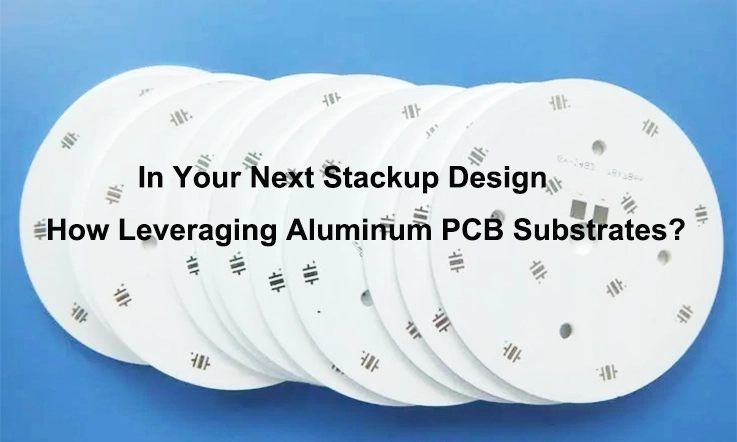
In the world of printed circuit board (PCB) design, the quest for top-notch performance and efficiency is a constant journey. One solution that has gained traction is the use of aluminum PCB substrates in stackup design. With their outstanding thermal conductivity and distinctive properties, aluminum substrates open the door to enhanced thermal management, improved signal integrity, and overall performance boosts.
By leveraging aluminum substrates, designers can craft PCBs that not only meet but exceed modern electronic demands. Whether it’s about keeping temperatures in check or ensuring signals travel without a hitch, aluminum substrates have got your back. Let’s explore how these materials can elevate your designs to the next level!
Key Benefits of Using Aluminum PCB Substrates
Enhanced Thermal Management in Stackup Design
When it comes to electronic design, managing heat is a major player, especially for components operating at high power levels. Aluminum substrates shine in this area, offering superior heat dissipation compared to traditional FR4 materials. Research has demonstrated that aluminum can significantly lower thermal resistance, enabling components to function within safe temperature limits—ultimately prolonging their lifespan.
For instance, in the world of LED technology, excessive heat can lead to performance issues. Aluminum substrates serve as effective heat sinks, dissipating heat efficiently and keeping temperatures in check. By incorporating aluminum into your stackup design, you’re not just reducing risks—you’re laying down the groundwork for peak performance and reliability.
Example Table: Thermal Resistance Comparison
Material Type | Thermal Resistance (°C/W) | Maximum Operating Temperature (°C) |
Aluminum PCB | 0.2 | 150 |
FR4 PCB | 0.8 | 130 |
Copper PCB | 0.15 | 200 |
This table shows how aluminum outperforms its competitors in thermal management, underscoring its value in high-performance applications.
Cost-Effectiveness in Stackup Production
Now, let’s get real: while the initial price tag of aluminum substrates might catch you off guard, the long-term benefits are hard to ignore. The durability of aluminum leads to fewer failures and replacements, which translates to less downtime and lower maintenance costs. It’s like investing in a solid pair of boots for a hike—you’ll save yourself the hassle of replacements down the road.
Moreover, the thermal efficiency of aluminum can reduce energy consumption, creating a win-win situation for both the environment and your wallet. A thorough analysis of production costs indicates that aluminum substrates can significantly lower operational expenses over time, proving to be a savvy choice for manufacturers.
Example Cost Analysis Table
Expense Type | FR4 PCB Costs | Aluminum PCB Costs | Estimated Savings (%) |
Material Cost | $0.10/sq in | $0.15/sq in | – |
Maintenance & Downtime | $200/month | $50/month | 75% |
Energy Consumption | $500/month | $300/month | 40% |
This table illustrates the potential savings when switching to aluminum substrates, highlighting the overall cost-effectiveness of aluminum in stackup production.
Aluminum PCB Substrate Materials and Dielectric Materials
Choosing the right materials for aluminum substrates is essential for optimizing their performance. Typically, aluminum is paired with dielectric materials like polyimide or epoxy resin, which deliver excellent thermal stability and insulating properties. This combination ensures that your designs perform like a charm, keeping everything running smoothly.
