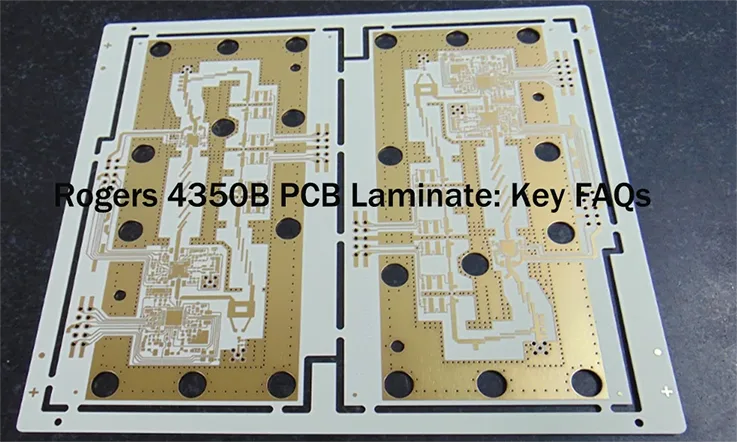
Rogers 4350B is a high frequency laminated material that is widely used in the fabrication of printed circuit boards (PCBs). This material is known for its excellent electrical properties and can maintain these properties over a wide range of frequencies. This guide will answer some of the most frequently asked questions about Rogers 4350b PCBs.
What is a Rogers 4350B PCB?
Rogers 4350B PCB is a printed circuit board made from Rogers 4350B material, a high-frequency laminated material developed by Rogers Corporation. It’s a hydrocarbon ceramic material designed for electronic circuits that operate at microwave frequencies.
What Are the Properties of Rogers 4350B?
Rogers 4350B possesses several unique properties that make it ideal for high-frequency applications:
● Relative Dielectric Constant: 3.48
● Loss Tangent: 0.0037 at 10 GHz
● Z-axis Thermal Coefficient of Expansion: 32 ppm/°C
● Decomposition Temperature: 390°C
● Moisture Absorption: 0.06%
● Volume Resistivity: >10^7 megohms
How Can You Verify The Performance Of Rogers RO4350B?
To verify the performance of Rogers 4350B, several methods and tests can be employed. Here are some common approaches to assess and validate the performance of Rogers 4350B PCBs:
Electrical Testing: Various electrical tests can be conducted to evaluate the performance of Rogers 4350B PCBs. These tests include signal integrity analysis, impedance measurements, insertion loss and return loss measurements, and power handling capabilities. By measuring these electrical parameters, the performance characteristics of the PCB can be assessed.
High-Frequency Testing: Rogers 4350B is often used in high-frequency applications, and specialized high-frequency testing can be performed to assess its performance. This testing may involve measuring S-parameters, which characterize the behavior of the PCB at different frequencies. S-parameters can provide insights into transmission line losses, signal reflections, and impedance matching.
Thermal Analysis: Rogers 4350B exhibits good thermal stability, and thermal analysis can be conducted to evaluate its performance under different temperature conditions. This analysis may involve thermal cycling tests, thermal shock tests, or thermal conductivity measurements to assess the PCB’s ability to dissipate heat and maintain its electrical properties.
Mechanical Testing: Mechanical testing helps evaluate the structural integrity and durability of Rogers 4350B PCBs. Tests such as bend testing, flex testing, and vibration testing can be performed to assess the PCB’s mechanical strength, resistance to mechanical stress, and its ability to withstand environmental conditions.
Environmental Testing: Environmental testing involves subjecting the PCB to various environmental conditions to evaluate its performance and reliability. These tests may include temperature and humidity cycling tests, salt spray tests, and accelerated aging tests. Environmental testing helps assess the PCB’s performance under different climatic and operating conditions.
Compliance Testing: Rogers 4350B PCBs must meet industry standards and specifications. Compliance testing ensures that the PCBs adhere to these standards. Common compliance tests include UL certification for flame retardancy, RoHS compliance for environmental regulations, and IPC standards for quality and reliability.
It is worth noting that the specific testing methods and parameters may vary depending on the application and requirements of the Rogers 4350B PCB. It is advisable to consult with the manufacturer’s recommendations and industry standards to determine the appropriate tests and procedures for verifying the performance of Rogers 4350B in your specific application.
What Are the Applications of Rogers 4350B PCBs?
Rogers 4350B PCBs are used in a variety of high-frequency applications:
● Microwave and RF applications
● Antennas
● Power amplifiers
● Cellular base station antennas
● Direct broadcast satellites
● Automotive radar and sensors
What Are the Advantages of Using Rogers 4350B PCBs?
