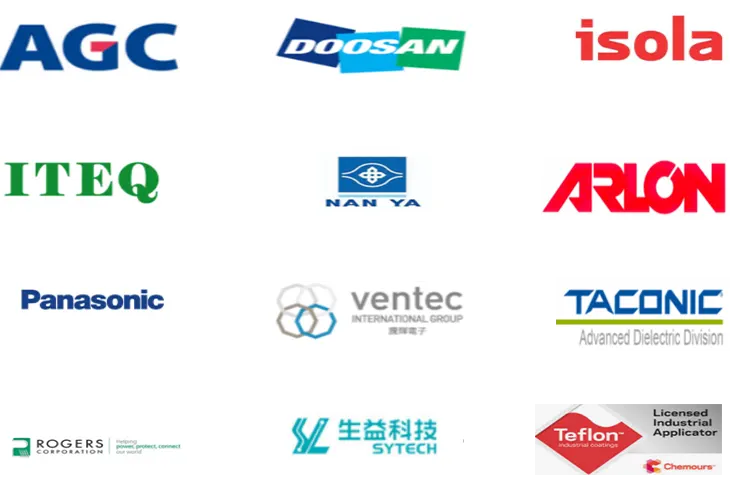
Printed Circuit Boards (PCBs) are the foundation of modern electronics, connecting and powering devices that define daily life and cutting-edge technology alike. The raw materials used in PCB fabrication—ranging from FR4 laminates and copper foils to advanced polymers—directly influence the performance, durability, and adaptability of these essential components. Choosing the right materials isn’t just about meeting specifications; it’s about aligning with the evolving demands of industries such as telecommunications, automotive, and consumer electronics.
This guide dives into the intricate details of PCB raw materials, offering insights into material properties, cost-performance balances, and the latest innovations shaping the industry. Whether you’re a manufacturer seeking to enhance your product’s reliability, a designer exploring new solutions for high-frequency applications, or a buyer navigating sourcing challenges, this comprehensive resource has you covered.
What Are PCB Raw Materials and Why Are They Essential?
PCB raw materials form the foundation of every printed circuit board, impacting their durability, functionality, and efficiency. The choice of materials used in a PCB isn’t just about the physical structure but directly affects the electrical and thermal performance, signal integrity, and overall reliability of the circuit board. These materials are not interchangeable—each type plays a very specific role in ensuring that PCBs perform as needed in demanding environments like consumer electronics, aerospace, automotive, and telecommunications. The materials used in a PCB are carefully selected based on their electrical conductivity, thermal resistance, flexibility, and the particular needs of the device in which the board will be used.
As we dive deeper into this, it’s important to understand the key materials that make up these PCBs, as well as why their characteristics matter. The raw materials impact circuit integrity, power management, and even the longevity of the final product. Now let’s break it down into the building blocks.
Understanding the Composition of PCB Raw Materials
PCB raw materials are the building blocks that give printed circuit boards their structure and functionality. They aren’t just “ingredients”—they are the unsung forces that make sure your devices work, from smartphones to satellites. Let’s break them down.
The core material of any PCB is typically the substrate—usually fiberglass or a composite material—which provides the board’s shape and support. This is often coated with a copper foil layer, which serves as the electrical pathway. These copper layers are then etched to form the circuit traces that power your devices. Between the copper layers, you’ll find prepreg (pre-impregnated) layers, made from resin and reinforcing fibers, which bind everything together.
Materials like ceramic substrates are also in the mix for specialized PCBs, offering higher thermal stability than traditional fiberglass-based ones. On the other hand, flexible PCB materials like polyimide have gained traction in designs that demand adaptability. These materials allow for the production of devices with dynamic, bendable structures, making them a go-to for foldable phones, wearable gadgets, and other cutting-edge products.
Here’s a quick look at some of the primary PCB materials you should know:
Material | Description | Applications |
Copper Foil | Thin sheets of copper used for circuit traces. | Found in all standard PCBs. |
FR4 (Fiberglass) | The most common PCB substrate material. | Consumer electronics, computers, etc. |
Prepreg (Resin) | Resin-soaked fiber layers that bond materials together. | Used to laminate multiple PCB layers. |
Polyimide | A flexible, high-temperature material. | Flexible PCBs in wearable electronics. |
Ceramic Substrates | High-thermal stability materials. | High-power applications (automotive, aerospace). |
As you can see, these raw materials serve different needs. The composition of PCB raw materials directly impacts how well a PCB performs, including its electrical conductivity, thermal resistance, and mechanical strength. Choosing the right material is no small task; it requires an understanding of not only the application but also the environmental demands the PCB will face.
Importance of PCB Raw Materials in Circuit Performance
The quality of the materials used in PCBs can make or break the performance of an entire circuit. It’s not just about the board’s structure but also how well it handles the electrical signals, heat, and physical stresses it’s exposed to during its life cycle.
For example, materials with low dielectric constants and low loss tangents ensure that signals travel efficiently with minimal interference. Copper foil provides low resistance, which means less energy is lost as heat, especially in high-speed circuits.
Selecting the right materials for a PCB ensures top-notch performance in areas like signal transmission and heat dissipation. High Tg laminates, such as advanced polyimides, maintain their stability even under intense thermal stress, making them a perfect fit for demanding applications. This is especially true for industries like automotive electronics, where components are exposed to fluctuating and extreme temperatures. These materials not only enhance durability but also ensure the board operates reliably under challenging conditions—proving their worth in situations where failure isn’t an option.
Let’s take a closer look at how different materials impact circuit performance:
Material | Effect on Performance | Applications |
Copper Foil | Low resistance, good signal transmission. | General-purpose PCBs. |
FR4 (Fiberglass) | Standard dielectric properties, excellent for most uses. | Consumer electronics, communication. |
Polyimide | High heat resistance, flexible, maintains signal quality. | Flexible and wearable electronics. |
Ceramic Substrates | High thermal stability, low loss. | Power electronics, automotive systems. |
These materials keep your circuits running smoothly and ensure they perform under pressure, whether you’re dealing with high-frequency signals in telecommunications or extreme heat in automotive systems.
Global Demand for PCB Raw Materials
With the proliferation of high-tech devices, the global demand for PCB raw materials has skyrocketed. The automotive, aerospace, and telecommunications sectors are driving much of this growth, and the need for reliable, high-quality materials has never been more pressing.
