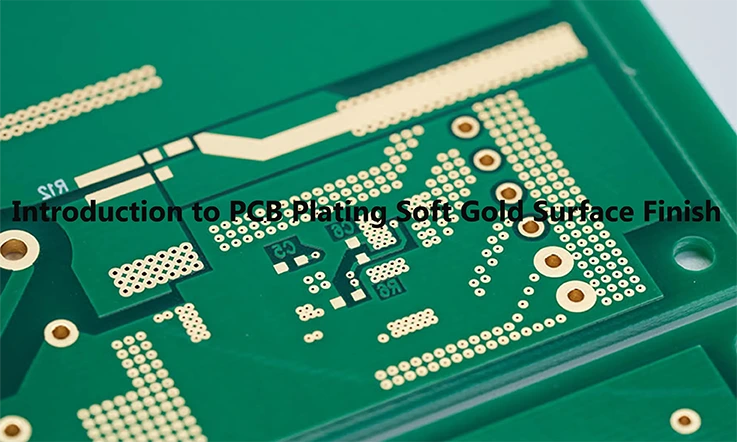
PCB plating plays a crucial role in ensuring the performance, reliability, and longevity of electronic circuits. One of the widely used surface finishes is the soft gold plating, known for its exceptional solderability, conductivity, and corrosion resistance. As circuit board engineers, understanding the benefits and considerations of soft gold surface finish is vital in selecting the most suitable surface for various applications.
In this article, we will delve into the intricacies of PCB plating soft gold surface finish, exploring its advantages, comparisons with other finishes, potential challenges, and methods for assessing its quality. By gaining insights into the unique characteristics of soft gold plating, engineers can make informed decisions and optimize their designs to meet the demanding requirements of modern electronic devices.
Overview of Soft Gold PCB Surface Finish
Soft gold PCB surface finish is a type of plating used on printed circuit boards (PCBs) to provide a protective and conductive surface. Soft gold, also known as pure gold or fine gold, is a thin layer of gold deposited onto the surface of the PCB.
The soft gold plating process involves immersing the PCB in a solution containing gold ions, and then applying an electric current to facilitate the deposition of gold onto the exposed copper surfaces. The resulting soft gold layer provides a reliable and durable surface for electrical conductivity, solderability, and corrosion resistance.
Properties and Characteristics of Soft Gold Surface Finish
Soft gold surface finish, or pure gold surface finish, possesses several properties and characteristics that make it suitable for various applications in the electronics industry. Some of these properties include:
Thickness: Soft gold surface finish is typically applied as a thin layer, generally ranging from 1 to 5 microinches (0.025 to 0.127 micrometers) in thickness. The precise thickness can be tailored to meet specific requirements.
Conductivity: Soft gold is an excellent conductor of electricity. It offers low electrical resistance, ensuring reliable signal transmission and minimizing signal loss or degradation.
Solderability: Soft gold surface finish provides excellent solderability, enabling reliable and robust solder joints during PCB assembly processes. The gold layer promotes good wetting and bonding with solder, facilitating a strong and durable connection.
Corrosion Resistance: Gold is highly resistant to corrosion, making soft gold surface finish well-suited for applications exposed to harsh environmental conditions or corrosive agents. It provides a protective barrier against oxidation and tarnish, ensuring long-term reliability and performance.
Shelf Life: Soft gold surface finish has good shelf life, meaning it retains its solderability and quality over extended storage periods. This property is advantageous for manufacturers who may need to store PCBs for a certain duration before final assembly.
Wear Resistance: Although relatively soft compared to other surface finishes, soft gold still exhibits a measure of wear resistance. It can withstand normal handling and use without significant degradation, making it suitable for moderate-duty applications.
Aesthetics: Soft gold has an attractive, golden appearance, providing an aesthetically pleasing finish to the PCB surface. This can be particularly important for applications where visual appeal is desired.
