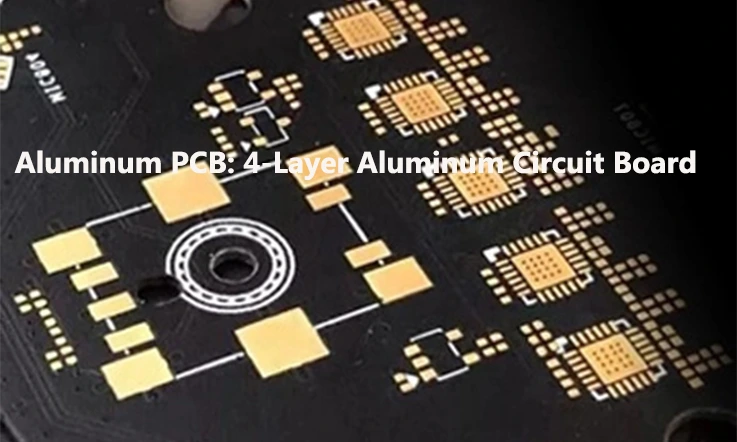
Thermal management is an increasingly important consideration in the design and construction of modern printed circuit boards. As component power densities rise and form factors shrink, dissipating heat effectively becomes paramount to ensure reliability and functionality. While traditional FR-4 laminate remains the workhorse material for most applications, its insulating properties can limit its suitability for demanding high-power use cases.
Aluminum PCB technology offers an attractive alternative, leveraging the excellent thermal conductivity of its core material. In this article, we will explore the key attributes and design aspects of 4 layer aluminum PCBs, analyzing their benefits and limitations compared to standard multilayer board technologies.
What is a 4 Layer Aluminum PCB?
A 4 layer aluminum PCB (printed circuit board) is a type of PCB that uses aluminum as the core conductive layer instead of the more common copper. And It consist of two inner aluminum core layers and two outer copper layers.
Layer Stackup and Construction of a 4 Layer Aluminum PCB
Here are the typical layer stackup and construction details for a 4 layer aluminum PCB:
Core Layers:
●2 inner layers made of aluminum metal, typically 1-2mm thick. These function as ground and power planes.
●Aluminum is preferred over copper due to its better thermal conductivity and lighter weight.
●Alloys like Al5052 and Al6061 are commonly used for the aluminum core.
●The aluminum layers are etched to form tracings, pads, and clearance holes.
Outer Layers:
●2 external layers made of copper foil, typically 35μm thick.
●Copper allows for easier soldering and component mounting.
●The copper layers are patterned with traces for signals and component connections.
Dielectric Layers:
●The aluminum and copper layers are separated by dielectric prepreg layers.
●These are typically made of epoxy resin impregnated fiberglass (FR-4).
●The dielectric electrically insulates the aluminum and copper layers while bonding them together.
Vias and Through Holes:
●Plate through holes allow connections between the aluminum and copper layers.
●Blind and buried vias can connect between layers.
So in summary, the core of a 4 layer Al PCB is 2 layers of aluminum, with 2 external copper layers to facilitate component mounting and soldering. Dielectric layers provide insulation between the conductive layers.
Performance parameter of 4 Layer Aluminum PCB
Thermal conductivity – Aluminum’s high thermal conductivity (~200 W/mK) allows efficient spreading of heat away from components. Much better than FR-4 PCBs (~0.25 W/mK).
Current carrying capacity – Wide traces can carry higher amperage than FR-4 before overheating. Lower trace impedance also improves power integrity.
Signal integrity – Skin effect is greater than FR-4 but proper trace widths/impedance control keeps SI similar to standard multilayer boards.
Layer stack up tolerance – Core/prepreg thickness tolerance is looser than FR-4, typically +/- 20 μm per layer. Tighter DFM needed for smaller holes/tracks.
Dielectric thickness – Thinner cores (0.5-1 mm) and prepregs (0.05-0.2 mm) provide lower thermal resistance than thicker boards.
