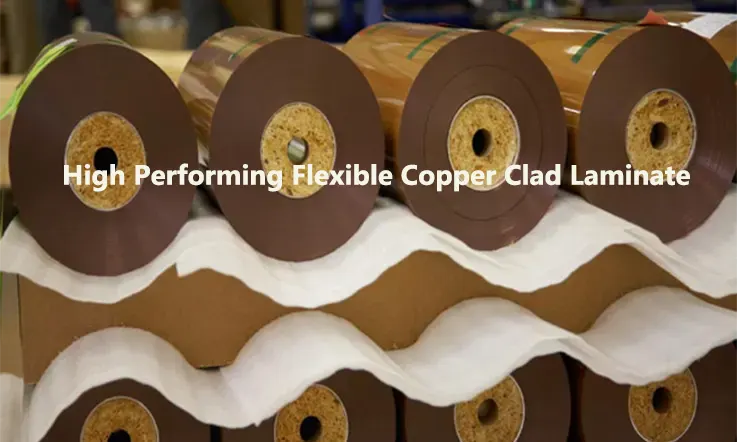
The application of flexible printed circuit boards (PCBs) has expanded significantly in recent years, with its use no longer restricted to the defense sector and instead making its way into the consumer market. As a result, flex PCBs are now widely used in various computer peripherals, automotive electronics, cameras, digital video cameras, instruments, office automation devices, health care equipment, and other consumer electronics.
Moreover, its application in Chip on Flex (COF) film for Liquid Crystal Display (LCD) modules has become increasingly prevalent. Due to their expanding range of uses, flexible PCBs have undergone significant structural and functional modifications, and their performance requirements have been raised. To meet these requirements, the substrate material of flexible printed circuit boards (PCBs) needs to possess qualities such as high heat resistance, dimensional stability, flexibility, low dielectric constant for high frequency, and non-halogenation. Therefore, the performance of flexible copper clad laminate (CCL), which serves as the substrate material for flexible PCBs, must be enhanced to achieve overall improvement in their performance.
This article aims to provide an overview of flex CCL’s fundamentals to assist in selecting an appropriate flexible substrate material to achieve optimal performance for your flexible printed circuit boards.
What Is Flexible Copper Clad Laminate (FCCL) ?
It’s essential to note that when designing printed circuit boards, rigid copper clad laminate (CCL) may not be suitable for all applications. Instead, flex circuits, which can range from highly flexible to slightly flexible, require a different design approach. These circuits demand a flexible CCL that consists of a single or double layer of insulating PI or polyester film substrate material with a thin copper foil conductor that possesses surface flexibility.
Flexible copper clad laminate (FCCL) is an essential component in the manufacturing process of flexible printed circuit boards (FPCs). In FCCL, copper foil and polyimide act as the electrical conductor and insulator, respectively, providing the necessary flexibility and strength for FPCs to function correctly. Therefore, the integration of FCCL is critical to producing high-quality FPCs while ensuring their optimal performance.
● Double-sided FCCL: with copper foil on both sides.
● Single-sided FCCL: with copper foil only on one side.
In the manufacturing of flexible copper clad laminates (FCCLs), there may or may not be adhesive between the polyimide and the copper foils. Furthermore, FCCLs are classified into different categories based on their composition and properties:
● Adhesive-Based FCCLs: As the name suggests, these types of FCCLs contain adhesive layers sandwiched between the copper foil and polyimide layers.
● Adhesiveless FCCLs: These FCCLs do not contain any adhesive layer, and the copper foil is directly bonded to the polyimide substrate.
● Coverlay FCCLs: Coverlay FCCLs have a layer of flexible material, usually polyimide or polyester, bonded to one or both sides of the FCCL. This provides additional insulation and protection to the circuitry.
Flexible PCBs can be produced using either single- or double-sided flexible copper clad laminates (FCCLs) that may or may not have adhesives. Additionally, FCCLs can be combined with rigid copper clad laminates (CCLs) and polypropylene (PP) to manufacture rigid-flex boards. This versatile and robust combination allows flexible PCBs to meet unique design requirements and operate efficiently for longer periods of time. It makes flexible PCBs ideal for portable electronic devices, medical equipment, and various other applications where flexibility and compactness are essential.
