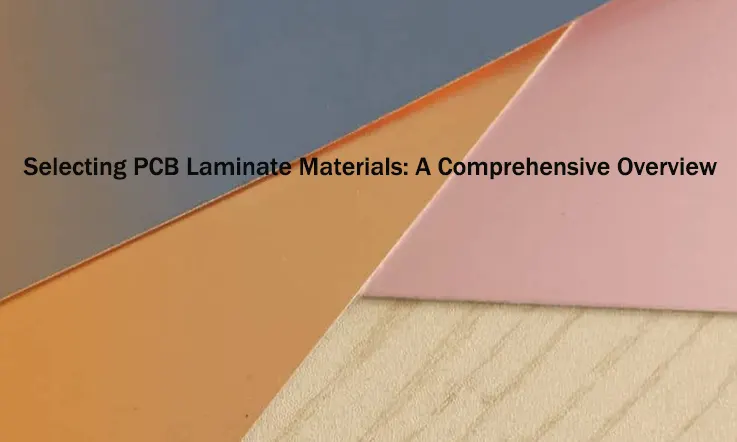
Welcome to our comprehensive guide, where we provide valuable insights into selecting the ideal material for your PCB. As a leading PCB manufacturer, we understand the importance of choosing the right PCB laminate material. In this guide, we will meticulously explore the diverse range of PCB laminate materials currently available in the market.
Whether you are a seasoned engineer or a beginner, we invite you to delve into the world of PCB laminates and expand your knowledge in this crucial aspect of PCB fabrication.
What is Laminate in PCB?
In the context of PCB (Printed Circuit Board) manufacturing, a laminate refers to the base material used to construct the PCB. It is a composite material composed of multiple layers, typically consisting of a substrate and a copper foil layer. The laminate serves as the foundation for the PCB, providing mechanical support and electrical insulation between the different circuit layers.
The substrate material in the laminate, often made of fiberglass-reinforced epoxy resin (FR-4), provides structural integrity and stability to the PCB. It is a non-conductive material that acts as an insulator, preventing electrical shorts between the copper layers.
The copper foil layer, bonded to the substrate, forms the conductive pathways and traces on the PCB. It allows for the flow of electrical signals throughout the board, connecting various components and circuitry.
Laminates can vary in thickness, dielectric constant, and other properties, depending on the specific requirements of the PCB design and its intended application. Different types of laminates offer distinct characteristics, such as high-frequency performance, thermal conductivity, or flexibility, catering to a wide range of PCB design needs.
Overall, the laminate is a critical component in PCB fabrication, providing the necessary structural integrity, electrical insulation, and conductive pathways required for the proper functioning of the circuit board.
PCB Laminate Materials for PCB Manufacturing
PCB (Printed Circuit Board) laminate materials are essential in the manufacturing of PCBs. They provide the mechanical base and electrical interconnection for the components of the electronic devices. The choice of laminate material affects the performance, reliability, and cost of the final product. Here are some of the most common PCB laminate materials:
FR-4
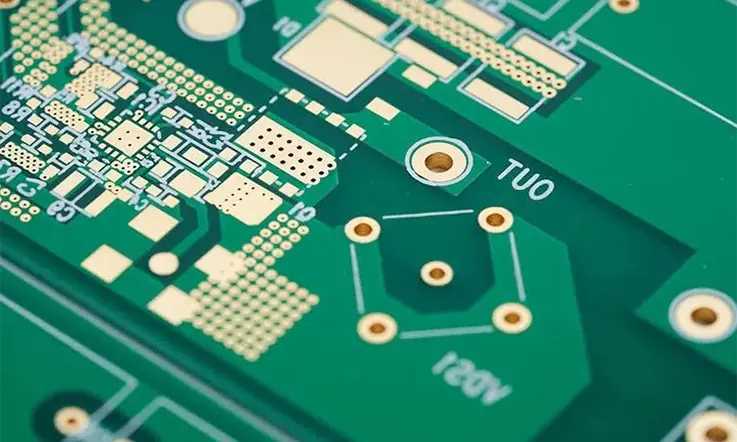
This is the most widely used material in PCB manufacturing. FR-4 is a composite material composed of woven fiberglass cloth with an epoxy resin binder. The “FR” stands for “flame retardant”. It offers a good balance of electrical properties, mechanical strength, cost, and performance.
