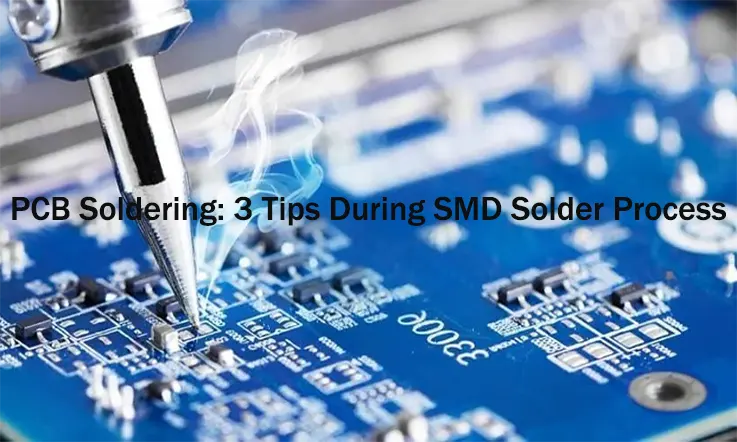
Surface mount technology (SMT) has revolutionized printed circuit board (PCB) assembly by enabling miniaturized and highly reliable electronics production. However, soldering SMT components requires great precision and process control to avoid common defects. This article will provide PCB manufacturers and assemblers with three key tips to optimize the SMD soldering process for maximum yield and reliability.
What is PCB Soldering ?
PCB soldering is a crucial process used in both through-hole and surface mount printed circuit assemblies. In the case of surface mount technology (SMT), electronic components are placed on the PCB surface using specialized equipment and then subjected to a molten solder wave.
JarnisTech provides reliable PCB soldering services in China, catering to customers who seek high-quality soldering at competitive prices. Our company operates its own PCB soldering plant in Shenzhen, enabling us to meet a wide range of specifications.
Unlike other electronic contract manufacturers, we have the advantage of owning a production facility in China solely dedicated to providing efficient soldering services. With a highly skilled workforce of 500 experienced employees, we are capable of handling various soldering requirements for different technologies.
We are equipped to perform PCB lead-free soldering processes based on specific needs. To ensure compliance with RoHS regulations, we have implemented two additional production lines exclusively for this purpose. Our soldering processes adhere to the recommended guidelines, and we employ modern techniques for quality inspection, guaranteeing the highest standards of workmanship.
3 PCB Soldering Tips During SMD Solder Process
Soldering Surface Mount Devices (SMDs) onto Printed Circuit Boards (PCBs) can be a delicate process that requires precision and care. Here are three tips to help you achieve better results during the SMD soldering process:
Preheat Your PCB
Before you begin soldering, it’s a good idea to preheat your PCB. This will help to prevent “thermal shock” to the components, which can occur when they are suddenly exposed to high heat. Preheating the PCB will also help the solder flow more evenly across the board.
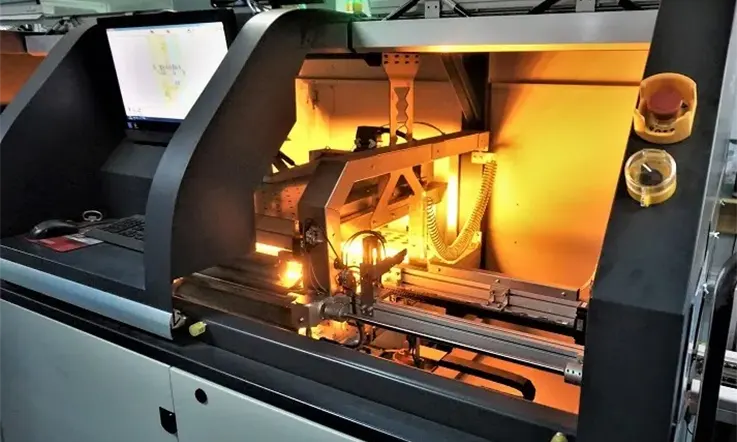
Tip: Use a hot air gun or a preheating plate to gently warm the PCB. Make sure to monitor the temperature closely to prevent overheating.
