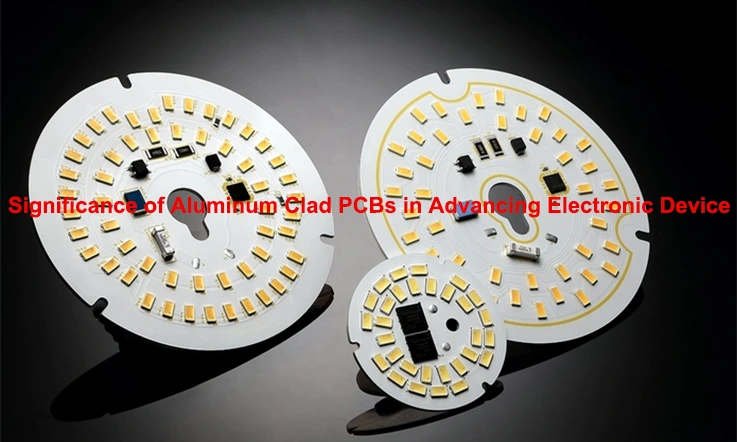
Aluminum clad PCBs provide a solid foundation for electronic device design, tackling challenges like thermal management, signal integrity, and miniaturization. By merging the exceptional thermal conductivity of aluminum with the flexibility of PCB technology, these boards present a winning solution across various applications. For instance, in LED lighting, aluminum clad PCBs facilitate effective heat dissipation, allowing LEDs to shine brighter and last longer. This combination not only keeps components cool but also ensures reliable performance, making them a no-brainer for manufacturers looking to boost efficiency.
Therefore, aluminum clad PCBs are transforming the electronics landscape by enhancing thermal performance and enabling compact designs. Embracing these boards means stepping up to the plate, ensuring that products are not only high-performing but also ready for the future of technology.
The Significance of Aluminum Clad PCBs in Modern Electronics
Introduction to Aluminum Clad PCBs
In today’s dynamic electronics landscape, aluminum clad PCBs have become a go-to solution for engineers and manufacturers looking to elevate performance and thermal management in their devices. These boards are not just a trend; they represent a practical approach to tackling heat dissipation and reliability challenges in high-performance applications.
Let’s break down the unique benefits of aluminum clad PCBs:
Feature | Description | Example Application |
Thermal Conductivity | Aluminum’s excellent heat dissipation keeps components cool, minimizing the risk of overheating. | LED lighting systems, automotive control units |
Mechanical Strength | The robust construction of aluminum clad PCBs enhances durability in demanding environments. | Industrial machinery, aerospace components |
Cost-Effectiveness | Reduced need for additional cooling components translates to lower overall manufacturing costs. | Consumer electronics, home appliances |
Design Flexibility | Easy customization for various applications allows for innovative designs without significant cost increases. | Prototyping for new tech products |
Take, for instance, a well-known LED manufacturer that switched to aluminum clad PCBs. They reported a notable 30% increase in lumen output, showcasing the direct benefits of enhanced thermal management. This move not only improved performance but also solidified their position in a competitive market.
By embracing aluminum clad PCBs, businesses can streamline production processes while ensuring that their products meet the demands of modern consumers. Whether it’s keeping LEDs bright or ensuring automotive systems run smoothly, aluminum clad PCBs are a solid choice for anyone looking to push the envelope in electronic design.
Definition and Composition
Aluminum clad PCBs consist of a tri-layer construction, featuring an aluminum base layer, a dielectric layer, and a copper circuitry layer. This unique setup not only enhances thermal conductivity but also bolsters the mechanical strength of the PCB, making it a reliable choice for various applications.
Layer | Material | Purpose |
Base Layer | Aluminum | Provides superior heat dissipation and durability. |
Dielectric Layer | Epoxy or FR-4 | Insulates the copper circuitry from the aluminum. |
Circuitry Layer | Copper | Conducts electrical signals with minimal resistance. |
For instance, in high-power applications like LED lighting and automotive systems, aluminum clad PCBs shine by effectively managing heat, ensuring components stay cool and functional. A leading automotive manufacturer found that integrating aluminum clad PCBs in their control units led to a marked improvement in thermal performance, significantly reducing the risk of failure in harsh conditions.