●Take the automotive industry as a case in point. The surge in electric vehicles (EVs) has ramped up the need for high-performance PCBs that can handle both high voltages and intense heat. Materials like ceramic-based PCBs and high-Tg laminates ensure that these systems can operate efficiently and safely under demanding conditions. In EVs, where the electronics must withstand fluctuating temperatures and harsh environments, these materials step up to the plate—ensuring that everything from battery management systems to infotainment operates without a hitch. Without these advanced materials, the reliability and performance of these critical systems would be severely compromised.
●Similarly, the aerospace sector demands materials that can withstand extreme conditions. Ceramic and polyimide-based substrates are commonly used in space applications where heat dissipation and durability are a must. These materials are designed to endure high radiation levels, which is why they’re favored for satellite systems and space exploration.
●The telecommunications sector, with its ever-growing need for 5G connectivity, requires high-frequency PCB materials that can handle the demands of fast data transmission. PTFE (polytetrafluoroethylene) laminates are gaining popularity in this space for their ability to minimize signal loss.
Key Types of PCB Raw Materials
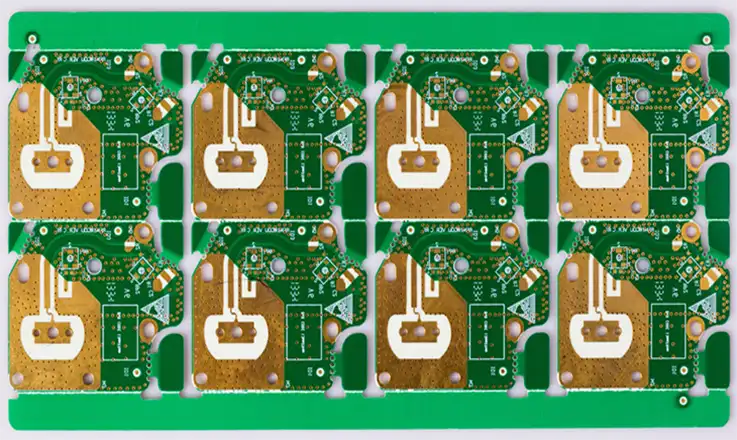
When you’re diving into the world of PCB manufacturing, understanding the raw materials you’re working with is half the battle. Choosing the right material isn’t just about performance; it’s about making sure your board can handle whatever the end-user needs it to do. From standard FR4 to specialized metal core and flexible designs, each PCB material serves a different function, offering unique strengths and performance characteristics.
In this section, we’ll break down the core materials that make up the majority of PCBs today and explore what makes each type stand out in the design and manufacturing process. We’ll also highlight the trends and advancements that are shaping the industry’s material choices.
Overview of FR4 and Its Variants
FR4 is the most common material used in rigid PCB manufacturing. Its blend of glass fiber and epoxy resin makes it strong, reliable, and cost-effective, which is why it’s the go-to choice for most standard PCBs. The fiberglass provides the strength needed for the PCB to withstand physical stress, while the epoxy resin binds everything together, ensuring that it remains stable at room temperature and in various electrical conditions.
While FR4 remains a go-to standard in the industry, it’s far from a one-size-fits-all material. There are several specialized variants of FR4 that cater to specific needs and applications. High-TG FR4, for example, is designed with a higher glass transition temperature, offering better thermal resistance for environments that experience higher heat. Low-loss FR4 is tailored for high-frequency applications, ensuring minimal signal loss, making it a good choice for RF and high-speed designs. Then, there’s halogen-free FR4, which is used in projects where environmental impact is a concern, like in the manufacture of eco-friendly electronics.
Variant | Description | Applications |
Standard FR4 | Fiberglass reinforced with epoxy resin, general-purpose. | Consumer electronics, automotive. |
High-TG FR4 | Higher glass transition temperature, more heat-resistant. | Servers, networking equipment. |
Low-Loss FR4 | Optimized for high-frequency use with lower loss factor. | Communication devices, RF equipment. |
Halogen-Free FR4 | No halogen content, environmentally friendly. | Green electronics, health-sensitive products. |
Metal Core PCB Raw Materials
When it comes to thermal management, metal core PCBs are often the go-to choice. Unlike traditional FR4 boards, which rely on external heat sinks or passive cooling systems, metal core PCBs integrate metal substrates into the PCB itself to help dissipate heat more efficiently.
These are particularly popular in industries like LED lighting, power electronics, and automotive electronics, where managing heat is a big challenge. By incorporating a metal core like aluminum or copper, these PCBs allow heat to spread evenly across the board, preventing overheating and ensuring the components stay within their optimal operating temperature.
-Aluminum PCB Materials-
Aluminum PCBs are made with an aluminum substrate layer, which provides excellent thermal conductivity. They’re especially useful in high-power applications, where heat management is a priority. Aluminum also offers a high thermal dissipation rate, making it ideal for LED modules and other high-power devices that need a robust cooling solution.
Aluminum-based PCBs are commonly chosen for lighting applications where effective heat dissipation is a priority. These substrates help draw heat away from sensitive components, ensuring that the system maintains consistent performance without overheating. This is especially useful in LED lighting, where efficient temperature management prevents premature failure and extends the overall lifespan of the product. By controlling the heat flow, aluminum-based PCBs can help maintain optimal brightness and system efficiency over time. Therefore, for applications like lighting, using aluminum-based PCBs means reliability and durability in the long run.
Feature | Description | Applications |
Material: Aluminum | Excellent thermal conductivity, light weight. | LED lighting, power electronics. |
Thermal Conductivity | Higher than traditional FR4, dissipates heat. | High-power automotive, LED modules. |
Copper Core PCB Materials-
Copper core PCBs take the heat-dissipating properties of metal core PCBs a step further. With a copper base layer, these PCBs offer even better thermal management than aluminum. Copper’s high thermal conductivity ensures that heat is spread evenly across the board, preventing hot spots that could damage sensitive components.
Copper core PCBs are commonly found in RF power amplifiers, automotive electronics, and other high-performance applications that require precise heat management and electrical signal integrity.
Feature | Description | Applications |
Material: Copper | Superior thermal conductivity for better heat dissipation. | High-frequency RF circuits, power supply units. |
Thermal Efficiency | Better heat dissipation, preventing overheating. | Power electronics, automotive systems. |
Ceramic PCB Raw Materials
Ceramic PCBs are used in applications that require both high thermal conductivity and electrical insulation. Unlike metals like aluminum and copper, ceramics provide superior heat resistance and are often used in high-temperature environments, such as aerospace and automotive industries. They are also favored in high-frequency circuits because they are dielectric materials that reduce signal loss.
Common ceramic materials include alumina and aluminum nitride, both of which offer exceptional heat resistance and are commonly found in high-performance electronics.