Types of Aluminum PCB Substrate Materials
Let’s break down the four primary types of aluminum substrates you might encounter:
●6061 Aluminum Alloy: This Al-Mg-Si alloy offers medium strength and great machining capabilities, making it suitable for CNC and V-Cut processing. However, its high price can be a bit of a sticker shock.
●5052 Aluminum Alloy: As an Al-Mg alloy, 5052 provides medium strength and excellent bending performance, making it a solid choice for punch forming. The price is fair, striking a balance between quality and cost.
●3003 Aluminum:This pure aluminum option boasts good thermal conductivity and reasonable machining performance, all while being easy on the wallet.
●1100 Aluminum: Similar to 3003, 1100 is pure aluminum known for its excellent thermal properties and cost-effectiveness. Both 3003 and 1100 are great options if you’re looking to keep your budget in check.
●Table: Aluminum Substrate Material Comparison
Material Type | Strength | Thermal Conductivity | Price |
6061 | Medium | Good | $$$$ |
5052 | Medium | Fair | $$ |
3003 | Low | Good | $ |
1100 | Low | Excellent | $ |
Dielectric Layer Considerations
When working with aluminum substrates, you need a reliable dielectric layer to prevent shorts between the conductive aluminum and copper circuit layers. The dielectric material we recommend is a special polymer filled with ceramics. This polymer boasts excellent dielectric strength, is resistant to aging, and provides high bonding capabilities.
The ceramic medium enhances thermal conductivity and viscoelasticity, allowing the substrate to withstand mechanical and thermal stresses during welding and operation. This combination is what keeps everything working harmoniously.
●Example of Dielectric Material Properties
Property | Description |
Dielectric Strength | High, preventing electrical shorts |
Temperature Resistance | Can withstand up to 200°C |
Mechanical Resistance | Withstands thermal and mechanical stresses |
For double-sided aluminum PCBs, using a ceramic-filled polymer as the dielectric layer is non-negotiable. This ensures you get reliable performance and longevity in your applications.
Therefore, when selecting dielectric materials, focus on factors like thermal conductivity and dielectric strength. These aspects are key to maximizing the overall efficiency of your PCB and ensuring your design performs like a well-oiled machine.
Comparing Aluminum PCB Substrates to Other Options
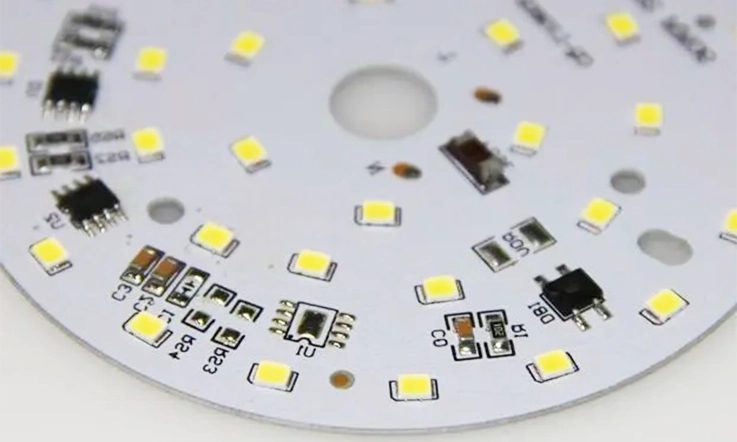
When you stack aluminum PCB substrates against other materials, the advantages really stand out. Traditional substrates like FR4 often struggle with heat management, especially in high-power applications. In these scenarios, aluminum substrates deliver a dependable solution that can handle elevated temperatures without breaking a sweat. This is particularly critical in environments where heat can derail performance.
Heat Management Comparison Table
Material Type | Maximum Operating Temperature (°C) | Thermal Conductivity (W/m·K) | Typical Applications |
Aluminum PCB | 150 | 205 | LED lighting, power supplies |
FR4 PCB | 130 | 0.25 | General electronics |
Copper PCB | 200 | 390 | High-performance applications |
From this table, it’s clear that aluminum substrates outperform FR4 in thermal management, making them a solid choice for demanding applications.