It’s worth noting that soft gold surface finish may have specific limitations or considerations. For instance, its softness can lead to increased wear and tear in high-cycle applications or during contact mating and demating. Additionally, soft gold may not be ideal for certain extreme high-temperature applications or in environments with very aggressive chemicals.
Overall, the properties and characteristics of soft gold surface finish make it widely utilized in industries requiring reliable electrical connections, excellent solderability, corrosion resistance, and appealing aesthetics.
Benefits and Advantages of Soft Gold PCB Surface Finish
Soft gold PCB surface finish offers several benefits and advantages, making it a popular choice for various applications in the electronics industry. Some of the key benefits include:
Excellent Solderability: Soft gold surface finish provides excellent solderability, ensuring reliable and robust solder joints during PCB assembly processes. The gold layer promotes good wetting and bonding with solder, facilitating strong and durable connections.
High Conductivity: Soft gold is an excellent conductor of electricity. It offers low electrical resistance, enabling efficient and reliable signal transmission without significant loss or degradation.
Corrosion Resistance: Gold is highly resistant to corrosion, making soft gold surface finish well-suited for applications exposed to harsh environments or corrosive agents. It provides a protective barrier against oxidation and tarnish, ensuring long-term reliability and performance.
Good Shelf Life: Soft gold surface finish has a good shelf life, meaning it retains its solderability and quality over extended storage periods. This property is advantageous for manufacturers who may need to store PCBs for a certain duration before final assembly.
Compatibility: Soft gold surface finish is compatible with a wide range of components, including fine-pitch devices and components with small pads. Its relatively soft nature helps minimize pad damage during soldering, making it suitable for delicate components.
Appealing Aesthetics: Soft gold has an attractive, golden appearance, providing an aesthetically pleasing finish to the PCB surface. This can be particularly important for applications where visual appeal or high-end branding is desired.
RoHS Compliance: Soft gold surface finish can be formulated to meet RoHS (Restriction of Hazardous Substances) compliance requirements, ensuring environmental friendliness and compliance with industry regulations.
Reliability: Soft gold PCB surface finish offers excellent reliability, making it suitable for critical applications that require long-term performance and durability.
It’s important to note that soft gold surface finish may have specific limitations or considerations, such as its relatively soft nature that can result in increased wear and tear over time, especially in high-cycle applications. Additionally, the cost of soft gold surface finish can be higher compared to other surface finishes.
Methods for Assessing and Verifying Soft Gold Plating Quality
Assessing and verifying the quality of soft gold plating can be done through various methods and techniques. Here are some common methods used for this purpose:
Visual Inspection:
Visual inspection involves examining the soft gold-plated surface visually to assess the overall quality. This includes checking for uniformity, smoothness, and any visible defects such as discoloration, pitting, or roughness. A trained inspector examines the plating under proper lighting conditions to identify any anomalies or deviations from the desired quality standards.
Thickness Measurement:
The thickness of the soft gold plating can be measured using non-destructive techniques such as X-ray fluorescence (XRF) or eddy current testing. These methods can determine the plating thickness accurately, ensuring it falls within the specified range. Measuring the thickness provides insight into the plating’s quality and adherence to the required specifications.
Microscopic Analysis:
Microscopic analysis is performed using techniques like scanning electron microscopy (SEM) or optical microscopy. These methods allow for a detailed examination of the soft gold plating’s surface and interface with the substrate. Microscopic analysis aids in identifying issues like nodules, cracks, voids, and adhesion problems that may affect the plating quality.
Adhesion Testing:
Adhesion testing is conducted to assess how well the soft gold plating adheres to the substrate. Various testing methods can be used, such as tape adhesion tests, scratch tests, or pull tests. These tests evaluate the strength of the bond between the plating and the substrate, ensuring its durability and resistance to detachment or delamination.
Solderability Testing:
Solderability testing involves assessing the ability of the soft gold-plated surface to wet and bond with solder. This is typically done by performing solderability tests, such as solder dip or solder joint assessments. The solderability testing helps verify that the soft gold plating provides good solder wetting and facilitates reliable solder joints.
