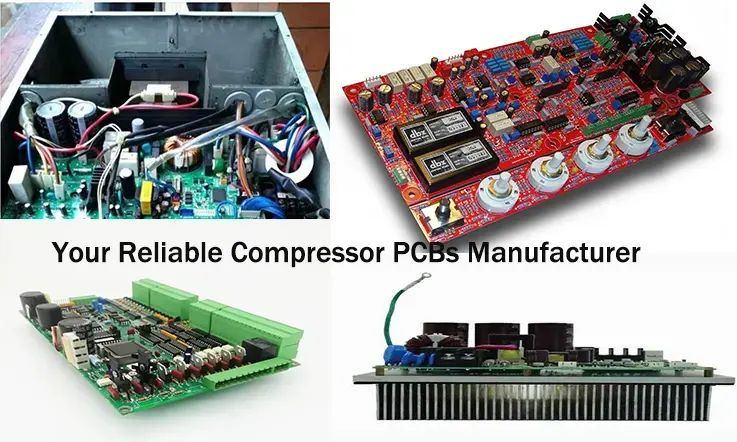
Compressor PCBs (Printed Circuit Boards) play an integral role in the functionality of various compressor systems, from refrigeration units to air conditioning and industrial applications. These specialized PCBs are designed to manage electrical control, ensure precise operation, and maintain the efficiency of compressors in different environments. The process of designing and manufacturing compressor PCBs involves multiple stages, including material selection, advanced manufacturing techniques, and rigorous testing to guarantee the performance and reliability of each unit.
In this guide, we explore the different types of compressor PCBs, the various factors that affect their performance, and the latest techniques in PCB design and manufacturing to help you understand how to choose the right solution for your compressor needs.
The Evolution of Compressor PCBs: From Traditional Circuits to Advanced Smart Solutions
When we think of compressors, we tend to think of large industrial machines humming away quietly in the background. But the heart of these machines, often overlooked, is the Compressor PCB. Over the years, the design and manufacturing of these boards have come a long way, evolving from simple, traditional circuits to highly advanced, smart solutions that incorporate cutting-edge technology like IoT integration and smart sensors.
The Early Days of Compressor PCB Design
In the early stages, compressor PCBs were simple and straightforward. These circuits were primarily used to power the motor, control the compressor’s starting and stopping cycles, and handle basic functions. These early designs were limited by the available materials and technology, and often lacked the ability to handle complex data or integrate with modern systems.
At that time, the PCB design for compressors was fairly basic, often requiring manual assembly and relatively little focus on factors like energy efficiency or signal integrity. Many manufacturers worked with traditional materials, such as FR4, which could only withstand basic operating conditions. While these boards were functional, they lacked the performance needed to support more demanding and energy-efficient compressor systems.
Transitioning to Smart, IoT-Enabled Compressor PCBs
As industries began to demand more energy-efficient, connected, and intelligent systems, the Compressor PCB design evolved to meet these needs. The rise of smart compressors led to the development of IoT-enabled compressor PCBs, which allowed these systems to communicate with cloud platforms and smart devices.
This shift to IoT-enabled designs brought in a new era of Compressor PCBs. These advanced PCBs are now capable of transmitting and receiving data, enabling predictive maintenance, optimizing energy use, and improving overall system performance. For example, sensor integration in Compressor PCBs allows real-time monitoring of the compressor’s health, such as temperature, pressure, and vibration. This data is then transmitted to maintenance teams or integrated with AI-driven systems to predict failures before they occur.
How Smart PCB Designs Are Shaping the Future of Compressor Efficiency?
The growing integration of smart technologies into Compressor PCBs has opened doors for a new wave of efficiency. With the incorporation of energy-efficient designs, AI-powered diagnostics, and predictive analytics, the future of compressor systems looks brighter than ever. Through advanced thermal management techniques, power distribution systems, and signal integrity management, modern compressor PCBs ensure optimal performance, even in the most demanding conditions.
By employing low-power materials and focusing on thermal efficiency, smart compressor PCBs are capable of providing better energy savings and longer lifespan, which is crucial in sectors like HVAC, automotive, and refrigeration. These boards no longer just control the compressor; they are becoming the brains of the operation, enabling compressors to operate more effectively while consuming less energy.
Compressor PCB Types: Tailored Solutions for Diverse Applications

Compressor PCBs serve as the brain of many different types of compressors used across various industries. Each type of Compressor PCB is meticulously designed to meet the specific demands of the compressor it supports, ensuring efficient and reliable operation. Let’s take a closer look at the main types of Compressor PCBs and how they’re tailored to fit unique application needs.
1. Refrigeration Compressor PCBs: Precision Control for Cooling Systems
Refrigeration compressors are the cornerstone of refrigeration and air conditioning systems, responsible for regulating the flow and pressure of refrigerants. Refrigeration Compressor PCBs are designed to offer precise control over parameters like temperature and pressure, which ensures that the compressor runs at optimal efficiency.
Key Design Features-
●Temperature Control: The PCB design for refrigeration compressors often incorporates precise temperature sensors and control algorithms to manage the cooling cycle.
●Pressure Regulation: Specialized components ensure that the PCB can adjust the compressor’s operation to maintain stable pressure levels, preventing overloading or inefficient performance.
●Energy Efficiency: These PCBs are optimized for energy savings, ensuring that the refrigeration systems don’t consume more power than necessary.
