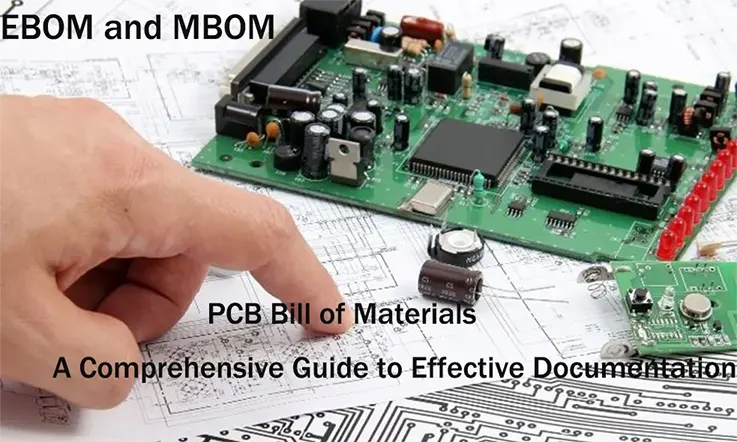
In the realm of electronics manufacturing, the creation of a well-structured and accurate Bill of Materials (BOM) is crucial for the successful assembly and production of printed circuit boards (PCBs). The PCB BOM serves as a comprehensive inventory list that outlines all the components required to build a PCB, encompassing everything from resistors and capacitors to integrated circuits and connectors.
A meticulously crafted PCB BOM not only ensures the procurement of the correct components but also streamlines the manufacturing process, reduces errors, and facilitates efficient inventory management. It acts as a vital reference document for design engineers, procurement specialists, and assembly teams, enabling seamless collaboration and effective decision-making throughout the product development lifecycle.
This guide aims to provide a comprehensive understanding of PCB BOMs, covering various aspects such as their importance, key components, organization, and best practices for their creation and maintenance. We will delve into the fundamental steps involved in creating a PCB BOM, including gathering component information, assigning part numbers, specifying quantities, and ensuring accurate documentation.
What Is A Bill Of Materials (BOM)?
Electronic products consist of a multitude of components and parts, and it is imperative for organizations involved in manufacturing and distributing such products to establish, review, and regularly audit a comprehensive list of features. This list, commonly known as the Bill of Materials (BOM), can be likened to a “shopping list” in more accessible terms.
The BOM serves as a vital document that encompasses all the necessary elements required to procure the specific parts essential for the electronic product. It must provide comprehensive answers to various aspects of the product, including component identification, assembly guidelines, staffing requirements, and resource allocation.
When drawing a parallel between the tech industry and the service industry, it becomes evident that proprietors of businesses in the service industry also rely on similar lists. They essentially possess their own version of a BOM, which aids them in supply ordering and staffing decisions.
Likewise, electronic product manufacturers must recognize the significance of creating a BOM tailored to their specific needs. Although the items on their list may differ from those in other industries, the fundamental principle remains unchanged: a well-structured BOM is indispensable. It serves as a crucial reference point for efficient procurement, assembly planning, workforce allocation, and overall operational management in the realm of electronic product manufacturing.
Types of BOM structure
The bill of materials (BOM) can be structured in two different ways, each serving distinct purposes:
Single-level BOM
The single-level BOM presents each part of the product along with the quantity required, resembling a shopping list. It is relatively straightforward to design. However, this type of BOM does not provide insight into the relationships between components, subassemblies, and assemblies used in the manufacturing process. Consequently, it is not the most suitable option for complex products. Additionally, if a product malfunctions, it becomes challenging to identify the specific component that requires replacement or repair. For instance, in a single-level BOM for a vehicle, a faulty door handle would not be differentiated from the parts used in other areas of the vehicle.
Multi-level BOM
A multi-level BOM reveals the hierarchical relationships between assemblies, components, and subassemblies. It identifies the materials that constitute higher-level assemblies, making it an indented BOM. While creating a multi-level BOM requires more time and effort, it provides greater detail and distinguishes between child and parent parts within a product. This comprehensive view of the BOM structure facilitates understanding and documentation of the product’s assembly hierarchy. Multi-level BOMs are particularly valuable for complex products that involve multiple levels of subassemblies and dependencies.
