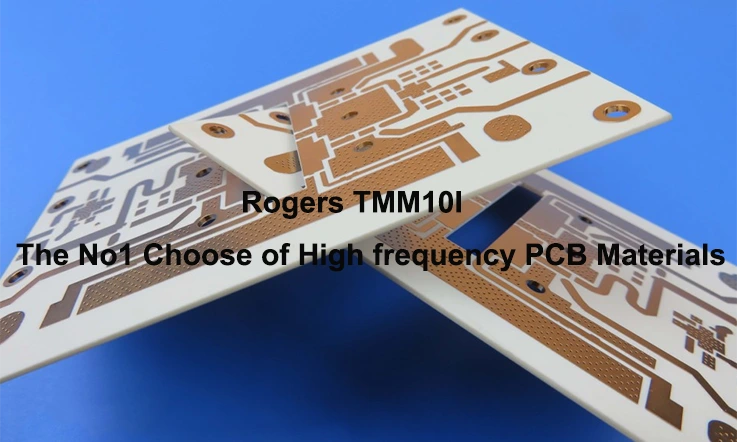
As an electrical manufacturer, ensuring optimal performance and reliability of your products is of utmost importance. In the fast-paced world of electronics, where high-frequency applications are becoming increasingly prevalent, selecting the right PCB materials is critical. Rogers TMM10I PCB materials offer a range of desirable properties that can significantly enhance electrical performance and meet the demanding requirements of modern electronic designs.
Introduction of Rogers TMM
TMM® thermoset microwave materials encompass a range of ceramic, hydrocarbon, and thermoset polymer composites specifically engineered for applications requiring high plated-thru-hole reliability in stripline and microstrip configurations. These TMM laminates offer a diverse selection of dielectric constants and claddings.
The unique electrical and mechanical properties of TMM laminates combine the advantages of ceramic and traditional PTFE microwave circuit laminates, without necessitating the utilization of specialized production techniques commonly associated with these materials. Unlike other laminates, TMM laminates do not require a sodium napthanate treatment before undergoing electroless plating.
Notably, TMM laminates exhibit an exceptionally low thermal coefficient of dielectric constant, typically measuring less than 30 ppm/°C. Furthermore, the material’s isotropic coefficients of thermal expansion closely match those of copper, enabling the production of highly reliable plated through holes and minimizing etch shrinkage. Additionally, the thermal conductivity of TMM laminates is approximately twice that of conventional PTFE/ceramic laminates, facilitating efficient heat dissipation.
As TMM laminates are based on thermoset resins, they do not soften when subjected to heat. This characteristic ensures that wire bonding of component leads to circuit traces can be performed without concerns of pad lifting or substrate deformation.
Combining desirable features of ceramic substrates with the ease of soft substrate processing techniques, TMM laminates provide a versatile solution. They can be clad with electrodeposited copper foil ranging from 1/2 oz/ft2 to 2 oz/ft2 or directly bonded to brass or aluminum plates. Substrate thicknesses between 0.015″ and 0.500″ are available. Moreover, the base substrate of TMM laminates exhibits resistance to etchants and solvents commonly used in printed circuit production. As a result, all standard printed wiring board (PWB) processes can be employed to manufacture TMM thermoset microwave materials.
What Is Rogers TMM10I?
Rogers TMM10I is a type of microwave material that belongs to the TMM® series. It is characterized by having an isotropic dielectric constant (Dk), which means that its Dk value remains consistent regardless of the orientation of the material. This property is advantageous for applications requiring uniform electrical performance in multiple directions.
Similar to other materials in the TMM® series, TMM10I offers a combination of desirable features found in ceramic and PTFE substrates. These features include high performance in microwave applications, excellent electrical properties, and mechanical stability. Additionally, TMM10I allows for the utilization of soft substrate processing techniques, which simplifies the manufacturing process and provides greater flexibility in circuit design and fabrication.
Features Rogers TMM10I PCB Laminates?
Rogers TMM10I PCB laminates offer several notable features:
1. Dielectric Constant (Dk): TMM10I has a dielectric constant of 9.80 +/- .245. This parameter determines the electrical properties of the material and affects signal propagation in the PCB.
2. Dissipation Factor: TMM10I exhibits a low dissipation factor of .0020 at 10GHz. The dissipation factor measures the energy loss in the material and influences the signal integrity and attenuation in high-frequency applications.