Therefore, choosing the appropriate FCCL category depends on the specific requirements of the application, such as flexibility, chemical resistance, or thermal performance.
Difference between Adhesiveless and Adhesive FCCL
Flexible copper clad laminates (FCCLs) can be classified into two main types based on the absence or presence of an adhesive layer. Non-adhesive FCCLs do not contain an adhesive layer between the copper and polyimide substrates.
● It’s crucial to note that adhesiveless FCCLs, while more expensive than adhesive FCCLs, offer more flexibility and a lower coefficient of thermal expansion (CTE), resulting in better dimensional stability. Thinner PI laminates are preferred for greater flexibility, while thicker ones are more expensive.
● JarnisTech, a leading manufacturer, recommends the use of adhesiveless FCCLs for applications such as HDI, rigid-flex, multilayer, impedance-controlled PCBs, and high-density SMDs with coverlay openings due to their superior flexibility and stability.
● However, adhesive FCCLs are recommended for the production of simple flex circuits, single-sided flex circuits, and double-sided flex circuits. Adhesive FCCLs have the advantage of being less expensive and not being restricted by thickness limitations.
In a word, selecting the appropriate FCCLs depends on the specific requirements of the application. As a result, it’s essential to consider factors such as flexibility, stability, cost, and thickness before making any decisions.
Flexible CCL: Classification
Flexible copper clad laminates (FCCLs) can be classified into different categories based on various parameters.
● Firstly, based on substrate material, FCCLs can be categorized into polyester type, polyimide (PI) type, and polytetrafluoroethylene (PTFE) type.
● Secondly, FCCLs can be classified into single-side flex CCL, double-side flex CCL, and multi-side flex CCLs based on the number of layers. The amount of trace density can also be used to classify FCCLs into ordinary flex CCL and high-density flex CCL.
● Finally, FCCLs can be categorized based on different product structures into 3L-FCCL and 2L-FCCL. 3L-FCCLs are sometimes referred to as adhesive flex CCLs, while 2L-FCCLs are commonly known as non-adhesive flex CCLs.
It’s essential to consider each of these factors when selecting the right FCCLs for specific PCB design requirements. This will ensure that the final product meets the required specifications and functions as intended.
Flexible CCL Performance
Flexible copper clad laminate (FCCL) offers various advantages for use in the printed circuit board (PCB) industry. It is easy to work with and can be utilized in several applications due to its high flexibility. Additionally, FCCLs are compatible with most solder masking materials, making them an excellent choice for new designs or existing products that require a more flexible substrate.
Some of the key advantages of FCCLs include excellent heat resistance, peel resistance, and dimensional stability. They are also flame retardant with a UL94V-0/VTM-0 rating and exhibit excellent mechanical and electrical properties.
Such features make FCCLs an ideal choice for a variety of applications across a range of industries, including consumer electronics, medical devices, and aerospace. PCB designers and engineers can leverage these advantages to create innovative and high-performance PCB designs that are both reliable and cost-effective.
Flexible CCL Application
Flexible copper laminates are utilized extensively in the Electronic manufacturing industry for creating electronic circuits and boards. This versatile material finds applications in a wide range of contexts, including the following:
● Electronic Display Panels: Flexible copper laminates with a thin coating of copper foil can be used to cover the glass surface of electronic display panels.
● Electronic Component Packaging: Flexible copper lamination can be utilized to wrap electronic components such as resistors, capacitors, and transistors to prevent shorting during transport or storage.
● Printed Circuit Boards (PCBs): Printed circuit boards, or PCBs, are fundamental components of electronic devices such as computers, mobile phones, and other digital appliances. Flexible copper laminates are extensively used in the construction of PCBs due to their high flexibility, excellent mechanical properties, and low cost.
The unique properties of flexible copper laminates make them an ideal material choice in various contexts, where they can be utilized to add flexibility to an otherwise rigid component, increasing its durability and functionality. Flexible copper laminates play a crucial role in electronic manufacturing, making it easier to design and manufacture more sophisticated electronic devices.
