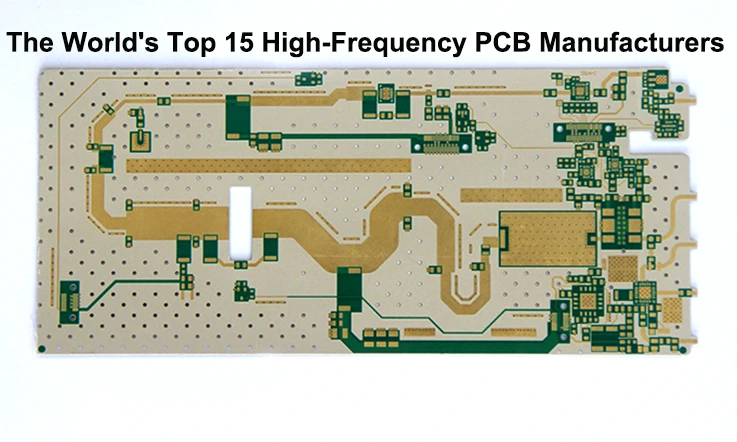
The demand for high-frequency PCB has been on the rise, driven by advancements in industries such as telecommunications, aerospace and automotive. These distinct circuit boards are engineered to manage frequencies far exceeding the capacities of regular PCB, facilitating the conveyance of signals with negligible loss and interference. This discourse introduces an exhaustive outline of the foremost 15 high-frequency PCB manufacturers globally. With their advanced technologies and comprehensive faculties, these corporations serve a key function in mapping the course of future high-frequency electronics.
1.JarnisTech
Situated in Shenzhen, China, JarnisTech leads the field in offering high-frequency PCB prototyping and mass production services, employing avant-garde fabrication methodologies and stringent testing processes. Our area of proficiency lies in fabricating sophisticated PCBs boasting up to 60 layers, exclusively fashioned for RF frequencies surpassing 10 GHz. The resultant PCBs find broad utilization across diverse applications such as mmWave antennas, radar systems, satellite communication, electronic warfare, and electronics in aerospace and defense sectors.
JarnisTech’s core capabilities encompass a variety of aspects crucial to high-frequency PCB manufacturing. They offer a comprehensive selection of PCB materials, including Rogers, Taconic, and Arlon, specifically tailored to meet the demands of microwave and mmWave frequencies. Their expertise extends to creating stackups with optimal signal-power-ground layer sequencing, ensuring optimal signal integrity and performance.
The company excels in fine line PCB fabrication, achieving impressive line and space widths as low as 2 mil, enabling the precise implementation of intricate circuitry required for high-frequency applications. JarnisTech employs laser drilling techniques to create microvias for high-density interconnect (HDI), enhancing the overall functionality and miniaturization of the PCB.
To maximize the high-frequency performance of their PCB, JarnisTech utilizes immersion silver plating, a technique known for its excellent electrical conductivity and signal transmission properties. This ensures optimal signal integrity and reliability in demanding high-frequency applications.
Beyond traditional rigid PCB, JarnisTech also specializes in the production of rigid-flex PCB, which offer enhanced flexibility and versatility for applications requiring complex form factors or space-constrained environments.
Quality is of utmost importance to JarnisTech. They employ a comprehensive 100% testing approach for both electrical functionality and overall quality assurance. This rigorous testing process ensures that each PCB meets the highest standards of performance and reliability, meeting the stringent requirements of high-frequency applications.
With their cutting-edge fabrication technologies, expertise in high-frequency PCB design and manufacturing, and unwavering commitment to quality, JarnisTech has set itself apart as a dependable collaborator for enterprises in search of dependable and high performance PCB solutions for their cutting edge applications.
2.TTM Technologies Inc
TTM Technologies Inc. is a prominent manufacturer in the realm of high-frequency PCB production, providing advanced PCB solutions to a spectrum of sectors encompassing telecommunications, aerospace, defense, and automotive. The company’s specialty lies in fabricating high-frequency and Radio Frequency (RF) PCBs, fundamental for operations that require high speed signal dissemination and robust data transmission speeds. Their impressive global footprint, high-grade merchandise, reliability in performance, and superior customer service have set TTM Technologies Inc. as an industry vanguard.