3. Thermal Coefficient of Dk: TMM10I has a thermal coefficient of Dk of -43 ppm/°K. This property indicates how the dielectric constant of the material changes with temperature. The negative coefficient ensures stability and minimizes variations in electrical performance over a wide temperature range.
4. Coefficient of Thermal Expansion (CTE): The CTE of TMM10I is carefully matched to copper. This characteristic ensures that the material expands and contracts at a similar rate as copper when exposed to temperature changes. This matching helps maintain the integrity of plated through holes and reduces the risk of mechanical stress and failure.
5. Thickness Range: TMM10I is available in a thickness range of .0015 to .500 inches with a tolerance of +/- .0015”. This variability in thickness allows for flexibility in designing PCBs with different layer stackups and meets the requirements of a wide range of applications.
Therefore, Rogers TMM10I PCB laminates offer a consistent dielectric constant, low dissipation factor, stable thermal behavior, and a range of thickness options. These features make TMM10I suitable for high-frequency applications that demand reliable electrical performance and dimensional stability.
Benefits of TMM10I PCB Materials
TMM10I PCB materials provide several benefits that contribute to their suitability for various applications:
1.Creep and Cold Flow Resistance:
TMM10I exhibits excellent mechanical properties, including resistance to creep and cold flow. These characteristics ensure that the material maintains its dimensional stability over time, even under high-stress conditions. As a result, TMM10I PCBs can withstand mechanical loads and maintain their structural integrity.
2.Chemical Resistance:
TMM10I is resistant to process chemicals commonly used during fabrication, such as etchants and solvents. This resistance minimizes the risk of damage or degradation of the material during the PCB manufacturing process, ensuring consistent performance and reliability.
3.Elimination of Sodium Napthanate Treatment:
Unlike some other materials, TMM10I does not require a sodium napthanate treatment prior to electroless plating. This simplifies the manufacturing process by eliminating an additional step, reducing production time and costs.
4.Thermoset Resin Base:
TMM10I is based on a thermoset resin. This characteristic ensures that the material does not soften or deform when exposed to heat. Consequently, reliable wire bonding of component leads to circuit traces can be performed without concerns of pad lifting or substrate deformation, enabling robust and consistent wire-bonding processes.
Compare with Other High Frequency PCB Materials
When comparing TMM10I PCB materials with other high-frequency PCB materials, several factors come into play. Here’s a comparison with some commonly used materials:
1. Rogers RO4000® Series: The RO4000 series (e.g., RO4350B, RO4003C) from Rogers Corporation is another popular choice for high-frequency applications. Both TMM10I and RO4000 series offer excellent electrical properties, low dissipation factor, and consistent dielectric constant. However, TMM10I exhibits a slightly lower dielectric constant (Dk of 9.80) compared to the RO4000 series (typically Dk of 3.38 to 6.15). The choice between the two would depend on specific design requirements, such as the desired Dk value and mechanical properties.
2. Isola FR-4: FR-4 is a widely used PCB material known for its affordability and versatility. Compared to FR-4, TMM10I offers superior electrical performance, including lower loss tangent and dissipation factor, making it more suitable for high-frequency applications. TMM10I also provides better dimensional stability and resistance to chemicals, which are important factors in demanding environments.
3. Teflon (PTFE): PTFE-based materials, such as Rogers RT/duroid® and Taconic TLY, are known for their excellent electrical properties and low loss characteristics. While TMM10I shares some similarities with PTFE materials, it offers advantages such as improved mechanical stability, resistance to creep and cold flow, and compatibility with soft substrate processing techniques. PTFE materials, on the other hand, excel in their lower dielectric constant options and higher temperature durability.
4. Arlon AD series: Arlon’s AD series, like TMM10I, is designed for high-frequency applications. Both materials offer low dissipation factors and stable electrical performance. However, TMM10I provides better mechanical stability and resistance to process chemicals, making it a favorable choice for applications requiring long-term reliability and ease of fabrication.
Ultimately, the choice of PCB material depends on specific application requirements, including electrical performance, mechanical stability, thermal management, cost considerations, and manufacturing constraints. Conducting a thorough evaluation of the material’s properties and considering the specific needs of the project will help determine the most suitable high-frequency PCB material.
What Factor Consider When Choose TMM10I In PCB Design?
When choosing TMM10I PCB material for a design, several factors should be considered:
1. Frequency and Signal Integrity: TMM10I is specifically designed for high-frequency applications. Consider the frequency range of your design and ensure that TMM10I’s electrical properties, such as its low dissipation factor and stable dielectric constant, meet the requirements for maintaining signal integrity and minimizing losses.