Corrosion Resistance Testing:
Corrosion resistance testing assesses the plating’s ability to withstand corrosion and oxidation over time. Techniques such as salt spray testing or humidity testing can be employed to simulate harsh environmental conditions. These tests evaluate whether the soft gold plating maintains its protective properties and resists degradation when exposed to corrosive agents.
Electrical Testing:
Electrical testing can be performed to verify the conductivity and electrical performance of the soft gold plating. This may involve measuring the electrical resistance or impedance of the plated traces or evaluating the plating’s impact on signal integrity, particularly for high-frequency applications.
Plating Techniques and Processes
There are several plating techniques and processes used in various industries for different applications. Here are some commonly used plating techniques:
Electroplating:
Electroplating is the most common plating technique. It involves the deposition of a metal onto a substrate using an electrolyte solution and an electric current. The substrate to be plated, known as the cathode, is connected to the negative terminal (cathode) of a power source, while the metal to be plated is connected to the positive terminal (anode). The metal ions in the electrolyte solution are reduced at the cathode, forming a metal layer on the substrate.
Electroless Plating:
Electroless plating, also known as autocatalytic plating, does not require an external electric current. Instead, it relies on a chemical reduction process to deposit a metal layer onto the substrate. The plating solution contains a reducing agent that spontaneously reduces metal ions on the substrate surface. This technique is commonly used for uniform plating on complex shapes or non-conductive substrates.
Electroless Nickel Plating:
Electroless nickel plating is an electroless plating process that deposits a layer of nickel-phosphorus alloy onto a substrate. It utilizes a reducing agent and a metal salt solution containing nickel ions. The reducing agent triggers the autocatalytic reaction, depositing the nickel-phosphorus layer onto the substrate. Electroless nickel plating offers excellent corrosion resistance, wear resistance, and solderability.
Immersion Plating:
Immersion plating involves immersing the substrate in a solution containing metal ions, allowing a chemical reaction to take place resulting in the deposition of a metal layer onto the substrate. Immersion plating is a simple and cost-effective technique but generally provides thinner and less controlled plating thickness compared to other methods.
Electrochemical Plating:
Electrochemical plating, also known as electrodeposition, is a broad term encompassing various plating processes that involve the use of an electric current. It includes techniques such as electroplating, electroforming, and electrochemical deposition. These processes rely on applying an electrical current to drive the metal deposition onto the substrate.
Vapor Deposition:
Vapor deposition techniques, such as physical vapor deposition (PVD) and chemical vapor deposition (CVD), involve depositing a thin film onto the substrate through a vaporized source material. PVD techniques use physical mechanisms like evaporation or sputtering, while CVD techniques rely on chemical reactions to deposit the material onto the substrate.
Overall, The choice of plating technique depends on several factors, including the desired metal layer, substrate material, complexity of the part, cost considerations, and the desired properties of the plated layer. Each technique has its advantages and limitations, and the selection is made based on the specific application requirements.
Comparison With Other Surface Finishes
Soft gold PCB surface finish can be compared with other common surface finishes used in the electronics industry. Here’s a comparison with a few popular surface finishes:
Electroless Nickel Immersion Gold (ENIG):
●Soft Gold: Soft gold offers excellent solderability and conductivity. It has a thin gold layer, providing good corrosion resistance. However, it is relatively soft and may experience wear over time.
●ENIG: ENIG offers good solderability, corrosion resistance, and a robust gold layer over a layer of nickel. It offers a durable surface finish, but the nickel layer can affect high-frequency performance. ENIG is widely used in various applications but can be more expensive compared to soft gold.
Hot Air Solder Leveling (HASL):
●Soft Gold: Soft gold has better solderability than HASL as it forms a direct gold-to-solder bond. It offers good conductivity and corrosion resistance. However, it is not suitable for applications with high-temperature requirements.
●HASL: HASL provides a thicker solder layer, making it suitable for high-power applications. However, it may have uneven surface topography, which can pose challenges for fine-pitch components. HASL is a cost-effective option but has limitations in terms of high-frequency performance and lead-free requirements.
