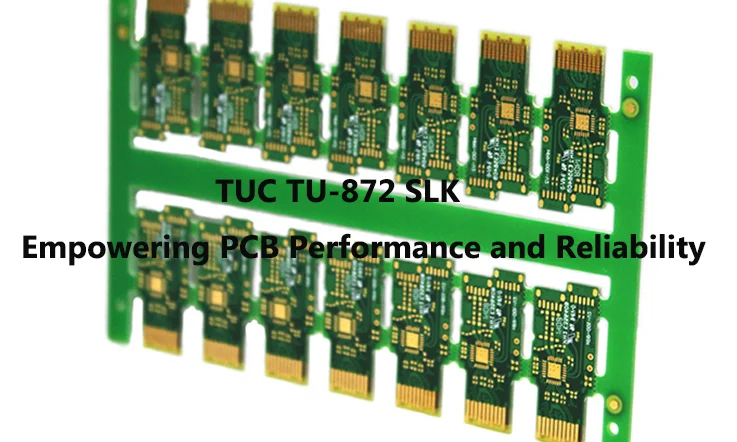
In high-frequency and high-speed PCB design, material selection directly impacts signal integrity, thermal stability, and long-term reliability. TUC TU-872 SLK stands out with low dielectric loss, excellent dimensional stability, and strong CAF resistance, making it well-suited for 5G networks, radar systems, and high-performance computing. Its consistent electrical properties and manufacturing-friendly features support HDI, multilayer, and RF applications, ensuring efficient production and dependable performance.
So, what makes TUC TU-872 SLK the go-to material for human pushing the limits of modern electronics? Buckle up, because we’re about to break it down.
Introduction to TUC TU-872 SLK – A High-Performance Laminate for Next-Gen PCBs
The demand for high-speed digital and RF PCBs has never been stronger. Whether it’s 5G networks, satellite systems, or next-gen automotive electronics, human are constantly looking for materials that support stable signal transmission, minimal loss, and reliable performance under challenging conditions.
Among the many laminate materials available, TUC TU-872 SLK has gained a solid reputation for handling high-frequency applications with ease. Its low dielectric constant (Dk) and low dissipation factor (Df) allow signals to move without interference, ensuring that performance remains consistent across a range of frequencies. But what really sets it apart? Let’s explore its standout features and how it compares to other materials in the TUC TU-872 series.
What Makes TUC TU-872 SLK Unique in High-Speed Digital and RF PCBs?
Every aspect influences high-frequency circuits. Signal integrity, heat management, and moisture resistance all affect PCB performance, and selecting the right laminate ensures the design stays within specifications. TUC TU-872 SLK is designed with these factors in mind, offering:
●Stable Signal Transmission: With its low Dk and Df, this material allows high-frequency signals to pass through without unnecessary loss or distortion. This makes it a great choice for 5G base stations, network switches, and other data-heavy applications.
●Resilience Under Heat: Some materials degrade over time when exposed to high temperatures, but TUC TU-872 SLK maintains its structure and electrical properties even in harsh operating environments.
●Minimal Moisture Absorption: In environments with fluctuating humidity, some laminates absorb moisture, leading to performance inconsistencies. This material is designed to resist that issue, ensuring stable electrical properties.
To put things into perspective, let’s look at an example: A major telecom equipment provider switched from a standard FR-4-based laminate to TUC TU-872 SLK for their high-frequency PCBs. After implementation, they observed a noticeable improvement in signal clarity, better heat dissipation, and fewer manufacturing defects. This translates to higher production efficiency and consistent end-product quality.
Comparing TUC TU-872 SLK with Other TUC Laminates (TU-872 LK, TU-872 SLK Sp)
The TUC TU-872 series includes several laminates designed for different applications. While all of them provide strong electrical performance, they each have their own strengths based on design requirements.
Here’s a side-by-side comparison of TUC TU-872 SLK, TU-872 LK, and TU-872 SLK Sp:
Feature | TUC TU-872 SLK | TUC TU-872 LK | TUC TU-872 SLK Sp |
Dielectric Constant (Dk) | Low (Optimized for High-Frequency) | Slightly Higher Than SLK | Similar to SLK |
Dissipation Factor (Df) | Low (Minimal Signal Loss) | Moderate | Low (Optimized for Extreme Speeds) |
Thermal Performance | Withstands High Temperatures | Moderate | High |
Moisture Resistance | High | Standard | High |
Best Use Cases | 5G, RF, Aerospace, Automotive Electronics | RF Circuits, Cost-Sensitive Applications | Ultra-High-Frequency Data Transmission |
If your design involves extremely high-speed data transfer, TU-872 SLK Sp might be the way to go. On the other hand, if you’re looking for a balance of cost and performance, TU-872 LK could be a solid choice. But for applications where signal clarity, thermal stability, and durability are at the top of the list, TUC TU-872 SLK is the material that consistently delivers.