2. Dielectric Constant (Dk): TMM10I has a dielectric constant of 9.80 +/- .245. Evaluate whether this Dk value is suitable for your design’s impedance matching, transmission line characteristics, and desired electrical performance. Ensure that the Dk value aligns with the target impedance and frequency requirements of your circuit.
3. Mechanical Stability: TMM10I offers excellent mechanical stability, resisting creep and cold flow. Consider the mechanical requirements of your design, such as the need for dimensional stability, load-bearing capacity, and resistance to deformation or warping. This is particularly important in applications with high operating temperatures or mechanical stress.
4. Thermal Management: Evaluate the thermal characteristics of TMM10I in relation to your design’s requirements. Consider the material’s thermal coefficient of Dk (-43 ppm/°K) and its compatibility with your thermal management strategy, including heat dissipation, thermal expansion matching with other components, and the ability to withstand temperature variations.
5. Manufacturing Process and Compatibility: TMM10I offers the advantage of soft substrate processing techniques, simplifying manufacturing and providing flexibility in circuit design. Consider the specific fabrication processes involved in your project and assess whether TMM10I aligns with your manufacturing capabilities and requirements.
6. Chemical Resistance: TMM10I is resistant to process chemicals commonly used during PCB fabrication. Evaluate whether the material’s chemical resistance aligns with the specific chemicals and processes involved in your manufacturing environment.
7. Thickness and Layer Stackup: TMM10I is available in a thickness range of .0015 to .500 inches. Consider the required thickness for your design and ensure that TMM10I’s available thickness options meet your needs. Evaluate the material’s compatibility with the desired layer stackup and any specific design constraints.
8. Cost Considerations: Assess the cost of TMM10I PCB material in relation to your project budget. Consider the value it provides in terms of electrical performance, mechanical stability, and manufacturing efficiency.
By considering these factors, you can make an informed decision regarding the suitability of TMM10I PCB material for your specific design requirements.
Some Typical Applications of TMM10I
TMM10I PCB materials find application in various industries and systems that require high-performance RF and microwave circuitry. Some typical applications of TMM10I include:
1. RF and Microwave Circuitry: TMM10I is well-suited for use in RF and microwave circuits, where its excellent electrical properties, low dissipation factor, and consistent dielectric constant contribute to optimal signal integrity and transmission.
2. Power Amplifiers and Combiners: TMM10I is used in power amplifiers and combiners, which are integral components in systems that require high-power RF signal amplification and combining.
3. Filters and Couplers: TMM10I is employed in the fabrication of filters and couplers used for frequency selection, signal separation, and power distribution in RF and microwave systems.
4. Satellite Communication Systems: TMM10I is utilized in satellite communication systems, including satellite transceivers and antennas, to ensure reliable signal transmission and reception in space-based applications.
5. Global Positioning Systems (GPS) Antennas: TMM10I is well-suited for GPS antenna applications, where its high dielectric constant stability, low dissipation factor, and mechanical properties contribute to precise and accurate positioning capabilities.
6. Patch Antennas: TMM10I is used in the construction of patch antennas, which are widely used in wireless communication systems, including Wi-Fi, Bluetooth, and cellular networks.
7. Dielectric Polarizers and Lenses: TMM10I can be employed in the fabrication of dielectric polarizers and lenses used in optical systems, where its electrical and mechanical properties facilitate efficient light manipulation and transmission.
8. Chip Testers: TMM10I is utilized in the construction of chip testers, which are used to evaluate the performance and functionality of semiconductor devices and integrated circuits.
Overview, TMM10I finds application in a wide range of systems and devices, including RF and microwave circuitry, power amplifiers, filters, satellite communication systems, GPS antennas, patch antennas, dielectric polarizers, lenses, and chip testers. Its excellent electrical properties and mechanical stability make it a reliable choice for demanding applications in the field of electronics.
In Conclusion
Rogers TMM10I PCB materials provide electrical manufacturers with a reliable and high-performance solution for their high-frequency applications. With its excellent electrical properties, mechanical stability, chemical resistance, and compatibility with manufacturing processes, TMM10I enables the creation of robust and efficient electronic products. By choosing TMM10I, manufacturers can ensure superior signal integrity, reduced losses, and enhanced overall performance, ultimately leading to customer satisfaction and success in today’s competitive market. Embrace the power of Rogers TMM10I PCB materials and take your electrical designs to new heights of excellence.
Our services
Rogers PCB Laminates & Series