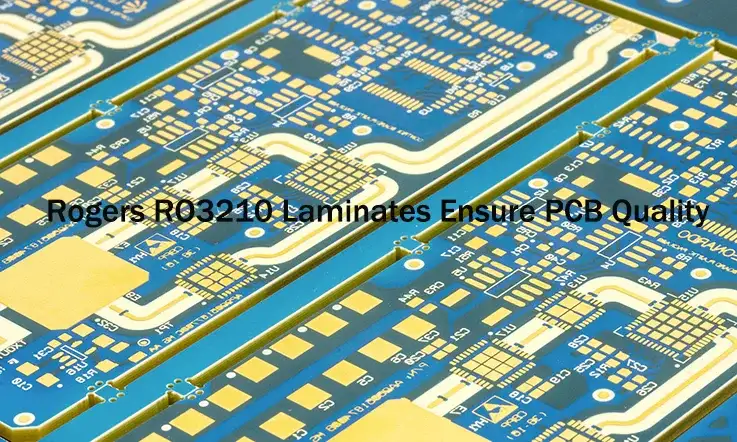
Are you considering improving the efficiency of your circuit to enable higher frequency operation? Or are you seeking enhanced thermal stability for the printed circuit boards in your sensitive devices? Rest assured, we have the perfect solution for you: Rogers 3210. Our extensive research has allowed us to compile a comprehensive guide that addresses common questions regarding the type, material, and applications of Rogers 3210. Without further ado, let’s delve into the details.
What Is Rogers 3210 PCB?
Rogers 3210 is a specialized type of printed circuit board (PCB) that utilizes a ceramic-filled laminate for its inner base. Unlike standard PCBs, Rogers PCB 3210 does not incorporate integrated fiberglass on the inner side. Instead, the circuit laminates are filled with woven fiberglass to enhance efficiency and current flow.
Rogers PCBs, particularly those from the 3000 series, are well-known for their compatibility with high-frequency circuit materials. The inclusion of Rogers 3210 in electric circuits significantly improves thermal and electrical conductivity. Moreover, these PCBs possess a unique dielectric constant value, ensuring high thermal stability.
The consistent dielectric constant value of Rogers PCB 3210 addresses the limitations often found in PTFE substrates used in base materials. Additionally, these PCBs exhibit low water absorption, making them suitable for high-humidity applications.
The primary purpose of incorporating Rogers PCB 3210 in electrical circuits is to enhance the mechanical stability and electrical performance of integrated components. Among the 3000 series options, Rogers PCB 3210 stands out by offering exceptional mechanical stability at competitive prices.
The Composition of Rogers 3210 Material
Rogers 3210 is a specialized printed circuit board (PCB) material that is composed of several key components. The materials used in the construction of Rogers 3210 PCBs typically include:
Reinforcement: Rogers 3210 PCBs commonly feature a reinforcement layer, which provides structural integrity and stability to the PCB. This reinforcement layer is typically made of woven glass fabric or non-woven aramid fiber material.
Resin System: The resin system used in Rogers 3210 PCBs is typically a blend of epoxy or phenolic resin combined with a curing agent. This resin system helps bind the reinforcement material together and provides electrical insulation.
Ceramic Filler: Rogers 3210 PCBs incorporate ceramic fillers, usually composed of a high-purity alumina or silica, to enhance the electrical properties and thermal conductivity of the material. These fillers improve the dielectric properties and overall performance of the PCB.
Copper Foil: Copper foil is utilized as the conductive layer on Rogers 3210 PCBs. It provides the necessary pathways for electrical current flow and facilitates the soldering of components onto the PCB surface. The copper foil used is typically high-quality, with specific thicknesses and surface treatments to meet the requirements of high-frequency applications.
Adhesive: An adhesive layer is often present to bond the copper foil to the core material of the PCB. This adhesive layer ensures the mechanical integrity of the copper traces and enhances the overall stability of the PCB.