Industry Applications of TUC TU-872 SLK in 5G, Aerospace, and Automotive Electronics
Many industries have embraced TUC TU-872 SLK for its ability to support high-frequency circuits without performance trade-offs. Let’s break down where this material shines:
5G Networks & Telecommunications-
●The need for faster, more reliable data transmission is pushing the limits of traditional PCB materials. TUC TU-872 SLK enables low-latency, high-speed data processing, making it well-suited for 5G base stations, network routers, and satellite communication systems.
Aerospace & Defense Electronics-
●Military radar systems, satellite communication, and avionics require PCBs that maintain stability under extreme conditions. TUC TU-872 SLK offers low-loss transmission, even in environments with high radiation and temperature fluctuations.
Automotive Electronics & ADAS (Advanced Driver Assistance Systems)-
●As vehicles integrate more AI-driven safety features, LiDAR sensors, and high-speed data connections, TUC TU-872 SLK provides the necessary electrical properties to handle these advanced systems without signal degradation.
Imagine a next-gen autonomous vehicle relying on real-time radar feedback to navigate through traffic. If the PCB material in its sensor modules doesn’t allow for stable high-frequency transmission, the entire system could become unreliable. That’s where TUC TU-872 SLK steps in—it keeps the circuits performing consistently, ensuring smooth operation without unnecessary data loss.
Core Electrical and Mechanical Properties of TUC TU-872 SLK for High-Speed Applications
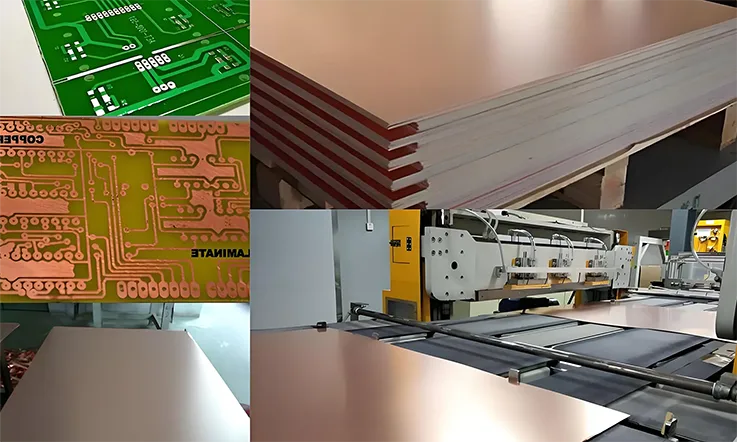
When designing high-frequency and high-speed PCBs, the choice of laminate material isn’t just about meeting baseline specs—it’s about ensuring that performance holds up under real-world conditions. Therefore, whether a PCB is being used in 5G telecom equipment, aerospace navigation systems, or next-gen automotive electronics, its material needs to support consistent signal integrity, thermal reliability, and long-term durability.
That’s where TUC TU-872 SLK steps in. This laminate is engineered to provide low signal loss, excellent thermal resistance, and strong structural integrity, making it a trusted choice for applications requiring high-speed transmission and stable electrical characteristics. Let’s take a closer look at the core properties that make this material a solid contender in high-performance PCB manufacturing.
Low Dielectric Constant (Dk) and Low Loss Tangent (Df) for Signal Integrity
High-frequency circuits demand precision. Even minor shifts in the dielectric constant (Dk) or dissipation factor (Df) can lead to signal distortion, impacting data transmission speed and clarity.
Why Does Dk and Df Matter?
The dielectric constant (Dk) determines how much a material slows down electrical signals. A higher Dk value can lead to delayed transmission, while an unstable Dk can introduce impedance mismatches, causing signal distortion. TUC TU-872 SLK is optimized for low and stable Dk, which means that signals travel with precision and reliability.
On the other hand, dissipation factor (Df) refers to the amount of energy lost as heat during signal transmission. A higher Df means more power loss, leading to weaker signals and higher operating temperatures. With its low Df, TUC TU-872 SLK allows cleaner, more efficient signal flow, making it a preferred choice for RF, microwave, and high-speed digital applications.
Comparison of Dk and Df Across Common PCB Materials-
Material | Dielectric Constant (Dk) | Dissipation Factor (Df) | Best Use Cases |
TUC TU-872 SLK | ~3.7 (Stable) | 0.005 (Low) | 5G base stations, high-speed data networks, aerospace electronics |
Standard FR-4 | 4.2–4.8 (Variable) | 0.020–0.030 (High) | General-purpose PCBs |
High-End PTFE-Based Laminate | ~2.5 (Ultra-Low) | 0.002 (Ultra-Low) | Extreme high-frequency circuits (e.g., radar, satellite systems) |
High Glass Transition Temperature (Tg) and Thermal Stability of TUC TU-872 SLK
PCB laminates don’t just need to handle signal transmission—they also need to withstand heat stress from soldering, prolonged operation, and extreme environmental conditions. The glass transition temperature (Tg) of a laminate determines at what point the material starts to soften and lose mechanical integrity. A low Tg can result in dimensional instability, leading to warping, cracking, and poor reliability over time.