Use Flux
Flux is a chemical cleaning agent that helps to improve the quality of solder joints by preventing oxidation. It allows the solder to flow more smoothly onto the pads, which is especially important when you’re working with tiny SMD components.
Tip: Apply the flux to the pads before placing the SMD components. Then, when you apply the solder, it will flow easily and evenly, creating a strong and reliable joint.
Precision is Key
SMD components are often very small, which makes precise placement crucial. Misalignments can lead to failed connections or short circuits. Using a pair of fine-tipped tweezers can help to place components accurately.
Tip: Use a magnifying glass or a microscope to ensure precise placement of SMD components. Some soldering stations even come with built-in magnification to aid in precision work.
Remember, practice makes perfect. Soldering SMD components onto a PCB can be challenging, but with practice, you’ll be able to achieve reliable and high-quality results.
How Many Types of PCB Soldering Processes?
Here are some common types of soldering processes used in PCB (printed circuit board) manufacturing:
Wave Soldering – The PCB passes over a wave of molten solder. Components on the bottom of the board make contact with the wave and are soldered. This is a fast, automated process suitable for high-volume PCB production.
Hand Soldering – A soldering iron is used by a technician to manually solder components onto a PCB. Useful for low-volume production, rework, and repairs. Requires skill and is more time-consuming.
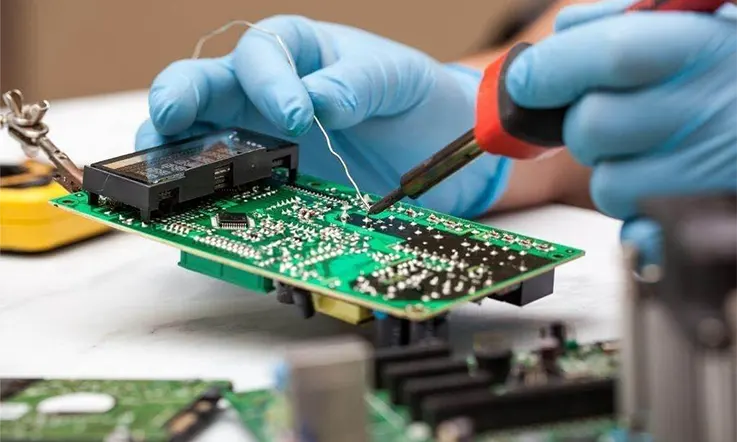
Selective Soldering – Solder is selectively applied only to the joints that require it. This focused soldering reduces waste and prevents issues from excess solder. Used for soldering SMT components or repair work.
Vapor Phase Soldering – The PCB is placed in an inert vapor that condenses on the board, transferring heat for soldering. It provides even heating and avoids PCB warping. However, the equipment is more expensive.
Laser Soldering – A laser beam provides targeted heat to melt solder and form the joint. Used for small-scale and fine-pitch soldering since it avoids collateral damage. Expensive equipment.
Induction Soldering – An induction coil generates a magnetic field that induces eddy currents on the PCB traces, heating them up to reflow the solder. Fast, efficient, and controllable process.
Reflow Soldering – Solder paste is first applied to the PCB. Components are then placed on top and the board passes through a reflow oven. The heat melts the solder paste, forming solder joints. This is a common technique for SMT (surface mount technology) components.
The printed circuit board (PCB) soldering reflow process involves four key temperature zones: preheating, soaking, reflow, and cooling.
●The Preheating Zone: In the preheating zone, the temperature is gradually increased from ambient to between 150-180°C over 220 seconds (approximately 3.5 minutes). The slow ramp rate of around 5°C/second allows solvents and moisture to evaporate from the solder paste and larger components to be heated evenly along with smaller components.
