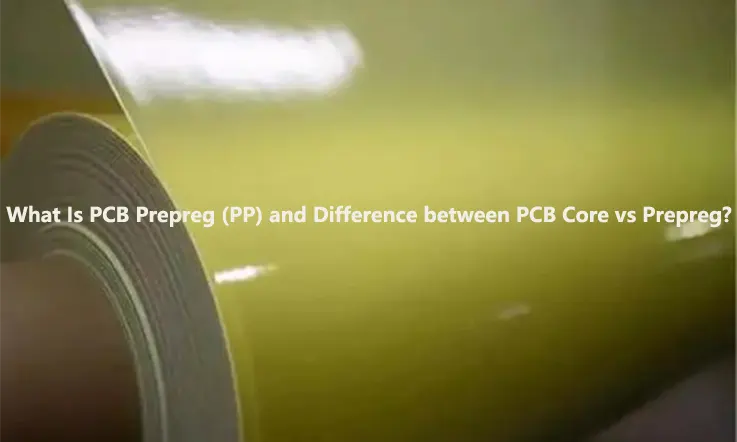
Prepregs serve as a critical insulation layer in printed circuit board (PCB) manufacturing, widely used for enhancing the dielectric properties of a PCB. It acts as a binding material, creating a sandwich with two distinct cores or between a copper foil and a core. Prepregs hold a vital function in the design and production of PCBs.
Prepregs offer a unique set of dielectric properties that can be customized as per the specific requirements of a given application. In a chemical reaction, by mixing specific catalysts and additives, a portion of the prepreg can be transformed into a special conductive zone, which is what we refer to as selective conductivity.
This article aims to offer an in-depth understanding of the role of prepreg material and its significance in the PCB manufacturing process. Additionally, we will delve into the PCB core material and highlight the differences between prepreg and PCB core.
What Is Printed Circuit Board ?
For PCB design engineers, it is crucial to have a thorough understanding of what a printed circuit board (PCB) is and its significance in modern technology. A PCB provides the foundation for almost all electronic devices, connecting various electrical components to enable the intended functionality of the device.
The primary components of a PCB include substrate sheets, copper layering, microscopic holes, a solder mask, and a coating that is typically applied using the tin-boiling process, among other elements before fusing. Although it may seem like a straightforward process, PCB production can be complicated and time-consuming, requiring precise calculations to avoid errors.
As a result, the design process for a PCB involves significant attention to detail and thorough planning to ensure its performance and reliability. PCB design engineers must consider various factors, such as the specific applications, functionality requirements, and electronic components to be incorporated, to create an accurate and functional PCB layout.
What ls PCB Prepreg ?
In PCB manufacturing, Prepreg, also referred to as Pre-Impregnated, B-stage, Bonding sheet, or Preg, is a composite material composed of fiberglass cloth impregnated with resin. During the Prepreg coating process, the resin undergoes partial curing, making it ready for bonding. Prepregs are instrumental in bonding the PCB stack-up, comprising copper foil or other materials, through heat and pressure during the pressing process.
Different types of fiberglass are utilized in producing Prepregs, with each number corresponding to a unique combination of characteristics such as Resin Content, Cured Thickness, Standard Size (Roll Type), Weight, among others. A parameter chart for Prepregs reveals that the resin content and cured thickness of the same glass fabric might vary.
The glass weave in Prepregs is enclosed in resin, with the production process being akin to yarn production. The tightness of the glass weave, which can range from tight (such as 7628 PP) to relatively loose (such as 106 PP) is adjusted using a loom. The electromagnetic characteristics of the yarn, including homogeneity, gaps, and overall dispersion, affect signal losses and any fiber weave effects observed on the PCB board. As a crucial part of the PCB manufacturing process, PCB manufacturers must carefully select the appropriate Prepreg specifications for a particular circuit board design to ensure a precise and durable end product.
Properties and Characteristics of PCB PP (Prepreg)
PCB PP (Prepreg) has several properties and characteristics that make it an ideal material for PCB manufacturing. Some of these properties and characteristics include:
● Excellent electrical properties: PCB PP (Prepreg) has high dielectric strength, low dielectric constant, and low dissipation factor, which makes it suitable for high-speed and high-frequency applications.