How Does TUC TU-872 SLK Handle Heat?
●High Tg (~190°C): Maintains structural stability during lead-free soldering processes and high-temperature operations.
●Minimal Expansion (Low CTE): Reduces the risk of delamination and layer separation, ensuring a longer lifespan for PCBs.
●Thermal Conductivity Optimization: Helps distribute heat efficiently, preventing localized overheating.
In industries like aerospace and military electronics, where PCBs must survive rapid temperature fluctuations, having a laminate like TUC TU-872 SLK ensures that performance doesn’t degrade over time.
Thermal Performance Comparison-
Material | Glass Transition Temperature (Tg) | Coefficient of Thermal Expansion (CTE) | Best Use Cases |
TUC TU-872 SLK | ~190°C | Low | High-reliability, high-frequency applications |
FR-4 (Standard) | 130–150°C | Moderate | General electronics |
Polyimide-Based Laminate | ~250°C | Very Low | Extreme-temperature environments (space, military, oil & gas) |
If your designs require lead-free soldering, long-term thermal stability, or exposure to high operating temperatures, TUC TU-872 SLK has the resilience needed to get the job done.
Conductive Anodic Filament (CAF) Resistance and Long-Term Durability
A PCB isn’t just about signal performance and thermal resistance—it also needs to survive years of use without suffering from electrical failures. One of the most overlooked failure modes in PCB manufacturing is Conductive Anodic Filament (CAF) formation.
What Is CAF and Why Does It Matter?
CAF develops when electrochemical growth creates unintended conductive paths between nearby vias or traces within a PCB. This can result in short circuits, electrical leakage, and early board degradation—problems that pose serious risks in applications such as medical equipment, aerospace technology, and military systems.
TUC TU-872 SLK is designed to resist CAF formation, ensuring that its electrical properties remain stable even in high-humidity, high-voltage environments.
How TUC TU-872 SLK Reduces CAF Risk:
●Optimized Resin Formulation: Reduces moisture absorption, preventing internal ion migration.
●Reinforced Glass Fabric: Strengthens the internal structure, limiting conductive pathways for CAF growth.
●Controlled Impurity Levels: Lowers ionic contamination, reducing the chances of electrochemical reactions.
CAF Testing Results for TUC TU-872 SLK-
Material | CAF Resistance Test (Hours to Failure) | Humidity Exposure (85°C/85% RH) |
TUC TU-872 SLK | >1000 hours | No CAF formation detected |
Standard FR-4 | ~300–500 hours | Moderate risk of CAF |
High-Reliability Epoxy Laminate | >800 hours | Low CAF risk |
TUC TU-872 SLK in High-Speed Digital and RF/Microwave PCB Design
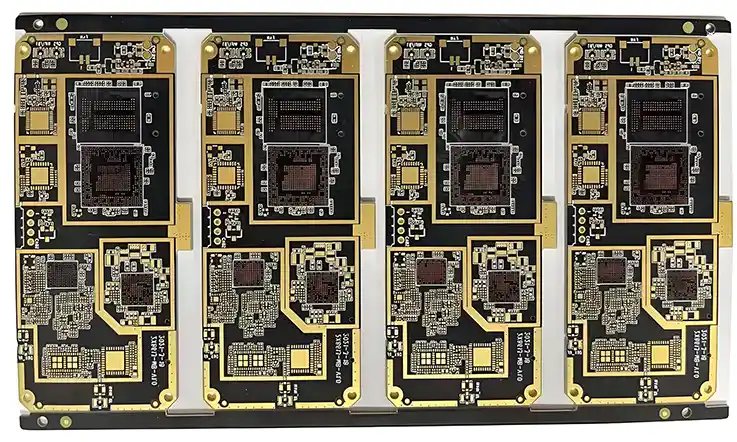
Designing high-speed digital and RF/microwave circuits isn’t just about slapping together traces and hoping for the best. At GHz frequencies, every small material inconsistency, impedance mismatch, or signal reflection can wreck performance. Engineers dealing with 5G infrastructure, radar systems, and high-speed data transmission need laminates that can handle low loss, stable dielectric properties, and reliable thermal performance.
That’s where TUC TU-872 SLK comes into play. This high-frequency laminate provides exceptional signal integrity, thermal stability, and low-loss performance, making it a solid choice for industries pushing the limits of RF, microwave, and high-speed digital design. Let’s break down how this material stacks up in demanding applications.