Operating temperature – Aluminum core allows continuous operation at higher ambient temps, typically up to 105°C max before de-rating components.
Thermal resistance (junction-to-case/ambient) – Much lower RθJC/θJA values, typically under 2°C/W. Allows greater power density in components.
Drill/hole quality – Diamond drills needed but produce smooth, high aspect ratio holes with tight tolerances when properly canned.
Impedance control – Wider impedance tolerances than FR-4 due to variable dielectric constants and conductive aluminum layers.
Stack up design – Inner power planes and optimized thermal vias maximize heat transfer through aluminum core.
Careful design validation against parameters like these ensures targeted thermal/electrical performance.
Design Considerations for 4 Layer Aluminum PCBs
Here are some key design considerations for 4 layer aluminum PCBs:
Layer stacking
Typically it will be Internal Power Plane, Internal Ground Plane, Signal Routing, Solder mask/component side. This provides a solid ground and power delivery structure.
Power/ground planes
Need to ensure adequate copper fill/pour on the power and ground planes for low impedance distribution. Use parallel paths when possible.
Decoupling
Need sufficient decoupling capacitors placed near components between power and ground planes to filter high frequency noise.
Thermal Management
Aluminum PCBs conduct heat well. Consider heat generation of components and use large thermal vias/traces to draw heat to the edges for heat sinks.
Trace widths
Can use narrower trace widths than FR-4 due to aluminum’s higher thermal conductivity. But wider is still better for power/ground traces.
Clearance/spacing
Requirements are more stringent than FR-4 due to aluminum’s increased conductivity. Follow IPC guidelines closely.
Drill sizes
Diamond-coated drills required. Verify drill size specifications with manufacturer.
Finishes
Common are HASL, ENIG, and Immersion Silver. Consider component placement clearance needs.
Stackup tolerances
Aluminum layer thicknesses tend to be looser than FR-4. Check manufacturer for stackup tolerances.
Rigidity
Aluminum PCBs are more rigid so need considerations for stresses during assembly/usage.
Manufacturing Process for 4 Layer Aluminum PCBs
Aluminum Core Material – Aluminum sheets of a specific thickness are used as the core/base material. Aluminum provides good thermal and electrical conductivity.
Surface Treatment – The aluminum sheets undergo surface treatments like anodizing or chemical etching to prepare the surface for circuit material bonding.
Inner Layer Circuitization – Thin copper layers are bonded to the aluminum core using adhesive bonding. Photolithography and etching forms the inner circuit patterns.
Dielectric Layering – Thin dielectric sheets (prepreg) like fiberglass are bonded over the inner copper layers using heat and pressure lamination. This provides insulation between layers.
Outer Layer Circuitization – As with inner layers, a thin copper layer is bonded to the prepreg surface. Photolithography and etching forms the outer layer circuit pattern.
Plated Through-Holes – Holes are drilled and then plated with copper to connect inner/outer layers and for component leads. Diamond drill bits used.
Solder Mask Application – A liquid photoimageable solder mask is applied and patterned to protect the circuits and define solder/component pads.
Finishing – Final surface finishes like HASL, ENIG or immersion silver are applied before component assembly.
Testing – Various tests check for continuity, short circuits before shipping for assembly.
Precision bonding, drilling and layer registration are critical for performance of multi-layer aluminum PCBs. Tight quality controls followed during manufacture.
Thermal Management with Aluminum PCBs
Here are some key points about thermal management with aluminum PCBs:
●Aluminum has much higher thermal conductivity than FR-4 laminate boards. This allows heat to dissipate much faster through the board.
●Thermal vias should be used to draw heat away from components directly into the inner aluminum core layers and edges. The size and number of thermal vias depends on component power.
●Component placement is important to maximize heat path shortness through the aluminum and availability of thermal vias. High power parts should be closer to board edges.
●Thicker aluminum core layers provide lower thermal resistance. Core thickness is selected based on maximum predicted component temperatures.
●Thermal traces on inner or outer layers can spread heat out over a wider area before exiting through vias/edges. This reduces hotspots.