These materials are carefully selected and combined to achieve the desired electrical, thermal, and mechanical properties of Rogers 3210 PCBs. The specific formulation and composition may vary among manufacturers, but the overall goal is to create a high-performance PCB material suitable for applications requiring excellent signal integrity and thermal management.
Why Use Rogers 3210 Laminate?
There are several compelling reasons why you should consider using RO3210 laminate for your high-frequency circuitry:
High Electrical Performance: RO3210 offers excellent electrical properties, including a high dielectric constant (Dk) of 10.2 ± 0.2. This high Dk allows for efficient signal transmission, making it ideal for high-frequency applications where signal integrity is crucial.
Low Loss: The laminate’s low dissipation factor (Df) of 0.0023 ensures minimal signal loss, resulting in improved overall circuit performance. Low loss is particularly important in high-frequency designs to minimize attenuation and maintain signal integrity.
Dimensional Stability: RO3210 exhibits good dimensional stability, meaning it retains its shape and size even under varying temperature and environmental conditions. This stability ensures consistent electrical performance over time, making it reliable for long-term applications.
Thermoset-Based Material: Being a thermoset-based laminate, RO3210 offers excellent thermal stability. It can handle high operating temperatures without significant degradation, making it suitable for applications where thermal management is crucial.
Durability: RO3210 laminate is designed to be mechanically robust, offering good resistance to impact, flexing, and bending. This durability ensures the reliability and longevity of the circuits, even in demanding environments.
Wide Range of Applications: RO3210 is commonly used in various high-frequency applications, including power amplifiers, antennas, radar systems, and microwave circuits. Its versatile nature and excellent performance make it suitable for a broad range of industries, such as telecommunications, aerospace, and automotive.
Established Track Record: Rogers Corporation, the manufacturer of RO3210, is a trusted and renowned provider of high-performance materials for electronic applications. With a long-standing reputation in the industry, using RO3210 offers the assurance of quality and reliability.
What Applications Require Rogers 3210 PCB Laminates?
The RO 3210 PCB laminate finds versatile applications in the commercial microwave and radio-frequency domains. Developed as an extension of the RO 3010, the RO 3210 laminate offers improved mechanical stability owing to its woven glass reinforcement.
The RO 3210 laminate is well-suited for deployment in various applications, including:
1. Collision avoidance systems for the automotive industry.
2. Automotive GPS antennas for enhanced positioning and navigation.
3. Base station infrastructure for reliable wireless communication networks.
4. Datalink systems in cables, ensuring efficient and secure data transmission.
5. Direct broadcast satellites, enabling high-quality satellite television broadcasting.
6. Wireless and LMDS broadband systems, facilitating high-speed wireless connectivity.
7. Microstrip patch antennas for wireless communications, enabling reliable signal transmission.
8. Power backplanes, delivering efficient power distribution in electronic systems.
9. Remote meter readers, ensuring accurate and remote monitoring of utility meters.
10. Wireless telecommunication systems, supporting seamless wireless communication services.
The RO3210 PCB laminate’s exceptional performance makes it a preferred choice for these applications, where reliability, signal integrity, and mechanical stability are crucial factors.
What Special Fabrication Processes for Rogers 3210 PCB Laminates?
The fabrication process for RO 3210 laminates follows the standard procedures employed for the RO 3000 series PCB materials.
Given that RO 3210 is a PTFE-based laminate, special considerations must be taken into account for the preparation of plated through-holes. Prior to depositing any conductive seed layer, it is essential to perform a pretreatment on the RO 3210 laminate. This pretreatment can be accomplished through either plasma treatment or sodium treatment.
Neglecting the pretreatment step can lead to issues such as plated voids or inadequate metal adhesion, compromising the integrity of the PCB.
Furthermore, it is crucial to desmear the RO 3210 material using plasma desmear before the copper deposition process. Chemical desmear methods should be avoided as highly alkaline chemicals and elevated temperatures can react unfavorably with the fillers and bond ply layers present in the laminate.
