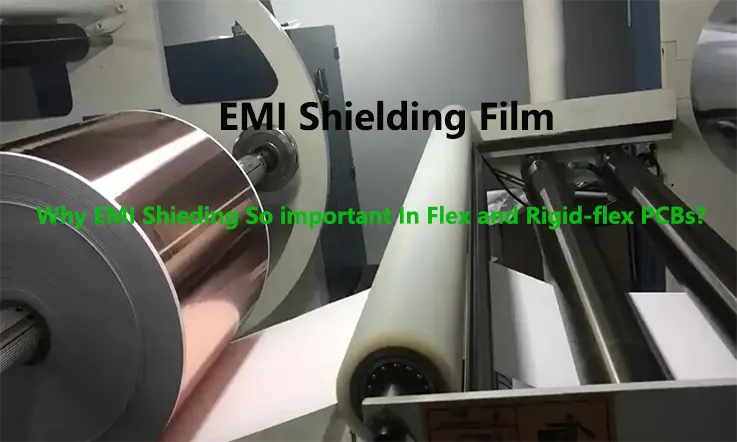
Electromagnetic interference (EMI) and radio frequency interference (RFI) can weaken the electronic signal’s integrity and strength, which can lead to disruptions and subpar performance in devices and systems that are sensitive to communication. The EMI/RFI Shielding decreases the likelihood of electrical malfunction by either blocking undesired electromagnetic waves from the outside or preventing electromagnetic waves from within the device from emitting and interfering with the operation of other circuits or devices.
This article will discuss EMI shielding and how they are used in the Flex and rigid-flex PCB industry.
What Is EMI Shielding ?
The method of preventing radio frequency interference (RFI) from causing damage to sensitive mechanical components is known as electromagnetic interference (EMI) shielding. It includes positioning die-cut materials, such as electromagnetic interference (EMI) shielding laminates, in the path of electromagnetic interference. After that, the materials absorb or reflect the electromagnetic radiation to prevent any malfunctions in the electronic gadgets.
Shielding from electromagnetic interference (EMI) is a standard practice across a variety of industries, including the consumer electronics, automotive, telecom & IT, and aerospace sectors.
Why do FPC and Rigid-Flex PCBs Need EMI Shielding Film ?
When it occurs in the radio frequency range, electromagnetic interference (EMI) is called Radio-Frequency Interference (RFI) and refers to a disturbance caused by an external source that affects an electrical circuit on printed circuit boards through electromagnetic induction, electrostatic coupling, or conduction. Your PCB assembly‘s performance may suffer or it may cease working entirely if this disturbance is present.
Depending on the purpose, shielding can be comprised of a variety of materials, but it must possess conductivity and grounding. When your flex PCB or flex-rigid PCB application demands restrictions on electromagnetic and/or electrostatic interference, you should employ EMI shielding. The shielding will vary based on the amount of EMI interface in the device, the conductivity requirements, and the degree of flexing the circuit will experience.
Because of the proliferation of wireless communication networks, such as mobile phones, earphones, and wireless printers, electromagnetic interference (EMI) is becoming a problem that can arise from a wide variety of sources, including those that are located outside of the electronic device itself. This can cause problems for electronic devices, equipment, and even entire systems. Thus, EMI shielding should be considered whenever it is required.
Design FPC and rigid-flex PCB Shielding: Considerations Factor
To protect a design from electromagnetic interference (EMI), it must first be encased on both sides in a layer of material that serves as a barrier against the EMI’s ability to absorb or radiate energy. Because these layers are connected to ground, any EMI that is present will be harmlessly dissipated.
Other Factor must be taken into account while selecting a shielding method and material.
Bend Requirements
Each type of shielding increases the overall thickness of the flexible circuit by a different amount. As the minimum bend capability is a function of the thickness, the design’s bend capabilities will be reduced or constrained. As part of the design and material selection process, the minimum bend radius and kind of bend required for shielded designs must be precisely defined and assessed.
Further limitations are imposed by the sort of bending that is required, which might be either static (bend just once to fit) or dynamic (repetitive bending). When compared to a static bend design, the minimum bend capability of a dynamic bend flex PCB application is significantly larger than what is possible with a static bend.
