fine-pitch components and multi-layer structures.
With AOI acting as a checkpoint, EMS manufacturers can maintain high-quality production standards while reducing waste and improving efficiency.
Design for Manufacturability (DFM) and Design for Assembly (DFA) in EMS
Bringing a PCB design from concept to production isn’t just about getting circuits onto a board—it’s about making sure the design works seamlessly with real-world manufacturing processes. Design for Manufacturability (DFM) and Design for Assembly (DFA) are the foundation of any EMS workflow, ensuring that a product moves through fabrication and assembly without delays, cost overruns, or performance issues.
Companies that overlook these principles often find themselves battling production bottlenecks, excessive scrap rates, or field failures. By considering material choices, layout efficiency, and component selection upfront, EMS providers help us refine their designs for streamlined manufacturing. Let’s dive into the core aspects of PCB layout optimization, common design missteps, and engineering challenges related to high-speed signals and thermal performance.
How EMS Providers Optimize PCB Layout for Cost-Effective Manufacturing?
PCB layout is where good intentions meet real-world constraints. A design that looks flawless on a screen might end up causing unnecessary delays and expenses if it’s not aligned with manufacturing processes. EMS providers help engineers fine-tune layouts so they integrate with standard fabrication techniques, automated assembly, and quality control procedures.
To make production flow without unnecessary setbacks, we focus on several aspects of PCB design:
●Component placement: Parts need to be arranged in a way that allows automated machines to place them accurately and efficiently.
●Trace routing: Poorly designed trace paths can lead to signal integrity issues and added costs during manufacturing.
●Drill hole sizing and spacing: Incorrectly specified holes can cause issues with plating and lead to board failures.
●Panelization strategies: Multiple PCBs are often fabricated in a single panel to improve throughput and reduce waste.
Taking the time to refine these aspects early means fewer production slowdowns, better material utilization, and a smoother transition from prototype to full-scale manufacturing.
Common PCB Design Mistakes and Their Impact on EMS Production
Even the best engineers occasionally overlook factors that affect manufacturing. Some mistakes might not show up until production begins—when it’s already too late to fix them without adding cost and delays.
EMS providers regularly see preventable issues that could have been caught with an early DFM check, such as:
●Mismatched footprints: Components that don’t align properly with the PCB pads can lead to soldering defects.
●Inconsistent trace widths: This can create electrical performance issues, especially in high-speed designs.
●Poor thermal relief design: Incorrect copper connections around component leads can cause soldering inconsistencies.
●Sharp angles in traces: This increases the risk of electrical noise and signal degradation.
●Overlapping copper pours: Unintended shorts can occur, leading to rework or scrapped boards.
Signal Integrity, Thermal Management, and High-Speed Design Considerations
Modern circuit boards are pushing limits in speed, power, and miniaturization. The smaller and denser a board becomes, the more engineers need to pay attention to signal integrity, heat dissipation, and electromagnetic interference.
When it comes to signal performance, trace width, spacing, and layer stack-up all play a role in reducing unwanted noise and ensuring signals reach their destination intact. Poor routing or improper impedance matching can lead to performance drops or even complete circuit failure.
Thermal management is another major factor, especially in designs where power-hungry components are packed into tight spaces. Without the right strategy, heat builds up quickly and can cause instability or shorten the lifespan of electronic devices. EMS providers use a combination of thermal vias, copper thickness adjustments, and heat sinks to keep temperatures under control.
Ignoring these factors isn’t just an inconvenience—it can mean the difference between a reliable product and one that struggles in real-world conditions.