Additionally, aluminum substrates usually boast enhanced mechanical strength. This robustness is a real asset for applications exposed to vibration or shock, ensuring your PCB stays solid over time. Think about automotive electronics or industrial machinery—these environments demand toughness, and aluminum substrates deliver just that.
Types of Aluminum PCB Substrates
Aluminum substrates come in various types, each tailored for specific applications. Here’s a quick rundown:
●Thermal Management PCBs:These are specifically engineered for high-power applications that require optimal heat dissipation. With advanced thermal properties, they excel in LED technology and high-efficiency power supplies.
●Standard Aluminum PCBs:These versatile options work well for general applications that have basic thermal management needs. If your project doesn’t demand high performance but still benefits from aluminum’s durability, this is a solid choice.
●Flexible Aluminum PCBs:Perfect for designs needing bending or manipulation without sacrificing performance. They’re ideal for wearable technology or portable devices where space is tight.
●Choosing the Right Type of Aluminum Substrate
Selecting the appropriate type of aluminum substrate depends on your project’s unique requirements, such as size, thermal management needs, and the environment in which the PCB will operate. Here’s a handy checklist to guide your decision:
Criteria | Thermal Management PCBs | Standard Aluminum PCBs | Flexible Aluminum PCBs |
Heat Dissipation Requirement | High | Medium | Variable |
Mechanical Strength | High | Medium | Medium |
Flexibility | Low | Low | High |
Cost | Higher | Moderate | Higher |
By considering these factors, you can ensure your choice aligns with your project’s goals, leading to a successful design that performs reliably under pressure.
Designing Your Stackup with Aluminum PCB Substrates
Key Considerations for Stackup Design
When you’re integrating aluminum substrates into your stackup design, a few key factors are essential for success. First off, layer configuration plays a significant role in achieving optimal thermal and electrical performance. Arranging components properly can significantly enhance both the efficiency and functionality of the PCB.
Material selection is another vital aspect. Evaluating the specific needs of your application—like temperature ranges and mechanical stresses—will help you make informed material choices. For instance, in a recent project centered around high-density LED applications, meticulous attention to layer configuration and material selection resulted in a 30% boost in thermal performance. Talk about a solid win!
Table: Key Design Considerations
Consideration | Description | Impact on Performance |
Layer Configuration | Arrangement of components | Enhances efficiency |
Material Selection | Choice of aluminum and dielectric materials | Influences thermal and mechanical properties |
Component Placement | Positioning of heat-generating components | Optimizes heat distribution |
Integrating Thermal Management Solutions in Stackup Design
To really maximize the thermal management benefits of aluminum substrates, consider integrating both active and passive cooling methods into your stackup design. Techniques like thermal vias can facilitate heat transfer away from sensitive components, while strategically placed heat sinks can further enhance thermal dissipation.
Additionally, taking a close look at component placement during the design phase can optimize thermal performance. For example, positioning high-heat-generating components away from sensitive parts can lead to better overall heat distribution. This approach creates a more reliable and efficient PCB. It’s all about playing it smart!
Example of Thermal Management Techniques
Technique | Description | Benefits |
Thermal Vias | Conductive pathways for heat transfer | Disperses heat effectively |
Heat Sinks | External structures to absorb and dissipate heat | Lowers temperatures significantly |
Component Placement | Strategic arrangement of components | Enhances thermal efficiency |
By leveraging these techniques and considerations, you can design a stackup that not only meets but exceeds performance expectations, all while keeping everything running cool and collected.
Stackup Design Techniques for Aluminum PCB Substrates
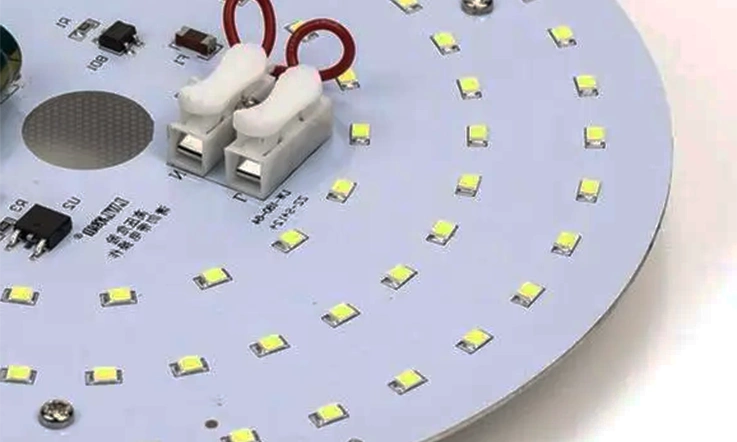
When diving into the design process with aluminum PCB substrates, it’s essential to pay close attention to the stackup design. This ensures optimal performance and reliability across your applications. Here are some tailored stackup design techniques that can help you get the most out of your aluminum PCBs:
Layer Arrangement
Signal and Power Layers: Position high-speed signal layers next to power or ground planes. This setup minimizes noise coupling and provides effective return paths, which is key for maintaining signal integrity.