High Frequency Performance: Rogers 4350B maintains its electrical properties over a wide range of frequencies, making it ideal for high-speed designs.
Thermal Stability: Rogers 4350B is stable at high temperatures and has a low coefficient of thermal expansion.
Low Moisture Absorption: Its low rate of moisture absorption makes it suitable for use in a wide range of environments.
Mechanical Strength: Rogers 4350B has excellent mechanical properties, which makes it a durable choice for PCBs.
Differences Between Rogers 4350B and FR-4
Rogers 4350B and FR-4 are two different types of substrates commonly used in printed circuit boards (PCBs). Here are the key differences between them:
Material Composition: Rogers 4350B is a specialized high-frequency laminate material, whereas FR-4 is a widely used general-purpose flame-retardant epoxy laminate. Rogers 4350B is designed specifically for high-frequency applications, while FR-4 is a more versatile material used in a wide range of electronic devices.
Dielectric Constant (Dk): Rogers 4350B has a lower dielectric constant compared to FR-4. The dielectric constant is a measure of a material’s ability to store electrical energy in an electric field. A lower Dk in Rogers 4350B means it provides better signal integrity and lower signal loss at high frequencies compared to FR-4.
Loss Tangent (Dissipation Factor): Rogers 4350B has a lower loss tangent compared to FR-4. The loss tangent represents the amount of energy lost as heat during the transmission of an electrical signal. A lower loss tangent indicates reduced signal loss and better performance at high frequencies.
Thermal Stability: Rogers 4350B exhibits better thermal stability compared to FR-4. It has a higher glass transition temperature (Tg), which means it can withstand higher temperatures without significant degradation of its electrical and mechanical properties. FR-4 has a lower Tg, limiting its suitability for high-temperature applications.
Cost: FR-4 is generally more cost-effective compared to Rogers 4350B. FR-4 is widely available and widely used, making it more affordable due to economies of scale. Rogers 4350B, being a specialized high-frequency material, is typically more expensive.
Applications: Rogers 4350B is commonly used in high-frequency PCB designs, such as RF/microwave circuits, cellular base stations, aerospace applications, and high-speed digital applications. FR-4 is suitable for a wide range of applications, including consumer electronics, automotive electronics, industrial controls, and general-purpose PCB designs.
It’s important to note that the choice between Rogers 4350B and FR-4 depends on the specific requirements of the PCB design, such as the operating frequency, signal integrity needs, thermal considerations, and budget constraints. Designers need to carefully evaluate these factors to select the most appropriate substrate for their application.
Key Differences Between Rogers 4350B and 4003C
Rogers 4350B and Rogers 4003C are two different types of high-frequency laminates manufactured by Rogers Corporation. Here are the key differences between them:
Material Composition: Rogers 4350B and 4003C are made from different materials. Rogers 4350B is an organic-based, glass-reinforced hydrocarbon laminate, while Rogers 4003C is a ceramic-filled hydrocarbon laminate. The ceramic fillers in Rogers 4003C provide it with different electrical and mechanical properties compared to Rogers 4350B.
Dielectric Constant (Dk): The dielectric constant is a measure of a material’s ability to store electrical energy. Rogers 4350B has a higher dielectric constant (Dk) compared to Rogers 4003C. The exact values of Dk may vary depending on the specific grade or thickness of the material chosen, but generally, Rogers 4350B has a Dk of around 3.48, while Rogers 4003C has a lower Dk of around 3.38. This means that Rogers 4350B provides slightly higher signal propagation speed compared to Rogers 4003C.
Loss Tangent (Dissipation Factor): The loss tangent represents the amount of energy lost as heat during the transmission of an electrical signal. Rogers 4350B has a lower loss tangent compared to Rogers 4003C. A lower loss tangent indicates reduced signal loss and better performance at high frequencies. The exact values of the loss tangent may vary depending on the specific grade or thickness of the material chosen.
Thermal Stability: Rogers 4003C exhibits better thermal stability compared to Rogers 4350B. It has a higher glass transition temperature (Tg), which means it can withstand higher temperatures without significant degradation of its electrical and mechanical properties. Rogers 4350B has a lower Tg compared to Rogers 4003C.
Applications: Both Rogers 4350B and 4003C are commonly used in high-frequency PCB designs, such as RF/microwave circuits, cellular base stations, aerospace applications, and high-speed digital applications. However, the specific choice between the two will depend on the design requirements and trade-offs. For example, Rogers 4350B may be preferred in applications where a higher dielectric constant is desired, while Rogers 4003C may be suitable for designs that require better thermal stability and a slightly lower dielectric constant.