Feature | Application | Benefit |
Temperature Control | Manages refrigerant temperature | Prevents overcooling and energy waste |
Pressure Regulation | Adjusts to maintain stable pressure | Ensures smooth compressor operation |
Energy Efficiency | Optimizes compressor’s power consumption | Reduces operating costs and energy usage |
2. Air Compressor PCBs: Optimizing Power and Pressure for Industrial Use
Air compressors are ubiquitous in industries ranging from automotive to construction, and they rely on Compressor PCBs for regulating pressure, flow rate, and temperature. Air Compressor PCBs are designed to be versatile, handling a range of pressures and flow rates while maintaining reliability across various applications.
Core Design Elements-
●Pressure Control: A core function of air compressor PCBs is managing and stabilizing the pressure of compressed air. Advanced sensors integrated into the PCB design for compressors allow for real-time monitoring and adjustment of air pressure, ensuring the system’s overall stability.
●Flow Rate Adjustment: The flow rate of compressed air is another factor, and air compressor PCBs use intelligent circuits to control how much air is delivered to various tools or systems.
●Temperature Management: Air compressor PCBs are designed to closely monitor and regulate temperature levels. By keeping an eye on temperature fluctuations, these PCBs adjust the compressor’s cycle to prevent overheating. This helps ensure the system runs at peak efficiency, avoiding any unnecessary wear and tear on the components.
Feature | Application | Benefit |
Pressure Control | Regulates air pressure | Prevents system failure and ensures stable air supply |
Flow Rate Adjustment | Manages compressed air flow | Guarantees precision in pneumatic tools |
Temperature Monitoring | Ensures the compressor stays within temperature limits | Increases operational life of the compressor |
3. Screw Compressor PCBs: Precision Engineering for Industrial Applications
Screw compressors are widely used in industries such as oil refining, gas processing, and chemical production. These compressors require Compressor PCBs designed for precision control over parameters like speed, pressure, and temperature to ensure smooth operation in demanding environments.
Design Considerations-
●Speed Control: Screw compressor PCBs often integrate variable-speed drives, allowing for dynamic control of the compressor’s speed. This ensures that energy consumption is minimized while still meeting the required output.
●Pressure Management: To manage the highly pressurized environment of a screw compressor, PCBs include sophisticated pressure regulation systems that adjust the compressor’s operation based on load conditions.
●Thermal Control: Heat management is a major consideration for screw compressors. These compressors are equipped with thermal control systems designed to manage heat buildup. By effectively dissipating excess heat, these PCBs help keep the system performing at its best over time. Whether through integrated cooling mechanisms or carefully designed heat dissipation paths, these systems ensure that screw compressors run within the optimal temperature range, maintaining efficiency and extending the system’s lifespan.
Feature | Application | Benefit |
Speed Control | Adjusts compressor speed dynamically | Reduces energy consumption and optimizes performance |
Pressure Regulation | Monitors and adjusts pressure within the system | Ensures consistent output and prevents compressor strain |
Thermal Management | Uses integrated cooling systems | Prevents overheating and extends system life |
4. Rotary Compressor PCBs: Optimized Performance for Versatile Applications
Rotary compressors are found in both residential and industrial applications such as air conditioning and refrigeration. These systems rely on Compressor PCBs to optimize speed, pressure, and temperature for varied operational needs.
Design Features-
●Speed and Pressure Control: Rotary compressor PCBs incorporate speed regulation circuits that enable the compressor to adjust its speed based on the demand, while also controlling air pressure for efficient cooling or heating.
●Compact Design: Because rotary compressors are often used in compact applications, PCB design is engineered to fit within smaller, more constrained spaces without sacrificing performance.
●Reliability: These PCBs are built for durability, incorporating advanced protection features such as overload protection and temperature sensors to ensure consistent operation in high-demand scenarios.
Feature | Application | Benefit |
Speed Control | Modulates compressor speed | Maximizes efficiency under varying load conditions |
Pressure Regulation | Adjusts pressure levels dynamically | Ensures optimal system performance |
Compact PCB Design | Utilizes space-efficient designs | Saves space while maintaining performance |
5. Scroll Compressor PCBs: Compact and Efficient for HVAC Systems
Scroll compressors are commonly used in HVAC systems, refrigeration, and heat pumps, where Compressor PCBs control the system’s performance in terms of speed, pressure, and temperature.
Key Design Considerations-
●Efficiency Focus: Scroll compressors are known for their efficiency, and the PCB design for compressors incorporates features that optimize power consumption while maintaining cooling or heating performance.
●Noise Reduction: Since scroll compressors are often used in noise-sensitive environments, PCBs in these compressors include noise reduction technology to minimize operational sound.
●Precise Control: Scroll compressor PCBs are designed with advanced sensors that offer precise control over the compressor’s operation, ensuring consistent performance in HVAC applications.
Feature | Application | Benefit |
Efficiency Optimization | Maximizes energy usage and cooling efficiency | Reduces energy consumption and costs |
Noise Reduction | Minimizes operational noise | Ideal for residential and office use |
Precision Control | Monitors and adjusts compressor operation | Ensures consistent and reliable operation |
Scroll compressor PCB designs are often more compact than their counterparts, and the PCB design for HVAC systems continues to evolve to meet the growing demand for quieter, more energy-efficient systems.