● Good mechanical properties: PCB PP (Prepreg) has good mechanical properties such as high tensile and flexural strength, resistance to puncture and impact, and excellent dimensional stability.
● High thermal stability: PCB PP (Prepreg) can withstand high temperatures, making it suitable for applications in which the PCB is subject to high heat.
● Chemical resistance: PCB PP (Prepreg) has excellent chemical resistance and can withstand exposure to a wide range of harsh chemicals and solvents.
● Low water absorption: PCB PP (Prepreg) has low water absorption, which reduces the risk of damage from moisture and humidity.
● High dimensional stability: PCB PP (Prepreg) has high dimensional stability, which ensures that the size and shape of the PCB remain consistent over time.
● Excellent adhesion: PCB PP (Prepreg) has excellent adhesion to copper and other metal surfaces, ensuring that the copper layers and other components remain securely bonded.
● Low outgassing: PCB PP (Prepreg) has low outgassing properties, which reduces the risk of contamination in sensitive applications such as aerospace and defense.
● Green properties: PCB PP (Prepreg) can be produced using eco-friendly materials and manufacturing processes, making it a more sustainable option compared to other types of PCB materials.
In a word, the properties and characteristics of PCB PP (Prepreg) make it an excellent choice for a wide range of electronic applications that require high performance and reliability.
Different Types of PCB PP (Prepreg)
There are several types of PCB PP (Prepreg), which are as follows:
● Epoxy Prepreg: This is the most common type of PCB PP (Prepreg). It is used for high-frequency applications and has excellent electrical and mechanical properties.
● Polyimide Prepreg: This type of PCB PP (Prepreg) is used for flexible and rigid-flex circuit boards. It has good thermal stability and can withstand high temperatures.
● Cyanate Ester Prepreg: This type of PCB PP (Prepreg) is used for high-frequency applications and has low loss characteristics. It also has good thermal stability.
● BT (Bismaleimide Triazine) Prepreg: This type of PCB PP (Prepreg) is used for high-temperature applications. It has excellent electrical and mechanical properties and can withstand high temperatures.
● PTFE (Polytetrafluoroethylene) Prepreg: This type of PCB PP (Prepreg) is used for microwave and high-frequency applications. It has low dielectric loss and can withstand high temperatures.
● Ceramic-filled Prepreg: This type of PCB PP (Prepreg) is used for high-frequency and high-power applications. It has good thermal stability and high glass transition temperature.
Applications of PCB PP (Prepreg)
PCB PP (Prepreg) has several applications in the electronics industry. Some of the common applications of PCB PP (Prepreg) are as follows:
● Consumer electronics: PCB PP (Prepreg) is used in various consumer electronics such as smartphones, laptops, and tablets that require high-performance and lightweight PCBs.
● Aerospace and defense: PCB PP (Prepreg) is used in aerospace and defense applications that require high-reliability and high-performance PCBs in harsh environments.
● Automotive: PCB PP (Prepreg) is used in automotive applications in areas such as engine control modules, anti-lock braking systems, and electronic steering systems that require high-temperature stability and reliability.
● Medical equipment: PCB PP (Prepreg) is used in medical equipment such as X-ray machines, MRIs, and CT scanners that require PCBs with high-density and low profile components.
● Industrial equipment: PCB PP (Prepreg) is used in industrial equipment such as automation systems, robotics, and process control systems that require high-performance and durable PCBs.
● Telecom and networking: PCB PP (Prepreg) is used in telecom and networking equipment such as routers, switches, and servers that require high-speed and high-density PCBs.
● LED lighting: PCB PP (Prepreg) is used in LED lighting that requires high thermal conductivity for efficient heat dissipation.
Manufacturing Process of PCB PP (Prepreg)
The manufacturing process of PCB PP (Prepreg) typically involves the following steps:
● Mixing: The resin and hardener are mixed together to form a homogeneous mixture.
● Impregnation: The mixture is then impregnated into the fibers of the reinforcing material (typically fiberglass or cellulose paper) to form the prepreg.
● B-stage: The prepreg is partially cured at a controlled temperature and pressure to the B-stage. This stage is known as the “preliminary cure” stage, which makes the prepreg semi-solid and tacky, yet still malleable.