Controlled Impedance
In order to meet controlled impedance signal requirements, the shielding method that can be utilized must adhere to additional restrictions. In order to attain the regulated impedance values that are necessary, the shield (or shields) in question need to have electrical properties that not only fulfill the EMI criteria but also function as reference planes. Not all types of shielding can simultaneously fulfill both of these requirements.
EMi Shielding Materials for Flex and Rigid-flex PCBs
The purpose of EMI shielding is to absorb radio waves and other types of EMI. Today, electromagnetic interference (EMI) is becoming more and more of an issue; how can one select the most effective way of EMI shielding? Copper plating, conductive silver ink printing, and EMI shielding film bonding are all examples of EMI shielding methods that can be used in FPCs and rigid-flex PCBs.
Copper Plating: Copper plating is a conventional shielding technique that has historically been employed in the production of FPCs. While copper is not ideal for applications requiring a high degree of flexibility, typically cracking when the circuit is bent or folded and producing burrs during the die-punching process, it is nonetheless widely used. Thin copper layers with a crosshatched pattern would be an excellent choice for multilayer flex Boards.
Conductive Silver Ink:A good way for EMI shielding is to use silver ink. In today’s world, the use of metal silver ink and coating technology can ensure the flawless operation of high-frequency on-board chips as well as their lightning-fast data transfer speeds. Conductive silver ink is also occasionally utilized in the design of flex PCBs; nevertheless, its expense is the highest among these four technologies, and its processing requires the maximum amount of time.
Metal Housing: The use of metal housing as an EMI shielding solution is a time-honored practice that is most commonly seen on rigid PCB boards and very infrequently seen on flex circuits. Due to the fact that it is unable to satisfy the prerequisites for miniaturization, it is no longer useful in FPCs. As electronics get smaller, metal casing can no longer function properly on such a small scale. In addition to this, the specific sections of the FPC will lose their flexibility if the housing is made of metal.
EMI Shielding Film: The incorporation of EMI shielding material into the layouts of flexible printed circuit boards (PCBs) and rigid-flex boards is becoming increasingly common. The EMI shielding layer design gives the flex PCB the best flexibility and the thinnest overall thickness. Moreover, it has the lowest overall thickness. The cost of producing flex PCBs will be decreased when compared to silver ink printing and copper layer design, and the level of shielding capability will be increased to a greater extent.
There are numerous benefits associated with EMI shielding film, including performance in terms of shielding, flexibility, affordability, and processing lead time. It is possible to replace the copper layer design with EMI shielding film, which allows for cost savings without sacrificing the flexibility of the board. EMI shielding film improves the shielding performance for the transmission of high-frequency signals and provides high flexibility, which prevents circuits from breaking when bent.
How to design flex boards to avoid EM and RF interference
● lsolate high-speed and low-speed signals.
● Avoid placing vias in differential pairs as it leads to parasitic capacitance.
● Ground and power planes should be pulled back from the edge of the board.
● If the design calls for separated ground planes, ensure that they are joined at a single location.
● Make sure that the present return path is as short as it may possibly be. Because of this, the size of the current loop and thus the radiation are both reduced.
● Sharp angles in the conductive lines might cause fluctuations in the characteristic impedance as well as signal reflections.These sharp bendsshould be avoided using curved traces.
The requirements for shielding are essential for any type of circuit board, and flex PCBs are no exception to this rule. In order to furnish a shielding that is operational, dependable, and cost-effective. It is imperative to perform a comprehensive analysis of all of the electrical and mechanical design considerations. If you would want our assistance in decreasing EMl in the design of your board, please get in touch with us at [email protected], and we will provide a professional pcb engineer response to any questions or concerns you may have.
Uses of EMI Shielding Film in Flexible and Rigid-flex PCB Designs
When using flex circuits for certain applications, designers will always add EMI shielding film so they can better manage electromagnetic interference (EMI). A great number of electronic devices that make use of flexible circuits and rigid-flex PCBs are vulnerable to either absorbing or generating electromagnetic interference (EMI). If electromagnetic interference (EMI) is not properly regulated, it has the potential to have a detrimental effect on the performance of the design, and in the worst-case scenario, it could even prohibit the design from functioning at all. EMI shielding film can be used for a variety of purposes, including the following:
● GPS.