By adhering to these recommended practices during the fabrication process, the desired quality and performance of the RO 3210 laminates can be achieved while ensuring proper hole plating and optimal adhesion of the conductive layers.
Differences Between Rogers 3210 and FR4 Materials
Rogers 3210 and FR4 are two different types of materials commonly used in the manufacturing of printed circuit boards (PCBs). Here are the key differences between Rogers 3210 and FR4 materials:
Composition: Rogers 3210 is a specialized high-frequency laminate material, while FR4 refers to a standard epoxy-based fiberglass material. Rogers 3210 is formulated specifically for high-frequency applications, whereas FR4 is a general-purpose material used in a wide range of PCB applications.
Dielectric Constant: Rogers 3210 has a lower dielectric constant compared to FR4. Dielectric constant refers to the material’s ability to store electrical energy. A lower dielectric constant in Rogers 3210 allows for better signal propagation at high frequencies, making it suitable for high-frequency and microwave applications. FR4, on the other hand, has a higher dielectric constant, which can result in increased signal loss at higher frequencies.
Loss Tangent: Rogers 3210 exhibits a lower loss tangent than FR4. Loss tangent is a measure of the energy dissipation in a material, and a lower value indicates lower signal loss. Rogers 3210’s lower loss tangent makes it ideal for applications requiring minimal signal loss and high signal integrity.
Thermal Properties: Rogers 3210 has superior thermal properties compared to FR4. It offers higher thermal conductivity and better heat dissipation, making it suitable for applications that require efficient thermal management. FR4, while still capable of dissipating heat, has lower thermal conductivity and may require additional measures for effective heat dissipation.
Cost: Rogers 3210 is generally more expensive than FR4. The specialized formulation and performance characteristics of Rogers 3210 contribute to its higher cost compared to the widely used and more economical FR4 material.
Therefore, Rogers 3210 is specifically designed for high-frequency applications, offering lower dielectric constant, lower loss tangent, and superior thermal properties compared to FR4. FR4, on the other hand, is a general-purpose material with a higher dielectric constant and is more cost-effective. The choice between Rogers 3210 and FR4 depends on the specific requirements of the PCB application, such as the desired frequency range, signal integrity, thermal management needs, and budget considerations.
What is the Difference Between Rogers 3210 and Rogers 3000 Materials?
Rogers Corporation offers two distinct product lines: RO3210 and RO3000TM. While both are high-frequency circuit materials, there are some differences between them.
RO3210 is a thermoset-based laminate material designed specifically for high-frequency applications. It has a dielectric constant (Dk) of 10.2 ± 0.2 and a dissipation factor (Df) of 0.0023. RO3210 features excellent electrical performance, low loss, and good dimensional stability. It is commonly used in applications that require high-frequency circuitry, such as power amplifiers, antennas, and radar systems.
On the other hand, RO3000TM is a series of high-frequency laminates that includes various product variations, such as RO3003TM, RO3006TM, and RO3010TM. These laminates are constructed using a ceramic-filled hydrocarbon material system. They offer a range of dielectric constants and thickness options to meet specific design requirements. RO3000TM laminates are known for their excellent electrical performance, low loss, and reliable mechanical properties. They find applications in telecommunications, automotive radar systems, satellite communications, and more.
Overall, while both RO3210 and the RO3000TM series are high-frequency circuit materials, RO3210 is a specific thermoset-based laminate with a fixed dielectric constant, whereas the RO3000TM series comprises a range of laminates with different dielectric constants and thickness options. The choice between the two depends on the specific needs and design requirements of the application.
Is it Possible to Construct a Multilayer PCB Using Rogers 3210?
Indeed, the Rogers RO3210 laminate is highly suitable for the fabrication of multilayer PCBs. Its unique properties make it an excellent choice, particularly for constructing epoxy hybrid multilayer PCB designs.
One notable advantage of the RO3210 laminate is its low coefficient of in-plane expansion. This characteristic ensures dimensional stability, making it well-suited for multilayer constructions. The material maintains its integrity even when subjected to temperature variations, reducing the risk of warping or delamination in the PCB.