High-Temperature Laminates (e.g., Polyimide)
These materials are used for applications requiring high operating temperatures, such as in aerospace and automotive industries. Polyimide laminates are known for their thermal stability, good chemical resistance, and excellent mechanical properties.
PTFE (Teflon)
This is used for high-frequency applications due to its low dielectric constant and low signal loss characteristics. However, it’s more difficult to work with and is more expensive than FR-4.
CEM (Composite Epoxy Material)
CEM materials are similar to FR-4 but have a mixture of woven glass and non-woven glass fibers. Common types include CEM-1 and CEM-3. They are less expensive and have slightly different electrical properties.
BT-Epoxy
BT-Epoxy is a thermoplastic that has lower moisture absorption and better heat resistance than FR-4. It’s often used for IC substrates.
Aluminum (Metal Core PCBs)
Aluminum-backed PCBs are used for high power applications and LED lights where heat dissipation is a concern. The aluminum is used as a heat sink to help dissipate heat away from the circuit.
Rogers Material
A brand of high-frequency laminate materials. They are used when FR-4’s electrical, thermal, or mechanical performances aren’t sufficient.
When choosing a laminate material, factors such as operating temperature, required electrical properties (like dielectric constant and loss tangent), mechanical strength, cost, and the specific requirements of the final application should be considered. The choice of laminate can significantly influence the performance and reliability of the final product.
Considerations Selecting Printed Circuit Board laminates Material
When it comes to selecting the right laminate material for printed circuit boards (PCBs), there are several important considerations to keep in mind. These considerations include:
Electrical Performance: Evaluate the electrical properties of the laminate, such as dielectric constant, loss tangent, and impedance control. The chosen material should provide the required electrical performance for your circuit design.
Thermal Management: Consider the thermal properties of the laminate, including thermal conductivity and coefficient of thermal expansion (CTE). These properties are crucial for effective heat dissipation and preventing thermal stress on components.
Mechanical Strength: Assess the mechanical strength and rigidity of the laminate material. It should be able to withstand the mechanical stresses encountered during PCB fabrication, assembly, and operation.
Dimensional Stability: Look for laminates with low moisture absorption and CTE to ensure dimensional stability over a wide range of environmental conditions. This helps prevent warping or distortion of the PCB.
Chemical Resistance: Consider the laminate’s resistance to chemicals, solvents, and other substances it may come into contact with during its lifespan. This is particularly important in harsh or corrosive environments.
Fabrication Compatibility: Ensure that the chosen laminate material is compatible with the manufacturing processes involved in PCB fabrication, such as etching, drilling, and soldering.
Cost-Effectiveness: Evaluate the cost of the laminate material and ensure it aligns with your budget while meeting the required performance criteria.
Industry Standards and Certifications: Verify that the laminate material complies with industry standards and certifications. This ensures reliability, safety, and regulatory compliance for your PCB.
Application-Specific Requirements: Consider any specific requirements of your application, such as high-frequency performance, impedance control, or specialized environmental conditions. Choose a laminate material that can meet these unique needs.