Why TUC TU-872 SLK Stands Out in High-Frequency PCB Designs?
At frequencies reaching into the tens of GHz, traditional PCB laminates start showing their limitations—higher signal loss, inconsistent impedance, and increased phase distortion. TUC TU-872 SLK is engineered to overcome these issues, making it a go-to material for RF and high-speed digital applications.
Key Advantages of TUC TU-872 SLK in High-Frequency PCBs:
●Stable Dielectric Constant (Dk): Ensures predictable impedance control across a wide range of frequencies.
●Low Loss Tangent (Df): Reduces signal attenuation, allowing cleaner data transmission at high speeds.
●Superior Moisture Resistance: Prevents Dk drift in humid environments, which is a major concern in RF circuits.
●Exceptional Surface Smoothness: Supports high-frequency wave propagation with minimal conductor loss.
How It Compares to Other Materials-
Laminate Type | Dielectric Constant (Dk) | Loss Tangent (Df) | Best Frequency Range | Best Applications |
TUC TU-872 SLK | ~3.7 (Stable) | 0.005 | Up to 40 GHz | 5G, Radar, Automotive ADAS |
FR-4 (Standard) | 4.2–4.8 (Variable) | 0.020–0.030 | Below 1 GHz | General PCBs |
PTFE-Based (e.g., Rogers 4000 Series) | ~2.5 | 0.002 | 40+ GHz | Satellite, High-End RF Systems |
With TUC TU-872 SLK, we can design low-loss RF circuits and GHz-speed PCBs without jumping to ultra-premium PTFE-based materials, which often come with higher costs and manufacturing challenges.
Signal Integrity Optimization with TUC TU-872 SLK in GHz-Speed Circuits
Designing high-speed circuits means keeping impedance steady, cutting down on insertion loss, and keeping crosstalk in check. TUC TU-872 SLK offers low dielectric loss and tight Dk control, helping us keep signals clean and distortion-free.
How TUC TU-872 SLK Enhances Signal Integrity-
●Consistent Impedance Matching: Ensures signals travel without unwanted reflections or losses.
●Low-Conductivity Losses: Supports higher signal fidelity over longer trace lengths.
●Controlled Resin Formulation: Prevents phase distortion, keeping data transmission accurate and reliable.
Example: 5G Base Stations
5G networks rely on millimeter-wave (mmWave) frequencies, often exceeding 28 GHz. At such high frequencies, even minor variations in PCB material properties can degrade signal clarity. TUC TU-872 SLK, with its low-loss profile, allows telecom manufacturers to build base station antennas and RF front-end modules with enhanced power efficiency and reduced heat generation.
Design Factor | Impact on 5G Performance | TUC TU-872 SLK Solution |
Signal Attenuation | Higher loss reduces signal reach | Low Df keeps losses minimal |
Thermal Stability | Heat impacts impedance stability | High Tg minimizes material drift |
Humidity Resistance | Moisture changes dielectric properties | Low moisture absorption prevents Dk shifts |
This makes TUC TU-872 SLK a practical solution for companies looking to balance cost, performance, and manufacturability in 5G PCB designs.
RF and Microwave Performance of TUC TU-872 SLK for 5G and Radar Systems
RF and microwave circuits don’t play by the same rules as standard digital PCBs. At high frequencies, PCB materials need to handle wave propagation, thermal fluctuations, and signal reflection challenges. TUC TU-872 SLK provides the low-loss dielectric properties needed for applications like:
●5G Antennas & Transceiver Modules
●Automotive Radar (24 GHz, 77 GHz, 79 GHz ADAS Sensors)
●Aerospace & Defense Radar Systems
Why Radar & 5G Systems Need Better PCB Materials?
Radar and 5G both operate at frequencies where standard PCB laminates start struggling. For example, automotive radar systems work at 76–81 GHz, which means even a slight material inconsistency can throw off signal timing.
TUC TU-872 SLK brings three major benefits to radar and telecom applications:
1.Minimal Phase Delay: Ensures signals stay accurate over long distances.
2.Low Loss Tangent: Reduces power dissipation, keeping radar signals strong.
3.Superior Surface Finish: Improves wave propagation efficiency in high-gain antenna structures.
Example: Automotive Radar PCB Design Considerations-
Factor | Impact on Radar Accuracy | TUC TU-872 SLK Benefit |
Dk Stability | Affects beam steering precision | Keeps impedance predictable |
Loss Tangent | Impacts signal reflection & strength | Reduces unwanted attenuation |
Thermal Stability | Avoids frequency shifts | High Tg ensures steady performance |
For companies developing autonomous vehicle sensor arrays or advanced military radar, choosing a low-loss, high-frequency laminate like TUC TU-872 SLK can lead to better signal processing and longer-lasting hardware.