The RO3210 laminate’s stable electrical performance and mechanical characteristics extend to other laminates within the RO3200 series. This consistency enables the utilization of materials with different dielectric constants on individual layers without encountering compatibility issues or warpage problems. This flexibility in layer selection facilitates the optimization of electrical properties and design requirements for specific circuit applications.
Furthermore, the compatibility of RO3210 with other cost-effective materials offers an opportunity to reduce production costs. By strategically combining the RO3210 laminate with other suitable materials, manufacturers can achieve an optimal balance between performance and cost, making it an attractive choice for various PCB manufacturing projects.
Overall, the Rogers RO3210 laminate’s stability, compatibility with different dielectric materials, and cost-effective utilization make it an excellent option for multilayer PCB fabrication. Its reliable electrical performance and mechanical properties contribute to the production of high-quality PCBs suitable for a wide range of applications.
Key Considerations Before Using Rogers 3210 Laminate
Before making use of the RO3210 laminate, there are several factors that should be carefully considered:
Design Requirements:
Evaluate your specific design requirements and ensure that the electrical and mechanical properties of RO3210 align with your project needs. Consider aspects such as dielectric constant, dissipation factor, thermal conductivity, and dimensional stability to ensure compatibility with your circuit design.
Frequency and Signal Integrity:
RO3210 is designed for high-frequency applications. Determine the frequency range of your circuit and verify that the laminate’s electrical performance meets your desired signal integrity goals. Consider factors like insertion loss, return loss, and dispersion to ensure optimal signal transmission.
Thermal Management:
Assess the thermal requirements of your application. While RO3210 offers good thermal stability, it is essential to consider factors such as power dissipation, operating temperatures, and heat dissipation mechanisms. Ensure that the laminate can effectively handle the thermal demands of your circuit to prevent performance degradation or damage.
Manufacturing Processes:
Understand the fabrication processes involved in working with RO3210 laminate. Consider factors such as compatibility with your chosen manufacturing methods, the ability to achieve desired layer thicknesses, and ease of handling during fabrication. Ensure that your manufacturing capabilities align with the requirements of working with RO3210.
Cost Considerations:
Evaluate the cost implications of using RO3210 laminate. While it offers excellent performance, it may have a higher price compared to other available laminates. Assess your budget and determine if the benefits provided by RO3210 justify the cost for your specific application.
Supplier Evaluation:
Choose a reputable supplier for the RO3210 laminate. Ensure that they have a proven track record of delivering high-quality materials and reliable technical support. Verify the availability of the laminate in the required thickness and sheet sizes for your project.
Environmental Considerations:
Consider any specific environmental factors that may affect the performance of the laminate. Evaluate parameters such as humidity, chemical exposure, and temperature variations that the laminate will encounter during its operational lifespan.
By carefully considering these factors, you can ensure that the use of RO3210 laminate aligns with your project requirements and leads to successful outcomes.
How to Select the Best Rogers 3210 Material?
When selecting the highest quality of Rogers 3210 PCBs, it is crucial to follow these essential steps:
Verify the Dielectric Constant: Prioritize checking the dielectric constant of the Rogers PCB 3210. Most Rogers PCBs have low dielectric constants, so it is important to ensure that the chosen PCB meets your specific requirements in terms of dielectric constant.
Assess the Thermal Expansion Coefficient: When choosing premium-quality Rogers PCB 3210, it is important to consider the coefficient of thermal expansion. This coefficient determines how much the PCB material expands or contracts with changes in temperature. Look for Rogers 3210 with a thermal coefficient of approximately 70pp, indicating a favorable thermal expansion characteristic.
Evaluate the Decomposition Temperature: Pay attention to the decomposition temperature of the Rogers 3210 PCB. This temperature indicates the stability of the PCB when exposed to high temperatures. It also determines the PCB’s ability to withstand the soldering process. Select a Rogers 3210 PCB with a decomposition temperature suitable for your desired application requirements.