3.Nippon Mektron Ltd
Nippon Mektron Ltd., a high frequency PCB manufacturer based in Japan has been a key player in the PCB industry since its establishment in 1949. The company is known for its expertise in creating cutting edge PCBs used across sectors such as automotive, telecommunications, consumer electronics and industrial equipmemt. Their focus lies in producing density high speed and high frequency PCB with a high quality, for continuous innovation and strict quality control practices. With operations spanning manufacturing facilities worldwide Nippon Mektron ensures a seamless supply chain and prompt delivery of its products globally.
4.Unimicron Technology Corp
Unimicron Technology Corp., since beginning its operations in 1990, has escalated to be a prestigious international purveyor of superior PCB services and related solutions. By securing a pivotal role in the global market, they has grown to be one of the cornerstone PCB manufacturer in Taiwan. Unimicron presents a comprehensive suite of PCB products that encompass high-density, high-speed, and high-frequency PCB, successfully addressing the requirements of diverse verticals, such as telecommunications, automotive, consumer electronics and industrial applications.
Unimicron holds a distinguished reputation for its cutting edge manufacturing prowess, technical mastery, and unyielding dedication to quality and dependability. The corporation places substantial emphasis on research and development, incessantly driving forward to originate innovative PCB remedies that echo the progressive requirements of its clientele. With a global network of manufacturing facilities and sales offices, Unimicron ensures efficient production and delivery of its products to customers worldwide.
5.Park Electrochemical Corp
Operating on a global scale, Park Electrochemical Corp. It is a leading entity in the realm of advanced materials. They have expertise in the designing and manufacturing of high efficiency composite materials, electronic materials and cutting edge PCB materials. Melville, New York, USA serves as the global base for the corporation’s operations.
Providing a variety of PCB products and solutions for various industries,, Park Electrochemical Corp. caters to a broad spectrum of industries such as aerospace, defense, automotive, telecommunications and electronics. The advanced PCB materials they offer are meticulously engineered to stand up to the stringent demands of high frequency and high speed operations.
Under their Nelco® brand, Park Electrochemical Corp. produces high-frequency and high-speed digital materials, including laminates, prepregs, and bonding materials. These materials are used in the fabrication of multilayer PCBs for applications such as RF/microwave circuits, high-speed digital circuits, and high-frequency signal transmission.
Nelco® materials have garnered acclaim for their superior electrical properties, minimal dielectric loss, high thermal reliability and good dimensional stability. Their applications span across the telecommunications sector, aerospace and defense fields, automotive electronics, as well as other high performance electronic systems.
Park Electrochemical Corp has a strong reputation for quality and innovation in the advanced materials industry. They consistently innovate, creating novel materials and advancing technical methodologies to keep pace with the rapidly evolving requirements of the electronics sector. Especially in high frequency and high speed applications.
6.Samsung Electro-Mechanics Co. Ltd
Samsung Electro-Mechanics presents a broad spectrum of offerings, covering passive components, such as MLCCs (Multilayer Ceramic Capacitors), tantalum capacitors, inductors and filters. They also offer modules and subsystems, including camera modules, RF modules and power modules.
In the context of PCB, Samsung Electro-Mechanics is involved in the production of high quality PCB for various applications. Their PCB designs are tailored to fulfill the rigorous standards of current electronic gadgets, including those possessing high-frequency and high-speed characteristics.
Samsung Electro-Mechanics has invested heavily, in research and development to enhance their PCB manufacturing capabilities. They aim to offers PCB solutions recognized for superior performance, dependability and compactness design, to meet to the changing demands of the electronics sector.
As a subsidiary of Samsung Group, Samsung Electro-Mechanics benefits from the group’s extensive resources, technological expertise, and global presence. This allows them to deliver cutting-edge electronic components and PCB solutions to customers worldwide.
7.Tripod Technology Corp
Tripod Technology Corp also referred to as Tripod PCB is a top tier producer of PCB located in Taiwan. The company specializes in manufacturing high quality PCB to meet various industries. Like telecommunications, automotive, consumer electronics and industrial equipment.
Tripod PCB offer comprehensive range of PCB solutions, encompassing single sided, double-sided and multi-layer PCB. They are known for their expertise in manufacturing high density interconnect PCB, which are designed to accommodate complex circuitry in a smaller footprint.
Leveraging cutting edge manufacturing processes and technologies, the firm guarantees top-tier quality and dependability in their PCB products. Via stringent quality control measures and compliance with global standards, they consistently cater to the complex demands of their clients
Tripod PCB is dedicated to staying in PCB technology through constant innovation and a commitment, to research and development. They collaborate closely with their clients to deliver tailor made solutions that address their needs and preferences.