What Are Materials Use for Compressor PCBs Manufacturing?
In compressor systems, the materials and manufacturing techniques used in Compressor PCBs can make a big difference in the board’s performance, durability, and efficiency. By adopting high-performance PCB materials and advanced manufacturing methods, we can create compressor systems that perform under challenging conditions, like extreme temperatures and heavy-duty operation.
Choosing the right materials not only ensures the reliability of the compressor systems but also helps meet thermal management needs and enhances long-term operational efficiency. Let’s explore some of the advanced materials and manufacturing techniques for Compressor PCBs in more detail.
High-Temperature Materials for Compressor PCBs
Compressor systems often operate in high-heat environments, which makes selecting the right high-temperature materials a fundamental part of the design process. To meet the demands of thermal management, high-performance PCB materials are necessary to ensure that the system remains functional despite the heat buildup.
The selection of materials for Compressor PCBs involves considerations of both heat resistance and conductivity. For example, materials like polyimide and ceramic-based composites are used to handle temperatures in excess of 250°C, ensuring that the system doesn’t overheat and lead to system failure. Thermal vias and heat-sink structures are often incorporated into the design to facilitate heat dissipation.
Material Type | Maximum Operating Temperature | Thermal Conductivity (W/mK) | Common Applications |
Polyimide | Up to 250°C | 0.35 | HVAC, industrial systems |
Ceramic-based Composites | Up to 300°C | 1.0 | Refrigeration, automotive |
FR4 with Thermal Vias | Up to 150°C | 0.45 | General compressor systems |
These materials ensure that Compressor PCBs maintain stable performance, even under high thermal loads.
Flexible and Rigid PCB Solutions for Compressors
In the design of compressor PCBs, flexibility and durability are necessary to ensure the system operates efficiently. Depending on the specific application, both flexible and rigid PCBs are used to meet the different needs of each project.
Flexible PCBs are used in applications where compactness and adaptability are needed. These PCBs are suitable for systems where space is limited or where the PCB needs to conform to curves and irregular surfaces. On the other hand, rigid PCBs provide structural strength and are typically used in stationary systems where high durability is required.
Multilayer PCB manufacturing allows for integrating both rigid and flexible elements in one design, providing additional flexibility in Compressor PCB layouts without sacrificing performance.
PCB Type | Flexibility | Application Area | Typical Thickness |
Flexible PCBs | High | Automotive, mobile refrigeration | 0.15 – 0.3 mm |
Rigid PCBs | Low | HVAC, industrial compressors | 1.0 – 2.0 mm |
Multilayer PCBs | Moderate | Hybrid systems, precision cooling | 0.5 – 1.5 mm |
The combination of rigid and flexible designs enhances the ability to create more compact and efficient systems, contributing to overall design versatility.
Using Sustainable Materials in Compressor PCBs
With growing concerns about environmental impact, there has been a shift toward using eco-friendly PCB materials in Compressor PCBs. This includes materials that are RoHS-compliant and lead-free, offering environmentally responsible alternatives to traditional materials.
The use of green PCB manufacturing methods is increasingly common, where materials like biodegradable substrates and non-toxic soldering materials are prioritized. This not only aligns with regulatory standards but also supports the growing demand for eco-friendly products in the market.
Material Type | RoHS Compliant | Lead-Free | Environmental Impact |
FR4 with Halogen-Free Resin | Yes | Yes | Reduced toxic emissions |
Bio-based PCBs | Yes | Yes | Compostable substrates |
Lead-Free Solder | Yes | Yes | Reduces heavy metal waste |
These sustainable materials are often selected for their ability to meet both environmental standards and performance requirements, offering an effective solution for manufacturers focused on reducing their carbon footprint.
Custom Compressor PCBs: Design, Manufacturing, and Assembly Solutions
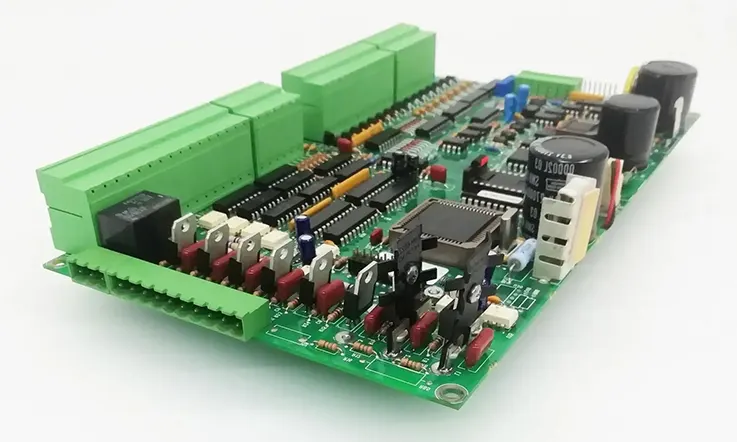
When designing compressor systems, Custom Compressor PCBs must meet the specific demands of various applications like HVAC, refrigeration, and automotive cooling. These tailored solutions are meant to provide the necessary functionality and efficiency, supporting compressor performance in various environments. As compressor systems evolve, the design and manufacturing of high-performance PCBs must be adaptive and precise.
The Benefits of Custom PCB Design for Compressors
Custom PCB design for compressors involves creating tailored solutions that cater to the unique requirements of compressor systems. Unlike generic PCBs, custom designs allow us to choose components, optimize layouts, and ensure that the board meets the electrical and thermal needs specific to compressors.