Prototyping and Quality Control in Electronics Manufacturing Services (EMS)
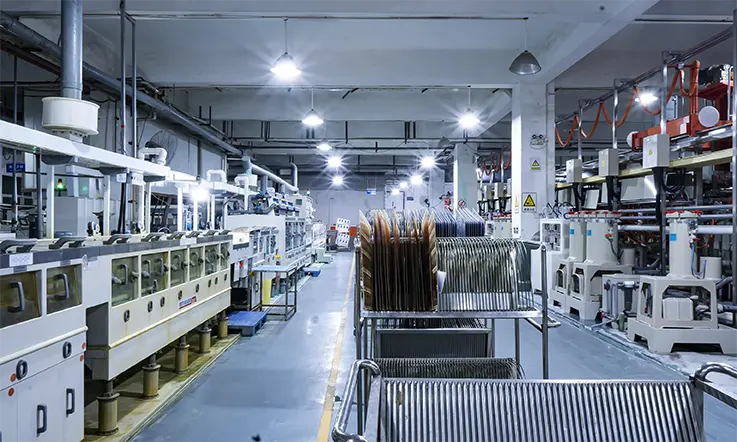
Transforming an electronic idea into a finished product is no simple task. Every step requires meticulous planning, precise execution, and strict validation. Before moving to full-scale production, PCB prototyping and quality assurance ensure a hassle-free transition.
EMS can providers help our engineers fine-tune designs, resolve manufacturing bottlenecks, and confirm performance expectations long before production ramps up. Without these steps, companies risk unexpected delays, excessive costs, and compromised product reliability—headaches no business wants to deal with.
Let’s break down how prototyping, testing, and compliance shape the electronics manufacturing landscape.
Rapid PCB Prototyping: Refining Designs Before Full-Scale Production
Prototyping is where ideas get stress-tested. Engineers get a chance to spot flaws, improve circuit layouts, and confirm electrical performance before committing to large production runs. EMS providers use various methods to keep this process efficient, including:
●Quick-turn PCB fabrication: Accelerates design iterations with rapid manufacturing of prototype boards.
●On-demand assembly services: Allows small-batch PCB assembly with precise component placement, even for fine-pitch and BGA packages.
●Additive manufacturing for test fixtures: Enables quick adjustments to connectors, enclosures, and mechanical parts.
While prototyping saves time and refines designs, we need to consider material compatibility, DFM constraints, and real-world manufacturing limitations. A well-executed prototype prevents unexpected surprises during full-scale production.
PCB Testing Methods: Preventing Failures Before They Happen
No manufacturer wants to deal with field failures, product recalls, or unhappy customers. That’s why EMS providers implement multiple testing strategies to detect design flaws, process inconsistencies, and performance issues before PCBs leave the factory.
●In-Circuit Testing (ICT): Detects component placement errors, shorts, and open circuits at the board level.
●Functional Testing: Simulates real-world operating conditions to confirm PCBs perform as intended.
●Environmental Stress Screening (ESS): Subjects PCBs to temperature fluctuations, vibration, and humidity to assess durability in harsh conditions.
Skipping these steps invites costly rework, delays, and customer dissatisfaction. Thorough testing ensures PCBs meet application requirements and maintain consistent performance over time.
EMS Industry Certifications: Meeting Manufacturing and Regulatory Standards
For EMS providers, compliance is non-negotiable. Certifications demonstrate adherence to manufacturing protocols, process controls, and regulatory requirements across various industries. Some of the most recognized certifications include:
●IPC Standards: Define quality benchmarks for PCB fabrication, assembly, and inspection.
●ISO 9001: Outlines best practices for maintaining consistent production processes and customer satisfaction.
●FDA Compliance: Applies to medical electronics, ensuring devices meet strict safety and performance regulations.
Electronics Manufacturing Services (EMS) and Supply Chain Management
Electronics Manufacturing Services (EMS) isn’t just about building printed circuit boards or assembling electronic devices—it’s about making sure every component, from microcontrollers to capacitors, arrives on time, meets specifications, and stays within budget.
With global supply chains becoming more unpredictable, EMS providers must navigate sourcing challenges, fluctuating lead times, and compliance requirements to keep production lines moving. Companies that fail to adapt to supply chain disruptions risk project delays, unexpected costs, and even lost customers.
Let’s explore how EMS providers handle supply chain risks, leverage AI-driven forecasting, and prevent counterfeit components from infiltrating production.