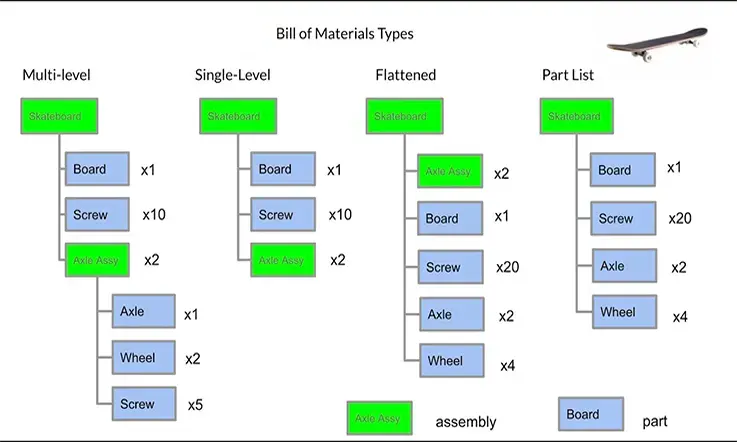
In summary, the single-level BOM offers simplicity but lacks the ability to capture complex product structures and component relationships. On the other hand, the multi-level BOM provides a detailed and hierarchical view, allowing for better comprehension of the product’s assembly structure, making it the preferred choice for intricate products.
Types of Bills of Materials
A Bill of Materials (BOM) is an essential document used in product development and replacement parts ordering processes, providing significant benefits in terms of planning acquisition orders and minimizing potential errors. BOMs can be categorized into two main types: Engineering BOMs and Manufacturing BOMs.
Engineering BOM
An Engineering Bill of Materials serves to define the design specifications of the final product. It encompasses various aspects, including alternative and substitute part numbers, as well as parts mentioned in the drawing notes. Each line of the BOM includes crucial information such as the product code, part name, part number, part revision, description, quantity, unit of measure, size, length, weight, and specifications or features of the product.
Typically, engineers organize the Engineering BOM based on computer-aided design (CAD) drawings. In the case of a finished product, multiple Engineering BOMs may be created. This process is an integral part of product lifecycle management.
Manufacturing BOM
A Manufacturing Bill of Materials represents a comprehensive list of assemblies and parts necessary for constructing a finished product that is ready for shipment. It encompasses not only the components but also the packaging materials required for delivering the product to the customer. The Manufacturing BOM contains detailed information about the manufacturing processes that need to be executed on the product before its completion. It serves as a repository of essential data for various manufacturing activities.
By employing both Engineering BOMs and Manufacturing BOMs, organizations can effectively manage the design and production phases of their products, ensuring accurate documentation, streamlined manufacturing processes, and improved overall efficiency.
Difference between EBOM and MBOM
The main difference between Engineering Bill of Materials (EBOM) and Manufacturing Bill of Materials (MBOM) lies in their purpose and level of detail:
Purpose
EBOM: The EBOM focuses on the design and engineering aspects of a product. It defines the components, their relationships, and specifications required to create the product based on its design intent. The EBOM serves as a reference for engineers during the product development phase, ensuring accurate design representation and facilitating collaboration between engineering teams.
MBOM: The MBOM, on the other hand, is oriented towards the manufacturing process. It includes all the assemblies, sub-assemblies, components, and packaging materials required to build the final product. The MBOM provides instructions for manufacturing operations, such as assembly steps, routing, and resource allocation. It serves as a guide for production teams to efficiently manufacture the product.
Level of Detail
EBOM: The EBOM is typically more detailed and granular, capturing the specific part numbers, revisions, descriptions, quantities, and specifications of each component. It may also include alternative or substitute part numbers and notes related to the design intent. The EBOM provides the necessary information for engineering teams to accurately represent the product design and make informed decisions during the development phase.
MBOM: The MBOM is generally less detailed than the EBOM, focusing more on the overall structure of the product and the manufacturing processes. It may include higher-level assemblies, standardized components, and general instructions for manufacturing operations. The MBOM provides the information required for production planning, resource allocation, and sequencing of manufacturing activities.
Lifecycle Stage
EBOM: The EBOM is primarily used during the early stages of product development, starting from the design phase and continuing through engineering changes and iterations. It helps engineers maintain design consistency and facilitates collaboration between cross-functional teams involved in product design.