With their commitment to quality, technological expertise, and customer-centric approach, Tripod Technology Corp has established a strong reputation as a trusted PCB manufacturer in the industry. Their client base spans across the globe, laying the groundwork for sustaining partnerships with top-tier corporations in diverse sectors.
8.Compeq Manufacturing Co. Ltd
Compeq Manufacturing Co., Ltd., an esteemed manufacturer of printed circuit boards situated in Taiwan, is renowned for its specialty in fabricating high quality PCB. Their products serve industries including telecommunications, automotive, consumer electronics and medical devices among others.
Compeq provides a broad spectrum of PCB solutions encompassing single sided, double sided and multi-layer PCB. They are known for their expertise in fabricating cutting edge PCB technologies like high-density interconnect PCB, flexible PCB, and rigid flex PCB have been exceptionally recognised in the industry.
The corporation possesses an unwavering concentration on research and development, consistently powering resources into contemporary technologies and production processes to cater to the ever-transforming requisites of the electronics industry. They establish intimate collaborations with their clientele to provision tailor-made solutions, assisting them across the entire spectrum of the product development cycle.
Compeq accentuates profoundly on quality assurance and dependability. They have instituted stringent quality control methods and have garnered an array of certifications like ISO 9001, ISO 14001, IATF 16949, and UL certification. This ensures that their PCB meet the highest industry standards and comply with the strictest quality requirements.
In virtue of their sophisticated manufacturing acumen, pledge towards innovation, and unwavering commitment to client gratification, Compeq Manufacturing Co., Ltd. has sterlingly ascended to the stature of a reliable PCB manufacturer. They serve customers worldwide and have established long-term partnerships with leading companies in the electronics industry.
9.Young Poong Electronics Co. Ltd
Young Poong Electronics Co., Ltd. Originating from South Korea is a known player in the PCB manufacturing industry globally. Since its inception in 1973 the company has built a reputation as a trusted manufacturer of top notch PCB, across different sectors.
Young Poong Electronics presents an extensive array of PCB resolutions incorporating single sided, double sided and multi-layer PCB. Their expertise lies in the creation of high-density interconnect PCB, recognized for their condensed dimensions and their capacity to handle intricate circuit designs.
Young Poong Electronics exhibits a robust pledge to the principles of quality and dependability. By initiating progressive manufacturing techniques along with effective quality control systems, they ensure that their PCB are met with the finest industry norms. The company’s accreditation in ISO 9001 and ISO 14001 manifests their unwavering commitment to premier quality management and environmental responsibility.
In addition to their PCB manufacturing capabilities, Young Poong Electronics provides value-added services such as PCB assembly and testing. This allows them to offer comprehensive solutions to their customers, from PCB production to final product assembly.
Young Poong Electronics serves a wide range of industries, such as telecommunications, automotive, consumer electronics, industrial apparatus, and more. They maintain a worldwide clients base and have forged long term partnerships with prominent firms across multiple sectors.
Leveraging vast experience, a firm commitment to quality, and a focus on customer needs, Young Poong Electronics Co., Ltd. has established itself as a dependable partner in the PCB industry. Persistently driving innovation and adapting to cater to the dynamic requirements of the electronics market, they ensure delivery of advanced PCB solutions to their clients.
10.Daeduck Electronics Co. Ltd
Daeduck Electronics Co. Ltd is an enterprise, rooted in South Korea, with notable proficiency in crafting printed circuit boards and associated electronic elements. Since its inception in 1972, the organization has blossomed into becoming one of the premier global frontrunners in the PCB manufacturing sphere.
Daeduck Electronics furnishes a broad selection of PCB commodities, encompassing single layer, double layer and multi layer PCB boards, in addition to high-density interconnect boards. These PCB find their application across a diverse range of sectors including telecommunications, automotive, consumer electronics and industrial applications.
Daeduck Electronics bears a well-earned reputation for its superior manufacturing abilities, robust technological proficiency, and an unwavering commitment to quality and trustworthiness. The company heavily invests in research and development, perpetually assimilating new technologies and groundbreaking solutions as a part of its endeavor to cater to the continually shifting requirements of its clients.
Having production units stationed in South Korea, China, Vietnam and Mexico, Daeduck Electronics ensures efficient manufacturing processes and global dispersion of its offerings. The organization also has a robust customer support system, offering technical aid and customizable services to cater to unique client specifications.