For instance, HVAC compressors require PCBs that are built to handle wide temperature fluctuations, while refrigeration compressors need boards that perform under extreme cold. Custom designs ensure optimal performance and longer service life in demanding environments.
Tailored PCB solutions enable compressors to function more efficiently. By incorporating sensors or specialized components, custom boards help compressors adapt to varying operational conditions, minimizing the risk of breakdowns and extending operational life.
Advanced PCB Manufacturing Techniques for Compressor Systems
The process of manufacturing Compressor PCBs requires a thorough understanding of the latest technologies and methods. The goal is to deliver boards that not only meet the performance requirements but also support compact, robust designs suitable for challenging environments.
PCB manufacturing techniques have advanced considerably, with the introduction of flexible PCBs for compressors and multilayer PCB designs as prominent examples of these innovations.
●Flexible PCBs for compressors are useful in applications where space limitations and durability are specials. These boards allow for bending and flexibility, making them suitable for compressors used in mobile or space-constrained environments, such as automotive or portable refrigeration systems. The flexibility of these designs improves system integration by reducing the need for additional components and optimizing space.
●Multilayer PCB design provides the capability to integrate multiple circuits in a single, compact board. This design choice is commonly used in more complex compressor systems, which require efficient space utilization and optimal signal integrity. By stacking multiple layers of circuits, we can integrate additional features such as sensors, temperature control, or communication circuits without taking up more space.
Example of Multilayer PCB Design in Compressor Applications-
In industrial refrigeration systems, multilayer PCB design is often used to handle various tasks such as regulating compressor speed, maintaining pressure, and monitoring performance through sensors. These multilayer designs help keep the overall compressor system compact and reduce the complexity of wiring and connections.
Multilayer PCBs also improve thermal performance by integrating heat dissipation layers that prevent overheating, which is especially useful in applications where compressors run at full capacity for extended periods.
Assembly Process for Custom Compressor PCBs
The assembly process for compressor PCBs ensures the board operates efficiently and meets performance standards. The assembly process involves precise techniques to place components and connect them securely.
PCB assembly services ensure the production of reliable, high-performance compressor PCBs. As compressor systems evolve, more precise assembly methods are needed. Using surface-mount technology (SMT), manufacturers can place components directly onto the surface of the PCB, enabling a compact and efficient design.
●SMT for compressor PCBs allows for more components to be placed on the same-sized board, which is especially helpful when designing compact systems. This method also reduces the risk of errors during the assembly process, ensuring that all components function as intended within the compressor system.
●Automated assembly systems ramp up both speed and accuracy in compressor PCB production. These systems employ robotics and advanced vision technology to precisely place and solder components, ensuring a consistent and high-quality build across every unit. The result? A faster, more reliable process that keeps everything in check.
How Enhancing the Performance of Compressor PCBs?
When developing Compressor PCBs, performance enhancement involves refining the some factors that influence their efficiency, durability, and overall functionality. Whether you’re optimizing signal integrity, refining power distribution, or improving thermal performance, every aspect of the PCB design can impact the system’s reliability. Let’s explore how to elevate the functionality of Compressor PCBs through targeted design and manufacturing approaches.
Optimizing Signal Integrity in Compressor PCBs
Maintaining signal integrity in Compressor PCBs is necessary to ensure stable and accurate operation. Proper PCB design helps reduce interference and ensures signals travel clearly without distortion or delay. In compressors, where precision is a priority, addressing challenges like signal degradation, noise, and impedance mismatches is necessary for smooth operation.
One way to improve signal integrity in Compressor PCBs is by incorporating high-speed PCB design for compressors. For designs requiring high-frequency signal transmission, special attention must be paid to trace impedance, signal routing, and appropriate material selection. By utilizing controlled impedance traces and solid ground planes, signal reflection and electromagnetic interference (EMI) can be reduced.
Additionally, minimizing noise in PCB circuits is must to preserving signal clarity. . This can be done by placing decoupling capacitors near sensitive components, isolating noisy circuits, and using shielding techniques. Moreover, low-inductance vias and via holes can reduce noise levels even further.
Here’s how signal integrity is managed:
Design Technique | Purpose | Benefit |
Controlled Impedance Traces | Ensures consistent signal propagation | Reduces reflection and distortion |
Ground Planes | Provides a stable reference for signals | Minimizes noise and EMI |
Shielding and Isolation | Prevents interference from external signals | Enhances signal clarity |
Power Distribution in Compressor PCBs
Effective power distribution in Compressor PCBs ensures that each component gets the required current and voltage without fluctuations that could impact performance. Proper PCB power management prevents problems like voltage drops and inefficiencies, keeping everything running smoothly. Proper routing and thoughtful component placement can make a world of difference in ensuring that power flows exactly where it’s needed.
For Compressor PCB design for power efficiency, integrating power planes and decoupling capacitors in the PCB layout is essential. Power planes help evenly distribute power across the board, reducing resistance and improving power delivery. At the same time, decoupling capacitors smooth out transient voltage changes and ensure a steady power supply.
Optimizing PCB power distribution also involves controlling power routing to minimize resistance, ultimately improving power efficiency. This ensures that the compressor operates at a stable level without excess power consumption or overheating.