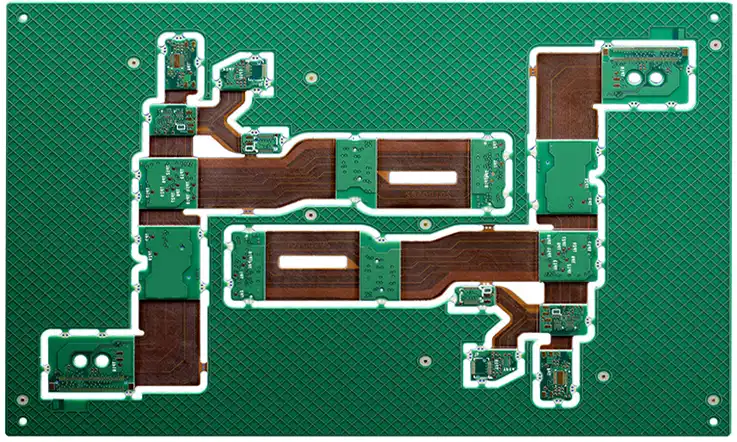
By carefully considering these factors, you can select a PCB laminate material that meets the electrical, thermal, mechanical, and environmental requirements of your specific application. This ensures optimal performance, reliability, and longevity of your printed circuit boards.
Difference Between Laminates and Prepregs
Laminates and prepregs are two distinct components used in the construction of printed circuit boards (PCBs). Although they are related, there are differences between the two:
Laminates: Laminates are composite materials consisting of multiple layers. They typically comprise a core substrate material, such as fiberglass-reinforced epoxy resin (FR-4), with a copper foil bonded to one or both sides. Laminates provide the structural foundation of the PCB and contribute to its mechanical strength and rigidity. They are available in various thicknesses and offer different electrical and thermal properties.
Prepregs: Prepregs, short for pre-impregnated materials, are also composite materials used in PCB manufacturing. Prepregs consist of a reinforcement material, such as fiberglass, impregnated with a resin, typically epoxy. Unlike laminates, prepregs do not have a copper foil layer bonded to them. Instead, they are used to build up the internal layers of a multilayer PCB. Prepregs are placed between copper layers or cores and are then subjected to heat and pressure during the lamination process. The heat causes the resin to flow and bond the layers together, creating a solid PCB structure.
In summary, laminates form the base material of the PCB, providing mechanical support and electrical insulation, while prepregs are used to create the internal layers of multilayer PCBs, serving as the adhesive material that bonds the layers together during the lamination process. Both laminates and prepregs are essential components in PCB fabrication, with each playing a specific role in the construction of the final PCB structure.
Importance of laminates in PCB fabrication
The utilization of laminates in PCB manufacturing is driven by several crucial factors that contribute to the overall success of the fabrication process. These key traits include enhanced impedance control, low moisture absorption, improved thermal management, and consistent performance in dynamic thermal reactions. As the electronic industry continues to evolve through discoveries and innovations, high-frequency laminates have emerged as a fundamental element for the advancement of PCB technologies.
JarnisTech excels in providing professional PCB layout and fabrication services, leveraging our skilled team of researchers and technical experts. We have developed effective lamination solutions tailored to your specific PCB projects. Our expertise encompasses a wide range of capabilities, including high-frequency laminates, achieving tighter hole-to-hole pitch, implementing exotic via structures, accommodating multiple lamination cycles, ensuring lead-free or halogen-free solder assembly with strict environmental considerations, and supporting high operating temperatures. These highlights demonstrate our commitment to incorporating robust laminate technologies.
To address any inquiries or request a quote, please feel free to reach out to us via email at [email protected] or by phone at 0086-0755-23034656. We are dedicated to providing solutions and assisting you in achieving your PCB objectives.
Benefits of Choosing a Reliable PCB Laminate Manufacturer
The selection of a dependable PCB laminate manufacturer holds paramount importance in guaranteeing the quality, reliability, and performance of your electronic devices. Here are several benefits associated with choosing a reliable PCB laminate manufacturer:
High-Quality Materials: A reliable manufacturer utilizes top-notch materials that ensure the durability and reliability of your PCBs. These materials exhibit resistance to heat, moisture, and other environmental factors that could potentially impact the performance of your electronic devices. By employing high-quality materials, manufacturers extend the lifespan of your PCBs, minimizing the need for frequent repairs or replacements.