11.Probe Test Solutions
Probe Test Solutions is a leading provider of cutting-edge probe card technologies and high-frequency PCB solutions tailored specifically for 5G communications, satellite RF testing, and aerospace/defense test applications.
Their core capabilities reside in the development and fabrication of high-frequency materials, inclusive of PTFE composites, for optimum effectiveness in strenuous conditions.
Additionally, They specialize in millimeter wave antenna in package solutions, facilitating efficient and reliable communication in advanced wireless networks. Simultaneously, they provide bespoke probe cards, explicitly fashioned for rigorous IC testing procedures.
12.AT&S
Based in Leoben, Austria, AT&S takes the lead as Europe’s grandest high-frequency PCB producer, serving diverse industries such as automotive, industrial, medical, and aerospace. Their wide-ranging proficiency enables them to excel in crafting sophisticated PCBs, such as HDI, multilayer, and rigid-flex boards, skillfully designed to function at frequencies surpassing 100 GHz.
AT&S provides an assortment of materials for their PCB production, encompassing PTFE, ceramic, and polyimide-based substrates. These PCB base materials are meticulously chosen to cater to the distinct prerequisites of high-frequency operations, therefore guaranteeing maximum efficiency and dependability.
The company excels in the production of HDI structures, incorporating 3 um vias/lines. This allows for the precise implementation of complex circuitry, enabling high-density interconnects and miniaturization of the PCBs. AT&S also provides specialized stackup designs tailored for mmWave applications, ensuring optimal signal integrity and performance in demanding high-frequency environments.
AT&S employs cutting-edge laser drilling methodologies and backplane technology to deliver the zenith of accuracy and functionality in their PCBs. Laser drilling facilitates the formation of microvias, promoting the incorporation of complex circuitry and boosting the holistic performance of the PCB.
AT&S utilizes several testing techonolies to ensure the quality and reliability of their PCBs. Such techonolies encompass automated optical inspection (AOI), microsectioning, and electrical scrutiny. These rigorous testing routines affirm the soundness of the PCBs and validate their adherence to the stringent industry benchmarks.
AT&S provide a frictionless progression from prototype design to bulk fabrication, facilitating their clientele to bring their high-frequency PCB designs to the market with efficiency. Their manufacturing presence is worldwide, permitting them to cater to global customers with unwavering quality and punctual distribution.
Being the most sizable high-frequency PCB producer in Europe, AT&S has cemented a strong reputation in delivering pioneering solutions to fields like automotive, industrial, medical and aerospace. Their expertise, commitment to quality, and global manufacturing capabilities make them out as a reliable partner for businesses aiming to find dependable and superior performance PCB solutions for their sophisticated applications.
13.Elec & Eltek
Being based in Taiwan, Elec & Eltek excels in fabrication custom high-frequency PCB specifically designed for communication infrastructure applications. These include platforms such as 5G antennas, base stations, small cells, and satellite communications. They provide an extensive array of sophisticated PCB solutions including HDI and RF boards, all engineered to cater to the stringent demands of such applications.
Elec & Eltek’s core capabilities encompass the utilization of key laminates such as Rogers RO4003C, RO4835, and Taconic RF-60A. These laminates are carefully selected for their superior performance characteristics in high-frequency applications, ensuring optimal signal integrity and reliability.
The company’s PCBs are designed to support frequencies up to 76 GHz, making them suitable for a wide range of high-speed communication applications. Elec & Eltek employs advanced technological techniques, including fractional microvia in pad technology, enabling the precise implementation of intricate circuitry and maximizing signal transmission efficiency.
Elec & Eltek offers a variety of copper options, ranging from 1oz to 2oz, on high TG (glass transition temperature) substrates. This allows for enhanced thermal management and improved signal integrity, ensuring the reliable operation of the PCBs in demanding high-frequency environments.
To meet the requirements of fine pitch components, Elec & Eltek utilizes the ENIG (Electroless Nickel Immersion Gold) surface finish. This surface finish provides excellent solderability, corrosion resistance, and flatness, ensuring reliable connections and optimal performance of the components.
Elec & Eltek critically focuses on the characterization and testing of RF. They utilize strict testing methods to authenticate the efficiency and dependability of their high-frequency PCBs. This paramount procedure ensures that their products comply with the rigid requirements typically seen in communication infrastructure applications.
Elec & Eltek provides an integrated manufacturing flow, from the initial prototyping phase all the way to mass production. This enables their clients to transition their high-frequency PCB designs to the marketplace in a highly efficient manner. They have the expertise and capacity to support projects of varying scales, ensuring consistent quality and timely delivery.