Managing Global Supply Chain Risks in EMS Manufacturing
The electronics industry has always been at the mercy of market fluctuations, geopolitical events, and material shortages. A single bottleneck—whether it’s a semiconductor shortage or a shipping delay—can send shockwaves through an entire production schedule.
EMS providers tackle these risks by:
●Diversifying suppliers: Relying on a single vendor for critical components is a recipe for trouble. EMS companies maintain a network of alternative suppliers to ensure steady supply.
●Strategic inventory planning: Stockpiling high-risk components and forecasting demand helps prevent last-minute scrambles for parts.
●Regional sourcing strategies: Nearshoring production can cut down on customs delays, tariffs, and transportation costs, keeping things more predictable.
Manufacturers that take a proactive approach to supply chain management can avoid the costly pitfalls that come with last-minute part substitutions, production halts, and rushed redesigns.
The Role of AI in Component Sourcing and Inventory Forecasting
AI is changing the game in how EMS providers source components, predict shortages, and optimize inventory levels. Traditional forecasting methods struggle to keep up with market volatility, but AI-driven solutions offer real-time insights that help manufacturers stay ahead.
Here’s how AI transforms supply chain management in EMS:
●Predictive analytics: AI-powered systems analyze historical purchase data, global supply trends, and real-time demand shifts to flag potential shortages before they happen.
●Automated supplier matching: Instead of relying on manual searches, AI can scan global databases and recommend alternative sources when parts are unavailable.
●Smart inventory control: AI can identify slow-moving stock and optimize reorder points, preventing overstocking or last-minute shortages.
EMS companies that embrace AI-driven supply chain strategies can make smarter purchasing decisions, minimize disruptions, and reduce excess costs tied to poor inventory planning.
Preventing Counterfeit Electronic Components in EMS Supply Chain
Counterfeit electronic components aren’t just a nuisance—they can lead to device failures, warranty claims, and even safety hazards. With counterfeiters getting more sophisticated, EMS providers need strict screening processes to keep fake parts out of their supply chain.
Here’s how EMS providers spot and eliminate counterfeit risks:
●Trusted vendor partnerships: EMS companies work only with authorized distributors and certified suppliers to avoid gray-market parts.
●Advanced component testing: X-ray inspection, decapsulation analysis, and electrical testing help detect counterfeit semiconductors and passive components.
●Blockchain-based tracking: Some companies use digital ledgers to trace components from manufacturer to end product, ensuring authenticity.
A robust anti-counterfeit strategy saves us from costly recalls, brand damage, and potential liability issues. Cutting corners in component sourcing isn’t worth the risk when product integrity is on the line.
Cost Optimization Strategies in Electronics Manufacturing Services (EMS)
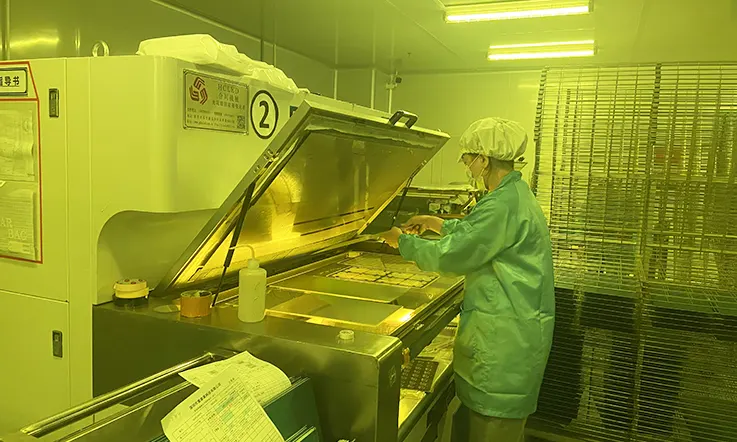
Electronics Manufacturing Services (EMS) providers are always on the lookout for ways to reduce expenses while maintaining production standards. Every decision, from PCB manufacturing methods to supply chain efficiency, directly impacts overall costs. Smart planning, material selection, and streamlined logistics can lead to significant savings without sacrificing reliability.