Organic Solderability Preservative (OSP):
●Soft Gold: Soft gold offers superior corrosion resistance compared to OSP. It provides a more durable surface finish and better long-term reliability. It also offers better solderability.
●OSP: OSP is a cost-effective option and environmentally friendly. It provides a flat surface, suitable for fine-pitch components. OSP, however, has limited shelf life and can be affected by humidity or handling during the assembly process.
Immersion Tin (ISn):
●Soft Gold: Soft gold offers higher solderability and conductivity compared to immersion tin. It has better corrosion resistance and long-term reliability. It is often used in high-reliability applications.
●ISn: Immersion tin provides a flat and solderable surface. It is suitable for fine-pitch components but is generally less durable than soft gold. It may require protective measures against corrosion and oxidation.
Ultimately, the choice of surface finish depends on the specific requirements of the application, such as solderability, conductivity, corrosion resistance, cost, and high-frequency performance. Soft gold offers excellent solderability and conductivity with good corrosion resistance, making it a preferred option for applications that demand reliable electrical connections, long-term reliability, and appealing aesthetics.
Potential Challenges and Limitations of Soft Gold Plating
While soft gold plating offers several advantages, it also has some potential challenges and limitations. Here are a few worth considering:
Softness and Wear: Soft gold is relatively softer compared to other surface finishes. This softness makes it more prone to wear, especially in applications with repeated insertions and removals of connectors or components. Over time, the soft gold layer may experience mechanical damage, resulting in diminished contact reliability.
Cost: Soft gold plating tends to be more expensive compared to some other surface finishes. The higher cost can make it less economically viable for certain budget-sensitive projects or applications.
High-Temperature Limitations: Soft gold plating has limited resistance to high temperatures. In applications where exposure to elevated temperatures is expected, such as during reflow soldering processes, soft gold may experience degradation or formation of intermetallic compounds, compromising the performance of the surface finish.
Limited Availability: Soft gold may not be as widely available or offered by all PCB manufacturers or suppliers. This limited availability might restrict its usage or make sourcing more challenging in some cases.
Environmental Considerations: Like other gold-based surface finishes, soft gold plating involves the use of gold, which is a precious and finite resource. The environmental impact associated with gold mining and processing should be taken into account when considering the choice of soft gold as a surface finish.
Compatibility with Certain Materials: Soft gold plating may not be compatible with certain materials or processes. For instance, certain flux formulations or chemicals used in specific manufacturing processes may adversely affect the soft gold layer, leading to degradation or performance issues.
High-Frequency Performance: Soft gold plating may not offer the same high-frequency performance as some other surface finishes, such as electroless nickel immersion gold (ENIG). For applications requiring optimal signal integrity at high frequencies, alternative surface finishes might be preferred.
It’s important to carefully evaluate the specific requirements, operational conditions, and constraints of the application when considering soft gold plating as a surface finish option. Alternative surface finishes may be better suited depending on the specific needs of the project.
Summary
The world of electronic circuits continues to evolve at a rapid pace, calling for surface finishes that can meet the ever-increasing demands of performance, reliability, and miniaturization. Soft gold plating, with its remarkable solderability, conductivity, and corrosion resistance, emerges as a powerful solution to address these challenges.
By embracing soft gold surface finish in PCB plating, circuit board engineers have the opportunity to elevate the quality and functionality of their designs. Aesthetically pleasing, highly conductive, and corrosion-resistant, soft gold plating empowers engineers to develop cutting-edge electronic devices that excel in both form and function.
In conclusion, soft gold surface finish stands as a testament to the relentless pursuit of excellence in the realm of electronic circuits. As the world of technology continues to advance, unlocking the potential of soft gold plating opens new doors for innovation, reliability, and unparalleled performance in the field of PCB engineering. By harnessing the benefits of this surface finish, engineers can shape the future of electronic devices, ushering in an era of enhanced connectivity, efficiency, and user experience.