Power Management Solution | Purpose | Outcome |
Power Planes | Distribute power evenly across the board | Reliable power delivery |
Decoupling Capacitors | Smooth out transient voltage changes | Efficient operation |
Low-Resistance Traces | Minimize power loss and voltage drop | Reduced energy usage |
Thermal Management in High-Performance Compressor PCBs
Thermal management is a primary concern in high-performance Compressor PCBs. Compressors tend to operate in environments where heat is a natural byproduct. Without managing this heat properly, it can lead to damage or premature failure of components. To prevent such issues, PCB thermal management solutions must be integrated to ensure that heat dissipates effectively, even under heavy loads.
Heat dissipation in compressor PCBs is managed through several strategies, such as thermal vias, heat sinks, and careful material selection. High-performance thermal PCB designs utilize materials with excellent thermal conductivity to ensure that heat is transferred away from sensitive components. Thermal vias help move heat from the top layer of the PCB to the bottom, where it can be dispersed. Heat sinks are commonly added to high-heat areas, further improving thermal management.
In addition to passive thermal management techniques, active methods like fans or thermoelectric devices may also be used in more demanding designs for improved cooling.
Thermal Management Solution | Purpose | Effect |
Thermal Vias | Conduct heat through layers of the PCB | Efficient heat dissipation |
Heat Sinks | Absorb and disperse heat from components | Prevents overheating |
High-Performance Materials | Use materials with superior thermal conductivity | Enhanced heat transfer |
By considering thermal management for Compressor PCBs in the design stage, we can prevent overheating, ensuring that systems remain stable and perform well under high temperatures.
What Are The Common Causes of Compressor PCB Failure?

Compressor PCBs play a central role in the operation of compressors, providing essential functionality in controlling pressure, speed, temperature, and other parameters. However, these PCBs can fail due to various factors, and such failures can result in serious issues, including downtime, increased maintenance costs, and reduced system performance. Below are some of the most common causes of Compressor PCB failure, as well as tips to avoid these pitfalls.
1. Overvoltage or Undervoltage: Power Struggles
Fluctuations in power supply are one of the top reasons for Compressor PCB failures. When the input voltage exceeds the rated limits (overvoltage) or falls below the required level (undervoltage), the electrical components on the PCB can suffer significant damage.
●Overvoltage: When the voltage spikes, it can cause components such as capacitors and transistors to burn out, potentially leading to catastrophic failure of the entire PCB.
●Undervoltage: On the flip side, when the voltage is too low, the PCB may not function correctly, causing premature component failure or erratic operation.
Preventive Measures:
●Use surge protection devices to shield the PCB from sudden power spikes.
●Implement voltage regulation systems that keep the power supply consistent within the safe operating range.
Issue | Effect | Preventive Measure |
Overvoltage | Component burnout | Surge protection, voltage regulators |
Undervoltage | Premature failure | Consistent power supply, voltage regulation |
2. Overheating: The Silent Killer
Excessive heat is another common enemy of Compressor PCBs. When electronic components run too hot, they can degrade quickly, leading to premature failure. Overheating can result from several issues:
●Malfunctioning Cooling Systems: If the cooling system that is supposed to dissipate heat is not working properly, the temperature of the compressor will rise and potentially damage the PCB.
●Poor Ventilation: Inadequate airflow in the housing or enclosure can trap heat, leading to thermal stress on sensitive components.
●High Ambient Temperatures: Compressors operating in hot environments are more susceptible to overheating.
Preventive Measures:
●Ensure the cooling system is regularly maintained and fully functional.
●Use high-performance thermal materials to aid in heat dissipation and maintain optimal operating temperatures.
●Design the PCB layout with sufficient space around heat-sensitive components to improve airflow and cooling.
Issue | Effect | Preventive Measure |
Malfunctioning Cooling System | Overheating, component failure | Regular maintenance, system checks |
Poor Ventilation | Heat buildup, thermal stress | Improve airflow, optimize design |
High Ambient Temperatures | Accelerated wear and tear | Use heat-resistant materials |
3. Moisture or Corrosion: The Invisible Threat
Moisture and corrosion are threats to Compressor PCBs. When moisture enters the system, either through condensation or leaks, it can damage the circuitry and cause the PCB to fail. Corrosion, particularly in industrial environments with high humidity or exposure to chemicals, can eat away at the PCB’s solder joints and electrical contacts, eventually leading to failure.
●Moisture Ingress: Can lead to short circuits or reduce the insulation resistance of components, making them prone to electrical failure.
●Corrosion: Often caused by exposure to salty air, chemicals, or harsh environments, corrosion can weaken the connections between components, leading to unreliable or failed operation.
Preventive Measures:
●Use sealed enclosures and waterproof coatings on the PCB to protect against moisture ingress.
●Implement corrosion-resistant materials such as gold-plated or tin-lead finishes on the PCB to prevent corrosion.
Issue | Effect | Preventive Measure |
Moisture Ingress | Short circuits, component failure | Sealed enclosures, waterproof coatings |
Corrosion | Weakened connections, failure | Use corrosion-resistant materials |
4. Physical Damage: Bumps, Bruises, and Breaks
Physical damage to Compressor PCBs can occur during shipping, installation, or even during operation. Vibration and impacts from rough handling or operation can cause fractures or loose connections on the PCB, making it unreliable or non-functional.
●Impact Damage: A heavy impact can physically crack the PCB or break the connections between components.