By following these steps, you can ensure that the Rogers 3210 PCB you choose possesses the desired dielectric constant, exhibits appropriate thermal expansion characteristics, and offers sufficient stability at high temperatures. These factors are crucial for achieving optimal performance and reliability in your circuit design.
Where to Purchase Rogers 3210 Material?
China has emerged as a leading global hub for the production of high-quality Rogers 3210 PCBs, with numerous reliable manufacturers operating in the country. Among them, JarnisTech stands out as a reputable Chinese manufacturer that prioritizes the production of top-notch PCBs over mass-scale manufacturing.
China’s reputation in the production of Rogers PCB 3210 is a result of the availability of many trusted manufacturers throughout the country. These manufacturers employ premium quality materials to ensure the production of reliable and high-performance PCBs.
JarnisTech, in particular, distinguishes itself as one of the best places in China to procure the highest quality Rogers PCB 3210. We meticulously adhere to all industry quality and safety standards during the manufacturing process. This commitment guarantees that customers receive PCBs that meet stringent quality requirements.
Moreover, JarnisTech caters to customer demands from various regions worldwide, exhibiting their ability to fulfill diverse requirements and specifications. Their global reach ensures that customers can rely on JarnisTech to deliver Rogers PCB 3210 that meets their specific needs.
Additionally, JarnisTech provides 24/7 customer assistance, emphasizing our dedication to addressing and resolving customer issues promptly. This commitment to exceptional customer support further enhances their reputation as a reliable supplier of high-quality Rogers PCB 3210.
How to Select Rogers 3210 Manufacturers?
When it comes to selecting a manufacturer for Rogers 3210 PCBs, it is important to follow these steps:
Choose a Reliable Manufacturer: Conduct thorough research to identify reputable manufacturers of Rogers PCB 3210. Look for manufacturers with a proven track record, positive customer reviews, and a strong presence in the industry. Selecting a reliable manufacturer ensures the fulfillment of your requirements.
Assess PCB Quality: It is crucial to evaluate the quality of PCBs offered by the manufacturer. Check for proper dimensions, precise components, and overall build quality. Consider visiting the manufacturer’s facility personally to assess their production processes and ensure they adhere to industry standards for producing high-quality Rogers PCB 3210.
Verify Fulfillment of Requirements: Before finalizing a manufacturer, verify whether they can fulfill all your specific needs. Contact their support team and communicate your requirements in detail. This will help you assess their ability to meet your demands and provide customized solutions.
Consider Competitive Costs: Gain a clear understanding of the costs associated with producing premium quality Rogers PCB 3210. Discuss pricing details and factors that influence the overall cost with the manufacturer. It is important to strike a balance between quality and cost-effectiveness when making your decision.
Seek a One-Stop Solution: It is advantageous to select a manufacturer that offers a comprehensive one-stop solution. This includes not only the production of Rogers PCB 3210 but also assistance with installation and replacement. Look for a manufacturer like JarnisTech, which can provide seamless support throughout the entire process, ensuring a hassle-free experience.
By following these steps, you can confidently choose a reliable manufacturer for Rogers 3210 PCBs. Consider factors such as quality, fulfillment of requirements, competitive costs, and the availability of comprehensive services. JarnisTech is a recommended supplier that can meet your needs for high-quality Rogers PCB 3210.
Final Thoughts
The Rogers RO3210 laminate exhibits exceptional dimensional stability, making it highly suitable for applications that demand precise and consistent manufacturing processes. This attribute contributes to a high production yield, minimizing the likelihood of errors or defects. Additionally, the RO3210 laminate is particularly well-suited for multilayer hybrid designs, allowing for seamless integration of different technologies within a single PCB. Furthermore, its surface smoothness enhances the line etching tolerance, resulting in improved accuracy and reliability during the etching process. These features make the Rogers RO3210 laminate an excellent choice for applications that require high-quality and reliable PCBs.
Our services
Rogers PCB Laminates & Series