MBOM: The MBOM becomes significant during the later stages of product development, when the design is finalized and ready for manufacturing. It plays a crucial role in production planning, material procurement, and assembly operations. The MBOM is continuously updated to reflect changes in the manufacturing process, component availability, and improvements in production efficiency.
Both EBOM and MBOM are essential documents in product development and manufacturing. While the EBOM focuses on design and engineering specifications, the MBOM provides instructions for production and guides the manufacturing process. Effective coordination and synchronization between these two BOMs are crucial to ensure a smooth transition from design to manufacturing and to achieve high-quality, cost-effective production of the desired product.
Impact of BOM on PCB Manufacturing Efficiency
The impact of the Bill of Materials (BOM) on PCB manufacturing efficiency is significant. The BOM serves as a critical reference document that lists all the components, materials, and specifications required for the assembly of a PCB. Here are some key ways in which the BOM influences manufacturing efficiency:
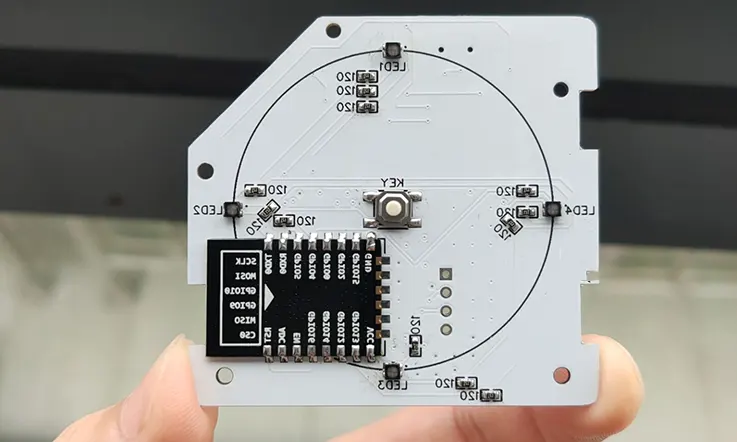
Component Selection and Availability
The BOM provides a comprehensive list of components needed for PCB assembly. By carefully selecting components based on availability, lead time, and compatibility with manufacturing processes, the BOM can help streamline the procurement process and reduce delays caused by component unavailability or substitution.
Manufacturing Process Planning
The BOM specifies the required materials, components, and their quantities, enabling efficient planning of the manufacturing process. It helps determine the order of operations, assembly sequence, and allocation of resources, ensuring a smooth and optimized production flow.
Cost Optimization: The BOM includes the cost information for each component, allowing manufacturers to evaluate the overall cost of the PCB assembly. By analyzing the BOM data, manufacturers can identify opportunities for cost optimization, such as selecting alternative components or negotiating better pricing with suppliers, leading to improved cost-efficiency.
Design for Manufacturing (DFM) Considerations
The BOM plays a crucial role in implementing DFM principles during PCB design. By considering the manufacturing constraints and guidelines outlined in the BOM, designers can optimize component placement, minimize manufacturing complexities, and reduce the likelihood of errors or rework during assembly.
Supply Chain Management
The BOM serves as a guide for managing the supply chain effectively. It helps manufacturers collaborate with suppliers, ensuring timely procurement of components and materials. With accurate BOM information, manufacturers can maintain efficient inventory levels, avoid shortages or excess stock, and minimize production delays.
Assembly and Testing Efficiency
The BOM provides detailed information about each component, including part numbers, specifications, and assembly instructions. This data facilitates the smooth execution of the assembly process, ensuring correct component placement, reducing rework, and minimizing the potential for errors. The BOM also guides testing procedures, enabling comprehensive and efficient quality control measures.
Documentation and Traceability
The BOM serves as a reference for documentation, allowing manufacturers to create accurate assembly instructions, test procedures, and product documentation. It enables traceability throughout the manufacturing process, facilitating quality control, troubleshooting, and future revisions or improvements.
By optimizing the BOM, manufacturers can enhance PCB manufacturing efficiency, reduce production lead times, minimize errors, and improve overall product quality. Accurate and well-managed BOMs contribute to better supply chain management, streamlined assembly processes, and cost-effective production, ultimately leading to increased operational efficiency.