●Vibration: Constant vibration can weaken solder joints, causing intermittent failure or complete disconnection of components.
Preventive Measures:
●Use shockproof enclosures during shipping and installation.
●Implement vibration dampening materials or designs to reduce physical stress on the PCB during operation.
Issue | Effect | Preventive Measure |
Impact Damage | Physical cracks, disconnected components | Shockproof enclosures, careful handling |
Vibration | Loose solder joints, intermittent failures | Vibration-damping designs |
5. Component Wear: The Inevitable Fade
Over time, electronic components on Compressor PCBs naturally wear out due to continuous use. Components such as capacitors, resistors, and transistors can degrade with prolonged exposure to heat, voltage fluctuations, and mechanical stress.
●Accelerated Wear: Factors such as poor maintenance, high operating temperatures, or excessive load can accelerate the aging process of components.
●Normal Wear: Eventually, even with the best care, components will wear out and need to be replaced.
Preventive Measures:
●Implement regular maintenance schedules to check and replace worn-out components before failure occurs.
●Design the PCB to handle overload conditions and operate at optimal temperatures to extend component lifespan.
Issue | Effect | Preventive Measure |
Accelerated Wear | Shortened component life | Regular maintenance, optimal operation conditions |
Normal Wear | Decreased efficiency, failure | Component replacement, proactive checks |
6. Power Surges: Unexpected Shocks
Power surges, often caused by lightning strikes, electrical faults, or sudden changes in power supply, can overload the Compressor PCB’s components, leading to failure. A sudden spike in voltage can cause transistors and capacitors to burn out almost instantly.
Preventive Measures:
●Install surge protectors or voltage stabilizers to shield against sudden electrical spikes.
●Use voltage-clamping devices to absorb power surges before they reach sensitive components.
Issue | Effect | Preventive Measure |
Power Surges | Component failure, burnout | Surge protectors, voltage stabilizers |
How Testing and Validation of Compressor PCBs?
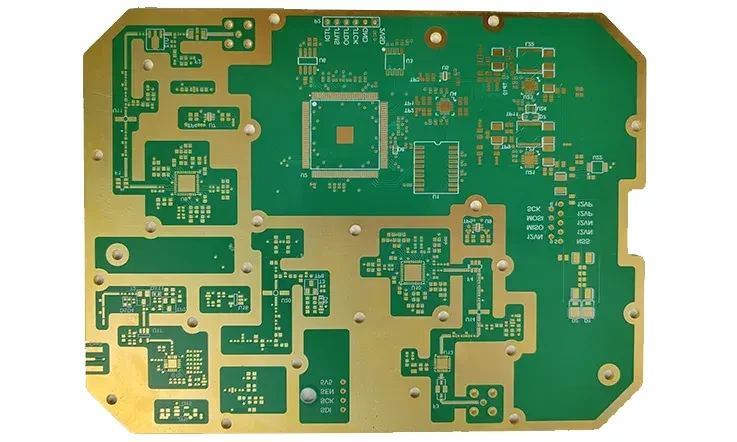
Testing and validation are necessary to ensure that Compressor PCBs perform reliably in their respective applications. This section explores how we go through PCB performance testing, ensure quality assurance in manufacturing, and improve designs through iterative testing.
PCB Performance Testing for Compressors
Testing is a must when it comes to verifying the performance and reliability of Compressor PCBs. This process involves several stages to assess their electrical capabilities, heat resistance, and how they hold up under mechanical stress. By running these tests, we can pinpoint any potential issues before they become a problem, ensuring the board can handle real-world conditions without breaking a sweat.
●Electrical Testing: Ensuring that the Compressor PCBs can handle the electrical load without failure involves testing for continuity, voltage drop, and current carrying capacity. Electrical testing checks that no components are improperly connected or at risk of short circuits.
●Thermal Cycling Tests: Compressors can experience a broad temperature range during operation. Thermal cycling tests simulate rapid temperature fluctuations to assess the Compressor PCB’s durability under changing conditions. This ensures the PCB can withstand thermal stresses without degradation in performance.
Test Type | Purpose | Expected Outcome |
Electrical Testing | Verify continuity and current-carrying capacity | Ensures uninterrupted functionality |
Thermal Cycling Test | Simulate temperature changes | Confirms PCB’s durability in fluctuating temperatures |
Vibration Test | Simulate mechanical stress | Verifies PCB reliability during operation |
These tests help ensure that Compressor PCBs remain functional throughout their lifecycle.
Quality Assurance in PCB Manufacturing for Compressors
The manufacturing process for Compressor PCBs involves strict protocols to verify that the final product aligns with industry standards. These standards guide the PCB design, material choices, and final inspection.
●PCB Manufacturing Standards: Following specific manufacturing standards ensures that Compressor PCBs meet all required specifications, like material quality and proper component placement. Sticking to these standards helps keep production on point and guarantees that the board performs consistently. By adhering to established guidelines, we can avoid mishaps, reduce errors, and maintain high-quality output that delivers on all fronts.
●Compliance Testing: After production, compliance testing ensures that Compressor PCBs adhere to safety and environmental regulations. For example, RoHS compliance guarantees the exclusion of harmful substances, while UL certifications confirm that the product meets safety standards.