When it comes to managing heat, aluminum variants truly know how to step up to the plate. Their robust design allows for a seamless blend of efficiency and reliability, giving manufacturers the confidence they need to innovate without worrying about overheating or component failure.
Advantages of Aluminum Clad PCBs for Manufacturers
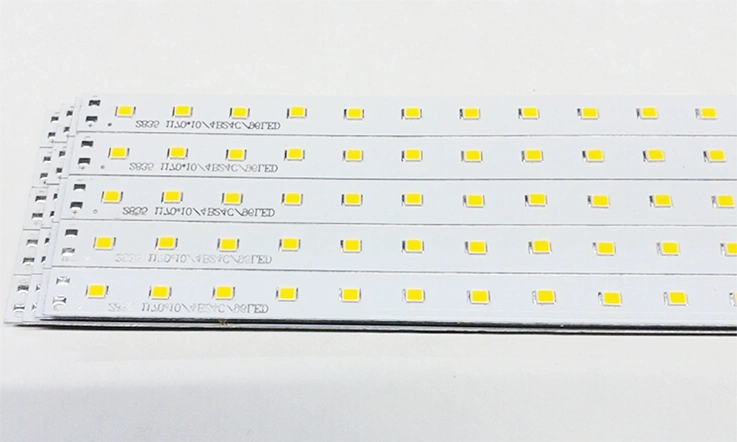
Superior Thermal Management
Aluminum clad PCBs excel in heat management, an increasingly pressing issue as electronic devices shrink and power up. Their outstanding thermal conductivity enables these boards to efficiently transfer heat away from critical components, maintaining optimal performance and reliability.
Application | Benefit | Example |
LED Lighting | Efficient heat dissipation enhances lifespan. | A prominent LED manufacturer reported a 30% increase in lumen output after switching to aluminum PCBs. |
Power Amplifiers | Reduces overheating, improving device reliability. | Systems with aluminum PCBs can achieve temperature drops of up to 20% compared to standard designs. |
In high-power applications like LED lighting and power amplifiers, excessive heat can hinder performance. Aluminum clad PCBs create a reliable path for heat to escape, prolonging device life. One automotive supplier noticed a significant drop in failures related to overheating after integrating aluminum PCBs in their systems—definitely a smart move!
Cost Efficiency and Design Flexibility
When evaluating the overall cost of electronic manufacturing, aluminum clad PCBs often take the lead.
Cost Factor | Description | Impact |
Material Comparison | Fewer components needed for effective thermal management. | Reduces reliance on costly heat sinks and complex cooling systems. |
Longevity | Durable aluminum design extends product lifespan. | Lowers replacement costs over time. |
While initial material costs may vary, aluminum clad PCBs typically require fewer additional components for heat management. This cuts down on expenses and simplifies cooling solutions. Plus, the long-lasting nature of aluminum means manufacturers save on replacements.
The design flexibility of aluminum clad PCBs is another significant advantage. Manufacturers can easily modify designs to fit specific application needs without hefty costs. This adaptability makes aluminum PCBs an excellent choice for prototyping, allowing engineers to test and refine designs efficiently. For instance, one electronics company found that this approach led to faster time-to-market and reduced waste—definitely a win-win!
Mechanical Strength and Reliability
Beyond thermal management and cost, aluminum clad PCBs offer impressive mechanical strength, making them suitable for various demanding applications.
Feature | Benefit | Example |
Durability | Withstands physical stress and extreme conditions. | Ideal for automotive and aerospace applications. |
Reliability | Sturdy construction enhances dependable performance. | Keeps electronic systems functioning smoothly under pressure. |
Built to endure, aluminum clad PCBs thrive in harsh environments, resisting physical stress and vibration. This robustness makes them a go-to choice for industries like automotive and aerospace, where components face rigorous demands. The reliable nature of aluminum clad PCBs provides peace of mind, ensuring that electronic systems perform consistently, even in critical applications.