Elec & Eltek, with their niche skill set in high-frequency PCB for communication infrastructure applications, has positioned themselves as a dependable supplier in the field. Their tenacity towards innovative technologies, meticulous quality assessments, and relentless pursuit of customer satisfaction establish them as a perfect ally for businesses seeking solid and proficient PCB solutions for their communication infrastructure endeavors.
14.San Francisco Circuits
San Francisco Circuits, based in the San Francisco Bay Area in California is a leading innovator in creating cutting edge RF, microwave and millimeter wave PCB tailored for communication infrastructure and aerospace/defense purposes. They specialize in manufacturing high frequency PCB that can function at frequencies reaching, up to 90 GHz.
San Francisco Circuits leverages a selection of high-performance materials, such as PTFE, quartz and hydrocarbon ceramic substrates. These materials are meticulously selected for their outstanding electrical properties, which permit the trustworthy delivery of high-frequency signals with nominal loss and disruption.
The company specializes in the design and fabrication of multi layer PCB, integrating RF, digital and mixed-signal circuitry. This methodology is an impeccable combination of a myriad of components and functionalities, boosting the performance capability and practicality of the PCBs in intricate applications.
San Francisco Circuits utilizes progressive modeling and signal integrity examination methods to guarantee the best performance of their high-frequency PCB. These techniques allow them to detect and neutralize potential signal integrity complications, including impedance mismatches and crosstalk. Resulting in improved signal quality and overall system performance.
To ensure reliable connections and protect exposed pads, San Francisco Circuits employs the ENIG (Electroless Nickel Immersion Gold) surface finish. This surface finish provides excellent solderability, corrosion resistance, and durability, enhancing the longevity and performance of the PCB.
Via stubs can introduce unwanted signal reflections and impedance variations in high-frequency PCBs. San Francisco Circuits employs via stub elimination techniques to minimize these effects, ensuring consistent signal transmission and impedance characteristics throughout the PCB.
San Francisco Circuits strongly values quality and dependability in their products. They conduct comprehensive electrical evaluations on their high-frequency PCB, confirming their functionality and compliance with exact requirements. This strict testing protocol ensures that only PCB of superior quality and reliability are sent out to their esteemed clientele.
With their focus on low to mid volume production, San Francisco Circuits offers flexible manufacturing solutions for various project sizes. Their expertise, combined with their commitment to quality and customer satisfaction, makes them a trusted partner for companies seeking advanced high-frequency PCB for communications infrastructure and aerospace/defense applications.
15.Cicor Group
Centrally located in Boudry, Switzerland, Cicor Group is a distinguished purveyor of advanced PCB and microelectronics resolutions. Their clientele spans multiple sectors inclusive of aerospace, defense, medical, and industrial automation. With an undeniable expertise in offering top-tier PCB technologies, Cicor Group is uniquely equipped to serve high-frequency application requirements.
The Cicor Group lays out a host of services tailored to address the particular demands of their clients. Their mastery stretches to RF designs carried out on materials like Rogers RO4003, renowned for their superior electrical performance and compatibility with high-frequency uses. This enables Cicor Group to provide reliable and high-performance PCB solutions for industries where signal integrity and frequency response are critical.
Besides RF design, Cicor Group shines in fabricating multilayer and HDI (High-Density Interconnect) circuit boards. These progressive PCB technologies enable intricate circuit integration and paves the way for high-density packing, which invariably enhances the functionality and simultaneously shrinks the size of electronic apparatuses.
Cicor Group also offers flex and rigid-flex PCB solutions, providing flexibility in design and enabling the creation of compact and flexible electronic systems. Their expertise in this area allows them to meet the demands of industries where space constraints and flexibility are key considerations.
The company is well-versed in advanced assembly techniques on ceramic substrates, enabling the integration of microelectronics and high-frequency components. This notable feature finds high merit in sectors like aerospace and defense, medical and industrial automation, wherein unwavering reliability and robust performance under rigorous conditions are paramount.
Cicor Group maintains clean room facilities for assembly and testing, ensuring the highest level of cleanliness and quality control during the manufacturing process. This enables them to meet the stringent requirements of industries where contamination can have a significant impact on product performance and reliability.