● Storage: The B-stage prepreg is then stored in refrigerated conditions until ready to use.
● Lamination: The prepreg is then placed between two or more copper-clad layers and heated under pressure to fully cure the resin. This process is called lamination.
● Drilling: Holes are drilled into the laminate for interconnection between copper layers.
● Plating: Copper is plated onto the walls of the holes to create the electrical connections.
● Etching: The excess copper that is not part of the traces or vias is etched away.
● Soldermask and Silkscreen: The board is coated with soldermask and a silkscreen legend to protect copper surfaces and to indicate component placement.
● Final testing: The final product is then electrically tested to ensure that it meets the required specifications.
Advantages of using PCB PP (Prepreg) in PCB manufacturing
The advantages of using PCB PP (Prepreg) in PCB manufacturing are as follows:
● High Performance: PCB PP (Prepreg) offers excellent mechanical, chemical, and electrical properties, making it ideal for use in high-performance PCBs.
● Easy to use: PCB PP (Prepreg) is easy to handle and can be used in a variety of manufacturing processes.
● Wide range of applications: PCB PP (Prepreg) can be used in a wide range of applications in different industries, including consumer electronics, aerospace and defense, automotive, medical equipment, industrial equipment, telecom and networking, and LED lighting.
● Thermal stability: PCB PP (Prepreg) offers good thermal stability, making it ideal for use in high-temperature applications.
● High dielectric constant and low loss: PCB PP (Prepreg) has a high dielectric constant and low loss characteristics, which makes it ideal for use in high-frequency and RF applications.
● Reliable and Durable: PCB PP (Prepreg) provides excellent reliability and durability, ensuring long-term performance of the PCB.
● Consistent Quality: PCB PP (Prepreg) is manufactured to strict quality standards, ensuring consistent quality in every batch.
● Environmentally friendly: PCB PP (Prepreg) can be produced using eco-friendly materials, making it more environmentally friendly compared to other types of PCB materials.
● Cost-effective: PCB PP (Prepreg) is cost-effective compared to other types of advanced PCB materials, making it an excellent choice for many applications.
Prepreg Selection for PCB Design and Fabrication
When it comes to constructing PCBs using prepregs, several factors are taken into account when choosing the right type. The required thickness is a crucial criterion among others. Based on their resin content, prepregs are available in different varieties, including Standard Resin (SR), Medium Resin (MR), or High Resin (HR). Generally, the higher the resin content, the more expensive the prepreg.
For a better understanding, the following table outlines the resin content of the different prepreg types:
PP Types | Resin Content | Glass | O/A | Delta | Unsupported Resin Volume |
106 | 75% | 0.0014 | 0.0023 | 0.0009 | / |
1080 | 65% | 0.0025 | 0.003 | 0.0005 | Low |
2113 | 56% | 0.0029 | 0.0039 | 0.001 | / |
2116 | 57% | 0.0038 | 0.0051 | 0.0013 | / |
2116 | 62% | 0.0038 | 0.0061 | 0.0023 | High |
1652 | 50% | 0.0045 | 0.0057 | 0.0012 | / |
7628 | 42% | 0.0065 | 0.0069 | 0.0004 | Low |
7628 | 50% | 0.0065 | 0.0085 | 0.002 | High |
Choosing the correct prepreg type is essential to ensure the reliable operation and longevity of the final product. PCB manufacturers must consider various parameters, such as the size of the board, board thickness, and specific application requirements when selecting the appropriate prepreg type.
How to Use Prepregs in multilayer PCB ?
PCB design engineers often utilize prepregs that are specifically tailored to intricate and multifaceted circuit board designs. This is critical for achieving the necessary board thickness and performance characteristics required for such applications.
In the case of multilayer PCBs, multiple prepreg layers are utilized to bind the various layers of the board. These layers are stacked and subjected to high temperatures to merge together. In such applications, the thickness of the prepreg layer and the overall thickness of the board are comparable.
To ensure that such complex and multilayered PCBs function correctly, engineers require prepregs with specific properties and attributes. The prepreg must have a smooth surface free of blemishes, excess resin powder, faults, oil stains, or foreign objects. Its surface must be visually appealing and have a smooth appearance, which is critical for ensuring the reliable operation of the final product.