Material | Description | Applications |
Alumina (Al2O3) | High electrical resistance, excellent thermal properties. | Power electronics, aerospace applications. |
Aluminum Nitride (AlN) | Best heat dissipation properties, low dielectric loss. | LED lights, high-power electronics. |
Flexible and Rigid-Flex PCB Raw Materials
The demand for wearable technology and compact electronics has made flexible and rigid-flex PCBs incredibly popular. These boards are made from flexible substrates that can bend, twist, and fold without compromising the integrity of the PCB’s performance.
●Rigid-flex PCBs combine both rigid and flexible materials, offering the flexibility of a flex PCB and the strength of a rigid PCB. This makes them ideal for wearables, medical devices, and automotive systems, where space is limited, but high-performance standards must still be met.
●Flexible PCBs use polyimide or PET (polyester), and in rigid-flex designs, flexible copper-clad laminates (FCCLs) are often combined with rigid substrates like FR4 to create versatile, reliable PCBs.
Material Type | Description | Applications |
Flexible Polyimide | Flexible, high-temperature material, low thermal expansion. | Wearables, flexible sensors. |
Rigid-Flex FR4 | A hybrid combining rigid and flexible material. | Medical devices, aerospace applications. |
FCCL (Flexible Copper-Clad Laminate) | Flexible copper layers used in rigid-flex PCBs. | Flexible electronics, compact systems. |
Properties of PCB Raw Materials for High-Performance PCBs
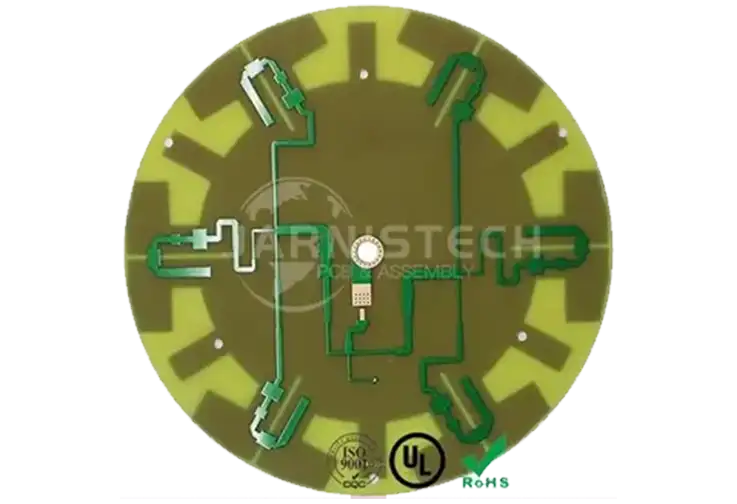
When designing a high-performance PCB, selecting the right raw materials is the cornerstone of ensuring that your board can withstand the demands of specific applications. Whether you’re working with power electronics, communication systems, or automotive technology, understanding the core properties of PCB materials will make or break your design.
High-performance PCBs must meet specific electrical, mechanical, and thermal standards. A deep understanding of these properties helps achieve the desired performance outcomes. This section covers the electrical, mechanical, and thermal characteristics of various PCB materials, emphasizing their influence on functionality and durability.
Electrical Properties of PCB Raw Materials
When selecting materials for PCBs, the electrical performance is influenced by factors like the dielectric constant.This property reflects how much electrical energy a material can store in an electric field. It’s particularly relevant for designs like RF circuits or systems involving fast data transfers. A material with the right dielectric constant ensures that signals are transmitted without significant losses or interference, leading to smoother operation in advanced electronic applications.
●Dielectric Constant: Materials with a low dielectric constant reduce signal loss and improve performance in high-speed circuits. For example, Teflon-based PCBs are often preferred in high-frequency communication systems due to their low dielectric constant, which minimizes signal attenuation.
●Loss Tangent: Loss tangent measures how much energy is lost as heat when an electrical signal passes through a material. For systems like 5G networks or military electronics, reducing this loss helps preserve signal quality. Materials such as PTFE (Polytetrafluoroethylene) and ceramic-filled epoxy are preferred for their low loss tangents. These materials allow signals to travel with minimal degradation, making them ideal for high-frequency or long-distance circuits where maintaining signal integrity over distance is necessary.
Material | Dielectric Constant | Loss Tangent | Applications |
PTFE | Low (2.0 – 2.5) | Very low | High-frequency, RF applications, aerospace. |
FR4 (Standard) | Moderate (4.0 – 5.0) | Moderate | General-purpose, consumer electronics. |
Ceramic-based | Low (3.0 – 4.0) | Low | Power electronics, military applications. |
When the material properties of a PCB are consistent, it becomes easier to manage impedance control, helping maintain uniform impedance across the entire board. This consistency minimizes signal degradation, which can happen in high-speed data transmission if impedance fluctuates. With more stable impedance, signals can flow smoothly, reducing data loss and ensuring that components in high-frequency applications, such as RF circuits or digital systems, perform reliably. Selecting materials that provide consistent impedance is a great way to support precision and efficiency in complex electronic systems.
Mechanical Strength and Stability
The mechanical durability of PCB raw materials ensures they withstand physical challenges while maintaining form and functionality. Properties such as dimensional stability, flexural strength, and peel resistance are particularly significant in scenarios involving vibration, bending, or varying temperatures. For instance, materials with high flexural strength reduce the risk of cracking under repeated stress, while stable dimensions prevent misalignments in multi-layer configurations. Additionally, robust peel resistance helps keep copper layers firmly adhered, even during mechanical strain or thermal expansion, contributing to the long-term reliability of the board.
●Peel Resistance: This is the ability of the PCB to resist the separation of layers under stress. Materials like polyimide offer better peel resistance compared to standard FR4 and are often used in flexible and rigid-flex PCBs. These materials are essential in devices that will undergo repeated bending or flexing, like wearable electronics.
●Dimensional Stability: As temperature or humidity changes, materials can expand or contract, leading to deformation or circuit damage. High-performance materials such as high-TG FR4 or polyimide are specifically designed to minimize this risk by offering enhanced dimensional stability, even in challenging environments.
Material | Peel Resistance | Flexural Strength | Applications |
Polyimide | High | High | Flexible PCBs, wearable devices. |
FR4 (High-TG) | Moderate | Moderate | Automotive, telecommunications. |
Aluminum PCB | High | Moderate | LED lighting, power electronics. |
For high-performance PCBs in automotive or industrial applications, dimensional stability is a must to ensure that the PCB maintains its functionality over a range of environmental conditions, including high temperatures and humidity. Materials like ceramic substrates and polyimide are designed to withstand harsher environments and maintain form and function.