Structure and Properties of Aluminum Clad PCBs
Mechanical and Thermal Properties
The mechanical strength of aluminum clad PCBs truly shines in a variety of environments, from automotive applications to consumer electronics. These boards are designed to endure temperature fluctuations and physical stress, making them a dependable choice for demanding settings.
Property | Description | Application |
Mechanical Strength | Withstands physical stress and vibration. | Automotive control modules. |
Thermal Stability | Maintains performance across temperature changes. | Consumer electronics and industrial equipment. |
For instance, in automotive control systems, aluminum clad PCBs excel in environments that require both resilience and thermal management. Their robust design ensures that they operate smoothly, even when faced with challenging conditions, giving manufacturers the confidence to push the envelope in their designs.
Performance Characteristics
Aluminum clad PCBs provide reliable electrical performance, a must-have for modern electronic devices. Their capacity to handle high currents with minimal voltage drop plays a significant role in optimizing device efficiency—nobody wants a sluggish circuit!
Performance Metric | Description | Benefit |
Current Handling | Effectively manages high currents. | Supports high-power applications without overheating. |
Voltage Drop | Keeps voltage loss to a minimum across connections. | Boosts overall device performance. |
One manufacturer of power amplifiers switched to aluminum clad PCBs and noticed a marked reduction in voltage drop, which translated to enhanced efficiency in their products. This kind of improvement can make a real difference, pushing devices to perform at their best and ensuring that they meet the demands of today’s technology landscape.
Key Applications of Aluminum Clad PCBs
Industrial Use Cases
In the automotive industry, aluminum clad PCBs are the real MVPs for thermal management and durability. These boards are instrumental for the operation of LED headlights, control systems, and various sensors, providing the reliability needed in demanding environments.
Application | Description | Example |
LED Headlights | Efficient heat dissipation boosts lifespan. | Found in cutting-edge automotive lighting systems. |
Control Systems | Supports complex electronic control functions. | Used in engine management and advanced safety systems. |
Sensors | Ensures reliable performance under extreme conditions. | Employed in temperature and pressure monitoring devices. |
For instance, a major automotive manufacturer integrated aluminum clad PCBs in their vehicle control units, resulting in enhanced reliability and efficiency. These boards can handle the heat—both literally and metaphorically—making them essential for modern vehicles.
Emerging Trends in the Market
As the demand for energy-efficient solutions continues to rise, the market for aluminum clad PCBs is heating up. Regulatory trends are nudging manufacturers toward greener materials and practices, establishing aluminum as a preferred choice for eco-friendly designs.
Trend | Description | Projected Impact |
Sustainability Focus | Shift towards environmentally friendly materials. | Promotes aluminum use in a broader range of applications. |
Market Growth | Anticipated increase in demand for aluminum PCBs. | Experts forecast a compound annual growth rate (CAGR) exceeding 6% over the next five years—definitely a trend to keep an eye on! |
As energy efficiency becomes a priority across industries, aluminum clad PCBs are leading the way. This shift benefits manufacturers aiming to comply with regulations and appeals to consumers who prioritize sustainability.