Flexible Copper Clad Laminated Manufacturing Process
The manufacturing process of flexible copper clad laminate typically involves the following steps:
● Film Preparation: The first step is to prepare the base film. Typically, a plastic film such as polyimide or polyester is used, which is first cleaned and then coated with a layer of adhesive.
● Copper Cladding: The next step is to apply a layer of copper to the surface of the film. This is typically done using a process called electroless plating, in which a thin layer of copper is deposited onto the surface of the film using a chemical reaction.
● Lamination: The copper-clad film is then bonded to a substrate using a high-temperature lamination process. The substrate material can be another layer of plastic film or a rigid material such as FR4.
● Etching: The next step is to selectively remove the unwanted copper from the surface of the film using a chemical etching process. This is typically done by applying a resist material to the surface of the copper and then etching away the unprotected areas using an acid solution.
● Drilling: Once the copper has been etched away to create the desired circuit pattern, the next step is to drill holes for the components that will be mounted onto the board.
● Surface Finishing: Finally, the board is finished by applying a layer of protective coating to the surface and adding any required surface finishes such as gold plating.
The exact manufacturing process may vary depending on the specific type of flexible copper clad laminate being produced.
Advantages and Disadvantages of Flexible Copper Clad Laminated
Advantages of flexible copper clad laminate include:
● Flexibility: The primary advantage of flexible copper clad laminate is its flexibility, which allows it to be shaped and bent to fit into tight spaces or irregular shapes, making it suitable for use in flexible or curved electronic devices.
● Lightweight: Flexible copper clad laminate is lightweight, reducing the weight of electronic devices and making them easier to transport.
● Enhanced Durability: Flexible copper clad laminate is more resistant to physical stress, vibration, and thermal shock compared to rigid PCBs, thereby increasing the durability of electronic devices using flexible PCBs.
● Space Savings: Flexible copper clad laminate takes up less space than rigid PCBs, making it ideal for small electronic devices.
● Low-cost: In some cases, flexible copper clad laminate can be more cost-effective than rigid PCBs, depending on the specific application and type of board needed.
Disadvantages of flexible copper clad laminate include:
● Limited Capabilities: Flexible copper clad laminate may not be able to handle the same current load and heat dissipation as rigid PCBs, which can limit its use in certain applications.
● Manufacturing Complexity: The manufacturing process for flexible copper clad laminate is more complicated and expensive than the process for rigid PCBs.
● Special Handling Required: Flexible PCBs require special handling, and incorrect handling could damage the circuits.
● Limited availability: The availability of some types of flexible copper clad laminate may be limited, depending on the specific requirements of the application.
● Design Restrictions: The flexibility of copper clad laminate can also create design restrictions that may limit the range of electronic devices in which it can be used effectively.
Basics of FPC PCB
Flexible printed circuits (FPC) are highly versatile circuit boards that can be used in various fields due to their ability to bend and stretch. Their physical properties allow the FPC to be shaped to fit within the constraints of electronic products or devices, whereas non-flexible circuits would force the device to change its shape to fit the circuit board. The thickness of copper, adhesive, PI/Kapton, and coverlay all play a role in determining the FPC’s flexibility.
Notably, when comparing adhesive vs. non-adhesive FCCL, adhesive-free FCCL is superior in terms of bendability. Additionally, when using the same adhesive-free FCCL, flexible bending with 1/2oz is superior to that with 1oz. Similarly, when copper thicknesses are the same (1OZ), flexible bending with hatching pour is superior to that with solid pour. Electronic manufacturers should consider these factors when selecting materials and designing FPCs to achieve optimal performance and functionality.
Flexible Printed Circuit Design: Considerations for Thickness and Impedance Control
To achieve the desired thickness and controlled impedance in flexible printed circuit (FPC) design, combinations of different flexible copper clad laminates (FCCLs), adhesives, coverlays, and bondplies can be used. This technique enables designers to achieve the desired performance while meeting the required thickness specifications.
However, it’s important to note that thicker polyimide thickness in FCCL equal to or more than 4mils is not commonly used due to the high material cost and decreased flexibility. Thicker polyimide layers can increase the overall weight of the FPC and make it less flexible, thereby reducing its performance and functionality.