PCB Prepregs (PP): Storage Conditions
To ensure the quality and reliability of prepregs in PCB production, it is crucial to store them under specific conditions. Proper storage conditions for prepregs include:
● Avoid exposure to UV rays and strong light.
● Store at a temperature below 23 °C and with relative humidity below 50% for a maximum period of 3 months.
● When storing at a temperature of -5 degrees Celsius, prepregs can have a shelf life of 6 months. However, to ensure proper function, it is recommended to let the material normalize at room temperature for at least four hours before use.
● Always take precautions against moisture and ensure storage in a damp-proof area. Moisture can compromise the bonding strength of prepregs, potentially affecting the performance and longevity of the final PCB product.
As a result, PCB manufacturers must carefully handle and store prepregs to prevent their degradation and ensure their optimal functionality during the production process.
PCB PP Resin Content: How to Test ?
The resin content of prepregs and laminates indicates the percentage of resin present in relation to the overall weight. Burnout testing is a typical method employed to determine the resin content in fiberglass reinforced prepregs and laminates. This test involves burning the sample at 1,100 degrees Celsius, and the difference between the initial and final weights represents the resin content percentage.
Managing the amount of resin used in PCB production depends on several factors, including the weight variation of the substrate fabric, coater operation consistency, and the fluctuation in the rheology of the resin solution from batch to batch. These variations can impact the resin content of prepregs and laminates, potentially affecting the performance and functionality of the final PCB product. Therefore, PCB manufacturers must closely monitor the resin content to ensure optimal performance and reliability.
Definition of PCB Core Material
A fundamental element of a printed circuit board (PCB) is a rigid base material that forms the core of the board. This base material is laminated with copper and utilized in the production of single and double-sided circuit boards, as well as PCBs with multiple layers. The combination of the base material and copper layers creates the foundation of a multilayered printed circuit board.
● Copper Foil
● PP Materials
● Copper Foil
● Core Materials
● Copper Foil
● PP Materials
● Copper Foil
Comparison of PCB Core and Prepreg
The manufacturing process of printed circuit boards (PCBs) involves distinct components, including prepreg and core. Despite their similarities, confusion between these two components can result in significant issues during the production process.
The core is a product of both prepreg and lamination, and as a result, it is significantly stiffer than prepreg. Copper is plated on both sides of the core, which is created with a flame-retardant laminate material consisting of fiberglass and epoxy.
In contrast, prepreg is partially dried, without lamination, and is less rigid than the core. Its dielectric constant is also distinguishable from that of the core. While the dielectric constant of the core remains constant during lamination, the dielectric constant of prepreg fluctuates before and after the lamination process. Furthermore, the constants of dielectric polarization are influenced by various factors, including the materials and production techniques used.
The various constants of dielectric polarization are also functions of the following:
● Glass weave.
● Type of resin.
● Resin content.
In PCB manufacturing, achieving precise impedance matching can be challenging due to the compatibility issues between prepreg and core materials. In addition, the use of different core/prepreg stacks can result in varying dielectric constants, making it difficult to accurately predict the dielectric constants of an interconnect and the losses it may incur.
These issues can impact the performance of the final PCB product, especially in situations where precise impedance matching is critical. It is essential to consider the compatibility between prepreg and core materials, as well as the various core/prepreg stacks’ dielectric constants, to ensure reliable, high-quality PCBs. Precise management and selection of materials and production techniques are crucial to achieving optimal impedance matching and minimizing loss in PCB interconnects.
Therefore, it is critical to accurately identify and differentiate between prepreg and core in PCB production to avoid issues that could compromise the quality and reliability of the final product.
The thickness of a printed circuit board (PCB) is determined by the type of prepreg used. A combination of thin prepreg sheets, known as prepreg plies, can be layered on top of each other to achieve the required thickness of the PCB.
Regardless of the core or prepreg materials used, high voltage applications may encounter issues with leakage and creepage currents. FR4 materials must meet creepage criteria to prevent copper from electromigrating and conductive filaments from growing. To address these concerns and raise glass transition and decomposition temperatures, non-dicyandiamide resins have become more popular in PCB manufacturing.