● Earphone.
● PC &Tablet.
● Mobile Phone.
● Infusion Pumps.
● Military Devices.
● Network Hardware.
● Patient Monitoring Systems.
● Magnetic Resonance Imaging (MRI).
Flexible and rigid-flex printed circuit boards always have a black film adhered to them if you are familiar with PCB and assembly manufacture. What is this movie? It is an EMI-blocking film. E.g. In the material roll of TATSUTA SF-PC5000/-C, this EMI film is comprised of five layers, from top to bottom, including a transfer film (PET) layer, an insulation layer, a metallic deposition layer, a conductive adhesion layer, and a protective layer (PET). Black and friction-resistant, the insulating layer is also colored black. Hence, it seems black.
Why Is EMI Shielding So Important in FPC and Rigid-flex PCBs ?
Electronic systems that are employed in crucial applications might be interfered with by electromagnetic interference (EMI). Examples include touch displays for industrial use, navigation and vehicle control systems, medical, military, and aerospace electronics, and public transportation systems. As we all know, rigid-flex and flexible PCB circuit boards are the main parts of these electronic gadgets. As a result, it is crucial to take electromagnetic interference Shielding into account while designing FPC and rigid-flex PCB.
There are many different factors that might contribute to electromagnetic interference, some of which are natural while others are the result of human activity. The aftermath can include anything from momentary disruptions and lost data to complete breakdown of the system and possibly even death.
● Natural Sources Electromagnetic Interference(EMI): Lightning and solar flares are two naturally occurring phenomena that have the potential to create electromagnetic interference. Problems caused by electromagnetic interference (EMI) can arise in older equipment that have EMI shielding materials that have worn out or that do not have any EMI shielding materials at all. In addition, interference can be caused by huge pieces of equipment, whether they radiate a strong signal or simply have a high volume. The employment of precision research applications can be complicated by the presence of stray magnetic or electric fields, which can be generated by electrical equipment and machinery, for example.
● Man-made Electromagnetic Interference(EMI): Interference will be caused by large, moving equipment such as elevators, heavy machinery, and HVAC equipment, as well as by vehicle traffic. Standard means of communication and generic radio transmissions are both capable of causing it.
EMI is, to put it succinctly, unavoidable. There is interference everywhere, and the fact that our electronic equipment do not take up more of it is a wonder of modern technology. This 21st-century marvel is known as EMI shielding.
How Should EMI Film Be Bonded ?
● Removing the protection layer on its bottom.
● Cutting the EMI as dimensional requirement.
● Stacking it at the right location on flex circuit.
● Laminating them together under heat and pressure.
The conductive adhesive flows and forms a link between the metallic deposition layer and the copper circuitry on the PCB, which ultimately results in the formation of an electrical connection serving as ground.
Summary
EMI shielding is an essential component in many different designs of flex PCBs, and it is this component that insures the overall performance of the finished product. Because of the many different methods and materials that may be used for shielding, it is possible to create efficient designs that meet all of the necessary electrical and mechanical standards.
By blocking radiation and interferences, EMI shielding helps reduce the consequences of electromagnetic interference (EMI). There is a wide variety of materials available for EMI shielding, including EMI film. The efficacy of the shielding is reliant on the nature of the material that was utilized in conjunction with the intensity of the signals. Contact JarnisTech, we are a PCB manufacturing and assembly factory, we can provide a wide pcb services, Cermaic PCB, Metal core PCB, Flex PCB and Special maerial PCB, Such as Rogers, Taconic, Isola etc., to find out more information about custom printed circuit boards and EMI shielding PCB design, please click this link.
Related Posts:
1. Selecting PCB Laminate Materials: A Comprehensive Overview
2. PCB Copper Trace Width and Space: Everything You Need to Know About Them
3. Which Types are Most Commonly Used in PCB Substrates?
4. What Is Fiberglass PCB and Why Fiberglass Used in PCB Manufacturing?
5. Standard PCB Thickness-Choosing the Correct Thickness for PCB