Key Considerations Prior to Bill of Materials Creation
Prior to creating a bill of materials (BOM), it is essential to consider certain factors to ensure a comprehensive and effective BOM creation process. Skipping any steps can result in inefficiencies and inaccuracies. Therefore, it is important to address the following questions and have clear answers before embarking on BOM creation:
Understanding the Scope of Your Project
Before initiating the BOM creation, it is crucial to have already commenced the design phase of your project. This phase will equip you with knowledge about the various parts, components, and assemblies that need to be included in the BOM. It is imperative to ensure that your design plan has been thoroughly tested and functions as expected.
Effective BOM Management Strategies
Creating a BOM involves multiple iterations and updates. Therefore, it is essential to establish a systematic approach for managing the BOM throughout its lifecycle. This includes maintaining the latest version of the BOM, implementing identifiers to track different versions, and granting appropriate access for a select group of individuals who can edit the document. Additionally, it is important to keep records of supporting documents such as work instructions and CAD drawings.
Identifying BOM Users and Stakeholders
Consideration should be given to the diverse group of individuals who will rely on the BOM. In many cases, face-to-face interactions may not occur with all users of the BOM. As a result, the BOM should contain comprehensive details that cater to the needs of different stakeholders throughout the product’s lifecycle. Designing the BOM with the intended users in mind ensures that it effectively serves their requirements.
Essential Components of a Comprehensive BOM
It is crucial to determine the specific information that should be included in the BOM. Every BOM should encompass fundamental details such as part names. Additionally, certain items may be optional depending on the project requirements. Furthermore, a decision needs to be made regarding the inclusion of consumables such as fasteners and glues. Manufacturers often deliberate whether to incorporate consumables in the BOM, and careful consideration should be given to their inclusion based on the specific project needs.
By addressing these key questions and understanding the necessary considerations, the BOM creation process can be approached methodically, resulting in a well-structured and comprehensive bill of materials.
How Do You Create a Bill of Materials?
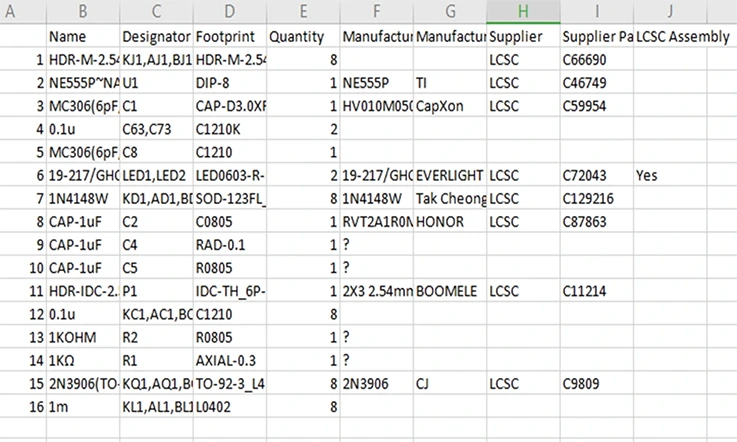
Creating a Bill of Materials (BOM) involves several steps to ensure accuracy and completeness. Here’s a general guide on how to create a BOM:
Gather product information: Collect all relevant details about the product, including its design specifications, drawings, and any other technical documentation. This information will serve as the foundation for the BOM.
Identify components and assemblies: Review the product documentation and identify all the components and assemblies required to build the product. This includes both purchased parts and internally manufactured parts.
Assign part numbers: Assign a unique part number to each component and assembly. Part numbers help in identifying and tracking each item within the BOM.
Provide descriptions: Write clear and concise descriptions for each part to ensure proper identification. Include key details such as dimensions, materials, and any other relevant specifications.
Specify quantities: Determine the quantity of each part required to build the product. This can be based on the product design, manufacturing requirements, or customer demand.
Determine unit of measure: Define the unit of measure for each part, such as pieces, meters, kilograms, or any other appropriate unit. Consistency in unit of measure is crucial for accurate inventory management and procurement.
Include additional information: Depending on the complexity of the product, consider adding supplementary information to the BOM, such as part revisions, supplier information, pricing, lead times, and any special instructions or notes.
Organize the BOM structure: Arrange the components and assemblies in a hierarchical structure, reflecting their relationships and dependencies. This structure helps to visualize the product’s assembly process.
Validate and review: Double-check the BOM for accuracy, completeness, and consistency. Engage relevant stakeholders, such as engineers, designers, and procurement specialists, to review and validate the BOM before finalizing it.