Let’s explore how EMS companies control production costs while ensuring efficiency remains high.
Reducing PCB Manufacturing Costs Without Compromising Quality
Lowering PCB manufacturing costs requires a combination of strategic design, material efficiency, and process refinement. Adjusting panelization, standardizing board sizes, and selecting cost-effective substrates all contribute to savings without causing performance issues down the line.
Approaches to Lower PCB Manufacturing Costs-
Cost Reduction Method | Impact on Expenses |
Optimized Panelization | Reduces material waste by increasing board yield |
Standardized Board Dimensions | Eliminates custom tooling fees |
Bulk Purchasing of Components | Lowers per-unit cost with supplier discounts |
Alternative Substrates | Finds balance between material cost and performance |
Layer Reduction | Cuts down on manufacturing complexity |
By focusing on these adjustments, EMS providers keep manufacturing expenses under control while ensuring PCBs meet performance expectations.
The Advantages of Outsourcing PCB Assembly to EMS Providers
Handing over PCB assembly to an EMS provider helps businesses streamline operations and reduce in-house expenses. With established infrastructure, experienced staff, and access to cost-effective materials, EMS companies handle production more efficiently than many in-house setups.
How EMS Outsourcing Reduces Expenses-
Factor | Effect on Cost |
Large-Scale Production | Lowers per-unit costs through high-volume assembly |
Skilled Technicians | Removes need for extensive in-house training |
Advanced Equipment Access | Avoids investment in costly machinery |
Shorter Lead Times | Minimizes storage and holding costs |
Established Supply Networks | Reduces component expenses through supplier relationships |
By outsourcing assembly, businesses shift focus toward innovation and market growth while keeping production costs manageable.
Just-In-Time (JIT) Inventory Management for EMS Production
Keeping excessive inventory ties up capital, increases storage costs, and raises the risk of component obsolescence. Just-In-Time (JIT) inventory management ensures materials arrive only when needed, cutting down on waste and unnecessary stockpiling.
JIT Inventory Benefits for EMS Providers-
JIT Strategy | Cost Impact |
Lower Warehouse Expenses | Reduces the need for large storage facilities |
Less Material Waste | Prevents outdated parts from sitting on shelves |
Better Cash Flow | Keeps funds available for other operations |
Flexible Supply Chain | Allows quicker response to demand changes |
With JIT inventory management, EMS manufacturers maintain a lean, efficient operation without unnecessary financial strain.
Choosing the Right Electronics Manufacturing Services (EMS) Partner
Selecting an EMS provider is more than just about production capabilities—it’s about building a long-term collaboration that supports efficiency, quality, and scalability. An effective partnership with an EMS company helps OEMs navigate supply chain challenges, optimize manufacturing costs, and ensure compliance with industry standards.
To make an informed decision, companies need to evaluate technical expertise, production capacity, regulatory compliance, and overall financial impact. Let’s dive into the essential aspects of choosing an EMS partner and how the right selection can streamline product development.
Factors to Consider When Selecting an EMS Provider
Choosing an EMS provider requires a detailed look at production capabilities, supply chain reliability, engineering expertise, and regulatory compliance. Beyond pricing, the ability to meet production demands, ensure consistent quality, and provide technical support can make a significant difference in the long run.
A provider with strong engineering resources can help refine designs, improve manufacturability, and troubleshoot issues before they become costly. Manufacturing capacity should align with both current needs and future scalability. A well-established supply chain network helps prevent delays and secures high-quality components. Certifications such as IPC and ISO indicate adherence to industry standards, ensuring that the final product meets all necessary regulations.
Cost transparency is another major factor. A low upfront cost does not always translate to lower overall expenses. Additional costs can arise from logistics, quality control, or unexpected delays, making it essential to evaluate the total financial impact.