Consistent Quality: A reputable PCB laminate manufacturer adheres to stringent quality control processes, ensuring that every PCB meets required standards. Utilizing advanced testing equipment, they meticulously identify and rectify any defects or issues in the PCBs, enabling consistent quality. Such consistency significantly reduces the risk of failures or malfunctions in your electronic devices.
Customization Options: A reliable manufacturer offers customized solutions tailored to your specific requirements. With their expertise and knowledge, they can design and manufacture PCBs that precisely align with your needs, optimizing the performance of your electronic devices. Customization options encompass various aspects such as size, shape, materials, and the integration of specific features or functionalities.
Cost-Effectiveness: Opting for a reliable PCB laminate manufacturer can yield long-term cost savings. By utilizing high-quality materials and implementing stringent quality control measures, they mitigate the risk of failures or malfunctions in your electronic devices. This, in turn, reduces the frequency of repairs or replacements, translating into significant cost savings over time.
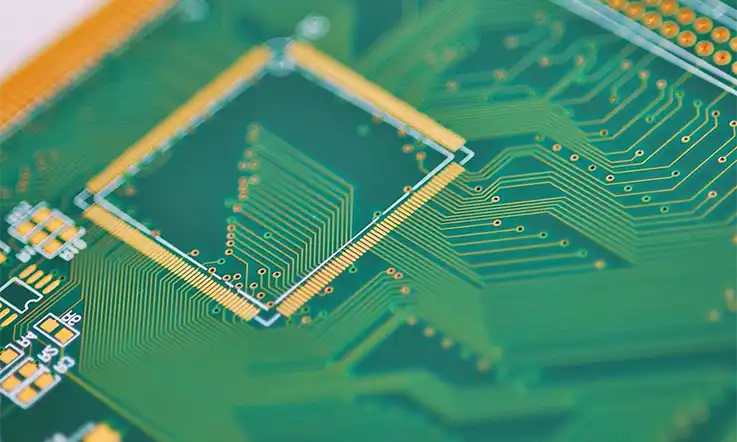
Timely Delivery: Recognizing the significance of timely delivery, a dependable PCB laminate manufacturer maintains a streamlined manufacturing process. This ensures that your PCBs are delivered punctually, minimizing any disruptions in your production timeline. Timely delivery allows you to meet your deadlines, ensuring that your electronic devices are available to your customers as planned.
All in all, the meticulous selection of a reliable PCB laminate manufacturer is essential for upholding the quality, reliability, and performance of your electronic devices. Their provision of high-quality materials, consistent quality, customization options, cost-effectiveness, and adherence to timely delivery schedules makes them an ideal choice for your PCB manufacturing needs.
Summary
With an extensive industry experience spanning over two decades, JarnisTech proudly stands as a leading PCB and PCB assembly manufacturer based in China. Our expertise lies not only in providing quick-turn PCB prototypes and assembly services but also in catering to medium and small volume PCB fabrication requirements. We possess a specialized focus on lamination and sequential lamination techniques, ensuring the long-term cost-effectiveness and optimal functionality of electronic devices.
Circuit board laminates serve multiple purposes in PCB construction, including providing electrical insulation between copper traces, offering mechanical support for electronic components, and ensuring consistent dielectric properties for optimal transmission of electrical currents through the copper traces without attenuation.
When working with circuit board laminates, it is advisable to seek guidance from a professional PCB manufacturer-JarnisTech. Our expertise can help ensure the appropriate selection and use of these materials in your circuit boards, leading to reliable and high-performance PCB assemblies.
Related Posts:
2. PCB Copper Trace Width and Space: Everything You Need to Know About Them
3. Which Types are Most Commonly Used in PCB Substrates?
4. What Is Fiberglass PCB and Why Fiberglass Used in PCB Manufacturing?
5. Standard PCB Thickness-Choosing the Correct Thickness for PCB