Ground and Power Planes: Ensure there are ample ground and power planes. This helps establish stable references for signal layers and improves thermal dissipation, keeping your PCB cool under pressure.
Signal Layer Distribution: Aim for an even distribution of signal layers across the stackup. This not only maintains symmetry but also reduces electromagnetic interference (EMI), making your design cleaner.
Signal Routing Strategies
Differential Pairs: Group and route differential pairs on adjacent layers to maintain controlled impedance and reduce signal skew. This technique is particularly handy for high-speed applications.
Signal Layer Allocation: Assign critical signals to internal layers, which shields them from external noise sources. It’s like giving your sensitive signals a cozy blanket to stay warm and protected.
Signal Layer Separation: Keep sensitive analog or high-speed digital signals apart from each other and from noisy power or high-current traces. This way, you can avoid unwanted crosstalk and ensure smoother operation.
Thermal Dissipation Optimization
Thermal Vias: Position thermal vias close to heat-generating components to efficiently transfer heat to the aluminum substrate. This technique is essential for effective thermal dissipation, preventing overheating.
Copper Pour and Planes: Use copper pours or planes on the top or bottom layers. This enhances heat spreading and improves thermal conductivity, keeping everything nice and chill.
Heat Sinks and Thermal Pads: Incorporate heat sinks or thermal pads for components that kick out a lot of heat. This extra layer of cooling helps maintain performance during heavy use.
Stacking Multiple Aluminum PCB Substrates
Alignment and Registration: Make sure to align and register multiple aluminum PCB substrates accurately. This ensures both electrical and mechanical integrity, helping to avoid potential hiccups down the line.
Interconnect Methods: Choose the right interconnect methods, like edge connectors or board-to-board connectors. Reliable electrical connections between stacked boards are essential to keep everything talking smoothly.
Thermal Interface Materials: Use thermal interface materials, such as thermal pads or thermal paste, between stacked aluminum PCB substrates. This enhances heat transfer and minimizes thermal impedance, ensuring efficient cooling.
Impedance Control and Transmission Lines
Controlled Impedance: Calculate and design trace widths, spacing, and dielectric thickness to achieve the desired controlled impedance. Remember to consider the higher dielectric constant of aluminum substrates during this process.
Differential Impedance: Keep a consistent differential impedance for high-speed differential signal pairs to maintain signal integrity. This helps your signals stay sharp and clear.
Transmission Line Termination: Apply appropriate termination techniques, like series resistors or parallel termination, to minimize signal reflections and keep the signal quality on point.
Design for Manufacturability
Aspect Ratio: Pay attention to the aspect ratio (board thickness to minimum hole size) to ensure manufacturability during drilling and plating processes. Getting this right can save you headaches later.
Panelization: Optimize panelization strategies to maximize the number of boards per panel. This boosts manufacturing efficiency and cuts costs.
Design Rule Check (DRC): Conduct thorough design rule checks to catch any potential manufacturing issues. Ensuring compliance with fabrication capabilities can save time and resources in the long run.
Manufacturing Process of Aluminum PCB Substrates
The manufacturing process for aluminum PCB substrates involves several critical steps, starting from material selection all the way to final testing. Grasping this process is vital for ensuring quality and reliability in your designs.
Key Steps in the Manufacturing Process
1.Material Selection
The journey begins with choosing the right aluminum alloy and dielectric materials. This choice impacts the thermal conductivity, strength, and overall performance of the PCB. For instance, selecting a high-quality aluminum alloy like 6061 can lead to superior thermal management.