Advanced PCB Fabrication Techniques for TUC TU-872 SLK-Based Designs
Designing with TUC TU-872 SLK isn’t just about choosing the right laminate—it’s about making sure the entire PCB fabrication process is optimized to take full advantage of its properties. Whether it’s multilayer stack-ups, HDI integration, or microvia processing, every step needs to be dialed in for precision and reliability.
This section explores the advanced fabrication techniques that we should consider when working with TUC TU-872 SLK-based PCB designs. If you’re dealing with 5G networking gear, aerospace radar systems, or next-gen automotive electronics, understanding these manufacturing principles is non-negotiable.
High-Density Interconnect (HDI) and Multilayer Stack-Up Considerations
The demand for high-speed, compact PCBs means we are constantly pushing the limits of layer count, via structures, and signal integrity. With TUC TU-872 SLK, we can leverage HDI (High-Density Interconnect) technology to create densely packed, high-performance boards.
Key Considerations for HDI Stack-Ups with TUC TU-872 SLK-
Parameter | Impact on PCB Design | TUC TU-872 SLK Advantage |
Layer Count | Higher layers increase routing density | Maintains mechanical strength with minimal warpage |
Microvia Density | More microvias improve signal routing | Compatible with laser-drilled via structures |
Impedance Control | Critical for high-speed signals | Low Dk variation ensures consistency |
Thermal Expansion | Uneven expansion leads to reliability issues | Stable Tg minimizes layer stress |
Example: HDI PCB in 5G Antenna Modules
Consider a 5G antenna PCB operating at 28 GHz. Traditional FR-4 laminates introduce excessive signal loss, making it difficult to maintain signal integrity. By using TUC TU-872 SLK, we can reduce loss, improve thermal stability, and enhance manufacturing yield.
Fine-Line Etching and Microvia Technology with TUC TU-872 SLK
When dealing with high-frequency circuits, trace widths, spacing, and via structures aren’t just minor design details—they determine whether your PCB meets performance targets or falls flat. TUC TU-872 SLK supports fine-line etching and microvia processing, enabling tighter geometries without sacrificing reliability.
Optimizing Fine-Line Traces with TUC TU-872 SLK-
●Smooth Copper Surface: Reduces conductor loss and enhances signal transmission.
●Consistent Etch Tolerance: Allows finer features without undercutting issues.
●Laser-Drilled Microvias: Supports high-density interconnect designs.
Why Microvias Matter in GHz-Speed PCBs?
Microvias—especially stacked and staggered structures—are a must for high-speed designs. Here’s how TUC TU-872 SLK enhances microvia fabrication:
Microvia Type | Best Use Cases | TUC TU-872 SLK Compatibility |
Blind Microvias | HDI PCBs, fine-pitch BGA substrates | Supports laser drilling with minimal resin recession |
Buried Microvias | High-layer count PCBs | Low CTE reduces via failure risk |
Stacked Microvias | RF & high-speed digital | Compatible with high-Tg processing |
By incorporating TUC TU-872 SLK into HDI stack-ups, we can push the envelope of miniaturization, signal integrity, and board density—all while maintaining high-yield production rates.
Laminating and Processing Guidelines for High-Reliability Manufacturing
Even the best laminate can’t fix poor processing techniques. To fully harness TUC TU-872 SLK’s capabilities, we need to fine-tune their lamination, drilling, and plating processes.
Best Practices for Lamination with TUC TU-872 SLK-
●Multistage Lamination Cycles: Helps prevent resin flow inconsistencies.
●Controlled Pressure & Temperature Profiles: Ensures uniform dielectric thickness.
●Proper Prepreg Selection: Matches resin properties for consistent bonding.
Example: Multi-Layer RF PCB Fabrication
Step | Challenge | TUC TU-872 SLK Solution |
Lamination | Uneven dielectric thickness affects impedance | Optimized flow control for uniformity |
Drilling | Glass fiber can cause hole wall damage | Smooth drill performance reduces delamination |
Copper Plating | Poor adhesion impacts via reliability | Enhanced resin-copper bonding |
Processing Considerations for Microvia & High-Speed Boards-
Drilling & Via Formation:
●Use low-impact laser drilling to prevent glass fiber pull-out.
●Optimize plasma desmear parameters to ensure resin removal without over-etching.
Copper Plating & Etching:
●Choose electroless copper solutions designed for low-Dk materials.
●Employ fine-line etching with chemical reinforcement to maintain trace precision.
With proper processing techniques, TUC TU-872 SLK-based boards can deliver high signal integrity, reliable microvia structures, and enhanced thermal stability—exactly what 5G, aerospace, and next-gen computing applications demand.