Thermal Properties and Heat Management
When it comes to thermal properties, managing heat is one of the top priorities in high-performance PCB design. PCBs used in power electronics, automotive applications, and LED lighting must effectively dissipate heat to prevent overheating, which can cause failure or reduced performance.
Thermal conductivity is what keeps a PCB from heating up like a baked potato in the oven. Materials with solid heat transfer capabilities, like aluminum and ceramic blends, act like heat highways, moving energy away from components that would otherwise fry under pressure. This ensures electronics can handle the heat without breaking a sweat, whether it’s a high-powered LED or a beefy power circuit. By avoiding those sizzling hotspots, these materials keep everything cool under the hood, giving devices a longer run and better efficiency.
●Aluminum and copper-based PCBs are commonly used in high-power applications where heat management is essential. These metals have excellent thermal conductivity, making them perfect for applications like LED lighting where heat needs to be quickly dissipated.
●Ceramic PCBs, such as aluminum nitride (AlN) and silicon carbide (SiC), are known for their outstanding thermal conductivity and are typically used in high-power applications like automotive electronics or power conversion circuits.
Material | Thermal Conductivity | Applications |
Aluminum PCB | High (~200 W/mK) | LED lighting, power supplies. |
Copper PCB | Very high (~400 W/mK) | Power electronics, RF circuits. |
Ceramic PCB (AlN) | Very high (~170 W/mK) | Power electronics, automotive systems. |
FR4 | Low (~0.3 W/mK) | Consumer electronics, general-purpose. |
Thermal management materials in PCBs serve as the backbone for handling demanding applications. For instance, copper core PCBs are a top choice in power converter systems, where heat dissipation can make or break performance. These materials are designed to channel heat away from sensitive components, reducing the risk of thermal stress and maintaining stable operations over time. This approach not only prevents overheating but also helps extend the lifespan of the device, making it well-suited for high-intensity, long-term use.
Innovations in PCB Raw Materials for Advanced Designs
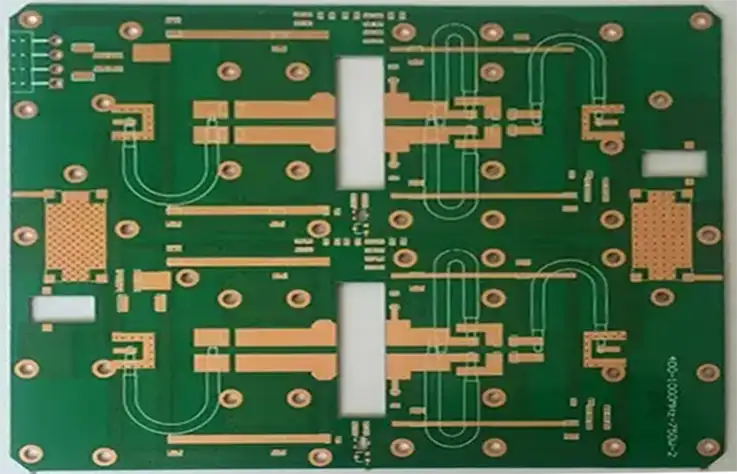
In the ever-evolving world of PCB design, staying ahead of the curve requires embracing cutting-edge materials that not only meet current demands but also anticipate future needs. With miniaturization, high-speed data transmission, and thermal management becoming central to advanced PCB applications, we must keep their finger on the pulse of innovation. Let’s take a deep dive into the innovative materials that are pushing the boundaries of what’s possible in PCB design and enabling next-generation electronic devices.
Emerging High-Density Interconnect (HDI) Materials
As devices become more compact and feature-packed, HDI PCBs are leading the way. These boards pack more interconnections into a smaller space, which allows for miniaturized designs without compromising on performance. HDI technology relies on using advanced materials that provide higher levels of signal integrity and electrical performance.
High-Performance HDI Substrates-
High-performance FR4 and ceramic-filled epoxy materials are paving the way for advanced HDI designs. Specifically crafted to handle the demands of higher frequencies, these materials fit seamlessly into applications like smartphones, wearables, and medical devices. Their lower dielectric constant and minimal signal loss ensure smooth high-speed data transmission, even in tightly packed circuit layouts. This makes them a go-to for designers tackling next-gen electronics, where every bit of performance needs to be squeezed out without compromising reliability.
Miniaturization & Thermal Management-
As HDI designs push the limits of miniaturization, thermal management becomes an increasing concern. Materials with higher thermal conductivity are being developed to manage heat more effectively in compact designs. Copper-filled polymers and ceramic-based HDI substrates are becoming go-to solutions for power-hungry devices like power amplifiers and 5G antennas, where overheating can lead to performance degradation.
Material | Dielectric Constant | Thermal Conductivity | Applications |
Ceramic-filled Epoxy | Low (~3.0) | Moderate (~1.0 W/mK) | Wearables, medical devices, RF circuits. |
High-TG FR4 | Moderate (~4.5) | Low (~0.3 W/mK) | General HDI, consumer electronics. |
Copper-filled Polymers | Low (~3.2) | High (~10 W/mK) | 5G networks, power electronics. |
These advanced materials help us create high-density interconnections in tighter spaces, enabling advanced miniaturized designs. The ability to pack more functionality into smaller devices is driving the growth of HDI PCBs in industries ranging from telecommunications to consumer electronics.
Graphene and Advanced Polymers
Graphene, an ultra-thin material with remarkable properties, has captured the attention of the electronics industry. With its exceptional electrical conductivity, mechanical strength, and thermal properties, graphene is poised to revolutionize PCB manufacturing. But how does it stack up against traditional materials, and how is it used in PCB designs?
Graphene in High-Speed Applications-
Graphene’s outstanding conductivity and flexibility make it a standout option for high-speed data transmission technologies. Researchers are actively investigating its application in interconnects for 5G infrastructure and advanced computing systems. Thanks to its ability to handle rapid signal processing with minimal energy loss, graphene offers a promising pathway for improving performance in scenarios where quick and efficient data handling is a must. Its potential to streamline data flow while keeping signal degradation to a minimum is reshaping expectations for cutting-edge electronics.
Advanced Polymers for Flexible Designs-
Advanced polymers, such as polyimide and liquid crystal polymer (LCP), are already in use for flexible and rigid-flex PCBs. These materials are being combined with graphene to create next-generation flexible PCBs that can handle higher frequencies and dissipate heat more effectively. Polyimide’s flexibility, combined with graphene’s thermal conductivity, enables the creation of flexible PCBs for applications like wearables and medical sensors.