From prototyping to medium volume production, Cicor Group offers comprehensive manufacturing services, allowing their customers to seamlessly transition from initial designs to full-scale production. Their ability to support projects of varying scales ensures efficient and reliable delivery of high-quality PCB and microelectronics solutions.
With their commitment to excellence and their comprehensive competence, the Cicor Group has setup a strong reputation of being a dependable collaborator for sectors in need of complex PCB and microelectronic remedies. Their focus on high-frequency applications, combined with their expertise in various industry sectors, positions them as a reliable provider of advanced electronic solutions to meet the evolving needs of aerospace, defense, medical and industrial automation industries.
Selecting a High-Frequency PCB Manufacturer: Key Considerations
When selecting a PCB manufacturer for high-frequency applications, it is important to consider the following factors:
1.Frequency Range:
Ensure that the manufacturer has experience and capabilities in supporting the desired frequency range, especially for applications involving mmWave boards exceeding 10 GHz.
2.Materials Expertise:
Seek out manufacturers that exhibit proficiency and established experience in handling high-frequency materials, including Rogers and Taconic substrates. This specific domain knowledge is of utmost importance in enhancing signal performance and minimizing possible losses.
3.HDI Capabilities:
Check whether the manufacturer provides High-Density Interconnect (HDI) technology featuring microvias and refined attributes. The inclusion of such technology promotes proficient routing and mitigates signal encroachment, thus becoming indispensable for high-frequency undertakings.
4.Stack up Experience:
Choose a manufacturer with expertise in designing optimal layer stacks that effectively separate digital and RF signals, minimizing cross-talk and maximizing performance.
5.Design Services:
Ensure that the manufacturer provides comprehensive design support, from schematic to fabrication, to help optimize the layout and ensure signal integrity in high-frequency applications.
6.Modeling and Analysis:
Look for manufacturers who offer simulation capabilities to accurately model and analyze signal integrity, power integrity, impedance, and electromagnetic interference (EMI) issues. This helps identify and address potential problems early in the design process.
7.Quality Systems:
Consider manufacturers with certifications like IPC, ISO, and AS9100, as they demonstrate a commitment to disciplined quality processes and reliable manufacturing practices.
8.Testing Capabilities:
Check if the manufacturer offer a range of electrical, RF, and functional tests to ensure the quality and performance of the high-frequency PCB.
9.Prototyping Abilities:
Evaluate the manufacturer’s capabilities in both low-volume prototyping and volume production. This ensures that they can support your needs throughout the product development cycle.
10.Applications Experience:
Look for manufacturers with specific expertise in the application area of your product, such as radars or 5G. This ensures that they understand the unique requirements and challenges of your industry.
11.Cost Effectiveness:
Consider the manufacturer’s pricing competitiveness while ensuring that it aligns with their strong technical capabilities. Balancing cost with quality is crucial to achieve a successful high-frequency PCB manufacturing partnership.
Frequently Asked Questions
Q:How Testing for High Frequency PCB?
A:Electrical Testing for High Frequency PCB: Insertion Loss, VSWR, Time Domain Reflectometry, Impedance and RF Functionality
Q:What are Challenges in Manufacturing High Frequency PCB?
A:Signal Integrity, Impedance Control, Thermal Management, PCB Distortion and Reliability.
Q:What are Fabrication Processes for High Frequency PCB?
A:Laser Drilling, Photolithography, Sequential Lamination, Controlled Impedance Traces, SI Analysis, and Modeling.
Q: What Are Supported Frequency Range of High Frequency PCB?
A:Operating Range of High Frequency PCB: From Microwave Bands (3-30 GHz) to mmWave Frequencies (>30 GHz).
Q: What are Key Materials Utilized in High Frequency PCBs Fabrication?
A:Prominent Materials for High Frequency PCB: PTFE Composites (e.g., Rogers 4000, Taconic RF Materials, Arlon), Isola Astra, and Ceramics (e.g., Aluminum Nitride).
Conclusion
With the ever-increasing demand for high frequency PCBs, the leading 15 manufacturers worldwide hold a pivotal role in fulfilling industry needs.. Through their technologies, deep expertise and unwavering dedication to quality these companies are driving innovation and exploring new frontiers in high frequency electronics.
Be it for communication infrastructure, aerospace endeavours, or medical apparatus, these corporations serve as trusted partners for sectors in need of trusted and efficacious high-frequency PCB solutions. As the torchbearers of technology’s evolution, these companies will undoubtedly remain at the forefront, shaping the future of high-frequency electronics and enabling the next generation of advanced applications.