Cost Considerations in Aluminum Clad PCB Design
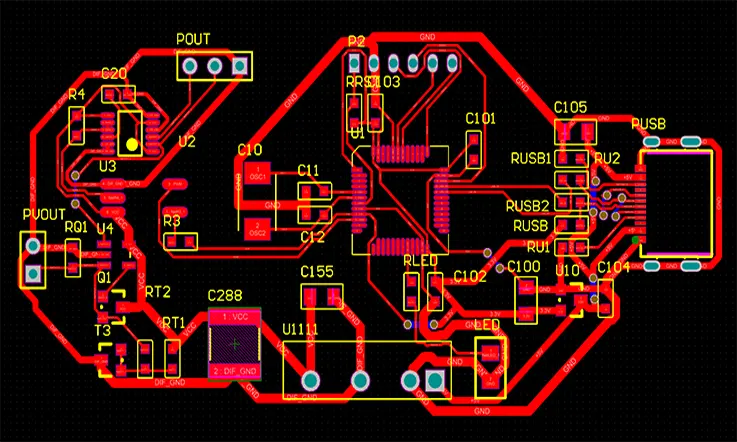
Long-Term Economic Advantages
Investing in aluminum clad PCBs can yield benefits that reach far beyond initial expenses. Their durability and thermal efficiency translate into notable savings in operational costs over time. A lifecycle cost analysis indicates that although the upfront investment may be higher, the overall savings in maintenance and energy efficiency can surpass 20% throughout the product’s lifespan—definitely a savvy move!
Cost Factor | Description | Potential Savings |
Initial Investment | Higher upfront costs compared to standard PCBs. | Justifiable through long-term gains. |
Maintenance Costs | Reduced frequency of repairs and replacements. | Saves both time and money. |
Energy Efficiency | Lower energy consumption due to superior thermal management. | Can lead to significant operational cost reductions. |
For instance, a manufacturer in the LED lighting sector switched to aluminum clad PCBs and reported a 25% reduction in energy costs within the first year. This shift not only enhanced their product performance but also allowed for more competitive pricing, proving that smart choices today can pay off in spades down the road.
Fabrication and Processing Considerations of Aluminum Clad PCBs
Overview of the Manufacturing Process
The fabrication of aluminum clad PCBs involves several key stages, starting from selecting high-quality materials to conducting final quality checks. Each phase is designed to ensure the boards can handle the demands of their applications. Integrating automated testing systems at various points helps uphold high standards throughout production.
Stage | Description | Key Considerations |
Material Selection | Choosing quality aluminum and dielectric materials. | Compatibility and performance. |
Layer Stacking | Aligning the aluminum base, dielectric, and copper layers. | Precision in alignment. |
Etching and Drilling | Creating circuits and vias with accuracy. | Minimizing defects. |
Final Inspection | Conducting thorough checks for quality assurance. | Meeting specifications. |
For instance, one prominent manufacturer adopted a multi-point inspection system during the layer stacking phase, reducing defects significantly. This meticulous attention to detail can lead to a more reliable product.
Best Practices for Fabrication
In fabrication, precision is key. Following established industry standards boosts the reliability of the PCBs and enhances the manufacturer’s reputation. Regular audits and quality control checks keep operations running smoothly.
Best Practice | Description | Benefits |
Standard Operating Procedures | Documented guidelines for each process step. | Ensures consistency and efficiency. |
Training Programs | Ongoing education for staff on best practices. | Enhances skills and knowledge. |
Real-Time Monitoring | Using software to track production metrics. | Facilitates quick issue identification. |
By implementing these best practices, manufacturers can ensure that their aluminum clad PCBs meet the performance standards expected in today’s market. This dedication to quality not only satisfies clients but also strengthens market presence.
Challenges and Solutions of Aluminum Clad PCBs

Common Manufacturing Challenges
Manufacturing aluminum clad PCBs presents several hurdles, such as sourcing high-quality materials and effectively managing heat during production. The precision required for handling aluminum and ensuring proper adhesion between layers can be quite demanding. Issues like delamination and inadequate thermal conductivity may arise if not addressed properly.
Challenge | Description | Impact |
Material Sourcing | Difficulty in obtaining high-grade aluminum. | Affects overall quality and performance. |
Heat Management | Managing temperature during the manufacturing process. | Leads to potential defects. |
Layer Adhesion | Ensuring strong bonding between layers. | Risks delamination in end products. |
Innovative Solutions for Optimization
Leveraging innovation is key to tackling these challenges head-on. Techniques such as enhanced design software and automated manufacturing processes can streamline production and reduce errors, ultimately resulting in a superior product. For example, the adoption of advanced laser processing technology has allowed manufacturers to achieve impressive precision levels, which has notably boosted yield rates.