Compliance Requirement | Purpose | Benefit |
UL Certification | Ensures PCB safety and performance | Meets recognized safety standards |
RoHS Compliance | Restricts hazardous substances | Supports eco-friendly PCB manufacturing |
IPC Standards | Defines the required PCB quality and specifications | Guarantees consistent quality and durability |
Iterative Testing and Design Improvements for Compressor PCBs
Iterative testing helps refine the Compressor PCB design and ensure its long-term functionality. The continuous cycles of design and testing provide valuable feedback, allowing for necessary adjustments.
●Iterative Testing: After each round of testing, the design is assessed, and changes are made based on the test results. This cycle continues, improving the design incrementally and ensuring that any issues are caught and resolved early.
●Design Optimization: With feedback from testing, PCB designs are optimized for better performance, reducing redundancies and improving component placement, layout, and electrical pathways.
●Feedback-Driven Design Process: The design process is dynamic, with ongoing feedback influencing design adjustments. This allows for the product to adapt and improve based on real-world testing and performance data.
Design Stage | Focus Area | Key Improvement |
Prototype Testing | Initial PCB functionality and durability | Identifying flaws and weaknesses |
Iterative Design Changes | Component optimization and layout adjustments | Improved efficiency and reliability |
Final Testing and Validation | Full functional testing and validation | Assurance of performance in actual conditions |
This continuous improvement cycle helps deliver Compressor PCBs that are fine-tuned to perform as required in compressor systems.
Cost-Effective Manufacturing Solutions for Compressor PCBs
Manufacturing Compressor PCBs comes with a need to balance performance, reliability, and cost. Many PCB manufacturers are constantly looking for ways to optimize production processes, reduce material waste, and ensure that their Compressor PCBs meet quality standards without going over budget. This section explores various strategies for achieving cost-effective PCB manufacturing, optimizing design choices, and finding efficient solutions for prototyping.
Optimizing Manufacturing Costs for Compressor PCBs
Cost optimization in Compressor PCB manufacturing requires a deep understanding of both material selection and manufacturing techniques. By refining these aspects, we can significantly lower production costs while still ensuring that the Compressor PCBs meet all functional and performance requirements.
●PCB Manufacturing Cost Reduction: One effective way to reduce PCB manufacturing costs is by choosing materials that provide a balance between performance and price. For instance, selecting standard-grade materials for certain non-critical components can reduce overall material costs. Additionally, employing more automated processes, such as automated PCB assembly (SMT), helps streamline production and reduce labor costs.
●Efficient PCB Assembly: Optimizing the PCB assembly process helps save both time and money. This includes using assembly methods like surface-mount technology (SMT), which speeds up the process and boosts accuracy compared to older through-hole techniques. Careful selection and placement of components also help avoid excess material use, keeping things efficient and cost-effective.
Strategy | Impact | Outcome |
Material Selection | Choose cost-effective materials | Reduces overall material cost |
Automated Assembly (SMT) | Use automated processes for assembly | Reduces labor cost and improves accuracy |
Component Selection & Placement | Optimize component layout | Minimizes unnecessary components and cuts down on material waste |
These approaches, when combined, can drastically reduce PCB manufacturing costs while still ensuring that the Compressor PCBs perform reliably.
Balancing Performance and Cost in PCB Design
Achieving a balance between high-performance Compressor PCBs and cost-effective solutions is a common challenge for our PCB designers. The trick lies in making design choices that maximize performance while minimizing cost without compromising reliability.
●Affordable PCB Design: Designers must carefully choose between different types of components, considering both their cost and functionality. Affordable PCB designs often leverage standard components for most parts of the circuit, while only using specialized parts where necessary. This ensures the design stays within budget without sacrificing essential features.
●Performance-Cost Balance in PCB: Achieving a performance-cost balance means considering trade-offs such as component selection, board layout, and material choices. For instance, a simpler PCB design with fewer layers may suffice for less demanding applications, saving costs while still providing reliable operation.
Design Factor | Focus Area | Optimization Strategy |
Component Selection | Use standard components for non-critical functions | Lowers overall design cost |
Layer Count | Reduce the number of layers where possible | Decreases manufacturing complexity and cost |
Specialized Components | Only use where absolutely needed | Ensures budget is spent on necessary features |
The goal is to design Compressor PCBs that provide the necessary functionality at the lowest cost, ensuring they are suitable for a wide range of applications.
Economical Prototyping for Compressor PCBs
Prototyping is a first stage in developing Compressor PCBs, and it doesn’t have to be expensive. With rapid prototyping techniques, you can speed up design iterations and testing, all while keeping costs lower than traditional methods. These faster and more affordable approaches allow for fine-tuning the design without draining your budget.
●Compressor PCB Prototyping: Traditional prototyping methods can be expensive and time-consuming. With the introduction of rapid prototyping technologies, we can now produce PCB prototypes more quickly and at a lower cost. This allows us to test different design iterations before committing to large-scale production.
●Cost-Effective PCB Prototypes: When designing prototypes, selecting the right prototyping method makes all the difference. For example, low-volume PCB manufacturing offers an affordable approach for early design iterations, allowing for smaller production runs at a fraction of the cost of large-scale production. This method provides an effective way to test and refine designs without the financial strain of mass production.
●Affordable PCB Design: Prototyping also presents an opportunity to test different design choices and material options, allowing designers to identify the most cost-effective approach before moving on to mass production.