Key Considerations When Evaluating EMS Providers-
Factor | Why It Matters |
Engineering Expertise | A strong team can assist in design improvements and DFM/DFA optimization |
Manufacturing Capacity | The facility should handle your volume needs, whether for prototypes or mass production |
Supply Chain Management | A well-connected provider can reduce lead times and secure reliable components |
Compliance and Certifications | Ensures products meet industry regulations (IPC, ISO, FDA, etc.) |
Cost Structure | A transparent pricing model prevents unexpected expenses |
Flexibility and Scalability | The provider should support future product iterations |
By assessing these areas, businesses increase their chances of forming a productive partnership that supports their long-term manufacturing goals.
How EMS Companies Improve Time-to-Market for OEMs?
In electronics manufacturing, keeping up the pace is a big deal. Production slowdowns can mean missed chances, increased expenses, and reduced profits. EMS providers with streamlined operations and well-organized supply chains help businesses launch products faster while ensuring consistent output.
Rapid prototyping services allow OEMs to refine their designs early in the development process, reducing time spent on revisions. Engineering support speeds up problem-solving, preventing design flaws from causing production delays. A well-integrated supply chain keeps components readily available, reducing downtime caused by material shortages. Automation in assembly ensures faster production cycles with greater precision, leading to shorter lead times.
How EMS Providers Shorten Time-to-Market-
Strategy | Impact on Time-to-Market |
Rapid Prototyping Services | Helps OEMs test and refine designs quickly |
In-House Engineering Support | Speeds up design revisions and problem-solving |
Integrated Supply Chain Management | Reduces delays in component sourcing |
Automated Assembly Processes | Increases production speed and consistency |
By leveraging these strategies, EMS providers help OEMs get their products into the market faster without sacrificing quality.
Understanding the Total Cost of Ownership (TCO) in EMS Outsourcing
When evaluating EMS providers, the quoted price per unit does not always reflect the actual financial impact of outsourcing. The total cost of ownership (TCO) takes into account factors such as logistics, quality assurance, potential rework, and supply chain risks.
Production costs go beyond just assembly—shipping expenses, customs fees, and warehousing costs can add up quickly. If a provider has a high defect rate, expenses related to rework and scrap can outweigh initial cost savings. Delays in sourcing materials or manufacturing setbacks can disrupt product launch schedules, leading to missed revenue opportunities.
Working with an EMS provider that maintains consistent production quality and supply chain reliability helps companies avoid unexpected costs. A careful evaluation of long-term financial impact ensures a stable and cost-effective manufacturing partnership.
Breaking Down TCO in EMS Partnerships-
Cost Factor | Why It Affects the Bottom Line |
Unit Price vs. Total Cost | A low per-unit cost doesn’t always mean lower overall expenses |
Logistics & Shipping | Long-distance suppliers may lead to higher freight and tariff costs |
Rework & Scrap Rate | Defective products increase overall manufacturing costs |
Lead Time & Delays | Late shipments can disrupt entire production schedules |
Service & Support Costs | Lack of engineering assistance can lead to expensive design flaws |
Understanding TCO prevents companies from making short-term decisions that lead to long-term financial strain.
Emerging Technologies in Electronics Manufacturing Services (EMS)
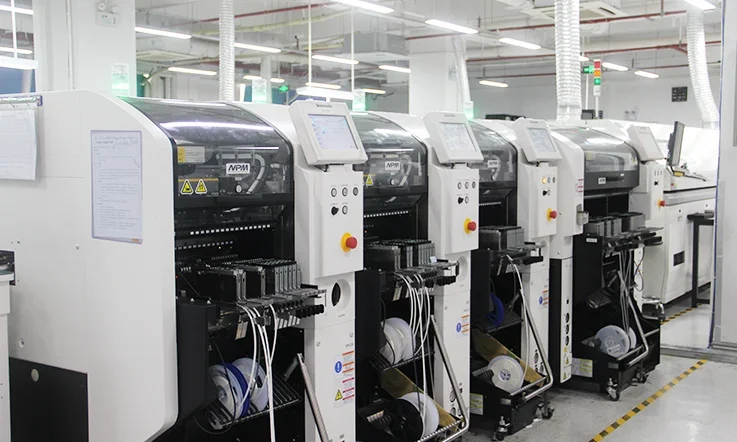
The electronics manufacturing industry is undergoing a transformation driven by new technologies. EMS providers are adopting advanced manufacturing techniques to improve efficiency, enhance product performance, and meet the growing demand for miniaturized, flexible, and high-speed devices.