Material | Electrical Conductivity | Flexibility | Applications |
Graphene | High (~106 S/m) | Moderate | High-speed data, 5G networks. |
Polyimide | Moderate (~10-100 S/m) | High | Wearables, medical sensors. |
Liquid Crystal Polymer | Moderate (~10-100 S/m) | High | Flexible PCBs, high-frequency applications. |
As these materials continue to evolve, graphene and advanced polymers are expected to drive the future of flexible electronics, making it easier to create lightweight, high-performance designs for consumer electronics, automotive systems, and wearable technology.
Laser-Drilled and Microvia-Compatible Laminates
As demand for more intricate, high-density PCBs continues to rise, so does the need for laser-drilled microvias. Microvias are tiny holes used to connect multiple layers of a PCB, enabling the creation of high-density interconnects (HDI). These interconnects make possible advanced designs that require precision and smaller components. Laser drilling ensures the fine accuracy necessary for these small yet intricate connections. It’s a technique commonly used in high-performance electronics, allowing for compact designs in devices like smartphones, wearables, and medical equipment.
Laser-Drilled Microvias-
Laser drilling has revolutionized the way microvias are produced. Unlike traditional methods, which can leave inconsistencies, laser drilling ensures a more precise, efficient process, leading to better signal integrity and reduced electrical noise. These microvias can be designed at a much smaller size, allowing for increased component density.
Materials for Microvia-Compatible Laminates-
For laser-drilled microvias to perform effectively, the laminate material must support high thermal cycling resistance and provide consistent performance across multiple layers. High-TG FR4, polyimide, and ceramic-filled epoxy are often chosen for these designs due to their high thermal stability and ability to handle the extreme conditions of laser drilling.
Material | Laser-Drill Compatibility | Thermal Stability | Applications |
High-TG FR4 | High | Moderate | Standard HDI designs, consumer electronics. |
Polyimide | High | Very high | Flexible PCBs, automotive applications. |
Ceramic-filled Epoxy | High | High | Power electronics, high-frequency designs. |
Laser-drilled microvias are now used extensively in applications that require high-density connections, such as smartphones, medical devices, and 5G communications. These materials allow us to pack more functionality into smaller spaces, meeting the growing demand for more compact and high-performance PCBs.
Selecting the Best PCB Raw Materials for Your Project
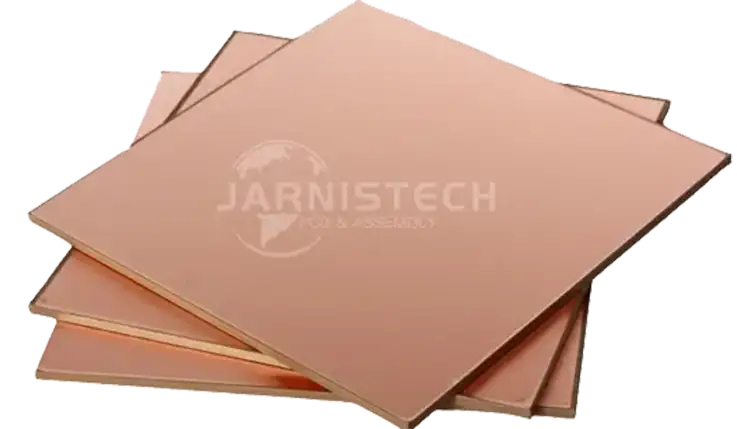
When selecting materials for PCB design, the choices you make are directly tied to the performance, efficiency, and cost-effectiveness of the end product. Every project, whether it’s a consumer device, medical equipment, or automotive system, requires a careful balance of various material properties. These materials determine not only how the board performs during use but also how easy and affordable the manufacturing process will be. In this section, we’ll cover the main factors involved in material selection, providing the insight needed to navigate through the decision-making process and make the right choices for your next PCB design.
Factors to Consider When Choosing PCB Raw Materials
Selecting the right PCB raw materials requires navigating a web of considerations—from managing costs to understanding the material’s performance characteristics and ensuring environmental compliance. It’s about finding a sweet spot that aligns with project needs without blowing the budget. Let’s break down the major factors that shape the material selection process:
1. Cost and Budget Constraints-
The cost of PCB raw materials varies significantly depending on the material type, performance characteristics, and source. While FR4 remains one of the most cost-effective choices for many designs, high-performance materials like ceramic-filled epoxies and polyimide laminates will carry a higher price tag. However, their advanced properties—like better thermal stability and signal integrity—may justify the additional expense if your design requires it.
2. Electrical and Thermal Performance-
For high-speed applications, the dielectric constant and signal loss of a material are key factors that will influence the choice of materials. Copper-clad laminates (CCLs) and ceramic-based substrates are commonly used in high-frequency PCBs for their excellent electrical conductivity and low loss properties. On the thermal side, materials with high thermal conductivity, such as copper-filled substrates or aluminum core PCBs, are ideal for designs that handle significant power loads, like LED drivers and automotive electronics.
3. Environmental and Regulatory Compliance-
In today’s market, environmental impact and regulatory compliance play a large role in decision-making. Industries like electronics and automotive must meet RoHS (Restriction of Hazardous Substances) standards, which limit materials such as lead and cadmium. With growing environmental concerns, the use of lead-free soldering and halogen-free materials in PCB designs is becoming more common.
Example Case: When designing wearable devices, selecting flexible PCBs made from polyimide ensures the material meets RoHS guidelines while also supporting the lightweight, bendable nature required for this application.
Matching PCB Raw Materials to Specific Applications
Different applications demand different performance characteristics from PCB raw materials. Whether you’re designing consumer products, industrial equipment, or military-grade technology, selecting the right material to match the specific needs of your application ensures the final product performs as expected, with durability and efficiency in mind.
●Automotive Electronics-
Automotive electronics face unique challenges, including extreme temperature variations and high vibration. Materials like aluminum core PCBs and high-TG FR4 are commonly chosen for their robustness and thermal management properties. Aluminum-based substrates are particularly effective in managing heat in automotive power systems, such as electric vehicle (EV) battery management circuits or LED lighting systems.
●Industrial and Medical Electronics-
In industrial applications, materials that can withstand high-frequency signals and harsh environments are a must. Ceramic substrates and PTFE-based options are well-suited to handle challenging conditions, ensuring stable signal transmission and effective thermal management. In the medical sector, materials must meet biocompatibility standards while ensuring long-term reliability. Polyimide, known for its flexibility and thermal stability, is commonly selected for medical devices, offering durability through multiple sterilization cycles.
