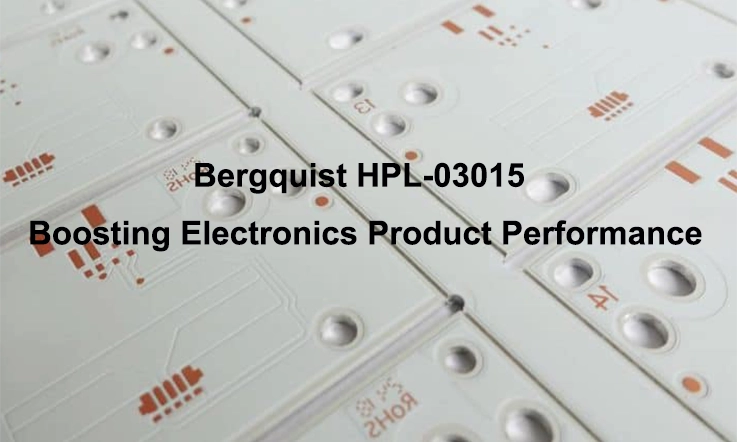
In the fast-paced world of electronics manufacturing, choosing the right materials for PCB (Printed Circuit Board) production is vital for achieving optimal performance and efficiency. Bergquist HPL-03015 PCB material is a cutting-edge solution that offers numerous advantages to electronic product manufacturers. This article explores the exceptional features and benefits of Bergquist HPL-03015, highlighting its significance in improving manufacturing processes and producing high-quality electronic devices.
Overview of Bergquist HPL PCB Materials
Bergquist is proud to introduce a new dielectric material, HPL, to its extensive line of Thermal Clad metal core PCBs (MCPCBs). HPL has been specifically developed to meet the rigorous thermal performance requirements of high-power lighting LED applications. With a thickness of just 0.0015″ (38µm), this thin dielectric demonstrates exceptional heat resistance, boasting a glass transition temperature of 185°C and an impressive thermal performance rating of 0.30°C/W.
Benefits of Using Bergquist HPL-03015
Utilizing Bergquist’s HPL-03015 offers a range of significant advantages for thermal management in various applications. The key benefits of this advanced dielectric material are as follows:
1. Exceptionally low thermal resistance: With a thermal resistance of only 0.02°Cin2/W (0.13°Ccm2/W), HPL-03015 enables efficient dissipation of heat, minimizing the risk of overheating and ensuring optimal performance.
2. High thermal conductivity: Boasting a thermal conductivity of 7.5 W/m-K, HPL-03015 facilitates effective heat transfer, allowing for efficient thermal management and maintaining stable operating temperatures.
3. Suitable for high temperature applications: HPL-03015 is specifically designed to withstand high temperatures, making it an ideal choice for demanding environments where heat resistance is crucial.
4. Compatibility with lead-free solder: This dielectric material is fully compatible with lead-free soldering processes, ensuring compatibility with industry standards and providing flexibility in manufacturing.
5. Eutectic AuSn compatibility: HPL-03015 is also compatible with eutectic AuSn, offering additional options for soldering and assembly methods, thereby accommodating diverse production requirements.
6. RoHS compliant and environmentally friendly: HPL-03015 is compliant with the Restriction of Hazardous Substances (RoHS) directive, demonstrating its commitment to environmental sustainability and meeting regulatory standards.
7. Compatibility with aluminum and copper substrates: HPL-03015 is available for use with both aluminum and copper metal substrates, providing versatility and allowing for seamless integration into various designs and applications.
By leveraging the benefits of Bergquist’s HPL-03015, manufacturers can achieve efficient thermal management, ensure reliable performance in high-temperature conditions, comply with environmental regulations, and enhance the overall longevity and effectiveness of their products.
Disadvantages of Bergquist HPL-03015
While Bergquist HPL-03015 offers several advantages for PCB manufacturing and design, it’s important to consider some potential disadvantages:
1. Cost: Bergquist HPL-03015 is a high-performance thermal interface material, and its advanced properties come at a higher cost compared to other conventional materials. The higher cost may impact the overall budget of the PCB manufacturing process.
2. Thickness limitations: HPL-03015 may have limitations in terms of available thickness options. If your application requires a specific thickness that is not within the range provided by HPL-03015, it may limit your design flexibility and thermal management options.
3. Electrical conductivity: HPL-03015 is primarily designed for thermal conductivity and heat dissipation rather than electrical conductivity. If your application requires a material with high electrical conductivity, HPL-03015 may not be the ideal choice.
4. Application-specific limitations: Depending on the specific requirements of your application, HPL-03015 may have limitations. For example, if your application involves exposure to harsh chemicals or extreme temperatures beyond the material’s specified range, it may not perform optimally or may degrade over time.
5. Complexity of application: HPL-03015 may require specific handling and application techniques to ensure proper installation and performance. If not applied correctly, it may lead to issues such as air gaps, reduced thermal conductivity, or inadequate heat dissipation.
It’s important to carefully evaluate these potential disadvantages in the context of your specific PCB manufacturing and design requirements. Consider alternative materials and compare their advantages and disadvantages to make an informed decision that aligns with your application’s needs and constraints.
Applications of Bergquist HPL-03015
The exceptional characteristics of Bergquist’s HPL-03015 make it well-suited for a range of applications that demand high watt-density and low thermal resistance. The key applications where HPL-03015 excels are as follows:
1.High watt-density applications:
HPL-03015 is particularly beneficial in applications where achieving low thermal resistance is crucial. Its remarkable thermal properties enable efficient heat dissipation, making it an excellent choice for high watt-density applications that require effective thermal management.