The following sections will explore some of the most impactful technological trends shaping the future of EMS.
Miniaturization Trends in EMS: Chip-on-Board and Embedded Components
As electronic devices become more compact, the demand for high-density packaging technologies continues to rise. Traditional component packaging is being replaced with more space-efficient solutions to optimize performance and streamline manufacturing processes.
Chip-on-Board (COB) technology eliminates the need for traditional component packaging by mounting bare dies directly onto the PCB. This approach reduces power consumption, improves heat dissipation, and accelerates signal transmission. Industries such as medical electronics, automotive, and aerospace are increasingly using COB to meet strict size and performance requirements.
Embedded components take integration a step further by incorporating passive and active elements within the PCB layers. This design reduces signal interference, enhances mechanical strength, and enables ultra-thin devices. However, embedded components present challenges in manufacturing, repairability, and design complexity.
Comparison of Miniaturization Technologies-
Technology | Features | Applications | Manufacturing Challenges |
Chip-on-Board (COB) | Eliminates packaging, improves thermal performance | Medical, automotive, aerospace | Requires precise manufacturing techniques |
Embedded Components | Integrates components within PCB layers | Ultra-thin devices, wireless communication | Complex fabrication and difficult rework |
As miniaturization advances, many manufacturers are adopting sophisticated inspection techniques such as high-resolution X-ray imaging and automated optical inspection (AOI) to ensure high-density PCB quality.
Flexible and Wearable Electronics: The Future of EMS PCB Design
Flexible electronics are redefining PCB design, enabling lighter, more durable, and adaptable solutions for wearable and foldable devices.
Flexible PCBs (FPCs) use materials like polyimide (PI) and liquid crystal polymer (LCP), allowing circuits to bend without performance loss. These circuits are widely used in foldable smartphones, automotive displays, and smartwatches.
Wearable electronics rely on flexible technology for comfort and long-term usability. Smartbands, medical sensors, and fitness trackers demand high-reliability flexible PCBs that can withstand mechanical stress and environmental conditions. As demand increases, EMS providers are optimizing manufacturing techniques, including advanced adhesives, precision soldering, and high-accuracy component placement.
Comparison of Flexible and Rigid PCBs-
PCB Type | Materials | Applications | Manufacturing Complexity |
Rigid PCB | FR4, ceramic substrates | Traditional electronics | Low |
Flexible PCB | Polyimide, LCP | Wearables, foldable devices | High |
Manufacturing flexible PCBs presents challenges such as substrate handling, connection reliability, and mechanical stress management. To address these issues, factories are deploying precision robotic arms and automated production lines to maintain high-quality standards.
How 5G and AI Are Transforming the EMS Industry?
The integration of 5G and artificial intelligence (AI) is reshaping the EMS landscape, enhancing automation, and optimizing supply chain operations.
5G technology improves data transmission speeds between machines, enabling real-time analytics and remote-controlled production lines. The low-latency, high-bandwidth connectivity supports smart factory operations, reducing downtime and optimizing resource allocation.
Artificial intelligence is being deployed in automated optical inspection (AOI), predictive maintenance, and supply chain management. For example, AI-driven algorithms can analyze manufacturing data to detect defects early, significantly reducing waste and improving yield rates.
Impact of 5G and AI on EMS-
Technology | Benefits | Typical Applications |
5G | High-speed data transfer | Remote equipment monitoring, smart factories |
AI | Quality inspection and forecasting | AOI detection, supply chain optimization |
AI-driven supply chain management helps EMS providers improve inventory forecasting accuracy and mitigate component shortages. By analyzing market trends and historical data, EMS companies can fine-tune procurement strategies, reducing risks associated with stockouts or excess inventory.