●Consumer Electronics-
When designing consumer electronics such as smartphones or smart home devices, there’s a need to strike the right balance between performance and cost. FR4 is often chosen for its adaptability and affordability, making it a suitable option for devices that don’t need extreme performance but still require reliable durability and effective signal management. This material serves as a great choice when you want to keep costs down while ensuring that the product meets performance needs.
Partnering with Reliable Suppliers
Once you’ve identified the materials you need, the next step is sourcing them from reliable suppliers. Having a trusted partner ensures you receive high-quality raw materials that meet your specifications and timelines. Here’s how to navigate the supplier landscape.
1. Sourcing Copper-Clad Laminates (CCLs)-
When sourcing copper-clad laminates (CCLs), it’s best way to choose suppliers that offer consistent copper foil thickness and prepreg quality. Choose for manufacturers who specialize in premium-quality CCLs to guarantee that your PCBs have consistent electrical performance and mechanical strength. Companies like Isola Group and Taiwan Union Technology offer high-performance CCLs suited for automotive and telecommunications applications.
2. Understanding Prepreg and Its Importance-
Prepreg materials are integral to the bonding process in multi-layer PCBs. When choosing suppliers, ensure the prepregs they offer align with the mechanical and thermal needs of your project. For example, high-TG prepregs are perfect for high-heat applications, such as in automotive electronics, while low-TG prepregs are ideal for consumer products that don’t demand such extreme thermal performance.
3. Vendor Quality Assurance-
Working with a supplier that provides certified quality assurance (QA) is a must. ISO 9001 and UL certifications can serve as indicators that the supplier adheres to internationally recognized quality management standards, ensuring that your materials meet both your performance and regulatory requirements.
Pro Tip: Always ask for material samples before making bulk purchases, so you can verify the thermal and electrical properties, as well as the overall consistency of the raw materials.
Supplier | Material Type | Specialization | Certification |
Isola Group | CCLs, FR4 | High-performance laminates | ISO 9001, UL |
Taiwan Union Tech | CCLs, High-TG FR4 | Automotive, telecom | ISO 9001, UL |
Rogers Corporation | PTFE-based materials | High-frequency, high-performance PCBs | UL, RoHS-compliant |
Comparing Costs and Performance of PCB Raw Materials
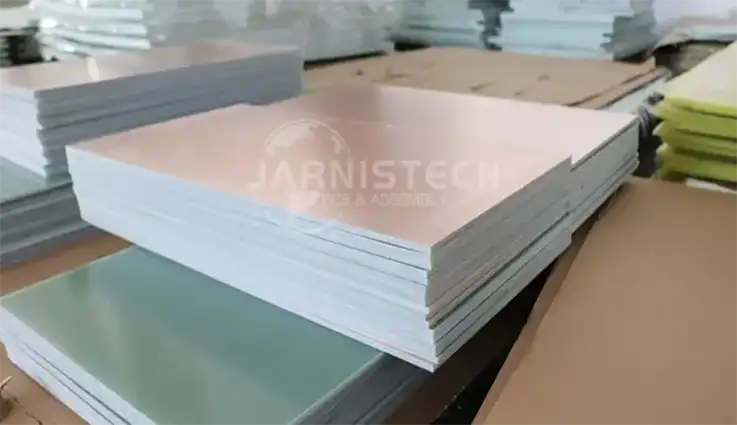
When it comes to choosing the right raw materials for PCBs, we often face a balancing act between cost-effectiveness and performance. Factors like material type, application demands, and overall lifecycle expenses must be carefully evaluated. This section provides a deep dive into material cost analysis, the long-term financial implications of material choices, and practical sourcing tips to optimize spending without compromising on quality.
Cost Analysis of Common PCB Raw Materials
One of the most debated aspects in PCB manufacturing is the trade-off between price and performance. FR4, the industry’s standard laminate, is a go-to option for many designs due to its affordability and satisfactory performance in general applications. However, when projects require high-frequency laminates or materials with enhanced thermal properties, the costs can quickly escalate.
FR4 vs. High-Frequency Laminates-
●FR4 Laminates: These materials are known for their versatility in standard PCBs. They balance electrical insulation, mechanical stability, and cost, making them suitable for consumer electronics and basic industrial applications. The average cost of FR4 laminates hovers around $10 to $20 per square meter, depending on thickness and specifications.
●High-Frequency Laminates: In contrast, these laminates, such as Rogers 3000 series or PTFE-based materials, are designed for applications demanding superior signal integrity and minimal loss at high frequencies. Used in 5G networks, aerospace systems, and radar equipment, their prices can range from $100 to $300 per square meter, reflecting their advanced properties.
Material Type | Typical Cost ($/m²) | Applications |
FR4 Standard | $10–$20 | Consumer electronics, automotive |
High-Frequency Laminates | $100–$300 | 5G, telecommunications, aerospace |
Metal Core Substrates | $50–$150 | Power electronics, LED lighting |
Total Cost of Ownership in PCB Manufacturing
When focusing only on the initial material costs, it’s easy to overlook other expenses that can pile up over time. The Total Cost of Ownership (TCO) approach looks beyond the upfront price and takes into account factors like performance reliability, reducing waste, and ongoing maintenance costs. By considering all these elements together, businesses are better prepared for long-term financial planning, especially when scaling up production. This approach helps ensure that the total financial picture is clear, avoiding unexpected expenses down the line and helping companies budget more effectively.
Balancing Initial Costs with Long-Term Benefits-
●Material Efficiency: Choosing high-performance materials often reduces waste during manufacturing. For example, laminates with better peel strength and dimensional stability yield higher-quality boards, minimizing rework and scrap rates.
●Reliability in Extreme Conditions: In industries like automotive and industrial electronics, materials such as polyimides or ceramics may have a higher upfront cost but significantly lower the risks of failure in high-temperature environments. Over time, this reliability translates into lower warranty claims and customer dissatisfaction.
Example: A telecom company opted for PTFE-based laminates for its high-speed routers. Although these laminates were ten times more expensive than FR4, their performance minimized signal loss, reduced downtime, and enhanced customer satisfaction—offsetting the initial expense over the product’s lifecycle.
Sourcing Strategies for Cost-Effective Materials
Navigating the market for PCB raw materials requires a strategic approach to sourcing. With increasing pressure from global supply chain disruptions and fluctuating material costs, we need actionable strategies to maintain quality while keeping expenses in check.