It’s important to consult the datasheets and specifications provided by Rogers Corporation to obtain precise information on the electrical, mechanical, and thermal properties of Rogers 4350B and 4003C, as well as their suitability for specific applications.
Rogers 4350B vs Panasonic Megtron 6: Key Differences
Rogers 4350B and Panasonic Megtron 6 are two popular materials used in the manufacturing of high-frequency printed circuit boards (PCBs). While both materials offer excellent performance, there are some key differences between them:
Composition: Rogers 4350B is a thermoset laminate composed of woven glass reinforced hydrocarbon/ceramic material, which provides good electrical and mechanical properties. On the other hand, Panasonic Megtron 6 is an advanced epoxy-based laminate with woven glass fabric reinforcement and modified epoxy resin. The specific composition of each material contributes to its unique performance characteristics.
Dielectric Constant: Dielectric constant (Dk) is a crucial parameter for high-frequency applications. Rogers 4350B typically has a lower Dk of around 3.66, which enables efficient signal propagation and reduced signal loss. Panasonic Megtron 6, on the other hand, has a higher Dk ranging from 4.3 to 4.5. The choice between the two depends on the specific requirements of the application.
Loss Tangent: The dissipation factor, also known as the loss tangent (Df), indicates the energy loss in the material. Rogers 4350B generally has a lower Df, contributing to lower signal loss and improved performance in high-frequency circuits. Panasonic Megtron 6 has a slightly higher Df compared to Rogers 4350B, but still offers good performance for high-frequency applications.
Thermal Properties: Both materials exhibit good thermal stability, but there are differences in their glass transition temperature (Tg) and coefficient of thermal expansion (CTE). Rogers 4350B has a higher Tg of around 280°C, providing better dimensional stability at elevated temperatures. Panasonic Megtron 6 has a slightly lower Tg of around 170-180°C but offers a lower CTE, which can be advantageous in applications where thermal expansion needs to be minimized.
Manufacturing Considerations: Rogers 4350B is known for its ease of handling during PCB fabrication and assembly processes. It does not require special through-hole treatments and is generally considered user-friendly. Panasonic Megtron 6, while still manageable, may require extra care during processing due to its higher resin content and potential for resin smear.
It’s important to consider the specific requirements of your application, including frequency range, signal integrity, thermal management, cost, and manufacturing considerations when choosing between Rogers 4350B and Panasonic Megtron 6. Consulting with PCB manufacturers and considering their recommendations based on your specific needs can help you make an informed decision.
What Are the Challenges in Manufacturing Rogers 4350B PCBs?
Cost: Rogers 4350B is more expensive than conventional FR-4 material, which can increase overall PCB production costs.
Manufacturing Complexity: Due to its unique properties, Rogers 4350B requires specialized handling and processing during PCB manufacturing.
Availability: Not all PCB manufacturers have the capability to work with Rogers 4350B, which can limit options when sourcing PCB production.
Therefore, Rogers 4350B is a high-performance PCB material that’s ideal for high-frequency applications. However, its use may increase costs and complicate the manufacturing process, so it’s important to work with a PCB manufacturer with experience in handling Rogers 4350B.
Rogers PCB Production Guidelines
RO4350B high-frequency circuit materials have been developed to offer comparable high-frequency performance to woven PTFE glass substrates, simplifying fabrication with epoxy/glass laminates. RO4350 is a thermoset material filled with hydrocarbon/glass reinforced ceramic, exhibiting an exceptionally high glass transition temperature (TG > 280 °C). Unlike PTFE-based microwave materials, it does not require any special treatment or vias. Consequently, the processing and assembly costs of RO4350 material circuits are comparable to those of epoxy/glass laminates.
Here are some fundamental guidelines for handling double-sided RO4350B boards. Generally, the parameters and treatment methods employed for epoxy/glass boards can be applied to RO4350 boards.
Input/Output Rogers PCB Material:
The input and output materials should be flat and rigid to minimize copper burrs. Recommended input materials include aluminum and rigid composite panels with thicknesses ranging from 0.254 to 0.635 mm. Most conventional starting materials, with or without an aluminum coating, are suitable.
Maximum Drilling Depth:
The thickness of the material to be drilled should not exceed 70% of the depth of the groove. This measurement includes the thickness of the input material and penetration into the substrate.
Drilling:
It is advisable to avoid surface speeds exceeding 500 SFM and chip loads below 0.05 mm (0.002″) whenever possible to ensure optimal results during drilling processes.