Prototyping Method | Benefit | Cost Reduction Strategy |
Rapid Prototyping | Quick turnaround and lower costs | Reduces time-to-market and prototyping costs |
Low-Volume PCB Manufacturing | Small-scale production runs | Cuts down on initial production expenses |
Material Selection for Prototypes | Choose cost-effective materials for testing | Reduces overall prototyping costs |
By employing these economical prototyping strategies, we can optimize our design iterations without incurring unnecessary costs.
Why Choose JarnisTech to Be Your Compressor PCB Fabricator?
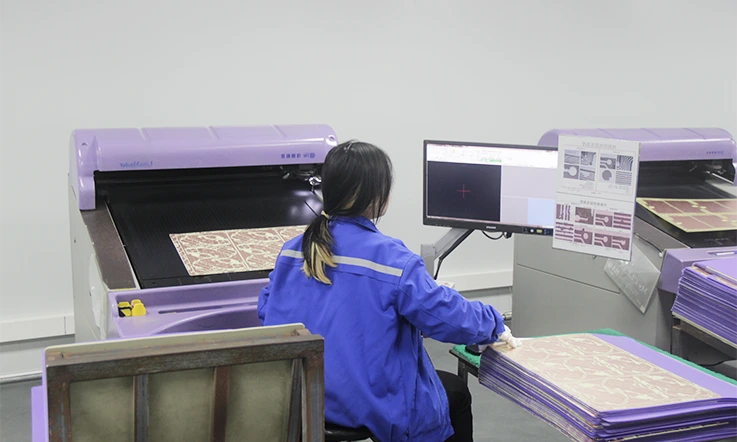
When it comes to finding a trusted manufacturer for your compressor PCBs, JarnisTech is the partner that stands out. With years of experience and a reputation for excellence, we specialize in producing high-performance compressor PCBs tailored to meet the needs of various industries. Based in China, we combine advanced manufacturing technologies with top-tier materials, providing you with a broad range of solutions for different compressor applications.
At JarnisTech, we don’t just create PCBs; we create solutions. Whether you need a high-performance PCB for industrial compressors or a cost-effective prototype for an air conditioning system, we have the technical expertise and resources to support you from the very first sketch to the final product.
Full-Service PCB Manufacturing for Compressors
When it comes to compressor PCB manufacturing, you want a partner that offers end-to-end solutions, and that’s exactly what we deliver. At JarnisTech, we handle everything from component sourcing and PCB layout design to assembly and final production, ensuring each step is performed with precision and quality. Here’s how we break it down:
●Component Sourcing: We work with a network of trusted suppliers to source high-quality components that ensure the long-term reliability and performance of your compressor PCBs. Whether it’s resistors, capacitors, or custom components, we have the expertise to procure exactly what you need.
●Design & Prototyping: Our design team works with you to understand your specific needs and create PCB layouts that align with your goals. If you’re looking for cost-effective PCB designs or high-performance layouts for your compressors, we’ve got you covered. Our prototyping process allows for fast turnarounds and the flexibility to make adjustments based on your feedback.
●Assembly & Fabrication: Our state-of-the-art assembly lines use the latest technology to assemble compressor PCBs efficiently and accurately. Whether you need multilayer PCBs or flexible PCB solutions, we have the capability to meet your manufacturing demands. With precision placement and SMT (Surface Mount Technology), we ensure your PCB performs reliably under demanding conditions.
●Production & Quality Control: Our quality control process includes thorough testing to ensure each PCB meets industry standards and complies with UL and RoHS certifications. We focus on getting your product right the first time, eliminating potential issues before they arise.
Why JarnisTech Stands Out?
When you choose JarnisTech as your compressor PCB fabricator, you’re not just getting a supplier; we will takes the time to understand your specific needs and provides tailored solutions. Here’s why:
●Experience and Expertise: With years of experience in the industry, we know the ins and outs of compressor PCB design and manufacturing. We’re not just about delivering parts—we’re about providing solutions that work.
●Customer-Centric Approach: We understand that every project is unique. Whether you’re building compressors for refrigeration, air conditioning, or industrial machinery, we work with you every step of the way to ensure your design meets your technical and budgetary requirements.
●Efficiency and Speed: Our advanced production methods and quick turnaround times make sure you don’t have to wait long to get your PCB designs into production. We understand time is money, and we strive to deliver on time without compromising quality.
●Global Reach: While we are based in China, we serve clients around the globe, providing efficient shipping and support for businesses everywhere.
Contact JarnisTech Today
Ready to take the next step in your compressor PCB design journey? Send us your inquiries, and let’s start a conversation. At JarnisTech, we’re committed to providing top-notch products and customer service that not only meets your expectations but exceeds them.
Get in touch now—let’s bring your compressor PCB designs to life and power up your business!
FAQs for Compressor PCBs
1.How do I choose the right PCB material for a compressor?
Material choice depends on factors like temperature, electrical needs, and durability. Common materials include FR4 and polyimide.
2.Can a Compressor PCB be repaired?
Minor repairs are possible, but severe damage often requires replacement.
3.Why is thermal management important in Compressor PCBs?
It prevents overheating and ensures components stay within their safe operating range.
4.How is signal integrity maintained in Compressor PCBs?
By using proper PCB layout, controlling impedance, and shielding against noise.
5.Can Compressor PCBs be customized for specific models?Yes, they can be tailored to meet the unique needs of different compressor models.