Maintain and update: As the product evolves or changes occur, keep the BOM up to date. Regularly review and update the BOM to reflect any modifications, new part numbers, or revisions.
Software applications specifically designed for BOM management, such as product lifecycle management (PLM) systems or enterprise resource planning (ERP) software, can greatly simplify the process of creating and maintaining BOMs. These tools provide centralized data management, version control, and collaboration capabilities, ensuring accurate and efficient BOM creation and management.
Advanced Uses for a Bill of Materials
In addition to the fundamental aspects we have discussed previously, it is important to highlight several advanced features associated with PCB BOMs. These features allow for enhanced organization and presentation of data within the BOM, as well as the inclusion of more detailed design information. The following examples illustrate these advanced capabilities:
Customizable BOM Format: The format of an electronic BOM can be tailored to meet specific requirements. Traditionally, BOMs are organized based on comment information, but it is possible to restructure them by grouping components according to their footprint information. This flexibility enables the BOM to be presented in a manner that best suits the needs of the project or the intended audience.
Inclusion of Un-fitted Components: The BOM PCB provides the option to include parts that are designated as un-stuffed or not fitted. This means that components which are not physically populated on the board during assembly can still be included in the BOM. Including un-fitted components in the BOM ensures comprehensive documentation of all intended parts, even if they are not present on the final assembled board.
Variant-specific PCB BOM Generation: In scenarios where different variations of a board exist with varying options for component placement (fitted or not fitted), it is possible to generate distinct PCB BOMs for each variant. This capability allows for the creation of separate BOMs that precisely reflect the specific stuffing options chosen for different iterations of the board. By generating variant-specific BOMs, accurate and targeted information can be provided to facilitate the assembly process for each board configuration.
By leveraging these advanced features, PCB BOMs can be customized, comprehensive, and well-structured, enabling efficient assembly and effective communication of design information throughout the manufacturing process.
Common Errors and How to Avoid Them
Failure to meet the necessary quality standards in a BOM can lead to various issues during production, including component mismatches, higher costs than anticipated, and delays in product release. One prevalent error involves the omission or incorrect placement of components within the BOM. In some cases, a missing component can be added during rework, but this will result in delivery delays and additional expenses.
If the BOM lacks explicit instructions on component placement, there is a risk of parts being interchanged during manufacturing. Immediate detection of this problem enables the manufacturer to modify or rerun the production batch. However, if the issue remains undetected until prototype testing or initial production, rectifying it becomes more challenging.
The primary types of errors in BOMs can be classified as follows:
Inventory Errors: Inaccurate specification of component quantities inevitably leads to project delays and increased costs. Similarly, missing components have the same detrimental impact on production schedules and expenses.
Product Evaluation Mistakes: The components specified in the BOM must align with the budgetary requirements established for production. Failure to meet these requirements may render the project financially unfeasible and necessitate its abandonment.
Use of Non-standard Parts: Certain electronic devices, such as medical equipment and wearables, must adhere to stringent safety regulations. The use of components that do not comply with these standards, such as substandard lithium-ion batteries, can result in severe consequences for users and damage the brand’s reputation.
Outdated or Untracked BOM: Before commencing production, it is crucial to ensure the accuracy of all information contained in the BOM and confirm that the version sent to the manufacturer is the most up-to-date. Even minor errors can have disastrous effects during PCB manufacturing.
By maintaining stringent quality control measures and diligently addressing potential errors in the BOM, manufacturers can mitigate production issues, minimize costs, and uphold the integrity and safety of the final product.
Conclusion
The utilization of a bill of materials (BOM) holds great significance in the realm of electronics and PCB manufacturing as it greatly facilitates the product development process. By employing a BOM, the occurrence of multiple errors can be effectively mitigated. BOMs find extensive application throughout the PCB manufacturing process.
Moreover, it is paramount to ensure the provision of precise and accurate information within the BOM list. This crucial document must encompass the correct quantities of raw materials, parts, and components required for the seamless manufacturing of a product.
Related Posts:
1. Gerber Files: How to Generate in PCB Design Process?
2. Gerber Files: Role in PCB Manufacturing
3. ODB++: The Ultimate FAQ Guide in 2023
4. Critical Information about Gerber Files for PCB Manufacturing