Why Choose Rogers RO4350B PCB Laminate
Rogers PCB laminates are engineered to meet specific custom requirements, with key features such as dielectric constant, materials, dissipation factor, glass transition temperature (Tg), coefficient of thermal expansion, and shear strength being crucial for selecting the best Rogers PCB laminate.
Among the highly competitive range of Rogers PCB laminates, Rogers 4350B PCB laminates stand out as a dependable choice. These laminates are designed to be compatible with high-frequency signals, making them suitable for various applications.
One notable advantage of Rogers 4350B PCB laminates is their lower dielectric constant of 3.66, coupled with a reduced dielectric thickness of 0.066. This combination allows for efficient signal propagation and improved performance in high-frequency circuits.
Furthermore, Rogers 4350B PCB laminates exhibit a low coefficient of thermal expansion (CTE), minimizing the risk of material distortion and ensuring dimensional stability across temperature variations. These laminates eliminate the need for through-hole treatments and can be utilized in high-power radio frequency applications, making them versatile and reliable.
In contrast to other Rogers PCB laminates or PTFE-based laminates, Rogers 4350B PCB laminates are known for their ease of handling, offering convenience during the manufacturing and assembly processes.
Affordability, coupled with significant flexibility, has been instrumental in driving the popularity of Rogers 4350B PCB laminates. These laminates provide cost-effective solutions without compromising on performance or reliability.
As a result, Rogers 4350B PCB laminates offer an optimal balance of high-frequency compatibility, low dielectric constant, reduced dielectric thickness, excellent thermal stability, ease of handling, and cost-effectiveness. These qualities have made Rogers 4350B PCB laminates a preferred choice in the competitive landscape of PCB materials.
Choosing the Best Rogers 4350B PCB Manufacturer
Selecting the best manufacturer for Rogers 4350B PCBs requires careful consideration of several important factors. To ensure a successful decision, it is crucial to assess the following properties:
Compliance with UL 94 Standards: The chosen manufacturer should utilize materials that adhere to UL 94 standards, which verify the flame retardation properties of plastics. A manufacturer capable of achieving UL 94 V-0 rating offers excellent flame retardancy.
Sufficient Raw Material Storage: A reliable manufacturer should maintain an adequate inventory of raw materials. Sufficient storage ensures a consistent and efficient fabrication process, allowing for fast turnaround times and optimal product quality.
Affordable Pricing: While quality is important, it is equally crucial to find a manufacturer that offers competitive and affordable pricing. This ensures cost-effectiveness without compromising on the quality of the final product.
Performance Verification: A reputable manufacturer should subject their Rogers 4350B PCBs to trusted performance tests such as in-circuit tests, automated optical inspection tests, and X-ray inspection tests. These tests validate the reliability and functionality of the PCBs.
Extensive Manufacturing Experience: Look for a manufacturer with a proven track record and substantial experience in Rogers 4350B PCB manufacturing. A wealth of experience demonstrates their expertise and ability to deliver high-quality products.
Diverse Project Portfolio: A manufacturer with a broad range of projects showcases their versatility and adaptability. It indicates their capability to handle various design requirements and complexities effectively.
Certification by Trusted Standards: Manufacturing facilities certified by recognized standards such as ISO-9001, ISO-14001, RoHS, and others demonstrate the manufacturer’s commitment to quality, environmental responsibility, and compliance with industry regulations.
24/7 Technical Support: Access to round-the-clock technical support is crucial for prompt assistance and issue resolution. A manufacturer that offers continuous technical support ensures a smooth and uninterrupted manufacturing process.
If you are seeking a reliable manufacturer for Rogers 4350B PCBs, we invite you to contact us. With over a decade of experience in assembly and manufacturing services, we possess the necessary certifications, including ISO-9001, ISO-14001, RoHS, and more, guaranteeing our commitment to quality and compliance. We are dedicated to providing exceptional service and support to meet your specific requirements.
Final Thoughts
Rogers 4350B PCB has emerged as an exceptionally efficient and high-performance choice for electric circuits. It boasts the ability to deliver maximum output in various applications. Throughout our discussion, we have endeavored to address all inquiries pertaining to RO4350B PCB, ensuring clarity and simplicity in our explanations.
We trust that our comprehensive coverage has equipped you with the necessary knowledge to select the optimal Rogers PCB for your specific needs. However, should you encounter any further queries or require assistance in identifying the most compatible Rogers 4350B PCB, we encourage you to reach out to us. Our team is readily available to provide prompt and reliable support, ensuring your satisfaction.
Our services
Rogers PCB Laminates & Series