2.Copper Foil Application
The next step involves applying a layer of copper foil to the aluminum substrate. This is typically achieved through a lamination process that ensures strong adhesion. A good bond between the copper and aluminum is key to maintaining thermal and electrical performance.
3.Circuit Patterning
Once the copper is in place, the circuit pattern is created using photolithography. This process allows precise design features and is essential for achieving the desired functionality of the PCB.
4.Etching
After patterning, the unwanted copper is removed through an etching process. This step is where the actual circuit paths take shape, ensuring that everything is wired just right for optimal performance.
5.Dielectric Layer Application
A dielectric layer is then applied to insulate the aluminum and copper layers, preventing any shorts. The use of high-quality dielectric materials enhances overall PCB reliability.
6.Final Testing
Finally, rigorous testing is conducted to ensure that the aluminum PCB substrates meet all specifications and industry standards. This includes thermal testing, electrical testing, and visual inspections.
Table: Aluminum PCB Manufacturing Process Overview
Step | Description | Key Considerations |
Material Selection | Choose aluminum and dielectric materials | Impact on thermal and mechanical properties |
Copper Foil Application | Laminate copper onto aluminum substrate | Strong adhesion is critical |
Circuit Patterning | Use photolithography to create circuit designs | Precision is key |
Etching | Remove unwanted copper to form circuit paths | Ensures functionality |
Dielectric Layer Application | Apply insulation layer to prevent shorts | Quality enhances reliability |
Final Testing | Conduct thermal, electrical, and visual tests | Ensures compliance with standards |
Compliance with IPC Standards
Throughout the manufacturing process, compliance with IPC standards is non-negotiable. Adhering to these guidelines guarantees that your aluminum substrates meet industry requirements, ensuring they perform reliably over time. This commitment not only enhances the durability and efficiency of your products but also fosters trust with clients and stakeholders.
By understanding and executing each step meticulously, manufacturers can produce high-quality aluminum PCBs that meet the demands of various applications, from consumer electronics to industrial machinery. It’s all about getting it right the first time, so you can keep your projects rolling smoothly!
Applications of Aluminum PCB Substrates in Stackup Design
Aluminum PCB substrates are making waves across various industries, thanks to their exceptional thermal management capabilities. Let’s dive into some of the most common applications where these substrates shine.
Common Applications
LED Technology: In the realm of LED technology, efficient heat dissipation is key for maintaining performance and longevity. Aluminum substrates are widely adopted in LED driver circuits and lighting fixtures. For example, in street lighting systems, using aluminum PCBs can significantly extend the lifespan of LEDs by keeping temperatures in check.
Power Supply Units: In power electronics, keeping temperatures low is essential for maximizing efficiency and reliability. Aluminum PCBs are frequently utilized in high-efficiency power converters. A notable case is in electric vehicle chargers, where these substrates help manage heat during high-speed charging, ensuring smooth operation without overheating.
Automotive Electronics: As vehicles become more sophisticated, reliable thermal management is increasingly sought after. Aluminum substrates are commonly found in automotive control systems, playing a significant role in ensuring optimal performance under challenging conditions. For instance, in engine control units (ECUs), aluminum PCBs help manage the heat generated by electronic components, ensuring they operate reliably in high-temperature environments.
Summary of Applications
Application Area | Description | Key Benefits |
LED Technology | Used in driver circuits and lighting fixtures | Enhances lifespan and performance |
Power Supply Units | Found in high-efficiency power converters | Improves thermal management |
Automotive Electronics | Integrated in control systems for vehicles | Ensures reliability in tough conditions |
These applications illustrate the versatility of aluminum PCB substrates in addressing diverse industry needs. Whether you’re lighting up the streets or powering your ride, aluminum substrates are there, keeping everything cool and running smoothly. It’s all about finding the right fit for your project and reaping the benefits of advanced thermal management!