Managing these factors is essential in PCB production to ensure the reliable and safe performance of high voltage applications. Careful selection of materials and production techniques can minimize the risks of issues like leakage and creepage currents and enhance the overall quality and durability of PCB products.
PCB PP and Core Hot Pressing Cycle
Our multilayer printed circuit boards are constructed from thin copper foils and pre-impregnated (B-stage) epoxy resin (PP) sheets of glass fabric, forming the outer layer. The lay-up operator places two PP sheets and a copper foil onto a steel baseplate before precisely positioning the pre-treated core on top of alignment pins. Two more PP sheets, another copper foil, and an aluminum press plate are then added, forming the massive stack. The entire unit is placed beneath a press, and computer-controlled application of heat and pressure melts and cures the PP’s epoxy resin. This process bonds the PCB layers together, ensuring that the bond is permanent over the life of the PCB.
For complex multilayer PCBs with more than ten or twenty layers, the stacks may be sub-assembled into cores, prepregs, and copper foils before drilling and plating to complete the final PCB.
After completion of the pressing cycle, the press operator carefully unloads the press and rolls the stacks into a clean room. The lay-up operator removes the top plate and de-pins the stacks. Each aluminum press plate is removed from panels as they are unloaded to ensure the copper surface is as smooth as possible. The copper foil is securely bonded in place, forming the outer layers of the PCB.
By using this method, we ensure that the PCB’s bond is secure and reliable. The computer-controlled process allows for precise management of temperature, pressure, and cooling to ensure consistent results. Our team takes great care to maintain quality control throughout the production process, minimizing the risk of defects and ensuring that the final PCB product meets or exceeds industry standards.
Future Trends and Developments of PCB PP (Prepreg)
The future trends and developments of PCB PP (Prepreg) are as follows:
● High-speed and high-frequency applications: PCB PP (Prepreg) will continue to be used in high-speed and high-frequency PCB applications, such as 5G communication systems and Internet of Things (IoT) devices, due to their high electrical performance.
● Miniaturization and high-density designs: As electronic devices become smaller and more compact, PCB PP (Prepreg) will play a significant role in enabling high-density designs with low profile circuits.
● Improved thermal management: There will be a greater emphasis on improving thermal management in electronic devices to optimize performance and prevent thermal damage. PCB PP (Prepreg) will be developed with materials that have improved thermal conductivity to dissipate heat more effectively.
● Sustainable manufacturing: There will be a greater focus on sustainable manufacturing processes for PCB PP (Prepreg), such as reducing waste and using eco-friendly materials.
● Integration with emerging technologies: PCB PP (Prepreg) will be integrated with emerging technologies, such as artificial intelligence (AI), to enable smarter and more efficient electronic devices.
● 3D printing: The development of 3D printing technology will lead to new possibilities in the manufacturing of PCB PP (Prepreg), allowing for the creation of intricate and complex shapes that were previously not possible with traditional manufacturing methods.
To Sump Up
In printed circuit board (PCB) manufacturing, both the core and prepreg materials are critical components. The prepreg holds together multilayer PCBs, while the core is a fundamental PCB material. The core is cured, while the materials used in prepreg are pliable and can be molded into sheets, making this the main difference between the two. When exposed to high temperatures, the substance melts, helping to fuse the layers together.
At JarnisTech, we prioritize using the highest-quality Copper Clad Laminate (CCL) materials in our PCB manufacturing, whether for prepreg or core materials. This ensures that every PCB board we supply to customers is made using qualified materials, making us one of the top PCB suppliers in China.
If you have any questions, please do not hesitate to contact us via email at [email protected] or by phone at 0086-755/23034656. Our team is always ready to assist you and provide guidance on the best PCB materials and production to meet your specific needs.
Related Posts:
1. Selecting PCB Laminate Materials: A Comprehensive Overview
2. PCB Copper Trace Width and Space: Everything You Need to Know About Them
3. Which Types are Most Commonly Used in PCB Substrates?
4. What Is Fiberglass PCB and Why Fiberglass Used in PCB Manufacturing?
5. Standard PCB Thickness-Choosing the Correct Thickness for PCB