Designers must carefully evaluate the material combinations and thicknesses they use in FPC design, keeping in mind the trade-offs between performance, weight, cost, and flexibility. A thoughtful approach to FPC design can result in highly efficient and flexible FPCs that meet the unique requirements of specific applications.
Why Choose Flexible Copper Clad Laminated ?
Flexible copper lamination is a widely-used material in the manufacturing of printed circuit boards (PCBs). This type of copper foil laminate is notable for its unique properties that distinguish it from others. The most significant advantage of this material is its capability to be shaped into any form, making it ideal for a range of applications, particularly in electronics and electrical devices.
The integration of flexible copper laminate in PCBs is primarily intended to enhance the board’s flexibility. This results in increased resistance to bending or breaking during regular usage, resulting in greater durability. Additionally, it allows for straightforward modification of designs on the board, enabling them to be molded into complex shapes without causing any damage to the designs or the board itself. Electronic manufacturers should consider these benefits when selecting materials for their PCB manufacturing process.
Trends in Flexible CCL Development
● Flexible copper clad laminates (FCCLs) are poised to play a crucial role in various fields in the future. Ongoing research and development efforts are focused on creating new types of FCCLs, including ultra-thin flex CCLs, high-speed flex CCLs, halogen-free and phosphor-free fire-resistant flex CCLs, and high-Tg flex CCLs.
● Ultra-thin flex CCLs are being developed to meet the growing demand for lightweight electronic devices. High-speed flex CCLs are also in demand due to the recent trend of high-frequency and high-speed signal transmission.
● Halogen-free and phosphor-free fire-resistant flex CCLs are being developed to meet the specific environmental protection regulations set by the EU and the demands of the public.
● For 3L-FCCLs, the development of high-Tg flex CCLs is essential in terms of improving adhesive heat resistance. The adhesive used in 3L-FCCLs is mostly composed of epoxy resin and acrylic acid. High-Tg flex CCLs must strike a balance between maintaining low manufacturing costs and delivering superior dimensional stability, insulation, and chemical resistance.
As a result, the development of these new types of FCCLs represents an exciting avenue for the future of electronic manufacturing. These cutting-edge materials will help designers and manufacturers to create more innovative and efficient electronic devices that meet the increased demands and specifications of the market.
Summary
Get an Instant and Reliable Quote on Flexible PCB from JarnisTech
Flexible Copper Clad Laminate (FCCL) is a vital component in modern electronics and has tremendous potential due to its flexibility, weight reduction, and durability. Its market demand is expected to rise in various industries as technology and smart packaging solutions advance. Although FCCL has some drawbacks, its numerous benefits make it a worthwhile choice for many applications. The manufacturing process of FCCL is complex and requires specialized handling. Nonetheless, with advancements in technology and manufacturing processes, it is likely that FCCL’s properties and capabilities will improve in the future. Therefore, FCCL is an essential material in the evolution of electronic devices, smart packaging solutions, and various other applications.
JarnisTech is a leading flexible copper laminate manufacturer in China with an exceptional track record of excellence for the past two decades. We offer a diverse range of high-quality goods to our clients and are committed to delivering a one-stop service that includes top-quality PCB production and assembly.
It is important to note that if you select a dependable PCB manufacturer, there is no need to place a separate order for flex CCL. This is because the PCB manufacturer’s responsibility is to provide flex PCBs with excellent performance based on the characteristics of flexible CCLs. Simply requesting a quote for flexible PCBs via our website, JarnisTech.com, makes you eligible for growth opportunities. As a reliable and devoted PCB and PCBA manufacturer, we pride ourselves on delivering exceptional customer service, competitive pricing, and superior quality to our clients.
Related Posts:
1. Selecting PCB Laminate Materials: A Comprehensive Overview
2. PCB Copper Trace Width and Space: Everything You Need to Know About Them
3. Which Types are Most Commonly Used in PCB Substrates?
4. What Is Fiberglass PCB and Why Fiberglass Used in PCB Manufacturing?
5. Standard PCB Thickness-Choosing the Correct Thickness for PCB