2.Backlighting:
The HPL-03015 dielectric material is highly suitable for backlighting applications. Its low thermal resistance and high thermal conductivity contribute to maintaining optimal operating temperatures, ensuring consistent and reliable performance in backlighting systems.
3.Headlamps:
HPL-03015’s ability to withstand high temperatures and its compatibility with various soldering methods make it an ideal choice for headlamp applications. It helps dissipate heat effectively, ensuring the longevity and reliability of headlamp systems.
4.LED applications:
HPL-03015 is specifically designed to meet the thermal management needs of LED applications. Its low thermal resistance and high thermal conductivity enable efficient heat dissipation, thereby enhancing the performance, reliability, and lifespan of LED devices.
Bergquist HPL-03015 Vs Standard PWBs
Bergquist’s Thermal Clad Metal Core PCBs excel in minimizing thermal impedance and effectively conducting heat compared to standard printed wiring boards (PWBs). The superior thermal conductivity of the Thermal Clad dielectrics surpasses that of other PCB materials, providing a cost-effective solution that eliminates the need for additional LEDs, simplifies designs, and streamlines the production process.
By utilizing Thermal Clad, operators can expect lower operating temperatures, significantly extending the lifetime of LEDs and ensuring enhanced durability for high-power lighting applications. This advancement in dielectric technology not only meets the demanding requirements of high-power LED lighting but also offers a reliable and efficient solution for various thermal management challenges in the electronics industry.
How Using Bergquist HPL-03015 for PCB Manufacturing?
To use Bergquist HPL-03015 in manufacturing PCB boards, follow these general steps:
1.Design Considerations:
Ensure that your PCB design includes appropriate areas for thermal management, such as heat sinks or mounting pads for components that generate significant heat. Consider the specific requirements of your application and determine where HPL-03015 will be used as a thermal interface material.
2.Surface Preparation:
Before applying HPL-03015, ensure that the surfaces of the components and the PCB are clean, flat, and free from any contaminants. Use appropriate cleaning methods and solvents to achieve a clean surface.
3.Cutting and Shaping:
Cut the Bergquist HPL-03015 material to the desired shape and size using appropriate tools. Ensure that the dimensions of the material match the areas where it will be applied, such as the size of the component or the heat sink.
4.Application:
Place the cut HPL-03015 material on the designated areas of the PCB or the component. Ensure that it covers the entire surface area that requires thermal management. Gently press down to ensure good contact and eliminate any air gaps.
5.Bonding:
Depending on the specific application and requirements, you may need to use additional bonding methods to secure the HPL-03015 material in place. This could include using adhesives or thermal tapes to provide additional stability and prevent movement during operation.
6.Assembly:
Continue with the assembly process, ensuring that the components are properly aligned and soldered onto the PCB. Take care not to displace or damage the HPL-03015 material during the assembly process.
7.Testing and validation:
Once the PCB assembly is complete, perform thorough testing and validation to ensure that the thermal management provided by HPL-03015 meets the desired performance requirements. Monitor temperature levels and assess the effectiveness of the material in dissipating heat.
Factors to Consider When Choosing Bergquist HPL-03015
When choosing Bergquist HPL-03015 for your application, several factors should be considered:
1. Thermal conductivity: The thermal conductivity of HPL-03015 determines its ability to dissipate heat efficiently. Higher thermal conductivity ensures better heat transfer and helps maintain lower operating temperatures, which is crucial for applications with high watt-density and thermal management requirements.
2. Thermal resistance: The thermal resistance of HPL-03015 affects how effectively it can dissipate heat. Lower thermal resistance allows for improved heat flow and reduced temperature differentials, contributing to better thermal performance and reliability in the application.
3. Thickness range: The flexibility of HPL-03015 in terms of available thickness options is important, as it allows for customization and adaptation to specific application requirements. Choosing the appropriate thickness ensures proper thermal interface and optimal heat dissipation.
4. Compatibility with assembly processes: Consider the compatibility of HPL-03015 with the assembly processes used in your manufacturing. It should be compatible with common soldering methods, such as reflow soldering, to ensure smooth and reliable integration into your production process.
5. Application-specific requirements: Evaluate whether HPL-03015 meets the specific requirements of your application, such as electrical insulation properties, dielectric strength, and compatibility with other materials used in your design. Ensure that the material’s characteristics align with the needs and specifications of your application.
6. Certifications and standards: Check if HPL-03015 has undergone certification and testing by recognized industry standards organizations, such as IPC (Association Connecting Electronics Industries) and UL (Underwriters Laboratories). These certifications validate the quality, reliability, and safety of the material.
By considering these factors, you can make an informed decision when choosing Bergquist HPL-03015 for your application, ensuring optimal thermal management, performance, and reliability.
Summary
As electronic product manufacturers strive to meet the ever-increasing demands for performance, reliability, and efficiency, the choice of PCB materials becomes crucial. Bergquist HPL-03015 PCB material emerges as a standout solution, providing exceptional thermal management capabilities, excellent electrical insulation properties, and compatibility with various manufacturing processes.
By incorporating Bergquist HPL-03015 into their production workflows, manufacturers can enhance heat dissipation, improve component reliability, and ultimately deliver superior electronic products to meet the needs of today’s technology-driven world. Embracing the advantages of Bergquist HPL-03015 is a testament to the commitment of electronic manufacturers to push the boundaries of innovation and deliver cutting-edge solutions to their customers.