Performance Characteristics of Aluminum PCB Substrates
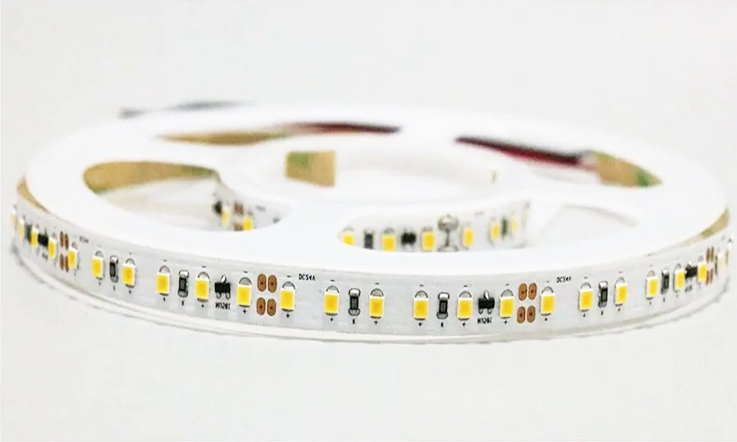
Aluminum PCB substrates are well-known for their reliability and durability, making them a solid option for demanding applications. Let’s explore some of the key performance characteristics that set aluminum apart from traditional materials.
High Temperature Resistance
Aluminum substrates can withstand higher temperatures compared to conventional materials like FR4. This capability is essential in applications where heat generation is a concern. For instance, in power supply units, aluminum PCBs can operate at elevated temperatures without compromising performance.
Table: Temperature Tolerance Comparison
Material Type | Maximum Operating Temperature | Typical Application |
Aluminum PCB | Up to 200°C | Power supply, automotive |
FR4 | Up to 130°C | General electronics |
Mechanical Stress Endurance
Another standout feature of aluminum substrates is their ability to endure mechanical stresses. This makes them a reliable choice for environments where vibrations or shocks are common, such as in automotive and industrial applications. For example, in automotive control units, aluminum PCBs can maintain their integrity despite the rough conditions they may face on the road.
Compliance and Testing
Thorough testing and adherence to industry standards validate the performance of aluminum PCBs. Ensuring that these substrates meet established guidelines allows manufacturers to deliver products that last. A recent study highlighted that aluminum PCBs exhibited a failure rate much lower than that of FR4 substrates when subjected to high thermal stress conditions. This not only reinforces their durability but also enhances the trustworthiness of the products using them.
Summary of Performance Characteristics
Performance Characteristic | Aluminum PCB | FR4 |
Temperature Resistance | Up to 200°C | Up to 130°C |
Mechanical Stress Endurance | High | Moderate |
Failure Rate | Lower under stress | Higher under stress |
These performance characteristics highlight why aluminum PCB substrates are a dependable choice for various applications. From automotive electronics to power supplies, aluminum substrates offer robust performance that keeps projects running strong. When you’re looking for materials that stand the test of time, aluminum is where it’s at!
Frequently Asked Questions (FAQ) About Aluminum PCB Substrates
What advantages do aluminum substrates have over traditional materials?
Aluminum substrates provide superior thermal management, making them ideal for high-power applications. Their mechanical strength ensures longevity and reliability.
How do I select the right dielectric material for my aluminum PCB?
Consider the specific thermal and electrical requirements of your application. Materials like polyimide and epoxy are often suitable due to their stability under varying conditions.
What applications are best suited for aluminum PCBs?
Aluminum PCBs excel in applications such as LED technology, power supply units, and automotive electronics, where efficient thermal management is critical.
Sum Up
Harnessing Aluminum PCB Substrates in Stackup Design
Utilizing aluminum PCB substrates in stackup design unlocks a plethora of opportunities. With superior thermal management, improved electrical performance, and enhanced mechanical strength, these substrates equip engineers to craft advanced PCBs tailored for today’s intricate electronic systems. As technology progresses, aluminum substrates are set to become even more influential in the evolution of PCB design.
The future looks promising for aluminum PCB substrates, offering a canvas for innovation. By incorporating these materials into your stackup designs, you’re not only keeping pace with industry trends—you’re also delivering products that stand out in a competitive market.
So, why hold back? Jump on the aluminum substrate bandwagon and elevate your designs to new heights. In the electronics field, maintaining composure under pressure is not just a saying; it’s a smart tactic. Let’s team up to ensure your next project is a hit—together, we can make it happen!