Solution | Description | Benefits |
Advanced Design Software | Tools that facilitate better design and analysis. | Improves accuracy and reduces errors. |
Automation in Production | Implementing robotic systems to manage tasks. | Increases efficiency and consistency. |
Laser Processing Technology | Utilizing lasers for precise cutting and drilling. | Enhances yield and minimizes waste. |
For instance, a leading manufacturer reported a 25% increase in yield rates after integrating laser processing technology into their production line. This kind of proactive approach not only alleviates manufacturing headaches but also positions companies favorably in a competitive market.
Procurement Considerations for Aluminum Clad PCBs
Selecting the Right Aluminum Clad PCB Supplier
For procurement specialists, choosing the right supplier is no small feat. Key factors like industry certifications, manufacturing capabilities, and customer service can really tip the scales. Establishing long-term relationships with trustworthy suppliers often leads to better pricing and enhanced support—after all, it’s all about working smarter, not harder!
Criteria | Importance | Considerations |
Certifications | Ensures compliance with industry standards. | Look for ISO, IPC, etc. |
Manufacturing Capabilities | Ability to handle custom orders and scalability. | Evaluate production capacity. |
Customer Service | Provides ongoing support and communication. | Check reviews and testimonials. |
For example, a major player in the automotive sector shifted to a supplier known for aluminum clad PCBs after conducting thorough research. This decision not only improved their supply chain reliability but also resulted in a 15% reduction in costs over the project lifecycle—proving that the right partnership can lead to valuable outcomes.
Cost Analysis for Procurement
Understanding the total cost of ownership is crucial for making informed procurement decisions. This means looking beyond just the initial purchase price to include maintenance and longevity factors, ensuring you’re getting a solid return on your investment. A detailed cost-benefit analysis can make a compelling case for choosing aluminum clad PCBs over traditional options.
Cost Element | Description | Long-Term Implications |
Initial Purchase Price | The upfront cost of acquiring the PCBs. | Higher investment upfront. |
Maintenance Costs | Ongoing expenses related to repairs or replacements. | Lower costs over time. |
Longevity | The lifespan of the PCBs and their reliability. | Extended lifespan leads to savings. |
In a recent study, a company that evaluated its total cost of ownership for aluminum clad PCBs found that, despite higher initial costs, their overall expenses were reduced by 30% due to lower maintenance and energy savings. This data reinforces the idea that informed procurement choices lead to better long-term financial health.
Wrapping Up
As electronic devices evolve and push the envelope of performance, aluminum clad PCBs emerge as critical components in this transformation. Their outstanding thermal conductivity, excellent signal integrity, and compact design make them must-haves across various applications, from electric vehicles and 5G communication to renewable energy systems and autonomous technologies.
These boards efficiently dissipate heat, boost signal transmission, and accommodate high-power components, enabling the creation of more reliable and innovative electronic devices. For example, in electric vehicles, aluminum clad PCBs help maintain optimal temperatures in battery management systems, contributing to longer lifespans and improved safety. As technology continues to advance, the demand for aluminum clad PCBs will rise, propelling further innovations in design and functionality.
All in all, aluminum clad PCBs serve as a robust foundation for next-generation electronics. By tapping into their unique properties, manufacturers and designers can unlock new possibilities and drive the future of electronic performance. Embracing these boards means staying ahead of the curve and powering the next wave of technological advancements.
Frequently Asked Questions (FAQs)
What distinguishes Aluminum Clad PCBs from other types?
Aluminum clad PCBs stand out due to their superior thermal management, mechanical strength, and cost efficiency, making them ideal for high-performance applications.
How do aluminum PCBs improve thermal performance?
Their high thermal conductivity allows heat to dissipate quickly, reducing the risk of overheating in demanding environments.