●Thermal paste or phase change pads between components and the PCB improves heat transfer at the interface.
●Heat sinks can be attached directly to the board edges or underside to dissipate heat before it builds up in the aluminum.
●Fin patterns machined into the aluminum can increase surface area for improved heat dissipation without sinks.
●Thermal simulations during design predicts temperatures and helps validate the thermal management approach.
●Extra precaution needed with exposed edge traces and components near edges to avoid condensation risks.
Proper thermal management is critical for reliability of devices using high power aluminum PCBs.
4 Layer Aluminum:Cost comparison to other PCB types
Here is a more detailed cost comparison of 4-layer aluminum PCBs versus other common 4-layer board technologies:
●4-layer FR-4: Typically the most cost effective at around $3-5 per square inch in low quantities. Tooling fees may apply for new designs.
●4-layer Aluminum: Generally costs around $8-12 per square inch due to more expensive raw aluminum versus FR-4 laminate, tighter fabrication tolerances required, and higher per board engineering fees.
●4-layer High-Frequency FR-4/PTFE: Slightly pricier than standard FR-4 at around $5-7 per square inch range due to using more expensive low-loss substrates and plating processes optimized for high speeds.
●4-layer Rigid-Flex: Adds complexity of rigid and flex circuit areas which requires extra fabrication steps like flexible tail bonding. Expect to pay $10-15 per square inch on average.
●4-layer Ceramic/AlN: Significantly higher at $25-50 per square inch or more depending on the specific ceramic/aluminum nitride substrate used. Mainly for high temp/thermal applications.
●4-layer Rigid-Flex with Components: Even more intricate process of embedding SMT components into flex areas. Can easily exceed $20-30 per square inch due to specialized tooling and process expertise needed.
So in summary, a 4-layer aluminum PCB is generally competitively priced compared to specialized board types offering similar thermal or flexibility capabilities. It represents a cost-effective balance of functionality versus more basic FR-4 or premium rigid-flex designs.
Limitations and Challenges with 4 Layer Aluminum PCBs
Tolerances – Aluminum stackup tolerances tend to be looser than FR-4 boards. Tighter DFM rules needed for layer registration and plated through-hole accuracy.
Drilling – Diamond-coated drills required to drill aluminum cause increased drill bit wear. Smaller holes and tighter aspect ratios than FR-4.
Rigidity – Aluminum boards are rigid which can cause stresses during assembly/repair work like rework. More fragile than flexible boards.
Component placement – Restricted near edges due to thermal/mechanical stresses. Need spacings from edges for heat dissipation.
Finishes – Some finishes like HASL not as durable on aluminum versus copper. Consider alternatives like immersion silver.
Trace widths – Wider traces recommended vs FR-4 to reduce high current density heating risks.
Impedance control – Skin effect can make tightly controlled impedance designs more difficult compared to FR-4.
Surface mount – Higher chance of splattering/dripping of solder during reflow onto exposed aluminum edges.
Rework – Removing/replacing components can be difficult without damaging the aluminum layers due to high thermal conductivity.
Cost – Aluminum boards generally cost more to manufacture than equivalent FR-4 layered boards.
Proper design margins/clearances, fabrication specifications with manufacturers, and acknowledging these limitations are important for reliable aluminum PCB designs.
Conclusion
4 layer aluminum PCBs present designers with an optimized solution for applications requiring rigorous thermal management. Their ability to rapidly draw heat away from components and spread it efficiently through the core prevents dangerous hotspots from developing.
While generally more expensive to manufacture than standard FR-4 boards and posing some limitations in terms of drilling and trace dimensions, aluminum PCBs open up new possibilities for product miniaturization and higher power densities thanks to their thermally superconductive substrate.
With careful consideration of fabrication tolerances, heat spreading strategies, and component placement schemes during the design phase, advanced thermal performance can be unlocked in a cost-effective multilayer PCB package. Aluminum technology therefore represents an attractive option for engineers where heat dissipation is a primary concern.