Optimizing TUC TU-872 SLK for Impedance Control and Signal Transmission
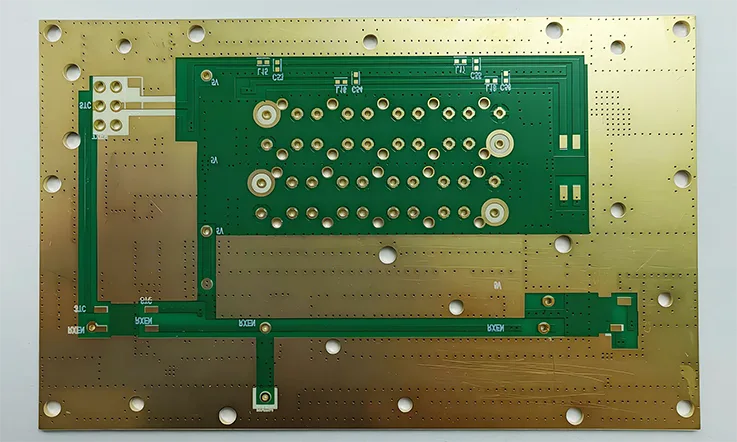
Designing high-speed and RF PCBs isn’t just about meeting specifications—it’s about achieving consistency and reliability. So, whether working on 5G infrastructure, satellite communications, or high-performance computing, keeping impedance in check and signals clear ensures the design performs as expected.
With TUC TU-872 SLK, we have access to a low-Dk, low-loss material that allows for tighter impedance tolerances and minimal signal degradation. But to fully tap into its potential, PCB layout strategies, material selection, and loss management must be dialed in with precision.
Let’s break down how to optimize PCB routing, mitigate interference, and enhance signal performance when working with TUC TU-872 SLK.
Differential Pair Routing Strategies for TUC TU-872 SLK PCBs
Differential pair routing is a go-to strategy for high-speed digital and RF circuits. It ensures signal integrity while reducing common-mode noise. But without proper spacing, width tuning, and reference plane optimization, even the best PCB materials won’t save your design from performance loss.
Best Practices for Differential Pair Routing with TUC TU-872 SLK-
Parameter | Impact on Signal Integrity | Recommended Guidelines for TUC TU-872 SLK |
Trace Width & Spacing | Controls impedance & reduces skew | Match impedance targets (e.g., 100Ω for USB 3.0) |
Length Matching | Prevents timing mismatch in signals | Keep traces within 10 mils of length difference |
Reference Plane | Ensures consistent impedance | Solid, unbroken ground plane underneath |
Via Usage | Excess vias cause reflections | Use minimal vias & back-drill where possible |
Example: PCIe Gen4 High-Speed PCB Design
A PCIe Gen4 interface runs at 16 GT/s, where even the slightest delay counts. With TUC TU-872 SLK, differential pairs can be precisely tuned to keep impedance steady while cutting down on attenuation. Tight spacing and solid grounding work together to keep noise in check and minimize skew, keeping data transmission clean even at peak speeds.
Minimizing Crosstalk and EMI Interference in High-Speed Circuits
Nothing ruins a high-speed PCB like unwanted interference. Crosstalk and electromagnetic interference (EMI) can cause data corruption, jitter, and overall performance degradation. Thankfully, TUC TU-872 SLK’s low-Dk properties and excellent insulation characteristics help mitigate these issues—but only if PCB layout follows best practices.
Techniques to Reduce Crosstalk & EMI with TUC TU-872 SLK-
●Increase spacing between aggressive and victim traces – The higher the frequency, the greater the risk of crosstalk. Use at least 3W spacing (three times the trace width) between signal lines.
●Route high-speed signals over a solid ground plane – A continuous reference plane reduces loop inductance and helps confine EMI.
●Use guard traces for extra shielding – Placing a grounded copper pour between sensitive signals can absorb stray energy and suppress interference.
●Avoid long parallel runs of high-speed signals – Parallel traces over long distances act as unintentional antennas—bad news for EMI compliance.
Example: Controlling EMI in Automotive Radar PCBs
Radar modules in autonomous vehicles rely on 77 GHz RF signals, making EMI control non-negotiable. In a TUC TU-872 SLK-based design, placing microstrip traces over a well-grounded reference layer can drastically reduce emissions, ensuring compliance with automotive EMC standards.
Insertion Loss Optimization and Material Selection for RF Applications
At microwave and mmWave frequencies, every dB of insertion loss matters. Even the best PCB layout won’t help if the wrong material choices lead to excessive signal loss. TUC TU-872 SLK is engineered for low insertion loss, but to maximize performance, we need to consider conductor surface roughness, copper type, and substrate properties.