●The Soaking Zone: During the soaking zone, the temperature is held between 150-180°C. This allows the solder paste flux to become active and remove oxidization on metallic surfaces, preparing them for forming high-quality solder joints between component leads and PCB pads.
●The Reflow Zone: Also known as time above liquidus (TAL), the reflow zone is when the peak temperature is reached, typically 20-40°C above the solder alloy’s liquidus point. This melts the solder and allows wetting of the surfaces to create the solder joint.
●The Cooling Zone: In the cooling zone, the temperature is gradually decreased until the solder solidifies and forms the joint. A controlled cooling rate around 4°C/second is recommended to prevent defects from occurring.
Proper temperature profiling during these zones is critical for a successful soldering process and high joint reliability. Precision heating equipment and strict process controls are utilized.
Profiles for Reflow Process
The soaking profile resembles a trapezoidal shape, with a period of time during which the temperature is held constant at a medium temperature prior to reaching the peak. This soak zone allows for gradual flux activation and evaporation of volatile compounds. The soaking profile is optimal for boards with a mix of fine-pitch or large components, such as BGAs, as it helps prevent defects like solder balling.
The slumping profile follows more of a delta shape, with a steady ramp up to the peak temperature followed by rapid cooling. This type of profile may be suitable for simpler boards with mostly standard eutectic solder and few large or complex components, as it provides efficient thermal transfer. However, the sudden changes in temperature can risk inducing solder joint defects.
Therefore, for boards with intricate components or component size variations, a soaking reflow profile is generally preferred, while a slumping profile may suffice for simple boards with consistent solder types and component sizes. Precision temperature control is critical throughout the process to produce reliable solder joints and minimize assembly defects.
Here is an overview of common temperature profiles used in the reflow soldering process:
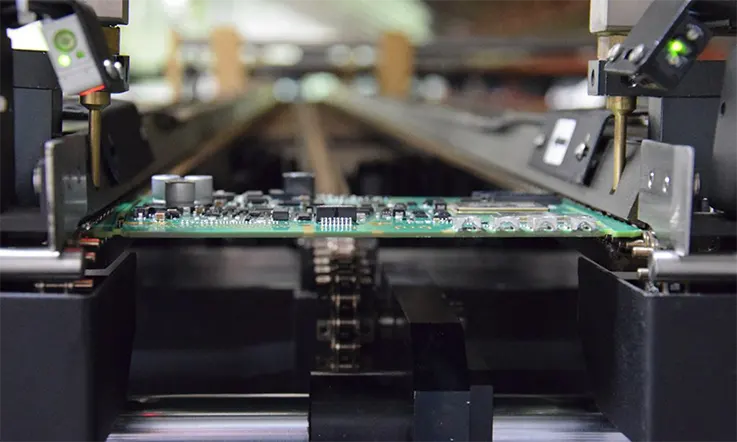
Ramp-to-Spike Profile
● Gradual ramp up to a peak temperature followed by rapid cooling.
● Can risk solder joint defects due to sudden changes in temperature.
● Typically used for standard eutectic solder alloys.
Soak Profile
● Includes a soaking zone at medium temperature before peak.
● Allows gradual activation of flux and evaporation of volatiles.
● Prevents defects like solder balling.
● Best for SAC alloys and for boards with a mix of component sizes.
Ramp-Soak-Spike Profile
● Combines features of ramp-to-spike and soak profiles.
● Provides a soaking stage and optimized spike and cooling zones.
● Preferred for lead-free solders and complex board assemblies.
Dual Peak Profile
● Has two peak temperatures – one for melting solder paste, one for components.
● Allows better control of soldering process for mixed assemblies.
● Minimizes thermal stress on temperature-sensitive components.
The optimal profile depends on factors like solder alloy, board and component complexity, thickness and thermal mass. Precision profiling is key for defect reduction and reliability. Profiling is tuned based on experience and testing.