Tips for Reducing Costs Without Compromising Quality-
1.Bulk Purchasing Agreements: Buying in larger quantities often opens the door to discounted rates. For commonly used materials like FR4 laminates and copper foils, long-term contracts with suppliers can lock in stable prices, safeguarding against market volatility.
2.Supplier Audits and Certifications: Working with certified suppliers ensures consistent material quality and minimizes the risk of defective batches. For example, vendors certified under ISO 9001 or IPC-4101 standards are more likely to deliver reliable products.
3.Localized Sourcing: While international suppliers might offer tempting lower prices, sourcing materials locally can often be more beneficial in the long run. Local sourcing cuts down on shipping expenses, reduces delivery times, and helps avoid the headaches that come with customs delays. This is especially useful for high-demand materials like copper-clad laminates (CCLs) and prepregs, where timing and reliability are a must. In the end, getting supplies closer to home can smooth out the process and save some serious cash, all while keeping things running without a hitch.
4.Material Substitution: For cost-sensitive applications, explore alternative materials that offer adequate performance. For instance, aluminum cores might replace copper cores in certain thermal management applications.
Interactive Tools for Choosing PCB Raw Materials
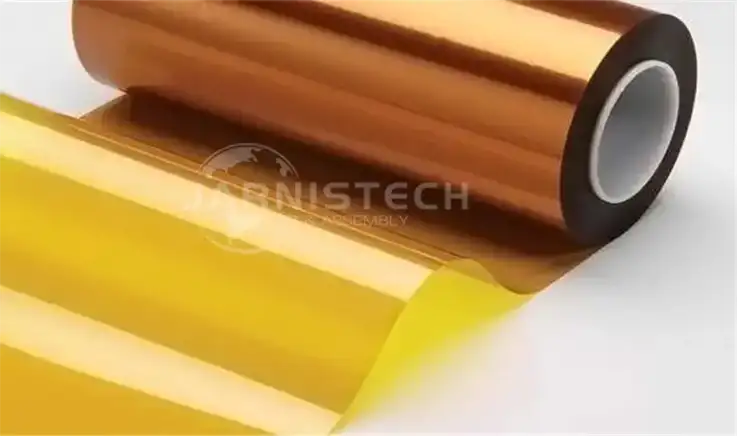
Navigating the complexities of selecting PCB raw materials can be daunting. With advancements in technology, interactive tools are streamlining the decision-making process for engineers, designers, and procurement teams. These tools help bridge the gap between application requirements and material capabilities, providing data-driven insights and eliminating much of the guesswork.
Whether you’re comparing laminate properties or calculating cost projections, leveraging digital solutions simplifies the task. Let’s explore some of the most impactful tools in this domain.
PCB Material Selector Tool
Selecting the right materials can feel like finding a needle in a haystack, especially when juggling diverse application demands. A PCB Material Selector Tool serves as an interactive guide, helping users match their specific needs with suitable raw materials. These tools often include filters for dielectric properties, thermal stability, mechanical strength, and environmental compliance.
How It Works-
●Input Parameters: Users provide key details such as operating frequency, temperature range, and application type (e.g., automotive, consumer electronics).
●Material Matching: The tool cross-references these parameters with a database of materials, presenting options that meet or exceed the criteria.
●Results and Recommendations: Detailed material profiles, including datasheets, pricing tiers, and supplier details, are provided for comparison.
Example: A telecom company designing a 5G base station might use a selector tool to find laminates with low dielectric loss and high thermal conductivity. Such tools can narrow options from hundreds of materials to a curated list of top contenders.
PCB Cost Estimation Calculator
Budget constraints often drive material decisions. A PCB Cost Estimation Calculator empowers users to forecast expenses by considering both raw material prices and manufacturing costs. These calculators are especially helpful for prototyping and small-scale production, where cost overruns can quickly spiral.
Key Features-
●Bill of Materials (BOM) Integration: Upload BOM data to calculate material costs, factoring in quantities and supplier rates.
●Customization Options: Adjust specifications such as layer count, board thickness, and copper weight to see how changes impact the budget.
●Shipping and Lead Time Insights: Some calculators incorporate logistics data, helping users estimate total project costs, including delivery fees.
Factor | Impact on Cost | Example |
Material Selection | High-frequency laminates cost more than FR4 | Rogers 4350 laminate for advanced RF circuits |
Layer Count | Multilayer boards increase costs | 8-layer PCB vs. 2-layer PCB |
Customization Features | Embedded components raise costs | Integrated capacitors for miniaturized designs |
Challenges and Opportunities in the PCB Raw Materials Market
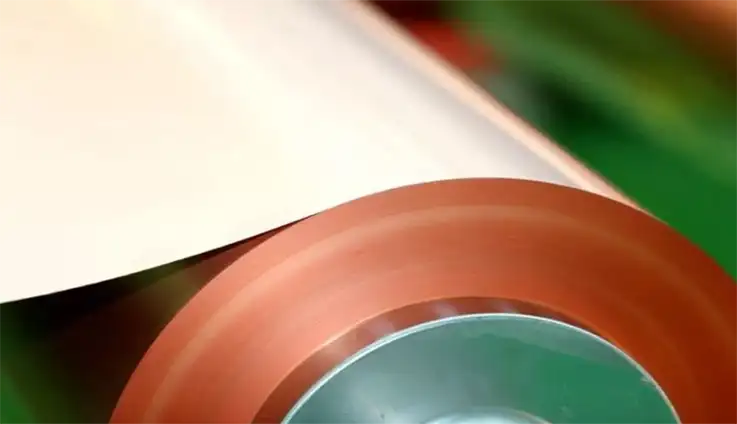
The PCB raw materials market is in a constant state of flux. Factors like rising material costs, supply chain disruptions, and the increasing demand for eco-friendly alternatives are making it harder for PCB manufacturers to keep costs low while maintaining high product quality. However, these challenges also bring forth opportunities, especially for those who are quick to adapt and leverage innovative solutions. In this section, we’ll dive into the hurdles faced by manufacturers and how they can turn these challenges into stepping stones for growth.
Managing Rising Costs of PCB Raw Materials
The price of PCB raw materials has seen significant fluctuations, particularly in key materials such as copper, resins, and substrates. As these raw materials are heavily influenced by global commodity prices, it’s essential for we to have strategies in place to manage cost increases without compromising product quality.
Strategies to Handle Fluctuations in Copper and Resin Prices-
The rising costs of copper—one of the most commonly used materials in PCB manufacturing—have been particularly disruptive. Copper prices are often affected by global market conditions, such as changes in demand from the automotive industry or fluctuations in supply from mining regions. Additionally, epoxy resins and prepreg materials have also become more expensive due to the rising costs of raw petrochemicals.