Factors Affecting Insertion Loss in TUC TU-872 SLK-Based Designs-
Factor | Impact on Signal Transmission | Recommended Approach |
Copper Roughness | Increases conductor loss | Use smooth HVLP copper for GHz-speed designs |
Dielectric Loss (Df) | Higher Df causes greater attenuation | TUC TU-872 SLK’s low Df ensures minimal loss |
Trace Width & Thickness | Affects impedance & loss | Optimize based on GHz-frequency targets |
Substrate Thickness | Influences dielectric absorption | Choose thin cores for mmWave designs |
Example: 5G mmWave Base Station PCB Design
A 28 GHz phased-array antenna requires ultra-low-loss materials to maintain signal strength over long distances. By using TUC TU-872 SLK with HVLP copper and fine-tuned impedance matching, we can reduce insertion loss while achieving excellent signal integrity, ensuring reliable 5G performance.
Reliability and Environmental Performance of TUC TU-872 SLK PCBs
When designing high-performance printed circuit boards (PCBs), long-term stability and environmental resilience are fundamental factors to consider. TUC TU-872 SLK, engineered with high-Tg and low-Dk dielectric materials, provides not only strong electrical properties but also robust mechanical strength, thermal reliability, and humidity resistance. To ensure consistent performance across various applications, it is necessary to evaluate its thermal cycling tolerance, moisture absorption behavior, and lead-free soldering compatibility.
Thermal Cycling and Mechanical Stress Testing for Long-Term Stability
PCBs go through constant temperature shifts, moving from extreme cold to high heat. When paired with mechanical stress from soldering, assembly, and use, this can result in delamination, micro-cracks, and signal loss. Selecting materials that can handle these challenges helps maintain the integrity of multilayer designs.
Durability of TUC TU-872 SLK Under Extreme Conditions-
Test Type | Conditions | Performance of TUC TU-872 SLK |
Thermal Cycling | -55°C to 125°C, 1000 cycles | Stable dielectric constant (Dk) and dissipation factor (Df); no delamination |
Tensile Strength | Stress test at 25°C | No degradation in mechanical strength |
Vibration Test | High-stress vibration simulation | No cracks; laminated structure remains intact |
With a high Tg of 175°C and a low Z-axis expansion rate, TUC TU-872 SLK minimizes structural damage caused by repeated heating and cooling, ensuring consistent performance in demanding conditions.
Moisture Absorption Resistance and Humidity Reliability of TUC TU-872 SLK
Humidity exposure can degrade PCB performance by increasing signal loss, altering dielectric properties, and triggering Conductive Anodic Filament (CAF) effects, which may lead to electrical failures over time. Using a low-moisture-absorption laminate significantly reduces these risks, ensuring that the PCB remains stable even in high-humidity environments.
TUC TU-872 SLK’s Performance in High-Humidity Conditions-
Property | Test Standard | TUC TU-872 SLK Results |
Moisture Absorption | 50°C, 90% RH, 24 hours | 0.08% |
CAF Resistance | 85°C, 85% RH, 1000 hours | No CAF formation |
Dielectric Property Stability in Humid Environments | Relative change in Dk under high humidity | Minimal variation |
Thanks to its exceptionally low moisture absorption, TUC TU-872 SLK retains its electrical properties even in challenging climatic conditions, making it a strong candidate for long-term reliability.
RoHS and Lead-Free Soldering Compatibility in PCB Assembly
Environmental regulations mandate that PCBs comply with RoHS and REACH standards, pushing human to transition away from traditional leaded soldering methods. However, lead-free soldering requires higher reflow temperatures, which can challenge the structural integrity of PCB materials. Selecting a laminate capable of withstanding these temperatures is necessary to avoid delamination, oxidation, and mechanical failures.
TUC TU-872 SLK’s Performance in Lead-Free Soldering Processes-
●High Tg (175°C) ensures thermal resilience – withstands lead-free soldering temperatures up to 260°C without delamination issues.
●Low Z-axis expansion minimizes PTH and microvia stress – prevents cracking caused by thermal cycling.
●CAF resistance extends operational reliability – reduces risk of electrochemical migration, preventing short circuits.
Whether for high-reliability applications or large-scale production, TUC TU-872 SLK supports lead-free manufacturing while maintaining mechanical strength and electrical stability post-soldering.