To manage these price fluctuations, manufacturers can adopt the following strategies:
●Supplier Diversification: By establishing relationships with multiple suppliers, PCB manufacturers can reduce their dependency on one source and potentially negotiate better rates.
●Material Substitution: Exploring alternative materials that can provide similar performance characteristics without the high price tag can be an effective cost-cutting measure. For example, aluminum-based substrates can sometimes replace copper cores in certain applications.
●Long-Term Contracts: Entering into long-term supply agreements can help stabilize costs, as it often locks in pricing for a set period, shielding manufacturers from volatile price changes.
Case Example:
When the cost of copper spiked in 2021 due to increased demand from the electric vehicle (EV) industry, many automotive PCB manufacturers shifted towards aluminum core PCBs for their heat dissipation properties at a lower cost. This not only helped reduce material costs but also aligned with the growing trend of eco-friendly designs in the automotive sector.
Addressing Supply Chain Disruptions
The global supply chain has faced significant disruptions in recent years, particularly in the wake of the COVID-19 pandemic. For PCB manufacturers, these disruptions can cause delays in the delivery of critical raw materials such as copper-clad laminates (CCLs), prepreg materials, and resins. These supply chain issues can result in extended lead times and increased production costs.
Solutions for Securing Consistent Supplies of Critical Materials-
To ensure that production doesn’t come to a halt, PCB manufacturers can adopt several strategies to address these supply chain challenges:
●Inventory Management: Maintaining a safety stock of essential raw materials can help manufacturers avoid delays during periods of supply chain disruption. However, this comes with the challenge of managing inventory costs effectively.
●Local Sourcing: Sourcing materials from local suppliers rather than international ones can mitigate the risks associated with long lead times. While the cost of local sourcing might be slightly higher, it ensures that production runs smoothly without delays.
●Supply Chain Transparency: By working closely with suppliers to ensure full transparency throughout the supply chain, manufacturers can better anticipate potential delays and take preemptive action.
Case Example:
PCB manufacturers in the consumer electronics sector faced significant challenges when prepreg shortages affected production timelines. By establishing closer relationships with local suppliers and investing in digital supply chain management systems, these companies were able to navigate delays and even reduce costs by streamlining their procurement processes.
Opportunities in Eco-Friendly PCB Raw Materials
As environmental concerns continue to grow, the demand for eco-friendly PCB raw materials has surged. Consumers and businesses alike are increasingly seeking sustainable solutions that minimize their environmental impact while maintaining high performance. The development of halogen-free and biodegradable materials has opened new opportunities for PCB manufacturers looking to stay ahead of the curve.
Development of Halogen-Free and Biodegradable Options-
●Halogen-Free Materials: Many traditional PCB laminates contain halogens like bromine, which can release toxic gases when incinerated. As RoHS (Restriction of Hazardous Substances) regulations continue to tighten, halogen-free materials have gained popularity. Epoxy-based and polyimide resins that don’t contain halogens are now commonly used for high-performance PCBs.
●Biodegradable Materials: The development of biodegradable PCB materials is still in its early stages, but there is growing interest in creating green PCBs that break down naturally after their lifecycle ends. Many companies are exploring biodegradable plastics and plant-based composites that could replace traditional plastic substrates and prepregs.
Opportunities in the Green Movement-
The shift toward eco-friendly PCB materials presents several opportunities for PCB manufacturers:
●Brand Differentiation: Companies that adopt green manufacturing practices can set themselves apart from competitors and appeal to environmentally conscious customers.
●Regulatory Compliance: As global regulations tighten around electronic waste and hazardous materials, being an early adopter of eco-friendly materials ensures compliance with future regulations and reduces the risk of costly fines.
Case Example:
A growing number of automotive companies are demanding halogen-free PCBs for electric vehicles (EVs) due to environmental concerns and stricter compliance with RoHS and WEEE (Waste Electrical and Electronic Equipment) regulations. Companies like Panasonic and Tesla have already begun adopting eco-friendly PCB materials in their EV designs to align with sustainability goals.
Environmental Benefits of Eco-Friendly PCB Materials-
Material Type | Benefit | Applications |
Halogen-Free Epoxy | Reduces environmental impact | Consumer electronics, automotive |
Biodegradable Plastics | Reduces waste and promotes sustainability | Packaging, wearable devices |
Polyimide-based Resins | Excellent thermal stability and eco-friendly | High-temperature applications in industrial sectors |
FAQ on PCB Raw Materials
What are the environmental impacts of commonly used PCB raw materials?
PCB raw materials such as FR4 laminates and copper foils can have environmental consequences if not properly managed during production and disposal. Issues include the release of hazardous substances and challenges with recycling halogenated materials.
How do PCB raw materials affect electromagnetic interference (EMI) shielding?
The choice of materials, such as copper or specialized laminates, directly impacts the ability of the PCB to shield against EMI, especially in high-frequency or sensitive applications.
What advancements have been made in biodegradable PCB materials?
Research into biodegradable substrates like paper-based laminates and non-toxic adhesives is gaining traction as the industry shifts towards more eco-friendly solutions.
How do humidity and moisture absorption impact PCB raw material performance?
Materials like FR4 are susceptible to moisture absorption, which can compromise electrical insulation and cause delamination under thermal stress.
Are there region-specific preferences for certain PCB raw materials?
Yes, regions with strict environmental regulations, such as the EU, often prefer halogen-free or lead-free materials, while other areas may prioritize cost over environmental compliance.
What testing methods are used to evaluate the reliability of PCB raw materials?
Techniques such as thermal cycling, peel strength testing, and dielectric breakdown testing are standard for assessing material reliability under operating conditions.
What are the cost implications of choosing high-frequency PCB materials over standard FR4?
High-frequency materials like PTFE laminates are significantly more expensive than FR4 but offer superior performance in RF and microwave applications, making them ideal for specific industries.
How do raw material choices impact the recyclability of PCBs?
Non-halogenated materials and metals like copper are more easily recyclable, while materials with mixed polymers or specialized coatings can complicate the recycling process.
Related Posts:
1. Selecting PCB Laminate Materials: A Comprehensive Overview
2. PCB Copper Trace Width and Space: Everything You Need to Know About Them
3. Which Types are Most Commonly Used in PCB Substrates?
4. What Is Fiberglass PCB and Why Fiberglass Used in PCB Manufacturing?
5. Standard PCB Thickness-Choosing the Correct Thickness for PCB