Mass Production and Cost-Effective Manufacturing with TUC TU-872 SLK
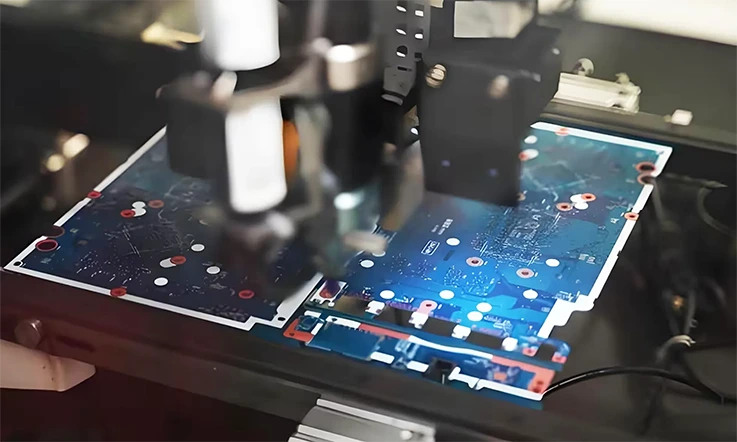
When designing PCBs for high-frequency, high-speed, and RF applications, choosing the right laminate isn’t just about electrical performance—it’s also about ensuring smooth fabrication, stable processing, and scalable production. TUC TU-872 SLK is designed to handle the demands of 5G infrastructure, radar systems, and automotive electronics, all while keeping manufacturing efficiency and cost-effectiveness in check.
For large-scale PCB production, we need to consider material consistency, automation readiness, and overall cost-performance balance. Let’s dive into how TUC TU-872 SLK stands out in high-volume manufacturing and whether it’s the right match for your fabrication needs.
Scalability of TUC TU-872 SLK for Large-Volume PCB Production
Scaling up PCB production brings unique challenges—batch-to-batch consistency, process stability, and production speed all play a role in keeping manufacturing efficient and reliable. A laminate that supports tight tolerance control, smooth processing, and high yield rates can make all the difference when producing thousands (or even millions) of boards.
How TUC TU-872 SLK Enhances Mass Production-
Factor | Why It Matters | TUC TU-872 SLK Benefit |
Batch Consistency | Ensures all boards meet design specs | Uniform Dk/Df, low moisture absorption |
Processing Stability | Reduces defects and material waste | Low Z-axis expansion, CAF resistance |
High-Speed Fabrication | Supports HDI, fine-line etching, and laser vias | Smooth drilling and layer registration |
With predictable electrical properties and strong mechanical durability, TUC TU-872 SLK supports large-scale PCB production without the usual headaches of material inconsistencies or processing challenges.
Process Automation and Quality Control in TUC TU-872 SLK Fabrication
Automation drives efficiency in modern PCB manufacturing. From laser direct imaging (LDI) to automated optical inspection (AOI), we depend on advanced tools to streamline production. A laminate compatible with automation-ready processes allows for higher throughput while minimizing defects.
Automation-Optimized Features of TUC TU-872 SLK-
●Fine-Line Imaging: The smooth surface and low-profile copper foil make precision etching and trace definition more consistent.
●Microvia Formation: Supports laser-drilled vias and stacked microvias, key for HDI and multilayer PCBs.
●Layer Alignment Stability: Ensures tight registration tolerances in complex stack-ups.
●Reliable Electrical Testing: Works well with high-speed impedance testing and AOI verification, catching issues before boards reach final assembly.
For manufacturers pushing high-speed and high-frequency designs, TUC TU-872 SLK keeps production streamlined without adding unnecessary complications.
Cost vs. Performance Analysis – Is TUC TU-872 SLK the Right Choice?
PCB material costs are only one part of the equation—processing efficiency, reliability, and long-term performance all contribute to the total cost of ownership. While TUC TU-872 SLK may have a higher initial material cost compared to standard FR-4, its processing advantages and electrical stability can translate to lower overall production costs.
Cost-Performance Breakdown-
Aspect | Standard FR-4 | TUC TU-872 SLK |
Material Cost | Lower | Higher upfront investment |
GHz-Range Signal Performance | Limited | Superior loss characteristics |
Thermal Stability | Moderate | High Tg (175°C) |
Reliability in Harsh Conditions | Average | Low moisture absorption, CAF resistance |
Production Yield | Lower in HDI and RF applications | Higher due to stable processing |
For 5G infrastructure, radar systems, and other high-speed applications, TUC TU-872 SLK offers a balanced approach to cost and performance, helping us avoid rework, performance issues, and fabrication challenges.
FAQs on TUC TU-872 SLK
1.What is the frequency range of TUC TU-872 SLK for RF applications?
It supports GHz-range signals, suitable for 5G, radar, and high-speed digital circuits.
2.How does TUC TU-872 SLK compare to PTFE-based laminates?
It offers lower processing complexity and better mechanical stability while maintaining low loss at high frequencies.
3.Can TUC TU-872 SLK be used in hybrid stack-ups?
Yes, but thermal expansion mismatches and press cycle adjustments must be considered.
4.How should raw TUC TU-872 SLK laminates be stored?
Keep in a dry, temperature-controlled area with sealed packaging to prevent moisture absorption.
Our services
TUC PCB Laminate & Materials Series